隧道二衬背后空洞分析及防治措施(中铁11局)
浅谈隧道初支及二衬背后脱空的防治方法
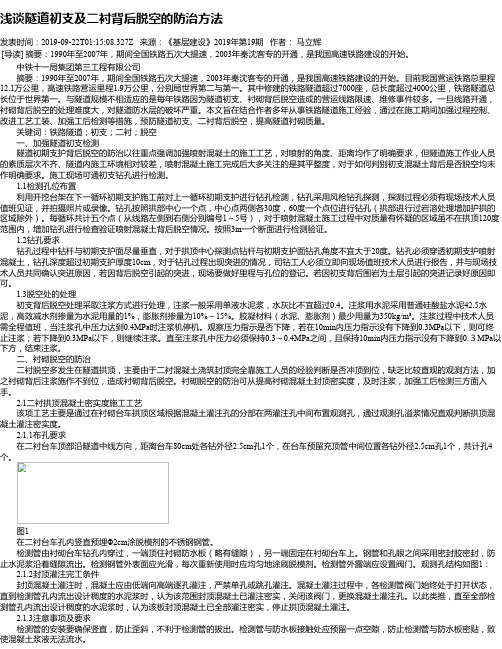
浅谈隧道初支及二衬背后脱空的防治方法发表时间:2019-09-22T01:15:08.327Z 来源:《基层建设》2019年第19期作者:马立辉[导读] 摘要:1990年至2007年,期间全国铁路五次大提速,2003年秦沈客专的开通,是我国高速铁路建设的开始。
中铁十一局集团第三工程有限公司摘要:1990年至2007年,期间全国铁路五次大提速,2003年秦沈客专的开通,是我国高速铁路建设的开始。
目前我国营运铁路总里程12.1万公里,高速铁路营运里程1.9万公里,分别局世界第二与第一。
其中修建的铁路隧道超过7000座,总长度超过4000公里,铁路隧道总长位于世界第一。
与隧道规模不相适应的是每年铁路因为隧道初支、衬砌背后脱空造成的营运线路限速、维修事件较多。
一旦线路开通,衬砌背后脱空的处理难度大,对隧道防水层的破坏严重。
本文旨在结合作者多年从事铁路隧道施工经验,通过在施工期间加强过程控制、改进工艺工装、加强工后检测等措施,预防隧道初支、二衬背后脱空,提高隧道衬砌质量。
关键词:铁路隧道;初支;二衬;脱空一、加强隧道初支检测隧道初期支护背后脱空的防治以往重点强调加强喷射混凝土的施工工艺,对喷射的角度、距离均作了明确要求,但隧道施工作业人员的素质层次不齐、隧道内施工环境相对较差,喷射混凝土施工完成后大多关注的是其平整度,对于如何判别初支混凝土背后是否脱空均未作明确要求。
施工现场可通初支钻孔进行检测。
1.1检测孔位布置利用开挖台架在下一循环初期支护施工前对上一循环初期支护进行钻孔检测,钻孔采用风枪钻孔探测,探测过程必须有现场技术人员值班见证,并拍摄照片或录像。
钻孔按照拱部中心一个点,中心点两侧各30度,60度一个点位进行钻孔(拱部进行过岩溶处理增加护拱的区域除外)。
每循环共计五个点(从线路左侧到右侧分别编号1~5号),对于喷射混凝土施工过程中对质量有怀疑的区域虽不在拱顶120度范围内,增加钻孔进行检查验证喷射混凝土背后脱空情况。
隧道施工常见问题原因分析和处理措施方案

隧道施工中常见问题原因分析及处理预防措施问题一:二衬拱顶、拱腰个别地方存在空洞和不密实㈠原因分析:1、Ⅱ、Ⅲ级围岩光爆效果差,造成隧道开挖轮廓凹凸不平,有棱角⑴光爆设计不合理(孔网参数、装药结构、起爆网络等)。
⑵火工品的性能不稳定(炸药的爆速、非电毫秒雷管延期时间的精确性、火工品的可靠性)。
⑶钻爆时施工班组存在偷工行为,未按要求炮眼间距、数量布置炮眼。
⑷在开挖断面的下部位置,由于作业空间的限制和操作人员的操作水平的问题。
在钻眼时,未能较好的控制钻杆的角度和周边眼的间距。
⑸在周边眼施工放样时,放样精度不满足要求。
2、人为原因:⑴Ⅱ、Ⅲ级围岩初期支护砼厚度不足,喷射砼时未把凹凸面喷平,平整未达到规范要求。
⑵防水板铺设时未预留好足够的松铺系数,导致砼浇筑完毕后防水板未与初支面密贴。
⑶在砼浇筑到拱顶位置时,未及时的调整砼的坍落度,导致拱顶未被砼充填密实。
⑷在砼浇筑到拱顶位置时出现堵管现象,现场人员在未仔细分析原因的情况下就主观地认为已经管满,停止砼泵送造成二衬厚度不足,出现脱空现象。
⑸在浇筑二衬砼时,施工作业班组主观上存在偷工减料行为,表现为衬砌厚度不足,注浆不满、不实等现象;现场管理人员在砼最后补方时,向拌合站提供的补方数量不准确,造成拌合站停止砼搅拌,实际二衬砼在未注满的情况下停止,造成二衬脱空。
⑹在二衬砼未初凝前急于拆管,造成未自稳的砼掉在自重的作用下下落形成漏斗,造成二衬脱空。
3、技术原因:⑴砼的收缩徐变,导致空隙。
⑵砼施工配合比水灰比偏大、坍落度大、砼振捣不密实,砼自重下沉。
⑶用输送泵输送砼时,拱顶的砼在输送过程中把部分空气密闲在狭小空间内无法排出,造成空隙。
㈡处理措施1、加强Ⅱ、Ⅲ级围岩光爆控制,提高光爆效果和基岩面平整度。
⑴针对不同围岩、不同的开挖断面、有无仰拱三种情况重新进行光爆设计,其设计参数见(表1~表5及附图):⑵提高轮廓线放样精度,周边轮廓线的放样允许误差控制为±2cm。
隧道二衬背后空洞强度和厚度不足分析及防治措施

a.开挖成型差,局部欠挖未及时处理;b.初支变型,收敛沉降超出预留变型量;c.防水板铺设前未进行断面复测,初支侵线;d.防水板铺设松弛度控制不到位,挂点不牢固造成防水板脱落切割混凝土;e.模板台车定位不准,偏位或固定不牢形成位移造成二衬厚度不足;f.混凝土浇筑过程形成空洞造成厚度不足(主要形成原因见2.1)
2.2强度不足原因分析
2.2.1初支钢结构强度不足形成原因:
a.钢构件原材料进场把关不严,使用不合格钢材生产的钢构件造成强度不足;b.加工场加工工艺质量差,焊接不牢固,使用不合格焊接材料焊接造成钢构件强度不足;c.安装过程连接螺栓未上齐拧紧,使用不合格螺栓,随意切割焊接等造成钢构件强度不足;d.拱架连接筋数量不够、焊接不牢固、与锁脚锚杆焊接不牢固等造成初支钢结构强度不足。
2.3厚度不足原因分析
2.3.1初支喷射混凝土厚度不足形成原因:
a.开挖成型差,超挖后为减少喷射混凝土量,人为采用支挡、填塞杂物等方法或欠挖造成初支厚度不足;b.喷射工艺不到位,喷浆不饱满或平整度差造成初支厚度不足;c.喷射过程中围岩掉块未及时清理造成初支厚度不足;d.过程管控不严,作业人员偷懒造成初支厚度不足;e.软弱围岩人为缩减预留变型量或收敛沉降过大造成初支侵站二衬净空,为保证二衬厚度人为凿除造成初支厚度不足。
2.3.2仰拱及填充厚度不足形成原因:
a.仰拱开挖深度不足或开挖成型差,局部欠挖形成仰拱或填充厚度不足;b.偷工减料,人为提高仰拱开挖深度形成仰拱或填充厚度不足;c.工序验收把关不严,仰拱施工前未进行断面复测形成仰拱或填充厚度不足。
2.ቤተ መጻሕፍቲ ባይዱ.3二衬钢筋保护层厚度不足形成原因:
a.钢筋安装前测量放样不准或错误;b.架立筋安装偏位,未严格按照测量放点和技术交底布置定位筋;c.钢筋保护层垫块安装数量不足,未按照技术交底进行设置;d.因钢筋自重造成架立筋变型或弯曲,引起钢筋整体下移或偏移;e.工序验收把关不严,现场施工负责人,技术员对钢筋保护层垫块设置的重要性认识不足,“三检制”执行不严。
铁路隧道衬砌背后空洞影响及处理分析
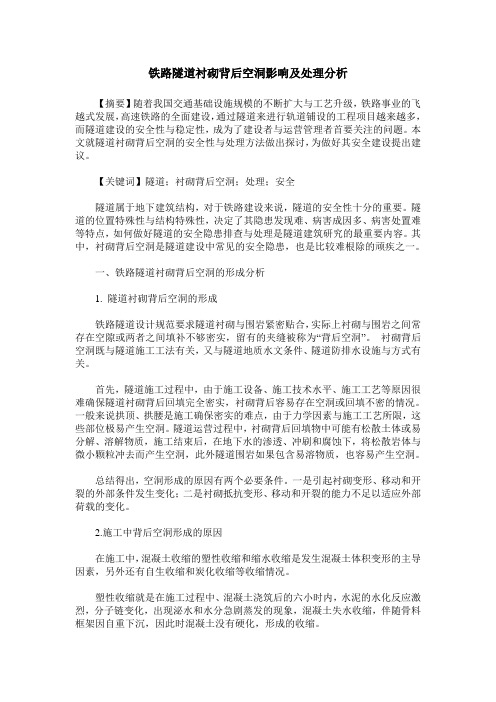
铁路隧道衬砌背后空洞影响及处理分析【摘要】随着我国交通基础设施规模的不断扩大与工艺升级,铁路事业的飞越式发展,高速铁路的全面建设,通过隧道来进行轨道铺设的工程项目越来越多,而隧道建设的安全性与稳定性,成为了建设者与运营管理者首要关注的问题。
本文就隧道衬砌背后空洞的安全性与处理方法做出探讨,为做好其安全建设提出建议。
【关键词】隧道;衬砌背后空洞;处理;安全隧道属于地下建筑结构,对于铁路建设来说,隧道的安全性十分的重要。
隧道的位置特殊性与结构特殊性,决定了其隐患发现难、病害成因多、病害处置难等特点,如何做好隧道的安全隐患排查与处理是隧道建筑研究的最重要内容。
其中,衬砌背后空洞是隧道建设中常见的安全隐患,也是比较难根除的顽疾之一。
一、铁路隧道衬砌背后空洞的形成分析1. 隧道衬砌背后空洞的形成铁路隧道设计规范要求隧道衬砌与围岩紧密贴合,实际上衬砌与围岩之间常存在空隙或两者之间填补不够密实,留有的夹缝被称为“背后空洞”。
衬砌背后空洞既与隧道施工工法有关,又与隧道地质水文条件、隧道防排水设施与方式有关。
首先,隧道施工过程中,由于施工设备、施工技术水平、施工工艺等原因很难确保隧道衬砌背后回填完全密实,衬砌背后容易存在空洞或回填不密的情况。
一般来说拱顶、拱腰是施工确保密实的难点,由于力学因素与施工工艺所限,这些部位极易产生空洞。
隧道运营过程中,衬砌背后回填物中可能有松散土体或易分解、溶解物质,施工结束后,在地下水的渗透、冲刷和腐蚀下,将松散岩体与微小颗粒冲去而产生空洞,此外隧道围岩如果包含易溶物质,也容易产生空洞。
总结得出,空洞形成的原因有两个必要条件。
一是引起衬砌变形、移动和开裂的外部条件发生变化;二是衬砌抵抗变形、移动和开裂的能力不足以适应外部荷载的变化。
2.施工中背后空洞形成的原因在施工中,混凝土收缩的塑性收缩和缩水收缩是发生混凝土体积变形的主导因素,另外还有自生收缩和炭化收缩等收缩情况。
塑性收缩就是在施工过程中、混凝土浇筑后的六小时内,水泥的水化反应激烈,分子链变化,出现泌水和水分急剧蒸发的现象,混凝土失水收缩,伴随骨料框架因自重下沉,因此时混凝土没有硬化,形成的收缩。
铁路隧道二次衬砌裂缝预防及控制措施
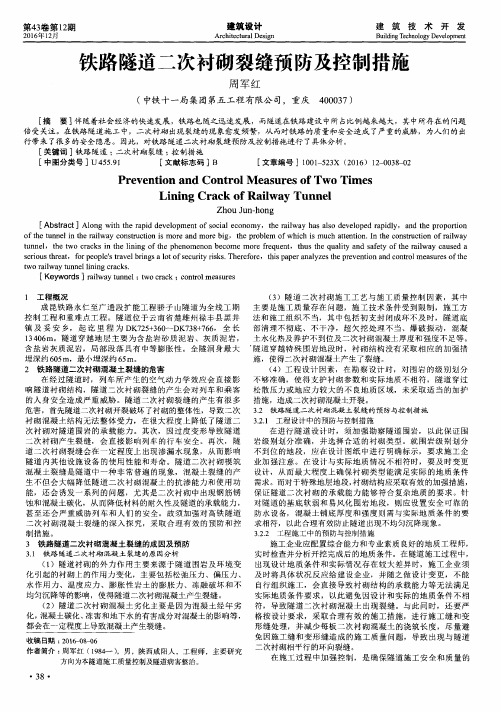
s e r i o u s t h r e a t ,f o r p e o p l e ’ S t r a v e l b r i n g s a l o t o f s e c u r i t y r i s k s . T h e r e f o r e ,t h i s p a p e r a n a l y z e s t h e p r e v e n t i o n a n d c o n t r o l me a s u r e s o f t h e
隧道 穿越特 殊 围岩地 段时 ,衬 砌结 构没有采 取相 应 的加 强措
施 ,使 得二 次衬 砌 混 凝 土 产生 了裂 缝 。 ( 4 )工程 设计 因素 ,在 勘察 设计 时,对 围岩 的 级别 划分 不 够 准 确 , 使 得 支 护 衬 砌 参 数 和 实 际 地 质 不 相 符 , 隧 道 穿 过 松 散 压 力 或 地 应 力 较 大 的 不 良地 质 区域 , 未 采 取 适 当 的 加 护 措施 ,造成二次衬砌混凝土开裂 。 3 . 2 铁路 隧道 二 次衬砌 混凝 土裂 缝 的预 防与控 制措施 3 . 2 . 1 工程设 计 中 的预防 与控制 措施 在进 行隧 道设 计时 ,须加 强勘 察隧 道围岩 ,以此保 证 围 岩级别划分 准确 ,并选择 合适 的衬砌类 型。就 围岩级 别划分 不 到 位 的地 段 ,应 在 设 计 图纸 中 进 行 明 确 标 示 , 要 求 施 工 企 业加 强注 意。在 设计与 实际地 质情 况不相符 时,要及 时变 更 设计 ,从而 最大程 度上确 保衬砌 类 型能满足实 际的地 质条 件
第4 3 卷第 1 2 期
2 0 1 6 年1 2 月
建筑 设计
Ar c hi t e c t ur a l De s i g n
浅谈隧道二衬背后脱空原因分析及其防治措施
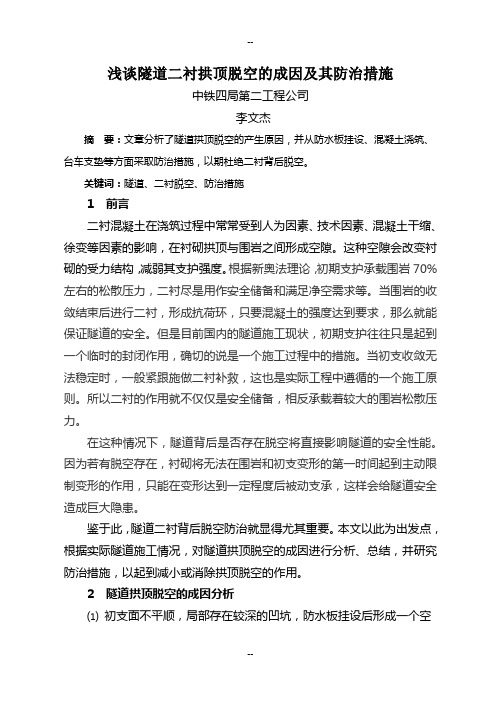
浅谈隧道二衬拱顶脱空的成因及其防治措施中铁四局第二工程公司李文杰摘要:文章分析了隧道拱顶脱空的产生原因,并从防水板挂设、混凝土浇筑、台车支垫等方面采取防治措施,以期杜绝二衬背后脱空。
关键词:隧道、二衬脱空、防治措施1 前言二衬混凝土在浇筑过程中常常受到人为因素、技术因素、混凝土干缩、徐变等因素的影响,在衬砌拱顶与围岩之间形成空隙。
这种空隙会改变衬砌的受力结构,减弱其支护强度。
根据新奥法理论,初期支护承载围岩70%左右的松散压力,二衬尽是用作安全储备和满足净空需求等。
当围岩的收敛结束后进行二衬,形成抗荷环,只要混凝土的强度达到要求,那么就能保证隧道的安全。
但是目前国内的隧道施工现状,初期支护往往只是起到一个临时的封闭作用,确切的说是一个施工过程中的措施。
当初支收敛无法稳定时,一般紧跟施做二衬补救,这也是实际工程中遵循的一个施工原则。
所以二衬的作用就不仅仅是安全储备,相反承载着较大的围岩松散压力。
在这种情况下,隧道背后是否存在脱空将直接影响隧道的安全性能。
因为若有脱空存在,衬砌将无法在围岩和初支变形的第一时间起到主动限制变形的作用,只能在变形达到一定程度后被动支承,这样会给隧道安全造成巨大隐患。
鉴于此,隧道二衬背后脱空防治就显得尤其重要。
本文以此为出发点,根据实际隧道施工情况,对隧道拱顶脱空的成因进行分析、总结,并研究防治措施,以起到减小或消除拱顶脱空的作用。
2 隧道拱顶脱空的成因分析⑴初支面不平顺,局部存在较深的凹坑,防水板挂设后形成一个空腔,因防水板松弛度所限,在混凝土浇筑后形成空洞。
⑵防水板挂设张弛度不适。
防水板如果挂设太松,在混凝土浇筑过程中会因受挤压形成褶皱,在褶皱之间留下空隙;防水板如果挂设太紧,会造成防水板与初支面之间留下空隙或因混凝土压力太大撑坏防水板。
⑶混凝土在浇筑过程中振捣不密实,内部存在气孔、空洞等,上部混凝土浇筑完成后在自重作用下下沉,在拱部造成空洞。
⑷拱部混凝土浇筑时,由于泵送压力或浇筑方式等问题,致使拱顶位置浇筑不到位,留下空洞。
铁路隧道二衬问题及现场施工质量控制措施[详细]
![铁路隧道二衬问题及现场施工质量控制措施[详细]](https://img.taocdn.com/s3/m/e8600be63c1ec5da51e2701f.png)
(三)隧道二衬浇筑施工质量控制及相关措施
隧道衬砌模板台车混凝土分配配管系统
隧道衬砌模板台车混凝土分配配管系统
隧道衬砌模板台车混凝土分配配管系统
二、 功效 展示:
1、配管 系统在国 内的应用:
2006年8月在中国大陆首 条海底隧道——厦门翔安 海底隧道首次使用。泵送 混凝土进入主管道后,快 速便捷的配管系统将混凝 土均衡、对称的输送到台 车的两侧,使台车两侧的 浇筑混凝土保持高度一致, 避免了模板台车施工过程 中人为因素而造成的施工
(三)隧道二衬浇筑施工质量控制及相关措施 二次衬砌防空洞工艺的改进
➢ 增设纵向注浆、排气管 纵向排气、注浆管安装采用防水板条焊接固定在易铺设防水板下
,排气管、注浆管以不同颜色区分。
纵向排气、注浆软管安装
(三)隧道二衬浇筑施工质量控制及相关措施 二次衬砌防空洞工艺的改进
➢ 增设纵向注浆、排气管
注浆、排气管采用φ20mm波纹管,波纹管需提前沿管路长度方 向按间距300mm、直径3mm钻设径向孔。且注浆管的钻孔应做好保护
①二衬背后空洞及厚度不足
(a)拱顶背后脱空
(b)设计40cm,实测19cm
(一)隧道二衬存在的质量问题
②混凝土离析及蜂窝麻面
(c)混凝土离析
③二衬剥落掉块
(d)蜂窝麻面
④二衬夹杂异物
(e)拱顶剥落掉块
(f)拱顶二衬夹杂异物块
(一)隧道二衬存在的质量问题
⑤钢筋布置不符要求
(g)仅布设单层钢筋
⑥止水带外露及衬砌渗漏水
(二)隧道二衬质量问题的原因分析
③二衬剥落掉块
➢衬砌钢轨保护层过大; ➢混凝土配合比不正确或拌合不均匀; ➢衬砌厚度或强度不足,脱模时间过早等。
隧道二次衬砌背后脱空以及厚度补强处理方案_secret

***隧道隧道衬砌背后脱空以及厚度不足的处理方案一、工程概述:我项目部施工的***隧道总长***m,2012年11月铁道部XX质量监督站对该隧道的衬砌质量进行了抽样检测,在检查中发现该隧道二次衬砌背后局部出现脱空及衬砌厚度微欠等现象,为了保证隧道二次衬砌质量符合验标规范要求,现对隧道二衬背后脱空进行分析处理。
并对脱空导致的衬砌厚度不足现象进行补强处理。
二、脱空以及厚度不足段落:1、脱空段落表1 长昆段隧道二衬背后脱空表2、厚度不足段落表2 长昆段二衬厚度检测结果汇总表13、二衬厚度不足段落在脱空范围内,初步拟定在脱空范围内采用高标号水泥砂浆进行二衬厚度补强处理。
三、原因分析:该隧道二衬背后脱空及厚度不足处位于拱腰等部位。
从二衬背后脱空部位分析,总结得出大致有以下几个原因:⑴初支面不平顺,局部存在较深的凹坑,防水板挂设后形成一个空腔,因防水板松弛度所限,在混凝土浇筑后形成空洞。
⑵防水板挂设张弛度不适。
防水板如果挂设太松,在混凝土浇筑过程中会因受挤压形成褶皱,在褶皱之间留下空隙;防水板如果挂设太紧,会造成防水板与初支面之间留下空隙或因混凝土压力太大撑坏防水板。
四、二衬背后脱空及厚度不足处理措施:通过对检测报告结果分析以及对现场情况的核查,总体情况为:1.二衬背后脱空3处;2.衬砌厚度不足2处,其中2处二衬厚度不足是由于二衬背后脱空所引起。
总体方案采用打孔注浆的方式进行处理,具体注浆措施如下:1、XX002+247.5-XX002+252二衬右拱腰背后轻微脱空;右拱腰XX002+250处抽检厚度为31cm-44cm,设计厚度为45cm,欠厚纵向长度约4m,环向宽度约1.1m。
线路方向环向DK103+250(图1)2、XX002+329-XX002+335段二衬右拱腰背后脱空;右拱腰XX002+330处抽检厚度为34cm~44cm,设计厚度为45cm,欠厚纵向长度约4.5m,环向宽度约0.8m。
线路方向环向DK103+332(图2)3、XX002+270-XX002+275.5段二衬右拱腰背后脱空。
- 1、下载文档前请自行甄别文档内容的完整性,平台不提供额外的编辑、内容补充、找答案等附加服务。
- 2、"仅部分预览"的文档,不可在线预览部分如存在完整性等问题,可反馈申请退款(可完整预览的文档不适用该条件!)。
- 3、如文档侵犯您的权益,请联系客服反馈,我们会尽快为您处理(人工客服工作时间:9:00-18:30)。
隧道二衬背后空洞分析及防治措施
高速铁路隧道病害较多,其中二衬背后空洞病害较为常见且危害大。
隧道二衬背后空洞将显著改变其结构受力状态,特别是在隧道开通后随着列车高速通过,产生较大的瞬间气压将增大二衬结构受拉破坏的可能性,进而影响到高铁营运安全。
因此施工过程中必须严格执行相关工艺、工法要求,杜绝二衬背后空洞情况的发生。
一、常见空洞分类
二衬背后空洞按照位置分四类。
一是初支空洞;二是防水板与初支间的空洞;三是二衬混凝土与防水板间空洞;四是二衬端头“两带”(环向背贴式止水带、中埋式止水带)与二衬混凝土之间的空洞。
二、空洞原因分析
(一)初支空洞
1.超挖后为减少喷射混凝土量,人为采用支挡、填塞杂物等方法,造成初支空洞;
2.喷射混凝土施工过程中围岩掉块未及时清理,造成初支背后空洞;
3.岩面渗水散流,未进行有效处理,导致喷射混凝土被渗蚀、冲刷后形成空洞;
4.喷射混凝土施工时未严格按照施工工艺要求施工,钢架周边存在喷射盲区,喷射不到位形成空洞。
(二)防水板与初支间空洞
1.初支平整度较差,防水板很难与初支密贴,形成空洞;
2.防水板铺设时松弛度不足,局部紧绷,在防水板与喷射混凝土面之间形成空洞;铺设防水板松弛度过大,固定点数不足,在二衬混凝土浇筑时受冲击,防水板脱落、褶皱,形成空洞。
(三)二衬混凝土与防水板间空洞
1.二衬混凝土浇筑时仅仅利用个别窗口,布料不均,混凝土依靠振捣流动至其他各窗口,流动距离过长,易造成粒料分布不均,混凝土不密实,浇筑完成后受自重下沉引起拱部脱空;下坡施工时,浇注段与上循环之间会形成空气囊(拱部)而造成衬砌背后空洞;
2.二衬混凝土冲顶时供应不及时、和易性不好、振捣不到位,造成局部形成空洞,而在拱顶带模注浆时注浆孔堵塞、注浆材料性能差、注浆工序操作不当等情况下,注浆不能完全消除二衬顶部空洞;
3.混凝土本身收缩、徐变较大,致使衬砌与防水板间出现空隙,此种原因造成的空隙一般小于2cm。
(四)衬砌端头“两带”(环向背贴式止水带、中埋式止水带)与衬砌混凝土之间的空洞。
1.环向背贴式止水带与防水板粘接不牢固,混凝土浇筑时止水带受挤压变形形成板缝空洞;
2.中埋式止水带固定不牢,混凝土浇筑时受挤压变形跑边、褶皱形成板缝空洞;
3.混凝土浇筑时端头堵缝采用土工布,下板二衬混凝土浇筑时未及时清理,形成空洞。
三、二衬防空洞措施
通过上述分析可知,影响二衬空洞的因素涉及施工的各个环节,需从开挖、初支、防水板铺设、砼浇筑、砼振捣、养护等环节加以控制。
工艺控制要点如下:
1.加强开挖控制,从源头上控制混凝土超耗量,提高工效,杜绝人为原因造成空洞。
黄土隧道采用机械人工相结合开挖方式,尽量减少对围岩扰动,开挖后及时封闭,防止围岩失稳掉块;石质隧道采用聚能水压爆破、光面爆破,减少对围岩扰动,减少超挖量。
2.岩面有渗水时,在喷射混凝土前预埋排水盲管,做好集中引排措施,避免围岩面水散流,造成喷射混凝土与围岩粘连不牢,后期流水渗蚀、冲刷混凝土形成空洞。
3.加强钢架周边喷射混凝土施工工艺控制,分片喷射自下而上进行,先喷钢架与壁面间混凝土,再喷射两榀钢架之间混凝土,保证钢架周边喷射混凝土无盲区。
4.喷射混凝土施工时设置厚度控制标识,对施工人员做好技能培训和交底,严格控制喷射混凝土表面平整度,保证防水板铺设平顺。
5.防水板铺设松紧适度。
固定点间距拱部按照50cm要求布置,拱腰按照80cm要求布置。
防水板搭接长度、焊缝及固定点焊接,严格按防水板施工作业要求施工到位。
6.二衬混凝土浇筑严格落实逐窗分层浇筑工艺要求,振捣到位。
每层窗口间安装一台附着式振动器,并安设一个对应专用电表,入模窗口、附着式振动器和集中控制柜开关统一编号管理,集中操作控制。
混凝土边入模边振捣,每次入模时,混凝土振实振平。
四层及四层以
下窗口采用“插入式振捣棒与附着式振动器”相结合方式振捣,五层窗口采用带压入模。
各预留孔洞封堵到位,拱部浇筑预留通气孔,防止下坡施工时,浇注段与上循环之间会形成空气囊(拱部)而造成衬砌背后空洞。
冲顶补方时,保证混凝土及时供应、和易性良好,冲顶孔使用顺序按照坡度方向,由下及上,充分利用附着式振动器辅助振捣密实,同时利用拱顶密贴度监控仪,实时监控二衬冲顶情况。
现场填写二衬施工可溯源管理信息表,为分析二衬混凝土施工情况提供基础数据,以便总结分析采取相应有效措施,指导后续二衬施工,提高二衬浇筑质量。
7.严格执行带模注浆工艺要求。
二衬浇筑完成4-6个小时后开始带模注浆。
拱顶带模注浆施工工序:安装RPC注浆管并固定—衬砌混凝土浇筑—安装注浆组合件——浆液拌制—注浆—拆卸注浆组件、衬砌脱模—衬砌混凝土表面清理—养护;现场主要有四个注浆孔,原则上除4#孔外每一个注浆孔均需注浆,但在注浆过程中进行其他孔注浆时未注浆的孔流出达到相同密度的浆体时,该孔也可封闭,不进行注浆。
注浆过程中主要以台车上部压力表和端模出浆情况来作为注浆双控标准。
如果端头模板圆弧最高点漏浆,先停止注浆,及时对浆漏处进行封堵,然后继续注浆,直至浆体与制浆机中一致,然后更换下一个注浆孔。
注浆时如果台车处压力表超过1.0Mpa,直接转至下一注浆孔。
及时跟进带模注浆情况,注浆异常时,一次一分析,不断总结提高注浆质量。
8.改善作业环境。
隧道衬砌台车作业平台二端增设鼓风机,降低
工作面温度,改善操作人员工作环境。
9.“两带”(环向背贴式止水带、中埋式止水带)均采取加固措施。
背贴式止水带利用衬砌端头环向内层主筋顶撑牢固,使之与防水板密贴,并用胶水与防水板粘接,再利用纵向衬砌Φ14构造筋水平支撑,环向间距按照40cm控制;中埋式止水带采用ψ8“U”筋进行固定,环向间距按照拱部40cm,拱腰以下60cm控制;每板二衬拆模后检查端头情况,及时清理堵缝土工布。
10.利用好自创轨行式自动控湿标养台车,做好二衬混凝土养生工作,减少因养护不到位引起的混凝土自身收缩、徐变而引起的砼与防水板间空洞。
11.对每板二衬做好敲击自检,一板不落,在衬砌施工150m后即安排雷达检测,以便能够及早发现问题,制定解决方案。
通过不断总结分析,改进工装和调整施工工艺,减少后续施工衬砌空洞现象的发生,促进衬砌混凝土施工质量的总体提高。