阵列涡流标准
核电厂反应堆水池覆面焊缝的阵列涡流检测
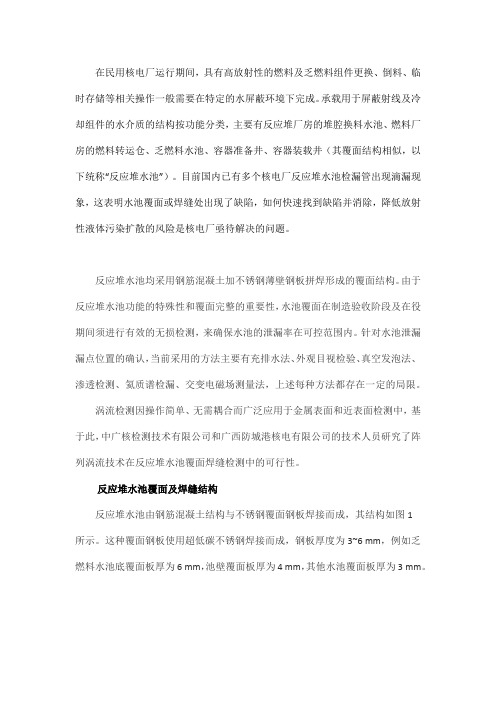
在民用核电厂运行期间,具有高放射性的燃料及乏燃料组件更换、倒料、临时存储等相关操作一般需要在特定的水屏蔽环境下完成。
承载用于屏蔽射线及冷却组件的水介质的结构按功能分类,主要有反应堆厂房的堆腔换料水池、燃料厂房的燃料转运仓、乏燃料水池、容器准备井、容器装载井(其覆面结构相似,以下统称“反应堆水池”)。
目前国内已有多个核电厂反应堆水池检漏管出现滴漏现象,这表明水池覆面或焊缝处出现了缺陷,如何快速找到缺陷并消除,降低放射性液体污染扩散的风险是核电厂亟待解决的问题。
反应堆水池均采用钢筋混凝土加不锈钢薄壁钢板拼焊形成的覆面结构。
由于反应堆水池功能的特殊性和覆面完整的重要性,水池覆面在制造验收阶段及在役期间须进行有效的无损检测,来确保水池的泄漏率在可控范围内。
针对水池泄漏漏点位置的确认,当前采用的方法主要有充排水法、外观目视检验、真空发泡法、渗透检测、氦质谱检漏、交变电磁场测量法,上述每种方法都存在一定的局限。
涡流检测因操作简单、无需耦合而广泛应用于金属表面和近表面检测中,基于此,中广核检测技术有限公司和广西防城港核电有限公司的技术人员研究了阵列涡流技术在反应堆水池覆面焊缝检测中的可行性。
反应堆水池覆面及焊缝结构反应堆水池由钢筋混凝土结构与不锈钢覆面钢板焊接而成,其结构如图1所示。
这种覆面钢板使用超低碳不锈钢焊接而成,钢板厚度为3~6 mm,例如乏燃料水池底覆面板厚为6 mm,池壁覆面板厚为4 mm,其他水池覆面板厚为3 mm。
图1反应堆水池不锈钢覆面安装结构示意水池覆面的焊缝以对接焊缝为主,角焊缝及搭接焊缝为辅,焊接方式主要有平焊和立焊,焊缝形态各异,有横焊缝、竖焊缝、圆形焊缝、矩形焊缝等,长度短至几十毫米,长则数米不等。
水池泄漏的位置主要为焊缝及热影响区域,也会出现在覆面本体及支撑预埋件区域。
反应堆存水的泄漏对核燃料的冷却效果造成一定影响。
针对容易产生缺陷的焊缝及热影响区,笔者在现场开展了阵列涡流试验。
非铁磁性传热管阵列涡流检测研究

科学技术创新2021.07非铁磁性传热管阵列涡流检测研究谷昊(辽宁红沿河核电有限公司,辽宁大连116300)1概述对于非铁磁性传热管,一般采用常规涡流检测方法(Bobbin )对其运行状况进行检查。
Bobbin 目前已经是一种比较成熟的无损检测方法,检测效率高、信号可记录、重复性好,尤其适合传热管的在役检测。
但是Bobbin 检测方法同时也存在不足之处,检测信号比较抽象、图像显示不够直观、不能区分开同一个圆周截面的多个缺陷、对于纵向的缓慢变形的长缺陷不够敏感、对信号显示的判伤较依赖分析人员的经验。
因此,采取合适的检测方法对Bobbin 进行补充很有必要。
旋转探头虽然检测效果良好,但检测速度慢、检验装置复杂且造价高、探头损耗严重、经济效益低[1]。
寻找一种既经济方便,又对非铁磁性传热管具有良好检测效果的涡流探伤新方法就成为当前的研究重点,本文介绍了非铁磁性传热管阵列涡流检测的试验过程与试验结果。
2传热管阵列涡流检测原理阵列涡流探头的常见激发方式主要分为绝对式及激励-接收式两种。
绝对式是指阵列涡流线圈中每个线圈既用于激发涡流,又用来接收感应的涡流信号。
当阵列涡流探头处于此种激发模式时,检测效果即可等同于若干个点式探头同时扫查,提高了检测效率。
然而,因为此种激发方式使检测探头的提离信号影响较大,不利于检测的实施,所以,阵列涡流更多采用激励-接受式的激发方式。
激励-接受式激发方式基本原理为:一个线圈针对工件激发感应涡流,另外一个或若干的线圈接收感应涡流产生的信号。
当被检工件存在电磁特性的不连续时,激励的涡流会被这种不连续干扰,进而被接收线圈接收到。
一对激励-接受组合的线圈会因缺陷方向的不同而产生不同的检测灵敏度。
当缺陷方向与涡流流动方向垂直时,缺陷干扰涡流的流动检出效果好;当缺陷方向与涡流方向相同时,缺陷对涡流的干扰较小,检测效果较差。
密布的线圈按照预先设计的激发顺序依次交替运行,在电磁场和涡流场发生高速旋转的同时,检测的焦点也发生高速旋转,以此达到对传热管内表面旋转扫查的目的,其效果近似于旋转探头的机械旋转。
涡流检测标准概述 ETIII

浙江省特种设备检验研究院 钟丰平 E-mail:zjupec@
提
纲
一、标准基础知识 二、国外电磁涡流检测相关标准 三、国内电磁涡流检测标准 四、验收标准
一、标准基础知识 “标准”定义:为了在一定的范围内获得 最佳秩序,协商一致制定并由有关机构批 准,共同使用和重复使用的一种规范性文 件。 标准的性质: (1)目的性 (2)层次性 (3)权威性 (4)时效性 (5)强制性与推荐性
二、国外电磁涡流检测相关标准
美国材料试验学会( ASTM ),编制的电
磁涡流检测方面的标准近20份,涉及电磁 分选、漏磁检测、涡流探伤、电导率测试 和覆盖层厚度测量、涡流仪器与检测线圈 性能评价等方面技术的实施方法,内容最 为广泛和系统。
ASTM 标准用标准代号 + 字母分类代码 + 标
(5)强制性与推荐性 强制性标准具有法律属性, ①全国必须统一的基础标准;②对国计民生重 大影响的产品标准;③通用的试验方法和检测 方法标准,计量检定;④有关人身健康和生命 安全方面的标准;⑤环境保护方面的标准。
推荐性标准又称自愿性标准,或非强制标准。 是指生产、交换、使用等方面,通过经济手段 或市场调节而自愿采用的标准。 从鼓励科技进步与技术发展出发,实行“严格 控制强制标准,积极采用推荐性标准”的政策。 国家标准 行业标准都可以分为强制性和推荐性
准序号+制定年份+标准英文名称来表示。
二、国外电磁涡流检测相关标准
ASTM Technical Committees E07.07
ASTM E215 - 11 Standard Practice for Standardizing Equipment for Electromagnetic Testing of Seamless Alumi国内标准代号 国家标准 序号 代号 含义
无损检测----涡流阵列检测技术典型应用
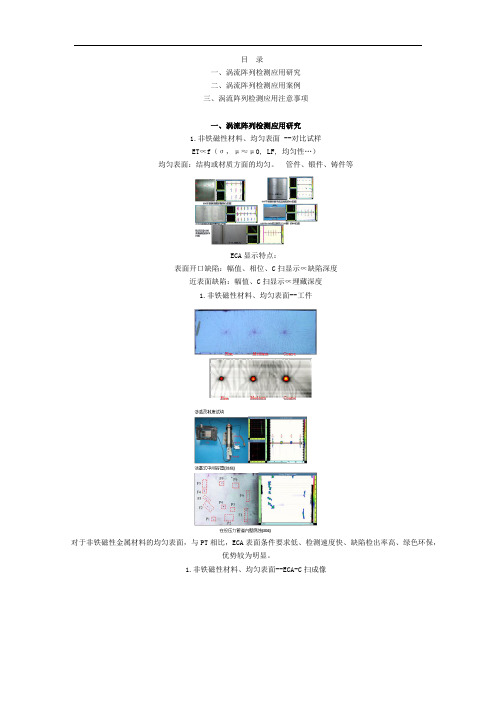
目录一、涡流阵列检测应用研究二、涡流阵列检测应用案例三、涡流阵列检测应用注意事项一、涡流阵列检测应用研究1.非铁磁性材料、均匀表面 --对比试样ET∝f(σ,μ≈μ0, LF, 均匀性…)均匀表面:结构或材质方面的均匀。
管件、锻件、铸件等ECA显示特点:表面开口缺陷:幅值、相位、C扫显示∝缺陷深度近表面缺陷:幅值、C扫显示∝埋藏深度1.非铁磁性材料、均匀表面--工件对于非铁磁性金属材料的均匀表面,与PT相比,ECA表面条件要求低、检测速度快、缺陷检出率高、绿色环保,优势较为明显。
1.非铁磁性材料、均匀表面--ECA-C扫成像绝对桥式阵列、小的线圈尺寸、多的阵列排数更有利于涡流阵列C扫成像。
均匀表面表面开口缺陷ECA-C扫成像可在一定程度上定性2.非铁磁性材料、非均匀表面--对比试块ET∝f(σ, LF, μ≈μ0, 均匀性…)对接接头:局部表面出现结构或材质不均匀。
2.非铁磁性材料、非均匀表面--模拟试块表面的不均匀性,在一定程度上影响ECA-C成像效果,直观性受到影响。
焊纹也会降低检测灵敏度。
2.非铁磁性材料、非均匀平面--工件3.铁磁性材料、均匀表面--对比试样ET∝f(σ, LF, μ, 均匀性…)管件、锻件、铸件等4.铁磁性材料、非均匀表面--动态提离补偿技术ECA C-scan Image对接接头:局部表面出现结构或材质不均匀。
4.铁磁性材料、非均匀表面--对比试样5.高温奥氏体不锈钢刻槽试板高温检测实验(300℃)6.低温低温情况下,PT无法实施,可考虑ECA。
二、涡流阵列检测典型案例——奥氏体不锈钢对接接头1.表面开口缺陷ECA可以比PT更容易发现缺陷。
2.近表面缺陷ECA可以在一定程度上检出近表面缺陷。
在线不打磨检测--动态提离补偿动态提离补偿技术,实现了碳钢对接接头的在线不打磨表面缺陷检测。
三、涡流阵列检测注意事项a)了解检测对象b)选探头c)选对比试样d)确定灵敏度e)扫查f)数据判读g)验证。
涡流检测标准

涡流检测标准
涡流检测是一种常用的无损检测方法,主要适用于金属和合金材料表面缺陷检测。
下面是一些涡流检测常用标准:
1.GB/T 7735-2004 金属材料表面缺陷检验压电式涡流探头及
其使用方法
2.GB/T 16826-1997 金属材料表面缺陷检验涡流探头及其使用方法
3.GB/T 17877.1-1999 非破坏性检测使用涡流检测通用原理
4.GB/T 19514-2004 铸铁件中有害夹杂物检验方法磁粉、涡流和超声波检验
5.GB/T 3098.11-2000 机械工程涂层专用术语第11部分:非破坏性检测
6.GB/T 13544-2013 焊缝非破坏检测涡流检测方法
以上标准主要包括了涡流检测的原理、设备、探头、检测方法、数据处理等方面的内容。
在进行涡流检测时需要根据实际情况选择相应的标准,并按照标准规范进行操作,以确保检测结果的准确性和可靠性。
阵列涡流检测

电涡流阵列的测试方法
• 电涡流传感器阵列测试的关键还在于线圈阵列的引线设计, 图3是几种常用的基于单线圈检测原理的引线设计模式。 图3(a)是敏感线圈两端分别引线的设计模式,图3(b)是行 列垂直扫描式的引线设计。采用行列垂直结构形式的目的 是为了减少传感器阵列的外接引线数目,这对于传感器的 实际应用具有重要意义,但同时又不可避免地带来了各阵 列单元间的串扰,降低了测量精度。解决串扰的问题,最 简单的方法就是每个阵列单元单独引线(图3(a)),另外也 可以将预处理电路与敏感单元集成,做成一体化的集成传 感器单元,而其代价将是高昂的制作成本。有时为了提高 扫描采样的速度,还会采用一种行扫描采样的方法,即每 次扫描一行,从而大大提高传感器阵列的测试速度,但需 要增加预处理电路的数量。
电涡流检测的基本原理
• 电涡流检测的工作原理是检测激励线圈磁 场和感应涡流磁场之间的交互作用。当敏 感线圈通入交流电流时,线圈周围就会产 生交变磁场,如图1(a),如果此时将金属 导体工件移入此交变磁场中,工件表面就 会感应出电涡流,而此电涡流又会产生一 个磁场,该磁场的方向与原线圈磁场的方 向正好相反,从而减弱了原磁场。
电涡流阵列的设计和制作
电涡流阵列的设计和制作
• 传感器的探头采用柔性印刷电路板(FPCB)E艺在聚酰亚胺薄膜上制作,探头敏感线圈 阵列的整体尺寸很大,能达到200 mm ×200 mm。,而厚度却很薄,不超过 0.15 mm,且具有良好的柔韧性,几乎能 够应用于各种几何形状形面的测量。
传感器系统原理
电涡流阵列的形式
• 与其它一些传感器相比,电涡流传感器具有一个 比较突出的优点——探头的结构非常简单。从电 涡流检测的基本原理可以看出,电涡流传感器探 头的关键部件是敏感线圈,因此电涡流阵列测试 一般都是采用线圈阵列的方法,而不是将多个独 立的传感器探头布置成阵列形式来使用。针对不 同的测试条件和技术指标要求,线圈阵列可以设 计成不同的结构和形式,以实现复杂形面部件的 检测,但线圈阵列及其匹配电路的针对性设计也 带来了相对昂贵的成本。
涡流检测标准

涡流检测标准涡流检测是一种非接触式的检测方法,它利用涡流感应原理来检测材料表面的缺陷和异物。
涡流检测广泛应用于航空航天、汽车制造、铁路运输等领域,是一种高效、精准的无损检测技术。
为了保证涡流检测的准确性和可靠性,制定了一系列的涡流检测标准,以规范和指导涡流检测工作的开展。
首先,涡流检测标准对设备和仪器的要求进行了详细规定。
涡流检测设备应具有良好的稳定性和重复性,能够满足不同工况下的检测需求。
同时,仪器的精度和灵敏度也是标准所关注的重点之一。
只有确保设备和仪器的性能达到标准要求,才能保证涡流检测的准确性和可靠性。
其次,涡流检测标准对操作人员的素质和技术能力提出了明确要求。
操作人员应经过专业培训,熟悉涡流检测的原理和方法,具备一定的工作经验和技能。
标准还规定了操作人员应具备的基本素质和行为规范,以确保他们能够独立、准确地完成涡流检测工作。
此外,涡流检测标准还对检测工艺和操作流程进行了规范。
标准要求制定详细的检测方案和操作规程,包括检测参数的选择、仪器的校准、样品的准备等内容。
在实际操作中,严格按照标准要求进行检测,可以最大程度地保证检测结果的准确性和可靠性。
涡流检测标准的制定和执行,对于提高涡流检测的质量和效率具有重要意义。
只有严格遵守标准要求,才能保证涡流检测工作的科学性和规范性。
同时,标准化的涡流检测工作也为相关行业的发展和进步提供了有力保障。
总的来说,涡流检测标准的制定是对涡流检测工作的规范和指导,是保证涡流检测准确性和可靠性的重要手段。
只有严格依照标准要求进行操作,才能保证涡流检测工作的科学性和规范性。
相信随着标准的不断完善和执行,涡流检测技术将在更多领域得到广泛应用,为相关行业的发展和进步做出更大的贡献。
无损检测---涡流阵列检测技术基本原理

目录一、什么是涡流阵列检测技术?二、涡流检测基础知识三、涡流阵列检测技术工作原理四、涡流阵列检测技术特点五、涡流阵列检测技术的国内外现状一、什么是涡流阵列检测技术?“涡流阵列”,又叫”阵列涡流”,英文名称“Eddy Current Array(简称ECA)”。
JB/T 11780-2014 无损检测仪器涡流阵列检测仪性能和检验阵列涡流检测具有按一定方式排布、且独立工作的多个检测线圈,能够一次性完成大面积扫查及成像的涡流检测技术。
C扫相关显示与缺陷形状像不像?并能形成直观性C扫图二、涡流检测基础知识1. ET工作原理—电磁感应①激励,悬空(电0→磁0 )空载阻抗 Z=Z0M—互感系数~提离R2—电涡流短路环负载~路径几何尺寸,σ2L2—电涡流短路环自感系数~路径几何尺寸,μ22.影响放置式线圈阻抗的因素a)提离b)边缘效应c)电导率d)磁导率e)工件几何尺寸f)缺陷g)表面状况h)检测频率影响阻抗变化的因素太多,限制了涡流探伤的应用!3.放置式涡流探头的分类4. 绝对式探头和差分式探头的对比绝对式信号来自1个感应线圈;每个缺陷产生1个闭路(半8字);对于小缺陷、长缺陷和渐变缺陷敏感;可用于测量材料性能差异.可能需要参考线圈执行系统平衡;对提离非常敏感。
差分式信号来自2个感应线圈的减法。
.每个缺陷产生2个闭路(8字)对小缺陷特别敏感,但渐变缺陷不敏感;对于小缺陷具有更好的信噪比;对于提离不太敏感。
检测前,应该根据用途、被检工件状况等确定探头的工作模式和信号响应模式!5. 常规涡流检测技术的特点优点■适用于各种导电材质的试件探伤;■可以检出表面和近表面缺陷;■检测结果以电信号输出,容易实现自动化;■由于采用非接触式检测,所以检测速度快;■无需耦合剂,环保。
缺点■不能检测非导电材料;■形状复杂的工件很难检测;■各种干扰检测的因素较多,容易引起杂乱信号;■无法检出埋藏较深的缺陷;■一次覆盖范围小,检测效率低;■检测结果不直观,不能显示缺陷图形,无法缺陷定性。
- 1、下载文档前请自行甄别文档内容的完整性,平台不提供额外的编辑、内容补充、找答案等附加服务。
- 2、"仅部分预览"的文档,不可在线预览部分如存在完整性等问题,可反馈申请退款(可完整预览的文档不适用该条件!)。
- 3、如文档侵犯您的权益,请联系客服反馈,我们会尽快为您处理(人工客服工作时间:9:00-18:30)。
阵列涡流标准
阵列涡流检测是一种无损检测技术,可用于检测金属和非金属材料表面和近表面的裂纹、夹杂物、孔洞等缺陷。
本文将介绍阵列涡流检测的标准,包括设备准备、检测流程、数据分析、质量评估、预防维护、安全规范、场地管理及应用领域等方面。
1. 设备准备
在进行阵列涡流检测前,需要准备好相应的设备和器材,包括:涡流检测仪、阵列涡流探头、电源、信号线、校准试块、数据处理计算机及相关软件等。
在设备准备过程中,需要注意以下几点:
* 涡流检测仪应选择具有高灵敏度、高稳定性的仪器,同时应具备自动化检测和数据处理功能;
* 阵列涡流探头应选择与被检材料和尺寸相匹配的探头,同时应注意探头的清洁和维护;
* 校准试块应选择与被检材料和尺寸相近的试块,用于校准探头和仪器,保证检测结果的准确性。
2. 检测流程
阵列涡流检测的检测流程一般包括以下几个步骤:
* 试块准备:选择合适的校准试块,将其放置在检测位置,用于校准探头和仪器;
* 探头安装:将阵列涡流探头安装在涡流检测仪上,连接信号线;* 仪器校准:使用校准试块对仪器进行校准,调整仪器参数,保证检测结果的准确性;
* 检测操作:将探头放置在待检测工件表面上,启动检测程序,进行检测;
* 数据采集:记录检测过程中的数据,包括缺陷的位置、大小、形状等;
* 数据处理:使用数据处理软件对采集的数据进行处理,生成检测报告。
3. 数据分析
数据分析是阵列涡流检测的重要环节之一,通过对采集的数据进行分析和处理,可以提取出缺陷的位置、大小、形状等信息,并生成相应的检测报告。
数据分析一般包括以下几个步骤:
* 数据预处理:对采集的数据进行预处理,包括去噪、滤波等操作,以提高数据的准确性和可靠性;
* 缺陷提取:通过图像处理和模式识别等技术,从预处理后的数据中提取出缺陷的位置、大小、形状等信息;
* 数据分析:对提取出的缺陷信息进行分析,包括缺陷的类型、分布规律等,以评估被检材料的质量和安全性。
4. 质量评估
质量评估是阵列涡流检测的重要环节之一,通过对检测结果进行评估和分析,可以判断出被检材料的质量和安全性。
质量评估一般包括以下几个步骤:
* 缺陷分类:根据缺陷的类型和严重程度,将缺陷分为不同的类别;* 统计评估:对每个类别的缺陷进行统计和分析,包括缺陷的数量、分布规律等,以评估被检材料的质量和安全性;
* 结果输出:将评估结果以报告的形式输出,包括缺陷的类型、数量、分布规律等信息,以及相应的建议和措施。
5. 预防维护
为了保障阵列涡流检测设备的正常运行和延长设备的使用寿命,需要进行预防维护。
预防维护一般包括以下几个环节:
* 日常检查:每天检查设备的运行状态和各项参数是否正常,如有问题及时处理;
* 定期维护:定期对设备进行全面检查和维护,包括清洁、润滑、紧固等操作;
* 更换易损件:定期更换设备的易损件,如探头、信号线等;
* 软件更新:定期更新设备的软件系统,以提高设备的性能和稳定性。
6. 安全规范
在进行阵列涡流检测时,需要遵守相应的安全规范,以保证设备和人员的安全。
安全规范一般包括以下几个方面:
* 操作人员需要经过专业培训合格后才能进行操作;
* 在检测过程中,操作人员需要佩戴相应的防护用具;
* 在检测过程中,操作人员需要随时观察设备的运行状态和各项参数是否正常;
* 在检测过程中,需要注意防止设备意外损伤人员或物品;
* 在检测过程中,需要注意防止设备发生电气故障或火灾等事故。
7. 场地管理为了保障阵列涡流检测的正常进行和安全可靠,需要进行场地管理。
场地管理一般包括以下几个方面:
* 选择合适的检测场地:选择平坦、开阔、无遮挡的场地作为检测区域;
* 检查场地设施:检查场地的基础设施是否完善、安全可靠;
* 安排专业人员管理:安排专业人员对场地进行管理维护。
8. 应用领域阵列涡流检测技术在许多领域都有广泛的应用。
以下是其中一些
主要的应用领域:汽车制造领域可用于检测汽车关键零部件的表面和近表面缺陷;航空航天领域可用于检测飞机零部件的表面和近表面缺陷;石油化工领域可用于检测管道、容器的表面。