阵列涡流检测
无损检测----涡流阵列检测技术典型应用
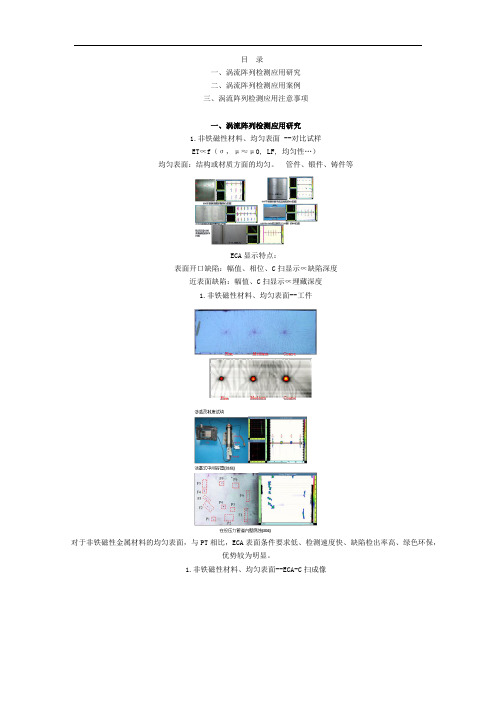
目录一、涡流阵列检测应用研究二、涡流阵列检测应用案例三、涡流阵列检测应用注意事项一、涡流阵列检测应用研究1.非铁磁性材料、均匀表面 --对比试样ET∝f(σ,μ≈μ0, LF, 均匀性…)均匀表面:结构或材质方面的均匀。
管件、锻件、铸件等ECA显示特点:表面开口缺陷:幅值、相位、C扫显示∝缺陷深度近表面缺陷:幅值、C扫显示∝埋藏深度1.非铁磁性材料、均匀表面--工件对于非铁磁性金属材料的均匀表面,与PT相比,ECA表面条件要求低、检测速度快、缺陷检出率高、绿色环保,优势较为明显。
1.非铁磁性材料、均匀表面--ECA-C扫成像绝对桥式阵列、小的线圈尺寸、多的阵列排数更有利于涡流阵列C扫成像。
均匀表面表面开口缺陷ECA-C扫成像可在一定程度上定性2.非铁磁性材料、非均匀表面--对比试块ET∝f(σ, LF, μ≈μ0, 均匀性…)对接接头:局部表面出现结构或材质不均匀。
2.非铁磁性材料、非均匀表面--模拟试块表面的不均匀性,在一定程度上影响ECA-C成像效果,直观性受到影响。
焊纹也会降低检测灵敏度。
2.非铁磁性材料、非均匀平面--工件3.铁磁性材料、均匀表面--对比试样ET∝f(σ, LF, μ, 均匀性…)管件、锻件、铸件等4.铁磁性材料、非均匀表面--动态提离补偿技术ECA C-scan Image对接接头:局部表面出现结构或材质不均匀。
4.铁磁性材料、非均匀表面--对比试样5.高温奥氏体不锈钢刻槽试板高温检测实验(300℃)6.低温低温情况下,PT无法实施,可考虑ECA。
二、涡流阵列检测典型案例——奥氏体不锈钢对接接头1.表面开口缺陷ECA可以比PT更容易发现缺陷。
2.近表面缺陷ECA可以在一定程度上检出近表面缺陷。
在线不打磨检测--动态提离补偿动态提离补偿技术,实现了碳钢对接接头的在线不打磨表面缺陷检测。
三、涡流阵列检测注意事项a)了解检测对象b)选探头c)选对比试样d)确定灵敏度e)扫查f)数据判读g)验证。
涡流阵列检测技术的研究进展现状分析

涡流阵列检测技术的研究进展现状分析张卫民;岳明明;庞炜涵;徐民东;陈国龙【摘要】简要介绍了阵列涡流检测技术研究进展和应用情况,指出阵列涡流传感器是涡流检测技术的一个新的发展方向,在重要机械零部件和关键结构监测中具有广泛应用前景.提出了一种检测小曲率曲面零件的新型阵列式检测技术方案和结构设计方案.%This paper briefly introduces the research progress and application of the eddy current array testing technology,and points out a new development direction that the eddy current array sensor is applied to its testing technology.It has a wide application pros-pect in monitoring the important mechanical parts. A new array testing technology and the system design scheme are proposed to test the small curved surface parts.【期刊名称】《机械制造与自动化》【年(卷),期】2018(000)001【总页数】3页(P181-183)【关键词】检测;涡流传感器;阵列式检测结构;研究现状【作者】张卫民;岳明明;庞炜涵;徐民东;陈国龙【作者单位】北京理工大学机械与车辆学院北京100081;北京理工大学机械与车辆学院北京100081;北京理工大学机械与车辆学院北京100081;北京理工大学机械与车辆学院北京100081;北京理工大学机械与车辆学院北京100081【正文语种】中文【中图分类】TP274+.50 引言涡流阵列传感器检测技术,亦属于涡流传感器技术新兴发展方向之一。
涡流无损检测

1无损检测(Nondestructive Testing, NDT)是一门涉及多学科的综合性应用技术,它以不损害被检对象的内部结构和使用性能为前提,应用多种物理原理和化学现象,对各种工程材料、零部件、结构件进行有效地检验和测试,检测被检对象中是否存在缺陷或不均匀性,进而评价它们的连续性、完整性、安全可靠性及某些物理性能【1-6]。
无损检测技术是现代工业发展必不可少的有效工具,在一定程度上反应了一个国家的工业发展水平,其重要性己得到世界范围内广泛公认。
无损检测技术的应用范围十分广泛,遍布工业发展的各个领域,在机械、建筑、冶金、电力、石油、造船、汽车、宇航、核能、铁路等行业中被普遍采用,成为不可或缺的质量保证手段,其在产品设计、生产和使用的各个环节中己被卓有成效的运用[4,7-16]。
2以德国科学家伦琴1895年发现X射线为标志,无损检测作为应用型技术学科己有一百多年的历史[l7]0 1900年,法国海关开始应用X射线检验物品;1922年,美国建立了世界第一个工业射线实验室,用X射线检查铸件质量,以后在军事工业和机械制造业等领域得到了广泛应用,射线检测技术至今仍然是许多工业产品质量控制的重要手段。
1912年,超声波检测技术最早在航海中用于探查海面上的冰山;1929年,将其应用于产品缺陷的检测,目前仍是锅炉压力容器、铁轨等重要机械产品的主要检测手段。
1930年后,开始采用磁粉检测方法来检测车辆的曲柄等关键部件,以后在钢结构上广泛应用磁粉探伤方法,使磁粉检测得以普及到各种铁磁性材料的表面检测。
毛细管现象是土壤水分蒸发的一种常见现象,随着工业化大生产的出现,将“毛细管现象”成功地应用于金属和非金属材料开口缺陷的检测,其灵敏度与磁粉检测相当,它的最大好处是可以检测非铁磁性物质。
经典的电磁感应定律和涡流趋肤效应的发现,促进了现代导电材料涡流检测方法的产生。
1935年,第一台涡流探测仪器研究成功。
到了二十世纪中期,建立了以射线检测(Radiographic Testing, RT、超声检测(Ultrasonic Testing, UT、磁粉检测(Magnetic Testing, MT、渗透检测(Penetrant Testing, PT)和涡流检测(Eddy Current Test, ECT五大常规检测技术为代表的无损检测体系【‘“]。
无损检测技术中的涡流检测方法详解

无损检测技术中的涡流检测方法详解无损检测技术是一种用于检测材料或构件内部缺陷或性能状态的技术方法,它可以在不破坏被检测材料的情况下对其进行评估和监测。
涡流检测作为无损检测技术的一种方法,被广泛应用于工业生产、航空、航天、汽车、电力等领域。
本文将对涡流检测方法进行详细解释和阐述。
涡流检测是一种基于电磁感应原理的无损检测技术。
其原理是利用交流电源产生的交变电磁场在被测材料中产生涡流,通过对涡流的测量,来判断被测材料的缺陷或性能状态。
涡流检测方法可以检测到多种类型的缺陷,如裂纹、腐蚀、疏松等。
涡流检测方法主要包括以下几个方面:1. 电磁感应原理:涡流检测是基于电磁感应原理的,通过交流电源产生的交变电磁场在被测材料中产生涡流。
当被测材料中存在缺陷时,涡流的路径和强度会发生变化,从而可以判断缺陷的位置和性质。
2. 探头设计:涡流检测中使用的探头通常由线圈和磁芯组成。
线圈通过交流电源激励产生交变磁场,磁芯则用于集中和引导磁场。
探头的设计对于检测效果起着重要的作用,不同类型的缺陷需要不同设计的探头。
3. 缺陷识别:通过分析涡流的强度、相位、频率等参数,可以判断被测材料中的缺陷类型和尺寸。
例如,对于裂纹缺陷,涡流的强度和相位会出现明显的变化。
通过对涡流信号进行数学处理和分析,可以得到准确的缺陷识别结果。
4. 检测技术:涡流检测技术可以分为静态检测和动态检测两种。
静态检测是指将被测材料放置在固定位置,通过探头对其进行检测。
动态检测则是指将探头和被测材料相对运动,通过对运动产生的涡流信号进行检测。
动态检测常用于对大型或复杂构件的检测。
涡流检测方法具有以下优点:1. 非接触性:涡流检测不需要直接接触被测物体,因此不会对被测材料造成损伤或影响其性能。
2. 高灵敏度:涡流检测可以检测到微小尺寸的缺陷,对于裂纹等细小缺陷具有很高的灵敏度。
3. 适用范围广:涡流检测方法适用于多种材料,如金属、合金、陶瓷等。
同时,它可以应用于不同形状和尺寸的材料和构件。
阵列涡流标准
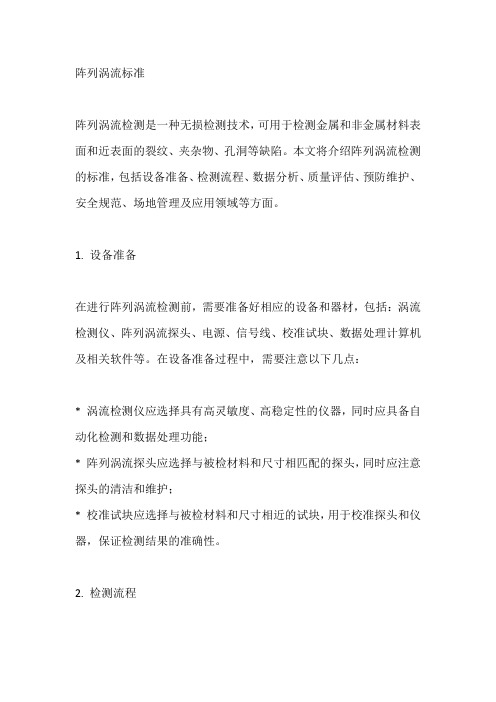
阵列涡流标准阵列涡流检测是一种无损检测技术,可用于检测金属和非金属材料表面和近表面的裂纹、夹杂物、孔洞等缺陷。
本文将介绍阵列涡流检测的标准,包括设备准备、检测流程、数据分析、质量评估、预防维护、安全规范、场地管理及应用领域等方面。
1. 设备准备在进行阵列涡流检测前,需要准备好相应的设备和器材,包括:涡流检测仪、阵列涡流探头、电源、信号线、校准试块、数据处理计算机及相关软件等。
在设备准备过程中,需要注意以下几点:* 涡流检测仪应选择具有高灵敏度、高稳定性的仪器,同时应具备自动化检测和数据处理功能;* 阵列涡流探头应选择与被检材料和尺寸相匹配的探头,同时应注意探头的清洁和维护;* 校准试块应选择与被检材料和尺寸相近的试块,用于校准探头和仪器,保证检测结果的准确性。
2. 检测流程阵列涡流检测的检测流程一般包括以下几个步骤:* 试块准备:选择合适的校准试块,将其放置在检测位置,用于校准探头和仪器;* 探头安装:将阵列涡流探头安装在涡流检测仪上,连接信号线;* 仪器校准:使用校准试块对仪器进行校准,调整仪器参数,保证检测结果的准确性;* 检测操作:将探头放置在待检测工件表面上,启动检测程序,进行检测;* 数据采集:记录检测过程中的数据,包括缺陷的位置、大小、形状等;* 数据处理:使用数据处理软件对采集的数据进行处理,生成检测报告。
3. 数据分析数据分析是阵列涡流检测的重要环节之一,通过对采集的数据进行分析和处理,可以提取出缺陷的位置、大小、形状等信息,并生成相应的检测报告。
数据分析一般包括以下几个步骤:* 数据预处理:对采集的数据进行预处理,包括去噪、滤波等操作,以提高数据的准确性和可靠性;* 缺陷提取:通过图像处理和模式识别等技术,从预处理后的数据中提取出缺陷的位置、大小、形状等信息;* 数据分析:对提取出的缺陷信息进行分析,包括缺陷的类型、分布规律等,以评估被检材料的质量和安全性。
4. 质量评估质量评估是阵列涡流检测的重要环节之一,通过对检测结果进行评估和分析,可以判断出被检材料的质量和安全性。
涡流检测ect检测技术标准
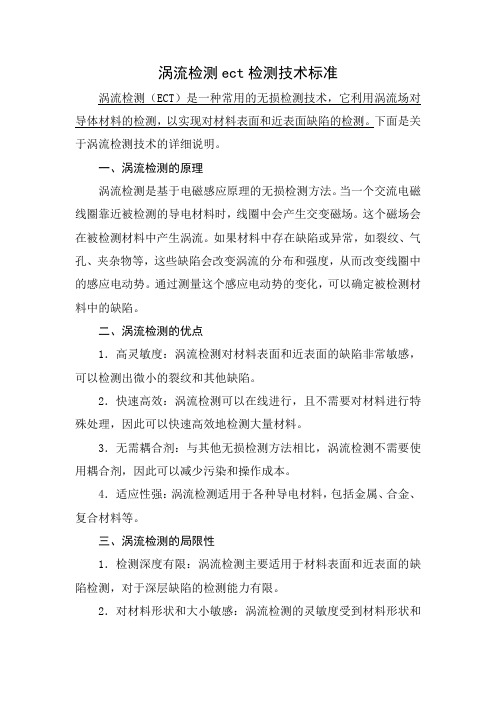
涡流检测ect检测技术标准涡流检测(ECT)是一种常用的无损检测技术,它利用涡流场对导体材料的检测,以实现对材料表面和近表面缺陷的检测。
下面是关于涡流检测技术的详细说明。
一、涡流检测的原理涡流检测是基于电磁感应原理的无损检测方法。
当一个交流电磁线圈靠近被检测的导电材料时,线圈中会产生交变磁场。
这个磁场会在被检测材料中产生涡流。
如果材料中存在缺陷或异常,如裂纹、气孔、夹杂物等,这些缺陷会改变涡流的分布和强度,从而改变线圈中的感应电动势。
通过测量这个感应电动势的变化,可以确定被检测材料中的缺陷。
二、涡流检测的优点1.高灵敏度:涡流检测对材料表面和近表面的缺陷非常敏感,可以检测出微小的裂纹和其他缺陷。
2.快速高效:涡流检测可以在线进行,且不需要对材料进行特殊处理,因此可以快速高效地检测大量材料。
3.无需耦合剂:与其他无损检测方法相比,涡流检测不需要使用耦合剂,因此可以减少污染和操作成本。
4.适应性强:涡流检测适用于各种导电材料,包括金属、合金、复合材料等。
三、涡流检测的局限性1.检测深度有限:涡流检测主要适用于材料表面和近表面的缺陷检测,对于深层缺陷的检测能力有限。
2.对材料形状和大小敏感:涡流检测的灵敏度受到材料形状和大小的影响,因此对于不同形状和大小的零件需要进行不同的检测设置。
3.不能检测非导电材料:涡流检测只能用于导电材料的检测,对于非导电材料的检测无能为力。
四、涡流检测的标准为了规范涡流检测的技术要求和应用范围,国际上制定了一系列相关标准。
下面是几个主要的涡流检测标准:1.ISO 18564-1: 无损检测-涡流检测-第1部分:一般原则和方法:该标准规定了涡流检测的一般原则和方法,包括检测设备的选择、检测程序、缺陷评定等方面。
2.ISO 18564-2: 无损检测-涡流检测-第2部分:设备:该标准规定了涡流检测设备的性能要求和测试方法,包括电磁线圈的设计、制造和测试要求等。
3.ISO 18564-3: 无损检测-涡流检测-第3部分:人员:该标准规定了从事涡流检测工作的人员要求,包括培训、资格认证、技能要求等方面。
涡流检测新技术

涡流检测新技术电磁涡流检测新技术主要有:1.1柔性阵列涡流传感器技术阵列涡流(Arrays Eddy Current, AED)传感器测试技术的研究始于2O世纪80年代中期,在20世纪80年代末到90年代初,出现了一批电涡流阵列测试方面的文献和专利。
近十年来,随着传感器技术的发展以及加工工艺技术水平的提高,电涡流传感器阵列测试的研究和应用得到极大的发展,不仅用来测量大面积金属表面的位移,而且由于具有同时检测多个方向缺陷的优点,被广泛应用于金属焊缝的检测,飞行器金属部件的疲劳、老化和腐蚀检测,涡轮机、蒸气发生器、热交换器以及压力容器管道等的无损检测中。
阵列式涡流检测探头是将很多小探头线圈按特定的结构类型密布在敞开或封闭的平面或曲面上构成阵列。
工作是采用电子学的方法按照设定的逻辑程序,对阵列单元进行实时/分时切换。
将各单元获取的涡流响应信号接入专用仪器的信号处理系统中去,完成一个阵列的巡回检测,阵列式涡流检测探头的一次检测过程相当与传统的单个涡流检测探头对部件受检面的反复往返步进扫描的检测过程。
对于高分辨率的大面积涡流检测,阵列式涡流检测探头明显比传统的扫描探头更具优势,阵列式涡流检测探头在检测时,其涡流信号的响应时间极短,只需激励信号的几个周期,而在高频时主要由信号处理系统的响应时间决定。
因此,阵列式涡流检测探头的单元切换速度可以很快,这一点是传统探头的手动或机械扫描系统所无法比拟的。
此外,传感器阵列的结构形式灵活多样,可以非常方便地对复杂表面形状的零件进行检测,而且这种发射/接收线圈的布局模式成倍的提高了对材料的检测渗透深度,因此,阵列式传感器的研究成为当前传感器技术研究中的重要内容和发展方向。
我国对于阵列涡流传感器技术的研究始于近年,清华大学、吉林大学、国防科技大学等单位发表了多篇关于涡流传感器阵列测试技术的研究文章;爱德森(厦门)电子有限公司则研制出工作频率为50KHZ—2MHZ、有效扫描宽度为55mm、双阵列、反射自旋式,用于铝合金板检测的阵列涡流传感器。
涡流阵列检测修正C扫描成像技术研究
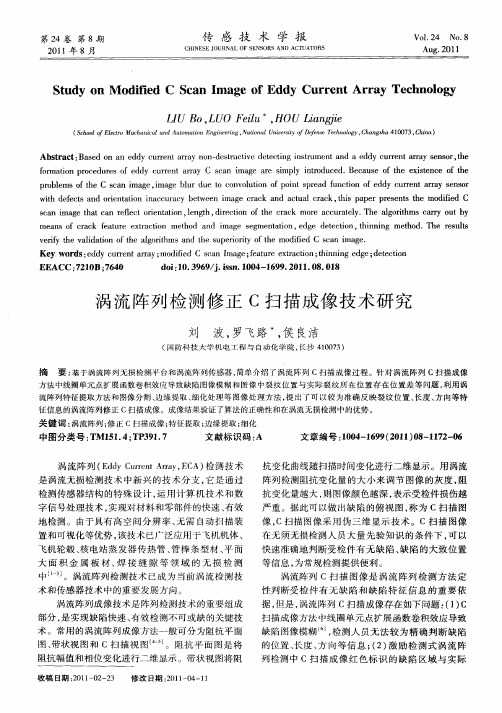
21 0 1年 8月
传 感 技 术 学 报
CH N S O NA EN OR D AC U T S I E E J UR L OF S S S AN T A OR
Vo . 4 No. 12 8
Au . 01 g2 1
S u y 0 1M o iid C c n I a e o dy Cu r n r y Te hn l g td 1 d fe S a m g f Ed r e tAr a c o o y
E AC 7 1 B;6 0 E C:2 0 7 4
d i1 .9 9j i n 1 0 — 6 9 2 1 . 8 0 8 o :0 3 6 / .s . 0 4 1 9 .0 1 0 . 1 s
涡流 阵列 检 测修 正 C扫描 成像 技术 研 究
刘 波 , 罗飞路 , 良洁 侯
( 防科 技 大 学 机 电 工程 与 自动 化 学 院 , 沙 4 07 ) 国 长 10 3
流阵列特征提取方法和 图像分割 、 边缘提取 、 细化处理等 图像 处理方法 , 出了可以较为准确 反映裂纹位 置、 提 长度 、 向等 特 方 征信息的涡流阵列修正 c扫描成像 。成像结果验证了算法的正确性和在涡流无损检测 中的优势。
关 细化
L U B , U e u HOU La g e / o L O F i , l in f i
( colfEet ca i l n uo ainE gnei N t n l nvrt ees eh o g , h nsa4 0 7 ,hn ) Sho o l r Mah nc dA tm t nier g,ai a i syo fneTcn l y C a gh 10 3 C ia co aa o n o U e i fD o
- 1、下载文档前请自行甄别文档内容的完整性,平台不提供额外的编辑、内容补充、找答案等附加服务。
- 2、"仅部分预览"的文档,不可在线预览部分如存在完整性等问题,可反馈申请退款(可完整预览的文档不适用该条件!)。
- 3、如文档侵犯您的权益,请联系客服反馈,我们会尽快为您处理(人工客服工作时间:9:00-18:30)。
电涡流阵列的测试方法
• 电涡流传感器阵列测试的关键还在于线圈阵列的引线设计, 图3是几种常用的基于单线圈检测原理的引线设计模式。 图3(a)是敏感线圈两端分别引线的设计模式,图3(b)是行 列垂直扫描式的引线设计。采用行列垂直结构形式的目的 是为了减少传感器阵列的外接引线数目,这对于传感器的 实际应用具有重要意义,但同时又不可避免地带来了各阵 列单元间的串扰,降低了测量精度。解决串扰的问题,最 简单的方法就是每个阵列单元单独引线(图3(a)),另外也 可以将预处理电路与敏感单元集成,做成一体化的集成传 感器单元,而其代价将是高昂的制作成本。有时为了提高 扫描采样的速度,还会采用一种行扫描采样的方法,即每 次扫描一行,从而大大提高传感器阵列的测试速度,但需 要增加预处理电路的数量。
电涡流检测的基本原理
• 电涡流检测的工作原理是检测激励线圈磁 场和感应涡流磁场之间的交互作用。当敏 感线圈通入交流电流时,线圈周围就会产 生交变磁场,如图1(a),如果此时将金属 导体工件移入此交变磁场中,工件表面就 会感应出电涡流,而此电涡流又会产生一 个磁场,该磁场的方向与原线圈磁场的方 向正好相反,从而减弱了原磁场。
电涡流阵列的设计和制作
电涡流阵列的设计和制作
• 传感器的探头采用柔性印刷电路板(FPCB)E艺在聚酰亚胺薄膜上制作,探头敏感线圈 阵列的整体尺寸很大,能达到200 mm ×200 mm。,而厚度却很薄,不超过 0.15 mm,且具有良好的柔韧性,几乎能 够应用于各种几何形状形面的测量。
传感器系统原理
电涡流阵列的形式
• 与其它一些传感器相比,电涡流传感器具有一个 比较突出的优点——探头的结构非常简单。从电 涡流检测的基本原理可以看出,电涡流传感器探 头的关键部件是敏感线圈,因此电涡流阵列测试 一般都是采用线圈阵列的方法,而不是将多个独 立的传感器探头布置成阵列形式来使用。针对不 同的测试条件和技术指标要求,线圈阵列可以设 计成不同的结构和形式,以实现复杂形面部件的 检测,但线圈阵列及其匹配电路的针对性设计也 带来了相对昂贵的成本。
电涡流阵列的设计和制作
• 根据上述的测试方法,设计并制作了一种扁平的柔性电涡流传感器阵 列,如图4,是传感器探头的结构简图。传感器的探头由敏感线圈阵 列及线圈引线所形成的一条引线电缆组成。在一般的使用情况下,探 头的线圈阵列多设计为与图2(a)类似的平面矩形结构(图4(a)),这里为 了更加方便、可靠地实现对复杂形状形面的检测,线圈阵列被设计为 一种条形分叉式结构(图4(b)),而且根据被测表面形状的不同,线圈 阵列的形状还可以有所不同。图4(b)中线圈阵列设计为两条平行的条 形结构,以实现金属管道的检测,如果被测曲面为一般平滑曲面,还 可以考虑设计成垂直条形结构或者6条分叉式结构。线圈阵列中各敏 感线圈的引线设计为一条细长的扁平引线电缆,这在大面积曲面间小 位移测量的应用中非常重要。引线电缆直接通过插头与处理电路连接, 由计算机控制实现传感器阵列的循环扫描测试。
电涡流阵列的形式
• 虽然电涡流线圈阵列结构形式的设计灵活多变,但仍然可以根据其检 测方式的不同,大体归为两种典型的阵列类型。① 基于单线圈检测的 电涡流阵列,如图2(a)所示,一般是直接在基底材料上制作多个敏感 线圈,布置成矩阵形式的阵列,而且为了消除线圈之间的干扰,相邻 线圈之间要保留足够的空间。这种电涡流阵列大多用于大面积金属表 面的接近式测量,检测部件的位置、表面形貌、涂层厚度以及回转体 零件的内外径等,也可以用来检测裂纹等表面缺陷。② 基于双线圈方 式的电涡流阵列检测,一般设计为一个大的激励线圈加众多小的检测 线圈阵列的形式,如图2(b),它能够非常有效地实现大面积金属表面 上多个方向的缺陷的检测,在无损检测的应用上具有较大的优势,已 基本取代单线圈检测的应用。除此以外,近年还出现了一种基于电涡 流效应的环绕线圈磁力计阵列L1 ,它实际上是一种基于双线圈检测 的阵列类型,通过对激励线圈和检测线圈阵列结构的特殊设计,以取 得较好的测试性能。
电涡流阵列的测试方法
电涡流阵列的测试方法
• 电涡流传感器阵列是用来实现金属表面的接近式 测量,故而采用单线圈检测的阵列形式。其测试 方法是在上述两种设计方案的基础上加以折中, 将所有线圈的一端作为公共端并接地,另一端分 别引出与模拟开关连接,如图3(c)所示。相对于 行列垂直引线,这种设计方法虽然引线数目较多, 但却能大大减小线圈之间的串扰,提高测量精度, 对于阵列数较少的测试系统,优势尤为明显。而 且采用这种引线方式,模拟开关便可选用一对多 的多路复用器,能够有效地简化控制电路,使后 续的处理电路进一步小型化。
电涡流检测的基本原理
• 另一种方法是双线圈检测,如图1(b),通过 使用另外一个线圈作为检测线圈,检测这 两个磁场的叠加效果。根据法拉第电磁感 应定律,检测线圈中将会产生一个感应电 动势: • 式中:ψ是通过线圈的交变磁场的磁通量; n是线圈的绕线圈数。 • 通过测量检测线圈中产生的电压即可非常 容易地得到磁场的变化情况。
通过计算机控制多路复用器,循环扫描采样所 有的阵列单元。传感器的变换电路采用调频式 振荡电路,电路输出的频率信号由计算机内置 的频率数据采集卡来采集,然后将采集到的数 据送入计算机进行处理,得到所需的被测曲面 的位置。
传感器系统原理
• 采用大面积的铁质平面对传感器阵列进行标定实验,实验 结果如图6所示,图6中4条曲线分别是传感器阵列中一条 支路上4个敏感单元的测试结果,4条曲线不重合的原因是 由于敏感线圈位置和引线的影响,采用软件补偿的方法即 能很好地解决。测试结果表明,在2 mm 的测量范围内, 传感器阵列的测试精度优于±0.25。采用传感器阵列进行 测试时,由于阵列单元间寄生电容的影响,振荡电路的中 心频率会有所降低,并导致传感器的灵敏度略有减小。为 了提高传感器的灵敏度,对振荡电路进行优化设计和改进, 提高振荡电路的中心频率,实验结果显示,在2 mm的量 程范围内,传感器的平均测量灵敏度约为70 Hz/μm,达 到了很好的效果。
电涡流传感器阵列检测技术
黑龙江省电力科学研究院 池永斌
概述
• 电涡流传感器是一种基于电涡流效应的无损、非接触式的 传感器,以其优良的测试性能,在机械量的测量以及金属 材料的无损检测等领域得到广泛应用。电涡流传感器阵列 测试技术的研究始于2O世纪80年代中期,在20世纪80年 代末到90年代初,出现了一批电涡流阵列测试方面的文献 和专利。近十年来,随着传感器技术的发展以及加工工艺 技术水平的提高,电涡流传感器阵列测试的研究和应用得 到极大的发展,不仅用来测量大面积金属表面的位移,而 且由于具有同时检测多个方向缺陷的优点,被广泛应用于 金属焊缝的检测,飞行器金属部件的疲劳、老化和腐蚀检 测,涡轮机、蒸气发生器、热交换器以及压力容器管道等 的无损检测中。
电涡流检测的基本原理
电涡流检测的基本原理
• 电涡流传感器通常有两种检测方法。一种是单线圈检测的 方法,通过检测敏感线圈阻抗的变化来反映磁场的变化情 况。线圈的等效阻抗z一般可表示为函数: • Z=F(σ,μ,f,x,r) • 式中:σ,μ分别是被测金属导体的电导率和磁导率;f是 激励信号的频率;x是线圈与金属导体的距离;r是线圈的 尺寸因子,与线圈的结构、形状以及尺寸相关。 • 可见,线圈阻抗的变化完整而且唯一地反映了被测金属导 体的电涡流效应。实际检测时,对不需要的影响因素加以 控制,就可以实现对上式中某个相关量的检测。作为接近 式传感器,线圈到金属工件之间的距离与线圈的阻抗直接 相关,而检测金属表面或近表面的缺陷时,缺陷的存在将 引起被测导体电导率和磁导率的变化,进而使线圈的阻抗 参数发生改变。
电涡流阵列的形式
电涡流阵列的测试方法
• 涡流传感器响应速度快的特点使其能够很 好地采用电子扫描测试的方法,通过控制 模拟开关,逐个扫描全部的阵列单元,实 现传感器阵列中所有敏感单元的检测。采 用扫描采样的方法,能够大大简化传感器 的后续电路,降低系统的成本,而且有利 于传感器系统的小型化,但是由于模拟开 关的引入,也导致传感器的测试精度有所 下降。
结束语
• 电涡流传感器阵列具有比传统电涡流传感器更加 优越的测试性能和广阔的应用前景。本文设计了 一种扁平柔性电涡流传感器阵列,以实现大面积 金属曲面部件位置的实时监测。通过对电涡流阵 列测试技术的研究,采用分时复用的扫描检测方 法和信号传输方法,将传感器线圈阵列中所有线 圈的一端设计为公共接地端,另一端分别接入多 路复用器,只用一套信号变换电路和信号调理电 路即完成传感器阵列中全部敏感线圈的采样,不 仅简化了系统电路,而且减小了各阵列单元间的 干扰,提高了传感器系统的性能,实现了电涡流 传感器阵列的快速、高精度测量。
概述
• 采用阵列式传感器,不需使用机械式探头扫描即可实现大 面积范围的高速测量,且能够达到与单个传感器相同的测 量精度和分辨率,有效地提高了传感器系统的测试速度、 测量精度和可靠性,此外,传感器阵列的结构形式灵活多 样,可以非常方便地对复杂表面形状的零件进行检测,因 此,阵列式传感器的研究成为当前传感器技术研究中的重 要内容和发展方向。 • 电涡流传感器阵列测试技术,一般采用时分多路的阵列测 试方法,实现大面积金属表面的接近式测量。通过对传感 器探头的线圈阵列及引线结构形式的合理设计,配合后续 的处理电路及计算机控制,完成电涡流传感器阵列的快速、 高精度测量及大面积金属曲面部件位置的检测。