第一章现代预焙铝电解槽的基本结构
铝电解槽制作、安装施工方案

铝电解槽制作、安装施工方案铝电解槽制作、安装施工方案电解槽壳制作:先作一样板槽,合格后方可大批下料制作。
1.1结构特点:槽壳是由钢板组成的船形结构,由一块底板、两块侧板和两块端板组成,斜侧板与直侧板及底板直接均呈135°角。
斜侧板与端板连接部分相贯形成部分椭圆,侧板与端板外均布置有加固围板和筋板,如图所示。
电解槽壳制作工艺流程图(见附图一)1.2电解槽壳制作方法:电解槽制作场地场地设置10t龙门吊2台。
铺设钢平台两座50m×20m。
制作场地总面积2000平米,场地布置见平面图。
电解槽壳制作分两部分:底板制作和槽壳壁板制作。
1.2.1底板制作:(1)底板是由两块或两块以上的钢板拼焊而成的,拼焊前,先检查钢板的不平度,要求是:1m凹凸不平度小于1mm,不合格进行校平,对接缝采用I型。
(2)底板在组对平台上点焊固定,组对平台用料约4吨,采用埋弧自动焊焊接,为保证质量加引弧板,材质与底板相同,焊缝最大间隙2-3mm。
为消除焊接变形做适当反变形,焊接采用先焊横缝后焊纵缝的焊接工艺。
焊完一面后反面用碳弧气刨清根再焊另一面,翻转底板时用[20制成的扁担夹具翻转。
(3)焊后检查平整度,要求同①,不合格校平。
(4)合格后划出中心线,按底板设计尺寸划线切割,切余部分可用做加强筋板。
1.2.2壁板制作壁板分端板结构和侧板结构两部分,端板结构是端板与其筋板组对焊接在一起形成的,侧板结构是直侧板,斜侧板及纵向水平筋板组对焊接在一起形成的。
(1)端板结构制作A.端板结构组焊胎具制作如图:B.加强筋板下料后组对焊接成数组丁字板,焊后一次调平、调直。
C.围带下料后以4条为一组在液压胎具上一次压制成形,控制内壁净尺寸。
D.端板下料后在液压胎具上压制成型,用内弧板检查弧度,控制内壁净尺寸为设计尺寸-10m。
E.将制好的端板扣在胎具上,用卡具使其与胎具紧密接触,然后划线组对筋板和围板,点焊对焊缝长度>40mm,进行焊接,焊接顺序为先焊筋板间焊缝,后焊筋板与端板间焊缝。
电解冶炼的电解槽结构

阳极的形状和尺寸根据电解槽的类型和工艺要求而 定,一般呈板状或棒状。
阴极
01
阴极的功能是吸引电解质中的阳离子,并将电子传递回电路中 。
02
阴极材料通常为导电性能良好的金属或合金,如钢、镍、铜等
。
阴极的形状和尺寸根据电解槽的类型和工艺要求而定,一般呈
03
板状或棒状。
电解质
01
02
03
电解质在电解过程中起 着传递离子和电子的作 用,是实现电化学反应
属。
氯碱生产
通过电解食盐水生产烧碱、氢 气和氯气。
电镀
利用电解过程在金属表面沉积 所需的金属或合金层,提高其 耐腐蚀性和美观度。
其他领域
电解过程还可应用于化学合成 、污水处理、食品工业等领域
。
02
电解槽的构成
阳极
01
阳极的功能是将直流电能转化为化学能,并传递电 子至电解质中。
02
阳极材料通常为导电性能良好的金属或复合材料, 如铁、铜、钛等。
生产过程中的噪音和振动等对环境的影响。
THANKS
感谢观看
温度异常
检查冷却水系统是否正常,电解槽内部是否有局部过 热现象。
气体泄漏
检查电解槽的气体密封是否完好,如有泄漏及时处理 。
电解槽的优化建议
改进电极结构
优化电极形状和尺寸,提高电极的有效面积和电流密度。
提高冷却效果
改进冷却水系统,提高电解槽的散热性能,降低温度波动。
优化电解质成分
根据生产需求调整电解质成分,提高电解效率并降低能耗。
电解槽通常由电极(阳极和阴极)、 电解质、隔膜和外壳等部分组成。
电解槽的种类
按电解质种类分类
按应用领域分类
铝电解培训教材
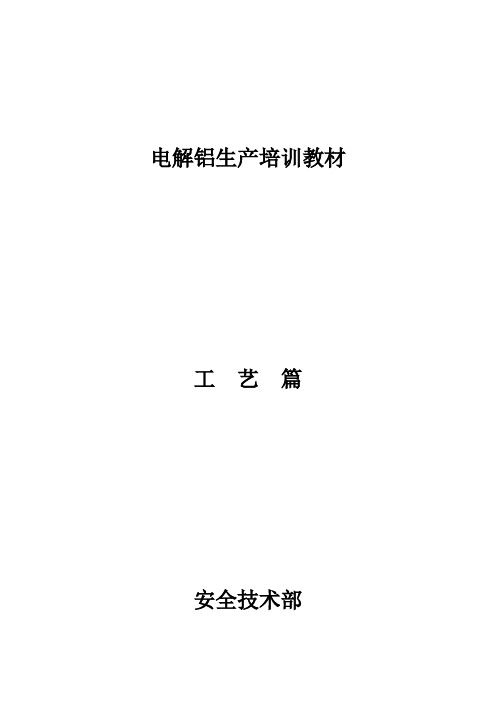
电解铝生产培训教材工艺篇安全技术部第一章铝电解概述第一节铝电解发展及现状铝(Aluminium)在自然界中分布极广,地壳中铝的含量约为7.5%,仅次于氧(O)和硅(Si),居第三位,在各种金属元素当中,铝居首位。
铝的化学性质十分活泼,但是自然界中发现了少量元素状态的铝,与其他矿物共生。
含铝的矿物总计有250多种,其中主要的是铝土矿、高岭土、明矾石等。
我国开采和利用铝矿有悠久的历史,很早就开始从明矾石提取(古称矾石),供医药及工业上使用。
汉代《本草经》一书中记载了16中矿物药物,其中就包括矾石、铅丹、石灰、朴硝、磁石。
明代宋应星所著《天工开物》一书中记载了矾石的制造和用途。
金属铝最初用化学法制取。
1825年,丹麦Oersted用钾贡还原无水氯化铝,得到一种灰色的金属粉末,在研磨时呈现金属光泽,但当时未能加以鉴定。
1827年,德国Wohler 用钾(K)还原无水氯化铝,得到少量细微的金属颗粒。
1845年,他把氯化铝气体通过熔融的金属钾表面,得到金属铝珠,每颗铝珠的质量为10~15mg,于是铝的一些物理性质和化学性质得到了测定。
1854年,法国Deville用纳代替钾还原NaCl-AlCl3络合盐,制取金属铝。
钠和钾同为一价碱金属,但钠的相对原子质量比钾小,制取1Kg铝所需的钠大约是3.0~3.4Kg,而用钾大约需要5.5Kg,故用钠比较经济。
当时称铝为“铝土中的银子”1855年,Deville在巴黎世界博览会上展出了12块小铝锭,总量约为1 Kg。
1854年,在巴黎附近建成了世界上第一座炼铝厂。
1865年,俄国Beketob提议用镁还原冰晶石来生产铝。
这一方案后来在德国Gmelingen铝镁工厂里被采用。
自从1887~1888年电解法炼铝工厂开始投入生产后,化学法便渐渐停止了,在此之前的30多年内采用化学法总共生产了200T铝。
原来在采用化学法炼铝期间,德国Bunsen和法国Deville继英国Davy之后研究电解法炼铝。
现代铝电解技术pdf
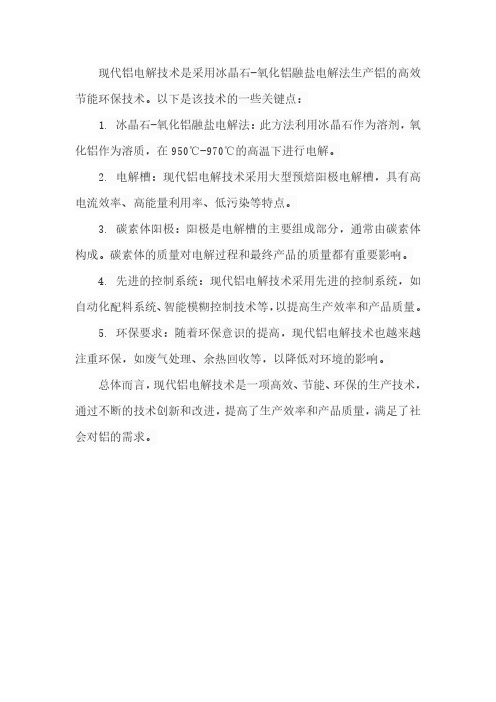
现代铝电解技术是采用冰晶石-氧化铝融盐电解法生产铝的高效节能环保技术。
以下是该技术的一些关键点:
1.冰晶石-氧化铝融盐电解法:此方法利用冰晶石作为溶剂,氧化铝作为溶质,在950℃-970℃的高温下进行电解。
2.电解槽:现代铝电解技术采用大型预焙阳极电解槽,具有高电流效率、高能量利用率、低污染等特点。
3.碳素体阳极:阳极是电解槽的主要组成部分,通常由碳素体构成。
碳素体的质量对电解过程和最终产品的质量都有重要影响。
4.先进的控制系统:现代铝电解技术采用先进的控制系统,如自动化配料系统、智能模糊控制技术等,以提高生产效率和产品质量。
5.环保要求:随着环保意识的提高,现代铝电解技术也越来越注重环保,如废气处理、余热回收等,以降低对环境的影响。
总体而言,现代铝电解技术是一项高效、节能、环保的生产技术,通过不断的技术创新和改进,提高了生产效率和产品质量,满足了社会对铝的需求。
电解槽基础

二、铝电解槽的阴极结构
(1)、槽壳 槽壳采用摇篮式结构。电解槽槽壳采用摇篮架式。内壁 尺寸:9800mm×4350mm×1350mm, 外廓尺寸: 10544mm×5100mm×1740mm,槽壳总重22.5吨。摇篮架 共有17个,其中两端的两个与电解槽焊接在一起,其余15 个用螺栓和翼板联结在一起,中间垫以10×285×300mm3 的石棉板,起到绝热作用。 摇篮架和槽壳之间由两块钢垫块隔开,钢垫块焊在槽壳 上,其规格为13×15×200mm3,槽底和摇篮架顶部垫有 尺寸为10×140×4370mm3的石棉板,翼使摇篮架在底于 200°C下工作,槽壳坐落在两根250×9300mm的工字钢 梁上(俗称A、B梁)。有4根支持梁与工字钢梁相联结, 用于支撑槽底阴极母线。
槽顶水平密封罩板与桁架焊接在一起,在密封板下部由 三角行集气罩,密封板A、B侧各留有12个缺口,一便
能进入阳极导杆。为提高烟气和粉尘的捕集效率,槽顶 部密封板和铝导杆之间采用石棉布密封。
铝制槽罩板上部与水平密封罩板绝缘,下部与槽沿板绝
缘,以防止阳极母线与槽壳间形成短路。
8
阳极炭块组
阳极炭块组由铝导杆、铝钢爆炸焊片、钢连接板梁、钢 爪头和预焙阳极炭块组成。其主要作用是导电,因此要 求其电 中间下料预焙电解槽每台共有16组阴极炭块,阴极尺寸为 3150×515×450mm3,相邻两组炭块之间缝隙为35mm,采用热糊 热扎技术扎缝。 电解槽侧部用1层炭块砌筑,以使电解槽成侧部散热型,易于形成 侧部炉帮。侧部炭块规格520×350×123mm3,炭块与电解槽侧壁 钢板之间有一定的间,作为伸缩缝,以满足电解槽投入生产后炭块 膨胀的需要。在侧部炭块与底部阴极炭块之间有用炭糊扎成的高 200mm、宽250mm的人造伸腿,以便于形成侧部电解质炉帮。 阴极炭块底部为2层耐火砖,每层厚65mm,耐火砖之间用耐火泥粘 结并错缝垒砌,耐火砖下层是一层65mm厚的氧化铝。氧化铝垫层 的作用,一方面是用于保温和防止电解质的侵蚀,另一方面是起到 缓冲热应力的作用。氧化铝下层是2层保温砖,每层厚65mm,中间 用2mm厚的氧化铝粉填缝和找平。最底部是1层65mm厚的硅酸钙特 种绝热板。总高度398mm,保温砖与耐火砖的周边充填耐火颗粒。
铝电解槽的上部结构

铝电解槽的上部结构铝电解槽的上部结构是指槽体之上的金属结构部分,统称上部结构。
可分为承重桁架、阳极提升装置、打壳下料装置、阳极母线和阳极组、集气和排烟装置。
1)承重桁架。
承重桁架采用钢制的实腹板梁和门形立柱,板梁由角钢及钢板焊接而成,门形立柱由钢板制成门字形,下部用铰链连接在槽壳上,一方面抵消高温下桁架的受热变形,同时又便于大修时的拆卸搬运。
门形立柱起着支承上部结构全部重量的作用。
2)阳极提升装置。
阳极提升装置有两种方式,一种是采用蜗轮蜗杆螺旋起重器阳极提升机构,另一种是采用滚珠丝杠三角板阳极提升装置。
蜗轮蜗杆螺旋起重器阳极提升装置由螺旋起重器、减速器、传动机构和电机组成,其工作原理为:整个装置由4个(或8个)螺旋起重器与阳极大母线相连,由传动轴带动起重器,传动轴与减速器齿轮通过联轴节相连,减速器由电机带动。
当电机转动时,便通过传动机构带动螺旋起重器升降阳极大母线,固定在大母线上的阳极随之升降。
变速机构可以安装在阳极端部或中部。
提升装置安装在上部结构的桁架上,在门式架上装有与电机转动相关的回转计,可以精确显示阳极母线的行程位置。
3)自动打壳下料装置。
该装置由打壳和下料系统组成。
一般从电解槽烟道端起安置4~6套打壳下料装置,出铝端设一个打壳出铝装置,出铝锤头不设下料装置。
打壳装置是为加料而打开壳面所用的装置,它由打壳气缸和打击头组成。
打击头为一长方形钢锤头,通过锤头杆与气缸活塞相连。
当气缸充气、活塞运动时,便带动锤头上下运动而打击熔池表面的结壳。
下料装置由槽上料箱和下料器组成。
料箱上部与槽上风动溜槽或原料输送管相通;筒式下料器安装在料箱的下侧部。
筒式定容下料器由一个气缸带动一个在钢筒中的透气钢丝活塞及一个密封钢筒下端的钟罩组成。
钟罩与透气活塞将钢筒的下部隔成一个定容空间,定容空间的上端开有下料口。
整个打壳下料系统由槽控箱控制,并按设定好的程序,由计算机通过电磁阀控制,完成自动打壳下料作业。
4)阳极母线及阳极组。
电解铝电解槽结构
电解铝电解槽结构电解铝是一种重要的金属材料,广泛应用于航空、汽车、建筑等领域。
而电解铝的生产过程中,电解槽是关键设备之一。
本文将介绍电解铝电解槽的结构和工作原理。
一、电解槽的概述电解槽是电解铝生产中的核心设备,其主要功能是通过电解过程将铝矾土中的铝氧化成金属铝。
电解槽一般由槽体、电解质、电极和电源等组成。
二、槽体结构电解槽的槽体一般采用钢结构,具有良好的耐腐蚀性和机械强度。
槽体内部由耐火材料涂层,以抵抗高温和化学侵蚀。
槽体的底部设有底部引流口,用于排出电解过程中产生的铝液。
三、电解质电解质是电解槽中的重要组成部分,它起到导电和溶解铝的作用。
电解质一般由氟化铝和氯化铝等盐类组成,能够在高温下保持液态状态。
电解质的浓度和温度对电解过程的效果有重要影响。
四、电极结构电解槽中的电极是电流的传导介质,一般由碳材料制成。
电解槽中有两种类型的电极,分别是阴极和阳极。
阴极是电解铝的产出端,它由导电炭块组成,能够吸附氧化铝并还原成金属铝。
阳极则是电解质的溶解端,它由碳块或碳钢制成,能够氧化成二氧化碳。
五、电源系统电解槽的电源系统是为电解过程提供电能的设备。
电源系统一般由整流器和变压器组成。
整流器将交流电转换为直流电,变压器则将高压电流降低到适合电解槽的电压。
六、电解过程电解过程是电解铝生产的核心环节。
在电解槽中,铝矾土经过磨碎、脱水等处理后,成为称为氧化铝的粉末。
氧化铝与电解质混合后,放置在电解槽中。
通电后,正极吸附氧化铝并还原成金属铝,同时负极产生氧化反应。
金属铝在槽底通过底部引流口排出,而氧化反应则产生二氧化碳。
七、电解槽的优化为了提高电解铝的生产效率和降低能耗,电解槽的结构也在不断优化。
例如,采用新型的槽体材料和涂层,能够提高抗腐蚀性和热稳定性;优化电解质的组成和浓度,可以提高电解效果;改进电极材料和形状,能够增加电流传导效率。
总结起来,电解铝电解槽是电解铝生产过程中的核心设备,其结构包括槽体、电解质、电极和电源等。
铝电解槽PPT课件
40~ 60
复 杂 (有 焦 化产物) 9 .2
铝冶金设备—融盐电解槽
铝电解槽系列
铝电解槽系列是铝生产的单元,每一个系列都有它 额定的直流电源和电解槽数目, 系列中电解槽串联连接,直流电从整流器之正极经 铝母线送到电解槽的阳极,经电解质和铝液层流过 阴极,然后进入下一台电解槽的阳极,依次类推,从最 后一台电解槽阴极出来的电流,返回整流器的负极,
电解厂房内电解槽的配置方式有纵向排列和横向排 列两种,每一种排列方式又可分为单行排列和双行 排列, 在电解厂房中间设有氧化铝贮仓, 大型槽采用各自的自动加料装置,
铝冶设备—融盐电解槽
2.3.4 未来铝电解槽的改进
目前的铝电解槽尚存在一些问题:生产过程能量利用率较低, 电流效率不太理想,单位产品的投资费用较高,控制污染的设备 费用也很贵, 1 .原有电解槽的改造:阴极材料、阳极材料及槽内衬等的改造, 2. 新型电解槽: Grjotheim的理想槽;该槽具有一系列优点,在双 极性电解槽设计中优先采用了不耗惰阳极和可泄性或可湿润 性的耐热硬质金属阴极,
10.2.3.3 连续预焙阳极电解槽
相对于非连续式有如下特 点:
优点:无阳极残极,预焙 炭块消耗量小;阳极电流 分布均匀,故阳极消耗均 匀;生产的连续性,
缺点:阳极不能用氧化铝 保温,热损失大;炭块之 间接缝存在接触电压降, 故槽电压较高,
连续式预焙阳极电解槽简图 1-阳极炭块;2-阳极棒;3-阳极母线;4-槽壳; 5-炭块接缝;6-阴极炭块;7-阴极棒;8-保温层
铝冶金设备—融盐电解槽
作业
1 试述融盐电解的原理、特征及适用范围, 2 铝电解槽的类型有哪些 各有何优缺点 3 阳极电流密度对铝电解技术经济指标的影响如何 与哪些因素有关 4 铝母线的配置方式有几种 各适用于哪些槽型, 5 什么叫经济电流密度 其大小如何确定
铝电解预焙阳极电解槽的介绍与展望
铝电解预焙阳极电解槽的介绍与展望铝电解预焙阳极电解槽的介绍与展望摘要:本文主要是对电解铝工业生产中的主要设备——电解槽的相关介绍,重点讲述预焙阳极电解槽的相关技术参数、指标、工艺等指数。
其后介绍现代关于铝电解槽的新工艺、新设备。
关键词:电解槽预焙阳极阳极炭块阴极炭块电解铝就是通过电解得到的铝。
现代电解铝工业生产采用冰晶石-氧化铝融盐电解法。
熔融冰晶石是溶剂,氧化铝作为溶质,以碳素体作为阳极,铝液作为阴极,通入强大的直流电后,在950℃-970℃下,在电解槽内的两极上进行电化学反应,既电解。
abstract: this article is mainly to the aluminum industrial production of main equipment-electrolytic cell related introduction, focuses on pre-baked anode cell related technical parameters, index, craft index. Introduced by modern about aluminum cell of new technology, new equipment.Key words: pre-baked anode cell anode block cathode carbon blocksAluminum electrolytic aluminum is through get. Modern aluminum industrial production adopts BingJingShi-alumina melts salt by electro-dialysis. Molten BingJingShi is solvent, alumina as solute, with carbon body is used as an anode, liquid aluminum as a cathode, ventilation with powerful dc, in 950 ℃-970 ℃, the poles in the elect ric in the electrochemical reactions, both electrolysis.1 预焙阳极电解槽的介绍电解槽是电解炼铝的核心设备,一百多年来铝电解槽的结构有了许多改进,其中以电解阳极的变化最大。
2-3铝电解槽结构
三、电解槽结构
自焙阳极旁插式电解槽 • 基础:绝缘 • 阴极:保温、坚固、密封防氧化、底糊
防侵蚀、挡板防淌料、侧部炭糊筑坡 • 阳极: 铝箱、钢质框架 • 上部金属结构:支柱、平台、AO料斗、
阳极升 降机构、槽帘和排烟系统 • 导电母线和绝缘设施
三、电解槽结构
自焙阳极上插式电解槽:
三、电解槽结构
四、电解槽系列
• 为保证系列的连续稳定运行,需备用电源;
• 电解槽排布方式:
• 横向排列 • 纵向排列
单行排列 双行排列
四、电解槽系列
铝电解
目录 CONTENTS
铝电解基本知识 铝电解槽结构 电解槽焙烧与启动 铝电解正常生产
02
铝电解槽结构
一、工作原理
• 电解质:冰晶石—氧化铝融盐, • 电流:直流电(4~22kA); • 电解温度:950~970℃; • 电极:阴、阳极均为碳质,阴极上析出铝、
而阳 极上析出CO2(70%)和CO2(30%) 气体; • 电解总反应: • 2Al2O3(aq)+3C(s)=4Al(l)+3CO2 (g)
部打壳电解槽
• 阳极炭块组:阳极导杆、钢爪、炭 块
• 阴极装置:阴极炭块、钢质导电棒 • 铝母线:阳极母线、阴极母线、立
柱母线
三、电解槽结构
连续预焙阳极电解槽 • 相对于非连续式有如下特点: 优点: • 无阳极残极,预焙炭块消耗量小; • 阳极电流分布均匀,故阳极消耗均匀; • 生产的连续性。 缺点: • 阳极不能用氧化铝保温,热损失大; • 炭块之间接缝存在接触电压降,故槽电压较大。
二、电解槽的发展
• 铝电解槽的发展从19世纪末至今已经有了一百多年的历史。 • 三个发展阶段: • 铝电解工业初期的小型预焙电解槽; • 20世纪20~40年代,相继采用旁插棒式自焙阳极和上插棒式自焙
- 1、下载文档前请自行甄别文档内容的完整性,平台不提供额外的编辑、内容补充、找答案等附加服务。
- 2、"仅部分预览"的文档,不可在线预览部分如存在完整性等问题,可反馈申请退款(可完整预览的文档不适用该条件!)。
- 3、如文档侵犯您的权益,请联系客服反馈,我们会尽快为您处理(人工客服工作时间:9:00-18:30)。
第二篇:铝电解生产的工程技术1、现代预焙铝电解槽的基本结构现代铝工业已基本淘汰了自焙阳极铝电解槽,并主要采用容量在 160kA 以上的大型预焙阳极铝电解槽(预焙槽)。
因此本章主要以大型预焙槽为例来讨论电解槽的结构。
工业铝电解槽通常分为阴极结构、上部结构、母线结构和电气绝缘四大部分。
各类槽工艺制度 不同,各部分结构也有较大差异。
图1、图2分别为一种预焙槽的断面示意图和三维结构模拟图;图3、图4为我国一种200kA 中心点式下料预焙槽的照片与结构图(总图) 。
阳极导杆 阳极炭块电解质液 铝液 阴极炭块阴极钢棒下料器 集气罩氧化铝覆盖料电解质结壳 钢壳 耐火与保温内衬rrT|i|TITTT图1预焙铝电解槽断面示意图图2预焙铝电解槽三维结构模拟图图3我国的一种200kA 预焙铝电解槽(照片)1.1阴极结构电解铝工业所言的阴极结构中的阴极,是指盛装电解熔体(包括熔融电解质与铝液)的容器, 包括槽壳及其所包含的内衬砌体,而内衬砌体包括与熔体直接接触的底部炭素(阴极炭块为主体)■nnJ10- ]【1 -心L—L J — —J图4 我国一种200kA 预焙铝电解槽结构图1.混凝土支柱;2.绝缘块;3.工字钢;4.工字钢;5•槽壳;6.阴极窗口; 7.阳极炭块组;8.承重支架或门;9.承重桁架;10.排烟管;11.阳极大母线;12.阳极提升机构;13.打壳下料装置;14.出铝打壳装置;15.阴极炭块组;16.阴极内衬rM〒■■mT XTI I5 6nu与侧衬材料,阴极炭块中的导电棒、底部炭素以下的耐火材料与保温材料。
阴极的设计与建造的好坏对电解槽的技术经济指标(包括槽寿命)产生决定性的作用。
因此,阴极设计与槽母线结构设计一道被视为现代铝电解槽(尤其是大型预焙槽)计算机仿真设计中最重要、最关键的设计内容。
众所周知,计算机仿真设计的主要任务是,通过对铝电解槽的主要物理场(包括电场、磁场、热场、熔体流动场、阴极应力场等)进行仿真计算,获得能使这些物理场分布达到最佳状态的阴极、阳极和槽母线设计方案,并确定相应的最佳工艺技术参数(详见本书第三篇“铝电解槽的动态平衡及物理场”),而阴极的设计与构造涉及到上述的各种物理场,特别是它对电解槽的热场分布和槽膛内形具有决定性的作用,从而对铝电解槽热平衡特性具有决定性的作用。
1.1.1槽壳结构槽壳(即阴极钢壳)为内衬砌体外部的钢壳和加固结构,它不仅是盛装内衬砌体的容器,而且还起着支承电解槽重量,克服内衬材料在高温下产生热应力和化学应力迫使槽壳变形的作用,所以槽壳必须具有较大的刚度和强度。
过去为节约钢材,采用过无底槽壳。
随着对提高槽壳强度达成共识,发展到现在的有底槽。
有底槽壳通常有两种主要的结构形式:自支撑式(又称为框式)和托架式(又称为摇篮式),其结构图分别见图5a,b。
过去的中小容量电解槽通常使用框式槽壳结构,即钢壳外部的加固结构为一型钢制作的框,该种槽壳的缺点钢材用量大,变形程度大,未能很好地满足强度要求。
大型预焙铝电解槽采用刚性极大的摇篮式槽壳。
所谓摇篮式结构,就是用40a工字钢焊成若干组”型的约束架,即摇篮架,紧紧地卡住槽体,最外侧的两组与槽体焊成一体,其余用螺栓与槽壳第二层围板连结成一体(结构示意图如图6所示)。
图6 大型预焙铝电解槽槽壳结构图a —纵向;b —横向图5铝电解槽的槽壳结构示意图a—自支撑式(框式);b—托架式(摇篮式)现代大型预焙槽槽壳设计利用先进的数学模型和计算机软件对槽壳的受力、强度、应力集中点、局部变形进行分析和相应的处理,使槽壳的变形很小并且还加强槽壳侧部的散热以利于形成槽膛。
例如沈阳铝镁设计研究院设计的SY350型350kA预焙槽的槽壳设计为:大摇篮架结构(摇篮架通长至槽沿板,采用较大的蓝架间隔);槽壳端部三层围板加垂直筋板;大面采用船形结构以减少垂直直角的应力集中;大面采用单围带(取消腰带钢板与其间的筋板)并在摇篮架之间的槽壳上焊有散热片以增大散热面积;摇篮架与槽体之间隔开,使摇篮架在300 C 以下工作。
图7所示是大摇篮架船形槽壳部分图。
有人认为,图7 ( b )所示的圆角型与图7 ( a)所示的三角型相比,圆角型船形结构槽壳受力更好,且更有效地降低槽两侧底部应力集中[1]。
a b图7大摇篮架船形槽壳部分图a —三角型b—圆角型对槽寿命要求的提高体现在电解槽大修中就是对槽壳变形修复要求的提高。
不仅要修理槽壳的外形尺寸,而且要定期对槽壳的结构进行更新,对产生了蠕变和钢材永久性变形的槽壳实施报废制度,更新整个槽壳。
1.1.2内衬结构内衬是电解槽设计与建造中最受关注的部分。
现在世界上铝电解槽内衬的基本构造可分为“整体捣固型”、“半整体捣固型”与“砌筑型”三大类:(1)整体捣固型:内衬的全部炭素体使用塑性炭糊就地捣固而成,其下部是用作保温与耐火材料的氧化铝,或者是耐火砖与保温砖。
(2)半整体捣固型:底部炭素体为阴极炭块砌筑,侧部用塑性炭糊就地捣固而成,下部保温与耐火材料与整体捣固型的类似。
(3)砌筑型:底部用炭块砌筑,侧部用炭块或碳化硅等材料制成的板块砌筑,下部为耐火砖与保温砖及其他耐火、保温和防渗材料。
根据底部炭块及其周边间缝隙处理方式的不同,砌筑型又分为“捣固糊接缝”和“粘结”两种类型,前种类型是在底部炭块砌筑时相互之间及其与侧块之间留出缝隙,然后用糊料捣固;后种类型则不留缝隙,块间用炭胶糊粘结。
上述的整体捣固型与半整体捣固型被工业实践证明槽寿命不好,加之电解槽焙烧时排出大量焦油烟气和多环芳香族碳氢化合物,污染环境,因此已被淘汰。
砌筑型被广泛应用。
砌筑型中的粘结型降低了“间缝”这一薄弱环节,被国外一些铝厂证明能获得很高的槽寿命,但对设计和材质的要求高,因为电解槽在焙烧启动过程中,没有间缝中的炭素为炭块的膨胀提高缓冲(捣固糊在碳化过程中会收缩),因此若设计不合理或者炭块的热膨胀与吸钠膨胀太大,便容易造成严重的阴极变形或开裂。
内衬的基本类型确定后,具体的结构将按最佳物理场分布原则进行设计。
当容量、材料性能以及工艺要求不同时,所设计出来的内衬结构便应该不同,但一旦阴极结构设计的大方案确定(例如选用“捣固糊接缝的砌筑型” ),则不论是小型还是大型槽,其内衬的基本结构方案可以是相似的,区别往往体现在具体的结构参数上,而对于同等槽型和容量的电解槽,结构参数上的区别往往由设计理念、物理场优化设计工具和筑槽材料性能上的差异所引起。
我国目前均采用捣固糊接缝的砌筑型。
图8 是我国大型预焙铝电解槽内衬基本结构方案的一个实例。
内衬底部构成为:底部首先铺一层65mm 的硅酸钙绝热板(或先铺一层10mm 厚的石棉板,再铺一层硅酸钙绝热板);在绝热板上干砌两层65mm 的保温砖(总厚度130mm ),或者为加强保温而干砌三层65mm 的保温砖(有种设计方案是在绝热板上铺一层5mm 厚的耐火粉,用以保护绝热板,然后在其上干砌筑保温砖);铺设一层厚130〜195mm 的干式防渗料(具体厚度视保温砖的层数而定,即两层保温砖对应195mm 厚度,三层保温砖对应130mm 厚度),或者在三层保温砖上用耐火粉找平后铺一层1mm 厚钢板防渗漏,再其上用灰浆砌两层65mm 的耐火砖;在干式防渗料上(或耐火砖上)安装已组装好阴极钢棒的通长阴极炭块组;阴极炭块之间有35mm 宽的缝隙,用专制的中间缝糊扎固。
内衬侧部(底部干式防渗料或耐火砖以上的侧部)的构成及特点为:对于与底部炭块端部对应的侧部,靠钢壁砌筑一道65mm 的保温砖,或者布设10mm 石棉板和40〜60mm 高温硅酸钙板;然后在该保温层与底部炭块之间浇注绝热耐火混凝土(高强浇注料);并留出轧制人造伸腿的空隙;在浇注料上方砌筑一层耐火砖,再在该耐火砖上方砌筑一层123mm厚的侧部炭块(或氮化硅粘结的碳化硅砖),并使其背贴碳胶到钢壳壁上;侧部炭块顶上用80mm 宽、10mm 厚的钢板紧贴住炭块顶部焊接在槽壳上,防止炭块上抬;底部炭块与侧部砌体之间的周边缝用专制的周围糊扎成200mm 高的人造坡形伸腿。
图8大型预焙阳极铝电解槽槽内衬结构图(实例)大型中间下料预焙槽从工艺上要求底部应有良好的保温,以利用炉底洁净;侧部应有较好的散热,以促成自然形成炉膛。
侧部炭块下的浇注料(或耐火砖砌)做成阶梯形,以抑制伸腿过长。
1.1.3筑炉的基本规范下面,主要结合上述大型预焙槽的内衬结构实例(图8),介绍当前我国大型预焙槽筑炉的基本规范,主要包括工艺要求与材料指标两个部分。
其中所列材料是当前我国电解槽内衬常用材料,而非最好、最先进的材料。
关于筑炉材料中的炭素材料(阴极炭块、侧部碳块及重要糊料等)还将在本书第六篇“铝用炭素材料与技术”中详细讨论。
1.1.3.1 槽底砌筑(1 )槽底砌筑的工艺要求:a.清理与放线:槽壳清理干净后,依据电解槽内衬施工图,进行基准放线作业。
b.铺石棉板:槽底铺一层10mm 石棉板,接缝小于2mm,石棉板间缝用氧化铝纷填平。
c.铺绝热板(硅酸钙板):绝热板的接缝小于2mm,所有缝间用氧化铝粉填满,绝热板与槽壳间隙填充耐火颗粒,粒度小于2mm ;绝热板的加工采用锯切割;根据槽底变形情况允许局部加工绝热板,但加工厚度不大于10mm。
d.砌筑(干砌)粘土质隔热耐火砖:隔热砖加工采用锯切割;砌筑时按画在槽壳上的砌体层高线逐层拉线控制;第一层隔热耐火砖在绝热板上进行作业,所有砌筑缝小于2mm,并用氧化铝粉填满,不准有空隙;隔热砖与侧部绝热板间填充耐火颗粒,粒度小于2mm,填实;第二层隔热耐火砖与第一层隔热砖应错缝砌筑,所有砖缝用氧化铝粉填满;第隔热砖与侧部绝热板间填充耐火颗粒,粒度小于2mm,填实。
e.铺干式防渗料:将干式防渗料铺在耐火砖上,用样板挂平,铺一层薄膜,薄膜上铺纤维板,然后用平板振动机。
要求分两层铺料、夯实达到设计要求的密实厚度,夯实完后按预先划好的基准线测量9点,要求水平误差不大于土2mm/m。
高度误差不大于土1.5mm,局部超出标准可进行整理,并保证阴极炭块组安装尺寸。
(2)槽底砌筑用主要材料的指标a.硅酸钙板:表1和表2所列为符合国家标准 GB/T10699-1998的硅酸钙板的主要指标。
表1硅酸钙板的性能指标注:最高使用温度槽底 侧部规格。
表2硅酸钙板的尺寸允许偏差和外观b.粘土质隔热耐火砖:表3和表4所列为符合国家标准 GB/T3994-1983的粘土质隔热耐火砖的主要指标。
表3粘土质隔热耐火砖的性能指标注:①砖的工作温度超过重烧线变化的试验温度。
NG-0.7与NG-0.6相同。
②表内导热系数指标为平板法试验数据。
表粘土质隔热耐火砖的尺寸允许偏差及外形( )注:宽度〜的裂纹不允许跨过两个或两个以上的棱。
c.粘土质耐火砖:表5、表6所列为符合国家标准YB/T5106-1993 的粘土质耐火砖的主要指标。