大滞后控制
大滞后系统控制方法

大滞后系统控制方法
大滞后系统控制可有点小麻烦呢。
你想啊,就像你喊一个人,结果他过了老半天才有反应,这多让人着急。
那对于这种大滞后系统,有一种预测控制方法。
这就好比你要去赶火车,你知道火车啥时候开,路上大概会堵多久,那你就能提前规划好出门时间。
预测控制就是这么个道理,它根据系统的模型,去预测未来的输出,然后提前调整控制量。
比如说在一些化工生产里,从原料投入到产品出来可能有很长的滞后,通过预测控制就能提前调整进料量、温度这些参数,让最后的产品质量啥的都能符合要求。
还有一种方法是史密斯预估器。
这个东西可神奇啦,它就像是给这个滞后系统找了个替身。
它把这个滞后环节单独拎出来,然后通过一个预估模型,让控制器看到如果没有滞后的话系统应该是什么样的反应。
这样控制器就不会被滞后给搞晕头转向啦。
打个比方,就像你在玩一个有延迟的游戏,这个预估器就像是告诉你,要是没有这个网络延迟,你的操作应该会有什么样的结果,然后你就能更好地玩游戏啦。
模糊控制也能在大滞后系统里发挥作用哦。
模糊控制就不那么死板,它不是说精确地算出一个数值来控制。
就像你做菜的时候,你不会精确到放多少克盐,而是根据感觉,大概、差不多就行。
模糊控制对于大滞后系统,就是根据一些模糊的规则,比如“如果偏差大而且变化快,那就大幅度调整控制量”这种感觉的规则。
因为大滞后系统很难精确建模,模糊控制这种有点“随性”的方法有时候反而能取得不错的效果呢。
大滞后系统控制虽然有点难搞,但有了这些方法,就像给我们在黑暗中摸索的人点亮了一盏盏小灯,让我们能更好地驾驭这些“反应慢半拍”的系统啦。
《基于PLC的面向加热水箱大滞后系统控制算法实现与优化》范文

《基于PLC的面向加热水箱大滞后系统控制算法实现与优化》篇一一、引言随着工业自动化技术的快速发展,可编程逻辑控制器(PLC)在工业控制系统中扮演着越来越重要的角色。
然而,对于加热水箱这类大滞后系统,传统的控制算法往往难以实现精确和稳定的控制。
因此,本文将探讨基于PLC的面向加热水箱大滞后系统的控制算法实现与优化,以期提高系统的控制精度和稳定性。
二、问题背景及研究意义加热水箱系统由于其固有的大滞后特性,常常导致温度控制不稳定,影响了生产效率和产品质量。
传统的PID控制算法虽然简单易行,但对于大滞后系统往往难以达到理想的控制效果。
因此,研究基于PLC的面向加热水箱大滞后系统的控制算法实现与优化,对于提高工业生产效率和产品质量具有重要意义。
三、相关技术综述在控制算法领域,针对大滞后系统的控制方法主要包括预测控制、模糊控制、神经网络控制等。
其中,预测控制通过建立系统模型,对未来输出进行预测,从而实现对系统的精确控制;模糊控制则利用模糊逻辑对系统进行控制,具有较强的鲁棒性;神经网络控制则通过模拟人脑神经网络的工作方式,实现对系统的自适应控制。
这些方法在加热水箱大滞后系统的控制中均有应用,但各有优缺点。
四、基于PLC的控制算法实现本文提出一种基于PLC的预测控制算法,实现对加热水箱大滞后系统的精确控制。
该算法通过建立系统的数学模型,预测未来一段时间内的温度变化趋势,并根据预测结果调整加热功率,从而实现精确的温度控制。
在实现过程中,我们采用了PLC的编程语言进行算法编写和调试,确保了算法的可靠性和稳定性。
五、算法优化及实验结果分析为了进一步提高算法的控制精度和稳定性,我们采用了多种优化措施。
首先,我们对系统模型进行精确的辨识和优化,提高了模型的预测精度。
其次,我们引入了自适应调节机制,根据系统实际运行情况动态调整算法参数,以适应不同工况下的控制需求。
最后,我们采用了鲁棒性较强的模糊逻辑对算法进行优化,提高了算法的鲁棒性和抗干扰能力。
大林算法在MIMO大滞后控制系统中的设计研究

总第 2 5期 2 20 0 8年第 7期
计 算 机 与数 字 工 程
Com p t r& D i t ue gi Eng n e n al ie r g i
Vol3 _ 6 No. 7
4
大 林 算 法在 MI MO大 滞 后 控 制 系统 中 的设计 研 究
G () 一 一 一 一
一
一
一
一
G( )
( = ) r
( )
式 ( ) T 为 对 象 时 间 常数 , 1中 对 象 纯 延 迟 时 r为
间 , 了简 化设其 为采样 周期 的整数 倍 , r 7 为 即 =Ⅳ 1 ,
Ⅳ 为正整数 。
otus( MO)l g_a yt h v enit dcd i ligwt oip tw u u uf ai l ss m,h eut upt MI a el ss m aebe r ue .Smu ̄ n i t u oo t t lvr be yt r g e no hw n t p m i a e te sl r s
曹 立学
( 陕西理工学 院电气工程系 摘 要 汉中 7 30 ) 2 0 3
介绍大林算法 的设计思想及大林控 制器 的设计 方法 , 及在 多输人 多输 出( MO) MI 大滞后 系统 中的应用 。结
大林算法 大滞 后 系统 MI MO 仿 真
合 二输入二输 出多变量 系统进行仿 真验证 , 果表明大林控制器能够使其控制质量满足性能要求 , 结 具有较好的控制效果。
1 引 言
由于多变量控 制系统各输入输 出之 间存 在着耦
针 对 工业 生产 过程 中含 纯 滞后 的控 制 对 象 的 控制 算 法 , 有 良好 的控 制 效 果 。其设 计 思 想 是 : 图 具 如 1 算机 控制 系统 结构 框 图 , 计 根据 具 有滞 后 的被控
被调量大滞后性的pid调节

被调量大滞后性的pid调节
现在有个汽轮机的液位要通过一个放水调节阀进行pid控制。
用的是西门子自带的fb41模块,开始扫描周期是100ms,p值为2,积分5秒,观察程序上ao输出,非常缓慢。
0.00几的变化。
后来减少积分时间,直到为0时,只有比例,ao输出很快。
但现在被调量液位变化缓慢,一般50秒后才变化,只采用比例时,阀门不断给开度控制,直到全关或全开,这过程可能就几秒,而液位一直没变化,到后反应过来,可能变化就不对了。
怎么调
最佳答案
这个紧靠pid的调节还是不好弄,最好采用pid的闭环液位控制加pwm比例带,调节长周期物理量的闭环控制,效果超好。
易稳定,且波动小。
它的原理就是根据实际的流量,改变水阀的接通关断比。
以保证液位不变。
大纯滞后在对象控制方法应用研究

大纯滞后在对象控制方法应用研究摘要:针对一般工业过程中存在的大纯滞后问题,提出了一种克服大纯滞后的预测控制方法。
利用递推最小二乘法进行参数估计,获得对象的一阶简化模型,提出了一种Smith预估神经元控制器设计方法,再用构建的神经网络预测模型预测出未来相应时刻的系统输出,然后用该输出来调整当前时刻的控制量,从而达到预期的控制目的,仿真结果验证了该方法的有效性。
关键词:神经网络;预测控制;大纯滞后0 前言一般工业过程中都具有非线性大纯滞后的特点,特别是滞后较大(即额定滞后S/T>0.5)的系统,常规控制往往无能为力。
采用Smith控制是解决对象大纯滞后问题的有效方法,但它需要建立对象的精确的数学模型,而且鲁棒性和抗干扰能力较差,面向对象的神经元模型及其学习算法具有算法简单、适应性好等优点,但是对于大纯滞后过程,由于被控量的偏差不能及时反映控制量的变化影响了神经元的控制效果。
预测控制是上世纪70年代兴起的一种新控制算法,在工业上已被广泛应用,其主要思想是:在当前时刻,基于过程的动态模型预测未来一定时域内每个采样周期(或按一定间隔)的过程输出,即可以根据当前的输入预测未来多个时刻的输出,从而根据控制要求调整下一时刻的控制量,有利于对纯滞后系统的控制,将预测函数控制应用于大纯滞后温度控制系统,减少了稳态静差,但超调量偏大,要有一种具有自补偿功能的非线性预测反馈校正法,提高了系统的鲁棒性,但该方法限于纯滞后时间已知的情况下,对于纯滞后参数未知或者改变的情况未加讨论。
根据上述情况提出一种用神经网络辨识系统的滞后时间参数,用预测控制算法实现对大纯滞后对象的控制方法。
其中预测模型是用神经网络逼近被控的动态对象而建立的,从而无需知道系统的精确数学模型。
1 神经元模型及控制系统1.1神经元模型针对将神经网络直观套用于自动控制中存在的局限性,提出了一种面向控制的神经元模型它的输出u(t)可以表示为u(t)=K∑wi(t) xi(t) (1)式中:K>0,为神经元的比例系数;xi(t)为神经元的n个输入状态;wi(t)为相应于xi(t)的加权值;wi(t)由某种学习算法确定。
大滞后PID控制说明
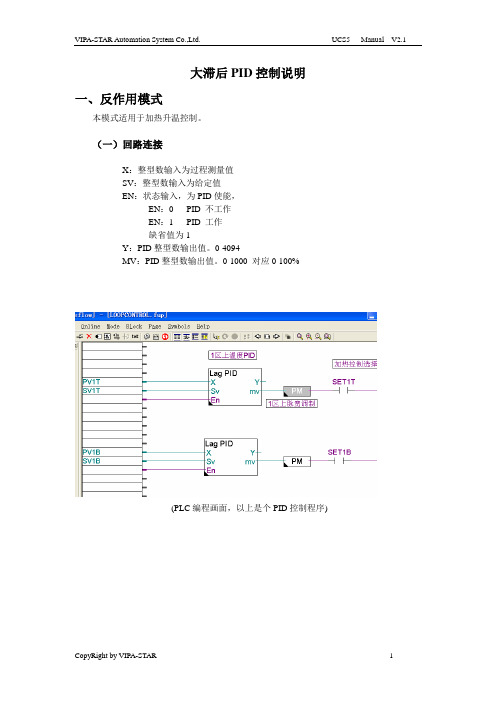
大滞后PID控制说明一、反作用模式本模式适用于加热升温控制。
(一)回路连接X:整型数输入为过程测量值SV:整型数输入为给定值EN:状态输入,为PID使能,EN:0 PID 不工作EN:1 PID 工作缺省值为1Y:PID整型数输出值。
0-4094MV:PID整型数输出值。
0-1000 对应0-100%(PLC编程画面,以上是个PID控制程序)(二)控制模式注:CS1、DS1、CS2、DS2为X1、X2、Y1、Y2区域分界,BS1、BS2、BS3、BS4为相应控制输出提前量动作说明:(1) 当测量温度在X1区域时,控制输出为100%,全功率加热。
(2) 当温度上升到X2区域时,控制输出为MV=100%-BS1,提前降热负荷。
(3) 当温度继续上升到PID 区域时,控制输出为PID 自动控制模式。
(4) 当温度继续上升,进入Y1区域时,控制输出为0%,停止加热。
(5) 当温度继续下降,进入PID 区域时,控制输出为PID 自动控制模式。
(6) 当温度继续下降,进入X1区域时,控制输出为100%,全功率加热。
测量值:X设定值:SV 精调下偏差:CS1 粗调下偏差:DS1精调上偏差:CS2 粗调上偏差:DS2时间输出值:100%输出(三)参数说明(四)举例说明3. 伟达科PID参数(5温区回流焊)4.1模拟量类基本的功能块对模拟量进行读,不需要更多的修改,模拟量数据以整型值表示:10位0-102312位0-4095所有UCS5模块数据以0-4095,以下是热电偶采集模拟量块双击UCS5.E37COM模块弹出如下窗口:以上窗口中CH0-CH9模块上道通,是滤波时间,可选择性的。
CH10通道是冷端补偿的,在硬件上只需要短接一下,测量出来是室温,在软件中是可调整的。
4.2模拟0-10V4-20MA输入模块如下图示:双击UCS5.E37块弹出如下窗口:CH0-CH10通道选择1:1信号为硬件模块的信号0-10V4-20MA。
PID+前馈控制在固井水泥车混浆系统等大滞后控制系统中的应用
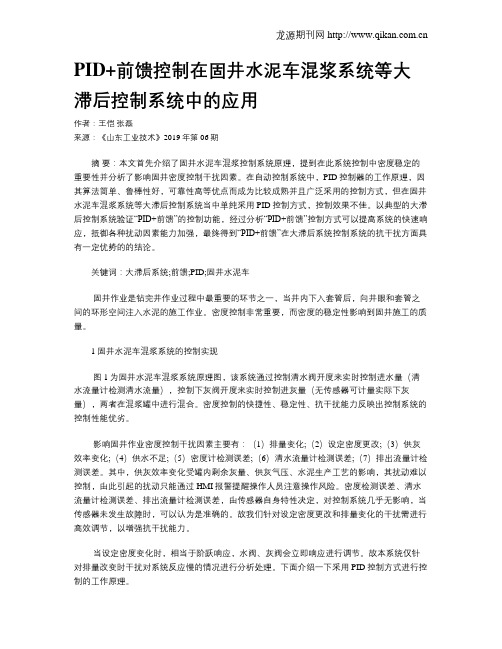
PID+前馈控制在固井水泥车混浆系统等大滞后控制系统中的应用作者:王恺张磊来源:《山东工业技术》2019年第06期摘要:本文首先介绍了固井水泥车混浆控制系统原理,提到在此系统控制中密度稳定的重要性并分析了影响固井密度控制干扰因素。
在自动控制系统中,PID控制器的工作原理,因其算法简单、鲁棒性好,可靠性高等优点而成为比较成熟并且广泛采用的控制方式,但在固井水泥车混浆系统等大滞后控制系统当中单纯采用PID控制方式,控制效果不佳。
以典型的大滞后控制系统验证“PID+前馈”的控制功能,经过分析“PID+前馈”控制方式可以提高系统的快速响应,抵御各种扰动因素能力加强,最终得到“PID+前馈”在大滞后系统控制系统的抗干扰方面具有一定优势的的结论。
关键词:大滞后系统;前馈;PID;固井水泥车固井作业是钻完井作业过程中最重要的环节之一,当井内下入套管后,向井眼和套管之间的环形空间注入水泥的施工作业。
密度控制非常重要,而密度的稳定性影响到固井施工的质量。
1 固井水泥车混浆系统的控制实现图1为固井水泥车混浆系统原理图,该系统通过控制清水阀开度来实时控制进水量(清水流量计检测清水流量),控制下灰阀开度来实时控制进灰量(无传感器可计量实际下灰量),两者在混浆罐中进行混合。
密度控制的快捷性、稳定性、抗干扰能力反映出控制系统的控制性能优劣。
影响固井作业密度控制干扰因素主要有:(1)排量变化;(2)设定密度更改;(3)供灰效率变化;(4)供水不足;(5)密度计检测误差;(6)清水流量计检测误差;(7)排出流量计检测误差。
其中,供灰效率变化受罐内剩余灰量、供灰气压、水泥生产工艺的影响,其扰动难以控制,由此引起的扰动只能通过HMI报警提醒操作人员注意操作风险。
密度检测误差、清水流量计检测误差、排出流量计检测误差,由传感器自身特性决定,对控制系统几乎无影响,当传感器未发生故障时,可以认为是准确的。
故我们针对设定密度更改和排量变化的干扰需进行高效调节,以增强抗干扰能力。
史密斯预估控制在大滞后过程控制系统中应用论文
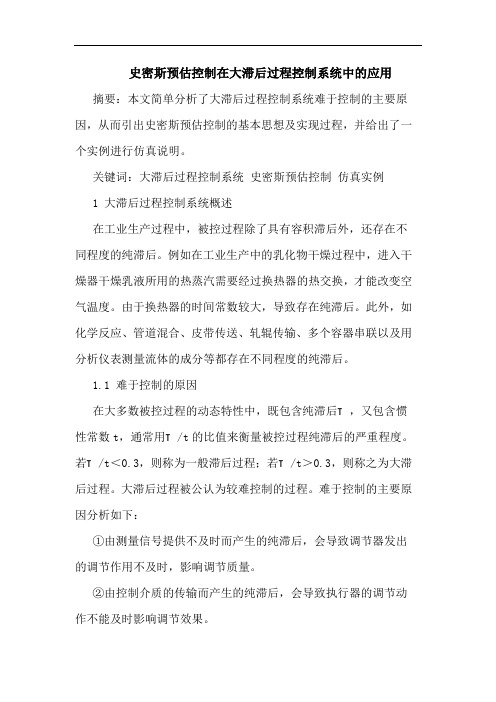
史密斯预估控制在大滞后过程控制系统中的应用摘要:本文简单分析了大滞后过程控制系统难于控制的主要原因,从而引出史密斯预估控制的基本思想及实现过程,并给出了一个实例进行仿真说明。
关键词:大滞后过程控制系统史密斯预估控制仿真实例1 大滞后过程控制系统概述在工业生产过程中,被控过程除了具有容积滞后外,还存在不同程度的纯滞后。
例如在工业生产中的乳化物干燥过程中,进入干燥器干燥乳液所用的热蒸汽需要经过换热器的热交换,才能改变空气温度。
由于换热器的时间常数较大,导致存在纯滞后。
此外,如化学反应、管道混合、皮带传送、轧辊传输、多个容器串联以及用分析仪表测量流体的成分等都存在不同程度的纯滞后。
1.1 难于控制的原因在大多数被控过程的动态特性中,既包含纯滞后τ,又包含惯性常数t,通常用τ/t的比值来衡量被控过程纯滞后的严重程度。
若τ/t<0.3,则称为一般滞后过程;若τ/t>0.3,则称之为大滞后过程。
大滞后过程被公认为较难控制的过程。
难于控制的主要原因分析如下:①由测量信号提供不及时而产生的纯滞后,会导致调节器发出的调节作用不及时,影响调节质量。
②由控制介质的传输而产生的纯滞后,会导致执行器的调节动作不能及时影响调节效果。
③纯滞后的存在使系统的开环相频特性的相角滞后随频率的增大而增大,从而使开环频率特性的中频段与(-1,j0)点的距离减小,结果导致闭环系统的稳定裕度下降。
若要保证其稳定裕度不变,只能减小调节器的放大系数,同样导致调节质量的下降。
2史密斯预估控制史密斯预估控制的基本思想是预先估计出被控过程的动态模型,然后设计一个预估控制器对其进行补偿,使滞后了τ时间的被控量提前反馈到调节器的输入端,使调节器提前动作,以减小超调和加速调节过程。
其控制系统框图如图1所示。
图1中,g0(s)是被控过程无纯滞后环节е-τs的传递函数;gs(s)是史密斯预估器的传递函数。
假设没有此预估器,则由调节器输出u(s)到被控量y(s)之间的传递函数为y(s)/u(s)= g0(s)е-τs (2-1)式(2-1)表明,受到调节器作用的被控量要经过纯滞后时间τ之后才能反馈到调节器的输入端,这就导致调节作用不及时。
- 1、下载文档前请自行甄别文档内容的完整性,平台不提供额外的编辑、内容补充、找答案等附加服务。
- 2、"仅部分预览"的文档,不可在线预览部分如存在完整性等问题,可反馈申请退款(可完整预览的文档不适用该条件!)。
- 3、如文档侵犯您的权益,请联系客服反馈,我们会尽快为您处理(人工客服工作时间:9:00-18:30)。
预估补偿:原理上能消除纯延时对控制系统的动态影响,但前提是具 有被控过程的精确模型,工程上往往难以实现。 采样控制:成本较低,但干扰加入的时刻对控制效果影响较大。 其他:大林算法、卡尔曼预估算法、灰色预测控制等。 一、改进型常规控制方案
核心思想:调一下,等一等,让控制动作慢一些,弱一些
K c (TI S 1)e s Y (S ) 微分先行 1 s X ( S ) TI SW0 ( S ) K c (TI S 1)(TD S 1)e
微分先行控制方案比PI+D控制系统闭环传递函数少了一个零点,所以 微分先行控制方案比PI+D控制方案超调量要小一些,提高了控制质量。
中间微分控制方案
只在动态过程中起调 节作用。
三种控制方案在设定值扰动下
过渡过程的比较见右图。
微分先行、中间反馈控制方案 简单易行,且对降低超调量有显著 的效果。
二、Simth预估补偿控制方案 1957年 史密斯(O.J.M.Smith)提出了一种以模型为基础的预估器补 偿控制方法。
设计思想: 预先估计出过程在基本扰动作用下的动态响应,然后由预估
器进行补偿,试图使被延时了τ 的被控量超前反馈到控制器,使控制器提前 动作,从而大大降低超调量,并加速调节过程。 Smith预估器补偿器控制原理图如下:
W0 ( S )
对于单回路大滞ห้องสมุดไป่ตู้系统:
Wd ( s ) Y (s) D( S ) 1 Wc ( s )W0 ( s )e s
Wc ( s )W0 ( s )e s Y ( s) X (S ) 1 Wc ( s )W0 ( s )e s
第二项含有滞后环节,只有在t>τ时产生控制作用,当t≤τ时无控制作用 ,所以SIMTH预估补偿控制对给定值的跟随效果比对干扰量扰动的抑制效果 好。
三、大滞后过程采样控制 其操作方法是;当被控过程受到扰动而使被控量偏离给定值时,即采样
一次被控量与给定值的偏差,发出一个操作信号,然后保持该操作(控制)信
号不变,保持的时间与纯滞后大小相等或大一些。经过时间τ后,由于操作 信号的改变,被控量必然有所反应,此时再按照被控量与给定值的偏差及变 化方向与速度值来进一步加以校正,校正后又保持其控制量不变,再等待一 个滞后时间τ。这样重复上述动作规律,一步一步的校正被控量的偏差值, 使系统趋向一个新的稳定状态。
微分先行控制方案
Kc (TI S 1)es Y (S ) 1 s X (S ) TI SW0 (S ) Kc (TI S 1)(TD S 1)e
Y (S ) TI Ses F (S ) TI SW01 (S ) Kc (TI S 1)(TD S 1)es
常规PI+D控制方案
Kc (TI S 1)(TD S 1)es Y (S ) 1 s X (S ) TI SW0 (S ) Kc (TI S 1)(TD S 1)e
Y (S ) TI Ses 1 s F (S ) TI SW0 (S ) Kc (TI S 1)(TD S 1)e
W0 ( S )
SIMTH预估控制的特点: 1、理论上SIMTH预估补偿控制能够克服大滞后的影响。但由于SIMTH
预估器需要知道被控过程精确数学模型,且对模型的误差十分敏感,因而难
于在工业生产过程中广泛应用。
Y ( s) 2、由于 D( S )
Wd ( s ) s W ( s )[ 1 W ( s ) e ] d 1 s Wc ( s )W0 ( s )e 1 1 (1 e s )Wc ( s )W0 ( s )
第四节 大滞后补偿控制系统
在许多工业生产过程中,例如:传送物料能量、测量成分量、皮带 运输、带钢连轧机,以及多容、多种设备串联等过程,都存在较大的纯时 延。
例:
大延时对象一般是指广义对象的时延与时间常数之比大于0.5。 控制系统中的大时延能导致系统的稳定性下降,甚至不稳定。
克服纯延时的几种常见方案
对比说明
由上面四个式子可见,微分先行控制方案和PID控制方案的特征方程
完全相同。但是从两个控制回路的闭环传递函数可以看出:
K c (TI S 1)(TD S 1)e s Y (S ) 常规PI+D 1 s X ( S ) TI SW0 ( S ) K c (TI S 1)(TD S 1)e
是不
W0 ( S )
Wc ( s )W0 ( s )e s 1 (1 e s )Wc ( s )W0 ( s ) Y ( s) Wc ( s )W0 ( s )e s X (S ) 1 1 (1 e s )Wc ( s )W0 ( s )
Wc ( s)W0 ( s) s e W1 ( s)e s 1 Wc ( s)W0 ( s)