姓名-精馏单元仿真操作实训报告
精馏系统实验报告
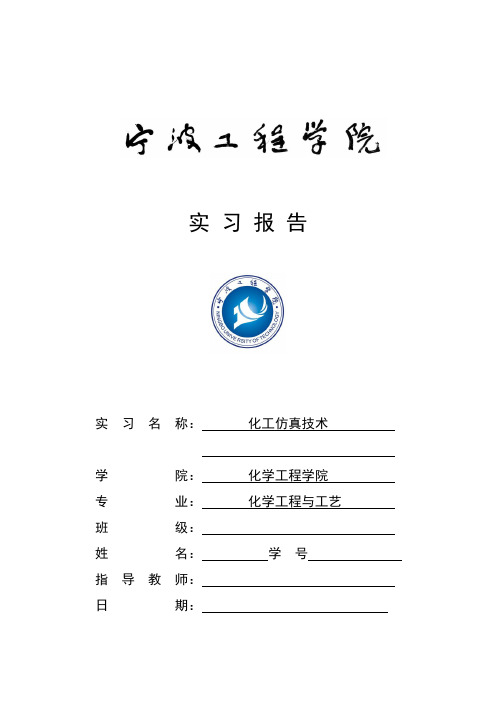
实习报告实习名称:化工仿真技术学院:化学工程学院专业:化学工程与工艺班级:姓名:学号指导教师:日期:第3章精馏系统一、实习目的化工仿真实习是我们大学学习计划的重要组成,解决了大学生的生产实习问题。
仿真实习使得我们不进工厂就能通过计算机得到开车、停车和事故处理操作的机会,使得我们能比较系统的学习生产过程的基本程序和具体操作方法,分析操作参数的合理性、设备及仪表是否运转正常,从而加强我们对基本理论的理解、基本方法的运用和基本技能的训练。
仿真教学有强调工业背景、适用面广、操作与控制界面先进、突出操作实践、内容由浅入深由简到繁、相互呼应、相互补充、附有大量思考题、实用性强、提倡新的教学方法等优点。
能从分发挥学生创造意识的环境。
可很好的将我们所学的理论知识和时间相结合,进一步巩固深化我们的专业知识和技能。
二、实习内容1、工艺流程简介脱丁烷塔是大型乙烯装置中的一部分。
本塔将来自脱丙烷塔釜的烃类混合物(主要有C4、C5、C6、C7等),根据其相对挥发度的不同,在精馏塔内分离为塔顶C4馏分,含少量C5馏分,塔釜主要为裂解汽油,即C5以上组分的其他馏分。
因此本塔相当于二元精馏。
工艺流程为:来自脱丙烷塔的釜液,压力为0.78MPa, 温度为65℃(由TI-1指示),经进料手操阀V1和进料流量控制FIC-1,从脱丁烷塔(DA-405)的第21块塔板进入(全塔共有40块板)。
在本塔提馏段第32块塔板处设有灵敏板温度检测及塔温调节器TIC-3(主调节器)与塔釜加热蒸汽流量调节器FIC-3(副调节器)构成的串级控制。
塔釜液位由LIC-1控制。
塔釜液一部分经LIC-1调节阀作为产品采出,采出流量由FI-4指示,一部分经再沸器(EA-405A/B)的管程汽化为蒸汽返回塔底,使轻组分上升。
再沸器采用低压蒸汽加热,釜温由TI-4指示。
设置两台再沸器的目的是釜液可能含烯烃,容易聚合堵管。
万一发生此种情况,便于切换。
再沸器A的加热蒸汽来自FIC-3所控制的0.35MPa低压蒸汽,通过入口阀V3进入壳程,凝液由阀V4排放。
精馏塔

精馏塔单元仿真实训报告班级:化工 (071)姓名:康华一、工艺流程说明1、工艺说明本流程是利用精馏方法,在脱丁烷塔中将丁烷从脱丙烷塔釜混合物中分离出来。
精馏是将液体混合物部分气化,利用其中各组分相对挥发度的不同,通过液相和气相间的质量传递来实现对混合物分离。
本装置中将脱丙烷塔釜混合物部分气化,由于丁烷的沸点较低,即其挥发度较高,故丁烷易于从液相中气化出来,再将气化的蒸汽冷凝,可得到丁烷组成高于原料的混合物,经过多次气化冷凝,即可达到分离混合物中丁烷的目的。
原料为67.8℃脱丙烷塔的釜液(主要有C4、C5、C6、C7等),由脱丁烷塔(DA-405)的第16块板进料(全塔共32块板),进料量由流量控制器FIC101控制。
灵敏板温度由调节器TC101通过调节再沸器加热蒸汽的流量,来控制提馏段灵敏板温度,从而控制丁烷的分离质量。
脱丁烷塔塔釜液(主要为C5以上馏分)一部分作为产品采出,一部分经再沸器(EA-418A、B)部分汽化为蒸汽从塔底上升。
塔釜的液位和塔釜产品采出量由LC101和FC102组成的串级控制器控制。
再沸器采用低压蒸汽加热。
塔釜蒸汽缓冲罐(FA-414)液位由液位控制器LC102调节底部采出量控制。
塔顶的上升蒸汽(C4馏分和少量C5馏分)经塔顶冷凝器(EA-419)全部冷凝成液体,该冷凝液靠位差流入回流罐(FA-408)。
塔顶压力PC102采用分程控制:在正常的压力波动下,通过调节塔顶冷凝器的冷却水量来调节压力,当压力超高时,压力报警系统发出报警信号,PC102调节塔顶至回流罐的排气量来控制塔顶压力调节气相出料。
操作压力 4.25atm (表压),高压控制器PC101将调节回流罐的气相排放量,来控制塔内压力稳定。
冷凝器以冷却水为载热体。
回流罐液位由液位控制器LC103调节塔顶产品采出量来维持恒定。
回流罐中的液体一部分作为塔顶产品送下一工序,另一部分液体由回流泵(GA-412A、B)送回塔顶做为回流,回流量由流量控制器FC104控制。
精馏装置操作实习报告

实习报告:精馏装置操作实习一、实习背景与目的随着我国化工产业的快速发展,精馏技术在石油、化工、医药等领域得到了广泛应用。
为了提高我国精馏技术的应用水平,培养具有实际操作能力的人才,我参加了为期两周的精馏装置操作实习。
本次实习旨在了解精馏装置的基本结构、掌握精馏过程的基本操作方法,提高分析问题和解决问题的能力,为今后的工作打下坚实基础。
二、实习内容与过程1. 实习前的准备在实习开始前,我们参加了安全教育培训班,学习了化工生产中的安全知识、事故预防及应急处理方法。
同时,我们还学习了精馏装置的基本原理、主要设备和操作流程。
2. 实习过程(1)了解精馏装置在导师的带领下,我们参观了精馏装置现场,了解了精馏塔、加热器、冷却器、泵等主要设备的作用和相互之间的关系。
(2)学习操作流程我们学习了精馏装置的操作流程,包括开车、正常运行、停车等环节。
在操作过程中,我们要严格遵循操作规程,确保设备安全、稳定运行。
(3)操作实践在导师的指导下,我们亲自操作精馏装置。
首先,我们进行了开车操作,包括开启电源、启动泵、调节温度等。
然后,我们进行了正常运行操作,包括调整回流比、控制塔顶和塔底温度等。
最后,我们进行了停车操作,包括关闭电源、停止泵、排放废液等。
(4)数据分析在操作过程中,我们定期采集样品,进行分析。
通过对比理论值和实际值,评估精馏效果,找出操作中存在的问题,并采取措施进行调整。
三、实习收获与反思1. 实习收获通过本次实习,我们掌握了精馏装置的基本操作方法,了解了精馏过程的原理。
同时,我们的团队合作能力、分析问题和解决问题的能力得到了提高。
2. 实习反思在实习过程中,我们认识到理论知识与实际操作的重要性。
只有掌握了扎实的理论知识,才能在实际操作中游刃有余。
此外,我们还意识到在操作过程中要严格遵守操作规程,确保生产安全。
四、总结通过本次精馏装置操作实习,我们对精馏工艺有了更深入的了解,操作技能得到了提升。
我们将以此为契机,继续努力学习,为将来从事相关工作打下坚实基础。
精馏实训实验报告

精馏实训实验报告
实验名称:精馏实训实验报告
实验目的:
通过对精馏实训实验的操作和分析,掌握精馏原理和工艺流程,加深对化工分离技术的理解和掌握,提高实验操作技能和实验报告撰写能力。
实验原理:
精馏是一种化学分离技术,基于液体的不同沸点而进行分离。
在精馏过程中,液体混合物被加热,使其产生汽化并进入冷凝器,被冷却成液态,进一步分离成纯液体。
实验步骤:
1. 将实验设备准备妥当,包括精馏塔、加热装置、冷却器等。
2. 准备洗涤瓶和试管,清洗干净后装入待分离的混合物样品。
3. 开始加热,通过不同气化温度和液态沸点,产生不同的沸点温度,使混合物中的组分分离。
4. 将冷却器中的液体收集起来,观察其纯度和色泽等特征。
实验结果:
通过实验,我们得到了两个不同混合物的分离产物。
通过实验后,我们发现其纯度较高、色泽明亮。
实验分析:
精馏是一种高效的化学分离技术,能够实现高纯度物质的分离,广泛应用于制药、化工、精细化工等领域。
实验结果表明,掌握精馏技术和流程对于提高化工实验能力和实践经验有重要作用。
实验结论:
精馏实训实验结果表明,通过掌握精馏技术和流程对于精细化工的研发和生产具有重要意义。
在实验操作和实验报告撰写方面,也有助于提高实验技能和综合能力。
双塔精馏单元仿真实训报告
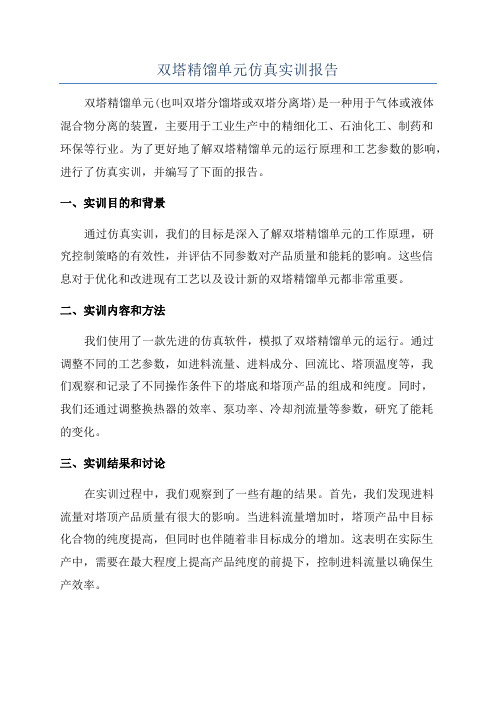
双塔精馏单元仿真实训报告双塔精馏单元(也叫双塔分馏塔或双塔分离塔)是一种用于气体或液体混合物分离的装置,主要用于工业生产中的精细化工、石油化工、制药和环保等行业。
为了更好地了解双塔精馏单元的运行原理和工艺参数的影响,进行了仿真实训,并编写了下面的报告。
一、实训目的和背景通过仿真实训,我们的目标是深入了解双塔精馏单元的工作原理,研究控制策略的有效性,并评估不同参数对产品质量和能耗的影响。
这些信息对于优化和改进现有工艺以及设计新的双塔精馏单元都非常重要。
二、实训内容和方法我们使用了一款先进的仿真软件,模拟了双塔精馏单元的运行。
通过调整不同的工艺参数,如进料流量、进料成分、回流比、塔顶温度等,我们观察和记录了不同操作条件下的塔底和塔顶产品的组成和纯度。
同时,我们还通过调整换热器的效率、泵功率、冷却剂流量等参数,研究了能耗的变化。
三、实训结果和讨论在实训过程中,我们观察到了一些有趣的结果。
首先,我们发现进料流量对塔顶产品质量有很大的影响。
当进料流量增加时,塔顶产品中目标化合物的纯度提高,但同时也伴随着非目标成分的增加。
这表明在实际生产中,需要在最大程度上提高产品纯度的前提下,控制进料流量以确保生产效率。
另外,我们还研究了回流比对分离效率的影响。
当回流比增加时,塔内的液相流动速度增加,分离效率提高。
然而,随着回流比的增加,能耗也显著增加。
因此,在实际操作中,需要找到一个平衡点,以尽可能提高分离效率,并保持合理的能耗水平。
四、结论和建议通过本次仿真实训,我们了解了双塔精馏单元的工作原理和关键参数对产品质量和能耗的影响。
根据实训结果,我们提出了一些建议和改进方案:1.控制进料流量:根据产品纯度和生产效率的要求,合理调整进料流量,以达到最佳性能。
2.优化回流比:找到回流比的平衡点,以提高分离效率和能耗的平衡。
3.定期维护和校准设备:确保换热器、泵和冷却剂等设备处于最佳工作状态,以保证系统性能的稳定和可靠。
另外,我们还注意到本次实训基于理想条件进行模拟,并未考虑到实际生产中的各种因素,如传热传质的限制、潜热和其他非理想性质。
实训报告总结化学精馏

#### 一、实训背景化学精馏作为化工生产中的一种重要单元操作,在石油、化工、医药等领域具有广泛的应用。
为了深入了解化学精馏的原理、过程及操作方法,我们进行了化学精馏实训。
通过本次实训,我们掌握了化学精馏的基本操作技能,加深了对化工生产过程的认知。
#### 二、实训目的1. 理解化学精馏的原理和过程;2. 掌握化学精馏设备的基本操作方法;3. 培养实际操作能力,提高安全意识;4. 增强团队协作能力,提高沟通协调能力。
#### 三、实训内容本次实训主要包括以下内容:1. 化学精馏原理及过程;2. 化学精馏设备介绍;3. 化学精馏操作步骤;4. 化学精馏异常处理及安全注意事项。
#### 四、实训过程1. 理论学习:首先,我们对化学精馏的原理、过程及设备进行了系统学习,了解了精馏的基本概念、操作原理、设备结构及操作方法。
2. 设备参观:随后,我们参观了实训现场,实地了解了精馏塔、冷凝器、再沸器等设备的结构及工作原理。
3. 操作实践:在理论学习和设备参观的基础上,我们开始进行化学精馏操作实践。
具体步骤如下:a. 检查设备状态,确保设备完好;b. 启动设备,进行冷态开车;c. 进料,调整塔内温度、压力等参数;d. 调整回流比,控制塔顶、塔底产品纯度;e. 观察设备运行情况,发现异常及时处理。
4. 异常处理:在实训过程中,我们遇到了一些异常情况,如塔内温度、压力波动等。
通过查阅资料和请教老师,我们学会了如何处理这些异常情况。
5. 总结与反思:实训结束后,我们对本次实训进行了总结和反思,分析了操作过程中存在的问题,并提出了改进措施。
#### 五、实训收获1. 理论知识的巩固:通过本次实训,我们对化学精馏的原理、过程及设备有了更深入的了解,为今后从事相关工作打下了坚实基础。
2. 实际操作能力的提高:在实训过程中,我们掌握了化学精馏的基本操作方法,提高了实际操作能力。
3. 安全意识的增强:通过实训,我们认识到化工生产过程中的安全重要性,增强了安全意识。
化工单元操作仿真实训总结
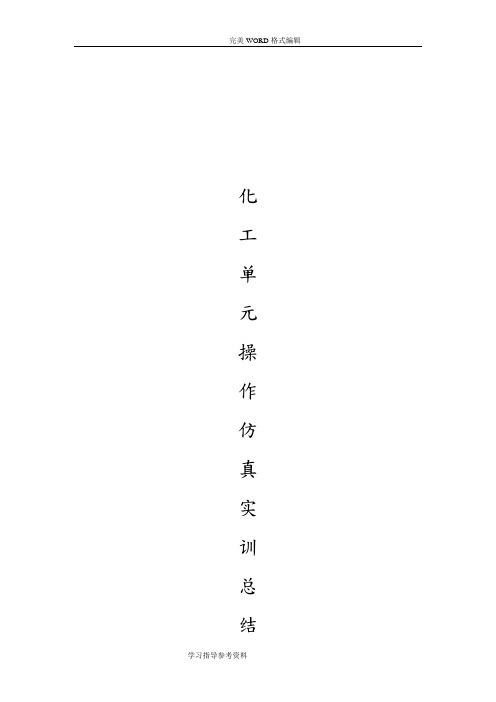
化工单元操作仿真实训总结姓名:XX班级;XX班学号:XXXX目录一、实训内容1、精馏塔仿真2、液位控制仿真3、吸收解吸仿真4、萃取仿真5、灌区仿真6、真空仿真二、仿真总结一、实训内容1、精馏塔仿真1.1操作原理:精馏原理精馏操作迫使混合物的气、液两相在精馏塔体中作逆向流动,在互相接触过程中,液相中的轻组分逐渐转入气相,而气相中的重组分则逐渐进入液相。
精馏过程本质上是一种传质过程,也伴随着传热。
在恒定压力下,对单组分液体在沸腾时继续加热,其温度保持不变。
但对于多组分的理想溶液来说,在恒定压力下,沸腾溶液的温度却是可变的。
一般而言,在恒定压力下,溶液气液相平衡与其组分有关。
高沸点组分的浓度越高,溶液平衡温度越高。
与纯物质的气液平衡相比较,溶液气液平衡的一个特点是:在平衡态下,气相浓度与液相浓度是不相同的。
一般情况下,气相中的低沸点组分的浓度高于它在液相中的数值.对于纯组分的气液相平衡,把恒定压力下的平衡温度称为该压力下的沸点或冷凝点。
但对于处在相平衡的溶液,则把平衡温度称为在该压力下某气相浓度的露点温度或对应的液相浓度的泡点温度。
对于同一气相和液相来说,露点温度与泡点一般是不相等的,前者比后者高。
1.2工艺流程:进料及排放不凝气启动再沸器建立回流调整至正常1.3仿真图:2、液位控制仿真2.1操作原理:缓冲罐V101仅一股来料,8Kg/cm2压力的液体通过调节产供阀FIC101向罐V101充液,此罐压力由调节阀PIC101分程控制,缓冲罐压力高于分程点(5.0Kg/cm2)时,PV101B自动打开泄压,压力低于分程点时,PV101B自动关闭,PV101A自动打开给罐充压,使V101压力控制在5Kg/cm2。
缓冲罐V101液位调节器LIC101和流量调节阀FIC102串级调节,一般液位正常控制在50%左右,自V101底抽出液体通过泵P101A或P101B(备用泵)打入罐V102,该泵出口压力一般控制在9Kg/cm2,FIC102流量正常控制在20000Kg/hr。
双塔精馏单元仿真实训报告

双塔精馏单元仿真实训报告实验目的:1.学习双塔精馏单元的基本原理和工作原理。
2.了解双塔精馏单元的操作过程和优化方法。
3.通过仿真实训,提高学生的实际操作能力和问题解决能力。
实验装置:我们使用了一套虚拟化工厂仿真软件,该软件可以模拟真实的化工装置和操作过程。
双塔精馏单元仿真装置由两个塔和一台加热炉组成。
其中,塔1为粗提塔,塔2为精提塔。
实验步骤:1.设定进料组分和流量,并开启加热炉,使进料加热到所需温度。
2.将加热后的进料引入粗提塔顶部,通过粗提塔内的塔盘进行分离。
塔盘上的液相会向下流动,与上升的蒸汽相进行传质传热,从而实现分离。
3.从粗提塔底部收集出塔床液相产物,以及从塔顶收集出的气相产物。
通过调整收集温度和流量,获取理想的产物组分。
4.将从塔顶收集出的气相产物引入精提塔,进行进一步分离。
精提塔的塔盘和粗提塔相似,但操作条件和设定略有不同。
5.最后,从精提塔底部收集出塔床液相产物和从塔顶收集出的气相产物。
根据实验要求,验证分离效果和产物组分。
实验结果:通过模拟实验,我们成功地实现了双塔精馏单元的分离过程。
在不同的操作条件下,我们获得了不同的产物组分。
通过对产物组分的分析,我们发现随着操作条件的改变,产物组分也发生变化。
在实验过程中,我们还发现了一些问题,如温度的控制、流量的调节等。
通过调整操作条件,我们解决了这些问题,并获得了较好的分离效果。
实验总结:通过该次仿真实训,我们深入了解了双塔精馏单元的原理和操作过程。
同时,我们也发现了一些需要改进的地方。
在以后的学习和实践中,我们将加强对于操作条件和工艺参数的掌握,以实现更好的分离效果。
另外,我们还发现了化工仿真实训的重要性和优势。
通过虚拟仿真实验,我们能够快速理解和掌握复杂的操作过程,大大提高了学习效率。
因此,我们将继续积极参与各类实训,以提升自己的实践能力和问题解决能力。
- 1、下载文档前请自行甄别文档内容的完整性,平台不提供额外的编辑、内容补充、找答案等附加服务。
- 2、"仅部分预览"的文档,不可在线预览部分如存在完整性等问题,可反馈申请退款(可完整预览的文档不适用该条件!)。
- 3、如文档侵犯您的权益,请联系客服反馈,我们会尽快为您处理(人工客服工作时间:9:00-18:30)。
《化工单元操作技术》仿真实训报告实训项目:精馏单元仿真操作班级:12化工301学号:报告人:王帅林操作成绩:报告成绩:1.精馏工作原理将液体混合物部分气化,利用其中各组分相对挥发度的不同,通过液相和气相间的质量传递来实现对混合物分离。
2. 工艺流程简介本流程是利用精馏方法,在脱丁烷塔中将丁烷从脱丙烷塔釜混合物中分离出来。
将脱丙烷塔釜混合物部分气化,由于丁烷的沸点较低,即其挥发度较高,故丁烷易于从液相中气化出来,再将气化的蒸汽冷凝,可得到丁烷组成高于原料的混合物,经过多次气化冷凝,即可达到分离混合物中丁烷的目的。
原料为67.8℃脱丙烷塔的釜液(主要有C4、C5、C6、C7等),由脱丁烷塔(DA-405)的第16块板进料(全塔共32块板),进料量由流量控制器FIC101控制。
灵敏板温度由调节器TC101通过调节再沸器加热蒸汽的流量,来控制提馏段灵敏板温度,从而控制丁烷的分离质量。
脱丁烷塔塔釜液(主要为C5以上馏分)一部分作为产品采出,一部分经再沸器(EA-418A、B)部分汽化为蒸汽从塔底上升。
塔釜的液位和塔釜产品采出量由LC101和FC102组成的串级控制器控制。
再沸器采用低压蒸汽加热。
塔釜蒸汽缓冲罐(FA-414)液位由液位控制器LC102调节底部采出量控制。
图1 列管换热器DCS流程图图2列管换热器现场图三、主要设备、调节器、各类仪表和阀件1.主要设备2.各类仪表四、实训步骤(一)冷态开车1.进料过程①开FA-408顶放空阀PC101排放不凝气,稍开FIC101调节阀(不超过20%),向精馏塔进料;②进料后,塔内温度略升,压力升高。
当压力PC101升至0.5atm时,关闭PC101调节阀投自动,并控制塔压不超过4.25atm(如果塔内压力大幅波动,改回手动调节稳定压力)。
2.启动再沸器①当压力PC101升至0.5atm时,打开冷凝水PC102调节阀至50%;塔压基本稳定在4.25atm后,可加大塔进料(FIC101开至50%左右);②待塔釜液位LC101升至20%以上时,开加热蒸汽入口阀V13,再稍开TC101调节阀,给再沸器缓慢加热,并调节TC101阀开度使塔釜液位LC101维持在40%-60%。
待FA-414液位LC102升至50%时,并投自动,设定值为50%。
3.建立回流随着塔进料增加和再沸器、冷凝器投用,塔压会有所升高。
回流罐逐渐积液。
①塔压升高时,通过开大PC102的输出,改变塔顶冷凝器冷却水量和旁路量来控制塔压稳定;②当回流罐液位LC103升至20%以上时,先开回流泵GA412A/B的入口阀V19,再启动泵,再开出口阀V17,启动回流泵;③通过FC104的阀开度控制回流量,维持回流罐液位不超高,同时逐渐关闭进料,全回流操作。
4.调整至正常①当各项操作指标趋近正常值时,打开进料阀FIC101;②逐步调整进料量FIC101至正常值;③通过TC101调节再沸器加热量使灵敏板温度TC101达到正常值;④逐步调整回流量FC104至正常值;⑤开FC103和FC102出料,注意塔釜、回流罐液位;⑥将各控制回路投自动,各参数稳定并与工艺设计值吻合后,投产品采出串级。
(二)正常停车操作1.降负荷①逐步关小FIC101调节阀,降低进料至正常进料量的70%;②在降负荷过程中,保持灵敏板温度TC101的稳定性和塔压PC102的稳定,使精馏塔分离出合格产品;③在降负荷过程中,尽量通过FC103排出回流罐中的液体产品,至回流罐液位LC104在20%左右;④在降负荷过程中,尽量通过FC102排出塔釜产品,使LC101降至30%左右。
2.停进料和再沸器在负荷降至正常的70%,且产品已大部采出后,停进料和再沸器。
①关FIC101调节阀,停精馏塔进料;②关TC101调节阀和V13或V16阀,停再沸器的加热蒸汽;③打开塔釜泄液阀V10,排不合格产品,并控制塔釜降低液位;④关FC102调节阀和FC103调节阀,停止产品采出;⑤手动打开LC102调节阀,对FA-114泄液。
3.停回流①停进料和再沸器后,回流罐中的液体全部通过回流泵打入塔,以降低塔内温度;②当回流罐液位至0时,关FC104调节阀,关泵出口阀V17(或V18),停泵GA412A(或GA412B),关入口阀V19(或V20),停回流;③开泄液阀V10排净塔内液体。
4.降压、降温①打开PC101调节阀,将塔压降至接近常压后,关PC101调节阀;②全塔温度降至50℃左右时,关塔顶冷凝器的冷却水(PC102的输出至0)。
(三)正常运行管理和事故处理操作1.正常操作2.事故处理1.热蒸汽压力过高原因:热蒸汽压力过高。
现象:加热蒸汽的流量增大,塔釜温度持续上升。
处理:适当减小TC101的阀门开度。
2.热蒸汽压力过低原因:热蒸汽压力过低。
现象:加热蒸汽的流量减小,塔釜温度持续下降。
处理:适当增大TC101的开度。
3.冷凝水中断原因:停冷凝水。
现象:塔顶温度上升,塔顶压力升高。
处理:(1)开回流罐放空阀PC101保压;(2)手动关闭FC101,停止进料;(3)手动关闭TC101,停加热蒸汽;(7)当回流罐液位为0时,关闭FIC104;(8)关闭回流泵出口阀V17/V18;(11)待塔釜液位为0时,关闭泄液阀V10;(12)待塔顶压力降为常压后,关闭冷凝器。
4.停电原因:停电。
现象:回流泵GA412A停止,回流中断。
处理:(1)手动开回流罐放空阀PC101泄压;(2)手动关加热蒸汽阀TC101;(3)开塔釜排液阀V10和回流罐泄液阀V23,排不合格产品;(4)手动打开LIC102,对FA114泄液;(5)当回流罐液位为0时,关闭V23;(6)关闭回流泵出口阀V17/V18(7)待塔顶压力降为常压后,关闭冷凝器。
(8)手动关进料阀FIC101;(9)手动关出料阀FC102和FC103;5.回流泵故障原因:回流泵GA-412A泵坏。
现象:GA-412A断电,回流中断,塔顶压力、温度上升。
处理:(1)开备用泵入口阀V20;(2)启动备用泵GA412B;(3)开备用泵出口阀V18;(4)关闭运行泵出口阀V17;(5)停运行泵GA412A;(6)关闭运行泵入口阀V19。
6.回流控制阀FC104阀卡原因:回流控制阀FC104阀卡。
现象:回流量减小,塔顶温度上升,压力增大。
处理:打开旁路阀V14,保持回流。
7.低压蒸汽停原因:停蒸汽。
现象:灵敏板温度、塔釜温度下降。
处理:(1)手动开回流罐放空阀PC101泄压;(2)手动关进料阀FIC101;(3)手动关出料阀FC102和FC103;(4)开塔釜排液阀V10和回流罐泄液阀V23,排不合格产品;(5)手动关加热蒸汽阀TC101;(6)手动打开LIC102,对FA114泄液;(7)当回流罐液位为0时,关闭V23;(8)关闭回流泵GA424A/GA424B;(9)关闭回流泵出口阀V17/V18;(10)关闭回流泵入口阀V19/V20;(11)待塔釜液位为0时,关闭泄液阀V10;(12)待塔顶压力降为常压后,关闭冷凝器。
8.塔釜出料调节阀FV102阀卡原因:塔釜出料调节阀FV102阀卡。
现象:塔釜产品无法采出。
处理:(1)将FC102关闭;(2)打开FC102的旁路阀V12,维持塔釜液位在50%。
9.再沸器严重结垢原因:再沸器严重结垢。
现象:塔釜温度降低。
处理:(1)打开备用再沸器EA408B蒸汽入口阀V16;(2)关闭再沸器EA408A蒸汽入口阀V13。
10.仪表风停原因:仪表风管线破裂。
现象:各调节阀、电磁阀不能有效运行。
处理:(1)打开FV101旁通阀V12;(2)打开TV101旁通阀V35;(3)打开LV102旁通阀V38;(4)打开FV102旁通阀V50;(5)打开PV102A旁通阀V15;(6)打开FV104旁通阀V14;(7)打开FV103旁通阀V11;(8)关闭气闭阀PV102A、PV101。
12.进料压力突然增大原因:进料量突然增加。
现象:塔的压力升高、温度降低。
处理:(1)将FIC101投自动;(2)调节FV101,使原料液进料达到正常值14056KG\H后投自动。
13.再沸器积水原因:FA414液位过高。
现象:再沸器出口温度降低,塔釜温度降低。
处理:(1)调节LV102,降低FA414的液位;(2)当灌FA414液位维持在50%左右,投自动,设定值为50%。
14.回流灌液位超高原因:FC103流量降低。
现象:回流灌液位超高。
处理:(1)将FC103设为手动模式,开大阀FV102;(2)打开备用泵GA412B前阀V20,开度50%;(3)启动备用泵GA412B;(4)打开备用泵GA412B后阀V18,开度50%;(5)将FC104设为手动模式;(6)当FA412B液位接近正常液位后,关闭泵GA412B后阀V18;(7)LC103稳定在50%后,FC103设为串级;(8)FC104Z最后稳定在14056KG/H后,将FC104设为自动,设定值为9664KG/H。
15.塔釜轻组分含量偏高原因:回流阀FV104流量高。
现象:塔釜轻组分含量偏高。
处理:(1)手动调节回流阀FV104;(2)当回流流量稳定在9664KG/H时,将FC104投自动,设定值为14056KG/H。
16.原料液进料调节阀卡原因:调节阀损坏。
现象:进料流量降低。
处理:(1)将FIC101设为手动模式;(2)关闭FIC101前截止阀V11;(3)关闭FIC101后止阀V31;(4)打开FIC101旁路阀V32,维持塔釜液位。
五、心得体会本流程是利用物质的沸点不同,把沸点低的先蒸馏出来,在设备运行的时候还要考虑设备的负荷,如果超负荷运行很有可能会发生一些必要的事故,在停车的时候应该先降负荷,然后在停止设备的运行,过程虽然繁琐单易于控制,同时在操作的同时要以严谨的太土来操作,这样减少一些不必要的损失。