409L不锈钢冶炼过程夹杂物特征及成因_付邦豪
304不锈钢中夹杂物的控制

304不锈钢中夹杂物的控制304不锈钢是一种广泛应用的奥氏体不锈钢,具有优良的耐腐蚀性和高温强度。
然而,夹杂物的存在可能会对其组织和性能产生不利影响。
因此,控制304不锈钢中的夹杂物对于保证其质量和性能具有重要意义。
本文将介绍夹杂物控制的重要性、夹杂物的来源和分类,以及夹杂物控制的措施和效果。
夹杂物是指存在于金属内部或表面的非金属杂质。
在304不锈钢中,夹杂物可能会破坏材料的连续性,导致应力集中,降低材料的耐腐蚀性和力学性能。
夹杂物对304不锈钢组织和性能的影响主要表现在以下几个方面:降低材料的耐腐蚀性:夹杂物能够破坏不锈钢表面的氧化膜,加速局部腐蚀,降低材料的耐腐蚀性。
降低材料的力学性能:夹杂物会破坏材料的连续性,导致应力集中,降低材料的强度和韧性。
影响材料的加工性能:夹杂物可能引起材料加工过程中的缺陷,如裂纹、折叠等,影响加工质量和精度。
夹杂物主要分为有意夹杂物和无意夹杂物。
有意夹杂物是人为添加的,如为了改善材料的某些性能而特意加入的合金元素。
无意夹杂物是在冶炼、加工过程中引入的,如炉渣、耐火材料、以及与炉气、熔剂、燃料等反应生成的产物。
为了控制304不锈钢中的夹杂物,可以采取以下措施:增加夹杂物球化处理:通过适当的热处理,使夹杂物呈球形颗粒分布,降低其对材料性能的不利影响。
控制原材料及熔炼过程:选用低杂质含量的原材料,严格控制熔炼工艺,避免过度氧化和污染。
精炼和净化处理:采用精炼技术,如电渣重熔、真空熔炼等,去除熔体中的夹杂物;同时,进行净化处理,如加入稀土元素细化晶粒,提高材料的纯净度。
合理安排工艺流程:在加工过程中合理安排工艺流程,避免过度变形和加热,以减少夹杂物的引入。
采取上述控制措施后,可以显著降低304不锈钢中的夹杂物数量和尺寸,改善材料的组织和性能。
具体效果如下:夹杂物形态:通过控制措施,可以使夹杂物呈球形或不规则形态分布,降低其对材料性能的不利影响。
夹杂物分布:采取控制措施后,夹杂物分布更加均匀,避免了局部浓度过高现象,降低材料脆性。
410S不锈钢冶炼过程全氧和夹杂物分析_王建新

作者简介:王建新(1969-),男,酒钢集团天风不锈钢有限公司,工程师,硕士,从事不锈钢炼钢工艺研究。
410S不锈钢冶炼过程全氧和夹杂物分析王建新,陈兴润,潘吉祥(酒钢集团天风不锈钢有限公司,甘肃嘉峪关735100)摘 要:对采用“铁水预处理→AOD→LF→CC”工艺路线生产410S铁素体不锈钢炼钢过程全氧和夹杂物进行了分析。
结果表明,随着AOD冶炼、LF精炼和连铸过程的进行,410S不锈钢钢水中全氧含量、夹杂物数量和夹杂物的尺寸呈逐渐减小的趋势。
AOD还原后、AOD脱硫后、LF精炼阶段和连铸中间包中夹杂物的类型主要为CaO-SiO2-MgO-Al2O3,但成分略有不同,各个阶段夹杂物的类型跟冶炼工艺有关。
在研究的基础上,提出了生产工艺的改进措施,有效改善了钢水中夹杂物水平,并大幅减少了冷轧产品表面缺陷的发生。
关键词:410S铁素体不锈钢;夹杂物;全氧含量中图分类号:TF764+.1 文献标识码:A 文章编号:1002-1043(2013)03-0032-04Analysis of the total oxygen content and inclusions in410S ferritic stainless steel during smelting processWANG Jian-xin,CHEN Xing-run,PAN Ji-xiang(Tianfeng Stainless Steel Co.,Ltd.,Jiuquan Iron and Steel Group Corporation,Jiayuguan 735100,China)Abstract:The total oxygen content and inclusions in 410S ferritic stainless steel pro-duced by the route of hot metal pretreatment→AOD→LF→CC were studied.The re-sults show that the total oxygen content,inclusions quantity and the inclusions size de-crease throughout the AOD→LF→CC process.The inclusions after the AOD reductionand are mainly CaO-SiO2-MgO-Al2O3compounds,while in LF refining and tundish.Ad-ditionally,the types of inclusions change at the different stage of the process.The vari-ation of the composition of the inclusions during the route of AOD→LF→CC are relatedto the smelting process.The technology improvement measures in manufacture havebeen accepted on the basis of the research.The inclusion level of the steel are improvedeffectively and significantly reduce the occurrence of surface defects of cold-rollingplates.Key words:410S ferritic stainless steel;inclusion;total oxygen content 410S不锈钢是目前应用最广的一种铁素体不锈钢,多用于厨房用具、建筑工业等领域,它具有成本低、导热系数高、线膨胀系数小等优点[1]。
浅谈铁基合金中的非金属夹杂物的产生原因及改善方法

浅谈铁基合金中的非金属夹杂物的产生原因及改善方法一、非金属夹杂物的产生原因1. 原料质量不高铁基合金生产过程中所使用的原料,如铁矿石、废钢、合金等,如果质量不高,其中便容易夹杂着一些氧化物、硫化物等非金属夹杂物。
这些非金属夹杂物会在合金的熔炼和冶炼过程中难以完全清除,最终残留在成品中。
2. 冶炼工艺不合理在铁基合金的冶炼过程中,如果温度、压力、气体流动等因素控制不当,就会导致非金属夹杂物的生成和残留。
在高温条件下,氧化物易于生成,并在熔体中产生。
如果冶炼过程中氧气、硫化氢等有害气体不能有效排除,也会导致非金属夹杂物的生成。
3. 设备磨损铁基合金冶炼设备的磨损、老化也是产生非金属夹杂物的重要原因。
设备的老化会导致设备表面产生氧化物,这些氧化物可能会脱落并夹杂在合金中。
二、改善方法1. 选择优质原料选用质量优良的原料是避免非金属夹杂物的重要手段。
采购者需对原料进行严格把关和筛选,确保原料中的有害夹杂物含量低,以减少对合金质量的不利影响。
2. 优化冶炼工艺优化冶炼工艺也是减少非金属夹杂物的重要方法。
合理控制冶炼过程中的温度、压力、气体流动等因素,以减少非金属夹杂物的生成和残留。
3. 定期维护设备定期维护和更换冶炼设备,能够有效减少设备磨损对合金质量的影响。
设备保养要及时,保证设备表面的清洁和光滑,减少氧化物的生成和残留。
4. 使用精炼剂在冶炼过程中使用精炼剂,能够有效地减少非金属夹杂物的生成和残留。
精炼剂在熔炼过程中能够吸附和分离非金属夹杂物,确保成品的质量。
三、总结在铁基合金的生产过程中,非金属夹杂物的产生是不可避免的。
通过选择优质原料、优化工艺、定期维护设备和使用精炼剂等方法,可以有效减少非金属夹杂物对合金质量的影响,提高铁基合金的品质和性能。
希望通过不断的研究和改进,能够进一步减少非金属夹杂物的生成,并提高铁基合金的质量和竞争力。
连铸坯夹杂物产生原因分析及改进

连铸坯夹杂物产生原因分析及改进连铸坯夹杂物是指在连铸过程中,坯料表面或内部存在的一些异物或杂质。
夹杂物的产生原因可以从原料、工艺和设备等方面来分析。
下面将就连铸坯夹杂物的产生原因进行分析,并提出改进措施。
一、原料方面的原因:1.1 原料中的杂质:连铸坯夹杂物可能是由于原料中掺杂了一些杂质。
这些杂质可能来自原料的边角料、废料或回收材料等。
这些杂质在冶炼过程中不容易完全溶解,从而在连铸过程中形成夹杂物。
改进措施:对原料进行严格的筛分、清洗和破碎处理,以减少原料中的杂质含量。
1.2 未完全熔化的原料:原料在冶炼过程中未能完全熔化,残余的固体颗粒在连铸过程中会形成夹杂物。
改进措施:加强炉内熔化过程的控制,提高熔化温度和熔化时间,保证原料能够完全熔化。
二、工艺方面的原因:2.1 不合理的浇注工艺:浇注工艺参数的不合理会影响连铸坯的质量。
浇注速度过快、注入速度不均匀、浇注过程中的气体无法及时排出等都会造成夹杂物的产生。
改进措施:合理调整浇注工艺参数,控制好浇注速度和注入速度,确保浇注过程中的气体能够顺利排出。
2.2 结晶过程中的扩散现象:连铸过程中,坯料在结晶过程中会产生一定的扩散现象,由于扩散速度不同,会导致夹杂物在坯料内部的分布不均匀。
改进措施:优化连铸过程中的结晶条件,控制好结晶速度和结晶温度,减小夹杂物的分布不均匀性。
三、设备方面的原因:3.1 保护气体的不足:连铸过程中使用的保护气体对坯料表面的氧化物有较好的隔离作用。
如果保护气体流量不足,氧化物无法及时有效地被逼出,就会形成夹杂物。
改进措施:增加保护气体的流量,确保保护气体能够充分覆盖整个铸造过程。
3.2 坯料包浇注系统的设计不合理:连铸坯夹杂物的产生还与坯料包浇注系统的设计有关。
如果坯料包浇注系统的设计不合理,容易导致夹杂物的形成。
改进措施:优化坯料包浇注系统的结构,确保坯料包内的流动状态稳定,防止夹杂物的产生。
连铸坯夹杂物的产生原因与原料、工艺和设备等方面都有关。
金属冶炼过程中的非金属夹杂物控制

扫描电镜(SEM)
总结词
扫描电镜是一种高分辨率的显微镜,能够观察金属材料表面和内部的微观结构,适用于非金属夹杂物的检测和表 征。
详细描述
扫描电镜利用电子束扫描金属材料的表面,通过收集和分析反射回来的电子信号,形成高分辨率的图像。该方法 能够观察夹杂物的形貌、大小、分布和成分等信息,具有较高的精度和分辨率。
对金属材料性能的影响
力学性能
非金属夹杂物会降低金属的力学性能,如强度、韧性、疲劳寿命等 。夹杂物的存在会导致应力集中,降低材料的抗拉强度和疲劳极限 。
物理性能
非金属夹杂物对金属的物理性能也有显著影响。例如,夹杂物会降 低金属的导电性、导热性和磁性等。
工艺性能
非金属夹杂物还会影响金属的加工性能,如焊接、热处理、塑性加工 等。夹杂物的存在可能导致焊缝开裂、热处理时组织不均匀等问题。
X射线衍射(XRD)
总结词
X射线衍射是一种用于分析金属材料 晶体结构和相组成的检测方法,可以 用于非金属夹杂物的鉴别和定量分析 。
详细描述
X射线衍射利用X射线照射金属材料, 通过分析衍射图谱来判断材料的晶体 结构和相组成。该方法能够鉴别夹杂 物的矿物组成和含量,具有较高的精 度和可靠性。
04
非金属夹杂物的控制技术与实践
金属冶炼过程中的非金属 夹杂物控制
汇报人:可编辑 2024-01-06
目录
• 非金属夹杂物的基本概述 • 非金属夹杂物的来源与控制策略 • 非金属夹杂物检测与表征技术 • 非金属夹杂物的控制技术与实践 • 非金属夹杂物控制的效果评估与优化建议 • 案例分析:某钢厂非金属夹杂物控制实践
01
非金属夹杂物的基本概述
定期检查熔炼炉内衬,确保其完 好无损,防止剥落物混入金属溶 液。
炼钢过程中气体和夹杂物的冶金控制
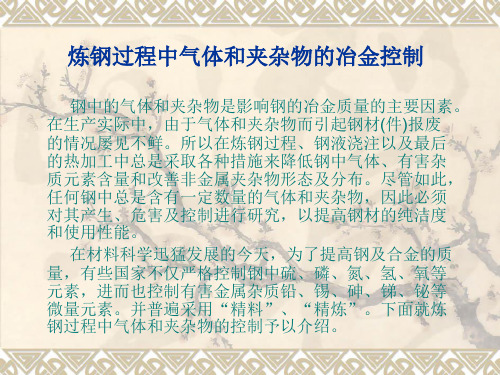
白点主要见于大中型锻件或钢坯。这 些钢件的尺寸愈大,对白点的敏感性也 愈大。把对白点敏感性大的钢锻轧成小 截面的型材及锻件时,很少发现白点。 例如在截面有效厚度小于50mm的钢中 一般不出现白点。 钢件在锻轧后的冷却速度对白点的产 生也起着重要的作用。对白点有敏感性 的钢锻轧后,以较快速度冷却则最易使 白点形成。
研究认为,钢的氢脆倾向除与形变速度、工 作温度及钢的强度水平有关外,还受下列因 素的影响: (1)钢中氢浓度 随着钢中氢浓度的增加,钢 的塑性降低或发生脆断所需时间减少。 (2)钢中微量有害元素 铁素体钢、马氏体钢 中的硫、磷在氢的共同作用下,使钢的脆 性更加明显。此外,Sb, Sn, As, Bi等有害微量 元素也会促进氢脆断裂。
2)采用钢包吹氢脱氢工艺对钢液进行 处理。
三、钢中氮的行为及去除 氮在钢中的作用并不像氢那样完全无 益,因为对于某些钢(例如奥氏体不锈钢) 来讲,氮可以作为合金元素提高钢在某 些方面的性能。尽管如此,由于氮是强 烈提高钢冷脆性的一个元素。所以对钢 中的氮也必须给予足够的重视。
(一)钢中氮的来源 钢中的氮主要来源于炼钢过程中的炉气和金 属原料(如含Cr, V, Al, Ti较高的废钢和铁合金)。 目前主要采用的炼钢方法中,以氧气转炉炼钢 法生产的钢材氮的质量分数最低,所以使用的 氧气越纯净,钢液中氮就越少。例如要使钢中 氮的质量分数小于0.003%,则氧气纯度必须大 于99%。而电沪冶炼的钢材一般含氮都较高, 因为高温电弧不但使炉气和原料中的氮分子易 于分解,而且也容易被熔池吸附。
从上式中可看出,当炉气中水的蒸汽压 PH2O增大时,ωH必定增大;而当ωO高时,不利 于水蒸气的分解。因此,在炼钢末期和电弧炉 炼钢的还原期,钢液最易于从炉气中吸氢。 此外,钢中含氢量与钢的冶炼方法、钢种成分 也有关系。在三种主要炼钢方法(碱性平炉、碱 性电弧炉、氧气顶吹转炉)中,电弧炉钢中的氢 含量最高,这主要是因为电弧区的高温(高于 3000℃ )使炉气中的水蒸气易于分解且被钢液 吸收。而氧气顶吹转炉使用工业纯氧进行吹炼, 炉气中水蒸气分压低,加之其熔池脱碳反应激 烈,故使钢中氢含量最低。
硫化锰夹杂物形成的原因

硫化锰夹杂物形成的原因
硫化锰夹杂物形成的原因主要与钢中的Mn和S元素有关。
在钢的熔炼、浇铸和钢材的制造过程中,Mn和S元素可能会通过原料和熔炼工艺引入钢中。
由于Mn和S元素具有很好的亲和性,它们在钢中往往会形成硫化锰夹杂物。
这些夹杂物通常以球形、条形和片状等形态出现,分布于钢中的晶界和内部,直接影响着钢的强度和韧性。
硫化锰夹杂物的析出与众多因素有关,包括钢的化学成分、熔炼工艺、热处理工艺以及冷却方式等。
为了控制硫化锰夹杂物的形成,需要严格控制工艺和操作,并找到提高钢材质量的对策。
以上内容仅供参考,如需更全面准确的信息,可查阅相关的钢铁冶炼和材料科学文献或咨询该领域的专家。
连铸坯夹杂物产生原因分析及改进

连铸坯夹杂物产生原因分析及改进连铸坯夹杂物的产生原因可以从多个方面进行分析和改进。
下面是一个大致的分析和改进措施,供您参考。
1. 原料质量问题:连铸坯夹杂物主要来自于熔化的金属和废钢原料,在回炉炉中的熔化过程中,可能会夹杂一些金属碎屑、渣滓和氧化物等杂质。
2. 冶炼工艺问题:连铸坯夹杂物的产生也与冶炼过程中的工艺参数有关。
冶炼温度不稳定、浇注速度过快或过慢、浇注过程中的氧气和杂质溶解等都可能导致夹杂物的产生。
3. 连铸机设备问题:连铸机的状态和性能也可能对夹杂物产生产生影响。
结晶器内部的损坏、结晶器震动不稳定、传动系统不正常等问题都可能导致夹杂物产生。
二、改进措施1. 提高原料质量:采用优质原料,并加强原料筛查和预处理,规范原料质量的控制。
可以采用一些物理和化学方法对废钢进行预处理,如磁选、浮选、热处理等,以减少夹杂物的含量。
2. 优化冶炼工艺:通过调整冶炼工艺参数,控制冶炼温度稳定性,避免过高或过低的温度对金属液中的杂质产生不良影响。
3. 改进连铸机设备:加强设备的维护保养,及时发现和修复连铸机设备的问题,确保连铸过程的稳定性和可靠性。
可以对结晶器进行优化设计,改进震动稳定性和结晶器内部布置,以减少夹杂物的产生。
4. 强化质量控制:加强连铸工艺过程的监测和控制,通过合理的浇注速度、浇注方式和辅助工具,减少夹杂物的产生。
建立完善的质量控制体系,追踪和分析夹杂物的来源和产生规律,以便更好地进行改进和控制。
5. 加强人员培训:提高工人的操作技能,加强工艺和设备知识的培训,使其能够熟练应对连铸过程中可能出现的问题,并及时采取正确的措施进行解决。
- 1、下载文档前请自行甄别文档内容的完整性,平台不提供额外的编辑、内容补充、找答案等附加服务。
- 2、"仅部分预览"的文档,不可在线预览部分如存在完整性等问题,可反馈申请退款(可完整预览的文档不适用该条件!)。
- 3、如文档侵犯您的权益,请联系客服反馈,我们会尽快为您处理(人工客服工作时间:9:00-18:30)。
第46卷 第6期 2011年6月钢铁Iron and Steel Vo l .46,N o .6June 2011409L 不锈钢冶炼过程夹杂物特征及成因付邦豪1, 侯海滨1, 成国光1, 潘吉祥2, 李 岩2, 潘 伟2(1.北京科技大学冶金与生态工程学院,北京100083; 2.酒泉钢铁集团公司,甘肃嘉峪关735100)摘 要:对409L 不锈钢A OD -LF -CC 冶炼过程的不同阶段取钢样,利用扫描电镜和能谱仪研究了钢液中夹杂物的类型,并分析了夹杂物的形成原因。
结果表明:A O D 钢液中夹杂物主要为CaO -SiO 2-A l 2O 3-M gO ;LF 中夹杂物主要为M gO -A l 2O 3-T iO x ;中间包中夹杂物主要为M gO -A l 2O 3-TiO x 和T iN 。
关键词:409L 不锈钢;夹杂物;特征;成因文献标志码:A 文章编号:0449-749X (2011)06-0040-05Characteristics and Origin of Inclusions in 409LStainless Steel During AOD -LF -CC ProcessFU Bang -hao 1, H OU H ai -bin 1, CH ENG Guo -guang 1,PAN Ji -xiang 2, LI Yan 2, PAN Wei 2(1.Schoo l o f M etallurgical and Eco log ical Enginee ring ,U niver sity o f Science and T echno lo gy Beijing ,Beijing 100083,China ; 2.Jiuquan Ir on and Steel Co .,Jiay ug ua n 735100,G ansu ,China )A bstract :T he inclusions in the steel samples taken at different stages of A OD -LF -CC pro cess during 409L stainless steelmaking and casting w ere observed by a scanning electro n mic roscope w ith an EDS X -ray analy zer .T he types o f inclusions f rom diffe rent stag es o f the pro ce ss we re analyzed and identified .T he inclusions in AO D we re mainly CaO -SiO 2-A l 2O 3-M gO compounds ,w hile in LF ,it was detected mainly M gO -A l 2O 3-T iO x inclusio ns .Both M gO -Al 2O 3-T iO x and T iN inclusio ns w ere found in tundish .T he o rigin of the inclusions fo rmed at diffe rent stage s was al -so discussed .Key words :409L stainless steel ;inclusio n ;char acte ristic ;origin作者简介:付邦豪(1985—),男,硕士生; E -mail :fu -bang hao @qq .com ; 收稿日期:2010-08-18 409L 不锈钢是一种钛稳定化铁素体不锈钢。
由于钢中含钛,提高了钢的高温耐蚀性、加工性及焊接性等性能,被广泛用于汽车排气系统及耐高温设备。
但是,Ti 的添加也给409L 不锈钢的冶炼及成品质量带来了一些不利影响,如浇铸过程中易发生水口结瘤、连铸坯表面缺陷等问题,产生这些问题的主要原因与钢中存在较多夹杂物有关[1-2]。
因此,搞清409L 不锈钢冶炼过程夹杂物的类型和形成原因,对于控制夹杂物类型、解决连铸水口结瘤及提高产品质量都有重要的指导意义。
1 冶炼条件和研究方法某钢厂409L 不锈钢采用AOD -LF -CC 冶炼工艺:首先将铁水和高碳铬铁在AOD 炉中进行吹氧精炼,然后转入LF 炉进行精炼和钛合金化操作,当钢液成分和温度达到要求后,将钢液运至连铸平台进行浇铸。
在冶炼过程中,分别在AOD 结束、LF 结束及中间包浇铸末期取钢样和渣样。
对所取钢样和渣样分别进行化学成分分析,并对钢样进行夹杂物的检测与分析。
分析方法如下所示。
1)夹杂物检测:将钢样切割、研磨、抛光,制成金相样。
首先在金相显微镜下观察夹杂物,然后通过扫描电镜及X 射线能谱仪对夹杂物进行形貌观察,并分析夹杂物的成分。
2)化学成分分析:将钢样和渣样送至国家钢铁材料测试中心,进行化学成分分析。
2 结果及分析2.1 钢液化学成分钢液化学成分如表1所示。
2.2 夹杂物分析2.2.1 夹杂物的类型及特征409L 不锈钢冶炼各阶段,典型夹杂物形貌及成分如图1~3所示。
从图中可以看出,在不同冶炼阶段,钢液中夹杂物的类型具有各自不同的特征。
第6期付邦豪等:409L 不锈钢冶炼过程夹杂物特征及成因表1 不同阶段钢液化学成分(质量分数)Table 1 Chemical co mposition of molten steel at different stages%项目C Si M n P S Ni Cr Al Ti N T .O AOD 0.0110.2400.3110.0200.00100.09811.50.004-0.00390.0051LF 0.0170.4360.3160.0210.00090.09011.40.0110.310.01010.0049中间包0.0190.4480.3160.0210.00080.09411.40.0090.270.01180.0023 AOD 冶炼末期夹杂物主要为CaO -SiO 2-Al 2O 3-M gO 系球形夹杂,所发现的夹杂物尺寸为10~30μm ,夹杂物的典型形貌如图1所示。
这类夹杂物在钢液中以液态形式存在,由于受到表面张力的作用而呈现为球形。
图4所示为夹杂物的平均成分及AOD 终渣成分,可以看出,夹杂物成分与AOD 终渣成分非常接近。
LF 中夹杂物主要为M gO -A l 2O 3-TiO x 系夹杂,所发现的夹杂物尺寸均在10μm 以下,如图2所示,没有发现单独存在的M gO -A l 2O 3夹杂物。
此外,LF 中没有发现AOD 中的CaO -SiO 2-Al 2O 3-M gO 系夹杂,由此推知,AOD 钢液中残存的CaO -·41·钢 铁第46卷图4 A OD 末期夹杂物及炉渣成分Fig .4 Chemical co mposition of inclusions andslag at the f inal stage of AOD processSiO 2-Al 2O 3-M gO 系夹杂在LF 中经碰撞、聚集、上浮,被排出了钢液。
这说明,钢包精炼处理对AOD中残留的较大颗粒夹杂物的去除是十分有利的。
从图2(b )、(c )可以看出,M gO -Al 2O 3-TiO x 夹杂物之间也存在凝聚现象。
LF 中夹杂物的平均成分如图5所示。
图5中a 、b 成分点分别对应图2(a )、(b ),即:图2(a )所示夹杂物的主要成分为TiO x ;图2(b )所示夹杂物的主要成分为M gO -Al 2O 3。
从M gO -Al 2O 3-TiO x 三元系相图[3]可知,LF 中夹杂物为固-液两相混合物:(a )为固相TiO x +液相Mg O -Al 2O 3-TiO x ;(b )为Mg O ·Al 2O 3尖晶石+液相M gO -Al 2O 3-TiO x 。
关于TiO x 的存在形式,Ono 等人[4]在研究钢液Ti -Mg -Al 复合脱氧时发现,夹杂物中TiO x 以Ti 2O 3+TiO 2形式共存。
Park 等[3]也证实,M gO -A l 2O 3-TiO x 夹杂物中TiO x 以Ti 3+和Ti 4+两种形式存在,但主要成分为Ti 2O 3。
在另一份研究中,Park 和他图5 LF 末期夹杂物成分Fig .5 Average composition of inclusions atthe final stage of LF process的同事Pak 等人[5]指出,当钛的质量分数大于0.25时,钢液中稳定存在的含钛氧化物为Ti 2O 3。
因此认为,409L 不锈钢LF 中夹杂物的组成主要为MgO ·Al 2O 3、液态MgO -Al 2O 3-TiO x 及固态Ti 2O 3。
中间包钢液中的夹杂物有3种不同的类型:M gO -A l 2O 3-TiO x 系夹杂、含芯的TiN 夹杂和纯TiN 夹杂。
其中,含芯的TiN 夹杂存在2种类型:以M gO -Al 2O 3-TiO x 为核心的TiN (如图3(b ))和以TiO x 为核心的TiN (如图3(c ))。
中间包钢液中所发现的夹杂物尺寸均在10μm 以下,夹杂物的典型形貌如图3所示。
2.2.2 夹杂物成因分析1)CaO -SiO 2-A l 2O 3-M gO 系夹杂物。
此类夹杂物仅出现在AOD 钢液中。
AOD 冶炼前期钢液吹氧脱碳,会有相当数量的Cr 被氧化进入炉渣,因此冶炼后期需对炉渣进行还原操作,还要对钢液进行脱氧、脱硫。
一般采用FeSi 对钢液脱氧。
通常,所用的FeSi 会含有一定数量的杂质元素,如Ca 、Al 等,这些杂质元素的存在,会对夹杂物的成分产生一定的影响[6]。
当采用含有Ca 、Al 的FeSi 脱氧时,Si 、Ca 和Al 均可与氧结合,从而生成CaO -SiO 2-Al 2O 3夹杂。
而Ca 和Al 又可将炉渣或耐材中的M gO 还原,生成的Mg 进入钢液:3(MgO )+2[Al ]=(Al 2O 3)+3[M g ](1)(M gO )+[Ca ]=(CaO )+[M g ](2)钢液中的Mg 与CaO -SiO 2-Al 2O 3反应,使得夹杂物的最终成分为CaO -SiO 2-Al 2O 3-Mg O 。
此外,由于炉渣和钢液界面的相互作用,炉渣组元会分解而向钢液供Al 、Ca 、M g ;炉渣与钢液的强烈搅拌,会使渣滴卷入钢液,这些都为CaO -SiO 2-Al 2O 3-M gO 夹杂的产生创造了条件。