小型PLC在电加热热处理炉改造中的应用(王胜利)
基于PLC的锅炉电加热控制系统设计

基于PLC的锅炉电加热控制系统设计摘要本文针对锅炉电加热控制系统的实际需求,基于PLC,设计了一种可靠的电加热控制系统。
该系统通过PLC的控制,实现了对电加热器的开启、关闭、电流的调节等功能。
同时,系统还通过人机界面进行了参数设置和异常报警等功能。
实验结果表明,该系统具有高可靠性、稳定性,能够满足锅炉电加热的实际需求。
关键词:PLC、锅炉、电加热、控制系统一、引言锅炉是工业生产中常用的一种设备,其主要作用是将水加热为蒸汽,并通过蒸汽驱动液体或气体来完成工业生产流程。
而锅炉的加热方式一般有煤、油、气、电等多种方式,其中电加热由于其无污染、易控制等优点,被广泛应用于各种工业生产环节中。
然而,锅炉电加热控制系统的设计存在一些问题,如控制精度低、容易出现故障等。
这些问题给锅炉电加热操作带来了很大的不便,因此,需要设计一种基于PLC的锅炉电加热控制系统,以提高其可靠性和稳定性。
二、设计思路和方法1.设计思路基于以上问题,本文设计了一种基于PLC的锅炉电加热控制系统。
该系统采用西门子S7-200 PLC作为主控制器,通过PLC与电加热装置进行连接,实现对电加热装置的开关控制和电流调节。
同时,本文还设计了人机界面,以便进行参数设置和异常报警等功能。
通过该系统,可以实现对电加热的精确控制,从而提高锅炉的加热效率和生产稳定性。
2.设计方法(1)硬件部分设计系统硬件包含主要的PLC、电加热器、人机界面等几个部分。
PLC:采用西门子S7-200 PLC作为主控制器,通过该控制器,实现对电加热设备的精确控制。
电加热器:采用模块化的电加热器,可以根据实际需求进行扩展和修改。
人机界面:设计了触摸屏人机界面,以便进行电加热控制和参数设置等功能。
(2)软件部分设计软件部分主要包含PLC程序和人机界面程序两部分。
PLC程序:由于锅炉电加热主要是控制电加热的开关和电流调节,因此,PLC程序中主要包含电加热开关控制、电流调节等基本功能。
基于PLC的加热反应炉电气控制系统的设计
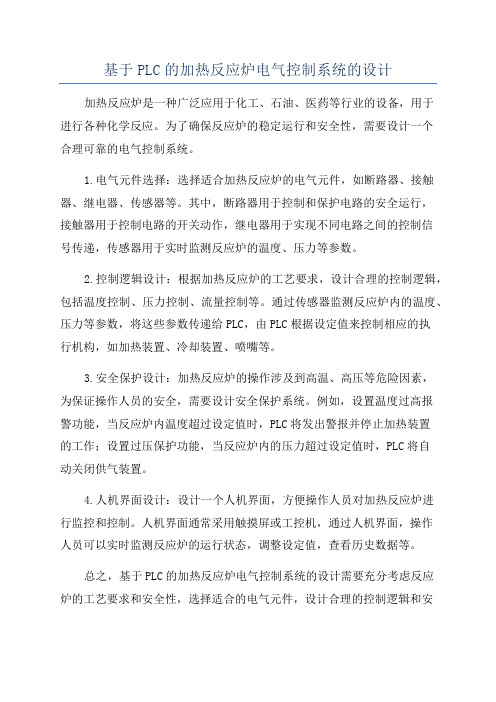
基于PLC的加热反应炉电气控制系统的设计加热反应炉是一种广泛应用于化工、石油、医药等行业的设备,用于进行各种化学反应。
为了确保反应炉的稳定运行和安全性,需要设计一个合理可靠的电气控制系统。
1.电气元件选择:选择适合加热反应炉的电气元件,如断路器、接触器、继电器、传感器等。
其中,断路器用于控制和保护电路的安全运行,接触器用于控制电路的开关动作,继电器用于实现不同电路之间的控制信号传递,传感器用于实时监测反应炉的温度、压力等参数。
2.控制逻辑设计:根据加热反应炉的工艺要求,设计合理的控制逻辑,包括温度控制、压力控制、流量控制等。
通过传感器监测反应炉内的温度、压力等参数,将这些参数传递给PLC,由PLC根据设定值来控制相应的执行机构,如加热装置、冷却装置、喷嘴等。
3.安全保护设计:加热反应炉的操作涉及到高温、高压等危险因素,为保证操作人员的安全,需要设计安全保护系统。
例如,设置温度过高报警功能,当反应炉内温度超过设定值时,PLC将发出警报并停止加热装置的工作;设置过压保护功能,当反应炉内的压力超过设定值时,PLC将自动关闭供气装置。
4.人机界面设计:设计一个人机界面,方便操作人员对加热反应炉进行监控和控制。
人机界面通常采用触摸屏或工控机,通过人机界面,操作人员可以实时监测反应炉的运行状态,调整设定值,查看历史数据等。
总之,基于PLC的加热反应炉电气控制系统的设计需要充分考虑反应炉的工艺要求和安全性,选择适合的电气元件,设计合理的控制逻辑和安全保护功能,并提供简单易用的人机界面。
只有设计合理的电气控制系统,才能保证加热反应炉的稳定运行和安全性。
PLC在中频无芯感应电炉中的应用
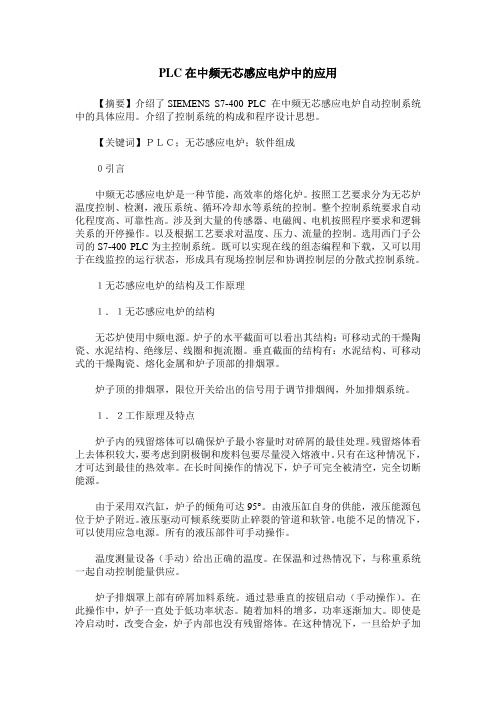
PLC在中频无芯感应电炉中的应用【摘要】介绍了SIEMENS S7-400 PLC 在中频无芯感应电炉自动控制系统中的具体应用。
介绍了控制系统的构成和程序设计思想。
【关键词】PLC;无芯感应电炉;软件组成0引言中频无芯感应电炉是一种节能,高效率的熔化炉。
按照工艺要求分为无芯炉温度控制、检测,液压系统、循环冷却水等系统的控制。
整个控制系统要求自动化程度高、可靠性高。
涉及到大量的传感器、电磁阀、电机按照程序要求和逻辑关系的开停操作。
以及根据工艺要求对温度、压力、流量的控制。
选用西门子公司的S7-400 PLC为主控制系统。
既可以实现在线的组态编程和下载,又可以用于在线监控的运行状态,形成具有现场控制层和协调控制层的分散式控制系统。
1无芯感应电炉的结构及工作原理1.1无芯感应电炉的结构无芯炉使用中频电源。
炉子的水平截面可以看出其结构:可移动式的干燥陶瓷、水泥结构、绝缘层、线圈和扼流圈。
垂直截面的结构有:水泥结构、可移动式的干燥陶瓷、熔化金属和炉子顶部的排烟罩。
炉子顶的排烟罩,限位开关给出的信号用于调节排烟阀,外加排烟系统。
1.2工作原理及特点炉子内的残留熔体可以确保炉子最小容量时对碎屑的最佳处理。
残留熔体看上去体积较大,要考虑到阴极铜和废料包要尽量浸入熔液中。
只有在这种情况下,才可达到最佳的热效率。
在长时间操作的情况下,炉子可完全被清空,完全切断能源。
由于采用双汽缸,炉子的倾角可达95°。
由液压缸自身的供能,液压能源包位于炉子附近。
液压驱动可倾系统要防止碎裂的管道和软管。
电能不足的情况下,可以使用应急电源。
所有的液压部件可手动操作。
温度测量设备(手动)给出正确的温度。
在保温和过热情况下,与称重系统一起自动控制能量供应。
炉子排烟罩上部有碎屑加料系统。
通过悬垂直的按钮启动(手动操作)。
在此操作中,炉子一直处于低功率状态。
随着加料的增多,功率逐渐加大。
即使是冷启动时,改变合金,炉子内部也没有残留熔体。
PLC在热处理炉电控系统中的应用现状及发展前景

PLC在热处理炉电控系统中的应用现状及发展前景摘要本文介绍了PLC技术原理和特点以及热处理炉电控系统的组成部分,重点描述了以PLC为核心的热处理炉电控系统在温度控制、压力控制、流量控制、点火控制和必要的连锁控制等方面的应用现状,总结了PLC在热处理炉电控系统中的发展前景。
1、PLC技术原理及特点1.1PLC技术原理PLC主要是由CPU、电源、存储器和专门设计的输入/输出接口电路等组成,如图1所示,因此可以更好的应用于电控系统等领域。
PLC都是采用“顺序扫描,不断循环”的方式进行工作的,属于串行工作方式。
即在PLC运行时,按照输入采样、用户程序执行、输出刷新三个阶段对数据进行处理,在输入采样阶段PLC将依次从输入接口读取数据在采样结束后将转入用户执行阶段,在用户执行阶段PLC将会按照事先编程好的梯形图执行并将处理后的数据输出写入输出状态寄存器中,输出状态寄存器的通断状态在输出刷新阶段送至输出锁存器中,并通过一定的方式(继电器、晶体管或晶闸管)输出,驱动相应输出设备工作。
[[1]]1.2PLC技术特点正因为PLC的技术原理是“顺序扫描,不断循环”的方式,所以使得PLC有了一下特点:(1)可靠性高、抗干扰能力强:用软元件代替大量机械触点,在系统的输入/输出回路中,采用光电隔离等措施有效防止了回路间的信号干扰;(2)编程简单、系统设计修改调试方便:编程语言是梯形图,形象直观,易学易用;(3)控制结构简单,通用性强,功能强大;(4)可以支持MODBUS通信协议,包括主机从机模式,可组网多个一体机使用灵活。
2、热处理炉电控系统组成热处理炉电控系统主要功能是按给定的温度曲线进行加热、保温及冷却等操作,对放入炉内的工件按照温度曲线完成相应的热处理,同时要完成对温度、压力、流量和系统整体的监测等。
下面是对两种热处理炉电控系统的简单介绍:2.1电阻炉电控系统组成电阻炉电控系统主要为温度控制系统,相对于燃料炉电控系统所包含的控制系统更简单,更加易于实现预期的控制,更易于保养和维护,也更加适合科研院所的教学与科研实验。
基于PLC和触摸屏的电热锅炉控制系统改造

为 了限 制循 环 泵 的起 动 电 流 , 化 起 动 过 程 , 原 有 循 环 泵 优 将 的 自耦 变 压 器起 动装 置 更 换 为 软 启 动 装 置 ,可 以利 用 软 启 动 装 置 的软 停 车 功 能 降低 停 泵 时 的 水锤 效 应 。
4 工 作 原 理
用单 片机 为 控 制核 心 的专 用 控制 系统 。
5 系统 设 计 5 1 系 统 硬件 设 计 ( ) 辑控 制 部 分 1逻
供 暖 系 统 主 要 由 2台 电锅 炉 、 中每 台 电热 锅 炉 包 含 有 1 其 O 组 8 W 加 热 器 。2台 75W 补 水 泵 、 k .k 2台 3 k 循 环 水 泵 以 及 0W 若 干管 道 、 门等 构 成 , 别 由 1台单 片 机控 制 系 统 控 制 , 水 阀 分 补 泵 和循 环 水 泵均 采 用 传 统 继 电器 控 制 。 工 作原 理 是 : 台锅 炉 其 两 并 列 运 行 , 片 机 控 制 系统 对 电热 锅 炉 内水 温进 行 监 测 , 据 温 单 根 度 情 况 对 电 加热 器 进 行 投 退 控 制 ,控 制 锅 炉 内水 温 度 在 设 定 范 围 内 , 同时 1台循 环 水 泵 运 行 将 锅 炉 内热 水 向办 公 区和 生 活 区
tols t m r yse wors, t i de cr t o ch un t n o l sgn k de al ed s i i p on fea f ci alm due de i ap oa . o pr ch
Ke wo d : L t c s ee ee ti i s,o to1r so mat y r s P C, ou h cr n,lc r bol c n r .an fr c er t i on
PLC在加热炉温度控制系统中的应用
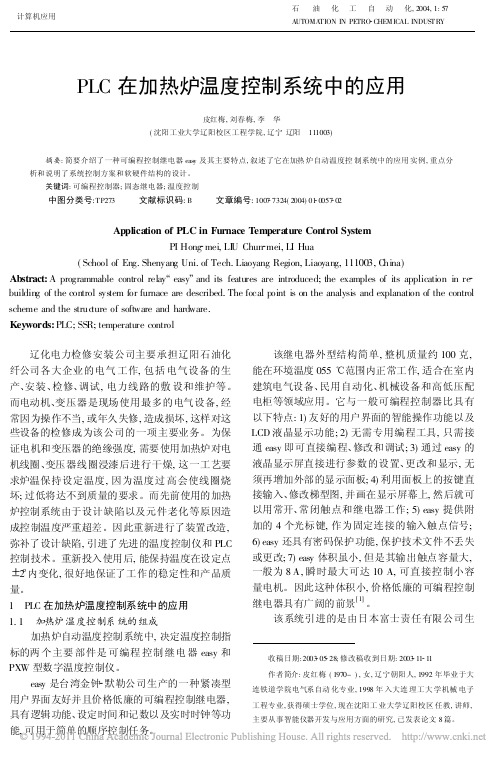
收稿日期:2003 05 28;修改稿收到日期:2003 11 11作者简介:皮红梅(1970-),女,辽宁朝阳人,1992年毕业于大连铁道学院电气系自动化专业,1998年入大连理工大学机械电子工程专业,获得硕士学位,现在沈阳工业大学辽阳校区任教,讲师,主要从事智能仪器开发与应用方面的研究,已发表论文8篇。
PLC 在加热炉温度控制系统中的应用皮红梅,刘春梅,李 华(沈阳工业大学辽阳校区工程学院,辽宁辽阳 111003)摘要:简要介绍了一种可编程控制继电器eas y 及其主要特点,叙述了它在加热炉自动温度控制系统中的应用实例,重点分析和说明了系统控制方案和软硬件结构的设计。
关键词:可编程控制器;固态继电器;温度控制中图分类号:TP273 文献标识码:B 文章编号:1007 7324(2004)01 0057 02Application of PLC in Furnace Temperature Control SystemPI Hong mei,LI U Chun mei,LI Hua(School of Eng.Shenyang Uni.of Tech.Liaoyang Region,Liaoyang,111003,C hina)Abstract:A programmable control relay easy and its features are introduced;the examples of its application in re building of the control system for furnace are described.The focal point is on the analysis and explanation of the control scheme and the struc ture of software and hardware.Keywords:PLC;SSR;temperature control辽化电力检修安装公司主要承担辽阳石油化纤公司各大企业的电气工作,包括电气设备的生产、安装、检修、调试,电力线路的敷设和维护等。
课程设计(论文)-基于PLC的电加热炉温度控制系统设计

课程设计(论文)-基于PLC的电加热炉温度控制系统设计引言电加热炉在很多工业生产过程中都扮演着重要角色,而温度控制是电加热炉设计中一个至关重要的问题。
在传统控制方式中,人工干预方案过程复杂,效率较低,不利于生产效率和产品质量的提高。
本文将介绍基于PLC的电加热炉温度控制系统的设计思路、实现原理和结果。
一、设计思路本设计将采用PID控制算法,该算法具有高效、稳定、精度高等优点。
通过对电加热炉加热、冷却及温度等变量进行采样处理,并将PID控制器中的比例、积分、微分三个参数进行调节,使电加热炉的温度控制在预定温度范围内。
二、实现原理本设计所用的硬件设备主要包括PLC、温度传感器、电源、电加热炉及调节阀等。
其中,PLC负责对相关参数的采集与计算,并通过输出信号控制电加热炉内加热、冷却和温度调节。
具体实现步骤如下:1.系统启动后,PLC获取温度传感器采集到的温度值,并将该值与预定温度进行比较,如果温度低于预定温度,PLC将对电源输出信号,让电加热炉进行加热;否则,PLC关闭电加热炉,让炉内温度保持稳定。
2.为了防止温度超过预定值,PLC同时监控温度,当温度高于预定值时,PLC会输出信号关闭电加热炉并打开冷却阀,降低炉内温度。
3.PLC采用PID算法计算比例、积分、微分三个参数,通过对这三个参数的调节,控制电加热炉的加热和冷却过程。
当温度波动较大时,PID控制器会对加热、冷却速度进行调整,使系统实现温度稳定控制。
三、实验结果在实验中,我们将预定温度设置为400℃,测试结果表明:通过使用本文设计的基于PLC的电加热炉温度控制系统,可以让电加热炉的温度控制在预定温度范围内,而且精度高、控制稳定且效率高。
整个系统具有操作简单,实现成本低等优点,可以满足很多工业生产过程中对温度精确控制的需求。
结论本文通过对基于PLC的电加热炉温度控制系统的设计、实现、测试与分析,证明了该系统具有高效、精度高、稳定性强等多方面的优点。
PLC在热弯炉加热器功率调节控制中的应用(精)
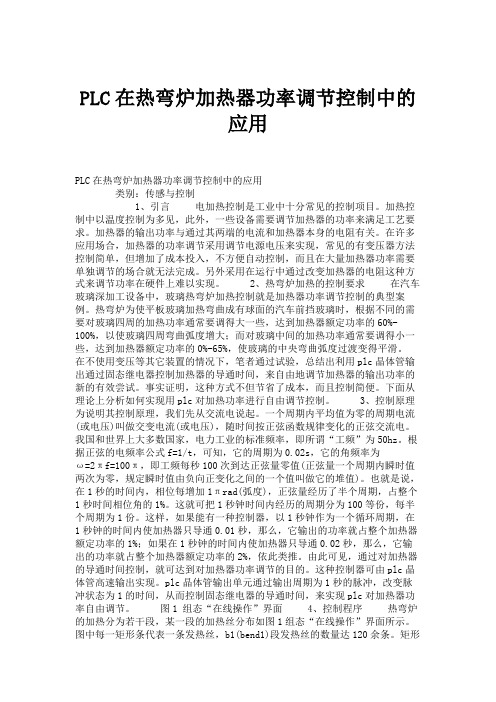
PLC在热弯炉加热器功率调节控制中的应用PLC在热弯炉加热器功率调节控制中的应用类别:传感与控制1、引言电加热控制是工业中十分常见的控制项目。
加热控制中以温度控制为多见,此外,一些设备需要调节加热器的功率来满足工艺要求。
加热器的输出功率与通过其两端的电流和加热器本身的电阻有关。
在许多应用场合,加热器的功率调节采用调节电源电压来实现,常见的有变压器方法控制简单,但增加了成本投入,不方便自动控制,而且在大量加热器功率需要单独调节的场合就无法完成。
另外采用在运行中通过改变加热器的电阻这种方式来调节功率在硬件上难以实现。
2、热弯炉加热的控制要求在汽车玻璃深加工设备中,玻璃热弯炉加热控制就是加热器功率调节控制的典型案例。
热弯炉为使平板玻璃加热弯曲成有球面的汽车前挡玻璃时,根据不同的需要对玻璃四周的加热功率通常要调得大一些,达到加热器额定功率的60%-100%,以使玻璃四周弯曲弧度增大;而对玻璃中间的加热功率通常要调得小一些,达到加热器额定功率的0%-65%,使玻璃的中央弯曲弧度过渡变得平滑。
在不使用变压等其它装置的情况下,笔者通过试验,总结出利用plc晶体管输出通过固态继电器控制加热器的导通时间,来自由地调节加热器的输出功率的新的有效尝试。
事实证明,这种方式不但节省了成本,而且控制简便。
下面从理论上分析如何实现用plc对加热功率进行自由调节控制。
3、控制原理为说明其控制原理,我们先从交流电说起。
一个周期内平均值为零的周期电流(或电压)叫做交变电流(或电压),随时间按正弦函数规律变化的正弦交流电。
我国和世界上大多数国家,电力工业的标准频率,即所谓“工频”为50hz。
根据正弦的电频率公式f=1/t,可知,它的周期为0.02s,它的角频率为ω=2πf=100π,即工频每秒100次到达正弦量零值(正弦量一个周期内瞬时值两次为零,规定瞬时值由负向正变化之间的一个值叫做它的堆值)。
也就是说,在1秒的时间内,相位每增加1πrad(弧度),正弦量经历了半个周期,占整个1秒时间相位角的1%。
- 1、下载文档前请自行甄别文档内容的完整性,平台不提供额外的编辑、内容补充、找答案等附加服务。
- 2、"仅部分预览"的文档,不可在线预览部分如存在完整性等问题,可反馈申请退款(可完整预览的文档不适用该条件!)。
- 3、如文档侵犯您的权益,请联系客服反馈,我们会尽快为您处理(人工客服工作时间:9:00-18:30)。
小型PLC在电加热热处理炉改造中的应用
王胜利,许庆谦
(马钢自动化工程公司计控部,安徽马鞍山 243000)
[摘要]本文主要介绍小型PLC系统在电加热炉中的应用及系统的硬件组成、软件结构等。
依据相关的技术要求,简述了电加热炉的温度控制原理及控制方案。
该系统运行稳定可靠,温度控制精度高,投资少,具有一定的应用推广价值。
[关键词]电加热炉、触摸屏、温度控制、位式调节
0 前言
马钢机制公司热处理车间1座用于热处理的4 m井式炉因设备陈旧、控制手段落后需要改造。
这座热处理炉采用电加热方式,额定电压为380 VAC,额定功率为264 kW,采用三角形联接方式,电加热功率元件采用的是双向晶闸管,从炉顶到炉底共设有4个加热段,每段设一根热电偶测量炉膛温度,使用带PID调节的记录仪表进行温度控制。
改造前该热处理炉已处于停运状态,要求控制系统这部分的改造费用不超过12万元。
1 技术要求
用户要求能按照给定的热处理温度曲线进行升温和保温。
在升温阶段,4段的实际炉膛温度与设定值的差值均不得超过±10 ℃,在保温阶段,4段的实际炉膛温度与设定值的差值均不得超过±5 ℃。
最高炉膛温度不高于900 ℃。
最复杂的热处理温度曲线为三阶段升温保温曲线,如图1所示。
系统应能编辑、保存和调用最多5组这样的热处理温度曲线。
升温保温过程要求全程自动控制,记录每段的实际炉膛温度,并要求设有温度超限报警。
2 控制方案
我们面对的控制对象虽然是一个简单的电加热炉,但是整个炉子的4个加热段在加热过程中会相互影响,若考虑这种影响,整个控制方案将会很复杂,幸而在加热过程中这种影响较小可以忽略。
因此为了简化控制方案,我们把整个炉子的4个加热段看成4个互不影响、相互独立的控制对象,这样采用小型的具有模拟量控制功能的PLC即能实现用户提出的要求,但需要采取一个合适的控制方法以满足用户对热处理温度控制的高要求。
下面以一个加热段为例,详细说明采用的控制方法。
首先我们认为升温阶段温度控制的目标是升温的速度,相当于随动控制,而保温阶段温度控制的目标是温度的恒定,是恒给定控制,两个阶段的控制特性不同,因此必须采用两套PID参数分别用于升温阶段的升温速度控制和保温阶段的温度控制,以满足不同阶段温度的控制要求。
其次,为了防止实际温度在调节过程中因超调而超出所要求的控制范围,我们还采用了位式调节以强制输出,即在升温阶段时,当炉温高出设定值8 ℃时,强制输出一个预先设定好的小的输出值,使炉温立即缓慢下降,当炉温降到高出设定值7 ℃时,又回到原来的PID调节;当炉温低于设定值8 ℃时,则强制输出一个预先设定好的大的输出值,使炉温立即缓慢上升,当炉温升到低于设定值7 ℃时,即又回到原来的PID调节,也就是说PID
调节在设定值±8 ℃的区间内起作用,超出这个区间由位式调节控制;同样,在保温阶段也是如此,但位式调节的强制输出是在温度超出设定值±4 ℃区间时起作用,恢复PID调节的限制值则设在超出设定值3 ℃或低于设定值3 ℃。
还有需要注意的是升温阶段PID参数与保温阶段PID参数之间的转换,为满足温度控制的要求,设立了两个转换条件,满足其中一条即进行转换。
一是当升温阶段的温度设定值达到保温阶段的温度设定值时,二是当实际炉温达到保温阶段温度控制范围的下限即低于设定值5 ℃时,即用保温阶段的PID参数进行调节。
其控制原理框图如图2所示。
图2 控制原理框图
按上述控制方案,我们预测炉膛温度的记录曲线会是一条以温度设定值为轴,升温阶段在±10 ℃区间波动,保温阶段在±5℃区间波动,幅度逐渐减小直至趋于直线的曲线。
另外,为了方便调试和处理意外情况,还保留有手动操作方式。
3 硬件配置
整个井式热处理炉的自动控制系统由小型PLC、触摸屏、检测元件、记录仪表以及功率控制柜组成一个整体。
操作人员通过触摸屏进行自动开炉、停炉以及编辑、调用、存储热处理温度曲线,通过选择开关来选择自动或手动操作方式,手动操作时可通过手动温控旋钮来手动控制炉温,使用小长图记录仪记录井式热处理炉4段的炉膛温度曲线。
具体的硬件配置如下。
(1)PLC采用的是GE VersaMax Rack,4通道AI模块、4通道AO模块、16通道DI模块、16通道DO模块各1块。
(2)操作界面采用的是6吋(1英寸=2.54 mm)触摸屏,触摸屏与PLC 之间的通信采用RS485串行方式。
(3)温度检测元件为K电偶,配以温度变送器将热电偶信号转换为4~20 mA。
(4)温度记录采用的是ER101系列的小长图记录仪,量程为0~1 000℃,
共4套。
(5)功率控制柜包含4套功率控制装置,采用的电加热功率元件是双向晶闸管,由PLC输出的4~20 mA信号到功率控制装置,以控制双向晶闸管的导通角,进而控制流过电阻丝的电流的大小,并最终控制炉子的温度。
整套控制系统的总费用在11万元左右。
4 软件的功能与设计
热处理炉控制软件的功能是实现热处理过程的自动运行,满足用户提出的控制要求,同时还要简化操作步骤,方便工作人员操作。
整套软件的设计包括两个部分:触摸屏画面设计和PLC程序编程。
我们为触摸屏设计了四幅画面:开炉停炉的操作画面、热处理温度曲线的编辑画面、温度趋势画面、功率控制装置的状态画面,工作人员操作起来非常方便。
这里需要特别说明的是热处理温度曲线的编辑,热处理温度曲线由三组加热(或保温)时间和目标温度共6个数据组成,在触摸屏上用热处理温度曲线的编辑画面进行编辑,编辑后的数据存储在PLC中,PLC中一共可存储五组热处理温度曲线的数据。
至于热处理温度曲线的初始温度按开炉那一时刻的炉膛温度计算。
PLC程序主要是实现我们设计的控制方案,完成热处理过程的全程自动控制,以及过程数据的采集、滤波和工程量转换,操作方式的手/自动切换,热处理温度曲线的存储等等。
最后,需要说明的是PLC程序用VersaPro编程组态软件编写,触摸屏画面则是用Quick Design触摸屏画面编辑软件编制的。
5 结束语
2002年8月份该电加热炉正式投入运行,由于在调试过程中,我们精心整定两套PID参数,使实际的炉温曲线与我们的设想极为接近,经炉子热处理后的工件温度、硬度非常均匀,用户很满意,改造后的4 m井式电阻炉成为用户的生产主力炉。
随后,我们又按照同一种技术方案改造了该用户的另一座4 m井式电阻炉和两座渗碳炉,取得了同样好的效果。