高炉熔渣处理及资源化利用技术概述
高炉炉渣中铁的回收和利用技术

高炉炉渣中铁的回收和利用技术随着钢铁工业的不断发展,生产中产生的废渣也越来越多。
其中,高炉炉渣作为钢铁生产废弃物的重要组成部分,一直被认为是一种资源性材料,固体回收利用具有广泛的应用前景。
高炉炉渣是一种带有一定氧化性的铁质物质,其中含有大量的铁,因此实现高炉炉渣中铁的回收和利用技术具有重要意义。
1.高炉炉渣中铁的含量高炉炉渣中含有的铁主要来源于铁矿石和焦炭。
在高炉内,铁矿石被还原为高炉渣中的还原铁,这样高炉内的铁就可以得到充分利用。
根据炉渣的不同组成成分,炉渣中所含的还原铁也不断变化,因此高炉炉渣中的铁含量的大小也是一个关键性问题。
炉渣中铁含量通常在20%到60%之间。
当炉渣中含有较高的铁时,可以采取回收和回用的方式使其得到充分利用。
回收的铁要求质量良好、不能受到污染,否则会对炉渣的利用产生不利影响。
2.高炉炉渣中铁的回收技术(1)重力选别技术重力选别技术是一种非常常见的采用的高炉炉渣铁的回收技术。
通过重力分离的作用,将铁和其他物质分开,这种技术能够有效地降低炉渣中铁的含量,从而提高资源的利用效率。
重力选别技术的基本原理是利用重力张力的不同,让炉渣中的铁与其他物质分离。
首先通过不同大小的筛网进行筛分,将炉渣分为不同的颗粒大小。
然后,将这些不同大小的颗粒进行分类,分别提取铁和其他物质,从而达到回收并循环利用的目的。
(2)磁选技术磁选技术是利用磁性材料本身所具备的特性,通过磁场作用将非磁性材料与磁性材料分开的一种技术。
高炉炉渣中含有大量的铁,其中些铁是具有磁性的,所以采用磁选技术可以获得高炉炉渣中铁的良好回收效果。
磁选技术的原理是利用磁性颗粒被磁场吸附的能力,使磁性颗粒与非磁性颗粒分离。
将高炉炉渣样品在磁场的作用下进行分离,可以得到不同富含铁矿物的产品。
(3)气固两相分离技术气固两相分离技术是利用气体和固体之间的密度差异来分离炉渣中的铁。
本技术是在熔融状况下对炉渣中的铁进行分离的。
通过高速流动的气体对炉渣进行喷浆,将含有可回收铁的气体部分与不含铁的固体部分分离出来。
炉渣处理及资源化利用
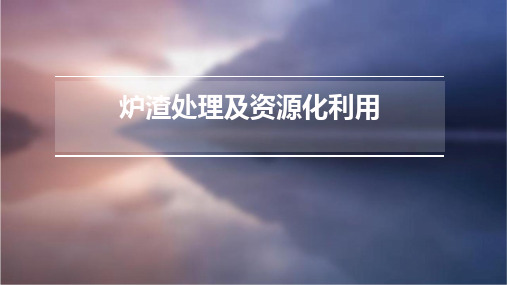
该钢铁企业采用先进的炉渣处理技术,将炉渣进行破碎、筛分和磁选等处理,分 离出铁、渣和尾矿等组分。其中,铁被回收利用,渣则进一步加工成各种建材产 品,如水泥、混凝土等,尾矿用作矿山采空区的充填料。
某水泥企业炉渣处理及资源化利用案例
总结词
以废治废、环境友好
详细描述
该水泥企业利用炉渣作为原料,与石灰石、页岩等共同研磨成生料,再经过高 温煅烧得到水泥熟料。这种方法不仅解决了炉渣的处置问题,还降低了生产成 本,实现了以废治废的目标。
生物法
利用微生物的代谢作用将炉渣 中的有机物转化为有用的物质 ,同时减少有害物质的排放。
综合利用法
将物理、化学和生物等多种方 法结合起来,实现对炉渣的全
面处理和资源化利用。
02
炉渣资源化利用技术
炉渣在建材工业中的应用
炉渣混凝土
利用炉渣作为骨料,与水泥、水 等材料混合制成混凝土,具有较 好的抗压、抗折强度和耐久性。
挑战
资源化利用产品的性能和价 值不高。
对策
加强科研力度,提高资源化 利用产品的质量和附加值, 如生产建筑材料、路基材料 等。
经济挑战与对策
挑战
处理和利用炉渣的成本 较高。
对策
制定优惠政策,如税收 减免、财政补贴等,降 低企业处理和利用炉渣
的成本。
挑战
资源化利用产业的市场 竞争力不强。
对策
加强产业联盟和合作, 降低生产成本,提高产 品质量和品牌影响力。
炉渣砖
将炉渣与适量的粘土、页岩等材 料混合,经过压制成型、干燥和 烧结,制成具有良好抗压、抗折 和耐久性能的砖块。
炉渣水泥
将炉渣作为混合材料,与石灰、 石膏等材料一起磨细并制成水泥 ,具有较低的水化热和良好的抗 渗性能。
化工生产炉渣资源化利用技术与装备选择解析
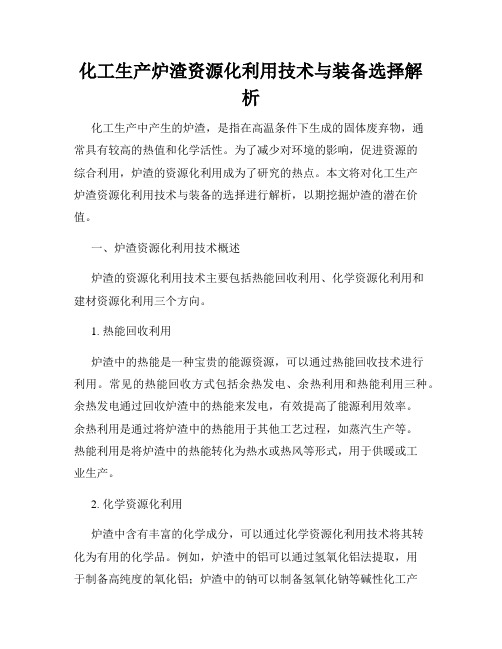
化工生产炉渣资源化利用技术与装备选择解析化工生产中产生的炉渣,是指在高温条件下生成的固体废弃物,通常具有较高的热值和化学活性。
为了减少对环境的影响,促进资源的综合利用,炉渣的资源化利用成为了研究的热点。
本文将对化工生产炉渣资源化利用技术与装备的选择进行解析,以期挖掘炉渣的潜在价值。
一、炉渣资源化利用技术概述炉渣的资源化利用技术主要包括热能回收利用、化学资源化利用和建材资源化利用三个方向。
1. 热能回收利用炉渣中的热能是一种宝贵的能源资源,可以通过热能回收技术进行利用。
常见的热能回收方式包括余热发电、余热利用和热能利用三种。
余热发电通过回收炉渣中的热能来发电,有效提高了能源利用效率。
余热利用是通过将炉渣中的热能用于其他工艺过程,如蒸汽生产等。
热能利用是将炉渣中的热能转化为热水或热风等形式,用于供暖或工业生产。
2. 化学资源化利用炉渣中含有丰富的化学成分,可以通过化学资源化利用技术将其转化为有用的化学品。
例如,炉渣中的铝可以通过氢氧化铝法提取,用于制备高纯度的氧化铝;炉渣中的钠可以制备氢氧化钠等碱性化工产品;炉渣中的硫可以制备硫酸等化学品。
化学资源化利用技术可以充分利用炉渣中的化学成分,实现从废弃物到有价值产品的转化。
3. 建材资源化利用炉渣中的某些成分可以用于制备建筑材料,如水泥、混凝土等。
例如,炉渣中的硅、铝、铁等可以通过适当的处理工艺制备高性能水泥;炉渣中的氧化镁和氧化铝可以用于制备耐火材料,广泛应用于高温装备。
二、炉渣资源化利用装备选择要点在进行炉渣资源化利用时,选择合适的装备是关键。
以下是几个重要的选择要点:1. 检测分析设备对炉渣进行全面的成分分析是确定资源化利用途径的基础,因此需要选择适用的检测分析设备。
常见的分析设备包括X射线荧光光谱仪、原子吸收光谱仪、红外光谱仪等。
2. 热能回收设备根据炉渣中的热能特性,选择合适的热能回收设备至关重要。
常见的设备有余热锅炉、余热发电机组、热风炉等。
高炉炉渣处理与资源化利用技术研究

高炉炉渣处理与资源化利用技术研究近年来,随着工业生产的不断发展,高炉炉渣作为一种常见的工业废弃物,如何进行有效的处理和资源化利用已成为一个备受关注的问题。
本文将从高炉炉渣的特点、炉渣处理技术以及资源化利用方面展开论述。
首先,我们需要了解高炉炉渣的特点。
高炉炉渣主要由矿渣和工艺渣两部分组成。
矿渣主要是铁矿石在高温条件下还原和熔化生成的,而工艺渣则主要是焦炭灰、烧结矿砂等在高炉内燃烧生成的。
由于高炉操作的连续性,炉渣中也会包含少量的冶炼渣、废弃物等杂质。
传统上,高炉炉渣的处理方式主要是填埋和堆放。
然而,这种处理方式存在很多问题。
填埋会导致土地资源的浪费和环境污染,而长时间的堆放则容易造成渗滤液的渗出和大气中有害气体的排放。
因此,炉渣处理技术的研究和创新势在必行。
目前,炉渣处理技术主要包括物理处理、化学处理和生物处理等几种方法。
物理处理主要是利用筛分、磁选、重力分选等方法将炉渣中的金属物质和其他有用物质分离出来,以达到减少炉渣体积和减少对环境的影响。
化学处理则是利用酸碱等化学试剂对炉渣进行脱硫、脱磷等处理,使得炉渣中的有害物质得到降解和转化。
生物处理是利用微生物的作用对炉渣进行降解和转化,实现对炉渣中有机物和重金属的去除。
除了传统的处理技术外,资源化利用技术也是炉渣处理的另一个重要方向。
在资源化利用技术中,炉渣可以被转化为建筑材料、水泥、道路铺设材料等高附加值的产品。
例如,在水泥生产过程中,炉渣可以取代部分水泥原料,减少对天然资源的依赖并降低环境污染。
此外,炉渣还可以被转化为颗粒活性炉渣、高温液相炉渣等陶瓷材料,用于建筑材料和环保装备制造。
为了进一步提高炉渣处理与资源化利用的效益,需要加强技术研究和创新。
一方面,通过优化处理流程、提高处理效率和降低处理成本,可以实现对炉渣的高效处理。
另一方面,通过开展新材料的研发和产业化推广,可以扩大炉渣的资源化利用范围。
此外,还需加强对炉渣处理过程中所产生的废水和废气的处理,以减少环境污染。
高炉炼铁过程中废渣资源化利用的技术创新

高炉炼铁过程中废渣资源化利用的技术创新由于工业化的快速发展,高炉炼铁已成为现代钢铁工业中不可或缺的环节。
然而,传统的炼铁过程会产生大量的废渣,给环境带来严重污染。
为了实现可持续发展,推动高炉炼铁过程中废渣资源化利用的技术创新势在必行。
本文将探讨当前废渣资源化利用的现状和趋势,并提出一些创新的技术解决方案。
一、废渣资源化利用的现状高炉炼铁过程中主要产生的废渣主要包括烧结矿、烟气净化渣和炉渣等。
这些废渣通常被视为浪费物料,被丢弃或填埋,给环境带来负面影响。
然而,废渣中含有很多有价值的可回收物质,如铁、钢、矿物等。
因此,将废渣转化为可再利用的资源是一种解决环境问题和实现可持续发展的有效途径。
目前,废渣资源化利用主要通过以下几种方式实现:1. 废渣回收再利用:将废渣中的有价值物质进行分离和提取,重新利用于炼铁过程或其他工业生产中。
例如,烧结矿中的铁含量较高,可以再次用于高炉冶炼过程中。
2. 废渣填充利用:将废渣用于填充坑道、道路建设和土地复垦等工程中。
废渣填充可以减少对自然资源的占用,同时改善了被填充地区的土壤质量。
3. 废渣综合利用:将不同种类的废渣进行混合利用,形成新的产品或材料。
例如,烟气净化渣中的硅酸盐可以与矿产废渣混合制备建筑材料。
尽管废渣资源化利用取得了一定的进展,但仍面临一些挑战。
首先,目前的废渣资源化利用技术还不够成熟,存在成本高、技术路线不清晰等问题。
其次,相关政策法规的缺失和监管体系不健全也制约了废渣资源化利用的发展。
二、废渣资源化利用的技术创新为了推动高炉炼铁过程中废渣资源化利用的发展,需要进行技术创新和研发。
以下是一些可行的技术创新方案:1. 废渣熔融处理技术:通过高炉炼铁过程中炉渣的熔融处理,将废渣转化为玻璃状物质。
这种熔融处理技术可以减少废渣体积,提高废渣中有价值物质的回收率,并且可以将熔融后的产品用于建筑材料或其他工业领域。
2. 废渣碳化技术:利用废渣中的碳含量,将其进行碳化处理,生成高价值的碳材料。
炉渣处理及资源化利用
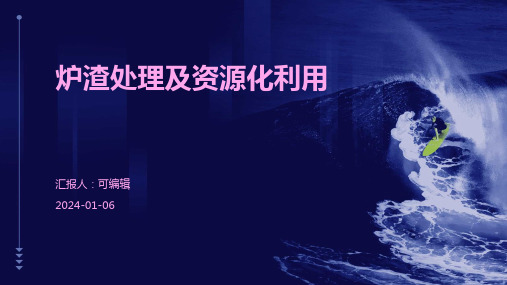
创造就业机会
炉渣处理与资源化利用产业的 发展将为社会创造更多的就业 机会,促进经济发展。
减少环境污染
通过炉渣处理与资源化利用, 减少废弃物对环境的污染,保
护生态环境。
04
炉渣处理与资源化利用的挑战与解决方 案
技术瓶颈与突破
高效分离技术
研发高效分离技术,将炉渣中的有价组分与杂质 进行分离,提高回收率。
循环经济
发展循环经济,推动废弃物资源化利用,符合国家可持续发展战略 ,为炉渣处理与资源化利用提供了重要的发展机遇。
经济效益与社会效益
降低废弃物处理成本
通过炉渣处理与资源化利用, 减少废弃物的处理费用,降低
企业的生产成本。
提高资源利用率
将炉渣转化为有价值的资源, 实现资源的有效利用,缓解资 源短缺问题。
炉渣可作为道路建设的填料,提高道 路的抗压强度和稳定性。
环保领域
炉渣经过处理后可作为吸附剂、催化 剂等用于废水处理、废气治理等领域 。
03
炉渣处理与资源化利用的前景
技术发展与创新
高效分离技术
利用先进的分离技术,如磁选、 浮选、重选等,从炉渣中高效分 离有价组分,提高新型固化剂和固化工艺,降 低炉渣中有害物质浸出风险,提
05
案例分析
某钢铁企业炉渣处理及资源化利用项目
总结词
技术先进、资源化程度高
详细描述
该钢铁企业采用先进的炉渣处理技术,将炉渣进行破碎、筛分和磁选等处理, 从中回收铁、锰等有价元素,同时将剩余的尾渣制成建筑骨料、路基材料等, 实现了炉渣的高效资源化利用。
某水泥企业炉渣处理及资源化利用项目
总结词
技术成熟、应用广泛
的影响。
资源化产品标准
03
高炉渣的处理和利用

利用高炉熔渣直接生产矿棉技术摘要:在当前钢铁产量居高不下,效益低迷,污染严重,耗能高的大背景下,钢铁企业越来越重视对生产钢铁中的副产品的处理和利用,其中作为最主要的组产品高炉渣的利用显得尤其重要。
虽然高炉渣已经取得广泛的工业用途,比如制成水泥和建筑材料,矿物棉等。
但是高炉渣出炉温度高达1400℃以上,热含量为1680-1900kj/kg,对于这部分显热,目前尚无很好的利用。
2012年7亿吨钢产量3 亿吨高炉渣生产矿棉85万吨高炉渣的利用↓↓优点:耐水性、耐热度、耐腐蚀等方面优点,市场需求十分巨大。
缺点:无法有效利用高炉渣的温度。
高炉出铁口出渣口甩棉机热冷热传统工艺:冷态处理出铁口高炉出渣口甩棉机先进工艺:直接热态处理炉的设计①能直接接收液态熔渣(高温1450℃)②具有调控温度的作用③具有缓冲、保存液态熔渣的作用④具有调整成分、成分混匀功能图实验装置示意图1-感应铜线圈; 2-坩埚; 3-感应炉; 4-CO2; 5-温度表;6-热电偶; 7-N2; 8-坩埚盖; 9-吹气石英管.升温降温25℃常温干渣、水渣1450℃高炉溶渣调质炉(1400℃):加入辅料进行调质离心机甩棉成纤得到矿棉制品1450℃高炉溶渣调质炉(1400℃):加入辅料进行调质离心机甩棉成纤得到矿棉制品本工艺与老工艺流程对比本工艺与传统工艺能耗对比能耗及成本对比吨棉生产能耗吨棉生产成本㎏标煤/t对比元/t对比本工艺16050~42239.266.6传统工艺320~380100359.4100节省量160~220120.2以2012年85万吨矿棉产量计算,在节能方面:本工艺至少将节省13.6万吨标准煤,折算为人民币1亿元。
重要意义本工艺传统工艺高能耗、高污染、高成本低能耗——充分利用熔渣显热,并减少二次加热;低污染——省去熔渣冷却,杜绝冷却污水的产生;省去二次加热,减少温室气体排放。
革新我国高炉渣生产矿棉工艺实现新形势下的钢铁工业节能减排本工艺应用前景传统工艺:本工艺:高能耗高污染高排放高成本低能耗低污染低排放低成本可以看出:此技术生产矿棉前景十分广阔参考文献[1] 闫兆民,周扬民,杨志远,等.高炉渣综合利用现状及发展趋势[J].钢铁研究,2010,38(2).[2] 吕晓芳.高炉渣处理、回收利用技术的现状与进展[J].南方金属,2010(03).[3] 秦跃林,邱贵宝,白晨光,吕学伟,邓青宇.化学法回收高炉熔渣显热的研究进展[J].中国冶金,2011(04).[4] 胡玉芬,元立峰,马晓健.炼铁高炉矿渣酸度系数调节试验.山东冶金,2009, 20(1):12-78.[5] 刘保瑶,张小兵.熔融高炉渣制造玄武岩棉的可行性分析[J].矿产综合利用,2006(01).[6] 金士照,梁天云.利废法生产矿棉新工艺—电厂旋风炉渣生产(矿棉)的研究与实践.节能,2002,2(2):23-26.[7] 宫艳玲,李兆华,李银河,等.以高炉渣为原料制取矿渣棉的实验研究[J].北方钒钛,2011(04).[8] 蔡九菊,王建军,陈青霞,等.钢铁企业余热资源的回收与利用徐莉[J].钢铁,2007,42(6):10-212.[9] 林杰.高炉液渣含热回收利用技术探讨.能源研究与利用,2005,11(2): 22-401.[10] 刘晓玲,周辰辉,冉松林,陈贺,朱义文,樊传刚.高炉矿渣成棉的调质研究[J].安徽工业大学学报(自然科学版),2013(01).[11] 陈登福,佐祥均,温良英,董凌燕,邱贵宝.液态高炉渣热量回收利用方法及问题[J].环境污染治理技术与设备,2006(07).[12]杨铧.高效利用高炉熔渣显热的一步法矿棉生产技术[J].新型建筑材料,2003(03).[13] 郭强,袁守谦,刘军,李海潮.高炉渣改性作为矿渣棉原料的试验[J].中国冶金,2011(08).谢谢!请老师批评指正。
高炉渣的资源化

用途
用途
0.87
马钢 37.97 33.92 11.11 8.03 2.15 0.23 1.1 0.93
包钢 38.2 32.04 7.96 7.63 1.02 1.75
0.82
宝钢 39.57 34.32 15.06 5.95 0.94 1.76
0.70
攀钢 23.10 25.30 11.20 9.00 2.40 0.96 23.50 0.82
用途
一般来说,酸度系数越高,矿渣棉的化学耐久性越好。但酸度系数过高时, 制成的纤维可能较长,虽然化学稳定性得到改善,使用温度提高,但较难熔 化,纤维较粗。
用途
用于制硅肥以调节土壤肥力
硅肥是一种含有氧化硅和氧化钙为主的矿物质 肥料,是农作物生长所需要的重要营养元素。 硅肥有利于农作物的光合作用,调节农作 物对 氮、磷、钾等元素的营养需求,还可降低重金 属对农作物造成的污染,提高农作物的产量等 。
高分炉类渣可根据处理方法的不同分为三类
1.水渣 2.矿渣碎石 3.膨胀矿渣
水分类渣
熔融状态的高炉渣用 水或水与空气的混合 物给予水淬;使其成 为砂粒状的玻璃质物 质。
这也是我国处理高炉 渣的主要方法。具体 水淬方式很多,常用
分类
矿渣碎石
高炉渣在指定的渣坑或渣 场自然冷却或淋水冷却形 成较致密的矿渣后,再经 过破碎、筛分等工序所得 到的一种碎石材料,为此 常用热泼法。
用途
矿渣微晶玻璃产品,比高碳钢硬,比铝轻,其机 械性能比普通玻璃好,耐磨性不亚于铸石,热稳 定性好,电绝缘性能与高频瓷接近。矿渣微晶玻 璃用于冶金、化工、煤炭、机械等工业部门的各
- 1、下载文档前请自行甄别文档内容的完整性,平台不提供额外的编辑、内容补充、找答案等附加服务。
- 2、"仅部分预览"的文档,不可在线预览部分如存在完整性等问题,可反馈申请退款(可完整预览的文档不适用该条件!)。
- 3、如文档侵犯您的权益,请联系客服反馈,我们会尽快为您处理(人工客服工作时间:9:00-18:30)。
第11卷 第5期 中 国 水 运 Vol.11 No.5 2011年 5月 China Water Transport May 2011收稿日期:2011-03-11作者简介:朱文渊(1981-),男,武汉都市环保工程技术股份有限公司工程师。
高炉熔渣处理及资源化利用技术概述朱文渊(武汉都市环保工程技术股份有限公司,湖北 武汉 430071)摘 要:文中针对钢铁企业高炉渣的处理及资源化利用技术进行了概述。
首先介绍了高炉熔渣的物性,然后概述了目前高炉渣处理及资源化利用的现状,并分析了其存在的问题,接着介绍了目前国外高炉渣处理及资源化利用的新技术,最后提出了高炉渣处理及资源化利用的工艺技术路线及发展趋势。
关键词:高炉渣;粒化;热能回收中图分类号:X705 文献标识码:A 文章编号:1006-7973(2011)05-0107-03一、引言高炉渣是冶炼生铁时从高炉中排出的一种熔融状态的废渣,其从高炉中排出的温度在1450~1650℃。
2010年我国生铁产量5.9亿吨,按平均每吨生铁产生0.35t 渣来计算[1],高炉渣产量为2.065亿吨。
由于高炉熔渣温度高,产量很大,如果得不到合理的处理和利用,不但是对二次能源及资源的极大浪费,而且还会对环境造成很大的污染,国内外都在对高炉渣的处理及资源化利用进行研究。
二、高炉熔渣的物性 1.成分高炉渣主要成分为CaO、SiO 2和Al 2O 3,另外含有少量的MgO、FeO 和一些硫化物如CaS、MnS 和FeS [2]。
碱度(CaO/SiO 2)大于1的高炉渣具有基本的水泥质特性(潜在的水硬活性),同时也可能具有一些火山灰质特性(与生石灰反应)。
2.温度及热焓高炉出口熔渣温度约为1450~1650℃。
1500℃时,高炉渣理论焓为1606.21kJ/kg,约合54.8kg 的标准煤。
3.粘度普通高温熔渣粘度为0.2~0.6Pa·S,熔化性温度为1250~1400℃[3]。
熔渣粘度随温度的降低缓慢增加,大约1320℃时开始出现凝固相后,熔渣粘度急剧增加。
成分对熔渣粘度的影响较大。
实验研究表明,刚粒化的热渣粒具有依赖于温度的粘附力,非晶质渣粒间的不粘附温度小于950℃,高温渣粒对被撞击表面的不粘附温度为1050~1070℃。
4.表面张力高炉熔渣的表面张力随温度的变化显示出明显的阶段性,不论成分怎样,T>1390-1400℃表面张力处于一稳定的较低水平(0.54-0.59N/m);T<1390℃,表面张力随温度下降急剧升高。
5.比热高炉渣的比热与温度有关,实验研究表明,温度在900K 以上时,比热与温度近似呈线性关系。
6.导热特性高炉渣的导热特性与其状态(温度)紧密相关,在液渣状态(T>1400℃),导热系数很小,仅0.1~0.3W/(m.K),在凝固过程中,导热系数迅速增大到2~3W/(m.K),在固化过程中,导热系数随着温度的降低而增加,约为1~2W/m.K)[4]。
三、国内高炉渣处理及资源化利用现状及存在的问题 1.现状目前,高炉渣主要通过水淬处理,产品作为水泥生产原料。
而对于高炉渣的显热回收,国内对此仍然处在工业试验性阶段,还没有完整的设备。
水淬处理工艺主要有INBA 法、图拉法、沉渣池法和底滤法、RASA 法、螺旋法等,这些水淬工艺按其形式可以分为两大类:1)高炉熔渣直接水淬工艺,其处理过程是首先将高炉熔渣渣流用高压水进行水淬,然后进行渣水输送和渣水分离;2)高炉熔渣先机械破碎,后水淬工艺,其处理过程是将高炉熔渣渣流首先采用机械破碎,形成运动的液滴后进行水淬粒化,然后进行渣水分离和输送。
在实际应用中,INBA 法、图拉法、沉渣池法和底滤法,RASA 法、螺旋法等水淬工艺方法采用较多。
2.存在的问题高炉渣水淬处理过程中存在的主要问题是:(1)水耗高。
水淬渣过程中水压大于0.2MPa,水渣之比为(8~15):1,吨渣新水消耗约0.8t~1.2t。
(2)在水淬渣的过程中产生的硫化物会随蒸汽排入大气造成大气污染,渣中的碱性元素会进入冲渣水中造成水污染。
(3)未回收显热。
1t 液态渣水淬时散失的热量约为1600~1800MJ,相当于标准煤55~61kg 完全燃烧后所产生的热量。
液态高炉渣的温度为1450~1500℃,从火用分析的角度看,其余热品质非常高,极具利用价值。
(4)需干燥处理。
高炉水渣含水率高达10%以上,作为水泥原料生产时须干燥处理,仍要消耗一定的能源。
(5)对于水渣系统而言,电耗和系统维护的工作量非常大。
水冲渣系统循环水中所含大量为细颗粒对水泵和阀门等部件的磨损和堵塞非常严重,故使用一段时间后会导致水压下降、电耗增加、冲渣效果变差,清除水中的微粒还需大量资金。
108 中 国 水 运 第11卷 四、技术进展由于传统的水淬工艺对熔渣显热基本没有回收,干式显热回收技术得到了国内外研究者越来越多的关注。
目前普遍认为具有工业应用前景的主要为风淬法、旋转杯粒化法和甲烷-水蒸汽重整法。
1.风淬法风淬法的工艺流程见图1。
将高炉排出的1,400℃以上的熔融炉渣导入风洞造粒部,采用3个均分渣流供渣,熔渣由喷嘴中出来的告诉空气射流吹射粒化,喷嘴处空气流速可调,风洞内设有分散板,使1,050℃左右的渣粒碰板落下,下落过程中由风洞下部吹入空气冷却,渣粒约在800℃左右排出风洞。
排出的热渣粒经称量机、振动筛后,储存在热渣粒储仓中,再通过二次流化床热交换器冷却到150℃左右排出,风洞内的冷却速度可以保证成品渣的品质。
炉渣虽然是从高炉间歇排出,但是通过二次换热器工序的补充运行,可以实现热回收的连续性,将风洞一级冷却塔内引出的高温空气转变成蒸汽或电力进行利用。
图1 风淬法2.旋转杯粒化熔渣显热回收技术(RCA)[5]图2 旋转杯粒化熔渣显热回收技术试验装置 典型的旋转杯粒化熔渣显热回收技术的工艺流程图(实验装置)见图2。
高炉熔渣通过密封的流槽(B)进人热量回收室(A),经流槽(B)排出,直接流人位于热量回收室中心的旋转杯气流粒化器(C)。
在旋转杯的边缘,熔渣在离心力的剪切作用下甩出粒化,渣粒沿径向喷射,方向略微向上。
在旋转杯的周围同时引入环形空气射流,使熔渣薄膜产生不稳定的波动,以促进熔渣的破碎。
高温渣粒撞击壁面后不会粘到容器壁上,而是直接落人初级流化床(D)内,被快速冷却至炉渣析晶温度以下。
随后,渣粒溢出到二级流化床(E)内,回收更多的热量。
最后,炉渣通过排渣槽(F)排出,热空气通过出口(G)排出并回收利用。
小型试验说明,渣粒能被快速冷却,渣粒平均直径约为2mm,且得到的产品中玻璃相大于95%。
3.甲烷-水蒸汽重整技术[6]甲烷-水蒸汽重整技术是将熔渣的余热回收与常规的化学反应相结合,熔渣的高温余热通过以下的吸热化学反应回收:CH4(g) + H 2O(g) → 3H 2(g) + CO(g) ΔH =206 KJ/mol同样的原理,还可利用熔渣显热进行沼气制氢。
发生的化学反应时为:CH 4(g) + CO 2(g) → 2H 2(g) + 2CO (g) ΔH =247 KJ/mol高温渣粒的余热可以给水蒸汽催化重整和烃类物质的炭化分解提供足够的能量。
不仅用高温熔渣的余热替代了原有制氢的能耗,还可以减少二氧化碳的排放。
将旋转杯粒化法和甲烷-水蒸汽重整反应结合的方法无疑是一种较为优异的熔渣粒化法。
其工艺流程(工业化设计图)见图3。
图3 RCA-甲烷水蒸汽重整工业化设计图 上段为RCA 熔渣粒化和甲烷一水蒸汽重整,下段为渣粒填料床。
甲烷水蒸汽混合气在填料床的底部进入,经填料床内高温渣粒的预热,通过和高温渣粒的直接接触或者通过含镍催化剂材料的间接催化作用,混合气转化为氢和一氧化碳,从顶部排出且收集。
五、结语目前,钢铁企业的节能减排已列入我国“十二五”规划的重点课题,高炉熔渣中所蕴含的高品位热能的回收及终产物的资源化利用对钢铁企业的节能减排具有重大意义。
结合我国钢铁生产的具体情况,采用干式粒化及热能回收技术将是我国高炉渣处理及资源化利用的发展方向。
根据钢铁企业的实际情况,可将高炉熔渣粒化过程中回收热能得到的热空气用于热风炉的助燃热空气,也可以加热水产生高品质的蒸汽用于发电,在具有甲烷气体来源充足条件的地方,最理想的方式是采用甲烷-水蒸汽重整的方式,直接利用高炉熔渣的热能。
(下转第135页).第5期 郑建新等:橡胶坝在工程施工质量控制措施 135消力池水平段混凝土施工工艺流程:基础的开挖→铺设好反滤土工布→铺设中粗砂→铺设碎石→齿槽砌石→混凝土垫层→铺设沥青油毛毡→钢筋网制作安装→安装模板→混凝土浇筑→拆模→养护。
② 下游消力池斜坡段混凝土施工消力池斜坡段的混凝土施工工艺流程为:凿毛及清洗基面→止水带的安装→钢筋网制作安装→安装模板→浇筑混凝土→拆模→养护。
混凝土施工浇筑时,由低向高处施工,其他施工方法同消力池水平段混凝土浇筑施工。
(7)坝底板抗冲蚀、抗磨部位的施工为了防止高速水流产生空蚀,施工过程中需要严格控制底板的表面平整度:① 进出口结构的混凝土表面要求光滑,与施工图纸所示理论线的偏差不得大于3mm/1.5m;② 一般过水混凝土凹凸不能超过6ram,凸部应磨平;③ 与坝袋接触的冲刷部位,混凝土表面必须高强光滑.以减少坝袋冲刷磨损。
应采取特殊措施,如将此部位的混凝土表面浮浆清除,用水冲净晾干刷涂3~5mm的高标号环气水泥砂浆,达到强度后,用磨光机打磨平整光滑。
4.止水及埋件施工橡胶止水带质量必须有保证,橡胶止水的连接需要根据图纸或产品的使用说明要求进行实际操作。
在埋件安装中,我们需要安装供排水管和套管、电气管道及电缆、设备基础、支架、吊架、坝袋锚固螺栓、垫板锚钩等固定件、接地装置等。
5.坝袋安装本工程坝袋安装包括1号橡胶坝25m和2号橡胶坝28m。
坝袋安装主要是将坝袋周边同定在锚同槽内。
坝袋的安装程序为:垫板和坝袋底板的清理→铺设底板垫片→水帽安装→铺垫好止水胶条→吊送后展开坝袋→安装、固定好导水胶管→坝袋安装就位→安装压板固定坝袋→检查验收。
6.电气设备及其埋件工程电气埋件主要包括:电缆管及电缆,接地系统,控制屏柜埋件。
机电设备地脚螺栓和各种固定架等。
电缆敷设:在电缆敷设前,应对照图纸并结合实际情况分析电路走向和电缆敷设位置。
确定敷设方法。
然后安排人员分工实施。
操作室屏、柜、箱安装:右岸泵房操作室内有水泵专用控制柜1个,电动阀门控制屏1个,照明配电箱1个。
照明及单相设备包括:室内照明灯具、室外照明灯具、吊扇、插座、开关等。
供排水设备、风机、电动葫芦安装,供排水设备主要有:离心水泵及电机、油浸潜水泵,阀门和仪表,电动蝶阀等。
电气设备系统调试:当全部电气设备安装完成后,可进行通电调试。
系统整体试运行:本项工程全部完成后,在业主和监理工程师许可的情况下,进行排水试运行,以了解排水系统的运行情况。