联合作业分析(外部)
改善知识联合作业分析第单元

(1)把现在的循环时间缩短至目标循环时间
(2) 在目标循环时间下减少配置人员
1 减少人员 2 多台设备
--Lisy
缩短现在的循环时间
教材篇-P3-OHP-2/3
现状
目标CT 150DM
改善后
人
除去切屑 夹紧
车床
除去切屑 夹紧
人
除去切屑 夹紧
车床
除去切屑 夹紧
等待
松开夹具 测定
现状CT 180 DM
a 生产量 b 模型外产品 c 设备故障 d 作业空间、技能 e 缺勤
针对于这些变动条件 ● 这个变动幅度如何压缩 ● 针对于条件变动要采取怎样的相应措施
有必要进行讨论
--Lisy
教材篇-P4-OHP-2/2
改善前
2名5台
作业者A
作业者B
机器1
机器2
机器3
机器4
安装重装1 移动1→2
安装重装4 移动4→5
安装重装
加工 停止
加工
安装重装
安装重装2
操作2 移动2→3 安装重装3 移动3→1
现在循环时间22秒
安装重装5 操作5 移动5→4
等待
加工
安装重装 加工
改善后
停止
加工
安装重装 加工
②适当空间 确保作业者能充分移动身体的空间
③工程数的增减和设备配置的弹力性 设计成能够应对变化,具有弹性
--Lisy
案的评价、选择
教材篇-P11-OHP-1/1
1 评价、选择已经讨论过了的案
1) 案的效果 2) 改善费用 3) 改善期间 4) 相对于条件变动的对应度
2 评价、总结被采用的案,制作代替案(选择A案和不能选择B案
人机联合作业分析表
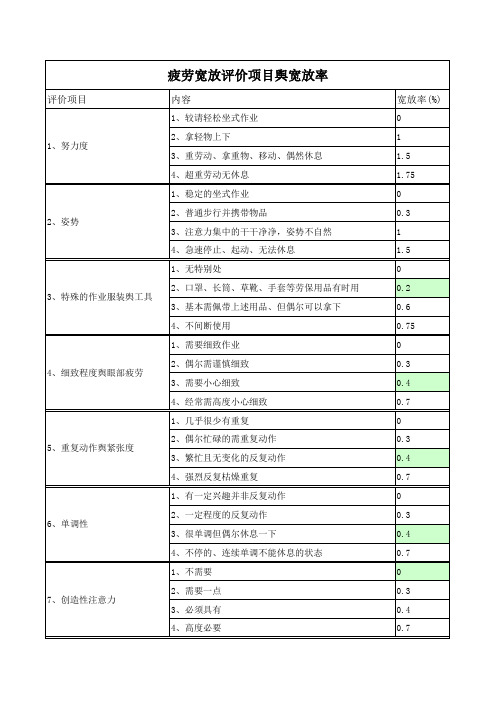
8、对责任舆危险注意度 9、环境 10、噪音 11、温度 12、光照度 13、地面
1、不需要 2、对他人的安全及责任需普通程度的留意 3、对自身及他人的安全责任需特别注意 4、超级危险作业需特别注意自己及他人安全 1、环境清洁 2、有少许烟尘和异味的污染 3、烟、污物、异气、尘灰很多 4、上述污染非常严重 1、没有噪音 2、少许噪音 3、有噪音,但有间隙 4、持续不断强噪音 1、有空调温度正常 2、普通的温度变化 3、有温度变化很大 4、温度变化极大,对人不利 1、光照度在标准之间 2、正常一般照明水平 3、光线弱或过强,影响人的情绪 4、非常弱的光线并且明暗变化剧烈,严重影响情绪 1、地面光洁 2、普通状态地面 3、潮湿不干净 4、潮湿容易滑倒的地面
疲劳宽放评价项目舆宽放率
评价项目 1、努力度 2、姿势 3、特殊的作业服装舆工具 4、细致程度舆眼部疲劳 5、重复动作舆紧张度 6、单调性 7、创造性注意力
内容 1、较请轻松坐式作业 2、拿轻物上下 3、重劳动、拿重物、移动、偶然休息 4、超重劳动无休息 1、稳定的坐式作业 2、普通步行并携带物品 3、注意力集中的干干净净,姿势不自然 4、急速停止、起动、无法休息 1、无特别处 2、口罩、长筒、草靴、手套等劳保用品有时用 3、基本需佩带上述用品、但偶尔可以拿下 4、不间断使用 1、需要细致作业 2、偶尔需谨慎细致 3、需要小心细致 4、经常需高度小心细致 1、几乎很少有重复 2、偶尔忙碌的需重复动作 3、繁忙且无变化的反复动作 4、强烈反复枯燥重复 1、有一定兴趣并非反复动作 2、一定程度的反复动作 3、很单调但偶尔休息一下 4、不停的、连续单调不能休息的状态 1、不需要 2、需要一点 3、必须具有 4、高度必要
联合分析ppt课件

,这个矩阵包含了两个属性水平的组
合
若有n个属性,则存在 阵
n 2
个兑换矩
15
轮廓法与二因素法 ①完成任务的难易程度。二因素法仅
要求受访者同时根据两个因素进行权 衡,比较容易完成 ②真实性。在对实际产品评价中,是 对所有属性的综合考虑,因此轮廓法 提供了一个更接近现实的设计
联合分析
1
概述
联合分析(conjoint analysis)在许 多文献中也被称为“联合测度”或“ 联系测度”,通过构建受访者对一个 产品组评价综合描述的过程,分析该 受访者的观点
Considered Jointly 按照目标设置不同分为两类:经典联
合分析、基于选择的联合分析
2
经典联合分析,对所观察的产品按受 访者的偏好进行排序
基于选择的联合分析,假定被观察的 产品组是先验选定的,不要求受访者 对于产品进行排序,而是要求受访者 指出对于他最合适的产品组
这两种联合分析共同点,通过产品的 排序或对于产品单个属性的基数成分 效用估值,计算出每个产品的总效用 值
3
例子:新产品引入问题,需要确定该 新产品的哪些属性和指标对于新产品 的引入具有决定意义
βB2*=-0.1667-(-0.1667)=0
43
标准化成分效用值
max jm J
*
*
jm
jm
{
*
}
40.3334
jm
j1 m
A1
0 4.3334
0,
A2
2 4.3334
0.462,
A3
4 4.3334
0.923
4联合作业分析_MM Chart

0.80
0.50 1.40 0.50 0.30 1.40 0.20 0.10
等待
4.55
14 15分
14.55 分 14.55 分
█ Man-Machine 分析
现象, 实测 第4cycle 机械 (1200Tpress) 18 人-① 材料投入 下个材料 投入 步行(Tape4.部品检查 (机械停止) 1.5
〈 问题 〉
1. 将现在的 方法 利用 M-M Chart 画出来 2. 思考改善案,说出其 要点 3. 画 改善后的 M-M Chart 假如 现象的 生产性 为 100% 时 改善后的 生产性 是多少?
练习题(2)
作 业 内 容 1. 拿起 制材原木 (A, B联合作业) 2. 为了 切断 Scrap 推 A, 拉 B 移动到 大纲的位置 3. 与 锯刃 对成 直角(A, B 联合作业) 时间 70 25 7 备注
移动到 原材料 Box里
█ 4W Chart
aluminum 铸造 作业 4W CHART 区分 A 场入口 B C A gas 抽出 B C A 出汤 操作 B C 铸造器 charging plate D E D E 5人 4 3 2 1
s ampling 出汤准备 出汤监视 出汤 操作 材料z装入
●
Scrap 抛进 Scrap 箱子里 (“C”单独) 推制材原木 对准 锯 (“A”单独)
B 等待 求改善后的生产性. A, C 等待
6. 将木材 按 规定尺寸 切断 (“B”单独)
7.
●
●
将切断的 木材 堆积 在 放置场 (“C”单独) 推制材原木 对准 锯 (“A”单独)
B 等待
8. 将木材 按 规定尺寸 切断 (“B”单独)
第12课联合操作分析
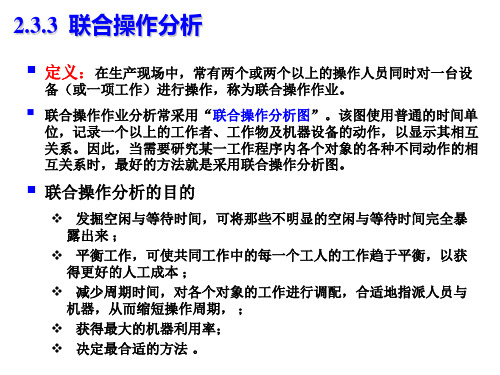
▪ 定义:在生产现场中,常有两个或两个以上的操作人员同时对一台设 备(或一项工作)进行操作,称为联合操作作业。
▪ 联合操作作业分析常采用“联合操作分析图”。该图使用普通的时间单
位,记录一个以上的工作者、工作物及机器设备的动作,以显示其相互 关系。因此,当需要研究某一工作程序内各个对象的各种不同动作的相 互关系时,最好的方法就是采用联合操作分析图。
3箱
联合操作程序图的绘制
▪ 联合操作分析图的绘制与人机操作图基本相同。图的顶部应
有工作名称、研究人员姓名、时间线所代表的单位,是现行 方法还是改良方法的说明。
▪ 绘图时首先要决定一周循环工作的起始点作为一周期,同时 又作为图形的起点和终点。
▪ 将每位操作者或机器设备名称填入各纵栏的顶端。然后根据
时间线,按照个动作的时间分别填入各纵栏内,并用不同的 形式分别表示“工作”、“空闲”或“等待”等。
❖ 堆高机正在运送No.1运板; ❖ 老王在等待; ❖ 老张继续装满No.2运板。
堆高机 老王 老张
min
0
② No.1
3No.Βιβλιοθήκη No.2①6No.2
9
6min 3min 2箱
6min 3min
6min 3min
工作 等待 搬运
2)6W分析(对第1次3min)
❖问:老张完成了什么? ❖答:什么也没做,正在等待。 ❖问:他为什么要这样做?是否必要? ❖答:因为老张要等待运板回来,所以必须等待。 ❖问:有无更好的办法,避免老张空闲? ❖答:老张可以与老王合装一块运板,省去等待运
▪ 填入资料时,应依次填入一个研究对象的动作,填写完毕后
再填写第二个对象的动作,以此类推。
联合操作分析的基本原则
联合作业分析

休 止
因 作業者 作業 , 而 發生的 機械的 停止,空轉
4. 人和人的 聯合作業
○定 議 : 複數 作業者 共同 進行的 作業
○ 分析方法 : 一般是 mantoman 方式
分析體系 順序
作業時間 觀 測 DATA 分 析 聯合作業表 作 成
集
計
改善檢討
•個別時間 •時間一致点 •橫軸-人. 종축-時間 graph化 •Timing 맞춤 •分析記號 •單獨 聯合, 待機別 集計
聯合作業
分
析
聯合作業分析
1. 目 的
•人和人, 人和 機械的 的 作業分擔 •作業量的 不均衡 明確化 •了解 人的 等待, 機械的 非稼動 部分
2. 分析體系
單純作業分析 基本分析 人-人聯合作業分析 聯合作業分析 重点分析 人-機械聯合作業分析
作業分析
3. 聯合作業 分析記號
人
記號 名稱 單獨 作業 說 明 記號 名稱
• 사람의 대기간의 比率減少
• 機械停止時間的 比率減少
• 人和人, 人和 機械的 聯合作業 減少 或 . • (治具的 改善, 機械的 改良, 自動化 等)
• 人和人 聯合作業 因 治具, 機械的 使用等 單獨 作業化
개선후 A 0.50 0.32 0.50 0.26
업
자
B 0.50
1’ 2
재료 넣기
2.50
1.38
1.20 0.60 0.80 0.50 1.40 0.50 0.30 1.40 0.20 0.10 1.00 0.45 0.30 0.20 0.20 0.40 2.00 14.55 분 커버 세트 스토퍼 제거 대기 형꺼냄 호이스트에 걸다 1호기에서 선반에 이동 호이스트 제거 스토퍼 정지 다음형에 호이스트를 걸다 1호기에 이동 호이스트 제거 치구에 넣는다 커버와 스토퍼 세트 0.20 0.60 1.00 0.80 0.50 1.40 0.50 0.30 1.40 0.20 0.10
第五章作业分析 解析

① 取适当的比例尺,如以1cm代表1min。 ② 用垂直竖线把人与机器分开。
析人
机 作 业 分
—
五、 人—机作业分析图
2. 图表部分
③ 分别在人与机器栏内,用规定的符号表示人(或机器)工作
或空闲或人与机器同时工作。并依作业程序和时间由上而下
记录人与机器的活动情况。如用
表示人或机器处于工
析人
机 作 业 分
—
工作部门
表号
统计项目 现行的 改进的 节省效果
产品名称
B239铸件
周程时间/min 2.0 1.36 0.64
作业名称
精铣第二面
人 工作时间/min 1.2 1.12 0.08 空闲时间/min 0.8 0.24 0.56
机器名称 速度v 进给量f 铣削深度ap
时间利用率/% 60% 83% 23% 周程时间/min 2.0 1.36 0.64
时间 机器 (min) 机器
0.2
改进方法 操作者 移开铣成件
量面板深度
0.4
用压缩空气吹净夹具装毛坯
锉锐边,压缩空气清洗之 放入箱内,取新铸件
0.6 0.56 0.8
开动铣削 锉去毛刺,吹净
压缩空气清洗机器 将铸件夹上夹头开机床 进刀
1.0
在铣床台上用样板量深度
1.2
成品入箱,取毛坯至台面
1.4
1.36
1.6
1.36
1.8
2.0
图5-1 精铣铸铁件的人—机作业图(现行方法和改良方法)
例5-2 某车工用自动车床加工轴,资料如下表 表 车工工序及工时
序号
1 2 3 4 5
工序内容
简记
取待加工的零件 装零件找正 车床自动加工零件 卸下零件 对零件打毛刺并存放
挑战IE综合能力之IE分析技法(工程、联合作业、生产线编成分析)

挑战IE综合能力之IE分析技法(工程、联合作业、生产线编成分析)改善思想1运转分析1、运转分析对某件事情进行一日或长时间的观测,再通过生产内容与非生产内容的分析,将其改善为更好的生产系统,以及设定(改订)标准时间的最恰当的闲置率为主目的的技法。
目的:①去除及减少操作者或设备的等待等非生产性因素,按计划进行生产(生产量/纳期的遵守)②通过时间别、日别的生产量或劳动变化的分析,提高生产性及所有资源的有效利用率(生产性的提高)③适当的人、设备、方法的决定(作业标准的设定)④设定标准时间时,决定适当的辅助作业时间或闲置率(标准时间的设定)⑤标准时间的精度或作业标准的检查(1)运转分析方法(2)作业分类(3)记录事例2.抽样对人或机械的运转情况及劳动的种类等进行瞬间观测,并把其结果整理统计,再以统计方式推测各观测项目的时间构成比率、运转率(非运转率)或其推移情况的运转分析技法。
抽样的用途:①了解设备或人的运转②通过掌握保留动力、改善作业分工,来提高运转率,研讨设备增设及增员与否,并掌握流水作业的均衡③有助于以标准资料设定的基础资料的活用,并有助于个别很不规则的操作④决定延迟、闲置率的基础资料⑤发生时间无规律,因此很难计算种类、内容多样的延迟因素各自的时间值,所以一般用百分比来表示。
抽样的特征:①适合作业周期长或“非反复性”作业②适合作业领域广、加工频率高的作业现场分析③实施程序简单,所以不需要对观测者的高度训练④不需要StopWatch等测定仪器,因瞬间观测,可以排解操作者的心理压力⑤观测数量少也可以测定,但比时间研究法(PTS法)观测误差大抽样的原理:①W/S是概率法则为基础。
样品不能存在偏向型。
②某集团里随意抽取的样品一般与原集团的性质类似。
③如增加样品数量,就与某集团的分布曲线(正规分布)是一致的。
④随着样品数的增加,调查费用也会增加,所以应从经济性和信赖度出发决定观测次数(Work Sampling)。
- 1、下载文档前请自行甄别文档内容的完整性,平台不提供额外的编辑、内容补充、找答案等附加服务。
- 2、"仅部分预览"的文档,不可在线预览部分如存在完整性等问题,可反馈申请退款(可完整预览的文档不适用该条件!)。
- 3、如文档侵犯您的权益,请联系客服反馈,我们会尽快为您处理(人工客服工作时间:9:00-18:30)。
1.联合作业分析的目的 2.人员与人员的联合作业分析 3.人员与设备的联合作业分析 4.联合作业的改进
1
1.联合作业分析的目的
1-1. 联合作业分析的目的 在单独作业的基础上,对联合作业的分析主要有以下内容: ·明确单独作业的基础、人员与设备的工作分担 ·明确工作量的不均衡状况 ·了解人员的等待、设备的非运转状况 通过分析把握情况,并通过明确其基本质性因素,更便于找到改善着眼点。 1-2. 作业分析体系
联 合
手 动 停 -3. 分析步骤
观 测作业时间
整理数据
个别时间 时间一致点 横轴:人、纵轴:时间…的图表 调整时机 分析符号
制作联合作业图表
统计
各单独、联合等待的统计
研究改善方案
4
3.人员与设备的联合作业分析
3-1. 关于人员与设备的联合作业分析 即由一名或若干名作业人员操作设备所进行的作业。 人员与设备的作业,不仅关系到工作量的均衡问题,同时可以对设备的停机等待以及高峰 作业(最需要人员的作业)进行了解分析是非常重要的。 3-2. 分析方法 即单独作业要领,对人员及设备周期性生产进行分析.此时,对设备运转周期的观测,将根据作 业人员的具体作业内容进行判断.例如:按电钮后,加工再一次开始等,或自动加工结束时,将 另行测定并根据有关资料计算统计出数据. 人员与设备的联合作业分析,近似于人员与人员的联合作业分析及分析要领.但最大的不同 是:「作业者的内容与设备行程各有专栏」
7
4-3. 改善原则 一切工作为了更有效地进行改善活动. 1. 要考虑排除 2. 要考虑问题的正反两方面 3. 要考虑定数与变数 4. 要考 虑正常与例外 5. 要考虑结合与分离 6. 要考虑集约性与分散性 7. 要考虑扩大 与缩小 8. 要考虑增加与取消 9. 要考虑平行与纵列 10. 要考虑顺序的转换 11. 要考虑普遍性与差异性 12. 要考虑替代与补充 下面详述的4点尤为重要。 ①排除(E:Eliminate) 首先应该考虑这项作业能否取消?不必要者必不为。如果能励行这项原则,那么改善效果的提高已 不成为问题。因此,这项「排除」必先实行于其他一切的改进原则。 ②「结合与分离」(C:Combine) 对很难排除的工作和作业,应周密地考虑用怎样的方法最有效?万不能用成见和偏见对待改善工作。 首先应尝试使用最简便的方法重新编成,这就是「结合与分离」的含义。 ③替代与补充(R:Rearrange) 即研究在何时、以何种方式、怎样进行的作业简化改善,会得到显著效果。 ④要考虑简化(S:Simplify) 要周全地考虑到每项作业的操作应简单轻松缩短移动距离、减轻重量等方面的改善。 ○5W1H的实施着眼点 为什么(Why)———在(理由·目的·结果)的基础上 确认项目 对象项目 →什么(What) → 对象物·范围 →谁(Who) → 人员·设备 →何时(When) → 时间·时刻·时期 →何处(Where)→ 位置·途径·方向 →如何(How) → 步骤·方法 改善的着眼点 → 排除不必要的作业——E →人员的组合与变更 →时间或顺序的结合与变更 C,R →场所的合并与变更 →方法的简化与改善——S
(单独)作业分析
基本分析
人—人联合作业分析 人—机联合作业分析
作业分析
重点分析
联合作业分析
IE方法的联合作业是指:在一人多机或多人共同完成一项作业,或多人共享多台 设备时,为避免时间上的等待对其进行效率改善. 由图表分析发现人和设备的等待、空闲时间.
2
2.人员与人员的联合作业分析(小组作业)
2-1. 人员与人员的联合作业(小组作业) 即由多名作业人员共同进行的作业。例如:由2名员工专职运送材料到大型冲压车间。或由5名员工 进行大件产品的组装。这种小组进行的不总是联合作业,有时也进行单独作业。 2-2. 分析方法 一般用一对一方式进行观测。即由一名员工作业时,就由一名观测人员进行观测。观测时,最好事 先记好联合作业的分析符号(请参照图表—1),这样会更方便些。
图表-1 联合作业图表的分析符号
人 符号 名称 单 独 说 明 与机械及其他作业 者在时间上无关的 作业 与机械及其他作业者 一起作业,有一 方要受到时间制约 的作业 因机械和其他作业 者的作业所造成的作 业者的等待状态 (非运转状态) 符号 名称 自 动
机 械 说 明 与作业者无关的 机械的自动作业 受到时间限制的换型 号、装配、拆卸等作 业者手工进行 的作业活动 因作业者作业操作上 的关系引起的机械的 停机或空转
通过制作图表,能够立即了解人员作业情况和设备运转的具体内容. 即明确以下内容: 作业人员的作业内容
·单独作业 ·联合作业 ·等待
设
备
状
况
·自动加工 ·手工加工 ·停机
5
3-3. 分析步骤 观 测 作 业 时 间 分 析 设 备 行 程 研 究 改 善 方 案
制作 联合 作业 图表
统
计
3-4. 4W分析方法 如同熔炉作业般由数名作业人员以联合或分担形式进行的,并移动于若干工位间的生产作业。 一般这种作业的生产周期较长。分析这种作业时,最好使用图表—5所示4W进行分析。 这种4W内增加了联合作业图表中明确「场所」项目的内容,经分析可明确下述几项。 谁 什么 何时 何地 (Who) (What) (When) (When)
6
4.联合作业的改善
4-1. 改善着眼点 ·缩短作业人员等待时间 ·降低机械设备的停机比率 ·减少人员与人员、人员与设备的联合作业,最终努力取消这种作业。 (改进夹具、改良设备、实现生产自动化等) ·通过夹具·机械设备使用,实现人员与人员联合作业的单独作业化 4-2. 改善目的 改善目的就在于必须要「重点思考」 无论多具有魅力的改善课题,如果改进习惯不能达到生产的要求程度,那么必须优先考虑其 他项目。判断的正确与否是改善实施过程中的重要因素之一。 重点思考的判断要点 ①提高生产安全性,减轻疲劳程度 ②提高产品质量 ③提高生产效率 ④削减经费开支 要满足以下条件: 安全地—————— 让作业员工能安心地工作 轻松地—————— 减轻作业人员的劳动强度 优质地—————— 提高产品质量 节俭地—————— 尽量减少经费开支