生产线平衡和计算..
生产线平衡

生产线平衡率的计算方法
平衡率是评价一条产线的重要指标,平衡率高就表示在同等 条件下平衡损失就少,也就是说平衡率高的产线人均产能就 高。
目的:通过平衡生产线提高生产效率同时使生产现场更 加容易理解“一个流”的必要性及对于真正实现“OPF”进 而导入“cell production”的重要意义。
平衡生产线的意义
游戏时间
平衡生产线的意义
通过Line balancing我们可以达到以下几个目的:
有效减少工时损失进而提高作业员及设备工装的工作效率; 减少产品的C/T和pitch time,最终导致Takt time 的减少,提高productivity. 提高OEE & OME. 减少WIP,更容易真正实现“OPF”。 在Line balancing 基础上,实现单元生产,提高了生产对柔性化市场的应变能 力。
Line balance rate = ∑Standard time/(bottleneck time*person qty) = ∑ Standard time/(Pitch time*person qty)
Line imbalance rate =1-Line balance rate
Remark: Pitch time 是指生产线每产出一个batch产品所消耗 的时间,这里我们定义batch size 为1pcs, 所以pitch time=bottleneck time, 理想情况下pitch time=Takt time.
1.不同产品的特性差异
产线平衡率计算公式标准
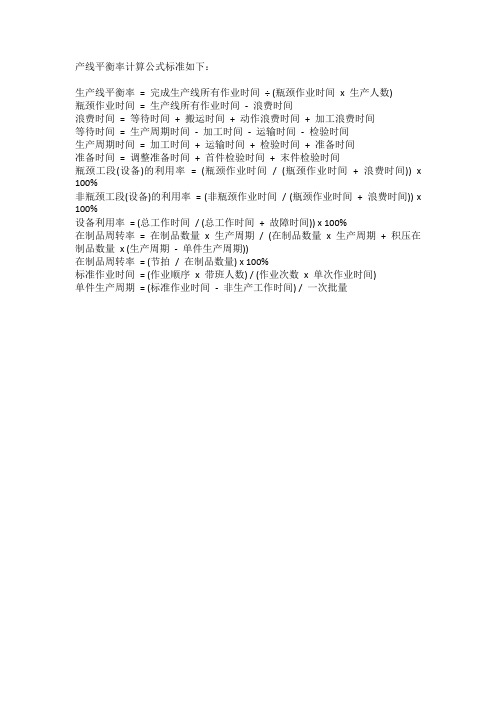
产线平衡率计算公式标准如下:
生产线平衡率= 完成生产线所有作业时间÷ (瓶颈作业时间x 生产人数)
瓶颈作业时间= 生产线所有作业时间-浪费时间
浪费时间= 等待时间+ 搬运时间+ 动作浪费时间+ 加工浪费时间
等待时间= 生产周期时间-加工时间-运输时间-检验时间
生产周期时间= 加工时间+ 运输时间+ 检验时间+ 准备时间
准备时间= 调整准备时间+ 首件检验时间+ 末件检验时间
瓶颈工段(设备)的利用率= (瓶颈作业时间/ (瓶颈作业时间+ 浪费时间)) x 100%
非瓶颈工段(设备)的利用率= (非瓶颈作业时间/ (瓶颈作业时间+ 浪费时间)) x 100%
设备利用率= (总工作时间/ (总工作时间+ 故障时间)) x 100%
在制品周转率= 在制品数量x 生产周期/ (在制品数量x 生产周期+ 积压在制品数量x (生产周期-单件生产周期))
在制品周转率= (节拍/ 在制品数量) x 100%
标准作业时间= (作业顺序x 带班人数) / (作业次数x 单次作业时间)
单件生产周期= (标准作业时间-非生产工作时间) / 一次批量。
生产线平衡计算

目相同情况下,作业时间最长的工序先排
规则2:遵循作业手顺原则,防呆性,不可拆分性
规则3:缩小空闲时间,减少周转等待时间
5-2、 排 工 位:
5-3、排工位:
2
1
1
A
B
G
2.4
H
C
D
E
F
3.25
1.2
.5
1
工序
A C D B E F G H
The end, thank you!
BA C None D A, C
2
1
1
A
B
G
C
D
E
F
3.25
1.2
.5
1
工序 E F G H
先行工序 D E B E, G
2.4 H
瓶颈C/T=1.2s ≤T/T = 3600/3000=1.2 s
3-1、确定瓶颈CT
1.0 A
C 1.08
1.0
1.0
B
G
1.2
H
D
E
F
1.2
0.5
1.0
瓶颈C/T=2.4s ≤T/T = 3600/1500=2.4s
后接工序数C/T (S)
6
2
4
3.25
3
1.2
2
1
2
0.5
1
1
1
1
0
2.4
工位 1
工位 2
工位 3
工位 4 工位 5
A (3.25-2=1.25) C (3.25-3.25)=0 E (3.25-0.5)=2.75 B (3.25-1)=2.25 H1.25-1.2=0.05)
生产线平衡计算范文
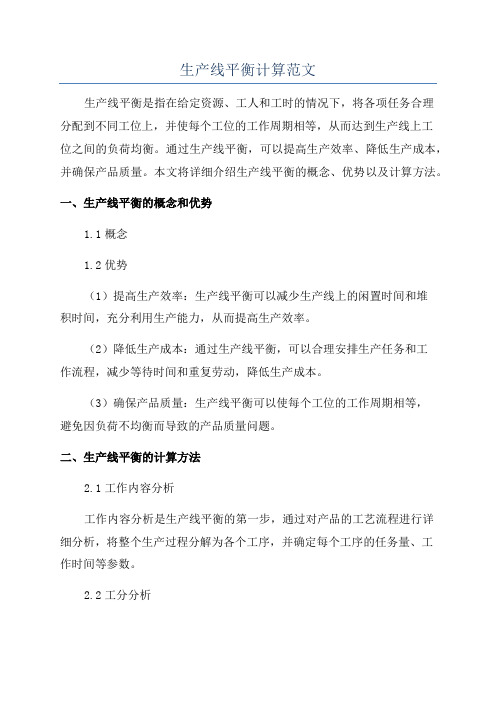
生产线平衡计算范文生产线平衡是指在给定资源、工人和工时的情况下,将各项任务合理分配到不同工位上,并使每个工位的工作周期相等,从而达到生产线上工位之间的负荷均衡。
通过生产线平衡,可以提高生产效率、降低生产成本,并确保产品质量。
本文将详细介绍生产线平衡的概念、优势以及计算方法。
一、生产线平衡的概念和优势1.1概念1.2优势(1)提高生产效率:生产线平衡可以减少生产线上的闲置时间和堆积时间,充分利用生产能力,从而提高生产效率。
(2)降低生产成本:通过生产线平衡,可以合理安排生产任务和工作流程,减少等待时间和重复劳动,降低生产成本。
(3)确保产品质量:生产线平衡可以使每个工位的工作周期相等,避免因负荷不均衡而导致的产品质量问题。
二、生产线平衡的计算方法2.1工作内容分析工作内容分析是生产线平衡的第一步,通过对产品的工艺流程进行详细分析,将整个生产过程分解为各个工序,并确定每个工序的任务量、工作时间等参数。
2.2工分分析工分分析是生产线平衡的核心,它是通过对每个工序进行工分,确定工序之间的工作时间差异,从而找出负荷不均衡的工位并进行调整。
工分分析的具体步骤如下:(1)确定标准工时:通过工作内容分析,确定每个工序的标准工时,即完成该工序所需的工作时间。
(2)计算工序机器机械劳动时间(MCT):根据标准工时和工龄调整系数,计算每个工序的机器机械劳动时间。
(3)计算工序人工劳动时间(HCT):根据标准工时和人工劳动调整系数,计算每个工序的人工劳动时间。
(4)计算工序总工时(TCT):将机器机械劳动时间和人工劳动时间相加,得到每个工序的总工时。
(5)计算累积工时(ACT):根据每个工序的总工时,计算每个工位的累积工时。
(6)计算工位工作周期(WCT):根据工位数量和生产线的工作时间,计算每个工位的工作周期。
2.3进行负荷均衡调整负荷均衡调整是通过调整工位之间的任务分配,使各个工位的工作周期接近,从而实现生产线平衡。
生产线平衡计算
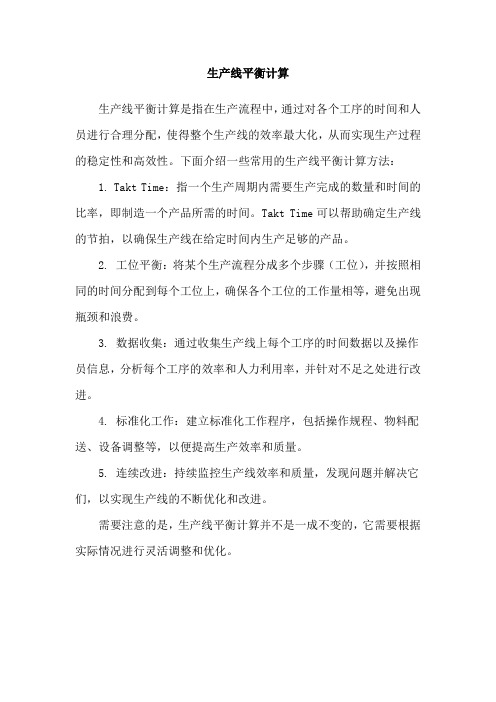
生产线平衡计算
生产线平衡计算是指在生产流程中,通过对各个工序的时间和人员进行合理分配,使得整个生产线的效率最大化,从而实现生产过程的稳定性和高效性。
下面介绍一些常用的生产线平衡计算方法:
1. Takt Time:指一个生产周期内需要生产完成的数量和时间的比率,即制造一个产品所需的时间。
Takt Time可以帮助确定生产线的节拍,以确保生产线在给定时间内生产足够的产品。
2. 工位平衡:将某个生产流程分成多个步骤(工位),并按照相同的时间分配到每个工位上,确保各个工位的工作量相等,避免出现瓶颈和浪费。
3. 数据收集:通过收集生产线上每个工序的时间数据以及操作员信息,分析每个工序的效率和人力利用率,并针对不足之处进行改进。
4. 标准化工作:建立标准化工作程序,包括操作规程、物料配送、设备调整等,以便提高生产效率和质量。
5. 连续改进:持续监控生产线效率和质量,发现问题并解决它们,以实现生产线的不断优化和改进。
需要注意的是,生产线平衡计算并不是一成不变的,它需要根据实际情况进行灵活调整和优化。
生产线平衡的计算及改善方法
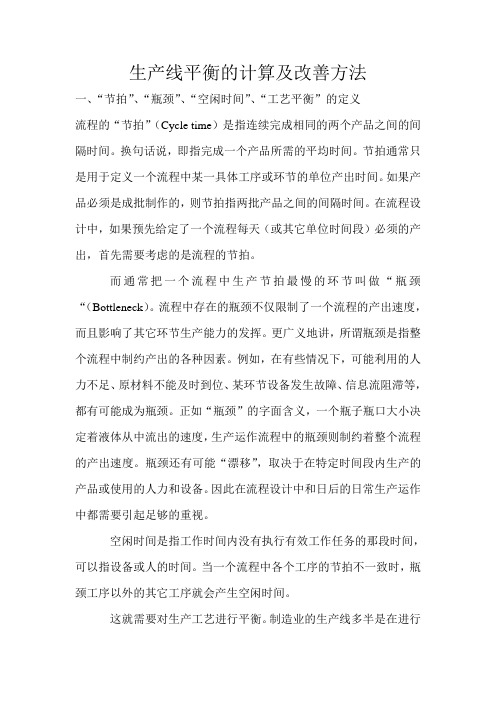
生产线平衡的计算及改善方法一、“节拍”、“瓶颈”、“空闲时间”、“工艺平衡”的定义流程的“节拍”(Cycle time)是指连续完成相同的两个产品之间的间隔时间。
换句话说,即指完成一个产品所需的平均时间。
节拍通常只是用于定义一个流程中某一具体工序或环节的单位产出时间。
如果产品必须是成批制作的,则节拍指两批产品之间的间隔时间。
在流程设计中,如果预先给定了一个流程每天(或其它单位时间段)必须的产出,首先需要考虑的是流程的节拍。
而通常把一个流程中生产节拍最慢的环节叫做“瓶颈“(Bottleneck)。
流程中存在的瓶颈不仅限制了一个流程的产出速度,而且影响了其它环节生产能力的发挥。
更广义地讲,所谓瓶颈是指整个流程中制约产出的各种因素。
例如,在有些情况下,可能利用的人力不足、原材料不能及时到位、某环节设备发生故障、信息流阻滞等,都有可能成为瓶颈。
正如“瓶颈”的字面含义,一个瓶子瓶口大小决定着液体从中流出的速度,生产运作流程中的瓶颈则制约着整个流程的产出速度。
瓶颈还有可能“漂移”,取决于在特定时间段内生产的产品或使用的人力和设备。
因此在流程设计中和日后的日常生产运作中都需要引起足够的重视。
空闲时间是指工作时间内没有执行有效工作任务的那段时间,可以指设备或人的时间。
当一个流程中各个工序的节拍不一致时,瓶颈工序以外的其它工序就会产生空闲时间。
这就需要对生产工艺进行平衡。
制造业的生产线多半是在进行了细分之后的多工序流水化连续作业生产线,此时由于分工作业,简化了作业难度,使作业熟练度容易提高,从而提高了作业效率。
然而经过了这样的作业细分化之后,各工序的作业时间在理论上,现实上都不能完全相同,这就势必存在工序间节拍不一致出现瓶颈的现象。
除了造成的无谓的工时损失外,还造成大量的工序堆积即存滞品发生,严重的还会造成生产的中止。
为了解决以上问题就必须对各工序的作业时间平均化,同时对作业进行标准化,以使生产线能顺畅活动。
“生产线工艺平衡”即是对生产的全部工序进行平均化,调整各作业负荷,以使各作业时间尽可能相近。
生产线平衡计算
G (2.25-1)=1.25
Idle=0.05
Idle = 0
Idle = 1.75
Idle = 1.25 Idle = 0.85
生产线平衡 - 19
5-4、排工位:
工作站1
2
A
工作站3
1
1
B
G
工作站5
1.4 H
C 3.25
工作站2
D 1.2
工作站1
E
F
.5
1
工作站4
生产线平衡 - 20
6、产线平衡率计算
瓶颈C/T=1.2s ≤T/T = 3600/3000=1.2 s
1.0
1.0
1.0
A
B
G
1.2
H
C
D
1.08
1.2
生产线平衡 - 13
E
F
0.5
1.0
3-2、拟定瓶颈CT
瓶颈C/T=2.4s ≤T/T = 3600/1500=2.4s
2.0
1.0
1.0
A
B
G
2.4
H
C
D
E
F
1.63
1.2
0.5
1.0
生产线平衡 - 2
瓶颈时间
时间
T2
瓶颈时间
T1
T3
T4
T5
S1 S2 S3
S4
S5
工站
生产线作业工时最长旳工站旳原则 工时称之为瓶颈。
产出旳速度取决于时间最长旳工站
生产线平衡 - 3
生产节拍
生产节拍 指生产线上连续出产两件相同制品旳时 间间隔。它决定了生产线旳生产能力、 生产速度和效率。 工作时间 节拍时间:Tact Time = 目的量
IE-生产线平衡
二、生产线平衡的计算
1.生产线平衡率与平衡损失率
衡量生产线平衡状态的好坏。
生产线平衡率= 各工序(工位)时间总和 作业周期×作业资源数
生产线平衡损失率=1-生产线平衡率
作业周期(CT—Cycle Time):生产线工序(工位)时间 最长的工序(工位)时间(瓶颈工序时间)。
CT=瓶颈工序单位产品产出时间
10 8 6 4 2 2 0 S1 S2 S3 0 1.5 1.5 0.5 4 6 3.5 0 1.5 0 1 2 1 3 1 0.5 S4 1.5 2 0 1 3 2 S5 0.5 1.3 2 1.5 2 3.5 1.8 S6 S7 0 1 3 0 1 2 4 3 2 1 S8 5 2 0.5 1 0.5 1.5 1 4 1 1.5 2.5 5 0 1 2 0.5 1 2 1.5 6.5 2.5 4 1 工站 0 2 0 1 2
四、生产线布局
合理的生产布局能够保证物料顺畅流动,减少无价
值的搬运动作,提高现场的管理透明度和生产效率。
1.无价值的搬运动作 搬运 倒退让路 排除路障 堆码、清点、整理、寻找 停顿与返回
考虑弹性生产线布置时追求的目标: (1)及时发现浪费 (2)灵活调整生产量 品质方面 优先使用不会产生次品, (3)考虑相关部门的浪费
秒
產品xxx工時山積表 M5 M4 M3 M2 M1
0
0 2 1 2 2
S9 S10 S11 S12 S13 S14 S15 S16
三、生产线平衡改善方法
1.生产线平衡改善的原则与方法
(1)原则
对瓶颈工序进行作业改善,如:良率、效率、设备开动率;
增加瓶颈工序的作业资源数; 分解瓶颈工序的作业内容;
生产线上产品分布不均的原因:
生产线平衡
= 94%
六、生产线平衡改善方法
1、首先应考虑对瓶颈工站进行作业改善,将瓶颈工站的 作业内容适当分给其它工位,依照动作经济原则,ECRS 方法及动作分析、工装自动化及IE七大手法等。 2、考虑瓶颈工站增加作业人员,提高生产线平衡率,人 均产出提高了,单位产品成本就下降了。
3、考虑取消作业时间过短的工位,将其作业内容分给其 它工位,精减人员,提高平衡率,节约成本。
工 作 時
增 加 节
間
拍
时
间
工序 1 2 3 4 5
降低线体速度,减少生产产量
工 作 時 間 工序 1 2 3 4 5
减少人力(2人)
因生产需求量降低而 可降低线体速度
将工序3﹑4的工作时 间分配至工序 1﹑2﹑5里﹐从而工 序3﹑4工作岗位的人 手可调配至其它生产 线去。
(4) 4种增值的工作
生产线平衡
• 制造工程部 • 2016-5-5
一、生产线平衡定义
什么是生产线平衡
生产线平衡是指构成生产线各道工序所需的 时间处于平衡状态,作业人员的作业时间尽 可能的保持一致,从而消除各道工序间的时 间浪费,进而取得生产线平衡。
对生产的全部工序进行均衡,调整作业 负荷和工作方式,消除工序不平衡和工 时浪费,实现“一个流”。
五、生产线平衡率计算实例
工位 装饰件来料全检
SIM卡塞点胶 装钢片、压合sim卡塞钢片
保压sim卡塞 装/热熔侧键
人数 1 1 1 1 1
标准工时 6.6 6.0 6.8 6.5 7.0
平衡率= ∑瓶(颈各岗工位序时的间作*业人时数间)* 100%
=
6.6+6.0+6.8+6.5+7.0 * 100% 7.0*5
生产线平衡率的计算
生产线平衡率的计算一、介绍在生产线的运作中,生产线平衡率是一个非常重要的指标。
它可以帮助企业管理者了解生产线的运作效率和生产效果,并为之后的决策提供依据。
本文将详细介绍生产线平衡率的计算方法。
二、计算方法生产线平衡率的计算方法是将生产线在一定时间内各工序的完成时间进行记录,并根据记录的时间来计算每个工序所占生产时间的比例(即产能率),最后计算出生产线整体的平衡率。
假设生产线上有三个工序,分别为A、B、C,它们的完成时间分别为2、3、4小时。
则在一定时间内,它们各自的产能率分别为:A: 2/(2+3+4) = 0.222B: 3/(2+3+4) = 0.333C: 4/(2+3+4)=0.444整个生产线的平衡率可以通过它们各自产能率的标准差来计算,计算公式如下:生产线平衡率 = 1 - (标准差/平均值)其中,标准差指各工序产能率与平均值之差的平方和的平均数的平方根,平均值指各工序产能率的平均值。
三、误区在计算生产线平衡率时,有些企业常常会犯一些误区。
比如,某些企业只关注生产线产能的总量,而忽略了各个工序的配比问题,导致每个工序的生产量差距较大。
这会导致生产线的平衡率过低,从而降低了生产效率。
另外,一些企业在计算生产线平衡率时,容易受到某个生产环节的瓶颈制约,而忽略了其他环节的运作效率。
这也会导致生产线的平衡率过低,从而影响整个生产流程的效率。
四、总结生产线平衡率是一个反映企业生产效率的重要指标。
通过对生产线各个环节的分析和生产时间的记录,可以计算出生产线的平衡率,帮助企业管理者了解生产线的整体情况,及时调整生产流程和工艺,提高生产效率,提高企业的市场竞争力。
同时,在计算生产线平衡率时,企业管理者也应该注意避免一些常见的误区,以保证计算结果的准确性和可靠性。
- 1、下载文档前请自行甄别文档内容的完整性,平台不提供额外的编辑、内容补充、找答案等附加服务。
- 2、"仅部分预览"的文档,不可在线预览部分如存在完整性等问题,可反馈申请退款(可完整预览的文档不适用该条件!)。
- 3、如文档侵犯您的权益,请联系客服反馈,我们会尽快为您处理(人工客服工作时间:9:00-18:30)。
生产线平衡把握9条原则
1、重要的是平衡物流,不是平衡能力。(不要绝对平衡 节拍和设备能力)
2、非瓶颈资源的利用率是由系统其它约束条件决定的, 而不是由其本身能力决定的。
3、让一项资源充分开动运转起来与使该项资源带来效益 不是同一涵义。
4、在瓶颈资源上损失一小时,是整个系统损失一小时。 5、想方设法提高非瓶颈资源生产率是徒劳的、无益的。 6、产销量和库存量是由瓶颈资源决定的,即瓶颈控制了 库存和产销率。
间最长的任务先排
6、产线平衡率计算
效率
=
任务时间总和 (T) 实际工位数目 (Na) x 瓶颈节拍
(CT B
)
效率
=
11.35 mins/台 (3)(4.1min s/台)
=
.923
案例
某生产线共有11道作业工序,测试现有工序作业时间 如下:
工序号 1 2 3 4 5 6 7 8 9 10 11
工序 1
2
34
5
67
8
9
10 11
分 钟 76.1 121.4 41.4 33.7 145.8 224 111.3 128.1 110.5 112.3 37.1
各个工序为完成600件任务所需要时间差别很大,最长需 要224分钟,而最短只需要33.7分钟。这样第4工序一天就产 生了190.3分钟空闲和等待,实际工作时间还不到等待时间18 %。又如第6工序作业时间是22.4秒,第7工序是11.13秒, 也就是说每生产1件,第7工序就会产生11.27秒等候时间损 失,即一半时间是处在等候加工。仍然按照每天600件计算, 第7工序等候时间就达到112.7分钟,综合考察整个生产线, 一天发生等候时间将有5个小时之多,无法做到同步化生产,
生产线平衡率
平衡率是衡量流程中各工站节拍符合度的一个 综合比值﹔ 单件标准时间总和 平衡率= ----------------------×100% 瓶颈时间×工站数
平衡率的目标:与大设备相连≧85% 其它≧ 95%
平衡率100%意义
1、工站之间无等待,前后产能一致 2、工站节拍相同﹐动作量相同(动作量是 指工站中各种必要动素的时间总量) 3、平衡损失时间为零 4、设计效率最大化 5、前后流程的设计可以更完善
工序
1
2
3
4
5
6
7
8
作业时间 13.63 15.09 14.01 15.75 12.81 11.05 11.23 3.71 (秒)
20 15 10
5 0
12 34 56 78
新工序号
作业时间 (秒)
生产线平衡后,各工序能力得以基本均衡,除第 8工序外,各工序作业时间均在11秒至15.75秒之 间,为实现同步化生产提供了可靠保证。而第8 工序是最后一道下线工序,尽管作业时间很低, 但对其他工序并不产生任何影响。生产线平均效 率达到了77.2%,比原来提高了30.9%。与此同 时,由于各工序作业时间基本接近,工序间在制 品大大降低,有效地保证了零件在工序间的“一 个一个流动”。因能力不平衡造成等候时间损失 大为减少,由原来5小时减少到2小时;生产线人 数已减少一人;生产能力提高,体现在生产效率 比原来提高了11.1%。
对瓶颈工序,采取下列措施,以缩短作业时间: ⑴ 部分独立作业内容,分解给时间较短工序; ⑵ 消除不必要操作和动作,如弯腰、折腾等; ⑶ 改进集装器具; ⑷ 增加必要设备及必须人员。 对作业时间最短工序,则从下列方面考虑:
⑴把此工序内容全部进行分解给其他工序,不要 这道工序; ⑵或合并同类项,组成一个新工序;
返修记录
设备检查
1、设备开机前注油 了吗?有记录吗? 2、电器检查了吗? 有记录吗? 3、焊机、焊枪、电 缆检查吗?有记录 吗? 4、按日检点卡的要 求做了吗?有记录 吗?
平 安 角
时间(Mins) 任务描述 2 装配外框 1 安装开关
3.25 装配马达架 1.2 将马达架装入外框 0.5 安装扇叶 1 安装格栅 1 安装电缆 1.4 测试
紧前务 无 A 无 A, C D E B F, G
1、确定TT
假定我们每天要装配100台风扇。周期时间 应是多少?
要求的
Tak t.Time
,
TT
=
每期的生产时间 每期要求的产出
TT
=
420 mins/天 100台/天
=
4.2 mins/台
2、画优先图
任务 紧前任务
2
1
A
B
任务 1
G
紧前任务 1.4 H
C
D
E
F
3.25
1.2
.5
1
3、确定CT
察看哪一个工序决定了最大产出率?
2
1
1
A
B
G
1.4
H
C
D
E
F
3.25
1.2
.5
1
任务C决定了生产线的CT,也就决定了最大 产出率
⑶或从其他工序移植部分作业内容,增加该工序 工作量。
IE 工作
世界上最大的浪费, 莫过于动作的浪费。
—吉尔布雷斯
关注你这双手
移
动 动
5cm 2.5cm
15cm
作
M1
M2
M3
30cm M4
45cm M5
1 MOD = 0.129 Sec = 0.00215分
1 Sec = 7.75 MOD 1 min = 465 MOD
作业时间 7.61 12.14 4.14 3.37 14.58 22.4 11.13 12.81 11.0 11.23 3.71
(秒)
根据以上作业时间,画出以下时间 曲线:
25 20 15 10 5 0
1 2 3 4 5 6 7 8 9 10 11
工序号 作业时间(秒)
从时间曲线可以明显看出,各工序的能力 很不均衡,作业时间最短的只有3.37秒
2、合并作业 省略工序
1人
作
业
2人
时
间
工序 1 2 3 4 5
3、减 人
生产线平衡排程步骤
1. 计算产距时间(Takt time) 2. 画优先图 3. 决定周期时间(CT=Takt time) 4. 确定理论工位数 5. 排程 6. 计算平衡率
生产线平衡案例
电风扇装配由下列任务组成:
任务 A B C D E F产能
作 业 时 间
工序 1 2 3 4 5
1、分割作业
作 业 时 间
工序 1 2 3 4 5
2、缩短时间
1人
作
2人
业
时
间
工序 1 2 3 4 5
3、增加人员
生产线平衡改善
2、减少人员
作 业 时 间
工序 1 2 3 4 5
1、分割作业 省略工序
作 业 时 间
工序 1 2 3 4 5
锅筒焊装线生产看板(OP01~02)
今天 您做了吗?
1、清扫— 您的工 位清扫了吗? 2、清洁— 您的工 位清洁吗? 3、整理— 用过的 物品整理了吗? 4、整顿— 用过的 物品摆到位吗? 5、素养— 养成5S 良好习惯吗?
关键工艺要求 关键控制点
1.清理坡口及两侧20mm 范围内的氧化皮、油锈、 水等杂物,使之露出金 属光泽。 2、采用埋弧焊要求先焊 内侧,焊满。 3、背面碳弧气刨清根, 砂轮机打磨后,采用埋 弧焊填满盖面。 4、清理焊缝周围熔渣,
1、点固引熄弧板,带 有焊接试板时,试板点 固在纵缝的延长部位。 2、筒节不符合以下要 求时应进行校圆,校圆 后应满足以下要求: 同一断面dmaxdmin≤4mm 棱角度≤3mm。
并按规定打焊工钢印。
焊工操作规程
1、电焊、气焊均为特殊工种, 经专业安全技术学习、训练和 考试合格,颁发“特殊工作操 作证”后,方能独立操作。 2、电焊机接地零线及电焊工作 回线都不准搭在易燃易爆的物 品上,也不准接在管道和机床 上,工作回线应绝缘良好,机 壳接地必须符合安全规定。 3、详见焊工操作规程。
这不仅仅是在单位时间内没有创造任何价值,更重要是每个 工序按一人计算,就损失了11个人工资费用以及影响交货, 不能快速响应市场,甚至失去市场。
改进方法:
运用工业工程(IE)中的八个字:“排除”、“组 合”、“替换”、“简化”。 “排除” →消除一些不必要作业及搬运动作; “组合” →两个或两个以上工序或工位组合成一个 ,或重新划分工序,以平衡各工序工作量; “替换” →用另一种方法或工艺代替,如工具、及 搬运手段的替代; “简化” →将作业动作简化,或将某工序一部分作 业内容分解出去。
4、确定理论最少工位数
理论上的最少工位数是多少?
理论最少工位数, Nt 任务时间总和(T)
Nt = Takt Time (TT)
Nt
=
11.35 mins/台 4.2 mins/台
= 2.702,
or 3
5、排程
主规则: 紧后工序数目最多的工作优先安排。
附加规则: 紧后工序数目相同情况下,作业时
瓶颈时间
时间
T2
瓶颈时间
T1
T3
T4
T5
S1 S2 S3
S4
S5
工站
生产线作业工时最长的工站的工时 称之为瓶颈。
产出的速度取决于时间最长的工站
节拍
节拍 指生产线上连续出产两件相同制品的时 间间隔。它决定了生产线的生产能力、 生产速度和效率。 工作时间 产距时间:Takt Time = 销售量
目标:按需求组织生产!
(第四工序),而最长的达22.4秒(第六 工序),是最短工序的6倍多,也就是说6 工序干一件活的时间,4工序可以干6件。 这样必然导致工序间在制品积压,设备和
人员等待,工时利用率和生产效率低。作