电化学(电解)去毛刺的基本原理
高频脉冲电化学去毛刺
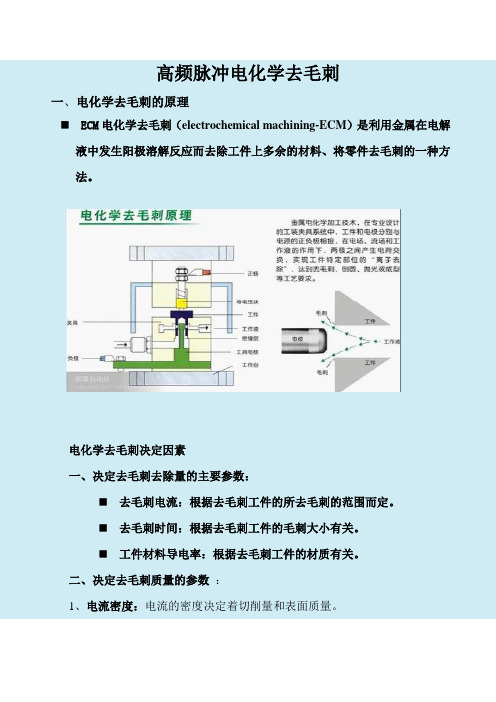
高频脉冲电化学去毛刺一、电化学去毛刺的原理⏹ ECM电化学去毛刺(electrochemical machining-ECM)是利用金属在电解液中发生阳极溶解反应而去除工件上多余的材料、将零件去毛刺的一种方法。
电化学去毛刺决定因素一、决定去毛刺去除量的主要参数:⏹ 去毛刺电流:根据去毛刺工件的所去毛刺的范围而定。
⏹ 去毛刺时间:根据去毛刺工件的毛刺大小有关。
⏹ 工件材料导电率:根据去毛刺工件的材质有关。
二、决定去毛刺质量的参数:1、电流密度:电流的密度决定着切削量和表面质量。
2、电导率:电化学液的浓度决定着电导率,单位[mS]。
根据去毛刺要求,电化学液的浓度应控制在8%-25%.(根据实际工件)。
当然,温度对电导率也有影响。
3、间隙:夹具(阴极)和工件(阳极)之间的间隙决定着电流大小和电解液的冷却能力。
4、电化学液压力:间隙中电化学液的压力影响着电流和材料的去除,它同时决定着电解液的流量和流速。
5、电化学液温度:温度影响着电解液的传导率,根据去毛刺要求,温度应控制在20℃到35℃。
(根据产品而定)6、电化学液的PH值:电化学液的PH值应该控制在6.5到8.5之间,(根据产品而定)电化学液的PH值决定着电解液的浓度和质量。
7、电化学液的纯度:纯净的电化学液能确保恒量生产,并且可防止工件和/或夹具被阻塞。
电化学液在工作的作用⏹ 为电化学去毛刺提供电路导通。
⏹ 冷却夹具。
⏹ 冲走去毛刺中产生的废屑。
电化学加工的反应(钢在与NaCl水溶液)一、阳极反应⏹ Fe—2e Fe+2⏹ Fe—3e Fe+3⏹ 4OH-—4e O2↑+2H2O⏹ 2CL-—2e CL2 ↑⏹ Fe+2+2OH- Fe(OH)2↓(墨绿色的絮状物)⏹ 沉淀为4Fe(OH)2+2H2O+O2 4Fe(OH)3↓(黄褐色沉淀)二、阴极反应(按可能性为)⏹ 2H++2e H2↑⏹ Na++e Na↓⏹ 按照电极反应的基本原理,电极电位最正的粒子将首先在阴极反应。
电解去毛刺技术在农业装备制造中的应用研究
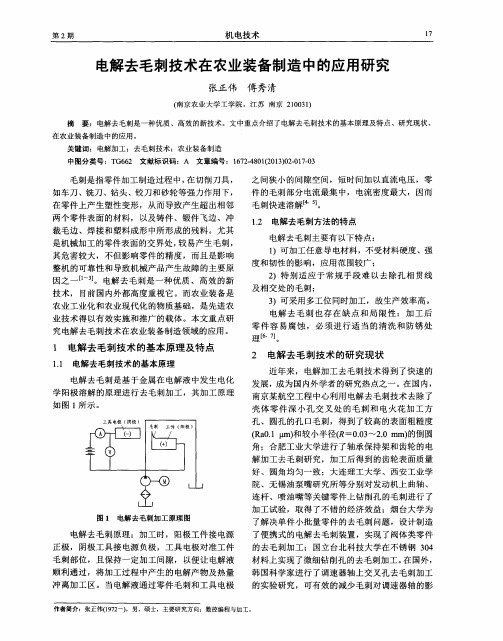
加 工 试验 ,取 得 了不错 的经济 效益 ;烟 台大学 为
图1 电解 去 毛 刺 加 工 原 理 图
了解 决单 件 小批 量零件 的去毛 刺 问题 ,设 计制造 了便 携 式的 电解 去毛 刺装 置 ,实现 了阀体 类零 件 的去 毛刺 加工 ;国立 台北 科技 大 学在 不锈钢 3 0 4 材 料 上实 现 了微细钻 削孔 的去毛刺 加工 。 在 国外 , 韩 国科 学 家进 行 了调速 器 轴上 交 叉孔去 毛刺 加 工 的实 验研 究 ,可有 效 的减 少毛 刺对 调速 器 轴 的影
作者 简介 :张 正伟 ( 1 9 7 2 一) ,男 硕 士 ,主 要研 究方 向:数控 编程 与加 工 。
l 8
响 ,提 高产 品 的质 量[ 8 - 1 2 J 。
机 电技 术
2法 ,不但 费时 费力而 且还 不 能很好 的去 除毛刺 。 喷油泵 需在 高速 、 高压 的环境 中工 作 ,其质 量 的好 坏直 接影 响 了整个 柴油机 的经济和 动 力性 能 ,而如 果喷 油嘴在 工作 时毛 刺脱 落 ,还会 形成 油路 堵塞而 造成 事故 。如 图 2所 示 的大马力 柴油 发动机 中的高 压喷油 泵装 置 。高压 油通 过其 腔 内 若干 直径为 3 mm 的细长 小孔进 入发 动机 ,各小
电解 去毛刺 原 理 :加 工时 ,阳极 工件 接 电源
正 极 ,阴 极工 具接 电源 负 极 ,工具 电极对 准工 件
毛 刺 部位 ,且 保持 一 定加 工 间隙 , 以便让 电解 液
顺 利通 过 ,将 加工 过程 中产 生 的 电解产 物及 热 量 冲 离加 工 区 。当 电解液 通 过零 件毛 刺 和工 具 电极
2 )特 别 适 应 于 常规 手段 难 以去 除孔 相 贯 线 及 相 交处 的毛刺 ;
用电解法去除齿轮上的毛刺
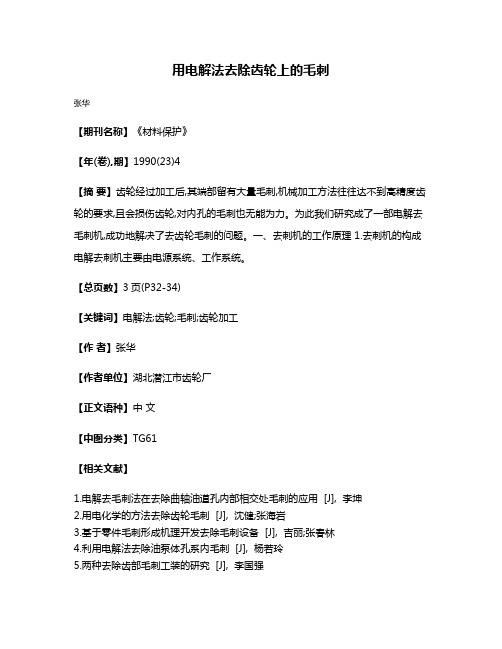
用电解法去除齿轮上的毛刺
张华
【期刊名称】《材料保护》
【年(卷),期】1990(23)4
【摘要】齿轮经过加工后,其端部留有大量毛刺,机械加工方法往往达不到高精度齿轮的要求,且会损伤齿轮,对内孔的毛刺也无能为力。
为此我们研究成了一部电解去毛刺机,成功地解决了去齿轮毛刺的问题。
一、去刺机的工作原理 1.去刺机的构成电解去刺机主要由电源系统、工作系统。
【总页数】3页(P32-34)
【关键词】电解法;齿轮;毛刺;齿轮加工
【作者】张华
【作者单位】湖北潜江市齿轮厂
【正文语种】中文
【中图分类】TG61
【相关文献】
1.电解去毛刺法在去除曲轴油道孔内部相交处毛刺的应用 [J], 李坤
2.用电化学的方法去除齿轮毛刺 [J], 沈健;张海岩
3.基于零件毛刺形成机理开发去除毛刺设备 [J], 吉丽;张春林
4.利用电解法去除油泵体孔系内毛刺 [J], 杨若玲
5.两种去除齿部毛刺工装的研究 [J], 李国强
因版权原因,仅展示原文概要,查看原文内容请购买。
ZOTEC佐技高精度零件去毛刺抛光机的原理

ZOTEC佐技高精度零件去毛刺抛光机的原理磁力抛光机,又被称为磁力去毛刺机,振动研磨机、磁力清洗机,其特有的网状结构交替变化电磁场在金属材料产品工件内产生立体式电磁感应现象功效,进而使产品工件造成转动、滚翻等姿势,与此同时网状结构交替变化电磁场推动经特殊工艺解决的磁力磨研钢针,造成多方位立体式网状结构快速盲射运动,与产品工件造成多方位冲击性撞击,进而起着混合、研磨、去毛刺、打磨抛光、清洗的功效。
对于机械加工去毛刺,冲压加工去毛刺,压铸件去毛刺,不规则的五金件去毛刺,内孔去毛刺,交叉孔去毛刺,异形孔去毛刺有良好的打磨抛光去毛刺效果。
用于去除金属材料、塑料等零部件表面光洁度的要求,去除各类零件加工后产生的毛刺,提高光洁度。
自动去毛刺机抛光机充分解决了各类繁杂样式、小、薄、易变形、高精密零部件、高精密产品工件去毛刺、倒角、高精密打磨抛光、镜面加工等技术性难题,没有改变产品工件的原始尺寸精度。
现阶段去毛刺的方式有下面几种:1、手工去毛刺手工去毛刺是传统式的,而修边刀逐渐替代了那些传统式的方式,无需技术性解决,降低成本而且环保。
2、化学去毛刺化学去毛刺用电化学反应原理,对金属材料制作而成的零部件自行地、有选择地进行去毛刺工作。
主要用于难以去除的内部毛刺、热处理后和精加工的零部件。
3、电解去毛刺电解设备去毛刺运用电解功效去除金属零件毛刺的一类电解加工方式,英文简称ECD。
将工具阴极(一般用黄铜)固定不动摆放在产品工件有毛刺的位置周围,二者相隔相应的空隙(一般为0.3~1mm)。
工具阴极的导电性一部分指向毛刺棱边,别的表层用绝缘层遮盖起来,使电解设备功效集中化在毛刺一部分。
加工时工具阴极接直流稳压电源负极,产品工件接直流电源正极。
压力为0.1~0.3兆帕的低压电解液穿过产品工件与阴极两者之间。
当连接直流稳压电源后,毛刺便造成阳极溶解而被去除,被电解液带去。
电解液有相应腐蚀,产品工件去毛刺后应通过清洗和防锈。
电化学去毛刺工艺
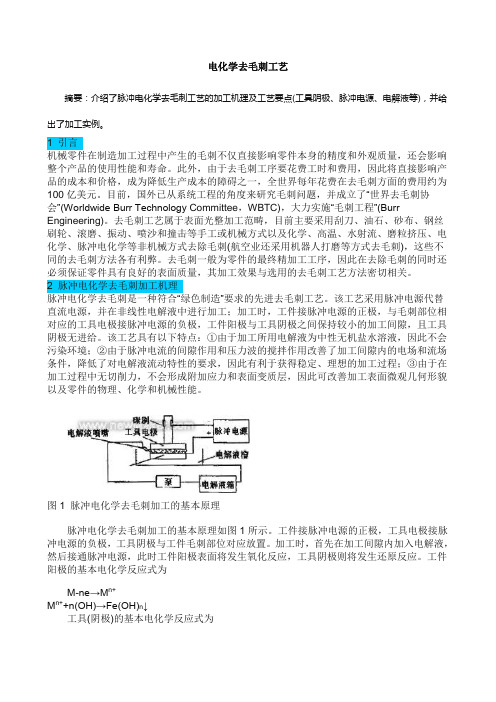
电化学去毛刺工艺摘要:介绍了脉冲电化学去毛刺工艺的加工机理及工艺要点(工具阴极、脉冲电源、电解液等),并给出了加工实例。
1 引言机械零件在制造加工过程中产生的毛刺不仅直接影响零件本身的精度和外观质量,还会影响整个产品的使用性能和寿命。
此外,由于去毛刺工序要花费工时和费用,因此将直接影响产品的成本和价格,成为降低生产成本的障碍之一,全世界每年花费在去毛刺方面的费用约为100亿美元。
目前,国外已从系统工程的角度来研究毛刺问题,并成立了“世界去毛刺协会”(Worldwide Burr Technolog y Committee,WBTC),大力实施“毛刺工程”(Burr Engineering)。
去毛刺工艺属于表面光整加工范畴,目前主要采用刮刀、油石、砂布、钢丝刷轮、滚磨、振动、喷沙和撞击等手工或机械方式以及化学、高温、水射流、磨粒挤压、电化学、脉冲电化学等非机械方式去除毛刺(航空业还采用机器人打磨等方式去毛刺),这些不同的去毛刺方法各有利弊。
去毛刺一般为零件的最终精加工工序,因此在去除毛刺的同时还必须保证零件具有良好的表面质量,其加工效果与选用的去毛刺工艺方法密切相关。
2 脉冲电化学去毛刺加工机理脉冲电化学去毛刺是一种符合“绿色制造”要求的先进去毛刺工艺。
该工艺采用脉冲电源代替直流电源,并在非线性电解液中进行加工;加工时,工件接脉冲电源的正极,与毛刺部位相对应的工具电极接脉冲电源的负极,工件阳极与工具阴极之间保持较小的加工间隙,且工具阴极无进给。
该工艺具有以下特点:①由于加工所用电解液为中性无机盐水溶液,因此不会污染环境;②由于脉冲电流的间隙作用和压力波的搅拌作用改善了加工间隙内的电场和流场条件,降低了对电解液流动特性的要求,因此有利于获得稳定、理想的加工过程;③由于在加工过程中无切削力,不会形成附加应力和表面变质层,因此可改善加工表面微观几何形貌以及零件的物理、化学和机械性能。
图1 脉冲电化学去毛刺加工的基本原理脉冲电化学去毛刺加工的基本原理如图1所示。
电解去毛刺设备的加工原理
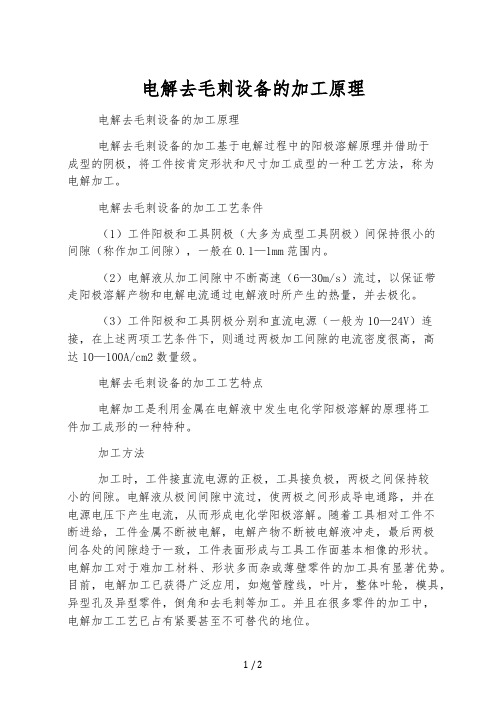
电解去毛刺设备的加工原理电解去毛刺设备的加工原理电解去毛刺设备的加工基于电解过程中的阳极溶解原理并借助于成型的阴极,将工件按肯定形状和尺寸加工成型的一种工艺方法,称为电解加工。
电解去毛刺设备的加工工艺条件(1)工件阳极和工具阴极(大多为成型工具阴极)间保持很小的间隙(称作加工间隙),一般在0.1—1mm范围内。
(2)电解液从加工间隙中不断高速(6—30m/s)流过,以保证带走阳极溶解产物和电解电流通过电解液时所产生的热量,并去极化。
(3)工件阳极和工具阴极分别和直流电源(一般为10—24V)连接,在上述两项工艺条件下,则通过两极加工间隙的电流密度很高,高达10—100A/cm2数量级。
电解去毛刺设备的加工工艺特点电解加工是利用金属在电解液中发生电化学阳极溶解的原理将工件加工成形的一种特种。
加工方法加工时,工件接直流电源的正极,工具接负极,两极之间保持较小的间隙。
电解液从极间间隙中流过,使两极之间形成导电通路,并在电源电压下产生电流,从而形成电化学阳极溶解。
随着工具相对工件不断进给,工件金属不断被电解,电解产物不断被电解液冲走,最后两极间各处的间隙趋于一致,工件表面形成与工具工作面基本相像的形状。
电解加工对于难加工材料、形状多而杂或薄壁零件的加工具有显著优势。
目前,电解加工已获得广泛应用,如炮管膛线,叶片,整体叶轮,模具,异型孔及异型零件,倒角和去毛刺等加工。
并且在很多零件的加工中,电解加工工艺已占有紧要甚至不可替代的地位。
与其它加工方法相比,电解加工具有如下特点:(1)加工范围广。
电解加工几乎可以加工全部的导电材料,并且不受材料的强度、硬度、韧性等机械、物理性能的限制,加工后材料的金相组织基本上不发生变化。
它常用于加工硬质合金、高温合金、淬火钢、不锈钢等难加工材料。
(2)生产率高,且加工生产率不直接受加工精度和表面粗糙度的限制。
电解加工能以简单的直线进给运动一次加工出多而杂的型腔、型面和型孔,而且加工速度可以和电流密度成比例地加添。
去毛刺新工艺4
去毛刺新工艺一、现今对复杂形体毛刺处理中遇到的问题1.复杂形体易变形,一般对工件表面要求比较高,而在加工过程中对毛刺处理比较难。
2.复杂形体毛刺处理速度慢,现如今依然停留在使用人工应用刮刀等手工刀具处理。
3.由于使用人工处理,质量稳定性很差,很容易出现问题。
4.由于形体复杂,有的地方用手工很难去毛刺。
二、去毛刺新工艺1、应用电化学方法对复杂形体进行一次性成型的去毛刺处理。
2、电化学去毛刺是利用金属在电解液中发生阳极溶解反应而去除工件上多余的材料、将零件毛刺去除的一种方法。
3、电化学去毛刺的决定因素:3.1决定毛刺去除量的主要参数:去毛刺电流:根据去毛刺工件的所去毛刺的范围而决定。
一般5到10A。
去毛刺时间:根据去的毛刺大小有关。
一般为十几到几时秒。
工件材料导电率:根据去毛刺的材质有关。
3.2决定去毛刺的参数:电流密度:电流密度决定切削量和表面质量。
导电率:电解液的浓度决定导电率,单位S/cm根据区毛刺的需要,浓度应该控制在8%到25% ,温度对其也有影响。
间隙:夹具(阴极)工件(阳极)之间的间隙决定电流大小和电解液的冷却能力。
电化学液压力:间隙中的液体压力影响着电流和材料的去除。
实施温度:一般控制在20到35度之间。
PH值:一般在6.5到8.0之间。
电解液纯度:纯净的电解液能确保恒定量的产生。
三、项目适用范围:本项目适用于扭簧也可以加工我厂的733-106、736-14、736A-13整流子组件等各类复杂形体的毛刺处理;可以去除不锈钢、中低碳钢等硬度比较大的导电材质。
四、电化学去毛刺的优点:1.表面质量好,因去毛刺过程中不产生切削热,可达到较低的表面粗糙度。
2.操作简单,它可以通过简单地操作来处理复杂形体的毛刺且不影响工件自身强度。
3.可长期使用,理论上电极可长期使用,无损耗。
4.去毛刺生产率高,一般一个工件可在十几秒内全部去除干净,可进行平行加工,一般适用于批量处理。
5.该工艺属于绿色加工方法,电化学液很环保,一般使用中性无机盐类就可以处理,例如NaCl溶液,NaSO4溶液等。
电化学去毛刺原理
产品简介
电化学去毛刺是一种先进的去毛刺技术,是电化学加工(电解加工)技术中发展较快、应用较广的一项新工艺。
作为电化学加工一种特殊的应用形式,它对加工工件无机械作用力,容易实现自动化或半自动化,适合去除高硬度、高韧性金属零件的毛刺,可以在工件的特定部位进行限定加工。
对于手工难以处理、可达性差的复杂内腔部位,尤其是交叉孔相贯线的毛刺,利用电化学去毛刺有着明显的优势。
电化学去毛刺对加工棱边可取得较高的边缘均一性和良好的表面质量,具有去除毛刺效果好、安全,高效节能环保等优点,去毛刺效果好,一般情况和传统工艺相比,效率可提高10-20倍以上。
适用行业:
汽车发动机、通用工程机械、航空航天、气动液压等众多行业,是电化学加工机床中生产批量较大,应用领域
最广的重要装备。
机器特点:
适用于难以去除的内部毛刺;
适用于热处理后精加工的零件;
适用于整个金属切削加工领域;
使用非线性电解液对人体无害。
电解法去毛刺的方法及应用
电解去毛刺工艺已成功运用于喷油嘴内孔、液压阀体内孔、活塞套、轴承保持架等。
要知道机加工件或者是机械零件在加工制造过程中产生的毛刺,对零件的精度、使用、再加工定位、操作安全和外观质量等许多方面都产生不良影响,同时,由于去毛刺要花费很多的时间和费用,也成为降低成本的最大障碍之一,所以,对于去毛刺要引起足够重视。
现介绍电解去毛刺方法。
一:电解去毛刺的原理电解去毛刺是利用电能、化学能,阳极溶解去毛刺的方法,零件与直流电源的正极相连,称为阳极,成形工具与直流电源的负极相连,称为阴极。
两极之间保持一定的间隙,让循环电解液流动.当阳极和阴极浸入溶液并通入直流电后,随着阳极表面发生电化学反应,在零件的表面上,由于被溶解金属与电解液组成一层粘性液体。
集中在零件表面低凹处,此粘性液体具有较高的电阻和较小的导电率。
可以保护零件表面不腐蚀或少腐蚀,而毛刺突出于零件表面,在温度差和湿度差的影响下,液膜难于形成,故通电后电力线高度集中于去毛刺部位,最接近阴极的毛刺将以最快速度溶解,直到毛刺全部溶解并且边缘逐渐形成圆角,达到去毛刺的目的。
其原理见图1。
1.直流电源2.工具阴极3.工件阳极4.电解液泵5.电解液二:需要涉及到的设备及工具电解去毛刺。
使用电解去毛刺机床。
生产批量不大时。
可用整流器将交流电变成直流电而制成简单设备。
根据零件设计专用夹具(工具阴极),设计成与零件相似形状,用黄铜或紫铜等良好导电材料制成,不加工的部位涂环氧树脂进行隔离保护,常用的电解液有NaC1溶液、NaNO 溶液、NaNO3溶液等。
三:电解去毛刺的优缺点如何?电解去毛刺的质量高,效果稳定,生产效率高,缺点是在工作过程中产生有害气体.电解液对周围的机械设备有一定的腐蚀作用。
四:适用的非标零部件范围适用于有色、黑色金属零件,特别适于复杂形状零件及用机械、手工方法难以去除的内孔、交叉子L、内表面毛刺。
并且,能去除特硬零件(如钼、镍、钛、淬火零件)上的毛刺。
电解加工去除毛刺的方法及改善
脉冲电解去除毛刺的方法及发展学院:学号:姓名:摘要:电解去毛刺加工是利用金属在电解液中产生阳极溶解的原理去除工件上多余材料的一种加工方法。
电解加工开始时,工件阳极与工具阴极的形状不同,工件表面上各点至工具表面的距离不等,因而各点的电流密度不同。
距离较近处通过的电流密度大,电解液的流速也常常较高,阳极溶液的速度较快;反之,距离较远处通过的电流密度小,阳极溶液的速度较慢。
当工具不断进给时,工件表面上各点就以不同的溶液速度进行溶解,工件的形状就逐渐接近于工具的形状,直到把工具的形状“复映”在工件上,得到所需要的形状为止。
关键词:电解脉冲电解去毛刺电解去毛刺的原理Abstract: the electrochemical deburring processing is the use of metal in electrolyte produced in the principle of anodic dissolution remove excess material of workpieces a processing method. Electrochemical machining began, the anode and cathode tools of different shapes, the surface at every point on the surface of the distance to the tools to differ, and that each point of current density is different. Distance is near the through current density, electrolytes and often high flow velocity, and the anode solution speed quickly; Conversely, distance is the distance through the current density is small, the anode solution at a slower speed. When tools for continuous feed, different points on the surface with different solution speed dissolved, the shape will gradually close to the shape of the tools, until the tools of the shape of the "complex reflected" on the work piece, the shape of the need to do so.一.引言:自20世纪70年代初起,前苏联、美国、日本、法国、波兰、瑞士、德国等-国家相继开始了对脉冲电流电解加工的研究。
- 1、下载文档前请自行甄别文档内容的完整性,平台不提供额外的编辑、内容补充、找答案等附加服务。
- 2、"仅部分预览"的文档,不可在线预览部分如存在完整性等问题,可反馈申请退款(可完整预览的文档不适用该条件!)。
- 3、如文档侵犯您的权益,请联系客服反馈,我们会尽快为您处理(人工客服工作时间:9:00-18:30)。
电化学去毛刺的基本原理电化学去毛刺的基本原理是利用金属在电解工作液中产生阳极溶解的电化学反应现象。
如下图所示:以工件为阳极,工具电极为阴极,当强迫使电解液通过工件上的毛刺和特殊设计的工具电极之间十分狭小的间隙同时,短时间加以电解电压,这时在工件的毛刺或棱边部分电流最集中,电流密度也最大,因而使毛刺很快被溶除,棱角也被倒圆。
在电化学去毛刺的过程中,工件和工具电极二者是相对固定不动的,即属于固定式工具阴极的电化学加工方法。
适合去除高硬度、高韧性金属零件的毛刺,可以在工件的特定部位进行限定加工,对于手工难以处理、可达性差的复杂内腔部位,尤其是交叉孔相贯线的毛刺。
脉冲电化学去毛刺是一种符合“绿色制造”要求的先进去毛刺工艺。
该工艺采用脉冲电源代替直流电源,并在非线性电解液中进行加工;加工时,工件接脉冲电源的正极,与毛刺部位相对应的工具电极接脉冲电源的负极,工件阳极与工具阴极之间保持较小的加工间隙,且工具阴极无进给。
该工艺具有以下特点:①由于加工所用电解液为中性无机盐水溶液,因此不会污染环境;②由于脉冲电流的间隙作用和压力波的搅拌作用改善了加工间隙内的电场和流场条件,降低了对电解液流动特性的要求,因此有利于获得稳定、理想的加工过程;③由于在加工过程中无切削力,不会形成附加应力和表面变质层,因此可改善加工表面微观几何形貌以及零件的物理、化学和机械性能。
脉冲电化学去毛刺加工的基本原理。
工件接脉冲电源的正极,工具电极接脉冲电源的负极,工具阴极与工件毛刺部位对应放置。
加工时,首先在加工间隙内加入电解液,然后接通脉冲电源,此时工件阳极表面将发生氧化反应,工具阴极则将发生还原反应。
工件阳极的基本电化学反应式为M-ne→Mn+Mn++n(OH)→Fe(OH)n↓工具(阴极)的基本电化学反应式为2H++2e→H2↓加工时,在工件阳极附近形成一层很薄的氧化膜,可在工件阳极与电解液之间起到隔离作用。
该氧化膜具有较高的电阻和较小的电导率,可阻止工件阳极表面进一步溶解,对工件阳极具有一定保护作用。
在电解液的快速冲刷作用下,工件阳极表面凹陷处的氧化膜因不易扩散而较厚;工件阳极表面凸出处(如毛刺、微观凸出部位等)的氧化膜因容易扩散而较薄。
由于氧化膜的分布不均匀,使毛刺等凸出部位始终与新鲜的电解液接触,因此毛刺部位的金属溶解速度远大于阳极表面的其它部位,从而使毛刺被迅速溶解、去除。
在阳极溶解过程中,根据电化学加工基本规律(法拉第电解定律)可推导出金属阳极(工件)沿进给方向的深度蚀除速度va(mm/min)为va=hwi式中:h——电流效率w——被电解物质的体积电化学当量(mm3/A·h)i——电流密度(A/cm2)当电解液的成分、浓度、加工温度等参数确定后,阳极某点的蚀除速度主要取决于通过该点的电流密度i。
根据电场理论可知,在零件表面毛刺等凸出部位电荷较集中,在表面凹陷处电荷则较少。
由于电力线分布不均匀,凸出部位的电力线分布密集,电流密度高,金属去除较多;凹陷部位的电力线分布相对稀疏,电流密度较低,金属去除较少。
由于毛刺处通过的电流密度远大于工件阳极表面的其它部位,因此毛刺被迅速溶解。
综上所述,由于氧化膜分布不均匀,工件阳极表面毛刺等凸出部位氧化膜较薄,可始终与新鲜电解液保持接触,因此电化学反应速度快;由于电力线分布不均匀,工件阳极表面毛刺等凸出部位电力线分布密集,电流密度大,蚀除速度较快。
因此,电化学去毛刺加工可达到迅速去除、溶解毛刺并形成光滑圆角的目的。
通过合理采用工具阴极遮蔽技术,可有选择地去除毛刺,不会影响工件阳极表面原有的尺寸精度和表面质量。
3 电化学去毛刺工艺要点影响脉冲电化学去毛刺加工效果的工艺因素较多,如工具阴极的合理设计、脉冲电源的参数选择、电解液的成分、浓度、压力和流速、极间间隙、电流密度、加工时间、流场特性等。
o 工具阴极o 脉冲电源o 电解液o 其它工艺因素工具阴极应根据具体毛刺情况进行合理设计,设计时应注意应用遮蔽技术,以保证在高效去除毛刺的同时保护工件阳极表面其它非毛刺部位的原有精度和表面质量。
此外,还应满足脉冲电化学加工的基本原则,即使电解液快速、均匀地冲刷加工部分,保证流场分布均匀、合理。
由于电极表面质量直接影响去除毛刺部位的表面质量,因此要求工具阴极表面平整、光滑。
理论研究和加工实践表明,采用脉冲电源代替直流电源进行去毛刺加工,可有效提高加工精度和表面质量。
在加工中,一般采用较窄的脉冲宽度和较高的脉冲频率进行加工。
由于脉冲电流的间隙作用和阶跃变化,使加工间隙中的电解液发生振荡,产生压力波,压力波的搅拌作用可改善加工间隙中电解液的流动条件,加速更新间隙中的电解液,消除加工间隙中电解液电导率分布的不均匀性,从而提高加工精度,改善表面粗糙度。
此外,由于电解液的周期性更新,使间隙内的电化学产物(阳极去除的金属、阴极析出的氢气和产生的焦耳热等)可及时、充分地排除。
脉冲电源参数应根据加工条件合理选择。
电解液成分是影响加工质量的主要因素。
以中性无机盐为主要成分的非线性电解液具有适用范围广、易于控制、杂散腐蚀小、加工表面质量好、对环境无污染等特点。
加工时,应根据毛刺的大小确定电解液的具体成分,同时合理设计电解液的流向、流速及压力,以便将去除的毛刺迅速冲离加工间隙,以免造成短路。
合理选择阴、阳极之间的间隙有利于提高蚀除速度和加工精度,改善加工表面质量。
电流密度和加工时间的选择也十分重要,电流密度过大会加剧杂散腐蚀,电流密度过小则会降低加工效率,延长加工时间,而加工时间过长会加剧晶界腐蚀。
在满足毛刺去除效率的前提下,加工时间主要应根据加工圆角的大小来确定。
4 应用实例脉冲电化学去毛刺工艺已成功运用于喷油嘴内孔、液压阀体内孔、活塞套、轴承保持架以及纺机分梳辊用金属针布等零件的去毛刺加工,去除毛刺的效果良好,形成了要求的光滑圆弧,且获得了较好的表面质量。
o 喷油嘴内孔去毛刺o 金属针布去毛刺喷油嘴内孔孔径一般为0.25~0.5mm,去毛刺工艺装置。
采用正交试验法得出优选工艺参数为:电解液为浓度约12%的硝酸钠溶液,加工间歇0.1mm,脉冲宽度200ms,脉冲频率1000Hz,加工电流5A,加工电压15V,加工时间6s。
加工后成功去除了喷油嘴内孔毛刺,并形成了约R0.1mm圆角,加工表面粗糙度达到Ra1.6um。
纺织机械中的分梳辊用金属针布外形。
由于该零件为低刚度薄壁零件,采用机加工方法去毛刺较困难。
采用脉冲电化学去毛刺时,优化工艺参数为:电解液为浓度约10%的硝酸钠溶液,加工间隙0.2mm,脉冲周期1ms,脉冲间隔0.5ms,加工电流5A,加工电压10V,加工时间5s。
去毛刺效果及加工表面质量良好。
由于电解液具有一定腐蚀作用,因此电化学去毛刺加工后应采用超声波清洗等方法及时清洗工件,也可采用硝酸钠和亚硝酸钠水溶液进行防腐处理。
DJK6032A电化学去毛刺机床主要由机床主机、电源电控系统、电解工作液系统、电极夹具等组成。
主机DJK6032A电化学去毛刺机床主机采用全防腐钢板焊接结构,工作区域为全不锈钢制成,用花岗岩制成工作台置于机床床身上,耐腐蚀,绝缘性好。
床身两侧为主柱,立柱支撑固定横梁,横梁上安置主轴部件和气控箱。
主轴部件也采用全防腐结构,用气控驱动,上下滑动采用双导柱形式。
在加工区域后侧为电解工作液进回液口。
进液口通过软管与电解工作液槽连通,回液口通过回液管使工作腔内的工作液回入电解液系统内。
在加工区域后上方备有空气抽风口,可与厂房通风管相联接,以消除加工过程中由于电解工作液的流动可能产生的雾气。
主要技术参数和规格:1、工作台尺寸:600mm×320mm2、主轴行程:200mm3、主轴至工作台最大距离:450mm4、压缩空气(现场提供):0.6 Mp电源及控制系统DJK6032A电化学去毛刺机床的电气系统分为直流电源和控制系统二部分。
电化学去毛刺电源:电化学去毛刺加工电源采用晶闸管整流电源。
电源电压可调,电流实现分档定值控制。
电源的输出具有稳压运行性能,还具有过流、短路等保护功能。
本机床配置电解电源主要参数:电源输出额定电压:DC24V电源最大输出电流:600A电源调压范围:DC 6—24V控制系统:控制系统由可编程控制器、机床电器、短路检测电路等组成。
可编程控制器用于手动操作和自动循环的控制。
手动操作是压紧导电块移动、主泵开关、短路检测、过滤启动等按钮开关来接通和断开各控制的工作方式。
自动循环是机床处在原位时,按下启动按钮,自动执行一个周期操作。
操作完后机床停在原位上。
机床电器是由控制电气系统的电源和温度检测组成。
电气系统的电源控制由急停按钮,带锁开关,准备按钮控制。
温度检测系统由探头、控制仪组成。
当探头(传感器)受工作液变化而变化,温度信号由探头送控制仪并显示。
考虑到电解加工时可能造成的零件与电极间的短路烧伤,机床在加工前采用短路检测电路对零件进行检测和显示。
当检测到电极与零件发生短路时短路检测电路将切断加工。
电解液系统电解液槽由优质不锈钢焊接而成,输液主泵采用国际著名泵业制造公司丹麦格兰富(GRUNDFOS)生产的 SPK 型浸入式不锈钢泵。
电解液在长期使用后,其中所含的金属氢氧化物和其它杂质不断增加,这将使电解液的粘度增大,影响电解液在加工间隙内的流动,严重时会发生短路,造成工件和电极的损坏。
本系统对电解液进行粗、精两道过滤。
粗过滤采用全防腐的纸带过滤机过滤,以去除电解液中的杂质和大颗粒蚀除产物。
精过滤采用滤芯过滤,由于蚀除产物——金属氢氧化物颗粒细微,须定期对过滤器及滤芯进行清洗和更换。
主要技术参数:(1)外形尺寸:1750×1050×700mm3(2)液槽容积:1.2 m3(3)主泵流量:4000L/H(4)主泵扬程:47m(5)主泵功率:AC380V 50HZ 1.1KW工具电极夹具单元及对工件的要求工具电极夹具采用固定式阴极结构,每套电极夹具根据工件去毛刺部位的具体去毛刺结构及要求,专门设计制造。
阳极和阴极(即工件和电极)之间的金属接触会出现短路,导致电极和工件的损坏。
因此有必要对工件上毛刺的大小和方向作如下规定:1、毛刺须与电极插入方向平行;2、毛刺长度不大于 0.8mm(特殊情况需方允许时特殊处理);3、毛刺厚度最大为 0.15mm。
4、去毛刺部位的位置度误差不能超过0.2mm,位置度误差过大时只能采用大于去毛刺部位大小的电极加工,扩大加工范围(在工艺允许时)。
如果由于前道工序非正常切削加工,而使工件产生超过上述要求的飞边毛刺时,应当调整切削加工工序,使产生的毛刺符合上述要求,或用手工工具将毛刺飞边预先去除后,方可进行加工。
吸附在工件上的脱落的切屑以及污物也会造成加工时的短路故障、加工缺陷以及不良的导电接触,因此,工件必须经过前道清洗后才能进行加工。