电镀生产工序之清缸处理方法
水平直接电镀之导电膜配方工艺DMSE操作方法

水平直接电镀之导电膜配方工艺DMSE操作方法(周生电镀导师)高分子导电膜工艺,又称导电胶工艺或水平环保通孔,都是在PCB孔内形成一层高分子导电膜层,然后直接电镀的工艺,最新的DMSE配方已经发展了四代,目前的工艺更加稳定,使用周期更长了。
本工艺可以替代化学镀铜工艺。
但是目前看DMSE 并不能完全替代化学镀铜,主要是附着力及可靠性问题,对于要求较高的汽车、军工等PCB还是需要传统化学铜。
一、开缸参数.周生电镀导师之【(@q)】:(3)(8)(0)(6)(8)(5)(5)(0)(9).电镀导师之[(微)(Xin)]:(1)(3)(6)(5)(7)(2)(0)(1)(4)(7)(0)需要注意的是:我们的配方是量产的成熟商业配方,网上是找不到的,电镀手册也没有。
网上卖配方百个配方,那种资料只能当做书籍读读,没有商业价值。
有些用户嫌贵了,尽管买书好了。
●配方平台不断发展完善我们的配方平台包含的成熟量产商业配方种类多,已有AN美特、乐思、罗哈、麦M德美、国内知名公司我们的配方平台帮助了很多中小企业提高产品技术水平,也有不少个人因此创业成功,帮助国内企业提升国产占有率是我们长期追求的目标。
●配方平台说明目前市场上有很多类似抄袭的,或者是买过部分配方后再次转卖的,他们有时候会改动数据,而且不还有建立Q群或者微@信群推广配方,我们没有建立任何群。
一切建&群的都是假冒。
(本*公*二、新设备清洗及开缸一、缸体清洗方法:二、开缸方法:流程操作条件水平环保通孔控制条件生产开缸量及千尺添加量分析、加药、产量记录为有效监测水平环保通孔工艺之稳定性, 化验室及生产部必须详细记录分析/加药数据于报表中:换缸条件及步骤生产注意事项1、每次生产前必须事先补充好液位,分析并调整好药水各参数到最佳范围后才能进行生产;2、生产首板前用测试板做哈林槽实验,检查基材上铜速率和孔内上膜状况;除胶线做除胶速率。
3、出板后需插架,待板面温度冷却至室温,方可叠板送至下工序;4、水平环保通孔后的板需要在7天内完成干菲林工序。
电镀工艺流程
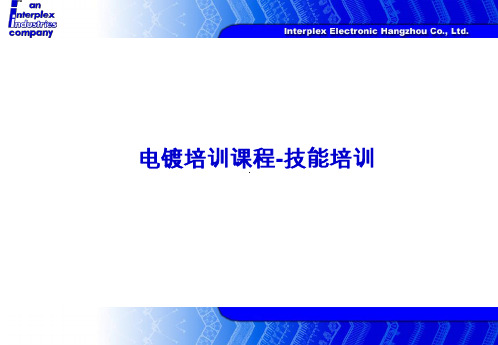
成分:H2SO4(98%) 条件:常温;Ni前活化浓度:110-150 g/L; Au前
活化浓度:160-200 g/L;
酸活化
注意/确认事项(责任岗位:放料员):
1、开缸时先加入1/2槽水后再缓慢加入硫酸,便于散热( 失效后常见不良图片 切勿先加硫酸再加水),再补充至标准液位; 2、生产时调整好风水刀,防止带入带出槽液; 3、液位不足时需补加硫酸,添加硫酸时必须带防护手 套、护目镜、口罩;原液接触皮肤须立即擦去,并 用大量清水冲洗; 4、保养:利用废酸液清洗阳极,脱脂工站地面等,清洗子 母槽,更换酸后水洗,更换腐蚀装置; 5、产品表面镀镍层裸露在空气中8S即钝化,再电镀金/ 锡会出现Peeling ,保持工件表面湿润可延缓钝化.
失效后常见不良: 产品镀Au区过大或偏小;
失效后常见不良图片
如:IA1382、IA1968、IA0638,马瑞利系 列产品等
多镀金部分
电镀:刷镀Au
作用:选择性刷镀Au 条件:同上
注意/确认事项(责任岗位:主操作) :
1、刷布更换及时,防止长Au后造成膜厚不足甚至短路 打火,更换下来的刷镀布有专人回收; 2、气囊漏气应及时更换,防止槽液溅出影响; 3、保持接线处干净无腐蚀且尽可能远离槽液,防止腐 蚀污染; 4、及时更换腐蚀铜刷; 5、槽液补水勤加少加.
失效后常见不良图片 刷镀打火起泡 选择性刷镀Au
失效后常见不良:
产品镀Au区过大或偏小;漏刷Au,刷布结晶导致导 电不良打火产生起泡、烧焦发黑不良等 主要运用在DSS3系列产品以及IA0576、IA0577 、IA0695等产品
刷镀漏镀 刷镀烧焦 刷镀漏镀
电镀:褪镀Au
作用:将轮镀与点线镀Au中多镀区与表面感 应Au进行化学剥离,从而使区域符合要求和外 观达到要求,同时可以进行Au 回收节约成本; 是恰好与电镀原理相反的一个制程. 成分:褪金粉 条件:常温;浓度由实验室根据褪金效果补充 注意/确认事项(责任岗位:主操作) :
电镀车间清缸的管理措施
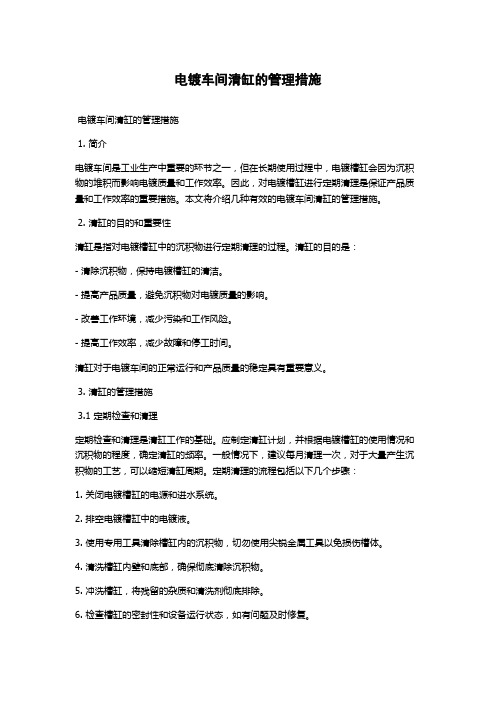
电镀车间清缸的管理措施电镀车间清缸的管理措施1. 简介电镀车间是工业生产中重要的环节之一,但在长期使用过程中,电镀槽缸会因为沉积物的堆积而影响电镀质量和工作效率。
因此,对电镀槽缸进行定期清理是保证产品质量和工作效率的重要措施。
本文将介绍几种有效的电镀车间清缸的管理措施。
2. 清缸的目的和重要性清缸是指对电镀槽缸中的沉积物进行定期清理的过程。
清缸的目的是:- 清除沉积物,保持电镀槽缸的清洁。
- 提高产品质量,避免沉积物对电镀质量的影响。
- 改善工作环境,减少污染和工作风险。
- 提高工作效率,减少故障和停工时间。
清缸对于电镀车间的正常运行和产品质量的稳定具有重要意义。
3. 清缸的管理措施3.1 定期检查和清理定期检查和清理是清缸工作的基础。
应制定清缸计划,并根据电镀槽缸的使用情况和沉积物的程度,确定清缸的频率。
一般情况下,建议每月清理一次,对于大量产生沉积物的工艺,可以缩短清缸周期。
定期清理的流程包括以下几个步骤:1. 关闭电镀槽缸的电源和进水系统。
2. 排空电镀槽缸中的电镀液。
3. 使用专用工具清除槽缸内的沉积物,切勿使用尖锐金属工具以免损伤槽体。
4. 清洗槽缸内壁和底部,确保彻底清除沉积物。
5. 冲洗槽缸,将残留的杂质和清洗剂彻底排除。
6. 检查槽缸的密封性和设备运行状态,如有问题及时修复。
7. 重新装入新的电镀液,并逐步升温、调整参数,恢复正常生产。
定期检查和清理是防止沉积物积累和维持电镀质量的基本措施。
3.2 沉积物监测和记录对电镀槽缸中的沉积物进行监测和记录,可以及时发现沉积物的生成过程和程度,为清缸工作提供依据。
监测可以通过目视观察、沉积物厚度测量仪器等方式进行。
同时,建立沉积物记录表,记录每次清缸时的沉积物情况、清理过程和维护措施。
通过沉积物监测和记录,可以更好地掌握电镀槽缸的运行情况,并及时采取相应的清缸措施。
3.3 保持操作规范为了减少沉积物的生成和堆积,应加强对电镀槽缸的操作规范。
电镀工艺的6大后处理技术

电镀工艺的6大后处理技术电镀后处理的目的是确保镀层的质量,提高镀层的防护性、装饰性和功能性。
镀后处理是很重要的,但往往易被人忽视。
在实际生产中常出故障,甚至前功尽废,故应引起有关人员重视。
电镀后处理工艺是根据电镀层的性能、使用要求、环境影响等因素来选定,通常有抛光、钝化、着色、涂膜、封闭、除氢等工艺。
1.抛光处理抛光是通过化学抛光或机械抛光来提高金属工件表面的平整性和降低表面粗糙度的工艺过程,它既能直接用于金属的表面加工,也用于金属工件镀前处理及镀后精加工。
如铜、镍等合金以及镀后的铜、镍、铬等金属镀层的装饰性精加工。
2.钝化处理所谓钝化处理是指在一定的溶液中进行化学处理,在镀层上形成一层坚实致密的,稳定性高的薄膜的金属表面处理方法。
钝化使镀层耐蚀性大大提高并能增加表面光泽和抗污染能力。
这种方法用途很广,镀锌、铜等后,都可以进行钝化处理。
3.除氢处理大部分金属基体如钢铁、铜,在前处理(酸洗、阴极电解除油)及电沉积过程中,都会产生“氢”,有部分还没来得及形成“氢气”即以“氢原子”的形式渗入到基体和镀层中,使镀件产生脆性,严重降低零件的抗拉强度,称为氢脆。
因此在航天航空、汽车制造等领域使用的零件镀后都必须经过“除氢”处理,有些在使用中要求抗拉强度高的零件也要进行“除氢”处理。
除氢处理是在200℃左右的温度下进行的,处理时间根据零件要求的抗拉强度来决定。
除氢处理应在镀后的3小时内进行。
4.着色处理金属表面着色是在特定的溶液中采用化学、电化学、置换或热处理等方法在金属表面形成一层颜色各异的膜或干扰膜层。
由于各种金属氧化物颜色不同,从而使着色金属表面呈现不同的颜色,改变了原有金属的外观,达到模仿昂贵金属、仿古、装饰等目的。
5.涂膜处理涂膜就是对银及仿金镀层的零件,涂覆或浸一层透明的有机膜层,起到防止或延续镀层变色的工序。
6.封闭处理就是为了提高工件在大气中的抗腐蚀能力,采用物理、化学或电化学的方法,使其表面(或中间镀层)均匀地覆盖一层膜层,这种工艺称为封闭。
电镀后处理中的清洗操作工艺环节介绍

电镀后处理中的清洗操作工艺环节介绍现代电镀网7月17日讯:(每日电镀行业最新资讯推送请关注微信公众号:现代电镀网)从电镀槽中镀出的合格产品,若不清洗掉零件夹带的镀液,有时会使镀层泛色或出现锈点、白点,最后仍不能得到满意的产品。
特别是镀锌、镀镉及它们的合金,若镀后清洗不彻底,不把渗入基体或镀层中的溶液洗净,那么在产品贮存期间会产生泛点(或渗点)。
如果加强镀后清洗,用冷水、热水交替处理,就可以防止产生这类故障。
一、常用的几种清洗方法①清洗有单级浸洗和多级浸洗,按浸洗的组织方法有多级逆流漂洗和间歇逆流漂洗。
为了强化浸洗效果,浸洗时加有零件摆动、空气搅拌、泵强制循环,还有超声波强化浸洗。
②与浸洗相对应的是喷淋,喷淋有连续喷淋和间歇喷淋,有定式喷淋和扫描式喷淋,有全喷和顶喷。
③浸洗加顶喷也是常用的方法,也有先浸洗后喷淋或先喷淋后浸洗的。
二、清洗操作要求①镀件与清洗水要加强接触。
镀件进入水槽之后要上下、左右抖动,使镀件与清洗水充分接触,.以达到清洗的应有效果。
②不要忽视挂钩的清洗。
当清洗槽深度较浅(逆流清洗槽的前几个槽深度更浅),带挂具清洗时挂具上部浸不到水面以下,在卸挂、干燥时,挂具上的溶液会污染镀件,引起镀层发花,出现斑点。
此时可用水龙头冲洗,或用水勺浇一下未清洗到的挂具上部,以避免这种故障。
③镀件清洗时速度不宜太快,最好在挂具提出清洗槽后能在槽上方暂停片刻。
以减少被带入下一个清洗槽的镀件表面所黏附的酸、碱污水。
④清洗时要防止镀(涂)层遭到机械损伤,否则会严重影响镀(涂)层的完整性,失去了镀(涂)层应有的防护和装饰功能。
为此,操作时一次数量不宜过多,且要轻拿、轻放。
⑤对于盲孔、狭缝中镀液的辅助除去,一是甩除法,即把难出水工件猛甩,积聚在这些部位的溶液即会甩出来,经清洗后再甩效果更好。
二是注水交换法,即采用医用注射器向盲孔、狭缝内注入清水,把隐藏在里面的污水驱逐出来,从而达到洁净的目的。
三、清洗对水质的要求①清洗水中不能含过多的钙镁离子,否则带入镀液后容易产生沉淀。
电镀前处理工艺流程

电镀前处理工艺流程电镀前处理工艺流程是指在进行电镀之前对工件进行处理,以保证电镀的质量和效果。
下面是一份常见的电镀前处理工艺流程:1. 清洗(Cleaning):将工件放入清洗槽中,使用碱性或酸性清洗剂清洗表面的油脂、污渍和其他杂质。
清洗槽中可以加热或超声波来增加清洁效果。
2. 酸洗(Acid Pickling):将工件放入酸洗槽中,使用酸性溶液(如硫酸或盐酸)进行酸洗,目的是去除表面的氧化物、锈蚀物和其他有害物质,以提高镀层的附着力。
3. 防酸处理(Acid Resistant Treatment):将工件浸入防酸液中,例如磷酸或硼酸液体,目的是形成一个防止酸洗液对工件表面的继续侵蚀和氧化的保护层。
4. 水冲洗(Water Rinsing):将工件从酸洗槽中取出,通过水冲洗去除残留的酸洗液和防酸液,以防止其对后续工艺造成不良影响。
5. 除油(Degreasing):将工件放入除油槽中,使用有机溶剂或碱性溶液去除表面的油脂和其他有机物,以提高电镀的附着力和均匀性。
6. 再水冲洗(Water Rinsing):将工件从除油槽中取出,通过水冲洗去除残留的溶剂或碱性溶液,以防止其对后续工艺造成不良影响。
7. 预光(Pre-polishing):将工件放入预光槽中,使用研磨材料或预光剂进行预光处理,以去除表面的凹陷、细微划痕和氧化物,以改善镀层的外观和质量。
8. 再次水冲洗(Water Rinsing):将工件从预光槽中取出,通过水冲洗去除残留的研磨材料或预光剂,以防止其对后续工艺造成不良影响。
9. 碱洗(Alkaline Cleaning):将工件放入碱洗槽中,使用碱性溶液进行碱洗,目的是去除预光过程中生成的氧化物和其他杂质,以提高电镀的质量和光亮度。
10. 最后水冲洗(Final Water Rinsing):将工件从碱洗槽中取出,通过水冲洗去除残留的碱洗液和其他杂质,以确保工件表面干净无污染。
以上是一份常见的电镀前处理工艺流程,其中细节还可以根据具体的工件和要求进行调整。
电镀前处理工艺流程
电镀前处理工艺流程
《电镀前处理工艺流程》
电镀前处理工艺流程是指在进行电镀之前,对待处理物体进行一系列的预处理工艺,以确保电镀涂层的附着力、光洁度和耐腐蚀性。
电镀前处理工艺流程通常包括以下几个步骤:
1. 清洗:将待处理物体浸泡在清洗液中,去除表面的油污、灰尘和其他污染物质。
清洗液通常是碱性或酸性的溶液,能有效去除表面污染物,并为后续处理步骤做好准备。
2. 酸洗:将清洗后的物体浸泡在酸性溶液中,去除表面的氧化层和锈蚀物质,提高金属表面的活性。
酸洗可以使用硫酸、盐酸或其他酸性溶液,根据待处理物体的材质和表面情况选择合适的酸洗液。
3. 除油和去污:采用机械除油或化学去污的方法,进一步去除表面的油污和残留的污染物。
这一步骤可以使用溶剂、碱性液体或高压喷洗等方法,确保物体表面完全干净。
4. 钝化处理:对金属表面进行钝化处理,使其在电镀过程中形成致密的氧化膜,提高电镀层的附着力和耐腐蚀性。
钝化处理可以使用铬酸、磷酸或其他化学品,根据不同金属材质选择合适的钝化方法和液体。
5. 上助剂:在进行电镀之前,有时需要在物体表面涂覆一层助剂,以提高电镀层的均匀性和光泽度。
助剂可以是特殊的化学
物质或表面活性剂,使电镀液更容易附着在物体表面,提高电镀质量。
电镀前处理工艺流程的每一步都十分重要,它们共同确保了电镀涂层的质量和性能。
只有经过严格的预处理工艺,才能获得均匀、光亮、耐腐蚀的电镀涂层,满足不同行业对金属制品质量和外观的要求。
电镀生产线清缸
4.5过滤机清洗要求:
1、当过滤机的压力表到达规定的压力值或到了规定的清洗周期,则需清洗。
各槽过滤机需清洗的最小压力为:
除油、除蜡、化学镍、哑镍、半光镍、脱解为0.5 KG/CM2;钯水、解胶为0.3 KG/CM2;光镍为1.0 KG/CM2;光铜为1.5 KG/CM2.
2、首先关闭过滤机电源。
3、关闭过滤机的进水和出水阀(当过滤机低于槽液面时),打开底部阀门,将药水放入桶中;当过滤机高于槽液面时,则可以直接打开过滤机盖,取出滤芯。
4、除油、除腊、钯水、解胶、酸铜需清洗的棉芯或滤纸在备用综合槽中进行,污水从综合管中排放。
5、化学镍、哑镍、半光镍、光镍、珍珠镍棉芯也在备用综合槽中进行清洗,污水从含镍水管中排放。
2用清洗干净的过滤机将槽液抽入清洗干净的备用槽,槽底的药水用人工打出,也倒入备用
槽。如果槽液需碳粉处理,过滤机里则可以不装棉芯或碳芯,如果不需碳粉处理则需要装棉
芯或碳芯。
3用水管对阳极袋冲洗,冲掉大部分的残留药水和阳极吸附物,将污水PH值调节到不小于3从各自的超标管中排放。
4取下阳极袋放到头过水缸或备用缸中用稀硫酸浸泡一小时左右,戴上胶手套搓洗,污水调节PH值不低于3后从综合水管排放。然后冲洗2-3遍,将内外两个阳极袋分开。
5.1电镀线槽液维护记录表FM/PD-020
六、附录
无
三、权责:
电镀部:负责电镀线槽液维护操作
工程部:负责制定槽液维护规范
四、内容:
4.1电镀线槽液维护要求:
水缸:水缸内不能有固体杂质和胶件,在打气过程中会擦花工件;水缸内壁不能有粘滑的感觉,也不能存在悬浮的有机物,会吸附到工件表面产生麻点。
铜、镍电镀槽的清洗操作
1.目的
指导作业,规范操作。
2.范围
适用于电镀铜槽、镍槽、电解槽清缸时的清洗,包括钛篮、钛篮袋、铜角、镍角、槽体与槽内附件的清洗。
3.使用工具
钢丝刷、百洁布、毛巾、围裙、雨鞋、安全帽、胶手套、胶桶、缽嘶。
4.工作前的准备
①穿戴好围裙、电镀设备雨鞋、手套、安全帽,手套必须过水、过酿、过烬;”才允许作业。
②关闭整流器、打气管、过滤机、加热管,洗净备用槽。
③揭开槽盖板及阳极杆盖板,将清缸的槽内溶液用过滤机抽至预备槽中。
④如有清洗槽为电解槽时则应取出电解板;如为电镀铜、镍槽需衛1夺:,钛篮袋无溶液流出时,再将其取出、置于清洗区内。
⑤当过滤机抽取溶液至预定液面时,改用小泵抽取,待小泵无液抽取时,采用人工打出,底层溶液需另外存放,待处理后,再加人大槽溶液中。
⑥电解板的清洗按照相关《极板清洗标准作业指导书》进行清洗。
5.操作
①钛篮、钛篮袋的清洗
②铜角、镍角的清洗
③槽体的清洗
(④将已清洗,装好铜角或镍角的钛篮挂回阳极杆上,将处理好的槽液用过滤机泵回镀槽,盖好阳极杆盖板。
⑤用纯水调整液面高度,分析调整镀液成分,开启过滤机并加热,70'槽试验调整光剂,小电流电解8h,待工艺参数正常后,方可试镀。
6,注意事项
①刷洗过程中,应轻拿轻放,注意安全。
②清槽时,在人未离开槽时,严禁启动行车调试。
③1清洗过程中,发现破损、漏液、变形等缺陷,应予以更换或修补。
④搞好工作场所的5S工作。
更多电镀设备,详见。
电镀清洗方法的分类和流程
电镀清洗方法的分类和流程电镀清洗是指在电镀工艺中,为了保证电镀件表面的质量和电镀层的附着力,需要对电镀件进行清洗处理。
电镀清洗方法根据不同的清洗过程和清洗剂的不同,可以分为多种类型。
常见的电镀清洗方法主要包括机械清洗、化学清洗和电解清洗。
1.机械清洗:机械清洗是通过利用机械设备来清除电镀件表面的杂质和污垢。
常见的机械清洗设备包括喷淋清洗机、喷流清洗机和超声波清洗机等。
机械清洗的主要流程如下:(1)预处理:将待清洗的电镀件进行初步清洗,去除较大的杂质和污垢。
(2)装载:将清洗件放入清洗机中,根据清洗机的工作原理选择不同的装载方式。
(3)清洗:启动清洗机,根据工艺要求选择合适的清洗剂和清洗工艺参数进行清洗,例如清洗时间、清洗温度和清洗喷嘴的位置等。
(4)排水:清洗后,将清洗液排出清洗机,进行处理或回收利用。
(5)干燥:将清洗干净的电镀件进行烘干或风干。
2.化学清洗:化学清洗是利用化学剂和溶剂来溶解或分解电镀件表面的杂质和污垢。
常见的化学清洗剂有酸性清洗剂、碱性清洗剂和复合清洗剂等。
化学清洗的主要流程如下:(1)预处理:将待清洗的电镀件进行初步清洗,去除较大的杂质和污垢。
(2)清洗剂配制:根据不同类型的清洗剂,按照一定的配方将清洗液配制好。
(3)浸泡清洗:将待清洗件放入清洗槽中,用清洗液进行浸泡清洗一定的时间,使清洗剂充分作用于电镀件表面的污垢。
(4)冲洗:清洗后,用水或其他溶剂将清洗剂冲洗干净。
(5)干燥:将清洗干净的电镀件进行烘干或风干。
3.电解清洗:电解清洗是利用电解化学原理来进行清洗,通过外加电源使电镀件与工艺溶液形成电池,利用阳极溶解物和阴极析物的通过电化学反应将电镀件表面的污垢清洗掉。
电解清洗的主要流程如下:(1)预处理:将待清洗的电镀件进行初步清洗,去除较大的杂质和污垢。
(2)电解槽配置:配置电解槽和电解液,在电解槽中放入阳极和阴极。
(3)电解清洗:将待清洗件放入电解槽中,通过外加电源使电镀件与电解液形成电池,清洗电镀件表面的杂质和污垢。
- 1、下载文档前请自行甄别文档内容的完整性,平台不提供额外的编辑、内容补充、找答案等附加服务。
- 2、"仅部分预览"的文档,不可在线预览部分如存在完整性等问题,可反馈申请退款(可完整预览的文档不适用该条件!)。
- 3、如文档侵犯您的权益,请联系客服反馈,我们会尽快为您处理(人工客服工作时间:9:00-18:30)。
99协和五金塑胶电镀制品厂HIP WO METAL AND PLASTIC ELECTROPLATING PRODUCT MANUFACT电镀生产工序之清缸处理方法1.目的:规范清缸操作2.适用范围:3.内容:3.1除油:不用做碳粉处理,清缸时需先关闭电热、蒸气和超声波,然后才能将溶液抽出,并用清水清洗干净棉芯、超声波等附属设备,要求每30-45天更换溶液。
3.2亲水:不用做碳粉处理,清缸时需先关闭电热和蒸气,然后才能将溶液抽出,并用清水清洗棉芯等附属设备,要求2-3个月更换全部溶液。
3.3粗化:要求每3-5个月更换一半溶液。
更换一半溶液时(约2200L),应先关闭电笔、蒸气和打气,静止2个小时以上,用专用泵从缸底抽一半溶液至预备好的沉降槽,然后往粗化缸内加入约1000L的纯水,启动打气,先加入计算量80%的铬酸片,待铬酸片完全溶解后,再徐徐加入计算量80%的硫酸(注:加入硫酸时,一定要注意粗化缸的温度不能超过80℃),加水至标准位,当粗化温度控制在61-63℃时,通知化验室取样分析,补加料后方可使用,每3个月清缸一次,清缸时先关闭电笔、蒸气和打气,用专用泵把粗化液抽至预备缸内,清洗干净缸体,加热等附属设备,疏通并安装好打气管,然后再将粗化液泵回,因清缸时,可能有溶液损失,故要通知化验室分析加料后,方可电镀生产。
3.4中和:不用分析和碳粉处理,每2-3天更换新溶液。
清缸时,先关闭打气及过滤系统,用潜水泵抽旧溶液至废水处理,清洗干净缸体及附属设备,然后方可重新开缸。
3.5 NP-8前盐酸缸:不用分析和碳粉处理,每1-2天更换新液。
清缸时,先关闭过滤系统,再用潜水泵抽旧溶液至废水处理,清洗干净缸体及附属设备,然后可重新开缸。
3.6 NP-8:不用作碳粉处理,但每星期需过缸滤,每2-4个月更换全部溶液。
清缸时,先将电热、冷水和过滤系统关闭,再把一台装有5-10UM棉芯的过滤泵的入口处蒙上细纱网,将NP-8溶液抽至清洗并抹干净的预备缸内,再将NP-8槽清洗并抹干净,用装有5-10UM的棉芯的过滤泵将NP-8抽回槽内,清洗干净循环过滤泵的棉芯,误启动循环过滤泵,电笔和冷水系统,通知化验室分析加料。
3.7活化硫酸:不用碳粉处理,1-2天更换新液。
清缸时,应先关闭电热,蒸所,打气和过滤系统,用泵将溶液抽至废水处理,清洗干净缸体,打气,加热用循环过滤系统,方可重新开缸。
3.8化学镍:化学镍的清缸是一个很重要的环节,也是防霉杀菌工作的重要手段,要求每周对镀液进行碳粉处理,碳粉添加量为3-5g/l,当亚磷酸钠的含量超过60g/l时,必须更换新溶液。
(a)关闭化学镍槽的电热,循环过滤泵系统,清洗并抹干净预备缸,并装好打气管。
(b)将装有5-10u的棉芯的抽液泵的入水口蒙上新纱网,抽化学镍溶液至预备缸内,在抽液的同进将计算量的活性碳粉徐徐加入镀液中,再启动打气(注:在加碳粉时,应将装活性碳粉的袋口浸入镀液中,再慢慢倒出活性碳粉,以避免碳粉四处飞扬,造成浪费和工作环境的污染)。
(c)当打气进行30-60分钟后,可停止打气,让镀液静止分层,便于以后过滤,同时可清洗干净化学镍镀槽及附属设备,若镀槽及其附属设备有上金属,要用炸水褪去,金属较厚的地方,用炸水褪除时较困难,所需时间较长,可用塑胶焊枪加温金属较厚的部位(注意:温度不能太高,造成胶体表面破损),然后设法剥去,注意千万不能将衬胶板的光洁表面破坏。
(d)镀槽衬胶的金属褪干净后,要用清水清洗并抹干净,再用装有5-10u棉芯的过滤泵经2级过滤后泵回化学镍槽(所谓二级过滤是指镀液要经过两个棉芯泵),以便将碳粉过滤干净,过滤完镀液后,过滤泵要清洗干净并要更换上新的棉芯,启动循环泵,加水至略低于标准水位,开启电笔,通知化验室分析加料,另外,清洗胶缸和过滤泵的清洗水要排放至高浓度废水处理槽,因为化学镍镀液是柠檬酸体系络合物,要经过特殊处理才能排出无害废水。
3.9化学镍后水洗:每天更换,用潜水泵将头过水抽至废水处理,清洗干净缸体,并用75%的酒精抹干净缸体杀菌,消毒,清洗干净后,再加入纯水,生产时应保持一定水流量。
3.10盐酸:不用作碳粉处理,1-2天更换新液,清缸时,先关闭循环过滤系统,然后用泵将溶液抽至废水处理,清洗干净缸体和过滤系统等附属设备,方可重新开缸。
3.11焦铜:每1-2星期作碳粉处理,清缸需按以下步骤进行:(a)关闭电热,蒸气,打气及循环过滤系统,准备好清洗干净并抹干的预备缸,并装好打气装置。
(b)用5u的棉芯泵将镀液抽至预备缸,并加入3-5g/l的活性碳粉,启动打气30-60分钟,然后让镀液静止分层,便于随后的过滤。
(c)清洗干净阳极,加热系统,打气管,导电铜棒,循环过滤系统,阳极袋及镀槽主体,并抹干净。
(d)添加电解铜至钛篮口,电解铜需经5%(v/v)的硫酸酸化1-2分钟,并清洗干净后方可加入钛篮并套上一层钛篮袋。
(e)碳粉处理后的镀液经静止1小时后,可用装有1-5um的棉芯泵作2级过滤回镀槽,然后将循环过滤泵换上新的1-5um的棉芯,加水至略低于标准水位,启动加热,打气,循环过滤系统,加热至工作温度后,通知化验室分析加热。
(f)清洗镀槽,胶缸,过滤泵的废水需排放至高浓度废水池进行处理。
3.12光铜前硫酸:不用作碳粉处理,每1-2天更换新液。
清缸时,先关闭循环泵,再将镀液排至废水处理,用清水清洗干净缸体和过滤系统,并抹干净缸体,方可重新开缸。
3.13光铜:每两周过滤缸一次,每30-45天需作碳粉处理(过滤缸与碳粉处理的方法基本相同,只是不加碳粉,以下只介绍碳粉处理的过程):(a)关闭冷水,循环过滤泵,整流机,打气,光剂自动添加系统等。
(b)准备好预备胶缸,清洗并抹干净,装好打气系统。
(c)用泵将镀液抽至预备胶缸内,加入3-5g/l的活性碳粉,并启动打气1-2小时。
(d)清洗干净阳极,阳极袋,冷却系统,打气管,导电铜棒,循环过滤系统及镀槽主体,并抹干净。
(e)补加磷铜角至钛篮口,磷铜需经3%(v/v)的稀硫酸浸泡1-2分钟,并清洗干净后,方可加入钛篮,随后套上3层阳极袋。
(f)活性碳粉处理后的镀液静止1小时后,可用1-5um的棉芯(或纤维芯)泵经2级过滤回光铜镀槽,过滤完后,要清洗干净胶缸和过滤泵及其棉芯。
(g)将光铜过滤泵清洗干净,并换上新的清洗干净的1-5um的棉芯,并启动循环泵,冷水系统,打气系统,加水至略低于标准位,通知化验室分析加料,调校光剂。
(h)所有废水均需排放至超标池。
3.14过硫酸铵:不用作碳粉处理,每2天更换新液,并清洗棉芯。
关闭打气和循环过滤系统,用泵将镀液抽至废水处理,用水清洗干净缸体和循环系统,并抹干净缸体,即可重新开缸。
3.15半光镍,光镍:每两周过缸滤一次,每30-45天需作碳粉处理(过缸滤和碳粉处理的基本相同,只是不加碳粉,下面只介绍碳粉处理过程):(a)关闭电热,蒸气,整流机,弱电解,打气,循环系统,PH值自动监测系统,光剂自动添加系统等。
(b)准备好打碳粉的胶缸,清洗并抹干净,装好打气系统。
(c)用泵将镀液抽至预备缸内,加入3-5g/l的活性碳粉,并启动打气1-2小时(注添加活性碳粉时,袋口一定要浸入镀液,再徐徐倒出活性碳粉)。
(d)清洗干净阳极,阳极袋,加热系统,打气管,导电铜棒,循环过滤系统,PH监测探头,弱电解猪笼,镀槽主体,并抹干净。
(e)添加镍角(或镍饼)至钛篮口,镍角需经3-5%(v/v)的稀硫酸浸泡1-2分钟,并用清水清洗干净后方可加入钛篮,随后套上3层阳极袋。
(f)经活性碳粉处理后的镀液静止1小时后,可用1-5um的棉芯(或纤维芯)泵作2级过滤回镀槽,过滤完后要清洗干净胶缸,过滤泵的棉芯。
(g)将循环过滤系统清洗干净并换上新的清洗干净的1-5um的棉芯(或纤维芯),加水至略低于标准水位后,启动循环过滤系统,加热系统,弱电解系统,PH监测系统,打气系统,当温度达到工作温度时,可通知化验室分析加料,调校光剂。
(h)所有废水需排放到超标池进行处理。
3.16封口镍:每30-45天作碳粉处理一次。
(a)关闭电热,蒸气,整流机,超振动器,循环过滤系统,PH值监测系统,光剂自动添加系统等,只保持打气,要待镀液抽毕后才可关闭打气。
(b)准备好碳粉处理胶缸,清洗并抹干净,装好打气管。
(c)在镀液温度低于40℃之前,用5-10um的棉芯泵将镀液抽至预备缸,加入3-5g/l 的活性碳粉,启动打气1-2小时(注添加活性碳粉时,袋口一定要浸入镀液,再徐徐倒出活性碳粉)。
(d)清洗干净阳极,阳极袋,加热系统,打气系统(一定要疏通),导电铜棒,循环过滤系统,PH自动监测探头,超振动器振板,镀槽主体并抹干净。
(e)添加镍角至钛篮口,镍角需经3-5%(v/v)的稀硫酸浸泡1-2分钟后,并用水清洗干净后方可装入钛篮,随后套上2层钛篮袋。
(f)经活性碳粉处理后的镀液静止1小时后,开启镀槽打气,再用1-5um的棉芯(或纤维芯)泵过滤回镀槽,过滤完毕后要清洗干净胶缸,过滤泵及其棉芯。
(g)将循环过滤系统清洗干净,并换上新的清洗干净的25-30um的棉芯,加水至略低于标准水位后,启动循环过滤系统,加热系统, PH自动监测系统,当温度达到工作温度时,可通知化验室分析加料,调整光剂,超振动器可在生产时才开启。
(h)所有清缸废水需排放到超标池进行处理。
3.17珍珠镍(暂不使用):正常开机时,每3-7天需作碳粉处理。
(a)关闭电热,蒸气,弱电解,整流机,打气,循环过滤系统,PH自动监测系统等。
(b)准备好碳粉处理胶缸,清洗并抹干净,装好打气管。
(c)在镀液温度低于40℃之前,用泵将镀液抽至预备胶缸,加入3-5g/l的活性碳粉,启动打气1-2小时(注:添加活性碳粉时,袋口一定要浸入镀液,再徐徐倒出活性碳粉)。
(d)清洗干净阳极,阳极袋(如有必要,阳极袋最好用10%(v/v)的稀硫酸和双氧水溶液浸泡1-2小时,加热系统,打气系统,导电铜棒,循环过滤系统,PH自动监测探头,镀槽主体并抹干净。
(e)添加镍饼至钛篮口,镍饼需经3-5%(v/v)的稀硫酸浸泡1-2分钟后,并用水清洗干净后方可装入钛篮,随后套上3层钛篮袋。
(f)经活性碳粉处理后的镀液静止1小时后,可用1-5um的棉芯(或纤维芯)泵作2级过滤回镀槽,过滤完毕后要清洗干净胶缸,过滤泵及其棉芯。
(注:由于珍珠镍的浓度较高,添加的碳粉也较多,容易造成过滤泵堵塞,所以在过滤过程中,要不时的暂停过滤,清洗棉芯)(g)将循环过滤系统清洗干净,棉芯泵换上新的清洗干净的1-5um的棉芯或纤维芯,碳粉泵则需换上新的清洗干净的碳粒,加水至略低于标准水位后,启动循环过滤系统,打气,当温度达到工作温度时,可通知化验室分析加料,做好开机生产前准备,至于光剂的调校,则需在开机生产前才调校,正式生产电镀时,不可开循环泵和打气,但须启动摇摆。