MRB异常处理作业规范
MRB作业办法

5.1特采处置方式
5.1.1会议决定通过对物料进行特采时。
5.1.2IQC对特采物料贴上特采物料标签,并在标签上注明特采原因,及使用条件。并发出《材
料不良通知单》给供应商分析改善。
5.1.3货仓在发特采物料给给生产时,必须在发料单上写明原因,使用条件。
5.1.4生产在领用特采物料上线时,必须通知工程和品管并依据工程的特采物料加工规范进行
加工。
5.1.5品管IPQC对特采物料上线需作特别追踪,一旦发生不良或异常,即通知停线,以免造成报废。
5.2返工处理方式
5.2.1会议决定通过对物料进行返工时。
5.2.2在第一时间通知供应商过来返工,若供应商未到我司处理,则由我司人员进行挑选,按14元/小时的单价,向供应商扣除返工工时费用。
5.2.3由IQC发出《材料不良通知单》要求供应商分析改善。
1.0目的
界定不良或可疑问题物料的处理方式,以免误用,造成品质问Байду номын сангаас。
2.0范围
适用于物料不良而无法判定处理方式。
3.0定义
MRB:(Material Review Board)物料评审委员会。
4.0权责
4.1成员构成:IQC+PMC+工程+采购
4.1.1IQC:将REJ之物料检验单立即交PMC并立即发出CAR。
4.1.2PMC:
a.填上材料上线日期。
b.依据材料紧急程度,决定是否召开MRB会议。如果是,则通知相关人员开会;如果不是,则将单据退还IQC,由IQC办理退货事宜。
4.1.3工程:做相关之实验,以作为WAIVE(特采)或其它决定依据。
4.1.4参与讨论执行MRB之结论(如向厂商扣款及要求及时补货等)。
QA2003 MRB处理流程A1
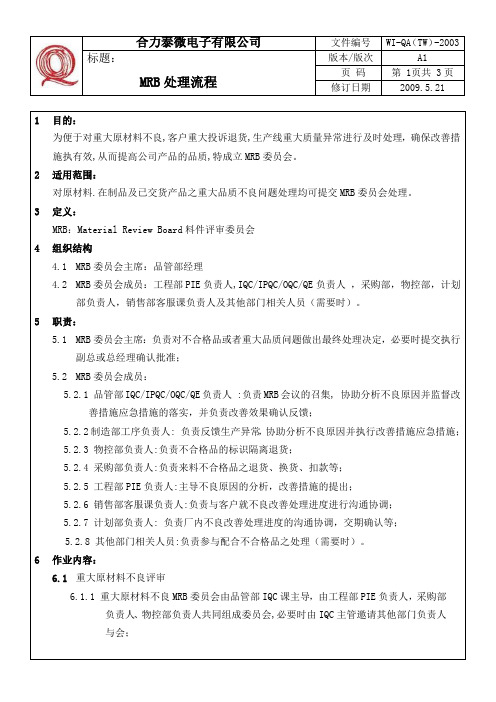
6.2.5报告评审完成后,各责任部门负责人需将应急由措施、改善措施、不良返工/补投/报废/全检。生产进度安排等传达相关岗位责任人执行,并由品管部IPQC人员对执行实施效果进行跟进及确认;纠正和预防措施验证效果不理想时,品管部IPQC负责人再次召集MRB委员会应进一步分析原因,按程序重新制定纠正和预防措施并组织实施,直至问题的解决。
6.3.3如品管部QE课人员与相关部门人员初步分析无法找到准确不良原因或认为质量问题严重时,则由品管QE主管立即召集MRB会议共同讨论分析,并将会议结论形成详细《客户退货分析报告》或《8D报告》;
6.3.4所有《客户退货分析报告》或《8D报告》均形成正式报告,均需经过MRB委员会共同评审并要求对应负责人签署,各责任部门负责人评审时需针对报告提出的原因分析、应急措施、改善措施、不良返工、补货安排等确认合理性、可行性;
7.2《客户退货分析报告》QR-WI/QA(TW)1010-01
7.3《8D报告》QR-QP/CH08-03
7.4《品质异常联络书》QR-WI/QA(TW)1015-01
编制
审核
批准
生效日期
6.1.3IQC判定不合格(含生产中发现的不合格)应批退之原物料或外协件,IQC人员即在填写“进料品质异常联络单”,由IQC主管初步确认签署;
6.1.4物控部人员看到“进料品质异常联络单”后,需充分考虑目前生产对此物料之急需程度及库存状况决定是否允许退货并确认签署;
6.1.5采购部人员看到“进料品质异常联络单”后,需充分考虑此物料之补货交期及计划部目前对此物料之急需程度判定是否接受退货并确认签署;
MRB作业指引

MRB作业指引1.0目的:严格控制资源浪费,规范MRB作业流程。
2.0范围:适用於PCB半成品及成品。
3.0使用工具:8倍镜修理刀黑色油性不脱色笔卡尺4.0作业流程:NG5.0作业步骤及内容:5.1 制程不良板需MRB确认的,须先由各工序责任人确认之后,方可於MRB确认,且有待MRB确认之型号及数量。
5.2 对客户退货板需MRB确认的,MRB作业按《顾客抱怨与投诉处理程序》7.0执行。
5.3 MRB审查员收到制程待打报废之板,应先认真核对型号及数量,确认无误后按质量检验规范《制程检验规范》和《成品检验规范》进行全检审查。
6.0审请报废板由MRB审查后,作以下两种方式处理:6.1 修理:PCB可以通过修理来达到或满足客户收货要求的,则退回相关部门修理。
6.2 报废:不能修理之板作报废处理且有相关部门主管或以上职级批准后方能生效。
7.0 报废品处理:7.1 制程半成品/成品单只打“X”仍可以收货的,需用黑色油性不脱色笔在PCB 正反两面打上“X”标记,如有客户要求,则按客户要求选择报废标记。
7.2 MRB审查员审查完之后,需将报废板之型号、工序、数量、及缺陷记入《物料异常报告单》中,报废板暂用红色(不良品)胶框存放,待相关工序查核后,按加工类型分类送至废品仓。
8.0 注意事项:8.1 MRB审查员对不能判定报废之板,须及时向直属上司反映,切忌自作主张。
8.2严格控制报废板,杜绝报废板再次外流。
8.3 品质审查标准:如客户没有要求,按本厂质量检验规范《制程检验规范》和《成品检验规范》或者IPC—A—600F进行检验、收货。
如有客户标准,则按客户标准进行检验、收货。
8.4凡是从事MRB作业活动,需由组长级或以上职级人员担任执行,其他任何人员无权从事MRB作业活动。
(特殊情况可以指定人员担任)8.5 MRB审查员有义务接受相关部门之监督。
9.0 参考文件:1.IPC—A—600F2.《制程检验规范》《成品检验规范》3.《客户投诉与退货处理程序》4.《物料异常报告单》。
MRB-流程制度
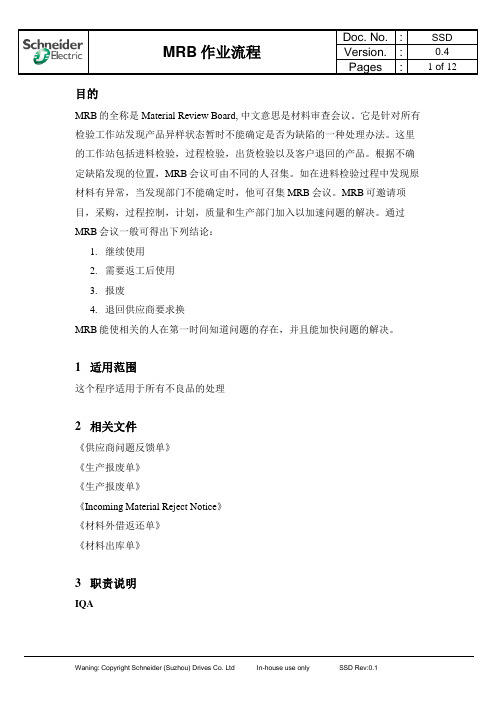
目的MRB的全称是Material Review Board, 中文意思是材料审查会议。
它是针对所有检验工作站发现产品异样状态暂时不能确定是否为缺陷的一种处理办法。
这里的工作站包括进料检验,过程检验,出货检验以及客户退回的产品。
根据不确定缺陷发现的位置,MRB会议可由不同的人召集。
如在进料检验过程中发现原材料有异常,当发现部门不能确定时,他可召集MRB会议。
MRB可邀请项目,采购,过程控制,计划,质量和生产部门加入以加速问题的解决。
通过MRB会议一般可得出下列结论:1.继续使用2.需要返工后使用3.报废4.退回供应商要求换MRB能使相关的人在第一时间知道问题的存在,并且能加快问题的解决。
1适用范围这个程序适用于所有不良品的处理2相关文件《供应商问题反馈单》《生产报废单》《生产报废单》《Incoming Material Reject Notice》《材料外借返还单》《材料出库单》3职责说明IQA负责对所有的来料进行检验,同时将检验出的不良品放置在IQC不良品区,填写《Incoming Material Reject Notice》,并且把不良品交给收货人员。
Receiving收货人员负责核对《Incoming Material Reject Notice》与不良品实物是否一致,并将实物放入MRB区域。
同时操作SAP系统。
SQE首先确认MRB的相关单据,把已经进入MRB区域的材料进行分类,并按照不同的类型处理SCM当IQA或SQE处理结果为退回供应商解决的时候,由SCM负责联系供应商,并按照退货流程处理4收货MRB流程5.1.仓库的收货人员按照收货流程收货,并且把收货单和实物交接给IQC。
5.2.IQC按照检验规定对需要检验的材料进行检验。
当发现不良品出现时,填写《Incoming Material Reject Notice》,并且把不良实物与《Incoming Material Reject Notice》一起交给Warehouse Receiving人员。
mrb小组与退补料作业指引+海能达产品特殊检验规范+客户投诉处理工作指引

版本
A
修改人
杨志刚
日期
2012.6.18
F329-A
版本
A
MRB小组与退补物料作业指引
编制
页码
4/5
审核
日期
2012.6.18
文件编号: WI-QC-052
批准
5.7.5生产线PO完成后须及时整理退料报告,来料坏物料经IPQC证实及IQC判定属实后入来料坏仓;生产坏料经IPQC证实后可直接退生产坏料仓。IQC负责指导生产线将来料坏物料按不同供应商分类和标识,并负责已入库来料坏物料已按供应商分开,仓库监督保证来料坏按供应商分类退料。
3)外购塑胶件素材不良的采购通知供应商返工补料, PMC部不申补物料.
4)外购塑胶件素材是良品,但经外发加工造成来料不良的, IQC要判定责任归属(是素材厂家还是加工厂家)及注明退料加工厂商名称,PMC部申补物料和按排退料作业,采购负责退料.
5)PMC依据<<采购申购单>>数量和《进料验收单》不良比例,综合判定是否需要依不良比例补料或部分补料.
4.3品管部:负责来料检验及物料不良报告的提出,生产线物料不良的分析确认,不良物料信息知会供应商和跟踪供应商的改进与处理,退补料的检验与判定。
4.4工程部/生产技术部:工程部协助品管部对物料不良进行分析和处理,并提供必要的检验工程图纸,样品及PCR给品管部。生产技术部对需要加工的物料提供技术及工具,治具支持。
a)包材料,吸塑类:PMC直接按《进料验收单》上的不良品比例安排申补,采购与供应商确认待生产完后退回不良品给供应商,不需要补货。不需要补货的,PMC打退货单时备注“不需要补货”。
MRB处理流程--属于三级文件。
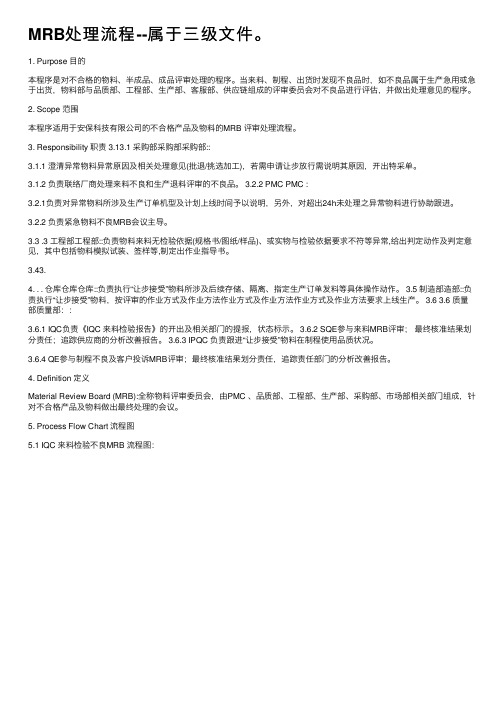
MRB处理流程--属于三级⽂件。
1. Purpose ⽬的本程序是对不合格的物料、半成品、成品评审处理的程序。
当来料、制程、出货时发现不良品时,如不良品属于⽣产急⽤或急于出货,物料部与品质部、⼯程部、⽣产部、客服部、供应链组成的评审委员会对不良品进⾏评估,并做出处理意见的程序。
2. Scope 范围本程序适⽤于安保科技有限公司的不合格产品及物料的MRB 评审处理流程。
3. Responsibility 职责 3.13.1 采购部采购部采购部::3.1.1 澄清异常物料异常原因及相关处理意见(批退/挑选加⼯),若需申请让步放⾏需说明其原因,开出特采单。
3.1.2 负责联络⼚商处理来料不良和⽣产退料评审的不良品。
3.2.2 PMC PMC :3.2.1负责对异常物料所涉及⽣产订单机型及计划上线时间予以说明,另外,对超出24h未处理之异常物料进⾏协助跟进。
3.2.2 负责紧急物料不良MRB会议主导。
3.3 .3 ⼯程部⼯程部::负责物料来料⽆检验依据(规格书/图纸/样品)、或实物与检验依据要求不符等异常,给出判定动作及判定意见,其中包括物料模拟试装、签样等,制定出作业指导书。
3.43.4. . . 仓库仓库仓库::负责执⾏“让步接受”物料所涉及后续存储、隔离、指定⽣产订单发料等具体操作动作。
3.5 制造部造部::负责执⾏“让步接受”物料,按评审的作业⽅式及作业⽅法作业⽅式及作业⽅法作业⽅式及作业⽅法要求上线⽣产。
3.6 3.6 质量部质量部::3.6.1 IQC负责《IQC 来料检验报告》的开出及相关部门的提报,状态标⽰。
3.6.2 SQE参与来料MRB评审;最终核准结果划分责任;追踪供应商的分析改善报告。
3.6.3 IPQC 负责跟进“让步接受”物料在制程使⽤品质状况。
3.6.4 QE参与制程不良及客户投诉MRB评审;最终核准结果划分责任,追踪责任部门的分析改善报告。
4. Definition 定义Material Review Board (MRB):全称物料评审委员会,由PMC 、品质部、⼯程部、⽣产部、采购部、市场部相关部门组成,针对不合格产品及物料做出最终处理的会议。
MRB特采作业管理办法
MRB特采作业管理办法1.0 目的1.1建立不良品信息沟通及处理平台,及时处理不良品,加强品质管控;1.2快速合理的进行品质缺陷判定,明确品质责任承担;2.0范围2.1 本文件适用于生产急用但与品质标准存在差异,需承担客诉风险之物料,且制造加工单位(含供应商)自身无法处理的物料管理,包括下述内容:2.1.1进料类【外协加工/采购物料经检验判退物料】;2.1.2制程在途类【制程加工在途物料/半成品及配件经检验判退物料】;2.1.3仓储类【仓储半成品及配件等物料经检验判退物料】;3.0 权责3.1 MRB小组组长:判定不合格物料处理结果以及责任承担单位;3.2 MRB小组成员:参与不合格物料评估并执行MRB决议,明确品质异常经济责任承担;4.0 管理办法内容4.1 MRB小组成员4.1.1 MRB小组组长—品质部经理;4.1.2 MRB小组成员—生产部经理、计划科主任、采购科主任、技术部经理、相关业务员;4.1.3必要时将临时邀请相关人员;4.2物料异常产生及MRB提出4.2.1公司所有外协加工/采购物料由品质部IQC人员予以检验,如发现来料与品质标准存在差异,但属于生产急用之物料,由采购科/计划科填写《紧急放行单》,品质部召集召开MRB会议;4.2.2制程在途与仓储异常物料,本车间无法修补的,由车间填写《产品质量异常信息反馈单》反馈至品质部,由品质部判定是否召集召开MRB会议;4.3 MRB评估4.3.1计划科:提供客户交期、计划编制、出货排程及补单安排;4.3.2 生产部:提供异常物料所造成进度影响,明确执行单位能否协助代加工/挑选,并承诺完成时间;4.3.3 技术部:评估异常物料能否正常使用,并提供技术支持;4.3.4 采购科:供应商信息沟通,供应商生产状况及供应商之回复,明确MRB产生费用归属,回复供应商返工之完成时间并办理退货、补货手续;4.3.5 业务部:客户沟通及确认;4.3.6 品质部:明确异常物料品质影响程度,判定结果【特采/返工/代加工/挑选/退货/正常使用】,判定责任承担单位并跟进MRB执行结果确认;4.3.7责任承担按《品质异常经济责任承担管理办法》实施;4.4 MRB评估决议及决议执行4.4.1 MRB评估内容须达成决议【特采/返工/代加工/挑选/退货/正常使用】并由品质部以《MRB评审记录表》记录存档,并通过公司邮箱传递相关部门;4.4.2 MRB小组成员须在《MRB评审记录表》签名确认;4.4.3 属生产部协助供应商代加工/挑选,则由生产部记录耗损的成本【工时/材料】,并填写《返修耗时/耗料记录表》上报采购科/财务部门;4.4.4 属品质部MRB全检执行挑选或代加工的(包括本厂制程产生的不良),由品质部负责将MRB产生费用及责任进行划分,并填写《返修耗时/耗料记录表》上报采购科/财务部,财务部执行扣款;4.5 MRB执行结果监督及确认4.5.1 品质部对MRB决议执行之结果予以监督,并判定是否符合要求;4.6 MRB全检组成人员4.6.1品质部品检科下属检验人员为主要实施人员;4.6.2 生产执行车间属MRB临时实施人员;4.7 实施4.7.1《MRB作业管理办法》自颁发日起实施;5.0 附件5.1《产品质量异常信息反馈单》;5.2《MRB评审记录表》;5.3《返修耗时/耗料记录表》;5.4《紧急放行单》;5.5《品质异常经济责任承担管理办法》;。
MRB作业规程
5.3.2.5采购部评估供应商退换货或重新采购对订单交期的影响,评估供应商关系,经济损失赔偿的难易程度。
5.3.2.6工程部评估不合格品处理对制造工艺、治具的影响程度,返修难易程度,对工艺、治具改善的影响。
5.3.2.7生产部评估对制程设备、人员、换线、物料及现场管理的影响,评估停线、挑选及返修的经济
5.3.4.4如果确定是“线上挑选”,IQC将不合格品贴“挑选”标签,通知仓库办理入库;然后由生产部办理领料领出,生产部安排线上全检,“合格品”直接使用,“不合格品”按《不合格品管理程序》规定进行标识与保存,待生产完结时集中将“不合格品”退回仓库,由采购部协调供应商办理退(换)货处理。IPQC全线跟踪该批物料的加工过程,监督线上挑选情况,并进行必要的抽检。生产部负责统计“挑选”人工费用,报财务部从供应商相应货款中抵扣。
5.3.4.3当判定结果是“挑选”时,如果是“线前挑选”,由采购部进行协调,确定由供应商或者IQC进行挑选,分出“合格品”与“不合格品”,并标识,如是供应商挑选,须经IQC按《来料检验标准》进行检验;“不合格品”由采购部协调供应商退换货,“合格品”通知仓库办理入库;如果是IQC挑选,IQC负责统计“挑选”人工费用,报财务部从供应商相应货款中抵扣。
广东锐涂精细化工有限公司
文件编号:
制定单位:品质部
制定日期:2017-7-11
三阶文件
MRB作业流程
修订日期:2017-7-11
版本:A/0
页数:4/6
损失等。
5.3.3各部门分别将评审结果填写在《MRB评审记录表》中,品质部经理再综合各部门意见,确定MRB结论,签字后报总经理审批。
5.3.4原物料MRB的处理
MRB物料评审作业办法
一. 适用范围:1.1 进料部分(进料检验判退部分)1.1.1 品质差异轻微超出允收水准,而生产急用者,但涉及品质标准(差异),设计规格(功能)及生产技术(结构组合技术)等,不易判定是否影响产品品质及生产技术。
1.1.2采购需求1.2 生产线部分(含已上线之原材料,半成品及成品部分)1.2.1生产线异常,经PE判定为材料不良。
二. 目的:对不合格品进行适当的处理,以减少不良品积压,同时便于不良品改善及追踪。
三. 定义:3.1 半成品:已部分加工并且等待继续加工之材料。
3.2 成品:已完成加工而可以销售之产品。
四.说明:4.1进料部分流程物料收料OKIQC检验原料仓NGQE会签Waive特采重工/sorting Reject4.1.1 IQC将退货讯息以电话方式知会QE和生管。
4.1.2生管依据生产计划物料紧急程度判定是否召开MRB meeting,并以通知QE,由QE召集相关单位(可采用会议形式或会签形式)。
4.1.3涉及单位如下:品质异常:生产,品管,生管,QE。
如有需要可要求其它相关单位参加,参加人员为各单位课级或课级以上主管指定代理人,并核签处理意见。
4.1.4 MRB会议做出以下决定:4.1.4.1针对退货之不良批,IQC依《不合格品控制程序》处理,由IQC通知生管于2日内要求厂商运回.4.1.4.2重工或SORTING针对原材料重工/SORTING,经MRB会议于“不合格品处理单”注明重工/SORTING方式,由生管通知厂商处理,需经IQC再次检验,如第二次检验仍判退,IQC有权拒收该LOT.4.1.4.3特采原材料,半成品,成品不符合原定规格而判定不会影响最终品质者依“特采申请单“特采,并由IQC于材料外箱贴附”特采”标签并注明MRB NO.如确属原材品质不良导致, 可经MRB会议决定追加扣款.4.1.5如因材料未承认退货依以下方式作业:A.用于or test阶段的材料,由台湾公司转售之材料,生管于“不合格品处理单”上注明“此批材料用于新机种试投”字样后, 生管部门主管签字即可.B.量产后未承认:由生管会签工程并Release to IQC.4.2生产线品质异常生产线品质异常IPQC判定原材料品质不良QE相关单位召开MRB meetingWaive特采 Rework/Sorting4.2.1生产线异常,由生管提出会议需求并通知QE.IPQC依据在开出“不合格品处理单“的同时暂停使用产品并贴附“不良标签”,由QE 召集相关单位召开MRB meeting.4.2.2涉及单位如下:QE 生管 IQC 仓库生产如有需要可要求其他相关单位参加。
MRB特采作业管理办法
MRB特采作业管理办法1.0 目的1.1建立不良品信息沟通及处理平台,及时处理不良品,加强品质管控;1.2快速合理的进行品质缺陷判定,明确品质责任承担;2.0范围2.1 本文件适用于生产急用但与品质标准存在差异,需承担客诉风险之物料,且制造加工单位(含供应商)自身无法处理的物料管理,包括下述内容:2.1.1进料类【外协加工/采购物料经检验判退物料】;2.1.2制程在途类【制程加工在途物料/半成品及配件经检验判退物料】;2.1.3仓储类【仓储半成品及配件等物料经检验判退物料】;3.0 权责3.1 MRB小组组长:判定不合格物料处理结果以及责任承担单位;3.2 MRB小组成员:参与不合格物料评估并执行MRB决议,明确品质异常经济责任承担;4.0 管理办法内容4.1 MRB小组成员4.1.1 MRB小组组长—品质部经理;4.1.2 MRB小组成员—生产部经理、计划科主任、采购科主任、技术部经理、相关业务员;4.1.3必要时将临时邀请相关人员;4.2物料异常产生及MRB提出4.2.1公司所有外协加工/采购物料由品质部IQC人员予以检验,如发现来料与品质标准存在差异,但属于生产急用之物料,由采购科/计划科填写《紧急放行单》,品质部召集召开MRB会议;4.2.2制程在途与仓储异常物料,本车间无法修补的,由车间填写《产品质量异常信息反馈单》反馈至品质部,由品质部判定是否召集召开MRB会议;4.3 MRB评估4.3.1计划科:提供客户交期、计划编制、出货排程及补单安排;4.3.2 生产部:提供异常物料所造成进度影响,明确执行单位能否协助代加工/挑选,并承诺完成时间;4.3.3 技术部:评估异常物料能否正常使用,并提供技术支持;4.3.4 采购科:供应商信息沟通,供应商生产状况及供应商之回复,明确MRB产生费用归属,回复供应商返工之完成时间并办理退货、补货手续;4.3.5 业务部:客户沟通及确认;4.3.6 品质部:明确异常物料品质影响程度,判定结果【特采/返工/代加工/挑选/退货/正常使用】,判定责任承担单位并跟进MRB执行结果确认;4.3.7责任承担按《品质异常经济责任承担管理办法》实施;4.4 MRB评估决议及决议执行4.4.1 MRB评估内容须达成决议【特采/返工/代加工/挑选/退货/正常使用】并由品质部以《MRB评审记录表》记录存档,并通过公司邮箱传递相关部门;4.4.2 MRB小组成员须在《MRB评审记录表》签名确认;4.4.3 属生产部协助供应商代加工/挑选,则由生产部记录耗损的成本【工时/材料】,并填写《返修耗时/耗料记录表》上报采购科/财务部门;4.4.4 属品质部MRB全检执行挑选或代加工的(包括本厂制程产生的不良),由品质部负责将MRB产生费用及责任进行划分,并填写《返修耗时/耗料记录表》上报采购科/财务部,财务部执行扣款;4.5 MRB执行结果监督及确认4.5.1 品质部对MRB决议执行之结果予以监督,并判定是否符合要求;4.6 MRB全检组成人员4.6.1品质部品检科下属检验人员为主要实施人员;4.6.2 生产执行车间属MRB临时实施人员;4.7 实施4.7.1《MRB作业管理办法》自颁发日起实施;5.0 附件5.1《产品质量异常信息反馈单》;5.2《MRB评审记录表》;5.3《返修耗时/耗料记录表》;5.4《紧急放行单》;5.5《品质异常经济责任承担管理办法》;。
- 1、下载文档前请自行甄别文档内容的完整性,平台不提供额外的编辑、内容补充、找答案等附加服务。
- 2、"仅部分预览"的文档,不可在线预览部分如存在完整性等问题,可反馈申请退款(可完整预览的文档不适用该条件!)。
- 3、如文档侵犯您的权益,请联系客服反馈,我们会尽快为您处理(人工客服工作时间:9:00-18:30)。
6.1 FM-QMD-033《品质异常处理单》 6.2 FM-QMD-038《IQC 来料检验报告》 6.3 FM-QMD-062《特殊放行申请表》
7.0 参考文件
7.1 COP8.3-01 《不合格品管理程序》 7.2 COP7.5-03 《标识和可追溯性管理程序》 7.3 COP4.2-02 《质量记录管理程序》 7.3 WI-QMD-006 《来料检验规范》
受”标贴时注明特采原因;
5.9.3 挑选加工:主要分为厂商挑选加工及本厂挑选加工。若为厂商挑选加工,物流部采
XXXXXX
文件标题:MRB 异常处理作业规范
文 件 编 号 : NNNNNNNNNNNN 版 本 号:A 生效日期:20 页 数:5/7
购员或 SQE 工程师通知厂商进行挑选加工处理,IQC 检验员负责监督和验收厂商挑 选加工效果及品质,如果重验 OK 则依《来料检验规范》办理允收作业,NG 则要求 厂商重新进行挑选加工,甚至要求判退处理;若为本厂挑选加工,不合格品物料急 于上线使用,而厂商不安排挑选加工时,将由 IQC 检验员或产线作业员临时安排挑 选加工作业,其挑选加工工时由临时挑选加工单位进行统计,具体挑选加工所耗工 时需转嫁供应商予以吸收,扣款单由物流部主导通知供应商并安排从供应商货款中 扣除。所有厂商挑选加工或本厂挑选加工后物料均需作好标示,以便可追溯其挑选 加工品质;
/仓库/生产管理部)进行备案存档;
5.8 MRB 成员评审签核及核准人员级别定义如下:
处理结果 退货
异常类别 1.外观不良退货 2.结构/尺寸/功能不良退货 3.RoHS 检测不良退货 4.来混料/来错料退货 1.外观不良特采
让步接受 2.结构/尺寸/功能不良特采
3.MRB 已判退,但物流部、销售部因料
5.2 异常单填写:IQC 在进料检验中发现不良,填写 4 联“IQC 来料检验报告”(若涉及尺寸 测量需一并填写“IQC 测量数据记录表”附页),对进料物料不良进行不良描述并提交 给 SQE 工程师进行确认 OK 后送各部门 MRB 成员评审;
5.3 当《IQC 来料检验报告》提报给各部门 MRB 成员评审时,非紧急物料按物料需求时间需 在 8H 内完成评审签核动作,紧急物料需在 4H 内完成评审签核动作。若《IQC 来料检验 报告》不能在规定时间内完成评审签核,IQC 将汇总《MRB 异常超时跟进明细》转生产管 理部协助跟进处理。若物料异常涉及结构、尺寸不良时,研发部/工程部工程师在评审签 核前必须进行模拟试装动作,以确保评审有效性;
电气设备中限制使用有毒有害物质指令; 3.3 让步接受:指物料在组装或使用过程中不影响产品主要结构与性能,或物料外观存在瑕
疵但不影响产品整体外观品质要求,或物料不良在使用过程中有明确解决与处理方法, 若满足以上之任一要求方可决定执行“让步接受”,也熟称之为“特采”;
4.0 职责
4.1 采购组:澄清异常物料异常原因及相关处理意见(批退/挑选加工),若需申请让步 放行需说明其原因,另外,协助联络厂商处理生产退料评审不良品;
文件名称:MRB 异常处理作业规范
文件编号: 版 本 号: 生效日期: 页 数:
A 201
7页
拟制/日期
审核/日期
批准/日期
(Prepared by/Date) (Reviewed by/Date) (Approved by/Date)
XXXXXX
文件标题:MRB 异常处理作业规范
文 件 编 号 : NNNNNNNNNNNN 版 本 号:A 生效日期:20 页 数:1/7
4.4 研发部:负责涉及研发人员主导设计产品或 NPI 新物料来料之异常物料无检验依据(规格 书/图纸/样品)、或实物与检验依据要求不符等异常给出判定动作及判定意见,其中包括 物料模拟试装、签样等;
4.5 仓库:负责执行“让步接受”物料所涉及后续存储、隔离、烘烤、先进先出、指定生产 订单发料等具体操作动作;
8.3 拆机物料MRB处理流程图
8.0 流程图
XXXXXX
文件标题:MRB 异常处理作业规范
8.1 来料物料MRB处理流程图
文 件 编 号 : NNNNNNNNNNNN 版 本 号:A 生效日期:20 页 数:6/7
XXXXXX
文件标题:MRB 异常处理作业规范
8.2 返修物料MRB处理流程图
文 件 编 号 : NNNNNNNNNNNN 版 本 号ຫໍສະໝຸດ A 生效日期:20 页 数:7/7
4.2PMC 部:负责对异常物料所涉及生产订单机型及计划上线时间予以说明,另外,对 超出 4H 未处理之异常物料进行协助跟进;
4.3 工程部:负责涉及工程人员主导设计产品或已量产物料来料之异常物料无检验依据(规 格书/图纸/样品)、或实物与检验依据要求不符等异常给出判定动作及判定意见,其中包 括物料模拟试装、签样等;
4.6 制造部:负责执行“让步接受”物料按评审要求在上线时作业方式及作业方法; 4.7 品质部:IQC 负责每日 MRB 异常提报、追踪、评估、核准,IPQC 负责跟进“让步接受”
XXXXXX
文件标题:MRB 异常处理作业规范
文 件 编 号 : NNNNNNNNNNNN 版 本 号:A 生效日期:20 页 数:3/7
5.4 MRB 成员组成主要为异常物料主要负责人,主要由物流部、生产计划部、工程部、研发 部、仓库、生产部、品质部、销售部或客服部等专员(含助理专员)以上级别成员组成;
5.5 当 MRB 成员对异常物料评审意见不一致时,SQE 工程师需对各成员评审意见进行评估确 认,原则上评估方向将遵循以下原则(主导单位为主、协助单位为辅。若异常物料为新 产品物料必须为研发部主导评审,若异常物料为曾已量产或曾已出货物料可以为工程部 主导评审。另外,若物流部、生产管理部若参与评审意见为让步放行,其评审结果仅作 参考);
物料所属 ALL
制造一部
不良类型 外观不良 功能不良
可靠性、RoHS 等其它不良
结构不良 尺寸不良
主导评审单位 IQC IQC
IQC
研发部 研发部
协助评审单位 OQC/物流部 研发部/工程部/物流部
OQC、工程部、制造部
工程部 工程部
XXXXXX
文件标题:MRB 异常处理作业规范
文 件 编 号 : NNNNNNNNNNNN 版 本 号:A 生效日期:20 页 数:4/7
Rev.
Revision History
修订摘要 (Revision description)
修订人
(Revised By)
修订日期 (Date)
XXXXXX
文件标题:MRB 异常处理作业规范
文 件 编 号 : NNNNNNNNNNNN 版 本 号:A 生效日期:20 页 数:2/7
1.0 目的
为使进料、制程物料异常能及时、有效的进行处理,杜绝异常物料被误判、误用进而影响生 产及出货,特拟定此程序;
物料在制程使用品质状况,IQC 对 MRB 最终核准结果划分权责归属并追踪责任单位分析 与改善; 4.8 销售部或客户部:负责客户指定物料或单品出货异常物料提供相关处理意见;
5.0 工作程序
5.1 材料异常提报: 5.1.1 进料物料异常由 SQE 工程师级以上人员进行确认; 5.1.2 制程物料异常由 IPQC/OQC 工程师级以上人员进行确认;
制造二部
结构不良 尺寸不良
自助研发部 自助研发部
工程部 工程部
单品出货
ALL Defects
IQC
销售部/客户服务部
拆机物料
ALL Defects
IQC
仓库/制造部/物流部
返修物料
ALL Defects
IQC
仓库/物流部
5.6 当 MRB 最终评审结果判定为退货,物流部、销售部等单位因料况紧张或其它原因,急需
申请“让步接收”(特采)时,由物流部主导提报申请《特殊放行申请单》送各部门 MRB
成员之主管以上级别进行评审签核确认;
5.7 IQC 依据 MRB 最终评审结果对物料执行最终处理动作(签核“到货单”并对物料外箱进
行加盖印盖或标贴),并将最终评审之“IQC 来料检验报告”附联转交 MRB 成员(物流部
况或其它原因申请改判为特采
挑选加工
1.外观/结构/尺寸/功能不良重工 2.制程不良重工
5.9 MRB 评审最终处理结果:
签核人员级别 MRB 各成员 MRB 各成员 MRB 各成员 MRB 各成员 MRB 各成员
MRB 各成员/MRB 各成员直属主管 MRB 各成员直属主
管/经理 MRB 各成员 MRB 各成员
核准极别 IQC 主管 IQC 主管 IQC 主管 IQC 主管 IQC 主管
IQC 主管
质量管理部经理/ 品质体系副总 IQC 主管 OQC 主管
5.9.1 退货:IQC 依《来料检验规范》办理物料验退工作,仓库负责将物料退厂商;
5.9.2 让步接受:IQC 依《来料检验规范》加贴“让步接受”标贴于最小包装并注意特采
原因后,并在《到货单》上进行签名确认,仓库根据《到货单》确认内容在 ERP 系
统中进行允收作业。生产线在使用特采物料时,IPQC 须监督物料上线使用方法及品
质状况并及时进行反馈。当 MRB 结果要求锁定生产订单/生产线别/客户机型等使用
时,由生产管理部 PMC 及仓库进行全程安排及操作,IQC 允收入库并加贴“让步接
2.0 适用范围
涉及本公司所有进料异常或制程异常,均列入此 MRB 评审会议之决定;
3.0 术语和定义
3.1 MRB(Material Review Board):物料评审委员会; 3.2 RoHS(the Restriction of the use of certain Hazardous Substances):关于在电子