机械加工质量技术
机械加工过程中的质量控制与检测技术

机械加工过程中的质量控制与检测技术随着科技的不断进步,机械工程在制造领域发挥着重要的作用。
机械加工是制造过程中不可或缺的环节,而质量控制与检测技术则是确保机械制造的关键。
本文将探讨机械加工过程中的质量控制与检测技术,并介绍其中一些常用的方法。
一、质量控制的重要性在机械加工过程中,质量控制是确保产品符合设计要求的关键。
一旦产品质量出现问题,不仅会影响到产品的性能和可靠性,还可能导致安全隐患和经济损失。
因此,质量控制在机械工程中具有重要意义。
二、质量控制方法1. 设计阶段的质量控制:在机械加工之前,设计阶段的质量控制非常关键。
通过合理的设计和工艺规划,可以减少制造过程中的错误和缺陷,提高产品的质量和可靠性。
2. 加工参数的控制:在机械加工过程中,控制加工参数是确保产品质量的重要手段。
例如,对于数控加工,控制切削速度、进给速度和切削深度等参数,可以保证加工精度和表面质量。
3. 检测与测量:质量控制离不开检测与测量。
通过使用各种测量工具和设备,如千分尺、游标卡尺和高度规等,可以对产品的尺寸和形状进行测量,以确保其符合设计要求。
三、常用的检测技术1. 硬度检测:硬度是材料抵抗外力的能力,对于机械加工来说非常关键。
硬度检测可以通过硬度计等设备进行,以评估材料的硬度是否符合要求。
2. 表面粗糙度检测:表面粗糙度对于机械零件的功能和耐久性有着重要影响。
通过使用表面粗糙度仪等设备,可以对零件表面的光洁度进行检测,以确保其满足设计要求。
3. 尺寸测量:尺寸测量是机械加工中最常见的检测技术之一。
通过使用精密测量工具,如三坐标测量机和光学投影仪,可以对零件的尺寸进行精确测量,以确保其符合设计要求。
四、质量控制与检测技术的挑战在机械加工领域,质量控制与检测技术面临着一些挑战。
首先,随着制造工艺的不断发展,产品的复杂性和精度要求不断提高,对质量控制和检测技术提出了更高的要求。
其次,制造过程中的变异性和误差也会对质量控制造成挑战,需要采取措施来减少其影响。
浅析机械加工中的质量技术问题

机 械 加 工 精 度
1 械 加 工 精 度 的 含 义 及 内容 机
加 工 精 度 是 指 零 件 经 过 加 工 后 的 尺 寸 、 何 形 状 以 及 各 表 面 相 互 位 置 等 参 数 几 的 实 际值 与 理 想 值 相 符 合 的 程 度 , 它 们 而
之 间 的 偏 离程 度 则 称 为 加 工 误 差 。 工 精 加 度在数值上 通过加 工误差 的大小来表示 。 零 件 的 几 何 参 数 包 括 几 何 形 状 、 寸 和 相 尺
互 位置 三 个 方 面 , 加 工 精度 包 括 :i尺 寸 故 () 精 度 。 寸 精 度 用 来 限 制 加 工 表 面 与 其 基 尺 准 问 尺 寸 误 差 不 超 过一 定 的 范 围 。2 几 何 () 形 状 精 度 。 何 形 状 精 度 用 来 限 制 加 工 表 几 面宏观几何形状 误差 , 圆度 、 柱度 、 如 圆 平 面度 、 线度 等 。3 相互 位 置 精 度 。 互 位 直 () 相 置精 度 用 来 限制 加 工 表 面 与其 基 准 间 的相 互 位置 误 差 , 平 行度 、 直 度 、 如 垂 同轴 度 、 位 置度 零 件 各 差 来 表 示 的要 求 和 允 许 用 专 门 的符 明 。 在 相 同 中 的各 种 因对 准 确 和 完 足 产 品 的工 加 工 方 法 , 生 产 条 件 下 所 加 工 出 来 的 的一批零件 , 由于 加 工 素 的 影 响 , 尺 寸 、 其 形 状 和 表 面 相 互 位 置 不 会 绝 全 一 致 , 是 总 存 在 一 定 的 加 工 误 差 。 时 , 满 作 要 求 的 同 从 公 差 范 围 的前 提 下 , 采 取 合 理 的 经 济 以 要 提高机械 加工的生产率和经济性 。
机械零件加工质量检验技术研究

机械零件加工质量检验技术研究摘要:在机械生产中,大部分机械零件都是批量生产的产品,在技术、环境等因素的作用下,很容易出现质量问题,所以要想进一步提升机械零件质量,就要加强机械零件加工质量检验工作。
机械零件加工质量检验内容机械零件的长度、角度及表面粗糙程度等测量,在这个过程中,需要应用专业的检测技术,同时,还需要完善相应的管理制度,以便于及时的发现零件缺陷,消除机械运行风险。
下文对此进行简要的阐述。
关键词:机械零件;质量检验;技术要点;控制策略一、机械零件加工质量检验技术要点(一)感觉检验法这种方法的一些精度较高的零件检验当中并不适用,同时对于检验人员自身也有着较高的标准和要求。
如果工作人员的经验较为丰富,那么检验结果的准确性就较高。
但如果工作人员的经验不够丰富,在运用这种方法后,检验的结果就无法得到保障。
所以这种检验的方式只能作为定性检验与鉴定的一种方法进行应用。
通常感觉检验法主要包括三种类型,第一种是目测法,就是通过肉眼或是利用放大镜对机械零件进行观察,这样就能够对零件的磨损破坏程度进行确定,如果零件有明显的变形,裂纹或是疲劳脱落则可以通过这种方法进行观察。
第二种是触觉法,即通过工作人员的手触摸零件表面一次进行判断,这种方法能够根据零件表面磨损痕迹的深浅度,对磨损的情况进行大致判断。
如果零件是刚进入工作状态,通过手就可以感受到零件的温度,这样就能对零件的具体工作情况进行评判。
第三种则是耳听法,也就是工作人员通过敲击或是零件工作过程中所发出的声音,对零件的实际运行状况进行评判。
如果对零件敲击时所发出的声音较为清脆,那么零件就不存在缺陷,如果声音较为沉闷,零件就有可能存在沙眼或是裂纹的情况。
在具体的应用中,工作人员也可凭借自身的工作经验,选择相应的感觉检验法对零件的质量进行检验及鉴定。
(二)仪器检验法在应用这种检验方法时,需要工作人员具备一定的技术操作能力,同时对于相关的检验工具也要有详细的了解,否则工作人员就无法操作相关的检验设备及器械。
机械加工质量技术分析

浅谈机械加工质量技术分析摘要:机械加工产品质量与很多因素有关,其中最重要的两个因素是:①零件的加工质量。
②产品的装配质量。
这两个影响机械加工质量的重要因素又是有一定关系的,其中零件的加工质量是保证机械加工产品质量的基础,零件加工质量的提高是提高产品装配质量的前提条件。
本文对机械加工质量技术进行了分析,重点探讨了机械加工精度以及机械加工工艺系统的几何误差。
关键词:精度质量工艺系统原始误差机械加工1 机械加工精度1.1 机械加工精度的含义与内容机械加工精度是衡量机械加工产品质量的一个重要指标,机械加工精度的含义指的是零件在经过机械加工以后的实测尺寸、零件的外形几何形状以及零件的各表面相互位置等参数的实际测量值与理想值差距程度,离理想值越接近代表精度越高,反之则精度越低。
零件加工处理后的实际测量值与理想值之间的偏离程度一般就称为机械加工误差。
零件的加工精度包括:①零件的尺寸精度。
②零件的几何形状精度。
③零件的相互位置精度。
1.2 影响机械加工精度的原始误差在机械加工过程中,对工艺系统产生影响的因素是非常多的,这也就是出现很多原始误差的一个重要原因,因此需要重点分析这些因素以便尽量减少对机械加工精度的影响。
原始误差的产生主要是由两方面所造成的,其中一方面是由于机械加工工艺系统本身的结构所决定的,这些原始误差因为系统各个部件以及部件之间的间隙等诸多因素构成了无法消除影响因素。
人们只能尽量减小这些因素对原始误差的影响但不可能消除其影响。
另一方面原始误差是由于零件在加工过程中进行了切削操作而产生的。
1.3 机械加工误差的分类1.3.1 系统误差与随机误差这两种分类的主要依据是看人们是否认识并掌控这种误差,凡是人们已经认识并能够掌控误差的大小和方向的都列为系统误差。
反之人们没有认识并掌控的一类误差就列为随机误差也叫偶然误差。
系统误差又可以根据误差数值是否是固定值来分为常值系统误差和变值系统误差。
1.3.2 静态误差、切削状态误差与动态误差误差的分类还有很多种方式,其中把工艺系统是否在切削状态下所产生的误差这一实际情况当做区分静态误差跟切削状态误差的判断依据。
关于对机械加工质量技术的分析

各方面性 能, 减少不稳 定性带来的误差。 ( 2 ) 机床主轴的回转精度对工件 的加工精度有直接影 响, 从而变成造成 主轴回转运动直接误差。所谓主轴的回转精度是指主轴的实 际回转轴线相 对其平均 回转轴线的漂移 。在原理上说 , 当主轴进行回转时, 在空间位置当 中其回转轴线 的位置是固定不变的, 也就是说理论上瞬时速度为零。 可是在
一
基准与工序基准作 比较, 使两项基准重合 , 即为: 实际当中的工件设计尺寸 大小和位置应与工序 图上规定的工件尺寸大小和位置所重合 。从而达 到其 正确精度 , 减小了定位误差。当进行几件加工的时候, 工件的几何元素就成 为了其主要基准, 如果几何元素的实际基准与规定基准不符合 , 就会 造成精 度不准确。 也就成为了基准补充和误差 的最大的变动量。 只有当采用调整法 生产工件的时候才会产生基准不重合误差, 在其它加工法 中不会出现。 夹具 中工件的位置是 由夹具中的定位元确定。定位 元件在制造 时肯定达不到理 想 的标准效果, 都在一定范围内变动。 当然 , 定位基准面也有制造误差。 定位 副制造的不精确再加上定为福建的间隙引起工件最大变动量 叫做定位副制
第 一 种 为 瞬 时 回转 轴 线 沿平 均 回 转轴 线 方 向的轴 向运 动 即 为轴 向窜 动 第
超过了金属相变的最高温度 , 从而 导致技术材料表面的物理特性发生改变, 破坏其表面 的组织结构, 造成材料无法符合原有 的要求。 所以一定要控制住 机械的物理摩擦, 提高物理冷却能力 , 从而减少 由于这方面 的误差带来的不
造 不 准 确误 差 。 它 和 基准 不重 合 误 差 的方 向不 太 相 同 。 而 定 位 误差 取 得 时 他 们 的矢 量和 。
量, 所 以如何保证其出产质量 , 保证其零部件的完好程度, 则成 了现在 工业 当中所要面对的一项重要课题 , 下面我们 就通过精度、 误差 、 粗 糙度等三 个 方面来系统的阐述一下。 1 . 机械加工质量
机械加工过程中的质量控制简版
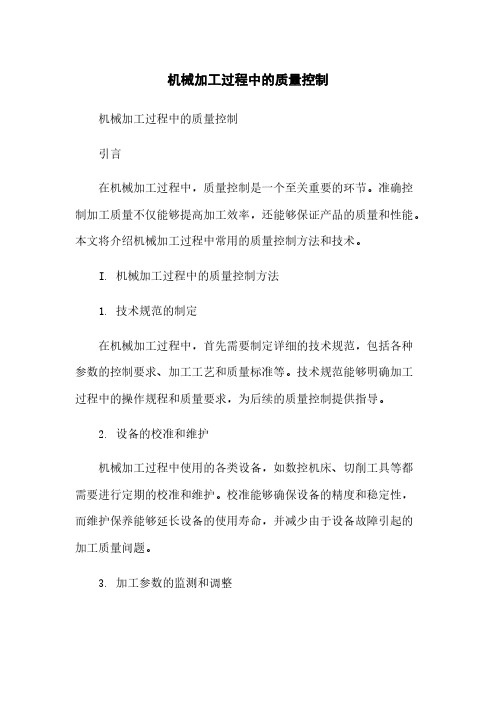
机械加工过程中的质量控制机械加工过程中的质量控制引言在机械加工过程中,质量控制是一个至关重要的环节。
准确控制加工质量不仅能够提高加工效率,还能够保证产品的质量和性能。
本文将介绍机械加工过程中常用的质量控制方法和技术。
I. 机械加工过程中的质量控制方法1. 技术规范的制定在机械加工过程中,首先需要制定详细的技术规范,包括各种参数的控制要求、加工工艺和质量标准等。
技术规范能够明确加工过程中的操作规程和质量要求,为后续的质量控制提供指导。
2. 设备的校准和维护机械加工过程中使用的各类设备,如数控机床、切削工具等都需要进行定期的校准和维护。
校准能够确保设备的精度和稳定性,而维护保养能够延长设备的使用寿命,并减少由于设备故障引起的加工质量问题。
3. 加工参数的监测和调整机械加工过程中的加工参数包括切削速度、进给速度、切削深度等。
通过实时监测和调整这些加工参数,可以保证加工过程中的稳定性和一致性,并避免加工中出现质量问题。
4. 质量检测和控制质量检测和控制是机械加工过程中最基础的质量控制环节。
通过使用各种检测设备和方法,如测量仪器、显微镜等,对加工过程中的尺寸、形状、表面质量等进行检测和判定。
对于不符合要求的产品,需要及时采取纠正措施,以保证产品达到质量标准。
II. 常用的质量控制技术1. 先进的数控技术随着科技的进步,先进的数控技术在机械加工过程中得到了广泛应用。
数控技术通过预先设定的程序来控制加工过程,实现高精度、高效率的加工作业。
同时,数控技术还能够监测加工过程中的各种参数,并根据实际情况进行自动调整,保证加工质量的稳定性。
2. 光学成像技术光学成像技术通过显微镜或相机等设备,对制件表面的质量进行实时观测和检测。
这种技术可以快速获得制件的表面形状、表面光滑度等质量指标,从而实现对加工质量的实时监控和控制。
3. 技术技术在机械加工过程中的质量控制中正发挥着越来越重要的作用。
通过对大量的数据进行分析和学习,技术能够自动识别和判断加工过程中的质量问题,并作出相应的调整和反馈。
机械加工质量技术控制[方案]
![机械加工质量技术控制[方案]](https://img.taocdn.com/s3/m/5b6b9735492fb4daa58da0116c175f0e7cd11916.png)
机械加工质量技术控制摘要:本文介绍了机械加工精度的概念及内容,分析了机械加工产生误差的原因,最后提出提高机械加工精度的工艺措施。
关键词:机械加工精度;几何误差;定位误差;工艺1机械加工精度的概念及内容机械加工精度是指零件加工后的实际几何参数(尺寸、形状和位置)与理想几何参数相符合的程度。
它们之间的差异称为加工误差。
加工误差的大小反映了加工精度的高低。
误差越大加工精度越低,误差越小加工精度越高。
加工精度包括三个方面内容:尺寸精度指加工后零件的实际尺寸与零件尺寸的公差带中心的相符合程度;形状精度指加工后的零件表面的实际几何形状与理想的几何形状的相符合程度;位置精度指加工后零件有关表面之间的实际位置与理想。
在相同中的各种因对准确和完足产品的工加工方法,的生产条件下所加工出来的一批零件,由于加工素的影响,其尺寸、形状和表面相互位置不会绝全一致,总是存在一定的加工误差。
同时,从满作要求的公差范围的前提下,要采取合理的经济以提高机械加工的生产率和经济性。
2机械加工产生误差主要原因2.1机床的几何误差加工中刀具相对于工件的成形运动一般都是通过机床完成的,因此,工件的加工精度在很大程度上取决于机床的精度。
机床制造误差对工件加工精度影响较大的有:主轴回转误差、导轨误差和传动链误差。
机床的磨损将使机床工作精度下降。
(1)主轴回转误差,机床主轴是装夹工件或刀具的基准,并将运动和动力传给工件或刀具,主轴回转误差将直接影响被加工工件的精度。
(2)导轨误差,导轨是机床上确定各机床部件相对位置关系的基准,也是机床运动的基准。
除了导轨本身的制造误差外,导轨的不均匀磨损和安装质量,也使造成导轨误差的重要因素。
导轨磨损是机床精度下降的主要原因之一。
(3)传动链误差,传动链误差是指传动链始末两端传动元件间相对运动的误差。
一般用传动链末端元件的转角误差来衡量。
2.2 刀具的几何误差刀具误差对加工精度的影响随刀具种类的不同而不同。
采用定尺寸刀具成形刀具展成刀具加工时,刀具的制造误差会直接影响工件的加工精度;而对一般刀具,其制造误差对工件加工精度无直接影响。
机械加工中的质量检测技术

机械加工中的质量检测技术引言机械加工是现代工业生产过程中不可或缺的一环。
在机械加工过程中,质量检测是确保产品质量的重要环节。
本文将介绍机械加工中常用的质量检测技术,包括尺寸检测、表面质量检测和材料质量检测等方面的内容。
尺寸检测尺寸检测是机械加工中最基本、最常用的一种质量检测技术。
它用于检测加工零件的尺寸是否符合设计要求。
在尺寸检测中,常用的工具有千分尺、游标卡尺、测微计和三坐标测量机等。
这些工具可以精确测量零件的直径、长度、宽度等尺寸参数,并与设计要求进行对比,以判断零件的质量是否合格。
表面质量检测表面质量检测是机械加工中另一个重要的质量检测技术。
它用于检测零件表面的光洁度、光滑度和平整度等指标。
常用的表面质量检测方法有目视检测、触摸检测和测量仪器检测。
目视检测是最简单的一种检测方法,操作方便,但只能判断表面质量是否达到一定的标准。
触摸检测则可以通过手感来判断表面的光滑度和平整度。
测量仪器检测则更加精确,可以使用光学仪器、扫描仪等设备对表面进行数字化测量和分析,以获取更详细的表面质量信息。
材料质量检测材料质量检测是机械加工中另一个关键的质量检测环节。
它用于检测加工材料的化学成分、物理性能和力学性能等参数。
常用的材料质量检测方法有化学分析法、光学显微镜观察和拉伸试验等。
化学分析法可以通过检测材料中的元素含量来判断材料的化学成分是否符合要求。
光学显微镜观察可以用来观察材料中的晶粒结构和夹杂物等微观结构信息。
拉伸试验则可以通过施加拉力来测试材料的力学性能,如抗拉强度、屈服强度和延伸率等指标。
其他质量检测技术除了尺寸检测、表面质量检测和材料质量检测外,机械加工中还有一些其他的质量检测技术。
例如,硬度检测可以用来测试零件的硬度,常用的方法有布氏硬度和洛氏硬度等。
渗透检测可以用来检测零件表面的裂纹和孔洞等缺陷,常用的方法有涂布法和浸泡法等。
磁粉检测可以用来检测零件表面和内部的裂纹和缺陷,常用的方法有湿法和干法等。
- 1、下载文档前请自行甄别文档内容的完整性,平台不提供额外的编辑、内容补充、找答案等附加服务。
- 2、"仅部分预览"的文档,不可在线预览部分如存在完整性等问题,可反馈申请退款(可完整预览的文档不适用该条件!)。
- 3、如文档侵犯您的权益,请联系客服反馈,我们会尽快为您处理(人工客服工作时间:9:00-18:30)。
机械加工质量技术分析研究
[摘要]:机械加工产品的质量与零件的加工质量、产品的装配质量密切相关,而零件的加工质量是保证产品质量的基础,它包括零件的加工精度和表面质量两方面。
[关键词]:机械加工精度几何形状工艺系统误差
中图分类号:tq320.67+1 文献标识码:tq 文章编号:1009-914x(2012)20- 0016 -01
一、机械加工精度
(一)机械加工精度的含义及内容
加工精度是指零件经过加工后的尺寸、几何形状以及各表面相互位置等参数的实际值与理想值相符合的程度,而它们之间的偏离程度则称为加工误差。
加工精度在数值上通过加工误差的大小来表示。
零件的几何参数包括几何形状、尺寸和相互位置三个方面,故加工精度包括:(1)尺寸精度。
尺寸精度用来限制加工表面与其基准间尺寸误差不超过一定的范围。
(2)几何形状精度。
几何形状精度用来限制加工表面宏观几何形状误差,如圆度、圆柱度、平面度、直线度等。
(3)相互位置精度。
相互位置精度用来限制加工表面与其基准间的相互位置误差,如平行度、垂直度、同轴度、位置度零件各差来表示的要求和允许用专门的符明。
在相同中的各种因对准确和完足产品的工加工方法,的生产条件下所加工出来的一批零件,由于加工素的影响,其尺寸、形状和
表面相互位置不会绝全一致,总是存在一定的加工误差。
同时,从满作要求的公差范围的前提下,要采取合理的经济以提高机械加工的生产率和经济性。
(二)影响加工精度的原始误差
机械加工中,多方面的因素都对工艺系统产生影响,从而造成各种各样的原始误差。
这些原始误差,一部分与工艺系统本身的结构状态有关,一部分与切削过程有关。
按照这些误差的性质可归纳为以下四个方面:(1)工艺系统的几何误差。
工艺系统的几何误差包括加工方法的原理误差,机床的几何误差、调整误差,刀具和夹具的制造误差,工件的装夹误差以及工艺系统磨损所引起的误差。
(2)工艺系统受力变形所引起的误差。
(3)工艺系统热变形所引起的误差。
(4)工件的残余应力引起的误差。
(三)机械加工误差的分类
1.系统误差与随机误差。
从误差是否被人们掌握来分,误差可分为系统误差和随机误差(又称偶然误差)。
凡是误差的大小和方向均已被掌握的,则为系统误差。
系统误差又分为常值系统误差和变值系统误差。
常值系统误差的数值是不变的。
如机床、夹具、刀具和量具的制造误差都是常值误差。
变值系统误差是误差的大小和方向按一定规律变化,可按线性变化,也可按非线性变化。
如刀具在正常磨损时,其磨损值与时间成线性正比关系,它是线性变值系统误差;而刀具受热伸长,其伸长量和时间就是非线性变值系统误差。
凡是没有被掌握误差规律的,则为随机
误差。
2.静态误差、切削状态误差与动态误差。
从误差是否与切削状态有关来分,可分为静态误差与切削状态误差。
工艺系统在不切削状态下所出现的误差,通常称为静态误差,如机床的几何精度和传动精度等。
工艺系统在切削状态下所出现的误差,通常称为切削状态误差,如机房;在切削时的受力变形和受热变形等。
工艺系统在有振动的状态下所出现的误差,称为动态误差。
二、工艺系统的几何误差
(一)加工原理误差
加工原理误差是由于采用了近似的成形运动或近似的刀刃轮廓进行加工所产生的误差。
通常,为了获得规定的加工表面,刀具和工件之间必须实现准确的成形运动,机械加工中称为加工原理。
理论上应采用理想的加工原理和完全准确的成形运动以获得精确的零件表面。
但在实践中,完全精确的加工原理常常很难实现,有时加工效率很低;有时会使机床或刀具的结构极为复杂,制造困难;有时由于结构环节多,造成机床传动中的误差增加,或使机床刚度和制造精度很难保证。
因此,采用近似的加工原理以获得较高的加工精度是保证加工质量和提高生产率以及经济性的有效工艺措施。
例如,齿轮滚齿加工用的滚刀有两种原理误差,一是近似造型原理误差,即由于制造上的困难,采用阿基米德基本蜗杆或法向直廓基本蜗杆代替渐开线基本蜗杆;二是由于滚刀刀刃数有限,所切出的齿形实际上是一条折线而不是光滑的渐开线,但由此造成的齿
形误差远比由滚刀制造和刃磨误差引起的齿形误差小得多,故忽略不计。
又如模数铣刀成形铣削齿轮,模数相同而齿数不同的齿轮,齿形参数是不同的。
理论上,同一模数,不同齿数的齿轮就要用相应的一把齿形刀具加工。
实际上,为精简刀具数量,常用一把模数铣刀加工某一齿数范围的齿轮,也采用了近似刀刃轮廓。
(二)机床的几何误差
1.主轴回转运动误差的概念。
机床主轴的回转精度,对工件的加工精度有直接影响。
所谓主轴的回转精度是指主轴的实际回转轴线相对其平均回转轴线的漂移。
理论上,主轴回转时,其回转轴线的空间位置是固定不变的,即瞬时速度为零。
实际上,由于主轴部件在加工、装配过程中的各种误差和回转时的受力、受热等因素,使主轴在每一瞬时回转轴心线的空间位置处于变动状态,造成轴线漂移,也就是存在着回转误差。
2.主轴回转运动误差的影响因素。
影响主轴回转精度的主要因素是主轴轴颈的误差、轴承的误差、轴承的间隙、与轴承配合零件的误差及主轴系统的径向不等刚度和热变形等。
主轴采用滑动轴承时,主轴轴颈和轴承孔的圆度误差和波度对主轴回转精度有直接影响,但对不同类型的机床其影响的因素也各不相同。
三、提高加工精度的工艺措施
(一)减少原始误差。
提高加工零件所使用机床的几何精度,提高夹具、量具及工具本身精度,控制工艺系统受力、受热变形产
生的误差,减少刀具磨损、内应力引起的变形误差,尽可能减小测量误差等均属于直接减少原始误差。
为了提高机加工精度,需对产生加工误差的各项原始误差进行分析,根据不同情况对造成加工误差的主要原始误差采取相应的解决措施。
对于精密零件的加工应尽可能提高所使用精密机床的几何精度、刚度和控制加工热变形;对具有成形表面的零件加工,则主要是如何减少成形刀具形状误差和刀具的安装误差。
(二)误差补偿法。
对工艺系统的一些原始误差,可采取误差补偿的方法以控制其对零件加工误差的影响。
1、误差补偿法:该方法是人为地造出一种新的原始误差,从而补偿或抵消原来工艺系统中固有的原始误差,达到减少加工误差,提高加工精度的目的。
2 、误差抵消法:利用原有的一种原始误差去部分或全部地抵消原有原始误差或另一种原始误差。
3、分化或均化原始误差。
为了提高一批零件的加工精度,可采取分化某些原始误差的方法。
对加工精度要求高的零件表面,还可以采取在不断试切加工过程中,逐步均化原始误差的方法。
4、转移原始误差。
该方法的实质就是将原始误差从误差敏感方向转移到误差非敏感方向上去。
转移原始误差至非敏感方向。
各种原始误差反映到零件加工误差上的程度与其是否在误差敏感方向上有直接关系。
若在加工过程中设法使其转移到加工误差的非敏感方向,则可大大提高加工精度。
转移原始误差至其他对加工精度
无影响的方面。
四、结语
总之,在机加工过程中,产生误差是不可避免的。
只有对误差产生的原因进行详细的分析,才能采取相应的预防措施以尽可能地减少加工误差,从而有效提高机加工的精度。
参考文献:
[1]郑渝.机械结构损伤检测方法研究 [d].太原理工大
学.2004年.
[2]杨春雷、尹国会.浅谈机械加工影响配合表面的原因及对策[n].中华建筑报.2005年.
[3]高原.不锈钢表面复合处理提高耐磨性的研究贴.转。