筒子纱染色重现性问题
村田自络筒使用中的常见问题及解决方法

村田自络筒使用中的常见问题及解决方法(一)N0.21C—S自动络筒机是日本村田公司的新型高速络筒机,最高速度可达2200 米/分,并且增加防飞管装置使设备的性能进一步完善。
N0.21C-S机型速度高,纱线直通道以及纱线控制环的独特设计,为纺纱技术进步提供了保障。
同时采用自动络筒机,不仅可以生产优质无结纱线,而且对节约用工,减轻工人劳动强度均有显著效果。
在使用过程中,N0.21C-S优势显而易见,但也存在一些问题,控制这些问题,是发挥自动络筒机功效,提高劳动效率,保证产品质量的基础。
捻接失误率高的原因及控制措施捻接失误率是反映捻接和上纱失误的综合参数。
捻接失误率过高时,大吸嘴重复无用功,容易出现连续打出管纱的现象。
造成捻接失误率增加的原因有以下几个方面:光电式纱线传感器积灰附花过多。
传感器始终检测到有纱存在,大吸嘴一直动作,造成系统中的捻接失误率高。
大吸嘴负压过低。
吸风道内积花积回丝多,影响风力,无法吸入纱线。
大吸嘴距管纱隔距过大,吸不到纱线,造成捻接失误。
车间内相对湿度过大,纱线的粘附力增强,紧贴在筒纱表面,大吸嘴无法捕捉到纱线断头,致使信息反馈为捻接失误。
大吸嘴纱线通道沟槽内有积花灰尘,大吸嘴锯齿条被花毛或灰尘堵塞,大吸嘴被回丝堵塞转动不灵活或不到位。
吸嘴吸纱通道被回丝阻塞,在捕纱动作时捉不到纱线。
插纱锭子位置不对,造成Bal-con跟踪式气圈控制器不下降。
捻接失误率的控制措施:通过可视查询系统,当MIS值大于10%,即可视为捻接失误率超过标准,及时观察运转状态进行整修。
每个工作日对纱线传感器进行清洁,每周对传感器装置用温水擦拭,避免传感器的误检测。
及时校正大吸嘴与筒纱的隔距,大吸嘴接近度调整为1.5mm~2.5mm为宜。
合理控制车间的相对湿度。
生产中表明,自络筒的相对湿度应低于普通络筒的控制标准。
当相对湿度大于75%时,捻接失误率明显增高。
一般应控制在70%左右。
清除大吸嘴沟槽内的积花灰尘,用汽油清洗大吸嘴锯条,清除堵塞的回丝。
涤棉筒子纱染色质量控制的研究
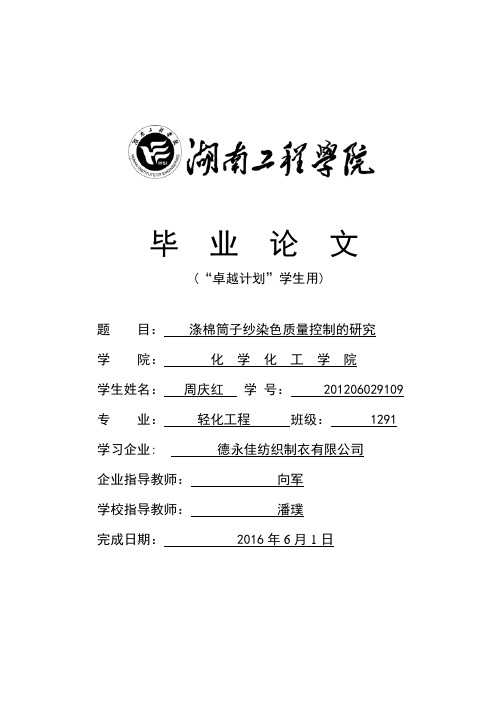
毕业论文(“卓越计划”学生用)题目:涤棉筒子纱染色质量控制的研究学院:化学化工学院学生姓名:周庆红学号: ************ 专业:轻化工程班级: 1291 学习企业: 德永佳纺织制衣有限公司企业指导教师:向军学校指导教师:潘璞完成日期: 2016年6月1日诚信声明本人声明:1、本人所呈交的毕业设计(论文)是在老师指导下进行的研究工作及取得的研究成果;2、据查证,除了文中特别加以标注和致谢的地方外,毕业设计(论文)中不包含其他人已经公开发表过的科研成果,也不包括获得其他教育机构的学位而使用过的材料;3、我承诺,本人提交的毕业设计(论文)中的所有内容均真实、可信。
作者签名:日期:年月日毕业设计(论文)任务书设计(论文)题目:涤棉筒子纱染色质量控制的研究姓名周庆红院部化学化工专业轻化工程班级 1291 学号 201206029109 学习企业名称德永佳纺织制衣有限公司企业指导教师姓名向军学校指导教师潘璞教研室主任陈镇一、基本任务及要求:1、课题内容: 1、训练学生的检索、搜集和分析文献资料的能力,培养学生创新意识、创业精神和创造能力和团队协作能力以及与人交流的沟通能力;2、结合现实可行性的原则,利用现有的实验条件,对学生进行一些必要的实验操作和科学记录的训练,培养学生的工作计划、组织能力及实验研究能力;3、了解涤棉筒子纱染色前处理、染色过程控制及后处理对染色质量的影响;4、将实验数据进行整理,采用Excel、Word等软件将所得的数据进行作图,培养学生的计算机运用能力;2、任务要求: a、完成2000字以上的文献综述一篇; 11000—13000字毕业论文一篇;并作好毕业论文开题报告和实验记录。
b、毕业论文资料含以下几个部分:毕业论文工作手册、开题报告(含开题报告、文献综述合订)、毕业论文(毕业论文及任务书合订、科学论文实验记录本、电子文档)。
具体格式与规范,详见教务处相关资料。
二、进度安排及完成时间:1. 第1—2周查阅资料、撰写文献综述、开题报告;2. 第 3 周检查、修改并提交文献综述、开题报告;3. 第 4 周论文准备;4. 第5—11 周查验资料,数据;5. 第12—13周数据整理、补充资料、撰写毕业论文初稿;6. 第14—15周修改并提交毕业论文、工作手册,原始记录;7 第16 周毕业论文答辩。
筒子纱染色如何避免染色上色不匀、白节白点、色渍色斑
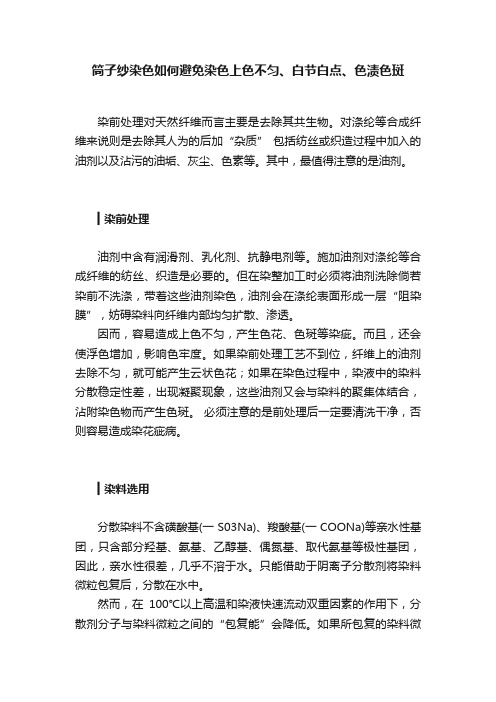
筒子纱染色如何避免染色上色不匀、白节白点、色渍色斑染前处理对天然纤维而言主要是去除其共生物。
对涤纶等合成纤维来说则是去除其人为的后加“杂质” 包括纺丝或织造过程中加入的油剂以及沾污的油垢、灰尘、色素等。
其中,最值得注意的是油剂。
▎染前处理油剂中含有润滑剂、乳化剂、抗静电剂等。
施加油剂对涤纶等合成纤维的纺丝、织造是必要的。
但在染整加工时必须将油剂洗除倘若染前不洗涤,带着这些油剂染色,油剂会在涤纶表面形成一层“阻染膜”,妨碍染料向纤维内部均匀扩散、渗透。
因而,容易造成上色不匀,产生色花、色斑等染疵。
而且,还会使浮色增加,影响色牢度。
如果染前处理工艺不到位,纤维上的油剂去除不匀,就可能产生云状色花;如果在染色过程中,染液中的染料分散稳定性差,出现凝聚现象,这些油剂又会与染料的聚集体结合,沾附染色物而产生色斑。
必须注意的是前处理后一定要清洗干净,否则容易造成染花疵病。
▎染料选用分散染料不含磺酸基(一S03Na)、羧酸基(一COONa)等亲水性基团,只含部分羟基、氨基、乙醇基、偶氮基、取代氨基等极性基团,因此,亲水性很差,几乎不溶于水。
只能借助于阴离子分散剂将染料微粒包复后,分散在水中。
然而,在100℃以上高温和染液快速流动双重因素的作用下,分散剂分子与染料微粒之间的“包复能”会降低。
如果所包复的染料微粒游离出来,就会重新聚集成更大的染料颗粒。
这种现象即为分散染料的“高温凝聚性”不同结构的分散染料,其热凝聚现象不同。
大体可分三种:一为不易发生热凝聚。
这类染料不会因升温、降温或相互碰撞而凝聚。
使用这样的染料染色一般不会造成染色不匀或色斑色渍。
二为容易发生热凝聚但随着染料分子向纤维内部扩散,染料的聚集体会再度解聚,只要染料在纤维表面吸附均匀,一般就不会造成色花、色渍。
三为容易发生热凝聚,而且在染色过程中,又难以解聚。
使用这类染料染色时,特别是当使用的分散剂或匀染剂高温分散能力较差时,就很容易由于染料的热凝聚而造成色泽不匀。
涤棉筒子染色工艺路线的改进

钢 管 染 色 , 再 加 上 涤 棉 的 热 缩 性 较 大 ( 同 的 厂 家 不 涤 纶 的 热 缩 不 同 , 一 般 在 3 ~ 7 左 右 ) 要 求 松 筒 % %
系 列措 施 :
Байду номын сангаас
( )白色涤棉纱用本色新管 1 ( )染浅色涤 棉纱 ( 度小于0 5 )时用沾污 2 浓 .% 较轻 的旧管 ,染不 同颜 色 内层有 沾污 纱现 象最终 做
松筒一前 处理 一涤染色 一棉染色一脱烘一倒筒 ( )工艺改进 以后 的路线 2
松 筒 一 染 色 前 处 理 ( 3  ̄ 缩 ) 一 脱 烘 一 二 次 10C热
淄博永嘉片碱 :
章丘 双 氧 水 :
松筒一皂煮一涤染色 一棉染色 一脱烘一倒筒 由图可看 出用钢 管 改变工 艺路 线 的方法 可 以有
用寿命 。 针 对 塑 料 管 染 涤 棉 纱 线 存 在 的 问 题 我 们 也 采 取
一
纶 ,再低温 染棉 ,需要 两 步 ,然 而 ,涤纶 在高温 下
收缩 比较严 重 ,使筒 纱密度 增大 ,给 染色 带来 很大 困难,纯棉纱线染色 时只 需要一 步恒温染色 即可。
12用钢管染色存在的 问题 .
l 涤棉 筒子染色存在 的问题
1 1涤棉纱和纯棉 纱在染 色过程 中存在 的差异 .
涤棉纱线在 染色时 ,需要先高温 ( 3 ℃ )染涤 10
13用塑料管染涤棉纱线存在的 问题 .
根据 钢管 染色 存在 的 问题 ,逐 步试验 更 换塑料 管 ,在染涤 时需要 高温 ( 3  ̄ 10C)染色 ,塑料管也会 被染 上颜 色 ,塑料 管在 高温下 容易 老化 ,缩 短 了使
筒子染色时内外色差原因及预防措施
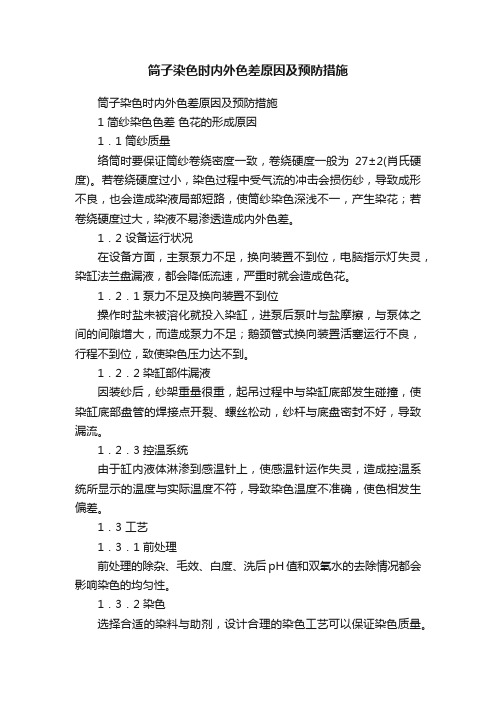
筒子染色时内外色差原因及预防措施筒子染色时内外色差原因及预防措施1 简纱染色色差色花的形成原因1.1 筒纱质量络筒时要保证筒纱卷绕密度一致,卷绕硬度一般为27±2(肖氏硬度)。
若卷绕硬度过小,染色过程中受气流的冲击会损伤纱,导致成形不良,也会造成染液局部短路,使筒纱染色深浅不一,产生染花;若卷绕硬度过大,染液不易渗透造成内外色差。
1.2 设备运行状况在设备方面,主泵泵力不足,换向装置不到位,电脑指示灯失灵,染缸法兰盘漏液,都会降低流速,严重时就会造成色花。
1.2.1 泵力不足及换向装置不到位操作时盐未被溶化就投入染缸,进泵后泵叶与盐摩擦,与泵体之间的间隙增大,而造成泵力不足;鹅颈管式换向装置活塞运行不良,行程不到位,致使染色压力达不到。
1.2.2 染缸部件漏液因装纱后,纱架重量很重,起吊过程中与染缸底部发生碰撞,使染缸底部盘管的焊接点开裂、螺丝松动,纱杆与底盘密封不好,导致漏流。
1.2.3 控温系统由于缸内液体淋渗到感温针上,使感温针运作失灵,造成控温系统所显示的温度与实际温度不符,导致染色温度不准确,使色相发生偏差。
1.3 工艺1.3.1 前处理前处理的除杂、毛效、白度、洗后pH值和双氧水的去除情况都会影响染色的均匀性。
1.3.2 染色选择合适的染料与助剂,设计合理的染色工艺可以保证染色质量。
工艺设计不好,选择三原色的配伍性差,也会造成色花。
2 防止色差色花的措施2.1 筒纱质量筒纱成形要严格把关,杜绝哑铃纱、喇叭纱、重叠纱、漏眼纱及硬边纱,卷绕密度要控制在要求范围之内,过硬过松的`要挑出,筒纱大小一致。
2.2 设备维修为保证设备正常运行,对上述所存在的问题要定期检查,这样才能保证设备运转良好和染色质量稳定。
定期对水、汽阀门进行检查,看有无开启不灵活和关闭不严现象,加强设备维护。
2.3 前处理工艺选择前处理工艺要煮透、煮匀,以便于染色。
为缩短时间,采用煮练漂白同浴法。
工艺处方(g/L)3O%氢氧化钠 4精练剂 2渗透剂 2双氧水 6稳定剂 3前处理工艺曲线(见图1)。
干货腈纶筒子纱染色,如何减小大小样色差?
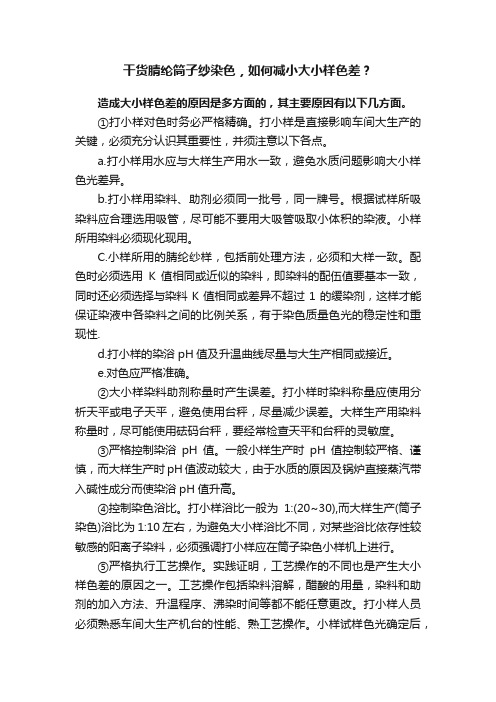
干货腈纶筒子纱染色,如何减小大小样色差?造成大小样色差的原因是多方面的,其主要原因有以下几方面。
①打小样对色时务必严格精确。
打小样是直接影响车间大生产的关键,必须充分认识其重要性,并须注意以下各点。
a.打小样用水应与大样生产用水一致,避免水质问题影响大小样色光差异。
b.打小样用染料、助剂必须同一批号,同一牌号。
根据试样所吸染料应合理选用吸管,尽可能不要用大吸管吸取小体积的染液。
小样所用染料必须现化现用。
C.小样所用的腈纶纱样,包括前处理方法,必须和大样一致。
配色时必须选用K值相同或近似的染料,即染料的配伍值要基本一致,同时还必须选择与染料K值相同或差异不超过1的缓染剂,这样才能保证染液中各染料之间的比例关系,有于染色质量色光的稳定性和重现性.d.打小样的染浴pH值及升温曲线尽量与大生产相同或接近。
e.对色应严格准确。
②大小样染料助剂称量时产生误差。
打小样时染料称量应使用分析天平或电子天平,避免使用台秤,尽量减少误差。
大样生产用染料称量时,尽可能使用砝码台秤,要经常检查天平和台秤的灵敏度。
③严格控制染浴pH值。
一般小样生产时pH值控制较严格、谨慎,而大样生产时pH值波动较大,由于水质的原因及锅炉直接蒸汽带入碱性成分而使染浴pH值升高。
④控制染色浴比。
打小样浴比一般为1:(20~30),而大样生产(筒子染色)浴比为1:10左右,为避免大小样浴比不同,对某些浴比依存性较敏感的阳离子染料,必须强调打小样应在筒子染色小样机上进行。
⑤严格执行工艺操作。
实践证明,工艺操作的不同也是产生大小样色差的原因之一。
工艺操作包括染料溶解,醋酸的用量,染料和助剂的加入方法、升温程序、沸染时间等都不能任意更改。
打小样人员必须熟悉车间大生产机台的性能、熟工艺操作。
小样试样色光确定后,打小样人员要深入车间做先锋试验,确保小样与大样生产的一致性.。
纯亚麻染色常见问题
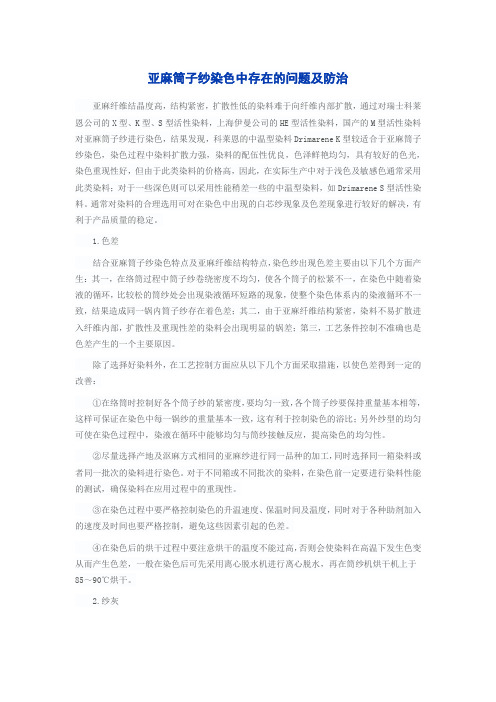
亚麻筒子纱染色中存在的问题及防治亚麻纤维结晶度高,结构紧密,扩散性低的染料难于向纤维内部扩散,通过对瑞士科莱恩公司的X型、K型、S型活性染料,上海伊曼公司的HE型活性染料,国产的M型活性染料对亚麻筒子纱进行染色,结果发现,科莱恩的中温型染料Drimarene K型较适合于亚麻筒子纱染色,染色过程中染料扩散力强,染料的配伍性优良,色泽鲜艳均匀,具有较好的色光,染色重现性好,但由于此类染料的价格高,因此,在实际生产中对于浅色及敏感色通常采用此类染料;对于一些深色则可以采用性能稍差一些的中温型染料,如Drimarene S型活性染料。
通常对染料的合理选用可对在染色中出现的白芯纱现象及色差现象进行较好的解决,有利于产品质量的稳定。
1.色差结合亚麻筒子纱染色特点及亚麻纤维结构特点,染色纱出现色差主要由以下几个方面产生:其一,在络筒过程中筒子纱卷绕密度不均匀,使各个筒子的松紧不一,在染色中随着染液的循环,比较松的筒纱处会出现染液循环短路的现象,使整个染色体系内的染液循环不一致,结果造成同一锅内筒子纱存在着色差;其二,由于亚麻纤维结构紧密,染料不易扩散进入纤维内部,扩散性及重现性差的染料会出现明显的锅差;第三,工艺条件控制不准确也是色差产生的一个主要原因。
除了选择好染料外,在工艺控制方面应从以下几个方面采取措施,以使色差得到一定的改善:①在络筒时控制好各个筒子纱的紧密度,要均匀一致,各个筒子纱要保持重量基本相等,这样可保证在染色中每一锅纱的重量基本一致,这有利于控制染色的浴比;另外纱型的均匀可使在染色过程中,染液在循环中能够均匀与筒纱接触反应,提高染色的均匀性。
②尽量选择产地及沤麻方式相同的亚麻纱进行同一品种的加工,同时选择同一箱染料或者同一批次的染料进行染色。
对于不同箱或不同批次的染料,在染色前一定要进行染料性能的测试,确保染料在应用过程中的重现性。
③在染色过程中要严格控制染色的升温速度、保温时间及温度,同时对于各种助剂加入的速度及时间也要严格控制,避免这些因素引起的色差。
涤纶筒子染色常见问题分析
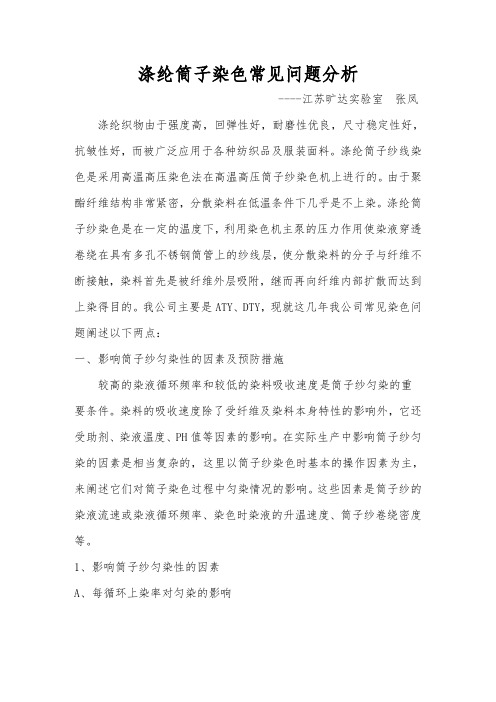
涤纶筒子染色常见问题分析----江苏旷达实验室张凤涤纶织物由于强度高,回弹性好,耐磨性优良,尺寸稳定性好,抗皱性好,而被广泛应用于各种纺织品及服装面料。
涤纶筒子纱线染色是采用高温高压染色法在高温高压筒子纱染色机上进行的。
由于聚酯纤维结构非常紧密,分散染料在低温条件下几乎是不上染。
涤纶筒子纱染色是在一定的温度下,利用染色机主泵的压力作用使染液穿透卷绕在具有多孔不锈钢筒管上的纱线层,使分散染料的分子与纤维不断接触,染料首先是被纤维外层吸附,继而再向纤维内部扩散而达到上染得目的。
我公司主要是ATY、DTY,现就这几年我公司常见染色问题阐述以下两点:一、影响筒子纱匀染性的因素及预防措施较高的染液循环频率和较低的染料吸收速度是筒子纱匀染的重要条件。
染料的吸收速度除了受纤维及染料本身特性的影响外,它还受助剂、染液温度、PH值等因素的影响。
在实际生产中影响筒子纱匀染的因素是相当复杂的,这里以筒子纱染色时基本的操作因素为主,来阐述它们对筒子染色过程中匀染情况的影响。
这些因素是筒子纱的染液流速或染液循环频率、染色时染液的升温速度、筒子纱卷绕密度等。
1、影响筒子纱匀染性的因素A、每循环上染率对匀染的影响由于纤维对染料的吸收作用,染液内染料浓度在染液流向方向上逐渐减少,引起染液流向下方纤维时染料的吸收量下降,即染料的吸尽作用。
反映染料吸尽作用最直接的指标是染液每循环一次纤维吸收染料的百分率,即每循环上染率。
每循环上染率越大,吸尽作用越强烈,所得的筒子纱匀染性越差。
B、流速对匀染程度的影响经过筒子纱的染液流速或筒子纱染色时染液的循环频率,是决定筒子纱染色质量的重要参数。
同一纤维品种用同样的染化料在相同条件下染色时,染料的最终平衡上染率是不变的,而达到匀染所需要的时间随染液流速的增加而减小。
也就是说,在相同的染色时间内,流速越高,筒子纱的匀染程度就越好;流速越低,筒子纱的匀染程度就越差;但流速过大易出现毛羽等疵病,因此,控制好流速也是非常重要的,一般是要控制在25~30 L·(min.kg)。
- 1、下载文档前请自行甄别文档内容的完整性,平台不提供额外的编辑、内容补充、找答案等附加服务。
- 2、"仅部分预览"的文档,不可在线预览部分如存在完整性等问题,可反馈申请退款(可完整预览的文档不适用该条件!)。
- 3、如文档侵犯您的权益,请联系客服反馈,我们会尽快为您处理(人工客服工作时间:9:00-18:30)。
纱线染色的重现性问题在相同的工艺处方、工艺染化料等条件下,结果却是不同批次之间总有色差。
而纺织企业,尤其是染纱工厂,其竞争力就在于即时生产与一次成功,且两者密不可分。
即时生产能迅速反应市场,在最短的时间内生产出产品,一次成功是指产品应符合质量要求。
产品质量一般包括两方面:内在质量与外观质量主要要求重现性。
染色纱线色光重现性差,其实质就是不同批次染色时所上染的染料重现性差。
为实现纱线染色的重现性,必须对染色过程中所有因素进行控制。
一般重现性差(即缸差)是指间歇式染色时,相同的被染物(纱线)用相同的染化料、处方、工艺进行染色,但不同染批被染物之间存在色差(色光不一、深浅不一或两者兼有之)的现象。
经常出现重现性差的场合一般为:小样之间,小样与中样之间,中样与大样之间,小样与大样之间;不同染机之间,或两只染机容量不同,或容量相同但制造厂家不同,甚至制造厂容量完全相同的染机之间;同一染机不同染批之间。
1 染色重现性差的原因产生色光重现性差的原因有很多,纱线筒子染色中出现色差的原因大致有:纱线、染化料、工艺设计及控制、操作、仪器设备、水质等,总的说来是分为外在的客观因素和人为的主观因素。
1.1客观因素1.1.1 纱线棉纤维在其生长过程中的某种差异,会产生纤维品质的差异,故不同生产厂家生产的纱线的品质是不一样的,导致纱线吸收染料的性能也不一样,染色后的重现性就会有差异。
另外,棉纤维的粗细(线密度)不同,染色后表观深度也有差异。
如棉纱线7S与40S经染色后,7S的表观就显深,粗者深,细者浅。
纱线的捻度、配棉、回潮率等也会影响色光的重现性。
即使是同组分、同规格纤维,由于生产工艺的波动,也会造成染色性能差异,至于用回收废料重新纺纱的纤维,染色性能与常规纤维也不同。
对染纱来说,当纤维批次变化,应进行小样试验,必要时进行处方调整,才能正式投产。
(若是两种或两种以上纤维的混纺纱,若混纺比有波动,染色处方两相不一,分批染色也会出现缸差)。
1.1.2 染化料染料生产大多是有机合成反应,流程长、反应复杂,生产中任一工艺参数的波动都会使生成物组分及品质发生偏离。
相同结构的染料,由于技术、设备、管理、操作、控制水平的不同,染料质量也不同;同一企业不同批次的同种染料同样存在着重现性问题,也会造成上染性能和被染物色光及深浅的差异。
还有,不同染料度染色各工艺条件的敏感性(依存性)是不同的,染料越敏感(依存性越大),重现性就越差。
另外,染料厂所提供染料的拼混处方的不同,对染色性能及深浅同样会产生很大的影响,同时染料的拼混也存在着重现性及拼混均匀性问题。
还有一点,染料也有其储存周期,有的染料(如活性、可溶性还原染料)储存时间或条件不当,很容易变质,大部分染料会吸湿潮解,从而直接影响染料的力分。
有时同种染料上、中、下层会发生色光和力分上的差异(色光差异经常发生在拼混染料上),可能是由于在运输过程中不同颗粒及比重的染料、助剂出现分层,当然也不排除个别中间商的拼混质量问题。
1.1.3 仪器设备(1)染色筒管、经轴盘管与衡器不同形式的筒管,其密封情况不同,因而有效流量率也不同,即使主泵吐出流量一致,其间差异也可达10%~40%,染液泄露程度不同,以致实际在纱线中循环的染液量不同,致使纱线上携带的染料量不同,因而造成深浅重现差的现象。
不同形式和不同设计的筒管穿透率差异变化,也会使流量变化,随之循环频率和次数也变化,长丝染色缸差。
不同染机其底碟、顶碟、顶锁密封不一,泄漏不一,所以有效流量不同,缸差也无法控制。
称取染料的衡器也要有严格的使用选择,不同称量范围应使用不同精度的衡器,切忌用大秤称小量。
一般称量容差范围如下表:称量容差范围表因而,染料称取时配备不同量程及相关感量的衡器是十分必要的,衡器的准确性也应定时标定检验。
(2)染色设备染色机对染色的重现性影响很大,染色工作者往往对染料、温度、时间等因素比较重视,但对染色机本身的问题不够重视,以致出现了缸差也找不到原因。
染机对棉纱线重现性的影响主要是,染液的循环次数和染浴温度的稳定性。
纱线筒子染色时,纱线被密实地卷绕成筒子,固定在染柱上。
染液在纱线(纤维)之间强制循环(即外扩散),将染液中的染料扩散到纱线各处。
染液在筒子中的由内向外(或由外向内)的循环决定了染料与纤维之间的接触、碰撞,即染液循环次数与染料上染及表观深度的密切关系。
染液在筒子纱中循环100次与循环80次的两次染色,色光肯定有差异。
不少染厂新机到厂后,或温度指示器新装时,并未对其进行严格的标定,日常使用中也不定期标定,当指示不正确时,温度表面一致,其实并不一致,从而影响染料的上染速度及平衡上染百分率,产生缸差,所以温度的指示一定要正确,温度的控制一定要准确。
1.1.4 对样光源物体的颜色与物体对光的反射、照射光源的光谱组成有关,不同光源照射在同一物体上时,表现出的颜色经常不同,如果在订货、小样、大生产,调色时用的光源不一,由于目标不同,结果肯定不同。
为此,染厂对色光应有约定的同一光源。
1.1.5 水质筒子纱染色(包括前处理)对水质要求很高,应该使用软水。
有的企业受条件限制,使用仅经过滤沉淀的地面水,其水质受自然状况的变化波动很大,造成半制品白度及染色色光的差异,因而企业应创造条件使用软水。
1.2 主观原因1.2.1 络筒质量我厂筒子纱染色是采用浸染法染色,表观色泽深浅很大程度上决定于染料与被染物的重量比。
一般筒染装纱时只计筒子的只数,不再另行称重,所以络筒重量决定装纱重量,因而络筒必须对所有松筒100%称重。
还有由于筒管和经轴盘管上布满孔眼,以供染液穿行,当筒子卷绕位置不当,或往复距离不够,会造成“露眼”,染液会从“露眼”时“短路”,不仅使筒子端面冲毛,也会影响其它筒子的流量。
再者,松筒的密度与染液循环时的阻力有着直接的关系,密度大、阻力大,以致影响染液的循环流量发生变化,随之染液循环频率及在规定时间内的循环次数等一系列参数都发生变化,从而造成被染物色泽深浅不一。
1.2.2前处理前处理的除杂程度、毛效高低、白度、洗后PH值、漂后双氧水去净情况等因素都会影响染料上染率和色光。
一般染厂对染料力分的测定和称量比较重视,但忽视对其它化学品的测定及计量,对所用的烧碱、纯碱、双氧水浓度不进行分析,只按说明书标示的计算,染液也很少进行滴定,因而前处理效果就会不一造成染色物色泽深浅和色相的差异。
1.2.3 染料的选用棉纱线的染料选用一般有:活性染料、还原染料、直接染料等。
但在我厂,棉纱线的染色一般是以活性染料为主,涤棉混纺纱是分散染料、活性染料,所以选用时要注意它们的相容性、敏感性及质量稳定性,才能保证重现性。
1.2.4染色工艺的合理性尽管选用了合适的染料,但染色工艺设计不合理,同样会出现缸差。
如温度设计、升温速率、保温速率、保温时间、助剂用量及加入方式的科学性和后处理工艺设计的合理性等,都会影响染料上染量的差异,从而造成色差。
如活性染料的固色及水解与染浴的PH值有很大关系,科学的加料方式是维持PH值在一个固定值(如PH值为11.5),这与加料方式与加料速率有很大关系,如果一次性加入,或忽快忽慢,则造成PH值波动不一,使固色和水解染料不一,从而出现色光深浅不一(而在本厂,操作工大多是此错误的操作)。
1.2.5 操作因素操作工的操作没有按照工艺要求,有些甚至是错误的操作,但操作者和管理者都没有意识到。
如打样工观察移液管的刻度时,移液管处于45°左右(应垂直);染色工不是专人负责染同一色泽,多人操作;称料工用同一只勺子取不同的染料,期间只用干抹布擦一擦;各只处方的染料都放在同一容器中,称后再倒入桶中。
还有,操作工操作不认真。
如装筒时筒子间密封不良不去纠正;络筒重量超标不进行处理;化料时料桶未认真清洗;助剂不进行正确称量以及由于管理人员未制定正确严格的操作方法,操作工自行其是,更何况,在手动或半自动的设备上,也常会发生工艺变更,工艺的不重现,会造成染色重现性差。
1.2.6管理问题染色重现性,不仅涉及染色工序,而且涉及生产全过程,是一个系统工程,其中与管理也有密切关系,如坯纱和半制品管理、染料管理、计量管理、技术管理和化验室管理:同一色号应使用同一批坯纱,若要更换就得重新复样,应做到“先练先用”、“后练后用”、“同色同批”;不同生产厂制造的染料,即使同厂不同批次的染料也会出现重现性问题等等这些由于在管理上的不注重,也易使筒子纱线的染色出现批次间生产的重现性差。
1.2.7实验室对大生产的跟踪首先实验室对生产的支持方式,不是将工艺及处方传递到大生产,而是在实验室模拟大生产,做到大生产——实验室的高度重现性。
当大生产出现色相不符要修色时,实验室应共同参加完成,实验室对大生产提供的信息(大小样色光差异),应进行分析及试验,找出各只染料大小样生产之间的相关关系,以减少修色。
另外,要做到大生产——实验室的高度重视,首先要做到实验室与实验室的重现性,以及大生产与大生产的重现性,否则大生产与实验室的重现性就差。
2 解决措施纱线染色的重现性差,在纱线的生产中经常遇到,根据我厂纱线的染色情况及我对生产操作的部分了解,觉得应在以下方面加强管理,尽量从基本保证纱线染色的重现:(1)设备的选用应选用能保证产品染色质量和缩短染色时间功能,采用自落顶锁装置,利用设备的内流进行筒纱的自然压缩的设备,以在设备上提供重现性的基本条件;(2)络筒质量为保证染透,筒纱的密度一般控制在0.35~0.40之间,压缩后的密度应控制在0.41~0.46之间;(3)染化料慎重选用染料的品种,注重染料批次间的检验,保证染料室清洁通风干燥,做好染料的防潮;(4)工艺参数工艺参数的制定与控制是染色的关键,一个好的染色工艺必须有一组科学、合理的参数来支撑。
如盐、碱用量,我们应注重加料的方式和加料的时间,可利用提前化好的盐,减少因盐未充分溶解造成染料聚集和沉淀,使染色出现重现性差现象;(5)打样与放样化验室的小样应尽最大程度仿照大生产的实际情况,包括循环时间、升温速率、盐和碱的加入、染色后处理、对色光源等;所以大样生产前必须做中样实验,化验室技术人员做好跟踪记录,作为大生产时的参考资料;大样投产时,工艺员要根据小样与大样的差异及以往的经验和对染料性能的掌握,对工艺进行适度调整,得出大样投产的工艺;小样与投产的用纱要一致,前处理工艺、后处理工艺要一致,换纱线要复样,打小样的染料母液存放时间不宜过长,以免染料浓度、力分变化;(6)操作因素打小样人员操作要规范,科学使用染料,另加大操作工的培训,减少助剂的使用种类,使用精确的计量器具;(7)其他因素小样用水应与大生产一致,尽量使用软水,软水的PH值应控制在7.0左右,以保证染色是PH值的稳定性,;加强助剂的质量检测;不同批次间的原棉和配棉使用,化验室要在染前复样,若色光有变化,要及时调整;前处理是染色的基础,前处理不好,基础打不牢,染色一样会出现重现性差,应注重纱线的前处理。