锻造工艺基础知识
《锻造技术培训》课件
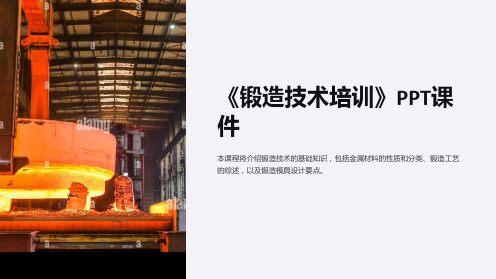
本课程将介绍锻造技术的基础知识,包括金属材料的性质和分类、锻造工艺 的综述,以及锻造模具设计要点。
金属材料的性质和分类
材料的分类
了解常见金属材料的分类和特性,包括钢、铝合金、铜合金等。
机械性能
讨论金属材料的强度、硬度、韧性等机械性能的重要性。
耐腐蚀性
了解各种金属材料的耐腐蚀性能及其应用领域。
故障排除
指导如何准确诊断和解决锻造过 程中的常见故障和问题。
锻造质量检验方法
目视检查
讲解如何通过目视检查来评估 锻造件的外观和质量。
非破坏性检测
介绍各种非破坏性检测方法, 如超声波检测和磁粉检测等。
力学性能测试
讨论锻造件力学性能测试的方 法和标准。
航天领域中锻造技术的应用案例,如发动机零部件和机身结构。
锻造工艺综述
1
锻造工艺类别
介绍常见的热锻、冷锻和半热锻等不同
步骤与工艺参数
2
类型的锻造工艺。
深入了解锻造过程中的步骤和关键工艺
参数,如温度、压力等。
3
设备与工具
讲解各种锻造工艺所需的设备、工具及 其作用。
锻造模具设计要点
1 模具结构设计
探讨锻造模具的结构设计原则和关键要点,以提高锻造效率和成品质量。
2 材料与制造工艺
介绍选择合适模具材料及制造工艺的重要性,并分享一些最佳实践。
3 模具维护与保养
指导如何合理维护和保养锻造模具,延长使用寿命和提高生产效率。
锻造常见问题及解决方案
缺陷分析
探讨常见的锻造缺陷,如气孔、 夹渣等,以及有效的解决方案。
工艺优化
分享提高锻造效率和成品质量的 工艺优化技巧和策略。
锻造实用速查手册

锻造实用速查手册
锻造实用速查手册通常包含了锻造工艺、材料选择、设备使用、安全规范等方面的关键信息,方便从事锻造工作的从业者快速查阅。
以下是可能包含在锻造实用速查手册中的一些内容:
锻造基础知识:
锻造的定义、原理和分类。
锻造与其他加工方式的对比。
锻造工艺:
锻造的工艺流程图。
不同类型锻造工艺的特点和适用范围。
材料选择:
常见锻造材料的特性和适用场景。
材料的热处理和硬度等相关信息。
锻造设备:
锻造锤、锻压机等设备的结构和工作原理。
设备的操作方法和注意事项。
工艺参数:
锻造工艺中常用的参数,如温度、压力、冲程等。
参数的调整对成品质量的影响。
模具设计:
锻造模具的设计原则和要点。
模具的制造和维护。
安全规范:
锻造现场的安全操作规范。
使用个人防护设备的要求。
常见问题和解决方法:
锻造过程中可能遇到的常见问题。
针对问题的解决方法和预防措施。
质量控制:
锻造产品的质量标准和检测方法。
如何进行质量控制和质量管理。
实用计算表格:
包括温度计算、力学参数计算等相关表格。
有助于快速进行工艺计算。
锻造工艺图谱:
锻造工艺的图谱,便于快速了解工艺流程。
案例分析:
锻造成功案例的分析和总结,包括成功经验和教训。
这些内容可以根据具体的锻造工艺、行业特点和用户需求进行调整和扩展。
速查手册的目的是为了提供方便快捷的信息查询和应对工作中常见问题的指导。
锻造锻件基础知识

锻造锻件基础知识1. 锻造锻件基础知识2. 锻件与铸件相比有什么特点3. 锻件和铸件有什么区别4. 锻件、铸件、不锈钢的区别5. 为什么大型锻件必须要用自由锻6. 不锈钢锻件的固溶热处理工艺7. 锻件锻造基本工序8. 自由锻件设备有那些9 .自由锻件基本工序10.飞机锻件11.兵器锻件12.核电及火电锻件1.锻造锻件基础知识锻造对金属坯料(不含板材)施加外力,使其产生塑性变形、改变尺寸、形状及改善性能,用以制造机械零件、工件、工具或毛坯的成形加工方法。
锻造的种类和特点当温度超过300-400℃(钢的蓝脆区),达到700-800℃时,变形阻力将急剧减小,变形能也得到很大改善。
根据在不同的温度区域进行的锻造,针对锻件质量和锻造工艺要求的不同,可分为冷锻、温锻、热锻三个成型温度区域。
原本这种温度区域的划分并无严格的界限,一般地讲,在有再结晶的温度区域的锻造叫热锻,不加热在室温下的锻造叫冷锻。
在低温锻造时,锻件的尺寸变化很小。
在700℃以下锻造,氧化皮形成少,而且表面无脱碳现象。
因此,只要变形能在成形能范围内,冷锻容易得到很好的尺寸精度和表面光洁度。
只要控制好温度和润滑冷却,700℃以下的温锻也可以获得很好的精度。
热锻时,由于变形能和变形阻力都很小,可以锻造形状复杂的大锻件。
要得到高尺寸精度的锻件,可在900-1000℃温度域内用热锻加工。
另外,要注意改善热锻的工作环境。
锻模寿命(热锻2-5千个,温锻1-2万个,冷锻2-5万个)与其它温度域的锻造相比是较短的,但它的自由度大,成本低。
坯料在冷锻时要产生变形和加工硬化,使锻模承受高的荷载,因此,需要使用高强度的锻模和采用防止磨损和粘结的硬质润滑膜处理方法。
另外,为防止坯料裂纹,需要时进行中间退火以保证需要的变形能力。
为保持良好的润滑状态,可对坯料进行磷化处理。
在用棒料和盘条进行连续加工时,目前对断面还不能作润滑处理,正在研究使用磷化润滑方法的可能。
2. 锻件与铸件相比有什么特点金属经过锻造加工后能改善其组织结构和力学性能。
锻造基础知识讲座

锻造基础知识讲座(一)锻造的基本概念。
锻造是锻压工艺的一部分,锻压包括锻造和冲压两部分。
锻造的根本目的:是获得所需形状和尺寸,同时要求其性能和组织符合一定的技术要求的毛坯。
锻造按温度来分有:热锻、温锻和冷锻。
不同的锻造温度对锻件的组织和性能的影响也是不同的。
下面介绍的内容主要是热锻部分知识。
锻造分自由锻和模锻两部分。
自由锻是自由锻造的简称,自由锻包括胎模锻,适用于单件小批生产。
模锻适用于批量生产和大批量生产,如汽车制造行业。
自由锻和模锻是锻造工艺的主要支柱。
发达国家的模锻件占锻件总重量的70%以上;我国在50年代模锻件占锻件总重量不到20%,现在有进步,但模锻件总重乃比自由锻件少。
自由锻又分手工锻和机器锻。
手工锻在现在工厂用得很少,只在工具修理部门有,农村的铁匠炉基本上还是用手工锻。
机器锻又分锤上自由锻和水压机上自由锻,前者用来生产大、中、小锻件;后者用来生产大型和特大型锻件。
自由锻特点:1.所用工具简单,通用性强,灵活性大。
2.靠工人的手工操作来控制锻件的形状和尺寸,因此,锻件的精度差,工人的劳动强度大,生产率低。
锻件的主要缺陷有:1.裂纹:有横向、纵向裂纹及其它各种裂纹。
2.过烧。
3.白点(锻件内部银白色、灰白色圆形的裂纹)4.折叠。
5.疏松、非金属夹杂物。
6.机械性能达不到要求(锻比不够)。
7.弯曲、变形。
产生以上缺陷的原因很多,有铸锭缺陷引起的,有锻造加热不当引起的,有锻造本身的原因,也有锻后冷却和热处理不当引起的。
总之,原因很多。
所以当锻件的缺陷发现后,需要综合起来进行分析,并要掌握在不同情况下产生缺陷的不同特征,以便具体问题进行具体分析。
(二)锻造设备简介。
1.自由锻设备:有锻锤和水压机两类。
(1)锻锤有:简易锻锤---夹板(杆)锤:最大吨位1~2吨。
弹簧锤:最大吨位100公斤左右。
钢丝锤:最大吨位3吨。
如我厂的3 吨落锤。
空气锤:规格有:40、65、75、150、250、400、560、750、1000公斤等。
锻造基础知识
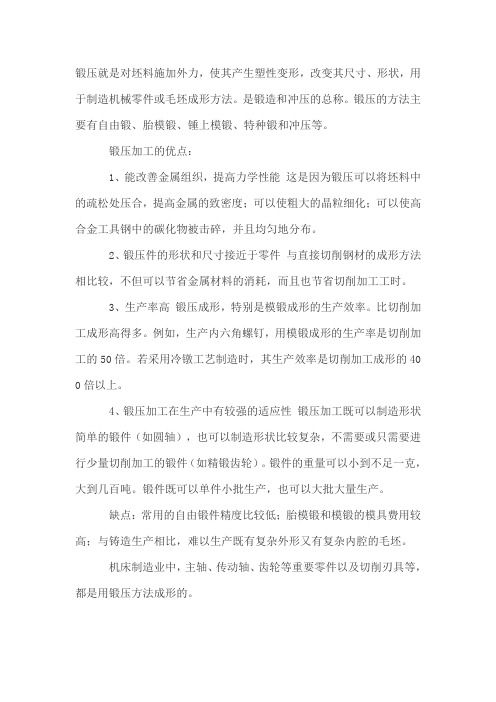
锻压就是对坯料施加外力,使其产生塑性变形,改变其尺寸、形状,用于制造机械零件或毛坯成形方法。
是锻造和冲压的总称。
锻压的方法主要有自由锻、胎模锻、锤上模锻、特种锻和冲压等。
锻压加工的优点:1、能改善金属组织,提高力学性能这是因为锻压可以将坯料中的疏松处压合,提高金属的致密度;可以使粗大的晶粒细化;可以使高合金工具钢中的碳化物被击碎,并且均匀地分布。
2、锻压件的形状和尺寸接近于零件与直接切削钢材的成形方法相比较,不但可以节省金属材料的消耗,而且也节省切削加工工时。
3、生产率高锻压成形,特别是模锻成形的生产效率。
比切削加工成形高得多。
例如,生产内六角螺钉,用模锻成形的生产率是切削加工的50倍。
若采用冷镦工艺制造时,其生产效率是切削加工成形的400倍以上。
4、锻压加工在生产中有较强的适应性锻压加工既可以制造形状简单的锻件(如圆轴),也可以制造形状比较复杂,不需要或只需要进行少量切削加工的锻件(如精锻齿轮)。
锻件的重量可以小到不足一克,大到几百吨。
锻件既可以单件小批生产,也可以大批大量生产。
缺点:常用的自由锻件精度比较低;胎模锻和模锻的模具费用较高;与铸造生产相比,难以生产既有复杂外形又有复杂内腔的毛坯。
机床制造业中,主轴、传动轴、齿轮等重要零件以及切削刃具等,都是用锻压方法成形的。
锻造工艺基础手工锻造是用手锻工具,依靠人力在铁砧上进行的。
这种方法简陋,仅用于修理性质和小批量生产的场合。
机器锻造是靠各种锻造设备提供作用力的锻造方法,是现代锻造的主要形式。
一、自由锻只用简单的通用性工具,或在锻造设备上、下砧间直接使坯料变形而获得所需的几何形状及内部质量的锻件,称为自由锻。
1、基本工序可分为拔长、镦粗、冲孔、弯曲等。
拔长:也称为延伸,它是使坯料横断面积减小、长度增加的锻造工序。
镦粗:是使毛坯高度减小,横断面积增大的锻造工序。
冲孔:是利用冲头在镦粗后的坯料上冲出透也或不透孔的锻造方法。
弯曲:采用一定的工模具将毛坯弯成所规定的外形的锻造工序。
锻造工艺要求

锻造工艺要求
锻造是一种金属加工工艺,通过对金属坯料进行加热、锤击或压力加工,使其形成所需的形状和尺寸。
锻造工艺要求包括以下几个方面:
1. 材料要求:锻造工艺需要使用适合的金属材料,通常包括低碳钢、合金钢、铝合金等。
这些材料具有较好的可锻性和可塑性,能够在锻造过程中形成所需的形状和尺寸。
2. 坯料要求:锻造工艺需要准备适当的坯料,通常采用圆钢、板材、棒材等。
坯料的尺寸和形状需要符合锻造工艺的要求,以便在锻造过程中形成所需的形状和尺寸。
3. 加热要求:锻造工艺需要将坯料加热到适当的温度,以便使其具有良好的可塑性。
加热温度的选择需要考虑材料的性质和锻造工艺的要求,通常需要在金属材料的相变温度范围内进行加热。
4. 锻造要求:锻造工艺需要使用适当的锻造设备和工具,如锻造机、锤击机等。
锻造工艺需要按照规定的锻造程序进行操作,以确保锻造出的零件具有所需的形状、尺寸和力学性能。
5. 后处理要求:锻造工艺需要进行后处理,如去毛刺、切割、热处理等,以确保锻造出的零件符合要求。
后处理的方法和工艺需要根据具体的锻造零件的要求进行选择和调
整。
总之,锻造工艺需要综合考虑材料、坯料、加热、锻造和后处理等多个方面的要求,以确保锻造出的零件具有所需的形状、尺寸和力学性能。
锻造基础知识大汇集

锻造基础知识大汇集 Document number:WTWYT-WYWY-BTGTT-YTTYU-2018GTforming1950专注锻造、冲压、钣金成形行业,汇聚作者与读者、用户与装配商、行业与市场最新动态,通过行业市场类、技术交互类、技术文章类题材为锻压行业打造一流的交流学习、技术传播、信息服务平台。
锻造工艺(Forging Process)是一种利用锻压机械对金属坯料施加压力,使其产生塑性变形以获得具有一定机械性能、一定形状和尺寸锻件的加工方法,锻压(锻造与冲压)的两大组成部分之一。
变形温度钢的开始再结晶温度约为727℃,但普遍采用800℃作为划分线,高于800℃的是热锻;在300~800℃之间称为温锻或半热锻。
坯料根据坯料的移动方式,锻造可分为自由锻、镦粗、挤压、模锻、闭式模锻、闭式镦锻。
1、自由锻。
利用冲击力或压力使金属在上下两个抵铁(砧块)间产生变形以获得所需锻件,主要有手工锻造和机械锻造两种。
2、模锻。
模锻又分为开式模锻和闭式模锻.金属坯料在具有一定形状的锻模膛内受压变形而获得锻件,又可分为冷镦、辊锻、径向锻造和挤压等等。
3、闭式模锻和闭式镦锻由于没有飞边,材料的利用率就高。
用一道工序或几道工序就可能完成复杂锻件的精加工。
由于没有飞边,锻件的受力面积就减少,所需要的荷载也减少。
但是,应注意不能使坯料完全受到限制,为此要严格控制坯料的体积,控制锻模的相对位置和对锻件进行测量,努力减少锻模的磨损。
锻模根据锻模的运动方式,锻造又可分为摆辗、摆旋锻、辊锻、楔横轧、辗环和斜轧等方式。
摆辗、摆旋锻和辗环也可用精锻加工。
为了提高材料的利用率,辊锻和横轧可用作细长材料的前道工序加工。
与自由锻一样的旋转锻造也是局部成形的,它的优点是与锻件尺寸相比,锻造力较小情况下也可实现形成。
包括自由锻在内的这种锻造方式,加工时材料从模具面附近向自由表面扩展,因此,很难保证精度,所以,将锻模的运动方向和旋锻工序用计算机控制,就可用较低的锻造力获得形状复杂、精度高的产品,例如生产品种多、尺寸大的汽轮机叶片等锻件。
锻造基础知识介绍

锻造基础知识介绍锻造是一门古老而重要的金属加工工艺,旨在通过改变金属材料的形状和性能,使其达到所需的工程要求。
在锻造过程中,金属材料被加热到一定温度,然后通过施加力量使其产生塑性变形,最终得到所需的形状。
锻造基础知识包括锻造工艺、锻件设计、锻造设备等方面,下面将对其进行介绍。
首先,锻造工艺是进行锻造操作的方式和方法。
常见的锻造工艺包括自由锻造、模锻、轧锻和冷锻等。
自由锻造是最基本的锻造工艺,也是最早发展的一种方法。
它通过锤击或压力将金属材料塑性变形成所需的形状。
模锻是在模具的作用下进行的锻造工艺,常用于大批量生产复杂形状的锻件。
轧锻是通过辊压将金属材料塑性变形成所需的形状,常用于生产长条状或较薄的锻件。
冷锻是在较低的温度下进行的锻造工艺,用于锻造高强度和高硬度的材料。
其次,锻件设计是在锻造过程中对待加工金属材料的形状和尺寸进行设计。
在锻件设计中,需要考虑到锻造过程中的塑性变形和金属流动的规律。
一般来说,锻件的截面积应该保持均匀,形状应该尽量简单,避免尖锐的转角和悬点,以提高铁水的填充率和金属流动的均匀性。
同时,锻件的尺寸应该考虑锻件收缩和加工余量等因素,以确保最终得到符合要求的锻件。
最后,锻造设备是进行锻造操作所需的机械设备。
常见的锻造设备包括锻造锤、压力机和辊锻机等。
锻造锤是最常用的锻造设备,通过高速下锤或上冲的方式对金属材料进行锻造。
压力机是一种通过油压或液压驱动上下滑块对金属材料进行压力加工的设备。
辊锻机则是利用辊轧原理对金属材料进行塑性变形,适用于生产大批量的长条状或较薄的锻件。
总之,锻造基础知识是进行锻造工艺操作的基础,对于掌握锻造技术和提高产品质量具有重要意义。
通过了解锻造工艺、锻件设计和锻造设备等方面的基础知识,可以更好地应用锻造技术,提高生产效率和产品质量。
此外,锻造的发展也需要不断创新和技术进步,以适应不同行业的需求和挑战,实现锻造工艺的更大发展和应用。
- 1、下载文档前请自行甄别文档内容的完整性,平台不提供额外的编辑、内容补充、找答案等附加服务。
- 2、"仅部分预览"的文档,不可在线预览部分如存在完整性等问题,可反馈申请退款(可完整预览的文档不适用该条件!)。
- 3、如文档侵犯您的权益,请联系客服反馈,我们会尽快为您处理(人工客服工作时间:9:00-18:30)。
25
(四)鍛壓常見不良
流料痕
流
料 痕
如左圖箭頭所示:產品局
部產生流料痕.
原因分析:由於胚料各 部分變形量不一致,產 生的流料痕,經過陽極 後會有色差.(鋁合金 鍛壓難點問題)
26
(五)861C成型仿真報告
861C成型仿真報告
(六)ACER案例評估
ACER案例評估分析
锻造工艺基础知识
1
內容介紹
一、鍛壓知識介紹 二、鍛造工藝流程介紹 三、產品特征對鍛造成型的影響 四、鍛造常見不良及原因分析 五、861C仿真報告
六、ACER案例評估分析
2
一、鍛壓知識介紹
1.鍛壓分類: (固體材料的一部分或整體,經鍛壓成型的過程)
鍛壓工藝分為自由鍛與模鍛 自由鍛:沒有限制胚料的成型特征,一般用於 大型工件的粗成型,常用於汽車,船舶行業。 模鍛件的工藝性:
23
(四)鍛壓常見不良
鏟料
如左圖所示:產品產生嚴 重疊料現象.
原因分析:由於胚料尺 寸規格與模具型腔規格 不一致,導致胚料先接 觸模具部分多余的材料 被刮下而造成.
24
(四)鍛壓常見不良
起皺皮
起
皺
如左圖箭頭所示:產品產
生起皺現象.
原因分析:由於胚料與 模具不是同時接觸,材 料流動不同步,而造成 材料往有空隙處流動.
細小,鍛壓時材料很難完全充填飽滿。一般高徑比控制
在1.5:1以下較為合適。
22
(三)產品特征對鍛造成型的影響(續)
1
13.產品特征倒圓角
*如圖所示:產品特征
1類圓角是鍛造時材料不
2
能完全填充模腔而產生
自然圓角,一般為R0.15
~R0.20;
2類圓角是鍛造時利於材 料流動,不至於產生缺陷, 一般為R0.30~R0.50;
15
(三)產品特征對鍛造成型的影響(續)
6.產品特征存在厚薄相差太大
圖A 9.4
A
0.2
2.5
圖示產品截面,厚度相差太大, 中間沒有走料的位置,影響鍛造 成型時的材料流動,出現厚特征 處不飽滿,薄特征處不能壓薄,且 鍛造壓力很大,模具壽命很低。 (如圖A示)
16
(三)產品特征對鍛造成型的影響(續)
7
(二)鍛壓工藝流程介紹(續)
3,飛邊,沖孔工站:
A,目的: 將上一成型工站所產生的廢料去除,以利
於下一工站的成型.
8
(二)鍛壓工藝流程介紹(續)
4,毛胚的軟化處理:
A,提高,恢復材料的塑性降低變形抗力,改善金 相組織,消除內應力.
B,金屬在(冷沖,冷壓,冷拉,冷紮)過程中,隨 變形量的增加,晶格發生歪扭,晶粒被破壞,破碎 拉長,晶粒間發生相對滑移,同時產生加工硬化現 象,使鋼的硬度,強度增加,而延展性和塑性降低, 所以後續加工必須利用退火過程中的再結晶來消 除冷作硬化.
6
(二)鍛壓工藝流程介紹(續)
2,粗鍛成型:
A,粗鍛成型原則:去除某些特征多余的材料; 填補某些特征處不夠的材料,使材料更利於少料 位置流動.
B,粗鍛模具圓角較大以保証模具的壽命與利 於材料的流動,成型壓力較小.
如右圖所示:產品六個凸 點材料很難流入達到飽滿 程度,所以粗模必須要想 辦法讓材料往難飽滿位置 流動.
磨,精切等輔助工藝來保証.)
5
(二)鍛壓工藝流程介紹(續)
毛胚的表面處理及潤滑: A,表面處理包括:去除表面缺陷,清潔,去脂,
洗滌,去除表面氧化層,在表面形成特殊的保護膜; 以利於潤滑劑更好的填充在胚料表層.常見表面 處理有酸洗,皂化處理,磷化處理等,
B,毛胚潤滑的意義:降低胚料與模具之間的摩 擦系數,減少材料流動成型阻力,提高模具壽命.
18(三)產品特征對鍛来自成型的影響(續)9.產品相鄰特征相差 太近
*如圖所示:產品螺柱 與邊框距離太近,會造 成鍛造時材料流料困 難,模具強度很弱,模 具壽命很低,產品設計 時應留意此問題.
19
(三)產品特征對鍛造成型的影響(續)
10.產品特征寬厚 比相差太大
*如圖所示:產品需要3.0mm厚的材料來鍛造,但 是由於產品部分特征厚度僅為1.29mm,而寬度為 6.92mm,鍛造時會造成材料流動困難,在模具局部 產生很大的拉壓應力,模具易開裂.產品設計時應 避免大平面的存在,或採取倒圓角來消除應力集 中點的產生。
*圖示產品形狀較為復雜,鍛 壓時材料很難充滿模腔,因為 模腔越窄,金屬向模腔內流動 的阻力會越大,使形狀很難成 型.
11
(三)產品特征對鍛造成型的影響(續)
2.產品需要有脫模角3度以上(詳見下圖所示)。
*為了方便產品脫模,減少產品與模腔壁的摩擦 阻力,提高產品的質量及延長模具的使用壽命, 要求產品特征必須有3度以上的脫模角。
R0.50以上
倒圓角處理
20
(三)產品特征對鍛造成型的影響(續)
尖角
11.產品特征與特征處 產生尖角
*如圖所示:此類尖角 處就是模具應力集中點, 會影響到模具的強度, 降低模具的壽命.此類 需倒角R0.50以上. 21
(三)產品特征對鍛造成型的影響(續)
12.留意產品設計時一些細小特征
*如圖所示:此特征高1.50mm直徑為0.80mm,圓柱比較
4.產品中有倒勾特征時,鍛壓不能脫模,此特征需後 續CNC加工.
圖示A處有倒勾,
鍛壓無法脫模,應
A
先把倒勾填充起
來待鍛壓完成後
銑削完成
圖示產品
有倒勾
14
0.60 3.00
(三)產品特征對鍛造成型的影響(續)
5.產品中有薄肋時,鍛壓無法成形.
*如左圖所示:產品特 征筋位太單薄(0.60mm) 高度(3.00mm),高徑 比太大造成鍛壓時材料 流料困難,出現筋位不 飽滿缺陷.一般要求產 品特征高徑比在1.5:1 以下。
7.產品需要有圓角,R過渡.
產品根部需要 全周有圓角 (R0.15~0.30) ,模具不會容 易崩塌,鍛壓 時延長模具壽 命.
17
(三)產品特征對鍛造成型的影響(續)
8.產品特征存在凹位
*如圖所示:產品凹位寬 度(1.23mm)深度 (2.00mm),鍛造時會造 成模具強度很弱,模具壽 命會很低,一般寬度與深 度比控制在1:1以內較合 適.
c.可提高零件的力學性能:鍛壓過程中金屬處於 三向壓應力狀態,金屬的塑性得到充分的發揮和 利用,擠壓後的材料組織結構更加致密;通過鍛造 成型產生的加工硬化可以提高產品的強度.
4
(二)鍛壓工藝流程介紹
1.鍛壓原材料:
對鍛壓原材料要求: A,良好的鍛造特性(屈服強度低,硬化系
數小.) B,良好的表面質量(有必要增加拋光,研
指金屬材料在壓力的作用下發生的塑性變 形,並通過模具來保証產品要求的形狀特征。
影響鍛壓件工藝的因素有: 產品幾何形狀/尺寸/精度/表面粗糙度。 產品材質/成型時的潤滑狀況/模具材料/ 設備精度
3
一、鍛壓知識介紹
2.鍛壓工藝優點:
a.材料利用率高;能成型機加工難以加工的特征; 加工余量較少;
b.可獲得理想的表面粗糙度和表面精度:鍛壓方 法成形的零件具有較為理想的表面粗糙度,一般 可達R0.2-R0.6,表面精度IT7-IT8.
9
(二)鍛壓工藝流程介紹(續)
5,精鍛成型:
A,精鍛成型特點: 由於受產品特征的限制,精鍛成型跟最後鍛 壓胚一樣;但是精鍛模具應避免存在尖角且必須 有脫模角的存在. 精鍛模壽命較低,成型過程中需經常用風槍 吹洗模具及增加模具拋光工序.
10
(三)產品特征對鍛造成型的影響
1.形狀過於復雜,不利於鍛壓時材料的流動成形.
12
(三)產品特征對鍛造成型的影響(續)
溢料位
3.產品需要留有溢料 位(分形面)(詳見下 圖所示)。
去
除
廢
料
方
產品圖
向
鍛胚圖
*如上圖所示,鍛壓時為了材料能完全充填飽滿產
品的每一特征,在上下模之間必須設有溢料位。溢
料位厚度一般為0.30mm以上,通過飛邊去除廢料後
會產生0.50以上的直身位。
13
(三)產品特征對鍛造成型的影響(續)