精益生产(经典课件)
合集下载
《精益生产培训》ppt课件

团队协作实践
通过团队建设活动、项目合作 等方式,促进团队成员之间的
协作和默契。
激励机制设计
物质激励
制定合理的薪酬和福利制度,根据员 工绩效和贡献给予相应的物质奖励。
精神激励
给予员工荣誉、表扬、晋升机会等精 神层面的激励,激发员工的工作热情 。
目标激励
设定具有挑战性的工作目标,鼓励员 工努力达成目标,并给予相应的奖励 。
80%
增强竞争力
通过持续改进、创新等方式提高 企业竞争力,使企业在激烈的市 场竞争中立于不败之地。
02
现场管理改善
现场5S管理
01
整理(Seiri)
清除现场内的杂物,将与工作无关的物品移出现场, 保持工作场所整洁。
02
整顿(Seiton)
对现场内的物品进行分类、标识和定位,方便快速找 到所需物品,提高工作效率。
03
清扫(Seiso)
保持现场清洁,定期清理垃圾和灰尘,创造一个干净 、舒适的工作环境。
04
清洁(Seiketsu)
维持现场的整洁和卫生,防止污染和异物的产生,确 保产品质量。
05
素养(Shitsuke)
培养员工良好的工作习惯和行为规范,提高员工素质 和企业形象。
目视化管理
01
02
03
04
标识明确
发展
随着全球制造业的快速发展,精益生产逐渐在全球范围内得到推 广和应用,成为现代制造业的重要管理思想和方法。
精益生产核心思想
消除浪费
精益生产强调消除生产过程中的一切浪费,包括时 间、人力、物力等方面的浪费,通过优化流程、提 高设备利用率等方式降低成本。
持续改进
精益生产鼓励员工积极参与改进活动,通过不断发 现问题、解决问题来推动企业的持续改进和发展。
通过团队建设活动、项目合作 等方式,促进团队成员之间的
协作和默契。
激励机制设计
物质激励
制定合理的薪酬和福利制度,根据员 工绩效和贡献给予相应的物质奖励。
精神激励
给予员工荣誉、表扬、晋升机会等精 神层面的激励,激发员工的工作热情 。
目标激励
设定具有挑战性的工作目标,鼓励员 工努力达成目标,并给予相应的奖励 。
80%
增强竞争力
通过持续改进、创新等方式提高 企业竞争力,使企业在激烈的市 场竞争中立于不败之地。
02
现场管理改善
现场5S管理
01
整理(Seiri)
清除现场内的杂物,将与工作无关的物品移出现场, 保持工作场所整洁。
02
整顿(Seiton)
对现场内的物品进行分类、标识和定位,方便快速找 到所需物品,提高工作效率。
03
清扫(Seiso)
保持现场清洁,定期清理垃圾和灰尘,创造一个干净 、舒适的工作环境。
04
清洁(Seiketsu)
维持现场的整洁和卫生,防止污染和异物的产生,确 保产品质量。
05
素养(Shitsuke)
培养员工良好的工作习惯和行为规范,提高员工素质 和企业形象。
目视化管理
01
02
03
04
标识明确
发展
随着全球制造业的快速发展,精益生产逐渐在全球范围内得到推 广和应用,成为现代制造业的重要管理思想和方法。
精益生产核心思想
消除浪费
精益生产强调消除生产过程中的一切浪费,包括时 间、人力、物力等方面的浪费,通过优化流程、提 高设备利用率等方式降低成本。
持续改进
精益生产鼓励员工积极参与改进活动,通过不断发 现问题、解决问题来推动企业的持续改进和发展。
《精益生产培训》ppt课件精品模板分享(带动画)
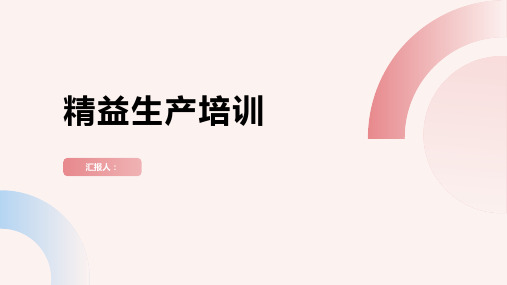
结论:美的集团 的精益生产成功 案例表明,通过 科学管理和创新 技术手段,企业 可以提高生产效 率和产品质量, 降低成本和缩短 交货期,增强市 场竞争力。
如何推广精益生产文化
第六章
提高员工意识
培训:定期组织精益生产培训,让员工了解精益生产理念、方法和工具。
宣传:通过内部宣传、精益文化墙等方式,宣传精益生产的重要性和优势, 增强员工的认同感和归属感。
建立示范点
选择具有代表性的生产现场作为示范点 制定具体的实施方案和计划 安排专业的技术人员进行指导和监督 总结经验教训,不断完善和优化实施方案
激励和奖励机制
建立精益生产知识竞赛,鼓励员工 参与
设立精益生产优秀员工奖,激励员 工积极参与
添加标题
添加标题
添加标题
添加标题
针对实施精益生产的部门或团队进 行奖励
增强客户满意 度
提高产品性能 和质量
提升企业品牌 形象和竞争力
增强企业竞争力
提高生产效率
降低成本
优化资源配置
提升产品质量
创新产品研发
增强市场竞争力
精益生产的核心工具
第三章
价值流分析
定义:识别和追踪产品或服务在生产过程中的所有活动 目的:找出浪费和不增值的环节 方法:绘制价值流图,包括生产流程、时间、人力、物力等 作用:为精益生产提供分析和改进的依据
添加标题
添加标题
它通过消除浪费、提高效率、减少 成本来最大化价值
浪费是指任何消耗了资源而不增加 价值的活动
精益生产的起源
目的:消除浪费,提高效率
起源:20世纪50年代,日本 丰田汽车公司
方法:采用生产流程分析和 改进工具,如价值流图、流
程图等
结果:提高了生产效率和质 量,降低了成本,增强了竞
精益生产(经典完整)ppt课件

• 多品种小批量
• 订单拉动
• 准时化
• 连续流
6
制造业面临的环境
➢ 快速并准时交货 ➢ 需求品种增加,特殊定制 ➢ 不断改进质量及降低销售价格 ➢ 产品的生命周期越来越短 ➢ 无国界,中国成为世界工厂 ➢ 紧缩与通胀
问题:如何面对环境挑战?用存货?
精选ppt课件2021
7
Lean -“精益”释义
13
业务流程中的八大浪费
➢ 计划不周 ➢ 信息不全 ➢ 过程不当 ➢ 沟通不畅 ➢ 调整审批 ➢ 检验返工 ➢ 批量等待 ➢ 动作技能
精选ppt课件2021
14
从增值比看改善的空间
增值比率 =
增值时间(Value added time) 制造周期(Manufacturing cycle timXe)100%
起源于20世纪50年代丰田汽车公司,而在80年中期被欧
美企业纷纷采用。随着微利时代的来临,精益生产模式 成为企业竞争的有力武器
精选ppt课件2021
5
制造系统演化史
手工生产 大批量生产 精益生产
?
精选ppt课件2021
Henry Ford
福特首创装配线
• 大规模 • 低品种 • 工人被当成机器
TPS 和 大野耐一
案例分享 模拟演练 讨论
精选ppt课件2021
3
1Lean Manufacturing System Briefing
精益生产系统简介
➢ 制造系统的要点
➢ 精益生产五项原则
➢ 精益企业之屋?
精选ppt课件2021
4
Lean Thinking and Lean Manufacturing System 精益思维和精益生产系统
《精益生产》课件

电子制造业采用精益生产方法, 通过减少浪费和优化供应链,提 高生产效率和产品质量。
航空制造业
航空制造业采用精益生产方法, 通过优化生产流程和提高工厂效 率,实现生产能力的提升和交付 时间的缩短。
结论
精益生产的优势和不足
精益生产的优势包括提高效率、降低成本和改善质量,但也存在实施难度、需求变化风险等 不足之处。
3
5S
5S是一种创建清洁、整齐、有序和高效工作环境的方法,以促进工作效率和员工安全。
4
Kaizen
Kaizen是一种通过小步骤持续改进的方法,以实现生产过程的不断优化和卓越。
精益生产的应用
汽车制造业
汽车制造业采用精益生产方法, 通过优化生产流程和提高质量, 实现生产效率的提升和成本的降 低。
电子制造业《精益生产》Fra bibliotekPT课件"精益生产"是一种致力于最大限度减少浪费和提高效率的制造管理方法。本 课件将介绍精益生产的概念、核心工具和应用,并分享汽车制造、电子制造 和航空制造等领域的成功案例。
简介
什么是精益生产?
精益生产是一种致力于通过 减少浪费、提高效率和优化 流程来提高生产和运营绩效 的管理方法。
精益生产的未来发展趋势
随着技术的发展和市场的变化,精益生产将更加注重数字化、智能化和可持续发展。
如何应用精益生产提高企业生产效率?
企业可以通过培训员工、优化流程和引入先进技术来应用精益生产,以提高生产效率和竞争 力。
精益生产的主要特点
精益生产的主要特点包括价 值流导向、一次制品流动、 持续改善和员工参与。
精益生产的重要性
精益生产可以帮助企业提高 质量、降低成本、提升交付 速度,并增强市场竞争力。
精益生产的核心工具
航空制造业
航空制造业采用精益生产方法, 通过优化生产流程和提高工厂效 率,实现生产能力的提升和交付 时间的缩短。
结论
精益生产的优势和不足
精益生产的优势包括提高效率、降低成本和改善质量,但也存在实施难度、需求变化风险等 不足之处。
3
5S
5S是一种创建清洁、整齐、有序和高效工作环境的方法,以促进工作效率和员工安全。
4
Kaizen
Kaizen是一种通过小步骤持续改进的方法,以实现生产过程的不断优化和卓越。
精益生产的应用
汽车制造业
汽车制造业采用精益生产方法, 通过优化生产流程和提高质量, 实现生产效率的提升和成本的降 低。
电子制造业《精益生产》Fra bibliotekPT课件"精益生产"是一种致力于最大限度减少浪费和提高效率的制造管理方法。本 课件将介绍精益生产的概念、核心工具和应用,并分享汽车制造、电子制造 和航空制造等领域的成功案例。
简介
什么是精益生产?
精益生产是一种致力于通过 减少浪费、提高效率和优化 流程来提高生产和运营绩效 的管理方法。
精益生产的未来发展趋势
随着技术的发展和市场的变化,精益生产将更加注重数字化、智能化和可持续发展。
如何应用精益生产提高企业生产效率?
企业可以通过培训员工、优化流程和引入先进技术来应用精益生产,以提高生产效率和竞争 力。
精益生产的主要特点
精益生产的主要特点包括价 值流导向、一次制品流动、 持续改善和员工参与。
精益生产的重要性
精益生产可以帮助企业提高 质量、降低成本、提升交付 速度,并增强市场竞争力。
精益生产的核心工具
《精益生产基础培训》ppt课件pptx
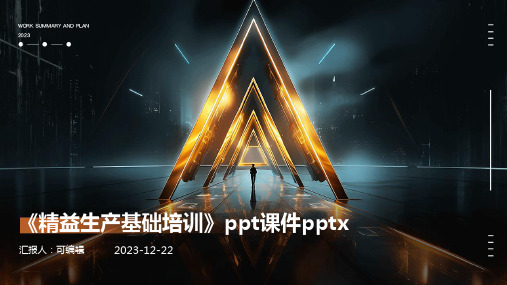
价值流图绘制与改进
绘制价值流图
根据价值流分析结果,绘制企业价值 流图,直观展示各环节之间的关系和 现状。
改进策略制定
针对价值流图中的瓶颈和浪费环节, 制定相应的改进措施和方案。
5S管理实施与标准化
5S管理推行
在企业内部推行5S管理,即整理、整顿、清扫、清洁和素养,提高现场管理水 平和效率。
标准化实施
精益生产的核心思想
01
02
03
04
价值流分析
识别并消除生产过程中的浪费 ,确保产品从供应商到客户的
过程是增值的。
流动与平衡
优化生产流程,确保产品在生 产过程中快速、顺畅地流动, 同时保持生产过程的平衡。
拉动系统
根据客户需求进行生产,采用 拉动系统实现准时化生产。
持续改进
不断寻求改进机会,通过不断 优化生产过程来提高效率、降
TPM有助于提高产品质量和生 产稳定性,降低生产成本。
TPM的实施需要制定详细的维 护计划和培训员工掌握维护技 能。
03
精益生产实施步骤
目标设定与价值流分析
目标设定
明确企业实施精益生产的目标,包括降低成本、提高效率、 优化流程等。
价值流分析
对企业业务流程进行全面分析,识别价值流中的瓶颈和浪费 环节。
02
精益生产工具与技术
价值流图
价值流图是一种可视化工具,用于描 绘产品从原材料到最终客户手中的整 个过程。
价值流图有助于企业了解客户需求, 制定出更符合客户期望的生产计划。
通过价值流图,企业可以识别出过程 中的瓶颈、浪费和不必要的环节,从 而优化流程,提高效率。
价值流图的应用范围广泛,适用于不 同规模和行业的企业。
01
精益生产(完美版)(PPT109页)
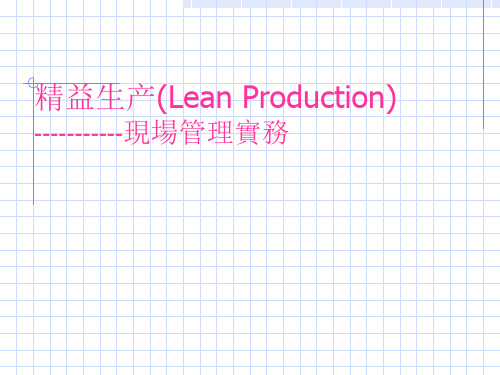
(3)消除浪费——管理的重要目的之一
Management
创造性的管理活动 提高产品和服务的附加价值
+1 增加价值
0
-1
消除浪费
最大限度地减少不增值劳动 封闭性的管理活动
精益思维(Lean Thinking)的5个基本原则
No.1 从顾客的角度而不是从某个公司、部门或机构 的角度确定价值;
No.2 确定设计、采购和生产产品的整个价值流中的 步骤,找出不增加价例 能力需求:100件/H
项目 能力 达成率 奖金 效率
工序1 100件/H
100% 标准产量奖金 个别效率合格
工序2 125件/H
125% 125%奖金 个别效率高
工序3 80件/H
80% 0
个别效率低
工序4 100件/H
80% 0
个别效率低
≠ 个别效率
整体效率
专业化作业有利于提高个别效率,不少企 业因此实行计件工资。
精益生产(Lean Production)
-----------現場管理實務
第一部分 精益生产簡介
很多精益技术源于日本企业的生产管理方法, 如看 板管理、全面质量管理(TQM)、快速换模等技术 都是 在丰田等日本公司的生产管理(NPS)中产生的。美国 的丹尼尔·琼斯教授等人通过大量细致的研究,并与 当 时欧美大量生产方式相比较后得出结论,正是这 些生 产管理方式使得日本企业(如丰田汽车公司)迅速成为 世界级的公司。这些管理思想和原则就是精益生产。
· 三不主义
77个个““零””目目标标 不良
保证
不良率高企, 批量事故多发, 忙于“救火”
· 零缺陷运动 · 工作质量 · 全员质量改善活动 · 自主研究活动 · 质量改善工具运用
精益生产(经典课件)
益生产的成功应用,将生产线分为多个小组, 大大提高了生产效率。
亚马逊零售业应用
精益生产方法的成功运用,将极大地提高亚马 逊的配送速度和交付准确率。
连托克成功案例
将精益生产方法成功应用于不同规模、不同产 品的生产企业。
结论
1 核心思想
2 方法
3 实战案例
价值导向、浪费削减和 流程改善。
精益生产应对了传统制造 的缺陷,使制造企业能够 更加灵活地适应市场需求。
精益生产思维和基本原则
精益生产思维
精益生产思维是一种以价值为导向、强调流程改 善和人员参与的生产方式。
基本原则
未价值增加的活动均属浪费;不合格的产品是浪 费的代表;减少浪费是精益制造的关键。
精益生产的目标和核心方法
1
少即是多
通过减少浪费、缩短生产周期、提高质量和降低成本来实现客户满意度的提升。
2
单一物流
精益生产的主要原则之一,通过减少库存和缩短运输时间来提高运营效率。
3
5S
一种工具和流程,旨在改善工作场所的卫生和安全,提高工作效率和精度。
4
快速换模(S MED)
一种生产工具和技术,能够缩短设备的准备时间,使生产任务更加高效和快速。
质量保证和流程改善
J id o k a
自动停机是精益生产的另一项核心技术,可大大提高生产线的效率和质量。
一致节奏
制定标准作业程序,使生产线上的工作效率更高,同时保证产品的质量。
价值流
通过对核心流程的改善,精益生产可以帮助企业提高产品质量和快速交付时间。
案例分析
丰田生产方式
精益生产最早的应用之一,完美地融合了精益 生产理念和实际实践。
单一物流、5S、快速换 模、Jidoka等一系列方 法和工具的综合运用。
亚马逊零售业应用
精益生产方法的成功运用,将极大地提高亚马 逊的配送速度和交付准确率。
连托克成功案例
将精益生产方法成功应用于不同规模、不同产 品的生产企业。
结论
1 核心思想
2 方法
3 实战案例
价值导向、浪费削减和 流程改善。
精益生产应对了传统制造 的缺陷,使制造企业能够 更加灵活地适应市场需求。
精益生产思维和基本原则
精益生产思维
精益生产思维是一种以价值为导向、强调流程改 善和人员参与的生产方式。
基本原则
未价值增加的活动均属浪费;不合格的产品是浪 费的代表;减少浪费是精益制造的关键。
精益生产的目标和核心方法
1
少即是多
通过减少浪费、缩短生产周期、提高质量和降低成本来实现客户满意度的提升。
2
单一物流
精益生产的主要原则之一,通过减少库存和缩短运输时间来提高运营效率。
3
5S
一种工具和流程,旨在改善工作场所的卫生和安全,提高工作效率和精度。
4
快速换模(S MED)
一种生产工具和技术,能够缩短设备的准备时间,使生产任务更加高效和快速。
质量保证和流程改善
J id o k a
自动停机是精益生产的另一项核心技术,可大大提高生产线的效率和质量。
一致节奏
制定标准作业程序,使生产线上的工作效率更高,同时保证产品的质量。
价值流
通过对核心流程的改善,精益生产可以帮助企业提高产品质量和快速交付时间。
案例分析
丰田生产方式
精益生产最早的应用之一,完美地融合了精益 生产理念和实际实践。
单一物流、5S、快速换 模、Jidoka等一系列方 法和工具的综合运用。
《精益生产》PPT课件
设备现场管理应用
在精益生产方式中,设备故障被视为无效劳动和浪费, 提出设备故障要向零进军,这就要求设备运行过程尽量 不发生故障,少发生故障。
实行全员维修和保养; 实行针对性预防检修; 实行改善性维修;
精益生产系统的五项原则
质量是 制造出来的
标准化
精益的 制造系统
持续改进
员工参与
短的制造周期
拉动式方法的特点:
坚持一切以后道工序需求出发,宁肯中断生产,也不搞超前超
1 量生产。拉动式生产的核心就是准时化,就是要求在需要的事
后,生产需要的产品和需要的数量,所以又把它称为准时化生 产(Just In Time)。
生产指令不仅仅是生产作业计划,而且还用看板进行为调节。
2 看板成为实施拉动式生产的重要手段。
看板来源于大野耐一从美国超级市场的启示。
拉动式方法 在生产制造过程中的具体运用
1 以市场需求拉动企业生产。
在企业内部,以后道工序拉动前道工序生产,以总装配拉动总
2 成装配,以总成装配拉动零件加工,以零件拉毛坯生产,用以
大幅度压缩在制品储备,消除无效劳动。
U型平面布置的“一个流”生产线; 多工序管理和多机床操作 成批轮番作业的生产线 快速换模技术,实现小批量多批次生产
jit以小批量生产为准则换模工作必须尽快完成消除浪费的方设计流程连接操作平衡工作站能力减小批量规减少安装换模时间2tqm全面质量管理尊重员工qcc小组合理化建议3稳定计划均衡计划不超过生产能力建立冻结区间指计划固定不弯一个时间区段4看板控制由后向前传送指令5与供应商紧密合作缩短提前期增加供货频率交货要及时保证质量可靠性6减少额外存货寻找其他区采用传送带运输机7改进产品设计产品标准化零件标准化及零件数减少改进过程设计产品质量期望jit七个前提条件61传统生产管理中的生产指令生产计划实际生产数量生产顺序表库存工序a工序b工序c库存完成生产指令计划生产数量与实际生产数量不同生产指令生产指令62jit生产计划实际生产数量生产顺序表看板工序a工序b工序c看板完成生产指令计划生产数量与实际生产数量相同63确定看板数量每个容器内数量64防止过量生产生产没有看板不能生产也不能运送目视管理看板必须附在实物上按照取下看板的顺序进行生产改善工具不能把不良品送往下一工序看板机能生产及运送的工作指令65生产系统
精选精益生产课件
计算如下: 60m / h 60s / h 21.2units / h 170s / unit 80units / h 3.8 21.2units / h
(取4个工作台,尚有生产能力剩余)
规划精益生产单元的布置。
实际设计生产精益生产单元时,可以考 虑设置两个铣、钻、磨加工区,每个加 工区由两个工作台组成,每个工作台配 备一个工人
生产指定产品每道工序的单位加工时间:
工序 加工时间(秒)工序 加工时间(秒)
铣(M) 80
装配线1 80
钻(D) 30
装配线2 180
磨(P) 60
包装 30
现对其进行精益化改造 经调查: 1.铣、钻、磨床尚有剩余生产能力,因
此在不影响其它生产条件下,可进行 适当调整 2.所有装配线和包装依靠手工完成,只 需提供工作台和工具
消除零件不必要的移动
生产布局合理是造成零件往返搬动的 根源,使得生产线长,生产周期长,占 用很多在制品库存,增加生产成本
按加工顺序安排设备,尽可能紧凑,消 除不必要的移动,节约生产时间
消灭库存 精益生产对库存的看法: 1、会掩盖许多生产问题 2、会滋长工人的惰性 3、占用大量的资金
因此,库存是最大的浪费,必须消灭
看待库存
是必要的
是万恶之源
业务观 严格分工和控制 相互协作,流程精简
质量观 次品是必然的
零缺陷
人
附属于岗位
强调能动性、协调
精益生产的实施方法
如何改进生产流程
消除检验和返工 把防错技术(POKA YOKE)的思想贯穿 到整个生产过程 从产品设计开始就把质量问题考虑进去, 保证每种产品只能严格地按照正确的方 式加工和安装,避免生产流程中可能发 生的错误
精益生产ppt优质版(89张)
消除浪费 消除浪费 消除浪费
没有浪费
浪 费
浪
浪
费
费
目 标
精
益
成
本
企业不断地强化自己的生产过程,随时消除生产过程中的 浪费,力求使生产过程中所用的资源绝对最少,从而使整个生 产看起来很“精”,但又能达到很“益”的结果。
16
二、认识浪费
1. 浪费等于在“烧钱” 2. 制造现场的八大浪费 3. 价值流图与分析方法 4. 价值流图绘制练习
焊接
自动
设备
组装1 组装2
检测
包装
1臂间距
极少数自动设备
多数手工作业 面向生产线
2H工位轮换 (多技能)
自主质量改进
28
三、精益生产方式
3.2 单件流
何谓“一个流”?
也叫“单件流”。是指从材料投入到成品产出的整个生 产过程,零件始终处于不停滞、不堆积、不贮存,按节拍 “一个一个”地流动下去的生产方法。
概念一:
Lean Production
简称LP
精益 ·生产
上世纪80年代,美国麻省理工学院数位国际汽车计划组 (IMVP)的专家对以日本丰田公司为代表的汽车制造商进 行了为期十年的调查,发现日本汽车企业在生产管理方面 有许多独到的生产方式,正是这些生产方式的实施,使日 本汽车企业能通过低成本、高品质占领国际汽车市场,将 这些生产方式进行总结,并称之为“Lean Production , 简称LP”。
77、好朋友的定D-义交是:付你、混得反好应,他速为度你高兴;你混最得柔不好性,交他为货你着急。
“零”故障
(造7)名营医销专自家己,的通D人e过才l学i。v习在i交r患y流者、就走诊进的社问区题、上对,口很支多援人、相专信家名讲医座专等家形,式有,时把为自能己够的找专知家名学专者家给宁“推可出零舍去近”,求得停远到。滞社因会此认我可们,必营须销在好医自院己重的点人打
- 1、下载文档前请自行甄别文档内容的完整性,平台不提供额外的编辑、内容补充、找答案等附加服务。
- 2、"仅部分预览"的文档,不可在线预览部分如存在完整性等问题,可反馈申请退款(可完整预览的文档不适用该条件!)。
- 3、如文档侵犯您的权益,请联系客服反馈,我们会尽快为您处理(人工客服工作时间:9:00-18:30)。
示了信息流与物流之间的联系
➢ Provides a communication tool for all levels 广泛沟通的工具 ➢ Helps establish priorities based on barriers to flow 确定优先次序
➢ Ties together lean concepts and techniques helps avoid cherry-picking 结合精益的概念与技术…避免“只挑容易的” 来改进
……否则,要检查一下你在哪里做错了!
-《精益思想》, Womack & Jones
构筑精益企业之屋
精益企业
消除浪费降低成本
库存降低
全
全
面
准时化生产
面
生
质
产
看板拉动
量
维
管
护
均衡混流生产
理
设 备
缩短生产周期
自 动
总
化
有
小批量生产
流动生产
及
效
防
性
作业快速转换
设备布局 多技能员工 错
观念转变,消除浪费,价值流管理,团队精神及5S,持续改进
案例分享 模拟演练 讨论
1 Lean Manufacturing System Briefing 精益生产系统简介
➢ 制造系统的要点 ➢ 精益生产五项原则 ➢ 精益企业之屋?
Lean Thinking and Lean Manufacturing System 精益思维和精益生产系统
Starting with Toyota in the late 50’s and catching
Warehousing
Is Product Available?
Yes
No
Pick product for order
Transportation Does Customer have other shipments?
No
Yes
Will Customer allow consolidated shipments? No
精益六西格玛工具Lean6Sigma Tools
标准化作业 Standard Work
单元化制造
Cellular
5S
Manufacturing
减少换型时间 Set Up Reduction
价值流图 Value Stream
Mapping
防错 Mistake Proofing
全面设备维护 Total
Future status 未来状态图
工作计划及 实施
➢ 设计一个精益价值流 ➢ 制订“未来状态”的实施计划
Value Stream Mapping – Icons 绘价值流分析图 之 图标
物流图标
ASSEMBLY
内部工艺过程
XYZ Corporation
外部资源
C/T = 45 sec C/O = 30 mins 3 Shifts 2% Scrap
两班生产
冲压
I
焊接 #1
焊接 #2
装配 #1
装配 #2
I
I
I
I
I
MCT =23.5 Days
VA = 188 Sec
我们怎样才能实现未来状态 精益三要素
1.
节拍Takt
2.
流动Flow
3.
拉动Pull
BUSINESS PROCESS MAPPING 业务流程分析
Typical Order Fulfillment Process
on in the mid – 80’s in the reminder of the industrial world, Lean Manufacturing has become a key strategy for manufacturers
起源于20世纪50年代丰田汽车公司,而在80年中期被欧
业务流程中的八大浪费
➢ 计划不周 ➢ 信息不全 ➢ 过程不当 ➢ 沟通不畅 ➢ 调整审批 ➢ 检验返工 ➢ 批量等待 ➢ 动作技能
从增值比看改善的空间
增值比率 =
增值时间(Value added time) 制造周期(Manufacturing cycle timXe)100%
增值时间:站在客户立场看制造过程中的增值动作和时间 如:改变形状、改变性能、组装、包装等
精益的“精”就是指更少的投入,而“益”指更多的产出
What is Lean Manufacturing 什么是精益生产-五个原则
Perfect 完美
没有任何事物 是完美的 不断改进
Value 价值
站在客户 的立场上
Lean Manufacturing
精益生产
Value Stream 价值流
从接单到发货 过程的一切活动
Ship Order
Customer Receives Order
Manufacturing
Will product be available before order ships? No
Is production scheduled to manufacture product? No
Yes Yes
Withdrawal Kanban
推动箭头
Signal Kanban
超市
Kanban Post
Value Stream Mapping Steps 价值流图析步骤
Product family 产品族
Current status 当前状态图
➢ 将注意力集中在单个的产品族上 ➢ 了解工艺工程当前是如何运作的
美企业纷纷采用。随着微利时代的来临,精益生产模式 成为企业竞争的有力武器
制造系统演化史
手工生产 大批量生产 精益生产
?
Henry Ford
福特首创装配线
• 大规模 • 低品种 • 工人被当成机器
TPS 和 大野耐一
• 多品种小批量 • 订单拉动 • 准时化 • 连续流
制造业面临的环境
➢ 快速并准时交货 ➢ 需求品种增加,特殊定制 ➢ 不断改进质量及降低销售价格 ➢ 产品的生命周期越来越短 ➢ 无国界,中国成为世界工厂 ➢ 紧缩与通胀
Is there any
Sales Customer Places Order
problem here?
Order Entry
Is order correct? Yes
No Call Customer and make corrections.
Send order to warehouse for picking
• “只要存在某个提供顾客的产品或者服务 ,就一定存在一个价值流。挑战在于如何 去看到它。”
Value Stream 价值流
价值流包含的是特定产品从进公司到发货至客户 的所有要素 (包括增值的和非增值的)。
需求
设计
82
总装厂
原材料
零件生产
发货
客户
Why Mapping the Value Stream 为什么要图析价值流
➢ Develops ability to see the total flow...beyond the single process level 建立超越单个工艺过程层次而看到宏观生产流程的能力
➢ Helps identify the sources of waste 帮助发现浪费源 ➢ Shows the linkage between information flow and the material flow 展
模具设计 修改
Productive Maintenance
拉系统Pull Systems
减少变异 Variation Reduction
识别和消除八大浪费
➢ Overproduction 过量生产 ➢ Inventory 库存 ➢ Transportation 搬运 ➢ Correction 返工 ➢ Processing 过程不当 ➢ Motion 多余动作 ➢ Waiting 等待 ➢ Aptitude 智力
分批地看板到达 看板收集盒
Value Stream Mapping - Current Status 当前状况图示
XX钢铁厂 卷材
每周两次
6 周预测 每周订货
信息控制
(销售、物料、采购、生产控制)
90/60/30 天预测 每天订单
XX装配厂
月需求18400 -12,00 左向 -6,400 右向 包装单位20
顾客
原材料/在制品/成品
2
Value Stream Mapping
价值流分析
供应商
信息控制
顾客
工序A
工序B
工序C
理解流程…看到价值…憧憬未来状态
Value Stream 价值流
➢“Whenever there is a product (or service) for a customer, there is a value stream. The challenge lies in seeing it.”
LEAN MANUFACTURING SYSTEM
精益生产系统
课堂纪律
➢ 1、关闭手机 ➢ 2、集中提问 ➢ 3、空杯心态 ➢ 4、积极参与
What Shall We Talk…? 内容安排
➢ 精益生产系统简介 ➢ 价值流分析 ➢ IE工业工程 ➢ TPM运行效率 ➢ 看板拉动系统 ➢ 精益生产推行策略
Yes Yes
Expedite manufacturing schedule
Cancel Order
I think it happens very
➢ Provides a communication tool for all levels 广泛沟通的工具 ➢ Helps establish priorities based on barriers to flow 确定优先次序
➢ Ties together lean concepts and techniques helps avoid cherry-picking 结合精益的概念与技术…避免“只挑容易的” 来改进
……否则,要检查一下你在哪里做错了!
-《精益思想》, Womack & Jones
构筑精益企业之屋
精益企业
消除浪费降低成本
库存降低
全
全
面
准时化生产
面
生
质
产
看板拉动
量
维
管
护
均衡混流生产
理
设 备
缩短生产周期
自 动
总
化
有
小批量生产
流动生产
及
效
防
性
作业快速转换
设备布局 多技能员工 错
观念转变,消除浪费,价值流管理,团队精神及5S,持续改进
案例分享 模拟演练 讨论
1 Lean Manufacturing System Briefing 精益生产系统简介
➢ 制造系统的要点 ➢ 精益生产五项原则 ➢ 精益企业之屋?
Lean Thinking and Lean Manufacturing System 精益思维和精益生产系统
Starting with Toyota in the late 50’s and catching
Warehousing
Is Product Available?
Yes
No
Pick product for order
Transportation Does Customer have other shipments?
No
Yes
Will Customer allow consolidated shipments? No
精益六西格玛工具Lean6Sigma Tools
标准化作业 Standard Work
单元化制造
Cellular
5S
Manufacturing
减少换型时间 Set Up Reduction
价值流图 Value Stream
Mapping
防错 Mistake Proofing
全面设备维护 Total
Future status 未来状态图
工作计划及 实施
➢ 设计一个精益价值流 ➢ 制订“未来状态”的实施计划
Value Stream Mapping – Icons 绘价值流分析图 之 图标
物流图标
ASSEMBLY
内部工艺过程
XYZ Corporation
外部资源
C/T = 45 sec C/O = 30 mins 3 Shifts 2% Scrap
两班生产
冲压
I
焊接 #1
焊接 #2
装配 #1
装配 #2
I
I
I
I
I
MCT =23.5 Days
VA = 188 Sec
我们怎样才能实现未来状态 精益三要素
1.
节拍Takt
2.
流动Flow
3.
拉动Pull
BUSINESS PROCESS MAPPING 业务流程分析
Typical Order Fulfillment Process
on in the mid – 80’s in the reminder of the industrial world, Lean Manufacturing has become a key strategy for manufacturers
起源于20世纪50年代丰田汽车公司,而在80年中期被欧
业务流程中的八大浪费
➢ 计划不周 ➢ 信息不全 ➢ 过程不当 ➢ 沟通不畅 ➢ 调整审批 ➢ 检验返工 ➢ 批量等待 ➢ 动作技能
从增值比看改善的空间
增值比率 =
增值时间(Value added time) 制造周期(Manufacturing cycle timXe)100%
增值时间:站在客户立场看制造过程中的增值动作和时间 如:改变形状、改变性能、组装、包装等
精益的“精”就是指更少的投入,而“益”指更多的产出
What is Lean Manufacturing 什么是精益生产-五个原则
Perfect 完美
没有任何事物 是完美的 不断改进
Value 价值
站在客户 的立场上
Lean Manufacturing
精益生产
Value Stream 价值流
从接单到发货 过程的一切活动
Ship Order
Customer Receives Order
Manufacturing
Will product be available before order ships? No
Is production scheduled to manufacture product? No
Yes Yes
Withdrawal Kanban
推动箭头
Signal Kanban
超市
Kanban Post
Value Stream Mapping Steps 价值流图析步骤
Product family 产品族
Current status 当前状态图
➢ 将注意力集中在单个的产品族上 ➢ 了解工艺工程当前是如何运作的
美企业纷纷采用。随着微利时代的来临,精益生产模式 成为企业竞争的有力武器
制造系统演化史
手工生产 大批量生产 精益生产
?
Henry Ford
福特首创装配线
• 大规模 • 低品种 • 工人被当成机器
TPS 和 大野耐一
• 多品种小批量 • 订单拉动 • 准时化 • 连续流
制造业面临的环境
➢ 快速并准时交货 ➢ 需求品种增加,特殊定制 ➢ 不断改进质量及降低销售价格 ➢ 产品的生命周期越来越短 ➢ 无国界,中国成为世界工厂 ➢ 紧缩与通胀
Is there any
Sales Customer Places Order
problem here?
Order Entry
Is order correct? Yes
No Call Customer and make corrections.
Send order to warehouse for picking
• “只要存在某个提供顾客的产品或者服务 ,就一定存在一个价值流。挑战在于如何 去看到它。”
Value Stream 价值流
价值流包含的是特定产品从进公司到发货至客户 的所有要素 (包括增值的和非增值的)。
需求
设计
82
总装厂
原材料
零件生产
发货
客户
Why Mapping the Value Stream 为什么要图析价值流
➢ Develops ability to see the total flow...beyond the single process level 建立超越单个工艺过程层次而看到宏观生产流程的能力
➢ Helps identify the sources of waste 帮助发现浪费源 ➢ Shows the linkage between information flow and the material flow 展
模具设计 修改
Productive Maintenance
拉系统Pull Systems
减少变异 Variation Reduction
识别和消除八大浪费
➢ Overproduction 过量生产 ➢ Inventory 库存 ➢ Transportation 搬运 ➢ Correction 返工 ➢ Processing 过程不当 ➢ Motion 多余动作 ➢ Waiting 等待 ➢ Aptitude 智力
分批地看板到达 看板收集盒
Value Stream Mapping - Current Status 当前状况图示
XX钢铁厂 卷材
每周两次
6 周预测 每周订货
信息控制
(销售、物料、采购、生产控制)
90/60/30 天预测 每天订单
XX装配厂
月需求18400 -12,00 左向 -6,400 右向 包装单位20
顾客
原材料/在制品/成品
2
Value Stream Mapping
价值流分析
供应商
信息控制
顾客
工序A
工序B
工序C
理解流程…看到价值…憧憬未来状态
Value Stream 价值流
➢“Whenever there is a product (or service) for a customer, there is a value stream. The challenge lies in seeing it.”
LEAN MANUFACTURING SYSTEM
精益生产系统
课堂纪律
➢ 1、关闭手机 ➢ 2、集中提问 ➢ 3、空杯心态 ➢ 4、积极参与
What Shall We Talk…? 内容安排
➢ 精益生产系统简介 ➢ 价值流分析 ➢ IE工业工程 ➢ TPM运行效率 ➢ 看板拉动系统 ➢ 精益生产推行策略
Yes Yes
Expedite manufacturing schedule
Cancel Order
I think it happens very