单阀与顺序阀切换的实实现
单顺序阀切换总结报告

单顺序阀切换总结报告一、引言单顺序阀切换是指在工业自动化系统中,通过使用顺序阀的原理和方法,实现对流体介质的切换和流量的控制。
在工业生产和设备操作中,顺序阀的应用非常广泛,具有重要的意义和作用。
本报告旨在总结单顺序阀切换的相关知识和应用,为工程实践提供参考。
二、单顺序阀切换的原理与方法1.单顺序阀切换的原理单顺序阀切换是基于顺序阀的工作原理。
顺序阀是一种基本的流量控制元件,由阀芯、阀座和弹簧等部分组成。
通过控制阀芯的运动来调节介质流量的大小和方向。
在单顺序阀切换中,通过控制顺序阀的开启和关闭时间,实现对不同介质的切换。
2.单顺序阀切换的方法(1)计时切换法:根据不同介质所需的时间长度,设置对应的开启和关闭时间。
通过定时器控制顺序阀的工作时间,实现切换。
(2)信号切换法:根据不同介质的信号特征,通过传感器检测介质的到达并发出切换信号,控制顺序阀的开启和关闭。
(3)手动切换法:通过操作人员手动控制顺序阀的开启和关闭,实现切换。
三、单顺序阀切换的应用1.工业自动化生产线在工业自动化生产线中,常常需要切换不同介质,以满足不同产品的需求。
通过单顺序阀切换,可以实现生产线的灵活转换,提高生产效率。
2.流程控制系统在流程控制系统中,常常需要对介质的流动方向和流量进行控制。
通过单顺序阀切换,可以实现对介质流动方向和流量的调节,实现流程控制。
3.液压系统在液压系统中,常常需要切换不同液压介质,以满足不同工作要求。
通过单顺序阀切换,可以实现对液压介质的切换和控制,提高系统的可靠性和稳定性。
四、单顺序阀切换的优缺点1.优点(1)操作简单:单顺序阀切换操作简单,容易掌握。
(2)切换效率高:单顺序阀切换速度快,切换时间短。
(3)可靠性高:单顺序阀切换操作可靠,不易出现故障。
2.缺点(1)对切换介质的要求高:单顺序阀切换需要对不同介质的压力、流量等参数进行准确控制,对切换介质要求较高。
(2)成本较高:单顺序阀切换需要采购和安装额外的顺序阀,增加了系统的成本。
汽轮机单顺阀切换分析与研究

汽轮机单顺阀切换分析与研究摘要:本文针对黄陵矿业煤矸石发电公司2*300MW发电机组汽轮机配汽方式进行论述,对单阀和顺序阀运行的优缺点进行了对比,介绍了单顺阀切换的目的。
通过对切换前后的各项技术参数进行统计、研究,以解决单顺阀切换过程中存在的问题。
关键词:300MW汽轮机;单阀;顺序阀;切换;振动;温度黄陵矿业煤矸石发电公司2*300MW发电机组汽轮机由上海汽轮机厂设计制造。
汽轮机进汽设有两个高压主汽门和两个中压主汽门、两个中压调门和6个高压调门,正常运行时,高压主汽门、中压主汽门、中压调门保持全开,高压调门调节汽轮机进汽量,调整机组负荷。
单阀运行时,6个高压调门同时动作,即同时开大或关小,顺序阀运行时,按照上海汽轮机厂说明书规定,新投产机组在单阀运行六个月后,允许单阀切换为顺序阀运行。
一、单阀/顺序阀单阀控制,调节方式为节流调节,进汽为全周进汽。
该运行方式优点为调节级处金属温度受热均匀,热应力较小,对汽轮机寿命有益;同时,机组响应负荷变化较快,在进行变负荷调峰时,调节级金属温度波动较小。
不足之处是,机组在部分负荷运行时,由于所有高压调门都未全开,导致进汽节流,造成节流损失。
发电汽耗增大。
顺序阀控制,调节方式为喷嘴调节,进汽为部分进汽。
该运行方式优点为,机组在带部分负荷运行时,调门按照DEH逻辑里设定好的阀门开启顺序进行开启,最终阀门状态为,一部分阀门全开或全关,只留一个调门进行调节负荷。
这样,进入汽轮机的蒸汽节流少,节流损失较小,发电汽耗减小。
缺点是调节级处为部分进汽,调节级处金属温度受热不均匀,热应力较大,对汽轮机寿命不利;同时,在机组负荷变化较频繁时,调节级处运行工况更加恶劣。
我厂在对#2汽轮机进行单顺阀切换时,切换过程历时5min,切换开始前,负荷:245MW,阀门为单阀控制,阀位为:27.5%。
负荷投入功率控制,切换开始后,高压调阀按照GV1,2(同时开启)-GV4-GV5-GV6-GV3的顺序进行切换。
汽轮机单、顺阀切换操作说明。
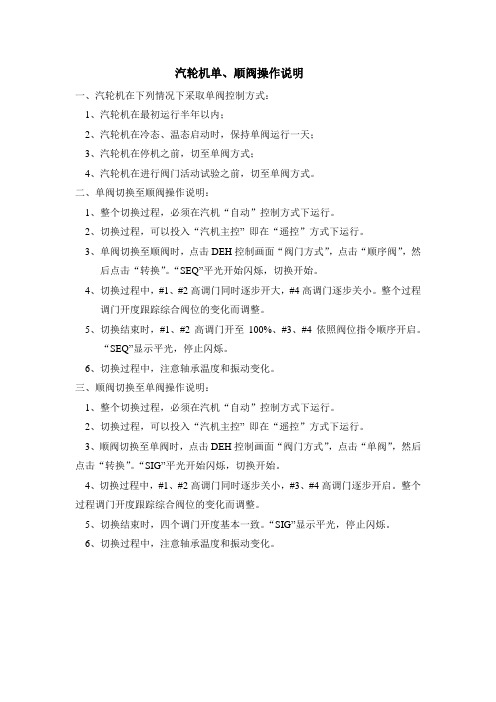
汽轮机单、顺阀操作说明
一、汽轮机在下列情况下采取单阀控制方式:
1、汽轮机在最初运行半年以内;
2、汽轮机在冷态、温态启动时,保持单阀运行一天;
3、汽轮机在停机之前,切至单阀方式;
4、汽轮机在进行阀门活动试验之前,切至单阀方式。
二、单阀切换至顺阀操作说明:
1、整个切换过程,必须在汽机“自动”控制方式下运行。
2、切换过程,可以投入“汽机主控”即在“遥控”方式下运行。
3、单阀切换至顺阀时,点击DEH控制画面“阀门方式”,点击“顺序阀”,然
后点击“转换”。
“SEQ”平光开始闪烁,切换开始。
4、切换过程中,#1、#2高调门同时逐步开大,#4高调门逐步关小。
整个过程
调门开度跟踪综合阀位的变化而调整。
5、切换结束时,#1、#2高调门开至100%、#3、#4依照阀位指令顺序开启。
“SEQ”显示平光,停止闪烁。
6、切换过程中,注意轴承温度和振动变化。
三、顺阀切换至单阀操作说明:
1、整个切换过程,必须在汽机“自动”控制方式下运行。
2、切换过程,可以投入“汽机主控”即在“遥控”方式下运行。
3、顺阀切换至单阀时,点击DEH控制画面“阀门方式”,点击“单阀”,然后点击“转换”。
“SIG”平光开始闪烁,切换开始。
4、切换过程中,#1、#2高调门同时逐步关小,#3、#4高调门逐步开启。
整个过程调门开度跟踪综合阀位的变化而调整。
5、切换结束时,四个调门开度基本一致。
“SIG”显示平光,停止闪烁。
6、切换过程中,注意轴承温度和振动变化。
单-顺序阀切换规定
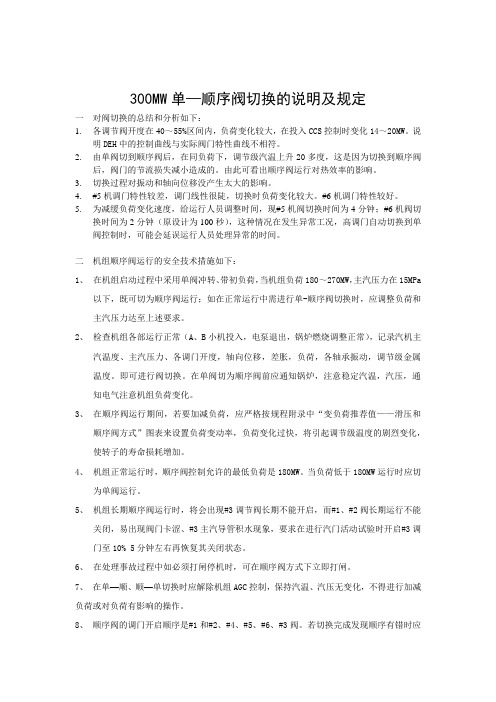
300MW单—顺序阀切换的说明及规定一对阀切换的总结和分析如下:1.各调节阀开度在40~55%区间内,负荷变化较大,在投入CCS控制时变化14~20MW。
说明DEH中的控制曲线与实际阀门特性曲线不相符。
2.由单阀切到顺序阀后,在同负荷下,调节级汽温上升20多度,这是因为切换到顺序阀后,阀门的节流损失减小造成的。
由此可看出顺序阀运行对热效率的影响。
3.切换过程对振动和轴向位移没产生太大的影响。
4.#5机调门特性较差,调门线性很陡,切换时负荷变化较大。
#6机调门特性较好。
5.为减缓负荷变化速度,给运行人员调整时间,现#5机阀切换时间为4分钟;#6机阀切换时间为2分钟(原设计为100秒),这种情况在发生异常工况,高调门自动切换到单阀控制时,可能会延误运行人员处理异常的时间。
二机组顺序阀运行的安全技术措施如下:1、在机组启动过程中采用单阀冲转、带初负荷,当机组负荷180~270MW,主汽压力在15MPa以下,既可切为顺序阀运行;如在正常运行中需进行单-顺序阀切换时,应调整负荷和主汽压力达至上述要求。
2、检查机组各部运行正常(A、B小机投入,电泵退出,锅炉燃烧调整正常),记录汽机主汽温度、主汽压力、各调门开度,轴向位移,差胀,负荷,各轴承振动,调节级金属温度。
即可进行阀切换。
在单阀切为顺序阀前应通知锅炉,注意稳定汽温,汽压,通知电气注意机组负荷变化。
3、在顺序阀运行期间,若要加减负荷,应严格按规程附录中“变负荷推荐值——滑压和顺序阀方式”图表来设置负荷变动率,负荷变化过快,将引起调节级温度的剧烈变化,使转子的寿命损耗增加。
4、机组正常运行时,顺序阀控制允许的最低负荷是180MW。
当负荷低于180MW运行时应切为单阀运行。
5、机组长期顺序阀运行时,将会出现#3调节阀长期不能开启,而#1、#2阀长期运行不能关闭,易出现阀门卡涩、#3主汽导管积水现象,要求在进行汽门活动试验时开启#3调门至10% 5分钟左右再恢复其关闭状态。
单阀顺序阀运行方式的切换

单阀、顺序阀运行方式的切换蒙映峰,罗 鹏,邓 涛(虹源发电有限公司,广西桂林 541003)[摘 要] 对桂林虹源发电有限公司135MW机组汽轮机的单阀、顺序阀切换过程进行了介绍,并对控制过程进行了分析。
结合现场数据,提出了进行切换的具体操作方法。
[关键词] 汽轮机;单阀运行;顺序阀运行;阀切换[中图分类号]T K263.7+2 [文献标识码]B [文章编号]10023364(2003)04003402 虹源发电有限公司装有2台上海汽轮机厂(上汽厂)生产的135MW凝汽式汽轮机,DCS系统是上海新华控制工程公司的XDPS400系统,DEH为上海FOXBOLO公司的IA’S系统,于2000年底投入试运行。
本文主要对自控系统进行单阀与顺序阀相互切换运行的操作方法予以介绍。
(1)单阀运行是指4个高压调门(亦称GV、高调门、调门)的开度基本保持一致,当负荷变化时,4个高压调门同时进行调节,至负荷稳定为止。
(2)顺序阀运行,分2种情况;1)在适当的负荷情况下,指有2个高压调门全开,1个高压调门全关,另1个则根据负荷的情况进行调节;2)当负荷量大,如承担调节任务的调门已全开,仍未满足负荷的需求时,全关的调门将开启,参与调节,至负荷稳定为止。
(3)采用单阀运行时,4个高压调门同步进行调节。
在这种方式下,将有4个调门产生节流损失。
而顺序阀运行时,由于2个高压调门全开,1个调门全关,另1个进行调节,则只有1个调门产生节流损失。
相比较而言,单阀运行的节流损失较大。
(4)根据厂家要求,汽轮机在刚投入运行时应采用单阀运行的方式;经过6个月左右的磨合期后,应采用顺序阀运行方式,以提高机组的经济性。
1 阀切换过程如图1所示,汽轮机的4个高调门为圆周布置,1号与2号对角,3号与4号对角。
单阀与顺序阀的切换过程如下。
图1 高调门布置示意(1)单阀切换至顺序阀。
操作员在DEH控制台上单击“阀门控制方式”、“顺序阀方式”再单击“投入”,则计算机开大GV1、GV2,同时,关GV4。
汽轮机顺序阀状态修正到单阀状态下的计算方法与流程

汽轮机顺序阀单阀状态下的修正方法与流程如果您是一名汽轮机工程师,那么您一定知道汽轮机顺序阀的重要性。
顺序阀的主要作用是控制汽轮机进气流量,从而维持机组的稳定运行。
但是,在汽轮机的顺序阀组中,往往会出现单个阀门状态被误判的情况,导致机组的性能受到损失。
研究表明,将汽轮机顺序阀状态修正到单阀状态下是解决这个问题的有效方法。
下面,我们将为您介绍汽轮机顺序阀状态修正到单阀状态下的计算方法与流程。
第一步:确定阀位规律首先,我们需要确定每个阀位的规律。
在顺序阀组中,不同阀位所对应的流量值不同,因此需要根据技术参数表和工作说明书,了解每个阀位所对应的流量大小。
同时,要对汽轮机的进气流量和出气流量进行测量,并将数据进行记录。
第二步:检测单个阀门状态在确定阀位规律的基础上,我们需要检测单个阀门的状态。
在实际工作中,顺序阀组中可能出现单个阀门状态被误判的现象。
这时,我们需要对该阀门进行详细的检测,以确定其实际状态。
第三步:修正阀位状态在确定单个阀门状态之后,我们需要对整个顺序阀组进行修正。
具体的修正方法是,将实际状态与阀位规律相比较,确定被误判阀门的实际状态,并将其所对应的阀位进行修正。
修正方式为增加或减少阀门的倾角,从而达到修正的目的。
第四步:再次检测顺序阀状态在对顺序阀状态进行修正之后,我们需要再次检测顺序阀状态,以确保修正效果达到预期。
具体的检测方法是,进行多次稳态工况下的实验,测量进气流量和出气流量,并记录实际数据。
通过比较实际数据与理论计算值,来确定修正后的顺序阀状态是否符合要求。
综上所述,汽轮机顺序阀状态修正到单阀状态下是一项需要技术和经验的工作。
通过以上的流程和方法,可以有效解决汽轮机顺序阀组中单个阀门状态被误判的问题,从而保证机组的正常稳定运行。
如何对汽轮机的进行单阀和顺序阀进行切换

•如何对汽轮机的进行单阀和顺序阀进行切换在实际的工作中,为了进一步提高汽轮机的使用效率,经常会需要对汽轮机进行单阀和顺序阀的切换,但是在操作的过程中,经常会发生各种各样的问题,因此本文就简单介绍如何对汽轮机进行单阀和顺序阀的切换。
单阀方式下,蒸汽通过高压调节阀和喷嘴室,在360°全周进入调节级动叶,调节级叶片加热均匀,有效地改善了调节级叶片的应力分配,使机组可以较快改变负荷;但由于所有调节阀均部分开启,节流损失较大。
假设阀门切换过程中汽机运行工况稳定,即真空和主蒸汽参数不变,不考虑抽汽的影响,汽机的负荷仅由蒸汽流量决定,而各个调节阀所控制的流量也只和阀门开度有关,那么可以认为汽机负荷进仅是阀门开度的单函数。
单阀系数乘以单阀开度指令与顺序阀系数乘以顺序阀开度指令相加后得到的就是各个阀门实际的开度指令。
单阀指令和顺序阀指令是当前负荷指令分别经过单阀曲线和顺序阀曲线转换后得出的。
在实际的阀门切换过程中,上述分析中的假设条件是难以成立的,所以不可避免地会有负荷扰动;但如果投入闭环控制,负荷扰动在一定程度上可以得到改善,即如果投入功率闭环回路,当实际功率与负荷设定值相差大于4%时,切换自动中止;当负荷调节精度达到3%以内时,切换又自动恢复。
投入调节级压力控制回路与此类似。
对于定压运行带基本负荷的工况,调节阀接近全开状态,这时节流调节和喷嘴调节的差别很小,单阀/顺序阀切换的意义不大。
对于滑压运行调峰的变负荷工况,部分负荷对应于部分压力,调节阀也近似于全开状态,这时阀门切换的意义也不大。
对于定压运行变负荷工况,在变负荷过程中希望用节流调节改善均热过程,而当均热完成后,又希望用喷嘴调节来改善机组效率,因此这种工况下要求运行方式采用单阀/顺序阀切换来实现两种调节方式的无扰切换。
电力工作者在实际的工作中,需要不断总结经验,掌握汽轮机单阀和顺序阀间切换的规律,保障汽轮机即高效又安全的运行。
汽轮机阀门控制的种类及功能

汽轮机阀门控制的种类及功能核心提示:汽轮机作为大型高速运转的原动机是当今火力发电厂的主要设备之一,它被用来拖动发电机从而使机械能转变为电能,供用户使用。
1、汽轮机阀门控制种类汽轮机作为大型高速运转的原动机是当今火力发电厂的主要设备之一,它被用来拖动发电机从而使机械能转变为电能,供用户使用。
汽轮机具有体积大、旋转快等特点。
当它由常温常压的静止状态下转入高温高压高速运行时,汽轮机的调节阀门起到了稳定转速、控制负荷的关键作用。
只有控制好阀门的稳定性、快速性和精确度,才能使汽轮机安全、平稳、高效的运行。
数字式电液调节(DEH)系统作为目前汽轮机的最基本的控制系统,是对阀门进行控制的最佳系统。
在这个系统中对阀门的控制有两种方式:单阀控制方式和多阀控制方式,两种方式之间可以进行无扰切换。
单阀控制是指在汽轮机的高压缸进汽时采用各个高压调节阀门同时进汽的方式,也就是说各个高压调节阀门的指令和开度都是一样的。
多阀控制是指在汽轮机的高压缸进汽时采用单个高压调节阀门逐步进汽的方式,也就是说各个高压调节阀门的指令和开度都是不一样的,每个高压调节阀门的开度是根据自身的流量曲线对应的指令输出的。
2、阀门控制的功能DEH控制系统中调节阀门的开度指令,实际上是由阀门控制输出的,而阀门控制所接收的信号是系统对进入汽轮机的总蒸汽流量的请求,即DEH系统的转速控制回路和负荷控制回路中所产生的流量给定值信号是通过阀门控制转换为各阀门的开度指令信号的。
这个给定信号输出到阀门控制卡(伺服卡)上与阀位传感器(LVDT)的实际阀位信号相减,经过伺服放大器放大后控制伺服阀达到要求开度。
因此,阀门控制实际上是一软件动态函数发生器,它的主要任务是:(1)当机组在单阀调节或多阀调节方式下运行时,阀门控制根据DEH系统提供的流量给定信号,通过阀门流量曲线确定各调节阀的开度,并以输出模拟信号;(2)保证在单阀调节和多阀调节相互切换的过程中,机组的功率始终保持不变;(3)在阀门进行切换的过程中,如果流量请求发生变化,将停止正在进行的阀门切换,先满足机组对流量的要求,然后再继续进行阀门的切换;(4)保证DEH系统能平稳地从手动方式切换到自动方式。
- 1、下载文档前请自行甄别文档内容的完整性,平台不提供额外的编辑、内容补充、找答案等附加服务。
- 2、"仅部分预览"的文档,不可在线预览部分如存在完整性等问题,可反馈申请退款(可完整预览的文档不适用该条件!)。
- 3、如文档侵犯您的权益,请联系客服反馈,我们会尽快为您处理(人工客服工作时间:9:00-18:30)。
单阀和顺序阀的对比1、单阀控制方式即所有进入汽轮机的蒸汽都经过几个同时启闭的调节阀后进入第一级喷嘴,也称节流配汽方式。
节流配汽的汽轮机在工况变动时第一级的进汽度是不变的,因此可以把包括第一级在内的全部级作为级组,也就是说除了工作原理不同外,调节级与其余各级并无其他区别。
采用节流配汽的汽轮机在设计工况下调节阀全开,机组的理想焓降到最大值;低负荷时调节阀关小,减少汽轮机的进汽量,主蒸汽受到节流作用使第一级级前压力下降,其值与蒸汽流量成正比。
此时,汽轮机的理想焓降减小但并不是很多,可见节流配汽主要是通过减少蒸汽流量来降低负荷。
当然,理想焓降的减少虽然不是很多,但仍然使机组的相对内效率降低,且负荷越低,节流损失越大,机组效率也就越低。
因此,节流配汽方式的应用范围不太广泛,一般用于小功率机组和带基本负荷的机组。
高参数、大容量机组在启动初期为使进汽部分的温度分布均匀,在负荷突变时不致引起过大的热应力和热变形,也经常使用节流配汽方式。
2、顺序阀控制方式即蒸汽经过几个依次启闭的调节阀后再通向第一级喷嘴,也称喷嘴配汽方式。
这种配汽方式在运行当中只有一个调节阀处于部分开启状态,而其余的调节阀均处于全开(或全关)状态,蒸汽只在部分开启的调节阀中受到节流作用,因此,在部分负荷时喷嘴配汽方式比节流配汽方式效率高,所以被广泛应用。
采用喷嘴配汽方式时,第一级喷嘴的通流面积随着调节阀的开启数目不同而变化。
调节级的变工况特性也和其余各级有很大区别。
当调节级通流面积改变时,蒸汽流量将发生变化,达到调节机组负荷的目的。
同时,在部分开启的调节阀中蒸汽流量受到节流作用,改变了理想焓降,但因流经该阀的蒸汽流量只占总流量的一部分,因此蒸汽焓降的改变对机组功率的影响较小。
采用喷嘴配汽方式时,在第一只调节阀刚刚全开时调节级的压力比为最小,调节级的理想焓降为最大,此时,通过第一组喷嘴的蒸汽流量也达到最大值,故第一组喷嘴蒸汽流量和焓降的乘积也达到最大值,工作在其后的动叶片所承受的应力也达到最大值。
可见,调节级的危险工况并不是在最大工况下,而是在第一只调节阀刚刚全开时。
3、单阀、顺序阀控制方式的应用实际生产中,汽轮机在部分负荷下运行时喷嘴配汽方式比节流配汽方式的效率高,且较稳定。
但在变工况下采用喷嘴配汽方式会使汽轮机高压部分的金属温度变化较大,调节级所对应的汽缸壁产生较大的热应力,从而降低了机组快速改变负荷的能力。
为了发挥两种不同配汽方式的优点,我们采取了节流配汽——喷嘴配汽联合调节的方式,即第一只喷嘴和第二只喷嘴同时开启,使汽缸均匀受热。
待第一、二只调节阀全开后再根据机组负荷需要依次开启其他调节阀。
这样,就同时发挥了节流配汽和喷嘴配汽两者的优点。
电厂汽轮机单阀/顺序阀切换的实现作者:时间:2010 年2 月电厂汽轮机单阀/顺序阀切换的实现摘要:汽轮机单阀/顺序阀切换的逻辑,是电厂节能降耗的手段之一,本文主要针对汽轮机的单阀/顺序阀切换逻辑的分析、存在问题的提出、分析以及解决过程,及切换功能的实现进行全过程论述。
关键词:单阀顺序阀切换逻辑一.概述“十一五”规划明确要求,到2010年我国单位GDP的能耗要比“十五”末期下降20%,衡量一个发电厂经济性的好坏,就是要看它的综合指标——发电成本,即对外供1度电所需的成本费用。
火力发电厂汽轮机作为能量转换的中间设备,运行方式的优化是节能降耗的主要手段,对保证机组的安全性和经济性起到关键作用。
**发电厂隶属**,电厂的主要设备是:锅炉采用**锅炉厂高温超高压一次中间再热、单汽包自然循环、****蒸汽锅炉(YG—***/13.74—M),汽轮机采用**汽轮机厂的超高压、单轴、双缸双排汽、一次中间再热、凝汽式汽轮机(N***—**.24/***/***型),发电机是**发电设备厂的WX**Z-073LLT。
热控系统主网主要采用DCS集散控制方式,辅网采用PLC控制系统。
汽轮机采用DEH控制方式,DEH控制系统为纯电调系统,整套系统采用北京ABB贝利控制有限公司的Symphony控制系统(软硬件由北京ABB贝利控制有限公司提供),液压部分采用常规低压透平油系统。
直接由DEH通过电液转换器进行控制调节汽阀油动机,以达到控制汽机转速和负荷的目的。
**积极响应国家的节能降耗的政策,立足于本厂实际,多方面、全方位的实施全厂的节能降耗各项工作。
本文重点介绍汽轮机单阀/顺序阀切换功能的实现。
所谓汽机单阀控制方式,是指根据负荷的给定值,经过汽机阀门管理程序的逻辑判断,所有高压调门开启方式相同,且各高调门的开度均一致。
因控制汽阀沿汽轮机的径向对称布置,因此这种方式将使汽轮机的高压缸第一级汽室内温度的分布比较均匀,在负荷变化时汽轮机的转子和定子之间的温差最小,减少了机组的热应力,使机组可以承受较大的符合变化率。
但是,从机组的运行经济上看,由于所有控制汽门都处于非全开状态,因而主蒸汽通过控制汽门的节流损失较大,降低了机组的热效率。
顺序阀控制方式,是指根据负荷的给定值,经过汽机阀门管理程序的逻辑判断和计算,按照预先设定的开启顺序开启相应的高压调节阀,各高调门累计流量呈线性变化。
这种控制方式只有一个汽阀处于半开启状态,其他的汽门处于全开或全关状态。
这样就减少了汽门的节流损失,提高了汽机的热效率。
但是存在进汽位置不对称,第一级汽室内的温度分布不均匀,机组的热应力较大,因此承担的符合变化率相对来说比较小。
两种控制方式各有优缺点,机组在不同的运行状态时应采用不同的控制方式。
一般机组冷态启动以及机组在承担尖峰负荷时,要求采用全周进汽,即单阀控制方式;机组带部分符合运行时,可以采用部分进汽方式,即顺序阀控制方式。
二、单阀/顺序阀切换的控制逻辑分析我厂汽轮机共有四只高压调节阀,编号为GV1、GV2、GV3以及GV4。
每只高调门均有一个独立的伺服控制回路。
信号的传递通道为:运行人员设定目标负荷设定值及速率,这两种信号到汽机负荷控制回路,得到GVMOUT信号,即设定负荷时作对应的调门开度总的叠加值。
GVMOUT信号到阀门管理回路,经过相应的逻辑计算和判断,送到DEH的I/O端子板,然后通过内部连接电缆到SVP 调门卡,SVP调门卡将阀位输出指令以及LVDT(线性位移差动传感器)的反馈信号进行对比计算,得到0~10V DC指令,经过中间端子盒到电液转换器进行调节。
信号的传递框图如下所示:阀门管理的基本功能框图如下所示:汽机的单阀/顺序阀之间的切换的允许条件反映在内部逻辑中,主要有以下几个方面:(1)、DEH控制系统处于“AUTO”控制方式。
自动控制方式是通过CRT画面操作,改变转速/负荷设定值,对DEH输出进行闭环控制(2)、安全油压建立,汽机已复位挂闸(3)、主油开关闭合,是指我厂发变组220KV断路器处于合闸位置。
(4)、系统不在ADS控制方式。
(5)、高压调门不在“试验”位。
(6)、中压调门不在“试验”位。
(7)、主汽门试验不在“试验”位。
(8)、单/顺阀切换状态按钮投入。
内部标签名为“Transfer”,是在单阀/顺序阀切换前需要将切换状态置“1”,信号类型是一种5秒触发延时的单脉冲定时器。
(9)、单/顺阀切换指令给出。
内部标签名是顺序阀“SEQ INPB”,单阀“SIG INPB”。
当此信号为逻辑“1”时,与“Transfer”信号进行“与”逻辑判断,得到切换指令,指令信号为3秒触发延时的单脉冲,因此,操作顺序必须是先将状态按钮置“1”状态,5秒内给出阀切换指令信号。
输出到阀门管理程序中(如简图所示)。
顺序阀指令切换状态单阀指令“SEQPB”或“SIGPB”信号到阀门管理程序内,还得经过二次判断,如果切换条件全部允许,则输出阀切换指令,若以上条件任一条件不满足,阀门控制则仍处于原控制方式。
然后,需要分析汽机高调门的阀门特性曲线。
GVMOUT的函数运算关系是:高调门1的阀门特性曲线:高调门2的阀门特性曲线:高调门3的阀门特性曲线:高调门4的阀门特性曲线根据高调门的特性曲线可以看出:GV1与GV2的阀门特性一致,GV3与GV4的特性一致。
并且,GV3与GV4在阀门逐渐开启的过程中的进汽流量要比其他两个高调门要高些。
GV1与GV2在0%~72.28%时,曲线接近于线性关系。
在进行阀门方式切换时,为了保证机组功率及主汽压力不会发生大范围内的波动,必须保证DEH算法逻辑的合理性。
以GV1为例,我厂的逻辑计算可以写成如下算法:GV1SPT=(GVMOUT`*A+GVMOUT`*B)F(GV1)其中,GV1SPT:#1高压调节门输出指令,%;GVMOUT:经过阀门管理程序的计算得到的总的阀门开度指令,%;A:在单阀控制方式下指令系数,0~1;B:在顺序阀控制方式下的指令系数,0~1;):#1高压调节门的阀门特性函数,%。
F(GV1当阀位控制方式处于单阀控制方式时,A=1,B=0;当顺序阀控制方式下时,A=0,B=1;两者之间的切换时,将受到速率限制器的作用,速率设置为0.05/秒,按照以上速率计算,0和1之间的切换时间应该为20秒左右。
因此,切换过程中不会引起负荷及主汽压力大范围内的波动。
按照以上所述,热工人员进行了切换演算:根据135MW时的数据,GVMOUT=95.874,GV1开度是43.15;GV2开度是43.15;GV3开度是49.25;GV4开度是49.25。
假设此时将阀位控制方式切成顺序阀,切换瞬间为无扰切换。
由于功能码FC8限速器的作用,高调门逐渐下降,直至内部运算值为3.42,经过阀门特性曲线的分段线性函数块,最终GV1的开度将在15%稳定住;GV2开度28%;GV3开度100%,GV4开度100%。
假设此时要求负荷下降,GVMOUT开度下降至80,则F(x)=65.45,阀位控制仍在顺序阀控制方式,则会出现GV1全关,GV2开度18.8%,GV3全开,GV4全开。
假设机组满负荷运行,GVMOUT=95.874,阀位管理方式为顺序阀控制,这时切换成单阀控制,则F(x)=91.307,切换瞬间,阀位值不变,为无扰切换,切换后,功能码FC8限速器的值由顺序阀时的0逐渐增加到1,速率限制为0.05/秒,这时阀位内部计算值由-1逐渐变化成0,阀位值慢慢增加至91.307,完成单阀时的阀位控制。
经过以上推算,我们得到以下结论:1、汽机单阀/顺序阀之间的切换为无扰切换,即切换过程中不会出现阀位瞬大范围的开关现象。
2、切换后,在保证汽机实际阀位-流量特性曲线与出厂设定曲线一致的情况下,汽机调门瞬时变化幅度较小,能够稳定在一个特定的阀位值上。
3、由于阀门重叠度的设置,开启顺序应该为4-3-2-1。
即:100%GV4-3单/顺阀切换GV1GV2100%蒸汽流量指令到此,阀切换之间的软件部分已经具备条件,汽机硬件方面的问题需要热工专业及汽机专业进行确认。