全裁工序质量标准
裁剪验片检验标准
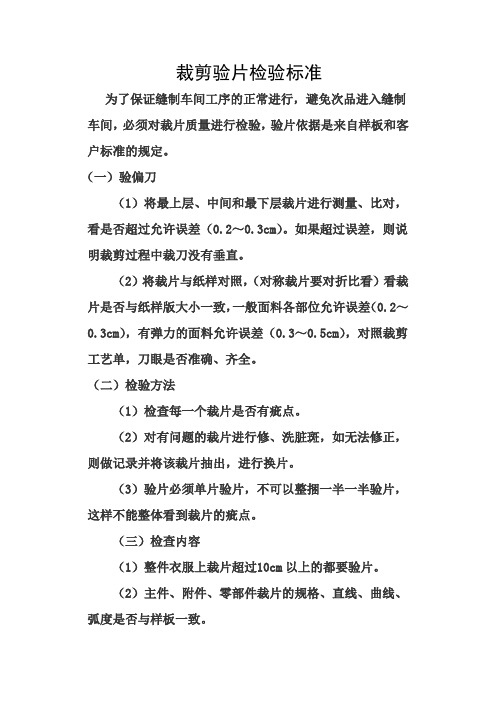
裁剪验片检验标准为了保证缝制车间工序的正常进行,避免次品进入缝制车间,必须对裁片质量进行检验,验片依据是来自样板和客户标准的规定。
(一)验偏刀(1)将最上层、中间和最下层裁片进行测量、比对,看是否超过允许误差(0.2~0.3cm)。
如果超过误差,则说明裁剪过程中裁刀没有垂直。
(2)将裁片与纸样对照,(对称裁片要对折比看)看裁片是否与纸样版大小一致,一般面料各部位允许误差(0.2~0.3cm),有弹力的面料允许误差(0.3~0.5cm),对照裁剪工艺单,刀眼是否准确、齐全。
(二)检验方法(1)检查每一个裁片是否有疵点。
(2)对有问题的裁片进行修、洗脏斑,如无法修正,则做记录并将该裁片抽出,进行换片。
(3)验片必须单片验片,不可以整捆一半一半验片,这样不能整体看到裁片的疵点。
(三)检查内容(1)整件衣服上裁片超过10cm以上的都要验片。
(2)主件、附件、零部件裁片的规格、直线、曲线、弧度是否与样板一致。
(3)裁片的疵点、色差、经纬丝缕是否符合质量标准。
(4)各定位标记是否准确。
(5)上下裁片相比,各层裁片误差是否超过规定标准。
(6)刀口、定位孔的位置是否准确,有无漏裁。
(7)对格、对花是否准确。
(8)裁片边缘是否光滑圆顺。
(9)左右对称片必须对合验片,以防纬斜、开刀走位造成大小不一。
二、换片(1)每卷面料的余料要做上缸号、床次、层次的记号,避免换片的出现颜色色差。
(2)换片时要根据每床裁片所对应的每卷面料的余料进行换片。
(3)换片时一定要看面料的丝缕与纸样的丝缕一致,相对应的尺码、大小要与纸样版一致,如要对格、对花型的要根据要求进行换片。
三、每天做好《验片记录表》。
服装裁剪车间质量管理控制规范

服装裁剪车间质量管理控制规范一、引言随着服装行业的快速发展,质量管理对于服装裁剪车间来说至关重要。
合理的质量管理控制规范是保证产品质量、提高生产效率以及增强企业竞争力的关键。
本文将介绍服装裁剪车间质量管理控制规范的重要性,并提供一些建议和方法来帮助车间实施有效的质量管理控制。
二、质量管理的重要性1. 客户满意度高质量的服装产品能够满足客户的需求和期望,提高客户满意度。
客户的满意度不仅能够带来重复购买,还能够增加口碑传播,对于企业的长期发展至关重要。
2. 生产效率通过建立良好的质量管理控制规范,车间能够减少次品率,降低废品损失,提高生产效率。
高效率的生产流程能够节约时间和成本,提高生产能力,使企业更具竞争力。
3. 品牌形象优秀的质量管理控制规范能够帮助企业树立良好的品牌形象。
通过不断提升产品质量,企业能够赢得消费者的认可和信赖,形成品牌忠诚度,提升企业的市场竞争力。
三、质量管理控制规范建议1. 设立质量目标车间应该制定明确的质量目标,并将其传达给所以员工。
质量目标应该具体、可衡量,并与企业战略目标相一致。
定期评估和跟踪质量目标的实现情况,并根据需要进行调整和改进。
2. 全员参与有效的质量管理需要全员参与。
车间应该建立一个团队合作的工作氛围,鼓励员工积极参与质量管理活动。
培训员工相关知识和技能,提升他们对产品质量的认知和重视。
3. 建立标准操作程序(SOP)车间应该制定并实施标准操作程序(SOP),确保每个工序按照规范进行操作。
SOP应该包括正确的工艺流程、操作规定、工序检查和记录要求等内容。
定期审查和更新SOP,确保其与实际生产相符。
4. 精益生产精益生产是一种以减少浪费和提高价值为核心的管理理念。
车间应该采用精益生产的原则,消除生产过程中的浪费和不必要的环节。
例如,通过优化布局、调整工序顺序、合理分配人员和资源等方式,提高生产效率和质量。
5. 建立质量检测和反馈机制车间应该建立完善的质量检测和反馈机制。
全裁工序质量标准
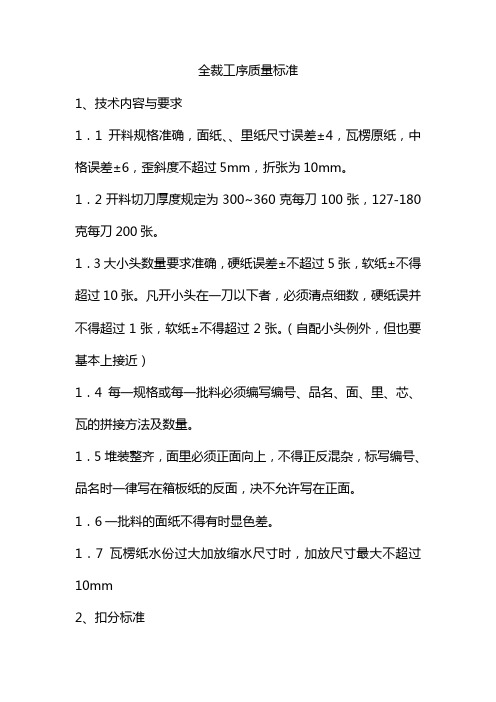
全裁工序质量标准
1、技术内容与要求
1.1开料规格准确,面纸、、里纸尺寸误差±4,瓦楞原纸,中格误差±6,歪斜度不超过5mm,折张为10mm。
1.2开料切刀厚度规定为300~360克每刀100张,127-180克每刀200张。
1.3大小头数量要求准确,硬纸误差±不超过5张,软纸±不得超过10张。
凡开小头在一刀以下者,必须清点细数,硬纸误并不得超过1张,软纸±不得超过2张。
(自配小头例外,但也要基本上接近)
1.4每一规格或每一批料必须编写编号、品名、面、里、芯、瓦的拼接方法及数量。
1.5堆装整齐,面里必须正面向上,不得正反混杂,标写编号、品名时一律写在箱板纸的反面,决不允许写在正面。
1.6一批料的面纸不得有时显色差。
1.7瓦楞纸水份过大加放缩水尺寸时,加放尺寸最大不超过10mm
2、扣分标准
2.1规格误差每超±1mm扣1分。
2.2歪斜度超标准±1mm扣1分。
2.3数量误差±1刀扣2分。
2.4堆装不齐每垛扣1分。
2.5左右面误差10张以每张扣1分。
2.6拼法写错每次扣1分。
2.7大小头多缺,折合成大张,每5张扣1分(利用纸边修例外)。
2.8一批料中的面纸有时显色差,每张扣1分。
凡因质量问题,使该产品无法补救,造成损失的均视为质量事故,构成质量事故的,按有关事故处理规定另行处理。
缝纫质量控制步骤
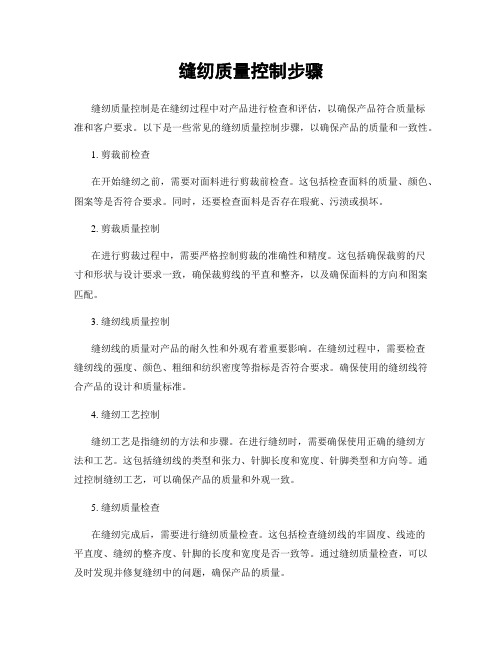
缝纫质量控制步骤缝纫质量控制是在缝纫过程中对产品进行检查和评估,以确保产品符合质量标准和客户要求。
以下是一些常见的缝纫质量控制步骤,以确保产品的质量和一致性。
1. 剪裁前检查在开始缝纫之前,需要对面料进行剪裁前检查。
这包括检查面料的质量、颜色、图案等是否符合要求。
同时,还要检查面料是否存在瑕疵、污渍或损坏。
2. 剪裁质量控制在进行剪裁过程中,需要严格控制剪裁的准确性和精度。
这包括确保裁剪的尺寸和形状与设计要求一致,确保裁剪线的平直和整齐,以及确保面料的方向和图案匹配。
3. 缝纫线质量控制缝纫线的质量对产品的耐久性和外观有着重要影响。
在缝纫过程中,需要检查缝纫线的强度、颜色、粗细和纺织密度等指标是否符合要求。
确保使用的缝纫线符合产品的设计和质量标准。
4. 缝纫工艺控制缝纫工艺是指缝纫的方法和步骤。
在进行缝纫时,需要确保使用正确的缝纫方法和工艺。
这包括缝纫线的类型和张力、针脚长度和宽度、针脚类型和方向等。
通过控制缝纫工艺,可以确保产品的质量和外观一致。
5. 缝纫质量检查在缝纫完成后,需要进行缝纫质量检查。
这包括检查缝纫线的牢固度、线迹的平直度、缝纫的整齐度、针脚的长度和宽度是否一致等。
通过缝纫质量检查,可以及时发现并修复缝纫中的问题,确保产品的质量。
6. 细节质量控制除了常规的缝纫质量控制,还需要对产品的细节进行质量控制。
这包括检查纽扣的固定度、拉链的顺畅度、袋口的对称性、装饰物的粘贴牢固度等。
确保产品的细节符合设计要求,达到客户的期望。
7. 最终质量检查在所有缝纫工序完成后,需要进行最终质量检查。
这包括对整个产品进行全面检查,确保产品的质量和外观符合要求。
同时,还需要检查产品的标签、包装和配件等是否齐全和正确。
8. 记录和反馈在缝纫质量控制过程中,需要及时记录和反馈问题。
这包括记录缝纫过程中的问题和不良品数量,以及采取的纠正措施和改进措施。
通过记录和反馈,可以及时发现并解决质量问题,提高产品的质量和一致性。
家具生产各工序工艺品质标准(图片)
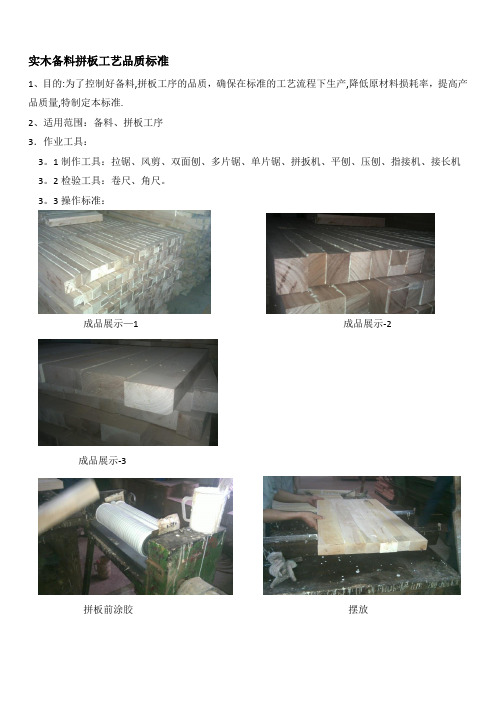
实木备料拼板工艺品质标准1、目的:为了控制好备料,拼板工序的品质,确保在标准的工艺流程下生产,降低原材料损耗率,提高产品质量,特制定本标准.2、适用范围:备料、拼板工序3.作业工具:3。
1制作工具:拉锯、风剪、双面刨、多片锯、单片锯、拼扳机、平刨、压刨、指接机、接长机3。
2检验工具:卷尺、角尺。
3。
3操作标准:成品展示—1 成品展示-2成品展示-3拼板前涂胶摆放固定成型3.4拼板前期准备:断料(下料)修边机双面刨4.品质工艺要求:4.1按照生产技术部门指定的图纸规格尺寸、数量、质量要求,根据板材的长度、宽度及厚度合理搭配用材。
4。
2面料选用树种统一、颜色接近、无虫眼、无死节、无油眼、无爆裂、无腐朽、无钝棱、无红、黑树芯的木材,含水率12%以下,按材质好坏。
分为面料、垫料、填芯料及颜色要求的筛选。
不符合用料要求及标准的材料不予加工。
垫料选用不能做面料的材料,填芯料选用不能做垫料的材料.锯路要求平面、光滑、角度正常。
4.3拼板料的拼接面要求平整光滑、底面与拼接面要成直角,不允许有不同木材、颜色、木质、木纹方向的料拼成一个整体,相邻两块板料的湿度不超过2%.同一块拼板料中,料与料之间厚度差不得超过2MM,长度差不得超过3MM.4.4拼缝线的宽度不允许超过0.2MM,涂胶量且要双面,涂抹均匀不得单面厚凃,以加压有均匀胶水刚挤出为宜。
4。
5常规替代材料:胡桃木使用楸木、桦桃木(需要擦底色)樱桃木使用桦桃木、赤杨,黄杨实木椅类用橡胶木橡木使用白栓木4.6封边实木代替:奥古曼、椴木、赤杨、黄杨4。
7硬木类(水曲柳、桦木、橡胶木等)加压压力要求12—15kg/cm2,软木类(奥古曼、黄杨、赤杨等)加压压力要求8—12kg/ cm2加压3小时以上(25度以上)卸压8小时后才可进行二次深加工。
4。
8所有须经车枳和雕刻的台脚或立柱不允许拼松软木质,以免在车床因紧固松紧程度不同影响工艺线大小不一致或因木质松软无法加工。
切裁工序质量控制标准
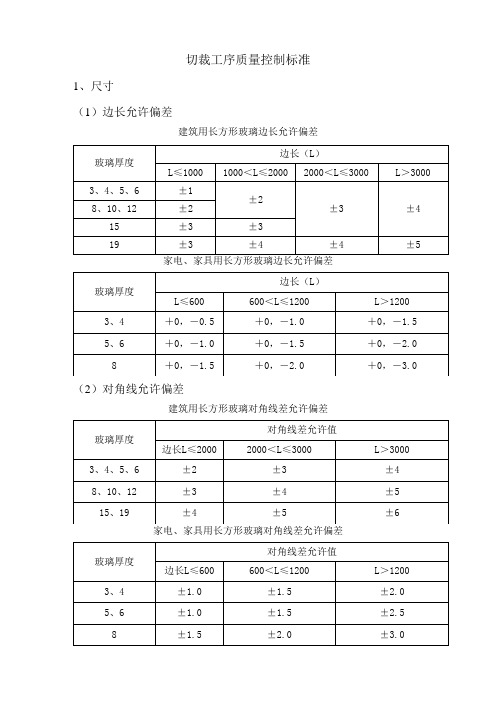
建筑中空用:长度不超过10mm,自边部向内延伸不超过订单要求纯胶深值,深度不超过玻璃厚度1/3的崩边,允许有1个。
非中空用:普通玻璃边部长度不超过5mm,自边部向内延伸不超过2mm,深度不超过玻璃厚度1/3的崩边,允许有1个。
划伤
宽度在0.1mm以下的轻微划伤,长度小于50mm的,每平方米面积内允许有4条;
订单有特殊要求时,以订单要求为准。
(3)原片厚度偏差
玻璃公称厚度
厚度偏差
厚薄差
2~6
±0.2
0.2
8~12
±0.3
0.3
15
±0.5
0.5
19
±0.7
0.7
(注:厚薄差是指玻璃测量厚度最大值和最小值之差。)
2、外观质量
缺陷名称
缺陷描述及允许缺陷数
崩边
家电:使用时装有边框的玻璃,边部长度不超过3mm,自边部向内延伸不超过2mm,深度不超过玻璃厚度1/3的崩边,允许有1个;
600<L≤1200
L>1200
3、4
+0,-0.5
+0,-1.0
+0,-1.5
5、6
+0,-1.0
+0,-1.5
+0,-2.0
8
+0,-1.5
+0,-2.0
+0,-3.0
(2)对角线允许偏差
建筑用长方形玻璃对角线差允许偏差
玻璃厚度
对角线差允许值
边长L≤2000
2000<L≤3000
L>3000
3、4、5、6
±2
±3
±4
8、10、12
±3
±4
±5
15、19
±4
±5
±6
板式家具工序质量标准及其检验标准规范

电子锯、台锯须经培训合格,熟练掌握设备操作、性能、安全防护措施和注意事项。
1、板料1) 板件中间严重分层开裂,涂胶面贴合面不密切,凹凸不平,粘压移位等板件不可投入本工序生产。
2) 饰面板面纸起皱、严重刮伤、纸与板面分层、纸纹方向不正确的板件不可投入本工序生产。
2、对来件每20 件抽检2-4 件,发现不良品,再次抽检,发现有10%以上不良品,退回上工序全检,问题严重时,应填写《产品质量事故报告单》向上汇报。
1 、所开板件须与图纸开料单和有关技术参数中规格、纹路颜色一致。
2、产品板件锯(切)面须平直、平整、光滑并与板面成直角90°,加工面无黑边、无爆边、无分层、无开裂、无脱纸、无气泡、无明显崩口现象.3、板件切(锯)面锯齿痕允许在0.1mm 内、锯面斜度≤1º。
1、各种规格、位置必须符合图纸和有关技术参数误差≤0.5mm 要求。
2 、要求拉槽无崩裂、烂纸、顺畅、平整光滑。
3、深度误差比图纸尺寸深0.5mm,宽度允许比图纸尺寸宽0.2mm,不能超过0.3mm。
1 、所有加工板件不能直接接触地面,要求叠放在地台板。
2 、堆叠板面(特殊注意双面板)叠面不能有任何易刮(划)伤表面的硬残存物,要使用纸条隔开,严禁贴纸面与面直接堆叠,以免板面与板面互刮。
3 、产品(板件)要求不能堆(停)放在易受潮的地方。
品检责任人:质检首件确认与巡检、作业员全数自检。
编制/日期:王红平/2022-4- 10 审核/日期:核准/日期:开料工序每批的第 1 件(块)板件每生产 10-30 件每生产 50-100 件每 20 件中间每 50 件之间1 件2—6 件6—8 件2—4 件6—8 件质检员操作者质检员操作者质检员检验工具:图纸(料单)、卷尺、角尺检验方法:工具测量、目视开料质量标准来料或者加工未达工艺图纸要求检验数量内,不良率超 10%检验中发现有一个或者一个以上的不良品时由操作者按图纸要求自检无误后方可批量生产。
产品质量标准.pdf
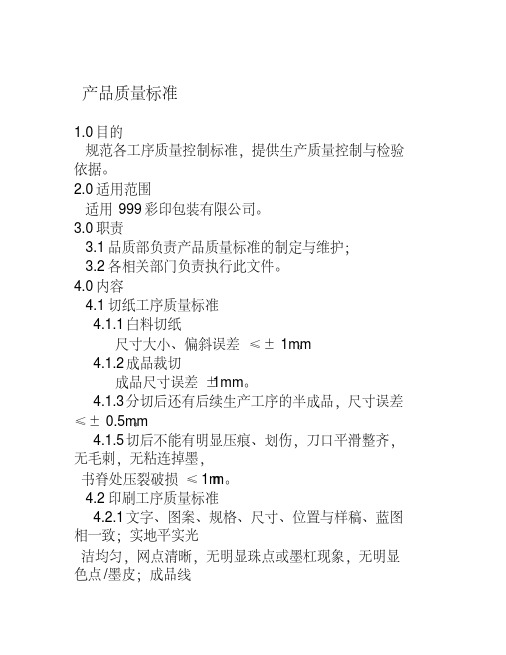
产品质量标准1.0目的规范各工序质量控制标准,提供生产质量控制与检验依据。
2.0 适用范围适用999彩印包装有限公司。
3.0 职责3.1 品质部负责产品质量标准的制定与维护;3.2 各相关部门负责执行此文件。
4.0 内容4.1 切纸工序质量标准4.1.1 白料切纸尺寸大小、偏斜误差≤±1mm。
4.1.2 成品裁切成品尺寸误差±1mm。
4.1.3 分切后还有后续生产工序的半成品,尺寸误差≤±0.5mm。
4.1.5 切后不能有明显压痕、划伤,刀口平滑整齐,无毛刺,无粘连掉墨,书脊处压裂破损≤1m m。
4.2 印刷工序质量标准4.2.1 文字、图案、规格、尺寸、位置与样稿、蓝图相一致;实地平实光洁均匀,网点清晰,无明显珠点或墨杠现象,无明显色点/墨皮;成品线以内不得有与内容无关的文字、野线,无明显擦花、刮花、水干、水大、脏污及过油喷粉不匀等不良现象。
4.2.2 印刷针位、拉规、班号、色标必须齐全一致,套印准确,套印误差≤0.5mm。
4.2.3 印刷色相严格按样生产,用SP60分光密度仪检测,同批同色色差范围在△E≤3.5以内。
4.2.4 印刷产品墨层及光泽度目测与样稿无明显差异,耐磨擦次数≥50次;金卡纸产品(不覆膜)试啤成型后对折无爆墨及掉墨现象。
4.3.5 防伪印刷产品必须符合特定防伪要求:在正常光源下,用40瓦紫光灯检测时,产品距离紫光灯20cm左右,图文变色清晰、不残缺、不糊板、不粘花、无水干、无野墨点。
4.3.6 条形码检测,数字显示核对无误,条码释读≥D级。
4.4 过油工序质量标准4.4.1油层均匀、干透,无刺激性气味。
4.4.2 光泽度效果达到样稿要求,无明显偏色;表面光洁,无起皱、发白、起泡、粘花、脏污或其它不良现象,背面无油渍。
4.4.3 糊盒产品,过油边到糊盒位压痕线的距离≤3MM。
4.4.4 过油后产品表面耐磨擦次数≥100次。
4.5 覆膜工序质量标准4.5.1 覆膜平整、均匀、到位,光泽度达到样稿要求,无明显偏色。
- 1、下载文档前请自行甄别文档内容的完整性,平台不提供额外的编辑、内容补充、找答案等附加服务。
- 2、"仅部分预览"的文档,不可在线预览部分如存在完整性等问题,可反馈申请退款(可完整预览的文档不适用该条件!)。
- 3、如文档侵犯您的权益,请联系客服反馈,我们会尽快为您处理(人工客服工作时间:9:00-18:30)。
全裁工序质量标准
1、技术内容与要求
1.1开料规格准确,面纸、、里纸尺寸误差±4,瓦楞原纸,中格误差±6,歪斜度不超过5mm,折张为10mm。
1.2开料切刀厚度规定为300~360克每刀100张,127-180克每刀200张。
1.3大小头数量要求准确,硬纸误差±不超过5张,软纸±不得超过10张。
凡开小头在一刀以下者,必须清点细数,硬纸误并不得超过1张,软纸±不得超过2张。
(自配小头例外,但也要差不多上接近)
1.4每一规格或每一批料必须编写编号、品名、面、里、芯、瓦的拼接方法及数量。
1.5堆装整齐,面里必须正面向上,不得正反混杂,标写编号、品名时一律写在箱板纸的反面,决不承诺写在正面。
1.6一批料的面纸不得有时显色差。
1.7瓦楞纸水份过大加放缩水尺寸时,加放尺寸最大不超过10mm
2、扣分标准
2.1规格误差每超±1mm扣1分。
2.2歪斜度超标准±1mm扣1分。
2.3数量误差±1刀扣2分。
2.4堆装不齐每垛扣1分。
2.5左右面误差10张以每张扣1分。
2.6拼法写错每次扣1分。
2.7大小头多缺,折合成大张,每5张扣1分(利用纸边修例外)。
2.8一批料中的面纸有时显色差,每张扣1分。
凡因质量问题,使该产品无法补救,造成缺失的均视为质量事故,构成质量事故的,按有关事故处理规定另行处理。