多晶硅还原反应的影响因素
多晶硅质量影响因素的探索

多晶硅质量影响因素的探索摘要:在三氯氢硅加氢还原生产多晶硅过程中,影响产品品质的因素有:三氯氢硅提纯、三氯氢硅加氢还原和外来杂质等。
多晶硅分析要求精度高而分析方法中存在不足,建议从整个多晶硅生产工艺来分析和判断多晶硅杂质产生的原因。
关键词:多晶硅;氢气;三氯氢硅;质量影响;因素;三氯氢硅(SiHCl3)加氢还原生产多晶硅是要求纯度高且工艺复杂的过程,中间每一个环节稍有不慎就可能造成最终产品质量下降。
从整个工艺进行分析判断,影响多晶硅质量的主要因素有:SiHCl3提纯、SiHCl3加氢还原和外来杂质等;其中,受主杂质主要来自SiHCl3提纯料,而施主杂质和碳杂质主要来自SiHCl3加氢还原工序。
一还原法制备多晶硅工艺经精馏塔提纯的SiHCl3,按还原工艺条件的要求,经316L不锈钢管道连续加入到蒸发器。
经尾气回收系统回收的氢气与来自制氢系统的补充氢气在管道中汇合后进入蒸发器,使蒸发器中的SiHCl3液体在一定的温度和压力下鼓泡蒸发,形成一定配比的氢气和SiHCl3气体沿着管道进入还原炉,在表面温度达1100℃的硅芯热载体上反应,多晶硅在载体上沉积,同时生成HCl、SiH,Cl,、SiCl。
气体等,未反应的氢气和SiHCl3气体排出还原炉,沿管道进入尾气回收系统,经冷凝一分离一冷凝的氯硅烷送至分离提纯系统进行分离与提纯,再返回多晶硅生产工序。
分离出来的氢气返回氢还原工艺的蒸发器,循环使用。
分离出来的HCl返回SiHCl3合成系统,用于合成SiHCl3。
二影响多晶硅质量的因素1影响硅料质量的因素(1 )还原炉炉壁与沉积硅载体如果还原炉炉壁与沉积硅载体的距离过小,特别是硅棒生长的后期,硅棒直径不断增大,使炉壁温度升高;当炉壁达到一定温度时,也会有硅沉积,在进一步沉积过程中,这部分硅散裂被气流带至硅棒载体表面,使硅棒表面粗糙或夹杂气泡,影响多晶硅的质量。
(2)还原炉各部件及发热体的清洗在安装硅芯之前,须先用氮气吹扫炉内的灰尘等,然后用洁净的纱布或无尘布擦去炉内各处的沉积物,最后用无水酒精等擦拭炉体各处,干燥后将炉体封闭,避免受潮。
浅析多晶硅还原生产常见问题及控制对策

Journal of Henan Science, 而且互联网的普及培育了受众 的网络购物习惯, 特别是年轻一代的受众, 在网络上寻找分类 信息、 交易、 交友、 找工作对他们来说已经不是新鲜事 。 当然, 任何新生事物都有很多问题, 在线分类广告也不例外, 信息可 内容同质化等问题是在线分类广告的弊病, 这使得报 信度低、 纸分类广告仍然有机会挽回颓势, 报业经营者可以选择借助 网络媒体对报纸分类广告进行多元化创新经营 。 参考文献: [ 1] 李军. 从报纸分类广告到分类网站 . 中国新闻技术工 作者联合会 2012 年学术年会、 五届四次理事会暨第六届“王 “人才奖 ” “优秀论文奖 ” 选新闻科学技术奖” 的 和 颁奖大会论 C] . 2012 文集[ [ 2] J] . 青年 王雪峰. 网络媒体运营模式及发展趋势探析[ 记者. 2012 ( 23 )
2013. NO. 06
工程与材料科学
Journal of Henan Science and Technology
河南科技
浅析多晶硅还原生产常见问题及控制对策
周修敬 ( 昆明冶研新材料股份有限公司, 云南 曲靖 655011 ) 摘 要: 随着光伏产业及半导体行业的发展与繁荣, 作为基础材料的多晶硅材料得到了广泛的应用 。在全球范围内新能源越 多晶硅行业取得了快速发展的契机, 在短短几年里取得了繁荣与发展, 同时呈现出过剩现象。 在多晶硅生 来越受重视的背景下, 。 产过程中, 还原生产工艺是最为关键的工艺 本文通过对多晶硅生产过程进行介绍, 对多晶硅还原生产过程中常见问题进行分 同时对相应控制对策进行探讨, 以期为多晶硅生产提供参考 。 析, 关键词: 多晶硅; 还原生产; 常见问题; 控制对策 中图分类号: TQ127 文献标识码: A 文章编号: 1003 - 5168 ( 2013 ) 12 - 0083 - 02 光伏产业的快速发展导致多晶硅材料的市场需求日益增 大, 对多晶硅行业的繁荣与发展发挥了巨大推动作用 。 对于 如何提高多晶硅生产质量, 促使多晶硅生产 多晶硅行业来说, 效率大幅提升, 是这一行业发展过程中必须解决的问题 。 多 晶硅行业要取得长远发展, 不能简单依靠盲目扩大多晶硅生 产规模来实现, 也不能对多晶硅生产技术进行盲目革新, 而是 、 需要在对现阶段生产中常见问题进行认真分析 不断改进的 基础上, 对生产工艺进行不断完善与优化, 在保证产品质量的 基础上提高生产产量。 1 西门子法多晶硅生产工艺 1. 1 多晶硅概念 多晶硅是单质硅形态之一 。 在过冷环境中, 熔融单质硅 内部的硅原子按照金刚石晶格形态进行排列, 在进行凝固时, 形成诸多晶核, 若这些晶核形成晶面具有不同取向的晶粒, 则 通过结晶作用即可形成多晶硅 。 这些晶粒互相结合, 1. 2 西门子法多晶硅生产 效粘合, 导致二者脱离现象。 之所以会出现这一问题, 主要是 因为在对硅芯进行酸洗过程中, 酸洗力度不足, 致使硅芯表面 形成氧化层。 2. 2 在生产过程中出现 “硅油” “硅油 ” 。“硅油 ” 在多晶硅还原生产中, 常会有 出现 常出 现在还原炉内温度较低的部位, 通常在窥视孔石英片、 底盘、 “硅油 ” 电极、 喷口与炉筒等位置沉积 。一旦出现 现象, 将会造 使多晶硅生产实收率大幅降低 。 成硅化合物出现大量损失, 同时, 在窥视孔石英片上沉积的硅油会导致镜片模糊, 给测温 对炉温调节造成影响, 在很多时候会导致硅 与观察造成阻碍, 棒上温度过高, 造成硅棒烧断现象。 同时, 硅油吸水能力比较 如果拆炉时炉内有硅油存在, 硅油会对空气内的水大量吸 强, 收, 其内部盐酸脱离出来, 从而对设备造成腐蚀, 严重时还会 造成自燃或爆炸事故。 2. 3 还原生产生成无定形硅 有时为追求低能耗与高产量, 在多晶硅诸多生产企业中, 对无定形硅的形成往往不加重视, 导致生产过程中形成大量 无定形硅。无定形硅的形成一般有两方面原因, 一是因为三 导致无定形硅产生, 这时还原炉中的生 氯氢硅反应温度过低, 产功率相对较低, 沉积速度相对较快; 二是物料中二氯硅烷含 导致大量无定形硅产生 。 尤其是在生产后期, 如果将 量过高, 温度控制在较高范围内, 则会造成炉内能见度剧降, 导致视镜 变黑或模糊。 2. 4 倒棒问题 在多晶硅还原生产中, 倒棒问题是极为常见的问题, 特别 是前期出现的倒棒问题, 常需更换硅芯并将还原炉进行反复 极为不便。之所以会出现倒棒问题, 主要是因为在硅芯 拆装, 安装时未保持垂直状态 、 硅芯不均匀、 横梁未进行良好搭接与 电流过快导致熔断等。 2. 5 硅棒中存在氧化夹层 如果多晶硅的还原生产中有氧或水汽混入原料, 则会使 导致 SiO2 氧化层形成并在硅棒上附着, 原料出现氧化或水解, 沉积硅在这一氧化层上沉积, 最终导致氧化夹层形成, 很容易 “硅跳” 在多晶硅向单晶硅拉制过程中出现 现象。 2. 6 裂纹问题 在生产中后期与停炉时, 如果物料未进行适当配比 、 电流 过快升降或者物料流量波动较大, 常会导致硅棒上出现裂纹 问题。 2. 7 高温下还原炉水管震动问题 高温下还原炉的水管振动不仅给在工作人员造成不适, 如果震动过强还会使管道保温脱落 、 管道结构及附件破坏、 弯 头与焊缝出现泄漏或爆炸, 引发严重安全事故。 还原炉内高 温水系统的压力及温度对还原炉运行的稳定具有决定性影 ( 下转第 245 页) 响。如果出现爆管问题或高温水泄漏现象,
多晶硅质量影响因素分析--论文1
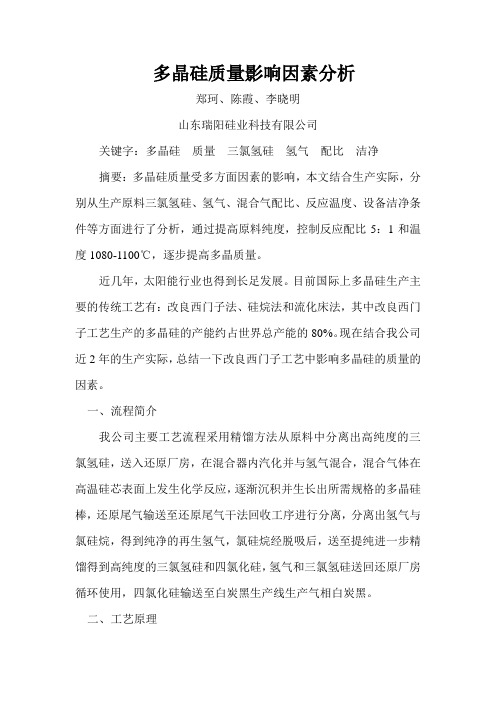
多晶硅质量影响因素分析郑珂、陈霞、李晓明山东瑞阳硅业科技有限公司关键字:多晶硅质量三氯氢硅氢气配比洁净摘要:多晶硅质量受多方面因素的影响,本文结合生产实际,分别从生产原料三氯氢硅、氢气、混合气配比、反应温度、设备洁净条件等方面进行了分析,通过提高原料纯度,控制反应配比5:1和温度1080-1100℃,逐步提高多晶质量。
近几年,太阳能行业也得到长足发展。
目前国际上多晶硅生产主要的传统工艺有:改良西门子法、硅烷法和流化床法,其中改良西门子工艺生产的多晶硅的产能约占世界总产能的80%。
现在结合我公司近2年的生产实际,总结一下改良西门子工艺中影响多晶硅的质量的因素。
一、流程简介我公司主要工艺流程采用精馏方法从原料中分离出高纯度的三氯氢硅,送入还原厂房,在混合器内汽化并与氢气混合,混合气体在高温硅芯表面上发生化学反应,逐渐沉积并生长出所需规格的多晶硅棒,还原尾气输送至还原尾气干法回收工序进行分离,分离出氢气与氯硅烷,得到纯净的再生氢气,氯硅烷经脱吸后,送至提纯进一步精馏得到高纯度的三氯氢硅和四氯化硅,氢气和三氯氢硅送回还原厂房循环使用,四氯化硅输送至白炭黑生产线生产气相白炭黑。
二、工艺原理多晶硅生产过程中,核心部分为多晶硅还原生产,其基本原理为在还原炉内,用高纯三氯氢硅为原料,高纯氢气为还原剂,在1080~1100℃高温下硅被还原出来,有部分三氯氢硅直接被热分解为硅,二者一同沉积在发热体硅芯上。
同时,高温下还会发生部分副反应。
其主反应为:HCl Si C H SiHCl 31100108023+−−−−−−→−︒-+副反应为:243239004H SiCl Si C SiHCl ++−−−−→−︒≥HCl Si H SiCl 4224+−→−+43212002SiCl HCl Si C SiHCl ++−−−−→−︒≥Cl SiCl SiHCl H 23+−−→−高温Cl B BCl H 6223+−→−ClP PCl H 6223+−→− 生产的目的为控制各项条件向主反应方向发生,尽量减少或杜绝副反应的发生。
西门子法多晶硅还原炉气相沉积反应探讨
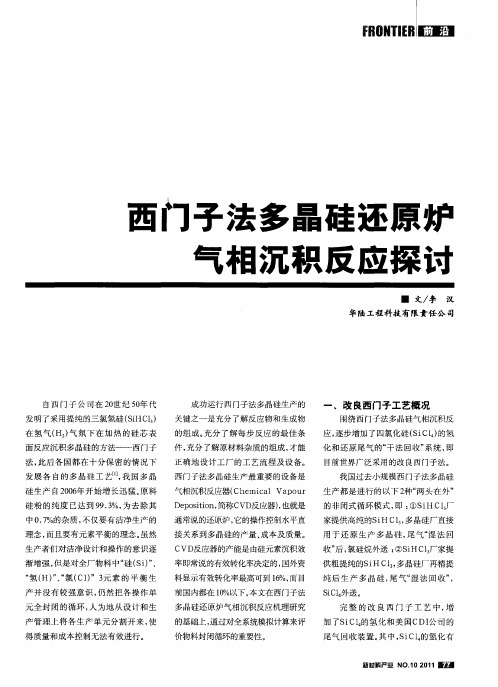
若 能 从 这些 不 确 定情 况 中简化 出
从S HC1 i 3 到二 氯硅 烷 ( i C 2再 到 S H2 1) 硅 的反应 规律 , 能够 完 成多 晶硅 生 就 产全 系统 的物 料 能量平 衡计 算 , 而 从
l
F O TE R NI I R E硼
西 门子 法 多 晶硅 还 原炉 气 相 沉积 反应 探 讨
■ 文/ 李 汉 华陆工程科技 有限 责任公 司
自西 门子 公 司 在 2 世 纪 5 年 代 0 0 发明 了采用提纯 的三氯氢硅 (i C Sl 1)
在 氢 气 ( ) 氛 下 在 加 热 的 硅芯 表 H:气 面反应沉 积多 晶硅 的方法—— 西 门子
渐 增强 , 但是对 全厂 物料 中“ ( ) 、 硅 Si”
我 国过去小规模 西 门子法 多晶硅 生产 都 是进行 的 以下 2 “ 头在 外” 种 两
的 非 闭式循环 模 式 , : i Cl 即 ①S H 厂 家提供 高纯的S H 多 晶硅 厂直接 i Cl , 用 于 还 原 生 产 多 晶 硅 , 气 “ 法 回 尾 湿
De oiin, p sto 简称 C 反应器)也就是 VD , 通常说 的还原炉 , 它的操作控制水平直 接 关系到 多晶硅 的产 量 、 成本及质量 。
CVD反应器 的产能是 由硅元素沉积效
收” , 硅烷外送 ; i 后 氯 ②S HC1 厂家提
率 即常说 的有效转化率决定的 , 国外资 料显示有 效转化率最高可到 1%, 目 6 而
加压 下 操作 , 温 下Si C1的硅沉 高 H 3
多晶硅还原生产常见问题及控制对策分析

多晶硅还原生产常见问题及控制对策分析摘要:近年来,我国的光伏产业有了很大进展,在光伏产业中,多晶硅的应用十分广泛。
在全球范围内新能源越来越受重视的背景下,多晶硅行业取得了快速发展的契机,在短短几年里取得了繁荣与发展,同时呈现出过剩现象。
在多晶硅生产过程中,还原生产工艺是最为关键的工艺。
本文首先对多晶硅还原生产工艺概述,其次探讨了多晶硅还原生产常见问题,最后就多晶硅还原生产问题的控制对策进行研究,以期为多晶硅生产提供参考。
关键词:多晶硅;还原生产;光伏产业引言太阳能光伏产业,作为新能源产业结构体系中发展较为成熟的产业,在碳中和背景下规模将进一步扩大,并成为“双碳”目标得以实现的重要保证。
多晶硅是制造集成电路、光伏太阳能等的关键材料。
因此,多晶硅生产企业迎来了机遇,但也面临更大的压力,因为市场对多晶硅品质的要求在不断提高。
只有不断提升自身的产品质量,实现闭式循环节能减排,才能长久持续发展。
1多晶硅还原生产工艺概述多晶硅生产中改良西门子法是其中一项西门子工艺,在1100℃高纯硅芯中,使用高纯氢还原高纯三氯氢硅,硅芯上方完成多晶硅沉积在。
这种改良西门子工艺,是以传统西门子工艺为前提进行创新,具备节能降耗、可回收利用的特征,多晶硅生产期间同时有H2、HCl、SiCl4一类的副产物和副产热能产生。
使用这种改良西门子法,多晶硅生长阶段多是在还原炉内部操作完成。
还原炉包括底盘、炉筒,其中底盘上有分布电极分布,常见的若干对棒还原炉即根据电极对数得名,例如常见的有24对棒还原炉和36对棒还原炉。
还原炉底盘在多晶硅重量承载这一方面是不可或缺的部件,也负责承担供电和物料进出、物料分布等,利用底盘的绝缘材料、冷却介质流通管路等,即可实现以上一系列操作功能。
还原炉炉筒对于多晶硅而言,也是非常必要的生长空间,还原炉炉筒高度、空间,都会对多晶硅实际产能、电耗指标等造成影响,利用炉筒视镜、冷却介质进回路,便可达到温度与多晶硅生长过程的实时监测目的,并实现设备的冷却。
多晶硅制备还原工艺的分析与优化

多晶硅制备还原工艺的分析与优化首先,硅源的选择对多晶硅的制备至关重要。
通常选择的硅源有二氧化硅、金刚砂等。
二氧化硅是一种常见的硅源,易于获取并且纯度较高。
金刚砂由于含有较高的杂质,需要经过预处理才能用于制备多晶硅。
选择合适的硅源可以保证多晶硅的制备效果。
其次,还原剂的选择也对多晶硅的制备起着重要作用。
常用的还原剂有石墨、氢气、金属硅等。
石墨是一种常见的还原剂,具有良好的热导率和化学稳定性。
氢气是一种理想的还原剂,能够在较低温度下将硅源还原成多晶硅。
金属硅具有较高的活性,但制备成本较高。
在选择还原剂时,需综合考虑还原效率、成本和工艺控制的难易度。
第三,反应温度的控制对多晶硅的制备具有重要影响。
反应温度过高会导致硅源过分还原,形成粒度较大的多晶硅颗粒;反应温度过低则会导致硅源未完全还原,形成纯度较低的硅。
因此,需要选择合适的反应温度,保证硅源在合适的温度下被还原成纯度较高的多晶硅。
第四,反应时间的控制也对多晶硅的制备有一定影响。
反应时间过长会导致多晶硅颗粒粒径增大,而反应时间过短则不利于硅源的完全还原。
在确定反应时间时,需要根据具体情况进行优化。
最后,多晶硅制备过程中杂质的去除也是非常重要的。
杂质的存在会降低多晶硅的纯度,因此需要采取适当的方法去除杂质。
常用的方法有冶金提纯、氧化提纯等。
综上所述,多晶硅制备的还原工艺主要包括硅源选择、还原剂选择、反应温度控制、反应时间控制和杂质去除等环节。
通过优化这些环节,可以提高多晶硅的制备效率和纯度。
未来的研究可以从更深入的角度探索多晶硅制备的还原工艺,以满足不同领域对多晶硅的需求。
电子级多晶硅产品在还原过程中的影响因素
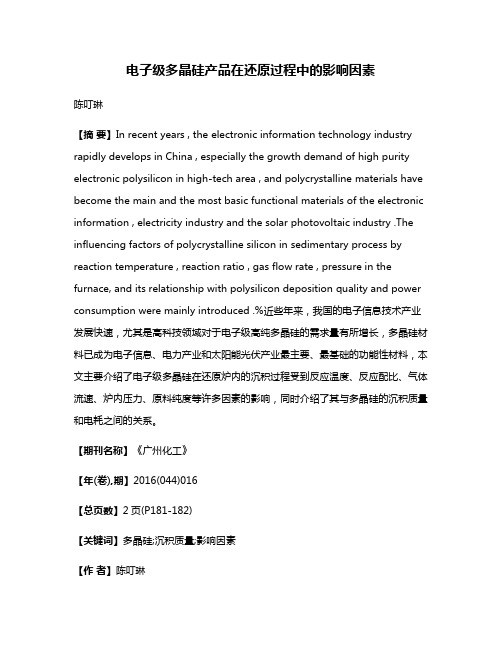
电子级多晶硅产品在还原过程中的影响因素陈叮琳【摘要】In recent years , the electronic information technology industry rapidly develops in China , especially the growth demand of high purity electronic polysilicon in high-tech area , and polycrystalline materials have become the main and the most basic functional materials of the electronic information , electricity industry and the solar photovoltaic industry .The influencing factors of polycrystalline silicon in sedimentary process by reaction temperature , reaction ratio , gas flow rate , pressure in the furnace, and its relationship with polysilicon deposition quality and power consumption were mainly introduced .%近些年来,我国的电子信息技术产业发展快速,尤其是高科技领域对于电子级高纯多晶硅的需求量有所增长,多晶硅材料已成为电子信息、电力产业和太阳能光伏产业最主要、最基础的功能性材料,本文主要介绍了电子级多晶硅在还原炉内的沉积过程受到反应温度、反应配比、气体流速、炉内压力、原料纯度等许多因素的影响,同时介绍了其与多晶硅的沉积质量和电耗之间的关系。
多晶硅 还原炉 产能

多晶硅还原炉产能多晶硅还原炉是制造多晶硅的主要设备之一,其产能通常受到多种因素的影响,包括设备规格、工艺条件、操作方式等。
以下是对多晶硅还原炉产能的详细分析:1.设备规格多晶硅还原炉的规格包括炉体尺寸、电热元件结构、加热功率等。
这些因素直接决定了还原炉的生产能力。
一般来说,还原炉的尺寸越大、加热功率越高,其产能也会相应提高。
1.工艺条件工艺条件包括反应温度、反应压力、气体流量等。
这些因素对还原炉的产能也有重要影响。
在适宜的工艺条件下,多晶硅的合成反应更加充分,还原炉的生产能力也会相应提高。
1.操作方式操作方式包括装料方式、加热方式、冷却方式等。
不同的操作方式对还原炉的产能也会产生影响。
例如,采用先进的装料方式可以增加物料在炉内的停留时间,提高还原反应的效率;采用高效的加热方式可以保证炉内温度的均匀性,提高产品质量;采用快速的冷却方式可以减少产品在高温下的热损伤,提高产品性能。
1.物料质量物料质量包括硅原料的纯度、颗粒度等。
硅原料的纯度越高、颗粒度越均匀,其反应活性也会相应提高,有利于提高还原炉的产能。
1.能耗成本多晶硅还原炉的能耗成本也是影响其产能的一个重要因素。
在保证产品质量和产量的前提下,降低能耗成本可以提高企业的经济效益。
综上所述,多晶硅还原炉的产能受到多种因素的影响,包括设备规格、工艺条件、操作方式、物料质量和能耗成本等。
为了提高还原炉的产能,可以从以下几个方面进行优化:1.选用合适的设备规格,根据实际生产需求进行选型配置。
2.优化工艺条件,通过试验和计算确定最佳的反应温度、反应压力和气体流量等参数。
3.改进操作方式,采用先进的装料方式、加热方式和冷却方式,提高生产效率和产品质量。
4.提高物料质量,加强对硅原料的质量控制,提高其纯度和颗粒度等指标。
5.降低能耗成本,采用先进的节能技术和设备,提高能源利用效率。
在生产实践中,可以通过对以上因素的综合考虑,制定出适合企业实际情况的生产方案,实现多晶硅还原炉的高效生产。
- 1、下载文档前请自行甄别文档内容的完整性,平台不提供额外的编辑、内容补充、找答案等附加服务。
- 2、"仅部分预览"的文档,不可在线预览部分如存在完整性等问题,可反馈申请退款(可完整预览的文档不适用该条件!)。
- 3、如文档侵犯您的权益,请联系客服反馈,我们会尽快为您处理(人工客服工作时间:9:00-18:30)。
2
多晶硅还原反应的影响因素
三氯氢硅在 900~1050℃范围内以热分解为主,在 1050~1200℃之间以氢还原为主。 但这只是一个大致的趋势,其实在 900~1050℃范围内也会有氢还原反应发生。三氯氢硅 反应温度较四氯化硅的略低,因此可以相应减少还原炉设备杂质挥发所引起的污染。
个分子,如果是气体,则 1 摩尔气体在标准状态下 (温度为 0 ℃,压力为 1 个大气压)的体
积为约 22.4 升。物质的摩尔数(m)与质量的关系为:
如果质量的单位为 kg,则算出的摩尔数单位为千摩尔(kmol ) ,如果质量的单位为 g ,
则算出的摩尔数单位为摩尔(mol)。
还原反应时,氢气与 SiHC13 的摩尔数之比 (也叫配比〕对多晶硅的沉积有很大影响。
只有在较强的还原气氛下,才能使还原反应比较充分地进行,获得较高的 SiHC13 转化率。
如果按反应式计算所需的理论氢气量来还原 SiHC13 ,那么不会得到结晶型的多晶硅,只会
得到一些非晶态的褐色粉末,而且收率极低。增加氢气的配比,可以显著提高 SiHC1图 7、不同 H2 摩尔流量下的各物料组成
8
多晶硅还原反应的影响因素
如图 7 是采用 ASPEN plus 计算了进料 TCS 为 1Kmol/hr 时,H2 从 1Kmol/hr~ 10Kmol/hr 时系统达平衡时各物料组成。可见,随着混合进料中 H2 的增加,抑制了热分 解反应,使氢还原反应占主导地位。通常,实际的转化率远远低于理论值。一方面是因为还 原过程中存在各种副反应,另一方面是实际的还原反应不可能达到平衡的程度。但是,总的 情况仍然是还原转化率随着氢气与 SiHC13 的摩尔比的增大而提高。但是氢气与 SiHC13 的配比不能过大,因为:
发热量也很大。随着生产的进行,硅棒变粗,电阻降低,反应温度也开始降低,此时三氯氢
硅还原反应占主导逐渐转变为三氯氢硅裂解反应占主导。这一点对于还原生产控制而言非常
关键,因此在编制进料表时必须要充分考虑此现象。
7
多晶硅还原反应的影响因素
2、反应配比
多晶硅还原反应的影响因素(二)
在这里要先介绍摩尔的概念,摩尔又称物质的量,1 摩尔 (mol) 物质含有 6.02×1023
另外沉积过程中,组份的输运还受 Soret 热效应的影响。Soret 热效应通常指凝聚相的 热扩散现象,即在不均匀的温度场中,混合物的组份向不等温的冷热两壁发生迁移浓缩,形 成浓度梯度,分子量大的向冷区聚积,分子量小的向热区聚积,故在硅棒表面邻近区域, HCl 比 TCS 更容易贴近硅棒表面,使得反应速率受到限制如图 3 和图 4 所示
图 1 温度对各组分含量的影响
1
多晶硅还原反应的影响因素
结合下面两反应式(1)和(2), SiHCl3+H2-→Si+3HCl - Q ………………………(1) SiHCl3+3HCl-→SiCl4+2H2+Q ………………………(2) 可以看出,随着反应温度增加,Si 和 HCl 的生成量在增加,氢气的耗量在增加,而 SiCl4 的生成量在减少。说明温度升高,对(1)有利,对(2)有抑制作用。另外反应(2) 从右向左即是 SiCl4 的热氢化工艺,即反应温度升高,不仅可以增加硅的收率,而且可以抑 制三氯氢硅变成四氯化硅。 温度升高,对硅的转化率有利,这是因为硅棒的生长主要是化学气相沉积。但另一方面, 硅在硅棒表面沉积,又是一个物理过程。根据 Langmuir 吸附公式,温度升高会导致解析速 率增加,吸附速率降低。所以在实际生产过程中,温度并非越高越好。实际沉积过程中,半 导体材料自气相向固态载体上沉积时都有最高温度 Tmax,当反应温度超过这个温度时,随 着温度的升高沉积速率反而下降,各种不同的硅卤化物有不同的 Tmax。此外,还有一个平 衡温度 T0,高于该温度才开始反应析出硅。一般在反应平衡温度和最大温度之间,沉积速 率随着温度升高而增大,如图 2 所示。
1、反应温度
SiHCl3 被氢气还原以及热分解的反应是吸热反应。所以,从理论上来说,反应的温度 愈高则愈有利于反应的进行,此时硅的沉积速率也就越高。温度愈高,沉积速度愈快,达到 反应平衡的时间也越短,趋向平衡的程度也越近。系统含 SiHCl3、SiCl4、H2、HCl、SiH2Cl2 以及硅粉的组份,在 800℃~1400℃之间的吉布斯自由能最小原则进行计算平衡时各组份 的平衡量,氢气和 TCS 的量分别为 3kmol/hr 和 1Kmol/hr。
所以过高温度是不适宜的,但是温度过低对反应也不利。还原炉生产中,很大程度上是
控制炉内温场,只有当炉内温场稳定,且符合工艺要求时,此时硅的沉积速度将越高,相应
还原电耗也会最低。
在实际生产中,前期通过增加还原炉的功率,提升反应温度至 1080℃以上,此时的反
应主要是还原反应。虽然此时的电流并不是很大,但由于硅棒比较细,电阻非常大,因此其
从图 6.1 就可以看出,随着温度升高,达到平衡状态时,系统的硅收率增加,STC 降低, H2 的耗量明显增加(系统中 H2 的含量随着温度的升高而降低)。在图 1 中,当温度升到 1150℃之后,TCS 的变化趋势和 1150℃之前相差不大,但 STC 的变化却加快。1150℃之 后 HCl 斜率几乎是之前的两倍。
一般说来,在反应平衡温度和最高温度之间,沉积速率随温度增高而增大。
2) 温度过高,沉积硅的化学活性增强,受到设备材质沾污的可能性增加,造成多晶硅
的质量下降。
3) 直接影响多晶硅品质的磷硼杂质,其化合物随温度增高,还原量也增大,从而进入
多晶硅中,使多晶硅的质量下降。
4) 温度过高,还会发生硅的腐蚀反应。
图 6、硅棒表面的气流分布 炉内硅棒的直径和电阻率的不同也是影响调节效果的重要因素。当直径为 20mm, 硅棒中心温度约 1222℃,表面温度达 1102℃;当直径为 15mm,硅棒中心温度约 1424℃, 表面温度达 1335℃,这时就容易熔断导致倒棒。所以在硅芯的制作过程中,力求每根硅芯 的粗细一样,以便能很好的对电流进行自动控制。 要保持高的沉积反应速率和好的生长质量,温度控制要相当灵敏。利用高温红外测温仪 在不同位置测量硅棒的表面温度,再由自动控制系统进行控制调节硅棒的加热电流值。然而, 由于红外高温测温仪非常容易发生飘移,造成所测温度偏差很大,故常常造成实际所需电流 与根据温度自动调节的电流不符。另外温度控制也可采用电流随时间的预定函数进行顺序控 制。还原炉内温度分布的均匀与否对沉积过程中的质量和能耗有相当大的影响。一般来说还 原炉内的温度分布均匀,各处的温度梯度小,沉积速率也相近,生长质量也会很好,电耗也 会下降。 一般来讲,反应温度高,硅的结晶性就好,而且表面具有光亮的金属光泽;温度越低,
6
多晶硅还原反应的影响因素
结晶变得细小,表面呈暗灰色。但反应温度也不能过高,因为
1) 硅与其他半导体材料一样,从气相往固态载体上沉积时有一个最高温度值,反应温
度超过这个值时,随着温度的升高沉积速率反而下降。各种不同的硅卤化物有不同的最高温
度值,反应温度不应超过这个值。此外,还有一个平衡温度值,高于该温度才有硅沉积出来。
硅的腐蚀反应:
由于硅的沉积速率受温度的影响最大,所以温度对硅棒表面形态的影响程度也很大。 多晶硅形态等级(morphologylevelrating)一般可以分为 7 级,1 级为硅棒光滑致 密,7 级为最粗糙,呈爆米花(popcorn)状。形态等级差的硅棒致使在化学清洗时不易处 理干净,杂质和水份残留在多晶硅表面,影响区熔成晶,甚至迫使中断拉晶操作。即使用作 直拉料,也会由于杂质玷污,使单晶纯度下降。 硅棒表面形态均匀性的根本原因是硅的沉积速度和硅棒表面所能吸收并使之形成晶体 的速度之间的差异。当化学反应沉积速度大于硅棒表面成晶速度时,晶粒来不及在硅棒表面 进行有序的排列,就会造成硅棒表面的不均匀。有许多因素可以影响硅的沉积速度从而造成 硅棒的畸形生长,影响多晶硅形态等级,例如硅棒表面温度及温度不均匀性,进料气体的流 量和组份的摩尔配比,原料混合气的纯度,甚至硅芯的安装垂直度等。 图 5 为各种硅棒表面的形态。
硅棒表面的形态还受其他因素的影响,例如杂质浓度对晶格的影响以及气体流速和配比 对反应速率和表面流动状况。但主要的温度对其形貌的影响具有主要作用。所以还原炉内, 尤其是硅棒表面应该保持在适当的速率范围内,不能过于强调反应速率而忽略产品质量,所 以温度应该保持在一定的范围(<Tmax)。
5
多晶硅还原反应的影响因素
a、不同位置处的硅棒表面形态 b、光滑的硅棒表面 c、粗糙的硅棒表面 图 5、各种硅棒表面形态 4
多晶硅还原反应的影响因素
硅棒生长过程中,具有“自调节效应”,使得硅棒在生长过程中,不会导致粗的地方越 粗,细的地方越细的现象,而是通过自调节,使得产品硅棒上下各处粗细趋向均匀。当硅棒 表面的温度超过某一个最大值(Tmax)时,气相向硅棒表面沉积的速度随着温度的升高反 而下降,随着温度的下降反而上升。在此温度区(>Tmax),由于受到对流的影响,硅棒表 面的温度分布会发生波动而不均匀。温度低的地方,沉积速度快而产生凸起,凸起的表面易 散热而会使温度变低,这样就使得这些地方可以保持较高的反应速度。另外,凸起的地方更 先于接触到反应气体,故最先进行反应,从而凸起的地方更凸。相反,温度高的地方,沉积 速度低而产生凹坑,凹坑的表面不易散热而会使温度变得更高,低凹的地方面气相容易发生 涡流,反应气更新速度慢,这样就使得这些地方的反应速度被限制的较慢,从而凹坑的地方 更凹。Soret 效应使得硅棒表面的高温区的 HCl 气体浓度很大,而气流在凹坑和凸起的地方 最容易形成环流。而凹坑和凸起逐渐发展,相邻近的相互连接在一起,其下面包裹杂质气体, 从而生长的硅棒粗糙和疏松。当温度低于 Tmax 时,由于具有“自调节效应”,表面可以消 除凹凸现象,使得硅的结晶致密,表面光滑而平整。当然,为了维持高的沉积速率,另外避 免生成无定型硅,硅棒表面的温度也不能过低。