热耗计算公式
采暖热力消耗计算公式
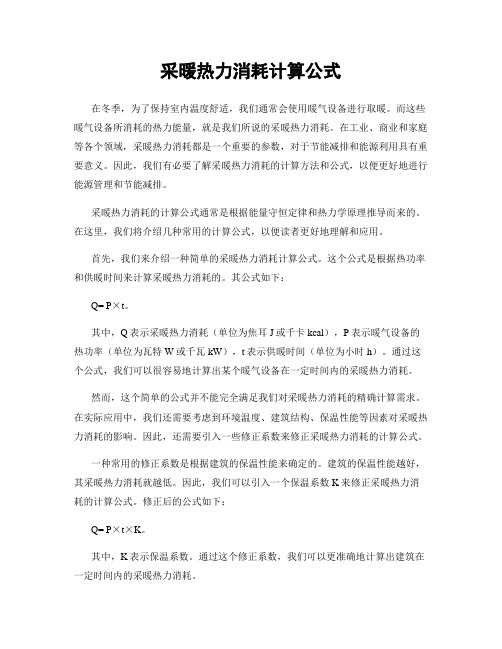
采暖热力消耗计算公式在冬季,为了保持室内温度舒适,我们通常会使用暖气设备进行取暖。
而这些暖气设备所消耗的热力能量,就是我们所说的采暖热力消耗。
在工业、商业和家庭等各个领域,采暖热力消耗都是一个重要的参数,对于节能减排和能源利用具有重要意义。
因此,我们有必要了解采暖热力消耗的计算方法和公式,以便更好地进行能源管理和节能减排。
采暖热力消耗的计算公式通常是根据能量守恒定律和热力学原理推导而来的。
在这里,我们将介绍几种常用的计算公式,以便读者更好地理解和应用。
首先,我们来介绍一种简单的采暖热力消耗计算公式。
这个公式是根据热功率和供暖时间来计算采暖热力消耗的。
其公式如下:Q= P×t。
其中,Q表示采暖热力消耗(单位为焦耳J或千卡kcal),P表示暖气设备的热功率(单位为瓦特W或千瓦kW),t表示供暖时间(单位为小时h)。
通过这个公式,我们可以很容易地计算出某个暖气设备在一定时间内的采暖热力消耗。
然而,这个简单的公式并不能完全满足我们对采暖热力消耗的精确计算需求。
在实际应用中,我们还需要考虑到环境温度、建筑结构、保温性能等因素对采暖热力消耗的影响。
因此,还需要引入一些修正系数来修正采暖热力消耗的计算公式。
一种常用的修正系数是根据建筑的保温性能来确定的。
建筑的保温性能越好,其采暖热力消耗就越低。
因此,我们可以引入一个保温系数K来修正采暖热力消耗的计算公式。
修正后的公式如下:Q= P×t×K。
其中,K表示保温系数。
通过这个修正系数,我们可以更准确地计算出建筑在一定时间内的采暖热力消耗。
除了保温系数,还有一些其他的修正系数也需要考虑。
例如,环境温度对采暖热力消耗的影响很大,我们可以引入一个环境温度系数来修正计算公式。
另外,暖气设备的效率、管道输送损失等因素也需要考虑在内。
因此,采暖热力消耗的计算公式往往是一个复杂的多变量函数,需要根据具体情况进行调整和修正。
在实际应用中,我们还可以利用计算机软件进行采暖热力消耗的精确计算。
汽轮机热耗的计算公式

汽轮机热耗的计算公式汽轮机是一种常见的热能转换设备,通过燃料的燃烧产生高温高压的热能,驱动汽轮机内的转子运动,从而将热能转化为机械能。
汽轮机的热耗是指在这个过程中热能的损耗,计算公式如下:热耗 = 输入热能 - 输出机械能输入热能是指燃料的燃烧释放的热能,通常以焓值的形式表示。
焓是热力学中的一个重要参数,表示单位质量物质在某一温度和压力下的热能。
在汽轮机中,焓的变化是通过燃料的燃烧来实现的。
输出机械能是指汽轮机产生的用于驱动负载的机械能,通常以功率的形式表示。
功率是指单位时间内所做的功,可以用来衡量机械设备的工作能力。
在汽轮机中,机械能是通过转子的旋转运动来传递的。
热耗是指在这个能量转换过程中损失的热能,它包括两部分:一部分是由于燃料的不完全燃烧而导致的热能损失,另一部分是由于摩擦、传热等非理想情况而引起的能量损失。
燃料的不完全燃烧是指燃料在燃烧过程中没有完全与氧气反应生成二氧化碳和水,而产生了一些未燃烧的碳氢化合物和一氧化碳等有害物质。
这些未燃烧的物质会带走一部分热能,造成热耗的增加。
摩擦和传热是指汽轮机内部各个部件之间的摩擦和热量传递过程中的能量损失。
在汽轮机中,高温高压的工作环境和高速旋转的转子使得各个部件之间会产生摩擦,从而导致能量的损失。
另外,热量的传递也会带走一部分热能,造成热耗的增加。
为了减少汽轮机的热耗,可以采取一些措施。
首先,优化燃烧过程,使燃料能够充分燃烧,减少未燃烧物质的产生。
其次,采用高效的传热和润滑系统,减少摩擦和能量损失。
此外,合理设计汽轮机的结构和工艺参数,提高汽轮机的热效率和机械效率,也可以有效降低热耗。
总结起来,汽轮机的热耗是指在能量转换过程中损失的热能,可以通过计算公式进行计算。
热耗的大小受到燃料的燃烧效率、摩擦和传热等因素的影响。
为了减少热耗,可以优化燃烧过程、改进传热和润滑系统,并合理设计汽轮机的结构和工艺参数。
这样可以提高汽轮机的热效率和机械效率,从而降低热耗,提高能源利用效率。
电厂主要指标计算公式
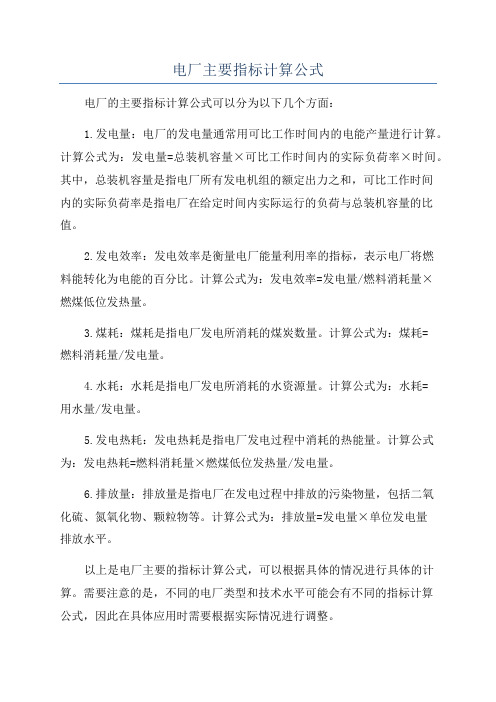
电厂主要指标计算公式
电厂的主要指标计算公式可以分为以下几个方面:
1.发电量:电厂的发电量通常用可比工作时间内的电能产量进行计算。
计算公式为:发电量=总装机容量×可比工作时间内的实际负荷率×时间。
其中,总装机容量是指电厂所有发电机组的额定出力之和,可比工作时间
内的实际负荷率是指电厂在给定时间内实际运行的负荷与总装机容量的比值。
2.发电效率:发电效率是衡量电厂能量利用率的指标,表示电厂将燃
料能转化为电能的百分比。
计算公式为:发电效率=发电量/燃料消耗量×
燃煤低位发热量。
3.煤耗:煤耗是指电厂发电所消耗的煤炭数量。
计算公式为:煤耗=
燃料消耗量/发电量。
4.水耗:水耗是指电厂发电所消耗的水资源量。
计算公式为:水耗=
用水量/发电量。
5.发电热耗:发电热耗是指电厂发电过程中消耗的热能量。
计算公式为:发电热耗=燃料消耗量×燃煤低位发热量/发电量。
6.排放量:排放量是指电厂在发电过程中排放的污染物量,包括二氧
化硫、氮氧化物、颗粒物等。
计算公式为:排放量=发电量×单位发电量
排放水平。
以上是电厂主要的指标计算公式,可以根据具体的情况进行具体的计算。
需要注意的是,不同的电厂类型和技术水平可能会有不同的指标计算
公式,因此在具体应用时需要根据实际情况进行调整。
计算汽轮机热耗公式

计算汽轮机热耗公式
预览说明:预览图片所展示的格式为文档的源格式展示,下载源文件没有水印,内容可编辑和复制
汽轮机热耗率计算公式
凝汽式机组(采用电动给水泵)毛热耗率=汽轮机进汽流量×(新蒸汽比焓-给水比焓)÷发电机输出的电功率
中间再热式机组(采用电动给水泵)毛热耗率=【汽轮机进汽流量×(新蒸汽比焓-给水比焓)+进入中压缸再热蒸汽流量(进入中压缸再热蒸汽实际比焓
-高压缸排汽实际比焓)】÷发电机输出的电功率
中间再热式机组(采用主机抽汽拖动给水泵)毛热耗率=【汽轮机进汽流量×(新蒸汽比焓-给水比焓)+进入中压缸再热蒸汽流量(进入中压缸再热蒸汽
实际比焓-高压缸排汽实际比焓)】÷(发电机输出的电功率+拖动给水泵用的汽轮机输出功率)
抽汽式机组(采用电动给水泵)毛热耗率=【汽轮机进汽流量×(新蒸汽比焓-给水比焓)-供热抽汽量(抽汽实际比焓-供热回水实际比焓)】÷发电机
输出的电功率
背压机组的毛热耗率=(进汽量×进汽焓-排汽量×排汽焓-加热器用汽量×加热器用汽焓-轴封漏汽量×轴封漏汽焓)/发电机输出的电功率 kj/kWh。
热能损耗量计算讲解

热能损耗量计算一、工作时热损耗计逄公式:Q=K(Q1+Q2+Q3+Q4+Q5)式中:Q——工作时总的热损耗(J/H)Q1——通过烘干室外壁散失的热损耗量(J/H)Q2——加热工件及输送机移动部分的热损耗量(J/H)Q3——加热涂料(或水份)和涂料中溶剂(或水份)气化潜热损耗量(J/H)Q4——加热新鲜空气的损耗量(J/H)Q5——通过烘室门洞散失的热量损耗(J/H)K——考虑至其它未估计至的热量损耗储蓄备系数一般耳K=1.1~1.3 通过烘干室外壁热量损耗Q1计公式Q=KF(t-t。
)K——(保温板传热系数,单位J/m2·h·℃)烘干室保温层厚150mm,取系数3500焦耳每平方米每小时每摄氏度 F——壁板面积(H2.45m+W2m)×2×38m=338m2风道及燃烧表面积26m2合计364m2t400℃-t。
30℃=370°Q1=3500J×364m2×370℃=471380000J/H=471380000÷4.1868=11258.178752kal≈11.26万大卡2台炉——11.26×2=22.52万大卡二、加热工件及输送机移动部分的热量耗量Q2=G×C×(t-t。
)式中:G——工件质量克C——工件的比热容[J/(kg·℃)]工件:铁板输入速度80m/min ,W1.25m,厚1mm铁密度为7.85g/cm3 铁比热为0.120卡/克℃G=125cm×8000cm×0.1cm×7.85g/cm3×60min=47100000g底漆炉 Q2=47100000克×0.120卡/克℃×230℃=129996000kal=129.996×104kal/h 面漆炉 Q2=47100000克×0.120卡/克℃×200℃=11304000kal=113.04×104kal/h三、加热涂料及溶剂蒸发热量耗量Q3=G×C×(t-t。
采暖小时耗热量计算公式

采暖小时耗热量计算公式在冬季寒冷的天气里,采暖是非常重要的。
为了保持室内温暖舒适,人们通常会使用暖气设备来加热室内空气。
而要确定需要多少热量来进行采暖,就需要使用采暖小时耗热量计算公式。
本文将介绍采暖小时耗热量计算公式以及其应用。
采暖小时耗热量计算公式的基本形式如下:Q=V×t×(t1-t2)×k。
其中,Q为需要的热量,单位为千焦尔(kJ)或千瓦时(kWh);V为需要采暖的空间体积,单位为立方米(m³);t为需要采暖的时间,单位为小时(h);t1为室内温度,单位为摄氏度(℃);t2为室外温度,单位为摄氏度(℃);k为热传导系数,单位为千焦尔/(米·小时·摄氏度)。
首先,我们需要确定需要采暖的空间体积V。
通常情况下,可以通过测量房间的长、宽、高来计算出房间的体积。
假设房间的长为L,宽为W,高为H,则房间的体积V=L×W×H。
接下来,我们需要确定需要采暖的时间t。
通常情况下,可以根据每天需要采暖的时间来确定。
假设每天需要采暖的时间为T小时,则需要采暖的时间t=T×365(一年的小时数)。
然后,我们需要确定室内和室外的温度差值(t1-t2)。
室内温度t1通常为人们所期望的舒适温度,室外温度t2则为当前的实际温度。
温度差值(t1-t2)可以直接由温度计来测量得出。
最后,我们需要确定热传导系数k。
热传导系数k是材料的热传导能力的一个物理量,不同的材料有不同的热传导系数。
通常情况下,可以通过查阅相关资料或者咨询专业人士来确定。
将以上参数代入采暖小时耗热量计算公式中,就可以得出需要的热量Q。
通过这个公式,我们可以比较准确地确定需要多少热量来进行采暖,从而选择合适的暖气设备和合理的供热方案。
除了以上的基本形式,采暖小时耗热量计算公式还可以根据具体情况进行一些修正。
例如,在考虑到房间的隔热性能、采暖设备的热效率、室内空气的流通情况等因素时,可以对公式进行修正。
热能损耗量计算讲解
热能消耗量计算一、工作时热消耗计逄公式: Q=K( Q1+Q2+Q3+Q4+Q5)式中: Q——工作时总的热消耗( J/H)Q1——经过烘干室外壁消散的热消耗量(J/H)Q2——加热工件及输送机挪动部分的热消耗量(J/H)Q3——加热涂料(或水份)和涂猜中溶剂(或水份)气化潜热消耗量(J/H)Q4——加热新鲜空气的消耗量(J/H)Q5——经过烘室门洞消散的热量消耗(J/H)K ——考虑至其余未预计至的热量消耗积蓄备系数一般耳K=1.1~1.3 经过烘干室外壁热量消耗 Q1 计公式Q=KF(t-t 。
)K ——(保温板传热系数,单位J/m2·h·℃)烘干室保温层厚150mm,取系数 3500 焦耳每平方米每小时每摄氏度F——壁板面积( H2.45m+W2m)×2×38m=338m2风道及焚烧表面积26m2共计 364m2t400℃-t。
30℃=370°Q1=3500J×364m2×370℃ =471380000J/H=471380000÷≈万11大.26卡2台炉—— 11.26 ×2=22.52 万大卡二、加热工件及输送机挪动部分的热量耗量Q2=G×C×( t-t。
)式中: G——工件质量克C——工件的比热容 [J/( kg·℃) ]工件:铁板输入速度80m/min ,W1.25m,厚 1mm铁密度为铁比热为 0.120 卡/克℃G=125cm×8000cm×××60min=47100000g底漆炉 Q2=47100000克×0.120 卡/克℃×230℃=129996000kal=129.996 ×104kal/h 面漆炉 Q2=47100000克×0.120 卡/克℃×200℃=11304000kal=113.04 ×104kal/h 三、加热涂料及溶剂蒸发热量耗量Q3=G×C×( t-t。
电厂经济指标计算公式
电厂经济指标计算公式1. 发电效率(Electric Efficiency)发电效率是指电厂从燃煤、燃气或其他能源中产生的能量转化为电能的比例。
一般以百分比表示,计算公式如下:发电效率=发电量/燃料热值×100其中,发电量表示电厂一定时间内(通常为一天或一年)产生的电能量,单位多为兆瓦时(MWh);燃料热值表示所使用的燃料每单位质量所含有的热能,单位一般为兆焦耳/千克(MJ/kg)或千卡/千克(kcal/kg)。
2. 热耗率(Heat Rate)热耗率是指发电厂每生成一单位电能所需的燃料热值。
一般以兆焦耳/千瓦时(MJ/kWh)或千卡/千瓦时(kcal/kWh)表示,计算公式如下:热耗率=燃料消耗量×燃料热值/发电量其中,燃料消耗量表示电厂一定时间内所使用的燃料质量,单位一般为吨或千克。
3. 燃料消耗率(Fuel Consumption Rate)燃料消耗率是指电厂在发电过程中每产生一单位电能所需要的燃料质量。
一般以克/千瓦时(g/kWh)表示,计算公式如下:燃料消耗率=燃料消耗量/发电量×1000其中,燃料消耗量表示电厂一定时间内所使用的燃料质量,单位一般为吨或千克。
4. 经济效益(Economic Benefit)经济效益是指电厂在一定时间内所创造的经济价值。
一般以万元为单位,计算公式如下:经济效益=应收入-总成本其中,应收入表示电厂一定时间内的发电收入,包括售电收入、热力销售收入等;总成本包括燃料成本、运维成本、设备折旧与维修成本等。
以上便是电厂经济指标的计算公式,通过这些指标的计算和分析,可以评价电厂的效益和经济状况,为电厂的管理和运营决策提供重要参考。
需要注意的是,在实际计算时需要根据具体情况确定参数的单位和数值,并考虑到影响电厂经济指标的各项因素。
器件热耗计算公式
器件热耗计算公式在电子设备中,器件的热耗是一个非常重要的参数,它直接影响着设备的稳定性和工作效率。
因此,准确地计算器件的热耗是非常重要的。
本文将介绍器件热耗的计算公式,并对其进行详细的解析和应用。
器件的热耗可以通过以下公式来计算:P = I^2 R。
其中,P表示器件的热耗,单位为瓦特(W);I表示器件的电流,单位为安培(A);R表示器件的电阻,单位为欧姆(Ω)。
这个公式简单而直观,通过电流的平方乘以电阻,可以得到器件的热耗。
在实际应用中,我们可以通过这个公式来计算器件的热耗,从而评估设备的热量产生情况。
在实际应用中,我们可以通过以下步骤来计算器件的热耗:1. 首先,我们需要确定器件的电流。
这可以通过测量电路中的电流来获得,也可以通过器件的参数来计算得到。
2. 其次,我们需要确定器件的电阻。
这可以通过器件的参数来获得,也可以通过实际测试来得到。
3. 最后,我们可以通过上述公式来计算器件的热耗。
将电流的平方乘以电阻,就可以得到器件的热耗。
通过这个公式,我们可以快速地计算出器件的热耗,从而评估设备的热量产生情况。
在实际应用中,我们可以根据计算得到的热耗数据,来优化设备的散热设计,从而提高设备的稳定性和工作效率。
除了上述的基本公式外,我们还可以根据具体的器件类型和工作条件,来进一步优化热耗的计算公式。
例如,对于半导体器件,我们可以考虑器件的导通损耗和开关损耗;对于电感器件,我们可以考虑器件的铜损耗和铁损耗。
通过这些更加细致的计算,我们可以更加准确地评估器件的热耗情况,从而更好地优化设备的热量产生情况。
总之,器件的热耗是电子设备中一个非常重要的参数,它直接影响着设备的稳定性和工作效率。
通过适当的热耗计算公式,我们可以快速而准确地评估器件的热耗情况,从而优化设备的热量产生情况。
希望本文介绍的热耗计算公式能够对大家有所帮助,谢谢大家的阅读!。
汽耗与热耗计算(经典)
1、汽轮发电机组热耗率
汽轮发电机组热耗率是指汽轮发电机组每发一千瓦时电量耗用的热量,单位为“千焦/千瓦时”。
它反映汽轮发电机组热力循环的完善轮程度。
汽轮发电机组的热耗率不仅受汽轮机的内效率、发电机效率、汽轮发电机组的机械效率的影响,而且受循环效率、蒸汽初、终参数的影响。
汽轮发电机组热耗率的计算公式如下:
1)无再热凝汽轮机组的热耗率
汽轮机耗用的主蒸汽量
汽耗率(千克/千瓦时)=
发电机的发电量
2、汽轮机的汽耗率
汽轮机汽耗率是指在发电机端每产生一千瓦时的电量,汽轮机所需要的蒸汽量。
计算公式为:。
- 1、下载文档前请自行甄别文档内容的完整性,平台不提供额外的编辑、内容补充、找答案等附加服务。
- 2、"仅部分预览"的文档,不可在线预览部分如存在完整性等问题,可反馈申请退款(可完整预览的文档不适用该条件!)。
- 3、如文档侵犯您的权益,请联系客服反馈,我们会尽快为您处理(人工客服工作时间:9:00-18:30)。
新热耗计 算结果
9127.218
主蒸汽流 量
省煤器入 口给水流 量1
过热器减 温水流量
至排汽装 置凝结水 补充水流 量
辅汽母管 焓
自冷再来 辅汽焓
979.5792 838.264 828.9564 726.2171 679.913 29.69485 7.504218 3121.317 3030.327
自冷再来 辅汽流量
除盐水焓
锅炉冷渣 器冷却水 供水流量
冷渣器闭 式水冷却 水供水焓
冷渣器闭 式水冷却 水回水焓
连排流量
连续排污 扩容器压 力
机组实际 负荷
汽包压力
0.296574 73.98107 530.2937 248.7684 323.152 2.308838 0.679468 240.7669 14.31078
பைடு நூலகம்
进连排焓
连排疏水 焓
连排蒸汽 焓
主蒸汽焓
再热蒸汽 焓
给水焓
高压缸排 汽焓
减温水焓
1高加入 口蒸汽焓
2高加入 口蒸汽焓
1高加疏 水焓
3421.103 3548.209 991.8019 3034.075 696.863 2780.007 3029.211 697.2577
2号高加 出口水焓
2高加至3 高加疏水 焓
3号高加 出口水焓
1号高加 进汽份额
1号高加 进汽量
2号高加 进汽量份 额
高加常数
2号高加 进汽量
连排回收 份额
1583.086 691.9231 2761.488 0.005869 3.990105 0.068748
0 46.74253 0.569396
连排回收 量
1.314644
老热耗计 算结果
8795.075