烧结技术综述
烧结技术综述

1文献综述1.1烧结生产概况1.1.1烧结及其发展烧结法是迄今为止除北美以外使用最为广泛的铁矿石造块方法。
自20世纪80年代起烧结技术得到了快速发展,主要体现在烧结工艺和新技术的研究开发和应用上。
烧结工艺方面如自动化配料、混合料强化制粒、偏析布料、冷却筛分、整粒技术及铺底料技术等;新技术主要表现为球团烧结技术、小球烧结技术、低温烧结技术等。
上述工艺和技术目前已经在大部分钢铁企业推广应用,并取得了显著的经济效益。
1897年,T.Huntington和F,Heberlein申请并注册了第一个有关烧结方面的专利。
1905年,E.J.Savelsberg首先把T.Huntington-F.Heberlein烧结杯用于铁矿石烧结,从而开辟了烧结法进行铁矿粉造块的新纪元。
在当今的冶金生产中,烧结已成为一道重要的单元工序并占有相当重要地位。
据统计,全世界约有一半的生铁是用烧结矿生产的。
过去十年中,世界上烧结矿年产量维持在538×106t~586×106t范围内。
从1989年起,由于独联体和其他部分东欧国家发生巨变,因此,它们的钢铁工业进行了重新调整,导致烧结矿产量有所下降。
欧洲和日本的经济衰退也影响了产量,但是不久烧结矿的产量又慢慢恢复。
东欧和独联体的产量将下降,而中国、朝鲜和台湾的产量将继续上升。
尽管出现新的炼铁工艺,但是在下一个十年中或更长的时间内,它们仍不可能对高炉产量有巨大影响。
因此,烧结矿产量在未来相当长的时间内仍将维持在目前水平。
1.1.2烧结生产目的铁矿粉烧结是一种铁矿粉造块的方法,是将细粒含铁物料与燃料、熔剂按一定比例混合,再加水润湿、混匀和制粒成为烧结料,加于烧结设备上,点火、抽风,借助燃料燃烧产生高温和一系列物理化学变化,生成部分低熔点物质,并软化熔融产生一定数量的液相,将铁矿物颗粒润湿粘结起来,冷却后,即成为具有一定强度的多孔块状产品一侥结矿。
烧结生产的目的主要是:1.将粉状物料制成具有高温强度的块状料以适应高炉冶炼、直接还原等在流体力学方面的要求;2.通过烧结改善铁矿石的冶金性能,使高炉冶炼指标得到改善;3.通过烧结去除某些有害杂质,回收有益元素以达到综合利用资源和扩大炼铁矿石原料资源的目的。
先进陶瓷新型快速烧结技术总结及优缺点

先进陶瓷新型快速烧结技术总结及优缺点先进陶瓷材料由离子键或共价键构成,因此具有高强度、高硬度、耐高温、耐磨损、耐腐蚀、生物相容性好等优异性能。
但是从陶瓷粉体到具有特定性能的多晶陶瓷材料需经高温烧结过程,这是因为陶瓷粉体成型后的素坯含有大量气孔。
从根本上说,烧结是粉末发生扩散传质产生致密化,从而使陶瓷材料具有均匀显微结构、稳定形状以及优异性能的过程。
在制备先进陶瓷的过程中,烧结是最重要的一个环节。
在烧结过程中,降低烧结温度、缩短烧结时间、细化晶粒、消除残余气孔是制备高性能陶瓷材料的关键,其中传统的烧结是在外加热场与常压或机械压力的作用下完成的,但是这些方法对特定材料体系的烧结具有局限性。
烧结新技术的产生为高性能陶瓷材料的制备开辟了新方法,并且丰富了陶瓷材料的烧结理论。
1 自蔓延高温烧结(SHS)自蔓延高温合成(Self-propagation High temperature Synthesis 缩写SHS),又称燃烧合成(Combustion Synthesis缩写CS)是20世纪80年代迅速兴起的一门材料制备技术。
由前苏联科学家Merzhanov提出的一种材料烧结工艺。
此方法是基于放热化学反应的原理,利用外部能量诱发局部发生化学反应,形成化学反应前沿(燃烧波),此后,化学反应在自身放出热量的支持下继续进行,随着燃烧波的推进,燃烧蔓延至整个体系,合成所需材料。
该方法设备、工艺简单,反应迅速,产品纯度高,能耗低。
适用于合成非化学计量比的化合物、中间产物及亚稳定相等。
图1 SHS烧结反应过程示意图20世纪80年代以来,自蔓延烧结技术得到了飞速发展,并成功应用到工业化生产,与许多其他领域技术结合,形成了一系列相关技术,例如,SHS粉体合成技术、SHS烧结技术、SHS致密化技术、SHS治金技术等。
SHS致密化技术是指SHS过程中产物处于炽热塑性状态下借助外部载荷,可以是静载或动载甚至爆炸冲击载荷来实现致密化,有时也借助于高压惰性气氛来促进致密化。
烧结技术国内外现状及发展趋势
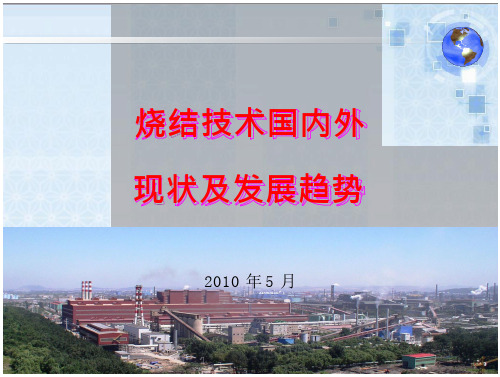
2、主要设备方面
■ 烧结机的大型化 众所周知,大型烧结机与多台小烧结机相比,具有很多的 优点。30年来,我国已先后投产了180~660m2烧结机 125 台套。这批大中型烧结机结构新颖,混合料布料平 整, 漏风率小,头尾部采用星轮装置,烧结机运转平稳,年日 历作业率可达98%。
■ 低温烧结 在厚料层烧结的基础上,可进行低温烧结,即以较低的 温度烧结,能产生一种强度高、还原性好的针状铁酸钙 为主要粘结相的烧结矿,既节能又减排。
1、工艺技术方面
■ 高铁低硅烧结 一般的说法是烧结矿的SiO2应为5.5~6.3%,才能保证足 够的液相。高铁低硅的烧结矿SiO2可达4.5~4.7%,从而 降低熔剂的用量,为高炉增产节焦和烧结节能减排创造 了条件。
■ 近年投产的大中型烧结都采用了现代化的工艺技术,装 备水平高,自动化水平先进,主要技术经济指标和环境 保护、节能减排大为改观,无论是烧结矿的产量还是质 量都已步入了世界强国之列。
1、工艺技术方面
■ 建立综合原料场 为稳定烧结和炼铁生产,并为提高其产品质量和降低能 耗创造条件,我国一大批大中型钢铁公司建立了综合原 料场,使得原料化学成分稳定(宝钢烧结矿TFe<0.5%, 已接近100%)粒度均匀、水分恰当。
二 . 与国外技术比较
表3 环境保护与节能减排表
序 主要项目
号
名称
国内水平
1 烧结机头 大中型烧结机采用干 烟气除尘 式电除尘器
国外水平
日本、韩国、西欧 采用干式电除尘器
对比与差距
国内可以达到国 家排放标准
2 烧结机尾 和环境废 气除尘
什么是烧结技术?

什么是烧结技术?烧结技术是一种重要的粉末冶金工艺,通过在高温条件下将粉末压制成型,然后进行烧结使之结合成为致密的固体材料。
下面将从不同角度介绍烧结技术的相关知识。
一、烧结技术的基本原理烧结技术背后的基本原理是粉末颗粒之间在高温下发生熔结和再结晶的过程。
当遇热自生过程进行时,粉末颗粒表面的氧化物将与其他颗粒的颗粒表面发生反应,产生化学键并形成致密固体结构。
通过调控烧结温度和时间,可以实现粉末颗粒之间的结合,从而制备出具有一定形状和力学性能的材料。
在烧结技术中,压力是一个重要的因素。
通过在烧结过程中施加一定的压力,可以增加粉末颗粒之间的接触面积,促进原子扩散和成核过程的进行,从而提高材料的致密性和力学性能。
二、烧结技术的应用领域1. 金属材料制备:烧结技术在金属材料制备中具有广泛的应用。
通过烧结工艺,可以制备出高强度、高硬度的金属材料,如不锈钢、钨合金等。
同时,烧结技术还可用于制备金属复合材料,如金属陶瓷复合材料,以提高材料的综合性能。
2. 耐磨材料制备:烧结技术在耐磨材料制备中也发挥着重要作用。
通过控制烧结过程中的温度和压力,可以制备出具有优异耐磨性能的材料,如陶瓷刀具、陶瓷磨具等。
3. 功能材料制备:烧结技术还可用于制备具有特殊功能的材料。
例如,通过加入适量的添加剂,可以在烧结过程中形成特定的结构或相,从而赋予材料特殊的光学、磁学或电学性能,如透明陶瓷、氧化锆等。
4. 环保材料制备:传统的材料制备过程中可能会产生大量的废水和废气,对环境造成严重的污染。
而烧结技术由于其无需使用溶剂和燃料,可有效减少环境污染。
因此,烧结技术也被广泛应用于环保材料的制备领域。
三、烧结技术的发展前景随着科学技术的不断发展,烧结技术正不断演进和改进。
通过引入新的材料、新的工艺和新的设备,可以进一步提高烧结材料的性能和制备效率。
未来,烧结技术有望在材料科学领域发挥更大的作用,为我们创造更多的可能性。
综上所述,烧结技术作为一种重要的粉末冶金工艺,通过高温压制和烧结过程制备出具有不同功能和性能的材料。
烧结技术

烧结生产0概述全世界的矿石储量2500亿吨,富矿20%我国矿石储量500亿吨,富矿5%随着钢铁工业的发展,天然富矿从产量和质量上都不能满足高炉冶炼的要求。
而且精矿粉和富矿粉都不能直接入炉冶炼。
为了解决这一难题,将粉矿制成块状人造富矿。
方法:烧结法和球团法。
一、现代高炉对原料的要求1、节焦上(1)、铁矿石品位高,杂质少。
首钢经验:品位提高1%,焦比下降2%,产量提高3%。
产量提高,单位热损失减少,加入熔剂少,减少热量支出。
(2)、熟料比高。
不用或少加熔剂,减少热量支出,冶金性能好。
(3)碱度高。
可以不加石灰石,减少热量支出。
C a C O=CaO+CO2 吸热32、透气性(1)粒度均匀大小不均造成小块填到大块中间破块透气性上限40~50mm下限5~10mm。
(2)粉末少(3)强度高3、冶炼性能(1)还原性好有利于铁氧化物还原,有利于煤气利用的改善与焦比的下降(2)低温还原粉化率低粉化率高粉末多影响透气性(3)软熔性能软化温度高软化区间窄使成渣带下移变薄改善透气性二、人工富矿的方法1、烧结法烧结是将各种粉状含铁原料,配入一定数量的燃料和熔剂,混匀后,进行燃烧,进行一系列的物化反应,产生一定数量的液相,冷凝后粘结起来的块状产品叫做烧结矿,这个过程叫烧结。
2球团法球团矿:把润湿的铁精矿粉和少量的添加剂混合,再造球设备中滚动成9~16mm左右的圆球,在经过干燥,预热,焙烧、均热、冷却、发生一系列的物化反映,使生球固结,成为高炉需要的球团矿。
三、烧结矿在钢铁工业中的重要地位1、扩大矿石来源贫矿经过选矿、造块、烧结制成烧结矿,供高炉使用。
富矿粉经过造块后,供高炉使用。
2、可以改善高炉技术经济指标改善了原料的物理化学性能。
孔隙率高,反应面积增大,加速冶炼过程。
粒度均匀,透气性好。
机械强度高还原性好。
低温还原粉化率低,高温还原软化性好,提高冶炼效果。
3、能够充分利用冶金工业和化学工业的废品。
烧结可以利用高炉炉灰,轧钢皮,硫酸渣、转炉尘作为原料,合理利用资源,降低生产成本。
烧结除尘技术综述

摘 要 根 据 烧 结 生 产 的特 点 , 烧 结 厂 各 主 要 产 尘 点进 行 了 较详 细 的介 绍 , 合 环 境 保 护 的 要 求 , 出 了 各 岗 位 对 结 指
应 选 用 的除 尘 方 式 和 除 尘 器类 型 。
关键词
烧 结 ; 尘 ; 放 浓 度 ;除 尘 器 粉 排
可 能 优 化 烧 结 工 艺 、 用 高 效 的 除 尘 设 备 , 采 取 有 选 并 针 对 性 的 措 施 , 量 减 少 粉 尘 排 放 量 , 保 满 足 不 同 尽 确 国 家 和 地 区制 定 的 污 染 物 排 放 标 准 。
烧 结 机 尾 部 粉 尘 主 要 是 指 热 烧 结 饼 从 烧 结 机 台
是 否 设 置 有 热 振 筛 而 不 同 。 目前 , 大 多 数 大 中 型 绝
ห้องสมุดไป่ตู้
烧结工艺工作总结

烧结工艺工作总结
烧结工艺是一种重要的冶金工艺,广泛应用于钢铁、有色金属和其他金属材料的生产中。
通过高温将粉末状原料烧结成块状产品,从而提高材料的密度、强度和耐磨性。
在烧结工艺中,各种工艺参数的控制和优化对产品质量和生产效率起着至关重要的作用。
以下是对烧结工艺工作的总结。
首先,烧结工艺的工作需要严格控制原料的成分和粒度。
原料的成分和粒度直接影响烧结后产品的质量和性能。
因此,在生产过程中,需要对原料进行严格的化验和筛分,确保原料的成分和粒度符合工艺要求。
其次,烧结工艺的工作需要合理控制烧结温度和时间。
烧结温度和时间是影响产品密度和结构的关键因素。
过高或过低的烧结温度都会导致产品质量下降,而烧结时间的长短也会影响产品的结晶结构和力学性能。
因此,需要通过实验和生产实践,确定最佳的烧结温度和时间参数。
另外,烧结工艺的工作还需要严格控制烧结气氛和气氛流动。
烧结气氛对产品的表面质量和氧化皮的形成都有重要影响。
而气氛流动则会影响产品内部的结构均匀性和密度分布。
因此,在烧结工艺中,需要通过合理设计和调整烧结炉的气氛控制系统,确保烧结气氛和气氛流动的稳定和均匀。
最后,烧结工艺的工作需要及时对生产过程进行监控和调整。
通过实时监测和分析产品的质量指标和生产参数,及时发现和解决生产中的问题,确保产品的质量和生产效率。
总之,烧结工艺工作的总结需要全面掌握烧结工艺的原理和技术要点,严格控制各项工艺参数,及时监控和调整生产过程,以确保产品的质量和生产效率。
只有这样,才能更好地发挥烧结工艺在冶金生产中的重要作用。
烧结_生产流程与工艺细节描述_概述说明

烧结生产流程与工艺细节描述概述说明1. 引言1.1 概述烧结是一种重要的金属冶炼工艺,它主要用于将粉末材料通过高温处理使其结合成坚固的块状物。
烧结生产流程与工艺细节对最终产品的质量和性能起着至关重要的作用。
本文旨在全面介绍烧结生产流程与工艺细节,以帮助读者深入了解该工艺的原理和操作要点。
1.2 文章结构文章分为四个主要部分,分别是引言、烧结生产流程、烧结工艺细节描述和结论。
首先,在引言部分,我们将简要介绍烧结工艺的概念和重要性,并概述本文的整体内容。
接下来,烧结生产流程部分将详细描述原料准备、配料混合以及成型与压制这三个主要步骤。
然后,在烧结工艺细节描述部分,阐述了烧结炉设备的类型和特点、温度控制的方法和关键因素,以及如何选择适当的燃料并进行调节。
最后,在结论中对整篇文章进行总结,并强调了烧结生产流程与工艺细节的重要性。
1.3 目的本文的目的是向读者全面介绍烧结生产流程与工艺细节,并强调其对最终产品质量和性能的影响。
通过详细描述每个步骤和关键要素,读者将了解到如何正确操作和控制烧结工艺以获得优质的成品。
此外,本文还旨在提高读者对烧结技术的认识和理解,为相关领域的从业人员提供一份有价值的参考资料。
2. 烧结生产流程烧结生产流程是指将粉末状原料通过热处理,使其在一定温度下发生化学反应和物理变化,形成固体块状的工艺过程。
下面将详细介绍烧结生产流程的三个主要步骤:原料准备、配料混合以及成型与压制。
2.1 原料准备在烧结生产中,首先需要对原料进行准备。
通常,原料主要包括金属粉末、陶瓷粉末或其他颗粒物质。
这些原料必须经过检测和筛分等处理程序,以确保其质量符合标准要求。
原料的选取和准备对于最终产品的性能具有重要影响。
2.2 配料混合在完成原料准备后,需要进行配料混合阶段。
这一步骤旨在将不同种类的原料按比例混合均匀,以获得所需的化学成分组成。
通常采用机械或化学方法进行混合,在此过程中需要严格控制各种原料的比例和混合时间。
- 1、下载文档前请自行甄别文档内容的完整性,平台不提供额外的编辑、内容补充、找答案等附加服务。
- 2、"仅部分预览"的文档,不可在线预览部分如存在完整性等问题,可反馈申请退款(可完整预览的文档不适用该条件!)。
- 3、如文档侵犯您的权益,请联系客服反馈,我们会尽快为您处理(人工客服工作时间:9:00-18:30)。
1文献综述1.1烧结生产概况1.1.1烧结及其发展烧结法是迄今为止除北美以外使用最为广泛的铁矿石造块方法。
自20世纪80年代起烧结技术得到了快速发展,主要体现在烧结工艺和新技术的研究开发和应用上。
烧结工艺方面如自动化配料、混合料强化制粒、偏析布料、冷却筛分、整粒技术及铺底料技术等;新技术主要表现为球团烧结技术、小球烧结技术、低温烧结技术等。
上述工艺和技术目前已经在大部分钢铁企业推广应用,并取得了显著的经济效益。
1897年,T.Huntington和F,Heberlein申请并注册了第一个有关烧结方面的专利。
1905年,E.J.Savelsberg首先把T.Huntington-F.Heberlein烧结杯用于铁矿石烧结,从而开辟了烧结法进行铁矿粉造块的新纪元。
在当今的冶金生产中,烧结已成为一道重要的单元工序并占有相当重要地位。
据统计,全世界约有一半的生铁是用烧结矿生产的。
过去十年中,世界上烧结矿年产量维持在538×106t~586×106t范围内。
从1989年起,由于独联体和其他部分东欧国家发生巨变,因此,它们的钢铁工业进行了重新调整,导致烧结矿产量有所下降。
欧洲和日本的经济衰退也影响了产量,但是不久烧结矿的产量又慢慢恢复。
东欧和独联体的产量将下降,而中国、朝鲜和台湾的产量将继续上升。
尽管出现新的炼铁工艺,但是在下一个十年中或更长的时间内,它们仍不可能对高炉产量有巨大影响。
因此,烧结矿产量在未来相当长的时间内仍将维持在目前水平。
1.1.2烧结生产目的铁矿粉烧结是一种铁矿粉造块的方法,是将细粒含铁物料与燃料、熔剂按一定比例混合,再加水润湿、混匀和制粒成为烧结料,加于烧结设备上,点火、抽风,借助燃料燃烧产生高温和一系列物理化学变化,生成部分低熔点物质,并软化熔融产生一定数量的液相,将铁矿物颗粒润湿粘结起来,冷却后,即成为具有一定强度的多孔块状产品一侥结矿。
烧结生产的目的主要是:1.将粉状物料制成具有高温强度的块状料以适应高炉冶炼、直接还原等在流体力学方面的要求;2.通过烧结改善铁矿石的冶金性能,使高炉冶炼指标得到改善;3.通过烧结去除某些有害杂质,回收有益元素以达到综合利用资源和扩大炼铁矿石原料资源的目的。
1.1.3烧结反应过程烧结反应过程是分层依次向下进行的。
抽入的空气通过已烧结好的热烧结矿层预热,在燃烧层中使固体碳燃烧,放出热量,获得高温(1300℃~1600℃)。
料层在加热过程中,熔点较低部分首先出现液相,将周围物料浸润和熔融,相邻液滴产生聚合,引起收缩和形成气孔,并在冷却过程中固结和产生结品,成为具有一定强度的多孔烧结块。
烧结过程中基本的液相是硅酸盐和铁酸盐体系。
从燃烧层下抽出的高温废气,经预热干燥层,将热量传给烧结料,使烧结料着火,将料中的游离水和化合水蒸发和分解。
废气继续下行,温度继续降低,其中水分又重新凝结,使物料过湿。
如将烧结料预热到一定温度,可以消除过湿现象。
1.2烧结矿的烧结特性烧结矿的质量主要指它的冷态强度和冶金性能。
冷态强度主要指机械强度;冶金性能主要指还原性、低温还原粉化性、高温软化和熔滴性。
烧结特性的研究是研究烧结矿的矿物组成和微观结构及其生成机理和对外部工艺条件的依赖关系,以便在烧结生产中有目的的控制烧结的反应过程和微观结构,以提高烧结矿的质量。
众所周知,由于高炉是逆流工艺,固体炉料相对上升气流而下降,所以必须供应块状的含铁炉料。
因此,必须通过烧结法或球团法将粉块造成块状。
烧结矿是高炉炼铁的基本原料之一,高炉生产要想实现良好的运行,就必须要求炉料具有较高的冷态强度和良好的冶金性能。
1.2.1机械强度机械强度指烧结矿在自然条件下的强度,一般用转鼓指数或落下指数表示。
烧结矿转鼓指数与高炉冶炼指标有密切的关系。
西德克虏伯公司NO7及NO8高炉的生产实践说明:烧结矿的机械强度与高炉产量存在着较好的线性关系;石钢提高烧结矿强度的工业实验表明:烧结矿强度上升 4.35%,则高炉利用系数提高0.116t/(m3·d),焦比下降28kg/t。
因此要提高高炉冶炼指标,就必须提高烧结矿的机械强度。
烧结矿的强度是受多方面影响的,主要有以下几点:1.原料破碎粒度一些研究者指出,如果原料破碎粒度较大,就会导致它们在烧结过程中不可能熔融。
如石灰的残余物遇水以后形成Ca(OH)2,使烧结矿破裂。
2.单个矿物的强度Loo等人研究了不同矿物的破裂强度,发现矿物强度按下列顺序递减:原生赤铁矿>次生赤铁矿>磁铁矿>SFCA>玻璃质。
也就是说,在所有的矿物中玻璃质的强度是最低的。
因此要使烧结矿强度增加,就要从结构消除这些玻璃质以及尽可能使它转变为结晶体。
3.烧结矿的矿物组成烧结矿是一个由多种矿物组成的复合体。
一般说来,烧结矿的矿物组成为:含铁矿物是磁铁矿、浮士体、赤铁矿;粘结相中有铁橄榄石、钙铁橄榄石、硅灰石、硅酸二钙、硅酸三钙、铁酸钙和钙铁硅石。
但是根据原料条件及烧结工艺条件的不同,其矿物组成各异。
如当铁矿脉石中氧化镁含量较高时,会出现新的矿物:钙镁橄榄石、镁黄长石及镁蔷薇辉石等,它们会使硅酸二钙生成量相对减少,粘结相增加且固溶于硅酸二钙中,对β硅酸二钙相变有稳定作用。
这些都有助于提高烧结矿的强度。
1.2.2还原性还原性是冶金性能的基础,烧结矿还原性对高炉冶炼,尤其对加强稳定性和降低焦比有很大影响,许多冶金工作者进行了大量的研究工作,发现还原度和烧结矿矿物结构、矿物组成及碱度有很大的关系。
1.烧结矿的矿物结构对还原性的影响磁铁矿是主要的含铁矿物,晶粒细小密集而粘结相少的磁铁矿容易还原;而大块磁铁矿或者被硅酸盐包裹时均难还原或者只是表面还原。
另外气孔率高(大孔和微孔)晶体嵌布松弛以及裂纹多的组织也容易还原。
2.烧结矿的矿物组成对还原性的影响赤铁矿和磁铁矿作为主要的含铁矿物,它们都能还原成浮士体,但进一步还原成金属的速度不同[24J。
赤铁矿还原的浮士体能均匀、迅速地还原,即使其中一部分被金属所包裹。
而磁铁矿还原的浮士体的还原是表面的化学过程,几乎所有的颗粒被金属迅速包裹,阻止了进一步还原。
SFCA的还原性与其形态、气孔率以及它是否在玻璃体中有关。
低温下生成的针状SFCA较易还原,而高温下生成的柱状SFCA难于还原。
Bristow等人研究了气孔率对还原率的影响,发现SFCA稳固了还原过程中产生的气孔,导致气孔率和还原度增加。
3.二烧结矿的碱度对还原性的影响在碱度特别低的烧结矿中,由于液相少,含铁矿物暴露面积大,因而有较好的还原性。
随着碱度的提高(超过酸性烧结矿,一般在1.0以上),烧结矿的气孔率增加,难还原的铁橄榄石被钙铁橄榄石所代替,烧结矿的还原性也就变好。
有些烧结矿在碱度2.0以上时,还原性又变坏,这可能由于相对还原性差的铁酸二钙出现的缘故。
1.2.3低温还原粉化性低温还原粉化性能是指铁矿石在低温还原条件下矿石还原粉化性能,它是衡量铁矿石在高炉上部块状带性能的一项指标,对高炉冶炼具有极大的影响。
国外研究表明,烧结矿RDL3.15,每提高5%,焦比增加约3kg,生铁产量下降1.5% ~5%。
另外,烧结矿低温还原粉化对炉龄、炉墙及热损失都有很大的影响。
冀东铁矿粉粒度粗,含Si和A12O3高,含P低,极易发生低温还原粉化现象,所以研究烧结矿发生低温还原粉化的机理及影响因素是非常重要的。
烧结矿发生低温还原粉化的最根本原因是烧结矿中的再生三氧化二铁在低温(450℃~550℃)时,由α-Fe2O3还原成γ-Fe3O4。
由于前者为三方晶系六方晶格,而后者为等轴晶系立方晶格,在还原气体的作用下发生了晶格的改变,造成了结构的扭曲,产生极大的内应力,导致在机械作用下严重的破裂。
影响烧结矿发生低温还原粉化的因素主要有微观组织结构、烧结矿碱度和其它成分(如MgO,A12O3,FeO和TiO2)。
1.2.4高温软化及熔滴性在过去20年中.由于日本和德国对运转的高炉进行熄火和解剖研究,人们对高炉内部状态的了解在本质上大大增加。
这些研究发现炉料在软熔带上部开始软化,在软熔带下部开始熔融。
由炉料软化到开始滴落这个区间形成一个与焦炭层交替的软熔带,其透气性很不好.因此高炉内软熔带对高炉操作,尤其对生产率有显著影响。
一个窄的软熔带,即软化和熔融之间的温度区间小在实际高炉操作中是非常必要的。
所以对软熔带内炉料的高温软化及熔滴性能进行研究具有重要的意义。
1.MgO对高温性能的影响在烧结混合料中添加MgO将大大改善烧结矿的高温性能。
这主要是由于MgO提高了烧结矿软化和熔融温度,增加了烧结矿在高温还原过程中料层的透气性。
2.碱度对高温性能的影响由于提高碱度能导致较高的熔化温度和较低的气流阻力,因此提高碱度能改善烧结矿高温性能。
一些研究指出烧结矿碱度对达到软熔带的初始还原度有重要影响,当碱度超过1.4时,还原度达到最大值。
Beppler等人也提出碱度提高到1.7以上将导致软熔带较宽。
1.3烧结矿的矿物组成和显微结构对其质量的影响烧结矿的质量主要表现在它的强度、还原性及低温还原粉化性上,它们与粘结相的发展程度、结晶条件、粘结相矿物的强度和还原性等有关。
由于液相冷却析晶时,浓度及温度的不均匀性以及矿物本身的特点不同,各种集合体可以以树枝状、针状、柱状、片状,板状等形式凝固组成,而这些不同形状的集合体的强度和还原性又有很大的差别,因此烧结矿冷凝时形成的矿物组成及其结构对烧结矿的性能有着重要的影响。
1.3.1烧结矿中不同矿物组成和显微结构对其强度的影晌1.烧结矿中各种矿物自身强度对其强度的影响近几年来国内外学者对烧结矿中各种矿物的机械强度作了大量的研究工作,发现烧结矿中的磁铁矿、赤铁矿、铁酸一钙、铁橄榄石、铁黄长石有较高的抗压强度,其次则为钙铁橄榄石、钙镁橄榄石及铁酸二钙,在钙铁橄榄石中,当χ=1.0时,其抗压性、耐磨性及脆性的指标均与前一类接近或超过,当χ=1.5时,其强度相当低。
而且易产生裂纹,它的晶格常数接近于2CaO·SiO2。
研究表明:铁酸钙的抗压强度为363N/cm2,玻璃相仅为45N/cm2。
因此在烧结矿的结构中应尽量减少玻璃相的形成,这有利于提高烧结矿的强度。
2.烧结矿在冷却过程中产生的内应力对其强度的影响在冷却过程中,产生不同的内应力:1)由于烧结矿表面与中心存在温差而产生的热应力。
这种应力主要取决于冷却条件,可采用缓冷或热处理的方法来消除。
2)烧结矿中各种不同矿物具有不同热膨胀系数,因而引起各矿物之间的应力,因此减少烧结矿中的矿物组分,有利于提高烧结矿强度。
3)熔剂性烧结矿中硅酸二钙在冷却中的多晶转变所引起的相变应力。
通常在熔剂性烧结矿中主要出现介β-C2S和γ-C2S。
当β-C2S在冷却转变为γ-C2S时,由于相变,体积膨胀10%,因而产生极大应力,导致烧结矿自动粉碎。