烧结工艺及设备
烧结工艺及余热发电简介
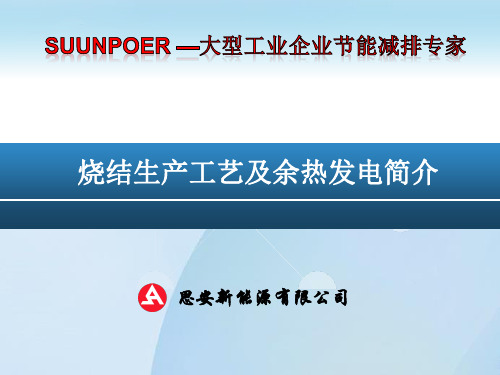
烧结余热回收段
序号
回收利用
1 用作点火、保温炉的助燃 空气
2 用于预热混合料
3 用于余热锅炉产蒸汽
4 用于余热发电
西安思安新能源有限公司
• 烧结中可广泛利用各种含铁粉尘和废料,扩大了矿石资 源,又改善了环境。因此自上世纪50年代以来,烧结生 产获得了迅速发展。
西安思安新能源有限公司源有限公司
2、 烧结反应过程
• 目前世界各国90%以上的烧结矿由抽风带式烧 结机生产,其他烧结方法有回转窑烧结,悬浮 烧结,抽风或鼓风盘式烧结和土法烧结等。
为使烧结的物料物性性质充分均匀,使烧结料内微粒物料造成 适宜的小球,在配料后设置混合工序。 一次混合的目的在于混匀,在沿混合机的长度方向均匀加水, 二次混合主要作用是造球,给水位置设在混合机的给料端。
西安思安新能源有限公司
2.4.5 设备(梭式布料机)
1、采用铺底料可以保护台车、 保证料层烧透、减少烧结烟气 含尘量。
烧结工艺过程及其设备
西安思安新能源有限公司
4、烧结工艺过程及其设备
1、烧结原、燃料及烧结矿 3、烧结 5、烧结矿冷却
2、配料 4、烧结饼破碎和筛分 6、烧结矿整粒和成品矿贮存
西安思安新能源有限公司
烧结前段工艺
烧结前段工艺流程
西安思安新能源有限公司
设备(料仓)
西安思安新能源有限公司
设备(混合机)
★烧结工艺设备环视
西安思安新能源有限公司
设备(烧结机)
西安思安新能源有限公司
烧结操作规程

烧结操作规程烧结操作规程一、烧结工艺概述烧结是一种将粉末颗粒在一定条件下通过加热使之相互融结并形成致密块体的工艺。
烧结操作规程是制定和规范烧结工艺的操作指南,通过严格执行操作规程,可以保证产品的质量稳定性和生产效率。
二、操作准备1. 烧结设备检查:检查烧结设备的各项参数和设备运行状态,确保设备正常工作。
2. 确定烧结工艺参数:根据产品要求和烧结设备的特性,确定烧结温度、时间、气氛和加热速率等工艺参数。
三、烧结操作步骤1. 入炉准备:将待烧结的物料按照工艺要求整理,清除表面杂质和水分。
然后将物料放入烧结炉,注意排列均匀,避免堆积过高或堆积不均匀。
2. 炉温升温:根据烧结工艺参数,将炉温逐渐升高至目标温度。
升温速率应控制在合理范围内,避免过快或过慢。
3. 保温烧结:当炉温升至目标温度后,保持一段时间进行保温烧结。
保持时间应根据具体产品的要求确定,一般在30分钟至2小时之间。
4. 炉温冷却:保温烧结完成后,将炉温逐渐降低至室温,冷却速率应适中,避免过快或过慢引起断裂或变形。
5. 取出产品:炉温冷却至室温后,打开烧结炉门,小心取出产品。
产品应进行质量检查,记录烧结参数和产品质量情况。
四、操作注意事项1. 操作人员应熟悉烧结工艺和设备操作规程,并佩戴相关的个人防护用品。
2. 物料应按照规定的品种、数量和质量进行装载和放置。
3. 炉温升降速率应根据具体物料和工艺要求合理确定,避免产生过快或过慢的冷却速度。
4. 在烧结过程中应定期监测和记录烧结设备和产品的温度、压力、气氛和形态等参数。
5. 若出现设备故障或异常情况,应及时停机检修或采取相应的应急措施,保证人员和设备安全。
6. 完成烧结后,应及时清理烧结炉和相关设备,做好设备维护和保养工作。
五、操作规程的执行和改进1. 烧结操作规程应由指定的技术人员编写,并明确操作人员的职责和权限。
2. 操作规程的执行应由质量管理部门进行监督和检查,确保操作的合规性和可靠性。
烧结工艺

四、180㎡烧结工艺流程图
第二讲 供料系统
一、烧结料组成
含铁料:精矿粉200目以下占60%以上 (考虑成球性)、富矿粉 (5~8mm,烧结中的骨架)、其他(炉尘、轧钢皮等)要求含铁原料 品位高,成分稳定,杂质少。 熔剂:以生石灰(CaO)为主, CaO ↑1%,烧结产量↑ 3%.要求有效 CaO含量高,杂质少,成分稳定,含水3%左右,粒度小于3mm的占85 %以上。 燃料:焦粉、无烟煤3~5%。要求是固定碳含量高,灰分低,挥发分低, 含硫低,成分稳定,含水小于10%,粒度小于3mm的占85%以上。
返矿:机尾筛下物(粒度小于5mm)
二、燃料破碎室
燃料破碎室设有两个燃料破碎系列,一个系列生产,一个系列备 用。每个系统生产能力为~45t/h,每个系列由1台Φ1200×1000对辊 破碎机和1台Φ1200×1000四辊破碎机组成,破碎后3~0mm合格粒级 燃料由胶带机送往配料室。 从一次料场来的燃料(25~0mm)由胶带机运至燃料破碎室顶部, 由可逆胶带机送至两个有效容积为180m³ 分配仓,每个仓下设有给料 闸门、给料胶带机和带式除铁器,将需破碎的燃料给至Φ1200×1000 对辊破碎机,进行粗破碎,将燃料破碎至10~0mm。每台对辊破碎机 下设臵一条胶带机,将经过粗破碎的燃料给至Φ1200×1000四辊破碎 机,进行细破碎,将燃料破碎至3~0mm。3~0mm合格燃料由胶带机送 往配料室。
主要技术参数 处理量:400t/h(正常)、480t/h(最大); 有效烧结长度:60m; 有效烧结面积:180m2; 台车数量:155; 台车规格:1.0×3.0×0.75m; 台车运行速度:1.3~3.9m/min; 栏板高度:0.75m; 头尾轮中心距:72745mm; 头尾轮节圆直径:3098.52mm; 主传动电机(变频调速)18.5kW×2; 圆辊给料机:Φ1282×3046,15kW; 原料给料料槽:30m3; 九辊布料机:7.5kW×2; 铺底料料槽:30m3。
烧结工艺的主要设备及其工作原理

烧结工艺的主要设备及其工作原理烧结技术是一种重要的粉末冶金技术,用于制备具有高密度和优异性能的金属、陶瓷和复合材料。
在烧结过程中,粉末颗粒通过热源和压力相互结合,形成致密的固体制品。
以下是烧结工艺的主要设备及其工作原理的详细介绍。
1.烧结炉烧结炉是烧结工艺中最关键的设备之一、它提供了所需的高温环境,使粉末颗粒能够熔融和结合成固体制品。
烧结炉通常由加热区、保温区和冷却区组成。
粉末颗粒在加热区内迅速升温,到达熔点后开始熔融和结合成形,然后在保温区内维持一定的温度和时间以确保完全烧结,最后在冷却区中冷却至室温。
2.加热元件加热元件是烧结炉的重要组成部分,用于提供高温环境。
常用的加热元件包括电阻线圈、电阻片和电炉管。
当通电时,加热元件会产生热量,将烧结炉内的温度升高到所需的烧结温度。
3.压力设备压力设备用于施加压力,使粉末颗粒之间发生变形和结合。
常见的压力设备包括冷压机、热压机和等离子压机等。
在烧结工艺中,压力可以促进粉末颗粒的扩散和结合,提高制品的致密性和强度。
4.模具模具用于塑造和限制粉末颗粒的形状和尺寸。
它们通常由金属或陶瓷制成,并具有所需的形状和孔结构。
在烧结过程中,粉末颗粒被放置在模具中,并在加热和压力的作用下,与模具中的空隙形成制品。
5.辅助设备在烧结工艺中,还需要一些辅助设备来辅助完成烧结过程,例如真空泵、气体循环系统和温度控制系统等。
真空泵常用于制备气密陶瓷制品,通过减少压力,可以排出气体和提高制品的致密性。
气体循环系统能够提供一种具有控制气氛的环境,以改善烧结反应的进行。
温度控制系统能够监测和调节烧结炉的温度,使其能够稳定控制在所需的温度范围内。
总的来说,烧结工艺的主要设备包括烧结炉、加热元件、压力设备、模具和辅助设备等。
烧结工艺的工作原理是通过高温和压力作用下,粉末颗粒之间发生扩散和结合,形成致密的固体制品。
这些设备与技术的应用使得粉末颗粒能够成功烧结形成优质的制品,广泛应用于航空航天、汽车、电子和医学等领域。
烧结工艺及设备
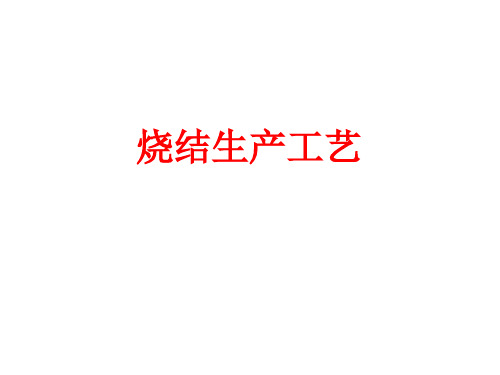
(5)其他烧结物料粒度 往往含有砖、石等夹杂物,应筛除,使之<10mm,以利配料、混匀
6.2烧结配料
6.2.1配料目的、要求、方法
目的: 使烧结矿的成分、物理性能、化学性能符合要求且稳定 控制配合料有害元素含量 使烧结料具有良好透气性,以获得较高的生产率
t 混合
L 有效
D 有效 2
• 2n 转速
• tan 前进
L 有效
D有效iN 临界转速 • sin 前进
L 有效
42.3
D有效i • D有效
• sin 安息 sin 倾角
i 一次= 0.2 ~0.3 i 二次= 0.25~0.35
增加混合机长度,无疑延长混合时间,有利于混匀和制粒。 一次混合机长度 9~14m 二次混合机长度12~18m 大型混合机长度21~26m,直径4~5m
远离燃料颗粒区域,温度低,烧结不均匀,出现夹生料, 强度差
布料时易偏析,使下层燃料多,温度过高,过熔、粘结篦条,返矿增多
太细: V燃↑,燃烧带过窄,温度降低,高温反应来不及进行, 烧结矿强度↓ ,返矿量↑ ,生产率↓
焦粉: 0.5~3mm 无烟煤: 0.5~4mm
(4)返矿粒度 来源:强度差的小块烧结矿 未烧透的烧结料 未烧结的 生料
烧结生产工艺
中和粉
6.1烧结原料的准备与处理
6.1.1原料的接受、储存、中和 原料的接受:进厂原料必须验货(品名、品种、产地、数量、性能)
(1)处在沿海并主要使用进口原料的大型烧结厂 采用大型专用轮船运输 有专门的卸料码头和大型高效的卸船机 卸下的原料直接由皮带运输机运至原料场
(2)距选矿厂较远的内陆大型烧结厂 采用火车运输或者轮船运输 可采用翻车机接受精矿、粉矿和块状石灰石等原料 生石灰可采用密封罐车或风动运输 辅料可用受料槽接收
烧结设备及工艺技术

不可避免的,但严重的跑偏会加大传动装置负载、台
台车跑偏示意图
车轮轴承损坏、轨道变形,必须及时处理。
如果是由安装质量引起的,可以从台车走行轨道的安
装尺寸、给矿侧大星轮中心线位置、尾部滑动摆架、
台车运行中有无刮碰处等方面处理。如果是由于设备
部件磨损等问题引起台车跑偏,必须要仔细从机械原
理上分析,寻找原因,从根本上解决烧结机组台车跑
三、烧结设备介绍
☞圆筒混合机
圆筒混合机是烧结生产工艺流程中
的重要设备之一,它的主要作用是将配
好的各种烧结原料进行润湿、混匀和制
粒,强化烧结料组分均匀,保证烧结过 程中的物理、化学性质一致。通过混匀
胶轮传动式混合机( 90、180m2烧结采用)
制粒还可以提高混合料在烧结过程中的
透气性,已获得高产、优质、低耗的成
永远不要对客户说不,客户需求就是我们的追求!
-10-
三、烧结设备介绍
☞配料设备—圆盘给料机
故障点:
1、蜗壳短管磨损,造成漏料严重,雨天
易喷料,特别是雨季,问题更加严重。
2、蜗壳短管及悬挂漏斗摆动严重,多出
现在更换蜗壳短管或悬挂漏斗之后,故
障原因为蜗壳短管中心与圆盘盘面中心 偏离较大引起。
圆盘给料机结构示意图
永远不要对客户说不,客户需求就是我们的追求!
-7-
二、烧结工艺流程
●原料准备与配料系统 目的:将铁矿粉、熔剂、燃料、附加物(轧钢皮、 钢铁厂回收粉尘)及返矿按照一定比例进行配料, 保证烧结矿的含铁量、碱度、S含量、FeO等主要 成分控制在规定范围内。 常用的配料方法:容积配料法和质量配料法 ●混合布料系统: 目的:使烧结料的成分均匀,水分合适,易于造 球,从而获得粒度组成良好的烧结混合料,以保 证烧结矿的质量和提高产量。 混合作业:加水润湿、混匀和造球。 一次混合的目的:润湿与混匀。 二次混合的目的:继续混匀,造球,以改善烧结 料层透气性。 ●点火烧结 目的:获得化学成分和物理性质稳定的烧结矿, 满足高炉冶炼的要求。 烧结作业:烧结台车上的物料,经点火炉进行料 面点火,从料面开始烧结,并在强制通风的情况 下使混合料中配入的燃料从上至下燃烧达到烧结 的目的,形成烧结矿。 ●烧结矿的处理: 目的:获得粒度均匀,温度适中的烧结矿,满足 高炉料入炉需求。 处理作业:对烧结矿进行破碎筛分,使烧结矿粒 度均匀和除去部分夹生料,为高炉冶炼创造有利 条件,筛子选用双层筛,其中6mm以下的作为返 矿进入配料,6-20mm作为铺底料,20mm以上进入 高炉矿仓。
烧结工艺及布局简介
烧结工艺操作 燃烧性和反应性,燃烧与反应速度过快, 燃烧性和反应性,燃烧与反应速度过快,高温保持时 间短,产生夹生料;若燃烧和反应速度过慢, 间短,产生夹生料;若燃烧和反应速度过慢,则燃料 不能充分燃烧,料层得不到必要的高温, 不能充分燃烧,料层得不到必要的高温,也会使烧结 矿的质量变差, 矿的质量变差,燃烧性和反应性取决于燃料的种类和 粒度。如焦粉的反应性接近于传热速度,无烟煤的反 粒度。如焦粉的反应性接近于传热速度, 应性一般偏高,故在使用燃料时, 应性一般偏高,故在使用燃料时,应注意其适宜的粒 度和用量。 度和用量。 (2)、具有良好的热稳定性: )、具有良好的热稳定性: 具有良好的热稳定性 热稳定性指煤受热后爆裂的情况。 热稳定性指煤受热后爆裂的情况。层状或片状结
烧结知识简介
现代烧结生产的特点
现代烧结生产的特点在连续作业, 现代烧结生产的特点在连续作业,大体上分为原 料准备和烧结两个部分。烧结主作业线是从配料开始, 料准备和烧结两个部分。烧结主作业线是从配料开始, 包括配料、混料、烧结、 包括配料、混料、烧结、冷却及成品烧结矿整粒几个 主要环节,作业线长达数百米。在烧结机上进行的烧 主要环节,作业线长达数百米。 结过程持续时间不长,在几十分钟内完成点火、 结过程持续时间不长,在几十分钟内完成点火、燃料 燃烧、传热和各种液相生成及冷却和再结晶过程。 燃烧、传热和各种液相生成及冷却和再结晶过程。烧 结机大型化有利于提高生产率和降低单位成本。 结机大型化有利于提高生产率和降低单位成本。
烧结工艺操作 量超过8%,渣难熔而不易流动。因此矿石中Al 量超过8%,渣难熔而不易流动。因此矿石中Al2O3 渣难熔而不易流动 要加以控制。一般矿石中SiO 比不宜大于2 要加以控制。一般矿石中SiO2/ Al2O3比不宜大于2 ~3。 铁矿石中常见的有害杂质时硫、 铁矿石中常见的有害杂质时硫、磷、砷以及铜、 砷以及铜、 锌、钾、钠等。这些有害杂质要少。 钠等。这些有害杂质要少。 硫在钢铁中以FeS形态存在招致“热脆” FeS形态存在招致 硫在钢铁中以FeS形态存在招致“热脆”。 磷和铁结合生成化合物Fe3P, Fe3P,此化合物和铁形成 磷和铁结合生成化合物Fe3P,此化合物和铁形成 二元共晶Fe3P Fe,导致钢材“冷脆” Fe3P- 二元共晶Fe3P-Fe,导致钢材“冷脆”。
烧结厂工艺流程及设备
烧结厂工艺流程及设备
当然没问题,咱们就说人话,把烧结厂那套事儿说得通俗点:
想象一下你在烤饼干,烧结厂的工作差不多就是这个原理,只不过是放大版的,而且烤的是石头饼干——烧结矿。
首先,你得把原材料准备好,比如铁矿粉啊,焦炭啊,还有石灰石啊,这些就像是你做饼干要用的面粉、糖和盐。
接着,把这些原料按照秘方混合均匀,就跟调面糊一样,还得加点水,让原料变成小颗粒,这样烤出来才香。
然后,这些混合好的小颗粒会被铺在一条超长的烤盘上,这条烤盘会慢慢地通过一个巨大的烤箱,也就是烧结机。
烤箱底下有风吹过,上面的小颗粒就被热气给粘成大块了。
等“饼干”烤好了,得让它凉快凉快,所以会有专门的设备给它降温。
这有点像你刚烤完饼干,得放凉了才能吃。
接下来,这些大块的“饼干”得被捣碎,筛一筛,好的“饼干”送去炼铁厂,那些碎的或者太小的就得重新加工,就像你做的饼干太硬或者太碎,得重新来过。
最后,为了不让烤饼干的时候弄得到处都是烟尘,还得有吸尘器一样的设备,把灰尘都吸走,保护环境嘛。
这就是烧结厂的大致流程,用的设备也都是工业级别的,效率高,自动化程度强。
希望这么说你能听懂,有啥不明白的,咱再聊!。
第5章 烧结工艺及设备
三氧化二铁,又称为赤铁矿、红矿, Fe2O3:三氧化二铁,又称为赤铁矿、红矿,一般 粉矿多以赤铁矿为主。 粉矿多以赤铁矿为主。
Fe3O4:又称为磁铁矿、黑矿,一般精矿多以磁铁 又称为磁铁矿、黑矿, 矿为主。磁铁矿的化学分子式可视为Fe +FeO, 矿为主。磁铁矿的化学分子式可视为Fe2O3+FeO, 其中FeO称为氧化亚铁,简称为亚铁。 FeO称为氧化亚铁 其中FeO称为氧化亚铁,简称为亚铁。在烧结生 产中, 产中,烧结矿的亚铁含量与烧结燃耗和烧结矿质 量密切相关, 量密切相关,因此亚铁是烧结工艺的一个重要指 标。
铅
铜 砷
钛
钾, 钠 氟
易挥发,在炉内循环累积,造成结瘤,降低焦炭及矿石的强度。 易挥发,在炉内循环累积,造成结瘤,降低焦炭及矿石的强度。 氟高温下气化,腐蚀金属,危害农作物及人体, 侵蚀破坏炉衬。 氟高温下气化,腐蚀金属,危害农作物及人体,CaF2侵蚀破坏炉衬。
冶金与材料工程学院
TFe:全铁, TFe:全铁,指物料中以各种化合物形态存在的 铁的总和。又称为含铁原料的含铁品位。 铁的总和。又称为含铁原料的含铁品位。烧结矿 的全铁越高,高炉的产量越高,渣量低,焦比低。 的全铁越高,高炉的产量越高,渣量低,焦比低。 过高的含铁品位可能导致烧结矿强度的降低 的含铁品位可能导致烧结矿强度的降低。 但过高的含铁品位可能导致烧结矿强度的降低。 由于烧结矿和含铁原料中,铁多以Fe 由于烧结矿和含铁原料中,铁多以Fe2O3和Fe3O4 形式存在,因此烧结矿和含铁原料化验TFe FeO, TFe和 形式存在,因此烧结矿和含铁原料化验TFe和FeO, TFe和FeO可计算 可计算Fe 的含量. 由TFe和FeO可计算Fe2O3和Fe3O4的含量.
冶金与材料工程学院
冶金自动化之烧结球团工艺流程及主要设备简介
烧结工艺流程介绍————冶金自动化系列专题【导读】:为了保证供给高炉的铁矿石中铁含量均匀,并且保证高炉的透气性,需要把选矿工艺产出的铁精矿制成10-25mm的块状原料.铁矿粉造块目前主要有两种方法:烧结法和球团法.两种方法所获得的块矿分别为烧结矿和球团矿。
本专题将详细介绍烧结生产的工艺流程,主要工艺设备的工作原理以及控制要求等信息,其次,我们将简要介绍球团法生产的工艺流程,主要工艺设备的工作原理以及控制要求等信息.由于时间的仓促和编辑水平有限,栏目中难免出现遗漏或错误的地方,欢迎大家补充指正。
铁矿粉造块的目的:◆综合利用资源,扩大炼铁用的原料种类。
◆去除有害杂质,回收有益元素,保护环境.◆改善矿石的冶金性能,适应高炉冶炼对铁矿石的质量要求。
铁矿粉造块的方法:烧结法和球团法。
铁矿粉造块后的产品:分别为烧结矿和球团矿。
(供高炉炼铁生产的主要原料)一、烧结生产的工艺流程介绍:烧结是钢铁生产工艺中的一个重要环节,它是将铁矿粉、粉(无烟煤)和石灰、高炉炉尘、轧钢皮、钢渣按一定配比混匀.经烧结而成的有足够强度和粒度的烧结矿可作为炼铁的熟料。
利用烧结熟料炼铁对于提高高炉利用系数、降低焦比、提高高炉透气性保证高炉运行均有一定意义。
烧结生产的流程目前生产上广泛采用带式抽风烧结机生产烧结矿.烧结生产的工艺流程如图下所示。
主要包括烧结料的准备,配料与混合,烧结和产品处理等工序。
(附件五铁矿粉烧结工艺流程简介)烧结的原材料准备:含铁原料:含铁量较高、粒度<5mm的矿粉,铁精矿,高炉炉尘,轧钢皮,钢渣等。
一般要求含铁原料品位高,成分稳定,杂质少。
熔剂:要求熔剂中有效CaO含量高,杂质少,成分稳定,含水3%左右,粒度小于3mm的占90%以上。
在烧结料中加入一定量的白云石,使烧结矿含有适当的MgO,对烧结过程有良好的作用,可以提高烧结矿的质量。
燃料:主要为焦粉和无烟煤.对燃料的要求是固定碳含量高,灰分低,挥发分低,含硫低,成分稳定,含水小于10%,粒度小于3mm的占95%以上。
- 1、下载文档前请自行甄别文档内容的完整性,平台不提供额外的编辑、内容补充、找答案等附加服务。
- 2、"仅部分预览"的文档,不可在线预览部分如存在完整性等问题,可反馈申请退款(可完整预览的文档不适用该条件!)。
- 3、如文档侵犯您的权益,请联系客服反馈,我们会尽快为您处理(人工客服工作时间:9:00-18:30)。
转速过大:筒体所产生的离心力太大,使物料紧贴在筒壁上, 以致完全失去混匀制粒作用。
转速适当:物料在离心力作用下带到一定的高度, 而后在自身重力作用下跌落下来, 如此反复滚动,以达到最佳的混匀制粒效果。
●混合机长度与混合时间
要求: 通过混合设备实施混合,达到混合目的
段数: 生产中采用的有一段混合和两段混合,有的还有三段混合 根据原料性质合理选择混合段数
●一次混合:加水润湿、混匀,使混合料的水分、粒度、组分分布均匀 当加入热返矿时,可预热混合料 当加入生石灰时,可使CaO消化、预热混合料、制粒
●二次混合:混匀、制粒 (使细粒物料粘附在核粒子上,形成粒度大小一定的拟似粒子) 还可通蒸汽预热混合料
2. 简易理论计算法 ●特点
准确 快 适用于少量原料种类(≤3) ●原理 物质守恒定律 ●计算的内容 计算:生产100 kg烧结矿需各种原、燃料的用量 计算:用上述原、燃料配比生产出烧结矿的化学成分,并校核 计算:配料室内各矿槽下电子皮带秤的每米皮带料量
●计算前须具备的条件 原、燃料的化学成分(其中元素含量按其存在形态折算成相应化合物含量) 由烧结试验、生产实践提供的有关经验数据 产品烧结矿的质量指标
制粒效果
制粒前后某一粒级产率的增量来表示 制粒前后混合料平均粒度的增值来表示
6.4烧结操作制度
6.4.1布料要求与方法 (1)布铺底料
粒度: 一般10~20mm的烧结矿
厚度: 约20~40mm
作用: ●防止燃烧带高温与篦条直接接触,既保证烧好烧透,又保护篦条、 延长篦条使用寿命、减少篦条消耗 ●防止细粒料、烧结矿堵塞或粘结篦条,减少散料,减轻清理篦条的 劳动强度 ●保持篦条的有效抽风面积不变,均匀气流分布,减少抽风阻力 ●起过滤作用,防止细粒料进入抽风系统,减少烟气含尘量,降低除 尘负荷,延长风机转子使用寿命
●步骤 ① 设生产100 kg烧结矿需各种原、燃料的用量为Qi ② 列平衡方程 TFe平衡方程
10•0TF烧e Qi •TFi e i
R平衡方程
Q i • CaO i
R 烧
Hale Waihona Puke iQ i • SiO 2 i
i
总质量平衡方程
10 0Q i•1Ii S i9 1 10 •F0e 烧 O
Q i•Fe i O
烧好、烧透是获得良好返矿的重要前提 良好返矿又为烧好、烧透奠定了基础
(5)其他烧结物料粒度 往往含有砖、石等夹杂物,应筛除,使之<10mm,以利配料、混匀
6.2烧结配料
6.2.1配料目的、要求、方法
目的: 使烧结矿的成分、物理性能、化学性能符合要求且稳定 控制配合料有害元素含量 使烧结料具有良好透气性,以获得较高的生产率
原料的贮存并中和:
原料场
(应考虑烧结厂原料场与整个钢铁厂原料场合用)
原料仓库
主要根据原料种类、数量、运距来定哪种设施贮存
选用原料场贮存的情况: 原料种类多、数量大、仓库容纳不下; 来料零散、成分复杂,需贮存到一定数量后集中使用; 原料基地远、受运输条件限制不能按期运来,需有保证连续生产的料;
中和:
准颗粒
=
核颗粒
+
>0.7mm,最好1~3mm
粘附细粒 <0.2mm
0.25~1mm的中间颗粒越少越好
●返矿质量与数量 返矿疏松、多孔、较粗,可成为制粒核心 过大:易偏析,影响混匀制粒; 过小:不能成为核颗粒 温度高:利于预热,不利于制粒 适宜数量:利于混匀制粒
●粘结剂 如: 生石灰、消石灰、皂土、腐植酸类、聚丙烯酸酯类、羧甲基纤维素类
特点: 设备简单 准确性差(物料粒度、湿度、料位都影响物料堆积密度) 操作方便 调整时间长 劳动强度大 难于实现自动配料
质量配料法
方法: 电子皮带秤按质量计量物料流量,由自动调节系统控制圆盘转速, 从而控制物料流量
特点: 自动配料 精确度高:当负荷50%时,质量法精确度 1.0%,容积法精确度 5%
(3)中型烧结厂(年产100~200万吨烧结矿) 采用火车或者汽车运输 可采用原料仓库(接受与贮存合用) 可采用受料槽接受量少、易起灰的原料
(4)小型烧结厂(年产20万吨烧结矿以下的) 采用火车或汽车运输 对原料的接受可因地制宜,采用简便形式 如:用电动手扶拉铲和地沟皮带运输机联合卸车,电耙造堆,原料棚贮存 或设适当形式的料槽,以解决原料接受和贮存问题
(2)设备状况 矿槽及闸门堵否 圆盘中心与料槽中心不重合(平行) 圆盘面不水平(圆盘中心与料槽中心相交) 圆盘面的粗糙度 电子皮带秤的好坏
(3)操作因素 矿槽料位高低 操作人员的技术水平
6.2.3烧结配料计算
常用的方法简易理论计算法和现场经验计算法
1.现场经验计算法 ●特点 快 误差大(经验) ●思路 设置配料比(根据原料种类、化学成分和烧结矿化学成分设置) 例:铁矿72% 生石灰 1.5% 石灰石10% 白云石7% 焦粉5.7% ●验证 用烧结矿化验结果来验证 ●调整 根据上一个班生产情况、现在生产情况,再估计一个配比,进行调整 ●确准 当验算结果与烧结矿质量指标相符合,确定为最终配比
远离燃料颗粒区域,温度低,烧结不均匀,出现夹生料, 强度差
布料时易偏析,使下层燃料多,温度过高,过熔、粘结篦条,返矿增多
太细: V燃↑,燃烧带过窄,温度降低,高温反应来不及进行, 烧结矿强度↓ ,返矿量↑ ,生产率↓
焦粉: 0.5~3mm 无烟煤: 0.5~4mm
(4)返矿粒度 来源:强度差的小块烧结矿 未烧透的烧结料 未烧结的 生料
粒度细、比表面积大、亲水性好、粘结性强, 加快造球速度,提高干、湿球强度与热稳定性
消石灰不仅形成胶体溶液,而且还有凝聚作用
(2)(水的性质、水的状态、)加水多少、加水方式、加水地点
混合料的适宜水分值与原料粒度、孔隙率、亲水性有关 磁铁矿 6~10% 赤铁矿 8~12% 褐铁矿 24~28%
当料粒度小,又配加高炉灰、生石灰时,水分可大一些
增加混合机长度,无疑延长混合时间,有利于混匀和制粒。 一次混合机长度 9~14m 二次混合机长度12~18m 大型混合机长度21~26m,直径4~5m
混合时间共约5min:一次混合约2min,二次混合约3min 也有9min的
●混合机充填率
充填率——圆筒混合机内物料占圆筒体积的百分数 充填率过小:产量低,且物料间相互作用力小,不利于混匀制粒。 充填率过大:在混合时间不变时,产量提高; 但增厚的料层,限制和破坏物料的运动,不利于混匀制粒。
将不同品种或同品种不同质量的原料,按一定比例借助某种机械进行混合, 使成分、物理性质、化学性质趋近均一
可在原料场、原料仓库进行中和作业
原料场的组成: 原料输入系统 一次料场(贮存料场) 破碎筛分系统 配料系统 二次料场(混匀料场) 混匀料输出系统
6.1.2烧结原料的粒度要求 (1)精粉、粉矿的粒度
(2)熔剂粒度 石灰石、白云石:粒度<3mm ,以保证其充分分解、矿化 粒度过粗,矿化不完全,烧结矿残存“白点” … 容易生成正硅酸钙 消石灰:粒度<3mm ,以利于混匀 生石灰:粒度<5mm ,以利于消化、混匀
(3)燃料粒度 过大:比表面积小,V燃↓,燃烧带增厚,透气性↓, V┴↓, 产量↓
燃料分布相对稀疏,粗燃料颗粒周围温度高、还原性气氛强、液相过多且流动 性好,形成难还原的薄壁粗孔结构,强度↓
一般:一次混合机的充填率为15%± 二次混合机的充填率要低些
6.3.3强化混匀与制粒的措施
●延长混合造球时间 ●寻求高效混合机 ●控制加水量,改进加水方式 ●预先制粒法 ●添加粘结剂 ●采用磁化水润湿混合料
6.3.4 混合作业效果
以混合前后混合料各组分的波动幅度来衡量(混匀效率) 以混合前后混合料粒度组成的变化 来衡量(制粒效果)
●三次混合:延长制粒时间、外裹煤
6.3.2 影响混匀与制粒的因素
(1)原料性质
●物料的粘结性、粒度与粒度组成、颗粒形状、密度 粘结性、润湿性强的物料易制粒、难混匀:褐铁矿>赤铁矿>磁铁矿 含泥质的铁矿粉易制粒 粒度相同的情况下,多棱角、形状不规则的颗粒比圆滑的颗粒易制粒 粒度差别大的物料,在混合时易产生偏析,难于混匀、制粒 各组分间密度相差悬殊时,其在混合机内被带到的高度不同而形成层状 分布,不利于混匀、制粒
i
i
MgO平衡方程
10•0 Mg烧O Qi •Mgi O i
③解方程 ④计算烧结矿化学成分,并校核有关指标 ⑤配料室内各矿槽下电子皮带秤的每米皮带料量
6.3混合料制备
6.3.1混合的目的、要求 目的:
使配合料中各组分分布均匀 加水润湿、制粒,以得到粒度适宜、具有良好透气性的混合料 预热混合料
分类:热返矿 冷返矿 高炉槽下返矿
作用:因粒度较大、孔隙较多,可↑料层透气性,↑V┴ 因粒度较大,可成为制粒核心、料层骨架料 因含低熔点物质,它有助于液相生成 热返矿可预热混合料
粒度:<5~6mm 过大,混匀中难于冷却、润湿,对成球不利 返矿周围成形条件变坏,很难结成一体,降低强度 降低成品率、产量 过小(特别是<1mm的比例过多),降低透气性
t混 合 D 有 2• 2 效 L n 转 有 • t速 效 a 前 n 进 D 有 i效 临 N L 有 界 • s 效 转 i前 n 速 进 D 有 L i• 有 效 4 D 有 效 .3 2 • 效 s s i i安 倾 n n息 角
i 一次= 0.2 ~0.3 i 二次= 0.25~0.35
化学成分配料法
方法: 用x萤光分析仪对原料进行化学成分分析 根据化学成分确定各种物料的配比(还是要称重) 再用x萤光分析仪对混合料进行化学成分分析
特点: 可保证化学成分的稳定性
问题: 试样的代表性,在什么位置取样,如何取样?
6.2.2影响配料准确性的因素分析