高温过热器传热特性及寿命分析
电站锅炉过热器的失效分析与寿命评估

过热 器 的腐蚀 包括 外部 腐蚀 和 内部 腐蚀 。外 部
腐蚀 主要 是 由于管 壁 外 的 高 温 黏结 性 灰 层 , 些 灰 这 层 中有低熔 点 的 复 合 硫 酸 盐 存 在 。在 5 0 7 0 5 ~ 1 ℃ 的 范 围内熔化 成 液 态 , 管 壁外 部造 成 腐 蚀 。 内部 对
中 图分类 号 : TM 6 1 2 2 .
文 献标 识码 : A
过热 器是 利用 烟 气 的 热 量加 热 饱 和 蒸 汽 的 , 高
反 复交 变应 力 , 造成 管 道 金 属 的疲 劳 寿命 损 耗 。但 由于过 热器 管道一 般较 薄 , 因而 其 内外壁 温差较 小 , 由此 产 生的热 应力 也较 小 , 因此 由热 应 力 造成 的疲 劳失 效 可不考 虑 。
第2卷 5
第 3 期
电
力
学
报
Vo _ 5 NO 3 l2 .
21 0 0年 6月 文 章 编 号 : 10 —5 8 2 1 )30 3 4 0 564 ( 00 0 2 50
J OURNAL 0F ElE CTRI OW ER CP
J n 2 1 u. 00
2 6 3
电 力 学 报
第 2 5卷
2 高 温 过 热器 寿 命 评 估 的 理论 依 据
高温过 热器 的奉 命评 估工作 主要是蠕 变 寿命 评
估 。 目前 大多 还是 采 用 拉 森一 米勒 公 式 计算 在一 定 的温度 、 应力 下的蠕 断时 间 , 再用 罗宾逊公 式计算 高 温蠕 变 寿命 损 耗 的百 分 数 , 果 越 接 近 1 寿 命 越 如 ,
锅炉 运行 过程 中燃料 品 质 的变 化 、 负荷 的变化 、 组 机
火电厂高温过热器老化评定和寿命评估

火电厂高温过热器老化评定和寿命评估杨迎春【摘要】结合高温过热器老化机理,分析了它的老化评定和寿命计算方法.【期刊名称】《云南电力技术》【年(卷),期】2011(039)001【总页数】4页(P70-72,81)【关键词】高温过热器;老化;寿命【作者】杨迎春【作者单位】昆明理工大学,云南昆明,650093;云南电力试验研究院(集团)有限公司电力研究院,云南,昆明,650217【正文语种】中文【中图分类】TK261 前言火电厂高温过热器是锅炉中的重要部件,其工作环境恶劣,随着运行时间的增加,会出现材料老化、高温持久性能下降,继而导致管子的爆管、泄漏,使锅炉的非计划停运增加。
目前,有很多材料老化评定和寿命评估的理论,大致可以归为应力解析法、非破坏性计测法和破坏试验法,下面进行探讨。
2 应力解析法应力解析法以诊断位置的结构尺寸和温度、压力等运行条件为基础,根据解析式或有限源法进行应力解析,计算热应力、内压应力,根据计算出的应力值和持久强度、疲劳强度等材料强度数据,用公式 (1)、(2)计算出蠕变损伤率和疲劳损伤率,评估部件的剩余寿命。
分别计算出蠕变寿命损耗量和疲劳寿命损耗量,两者相加即为诊断部件的总寿命损耗量。
式中Φc-蠕变损伤率;t——保持某应力条件下运行时间,h;tr——保持某应力条件下断裂时间,h;Φf——疲劳损伤率;N——启停及符合变化次数,次;Nf——到破断的循环次数,次。
应力解析法以解析求出部件材料的应力及材料强度数据为基础计算出部件的损伤程度,此方法的关键在于正确搜集到部件运行的完整的真实的资料,优点是能评价任意部位的材料,不受诊断对象所处位置的制约,但若运行历史或材料数据不准确将导致计算误差,且没有考虑材料老化这一因素。
3 非破坏性评定法3.1 珠光体的球化评定法珠光体中的片层状渗碳体在高温长期应力下运行,会逐步变为球状,这种现象称为碳化物的球化。
为了评定碳化物的球化级别,按球化对强度性能影响程度的不同,可将钢的球化分为未球化、轻度球化、中度球化、完全球化和严重球化。
超临界锅炉过热器-再热器的汽温特性及调节分析

超临界锅炉过热器\再热器的汽温特性及调节分析摘要:本文对直流锅炉的过热器、再热器汽温特性、变化特点、汽温调节进行了简要分析,并结合我厂实际情况阐述锅炉汽温偏差产生的原因,提出超临界压力锅炉运行中应关注的问题,与电力同仁共勉。
关键词:直流锅炉超临界过热器再热器汽温21世纪以来,为了提高锅炉效率,最大限度的降低能源消耗,电站锅炉逐步向超临界锅炉方向发展。
超临界锅炉的汽温特性与传统的汽包炉汽温特性有明显的不同,汽温过高将引起管壁超温、金属蠕变寿命降低,会影响机组的安全性;汽温过低将引起循环热效率的降低。
根据计算,过热器在超温10~20℃下长期工作,其寿命将缩短一半以上;汽温每降低10℃,循环热效率降低0.5%,而且汽温过低,会使汽轮机排汽湿度增加,从而影响汽轮机未级叶片的安全工作。
通常规定蒸汽温度与额定温度的偏差值在-10~+5℃范围内。
下面对直流锅炉的汽温特性进行分析,不断摸索调整汽温的最佳手段,控制汽温在允许范围内,保证锅炉安全运行。
一、过热器或再热器汽温特性1、过热器或再热器出口汽温随锅炉负荷的变化规律称为过热器或再热器的汽温特性。
过热器的汽温特性如图1-1所示。
图1-1 过热器的汽温特性l―辐射式过热器;2、3―对流式过热器23随着锅炉负荷的变化,辐射式过热器的汽温特性与对流式过热器相反。
当锅炉负荷增加时,燃料消耗量和过热器中蒸汽的流量都相应增大,由于炉内火焰温度变化不大,辐射式过热器吸收的炉膛辐射热增大不多,相对于每干克蒸汽的辐射吸热量反而减小,因此辐射式过热器的出口汽温随锅炉负荷的增大而降低。
辐射式过热器的汽温特性见图1-1中的曲线1。
当锅炉负荷增大时,燃料消耗量增大,烟气流速增大,烟温升高、对流传热量增加,相对于每千克蒸汽的对流吸热量增加,因此对流式过热器的出门汽温随锅炉负荷的增大而增大。
对流式过热器的汽温特性见图1-1中曲线2、3,过热器离炉膛越远,过热器进口烟温越低,烟气对过热器的辐射换热份额越少,汽温随负荷增加而上升的趋势更加明显。
锅炉过热器超温原因分析
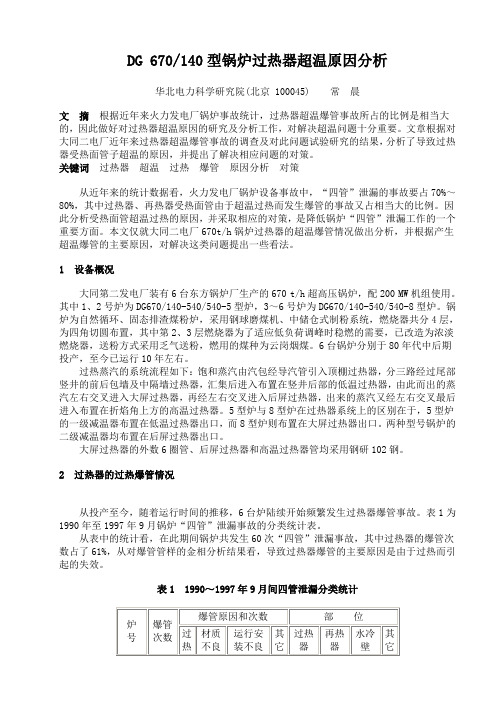
DG 670/140型锅炉过热器超温原因分析华北电力科学研究院(北京 100045) 常晨文摘根据近年来火力发电厂锅炉事故统计,过热器超温爆管事故所占的比例是相当大的,因此做好对过热器超温原因的研究及分析工作,对解决超温问题十分重要。
文章根据对大同二电厂近年来过热器超温爆管事故的调查及对此问题试验研究的结果,分析了导致过热器受热面管子超温的原因,并提出了解决相应问题的对策。
关键词过热器超温过热爆管原因分析对策从近年来的统计数据看,火力发电厂锅炉设备事故中,“四管”泄漏的事故要占70%~80%,其中过热器、再热器受热面管由于超温过热而发生爆管的事故又占相当大的比例。
因此分析受热面管超温过热的原因,并采取相应的对策,是降低锅炉“四管”泄漏工作的一个重要方面。
本文仅就大同二电厂670t/h锅炉过热器的超温爆管情况做出分析,并根据产生超温爆管的主要原因,对解决这类问题提出一些看法。
1 设备概况大同第二发电厂装有6台东方锅炉厂生产的670 t/h超高压锅炉,配200 MW机组使用。
其中1、2号炉为DG670/140-540/540-5型炉,3~6号炉为DG670/140-540/540-8型炉。
锅炉为自然循环、固态排渣煤粉炉,采用钢球磨煤机、中储仓式制粉系统,燃烧器共分4层,为四角切圆布置,其中第2、3层燃烧器为了适应低负荷调峰时稳燃的需要,已改造为浓淡燃烧器,送粉方式采用乏气送粉,燃用的煤种为云岗烟煤。
6台锅炉分别于80年代中后期投产,至今已运行10年左右。
过热蒸汽的系统流程如下:饱和蒸汽由汽包经导汽管引入顶棚过热器,分三路经过尾部竖井的前后包墙及中隔墙过热器,汇集后进入布置在竖井后部的低温过热器,由此而出的蒸汽左右交叉进入大屏过热器,再经左右交叉进入后屏过热器,出来的蒸汽又经左右交叉最后进入布置在折焰角上方的高温过热器。
5型炉与8型炉在过热器系统上的区别在于,5型炉的一级减温器布置在低温过热器出口,而8型炉则布置在大屏过热器出口。
高温过热器管长周期运行后的性能分析
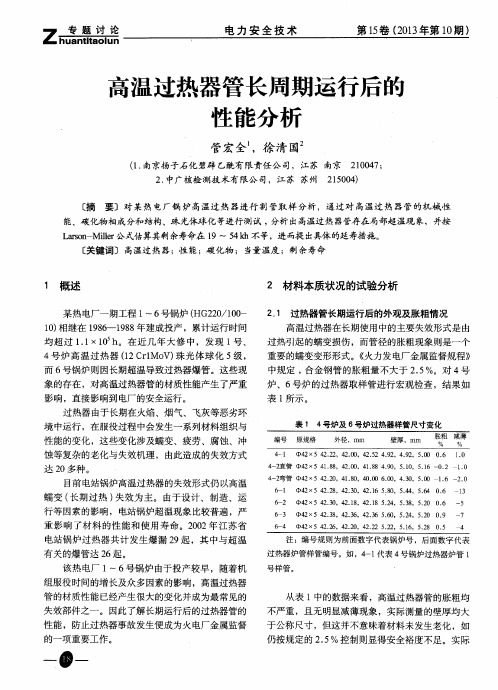
Z
电 力 安 全 技 术
第 1 5 卷( 2 0 1 3 年 第 1 0 期 )
高温过热器管长 周期运行后的 性 能分 析
管宏 全 ,徐 清 国
( 1 . 南京扬 子石 化碧辟 乙酰有 限责任 公 司 ,江苏 南京 2 1 0 0 4 7 ; 2 . 中广核检 测技 术有 限公 司,江 苏 苏 州 2 1 5 0 0 4 ) [ 摘 要 ]对 某 热 电厂 锅 炉高 温过 热 器进 行 割 管取 样 分析 ,通 过 对 高温过 热 器 管 的机械 性
1 概述
某 热 电厂 一期工程 l ~6 号 锅炉 ( HG 2 2 0 /1 0 0 — 1 0 ) 相 继在 1 9 8 6 -1 9 8 8年建成 投产 ,累计 运行 时 间 均超过 1 . 1 ×1 0 h。在 近 几 年 大修 中,发 现 1 号、
4号 炉 高 温 过 热器 ( 1 2 C r l Mo V) 珠 光 体 球 化 5级 ,
目前 电站锅 炉高 温过 热器 的失效形 式仍 以高温 蠕变 ( 长期 过 热 ) 失 效为 主 。 由于设 计 、制 造 、运 行等 因素 的影响 ,电站 锅炉超 温现象 比较普 遍 ,严 重 影 响 了材 料 的 性 能 和使 用 寿 命 。2 0 0 2年 江 苏 省
电厂锅炉过热器 再热器管壁超温原因分析及预防措施
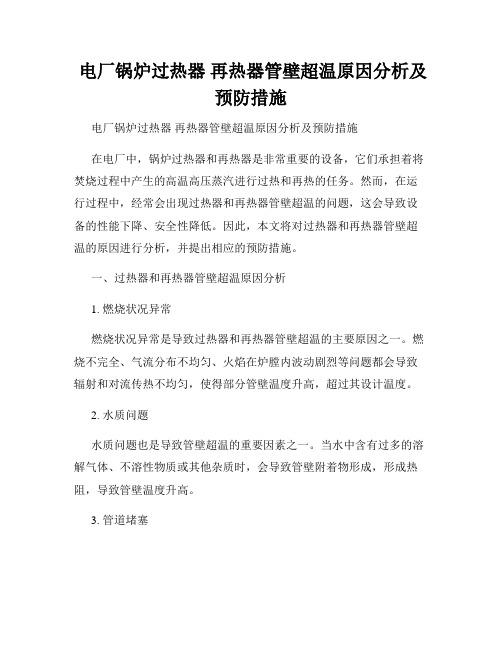
电厂锅炉过热器再热器管壁超温原因分析及预防措施电厂锅炉过热器再热器管壁超温原因分析及预防措施在电厂中,锅炉过热器和再热器是非常重要的设备,它们承担着将焚烧过程中产生的高温高压蒸汽进行过热和再热的任务。
然而,在运行过程中,经常会出现过热器和再热器管壁超温的问题,这会导致设备的性能下降、安全性降低。
因此,本文将对过热器和再热器管壁超温的原因进行分析,并提出相应的预防措施。
一、过热器和再热器管壁超温原因分析1. 燃烧状况异常燃烧状况异常是导致过热器和再热器管壁超温的主要原因之一。
燃烧不完全、气流分布不均匀、火焰在炉膛内波动剧烈等问题都会导致辐射和对流传热不均匀,使得部分管壁温度升高,超过其设计温度。
2. 水质问题水质问题也是导致管壁超温的重要因素之一。
当水中含有过多的溶解气体、不溶性物质或其他杂质时,会导致管壁附着物形成,形成热阻,导致管壁温度升高。
3. 管道堵塞管道堵塞同样会导致管壁温度升高。
当锅炉管道内的水垢、沉积物或其它杂质积聚过多时,不仅会降低热传导能力,还会阻碍管道内流体的流动,导致局部管壁温度升高。
4. 运行参数异常运行参数异常也会导致管壁超温的问题。
例如,过高的蒸汽流量、过低的供水温度、过高的供水压力等都会使管壁温度超过设计温度。
二、过热器和再热器管壁超温的预防措施1. 优化燃烧状况通过调整锅炉的燃烧参数和火焰分布,减少炉膛内火焰的波动,提高燃烧效率,降低管壁温度。
此外,定期清洗燃烧器、炉膛和锅炉的燃烧区域,避免积聚物的形成,以减少管壁温度升高的可能性。
2. 加强水质管理加强水质管理,控制水中的溶解气体、不溶性物质和杂质的含量。
定期进行水处理,清除管道内的水垢和附着物。
同时,排放并替换含有过多杂质的水,以保持良好的水质,降低管壁温度。
3. 定期清洗管道定期清洗管道,减少管道内的沉积物、水垢和杂质的积聚。
可以采用化学清洗、水冲洗等方法,对管道进行彻底的清洗和冲洗,保持管道的畅通,减少管壁温度升高。
电站锅炉过热器超温原因分析

科技视界Science &TechnologyVisionScience &Technology Vision 科技视界作者简介:李宁(1983—),男,汉族,本科,助理工程师,主要从事热电工程现场管理。
0前言发展大容量高参数锅炉是我国电力工业发展的一项重要技术政策。
锅炉蒸汽参数的提高,使得过热器系统成为大容量锅炉本体设计中必不可少的受热面。
这部分受热面内工质的压力和温度都相当高,且大多布置在烟温较高的区域,因而其工作条件在锅炉所有受热面中最为恶劣,受热面温度接近管材的极限允许温度;而锅炉容量的日益增大,使过热器系统的设计和布置更趋复杂,电站锅炉中过热器超温问题也日益突出。
许多电厂在发现过热器超温威胁爆管后不得不牺牲机组运行的经济性,使锅炉做降温运行但是即便如此,仍不能彻底解决其超温问题。
本文系统全面的探讨过热器超的原因,通过分析发现影响过热器超温的原因很多,有设计、施工、检修、运行、制造、管理和煤种等诸多方面,而且这些因素又相互作用。
因此往往不是由单一因素造成,而是几个因素同时存在并交互作用的结果。
1锅炉设计及制造对过热器超温的影响1.1设计原因1.1.1热力计算不当1)炉膛的传热计算不当从锅炉炉膛的传热计算计算目的而言,使用炉膛传热计算有两个目的,第一是,进行各受热面的热平衡计算,了解各级受热面的进出口烟温和汽温,第二是,了解炉膛中受热面的热负荷分布、烟温分布、烟温介质及流速分布等。
适合于以上的目的有以下两类炉膛传热计算方法。
(1)零维模型法该方法又称常规的炉膛传热计算方法,使用该方法只能计算出一个炉膛出口烟温,以确定各级受热面的热平衡,其中有代表性的影响较大的有以下几种:①1890年由Hnason 和Orrok 提出了的经验关系式[1]。
②Mullikin 根据辐射传热的Stefan-Boltzmann 定律提出的炉内辐射传热计算公式[2]。
③前苏联中央汽轮机锅炉研究所(ЦКТИ)以ГУРBИЧ为首的研究小组在综合了大量的试验数据的基础上,提出了锅炉炉膛传热计算的半经验方法,称为ЦКТИ法[3]。
锅炉过热器的性能分析与维护
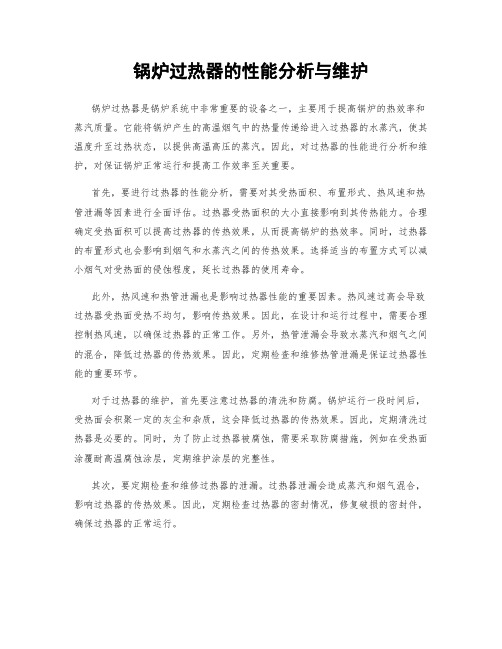
锅炉过热器的性能分析与维护锅炉过热器是锅炉系统中非常重要的设备之一,主要用于提高锅炉的热效率和蒸汽质量。
它能将锅炉产生的高温烟气中的热量传递给进入过热器的水蒸汽,使其温度升至过热状态,以提供高温高压的蒸汽。
因此,对过热器的性能进行分析和维护,对保证锅炉正常运行和提高工作效率至关重要。
首先,要进行过热器的性能分析,需要对其受热面积、布置形式、热风速和热管泄漏等因素进行全面评估。
过热器受热面积的大小直接影响到其传热能力。
合理确定受热面积可以提高过热器的传热效果,从而提高锅炉的热效率。
同时,过热器的布置形式也会影响到烟气和水蒸汽之间的传热效果。
选择适当的布置方式可以减小烟气对受热面的侵蚀程度,延长过热器的使用寿命。
此外,热风速和热管泄漏也是影响过热器性能的重要因素。
热风速过高会导致过热器受热面受热不均匀,影响传热效果。
因此,在设计和运行过程中,需要合理控制热风速,以确保过热器的正常工作。
另外,热管泄漏会导致水蒸汽和烟气之间的混合,降低过热器的传热效果。
因此,定期检查和维修热管泄漏是保证过热器性能的重要环节。
对于过热器的维护,首先要注意过热器的清洗和防腐。
锅炉运行一段时间后,受热面会积聚一定的灰尘和杂质,这会降低过热器的传热效果。
因此,定期清洗过热器是必要的。
同时,为了防止过热器被腐蚀,需要采取防腐措施,例如在受热面涂覆耐高温腐蚀涂层,定期维护涂层的完整性。
其次,要定期检查和维修过热器的泄漏。
过热器泄漏会造成蒸汽和烟气混合,影响过热器的传热效果。
因此,定期检查过热器的密封情况,修复破损的密封件,确保过热器的正常运行。
此外,定期检查和清洗过热器的烟道也很重要。
烟道积聚的灰尘和杂质会阻碍烟气的流动,影响过热器的传热效果。
定期清洗烟道可以减小烟气的流动阻力,提高过热器的传热效果。
同时,要定期检查烟道的密封状态,确保烟气不会泄露。
最后,要加强过热器的监测和故障诊断。
定期检查过热器的运行参数和传热效果,如进出口温度、压力差等,及时发现问题并进行调整和维修。
- 1、下载文档前请自行甄别文档内容的完整性,平台不提供额外的编辑、内容补充、找答案等附加服务。
- 2、"仅部分预览"的文档,不可在线预览部分如存在完整性等问题,可反馈申请退款(可完整预览的文档不适用该条件!)。
- 3、如文档侵犯您的权益,请联系客服反馈,我们会尽快为您处理(人工客服工作时间:9:00-18:30)。
高温过热器传热特性及寿命分析摘要:近年来,各种类型的大容量火力发电机组不断涌现。
过热器内部是高温高压的蒸汽,又布置在烟温较高的区域,工作条件最为恶劣,易造成锅炉爆管;同时锅炉设备实行状态检修需要了解管子蠕变损伤的程度。
因此,分析过热器爆管的原因和蠕变损伤的机理,并对高温部件剩余寿命作出正确的评估,已成为保证火电厂安全运行和提高经济性的关键课题之一。
本文通过研究高温过热器的传热特性,分析了高温过热器爆管的原因,并介绍了高温腐蚀对爆管的影响,而且按工质流程逐个对微元段进行热力计算,掌握高温过热器壁温分布情况,以便于从根本上减少爆管发生率。
同时根据拉——米参数式确定蠕变断裂时间,对过热器剩余寿命进行预测,以延长电厂的检修周期,提高电厂的经济性。
关键词:过热器;爆管;腐蚀;壁温计算;寿命分析Abstract:In recent years, various types of large-capacity thermal power generating units will continue to emerge.Inside the superheater there is steam with high temperature and high pressure, at the same time the superheater is in the region where the flue-gas temperature is higher, so the superheater’s working conditions are most poor, resulting in the explosion of boiler pipes easily.Meanwhile in order to overhaul the boiler equipment on the basis of operating condition,it is necessary to know about the tubes’ creep damage extent. Therefore, the analysis of reasons for superheater explosion and creep damage mechanism ,also to assess the remaining life of high-temperature boiler parts correctly, have become one of the key projects that guarantees safe operation of thermal power plants and improves the economical efficiency.This paper analyzes the reasons for high-temperature superheater blasting via the research on heat transfer characteristics of high-temperature superheater, and puts emphasis on illustrating the effects that high-temperature corrosion have on the superheater explosion.In addition, according to the flow path of work substance,it conducts the thermodynamic calculation of small tube section separately ,grasping the wall temperature distribution of high-temperature superheater, in order to reduce the rate of tube explosion radically. At the same time the creep-rupture time is determined by Larson-Miller Parameter,and the remaining life of superheater can also be predicted ,which will be used to extend the maintenance cycle and improve the economy of thermal power plants.Keywords:Superheater; Tube Explosion; Corrosion; Wall Temperature Calculation; Life Analysis1 引言随着我国电力工业建设的迅猛发展,各种类型的大容量火力发电机组不断涌现,锅炉蒸汽参数的提高,使得过热器和再热器系统成为大容量锅炉本体设计中必不可少的受热面。
这两部分受热面内工质的压力和温度都相当高,且大多布置在烟温较高的区域,因而其工作条件在锅炉所有受热面中最为恶劣,受热面温度接近管材的极限允许温度;而锅炉容量的日益增大,使其过热器和再热器系统的设计和布置更趋复杂[1]。
这不可避免地导致并联各管内的流量与吸热量发生差异。
当工作在恶劣条件下的承压受热部件的工作条件与设计工况偏离时,就容易造成锅炉爆管。
锅炉爆管严重威胁着火电机组的安全经济运行。
据有关资料统计,爆管引起的非计划停运时间占总停运时间的20%左右,少发电量占总少发电量的25%左右。
由此可见,其造成的经济损失十分巨大[2]。
事实上,当爆管发生时常采用所谓快速维修的方法,如喷涂或衬垫焊接来修复,一段时间后又再爆管。
爆管在同一根管子、同一种材料或锅炉的同一区域的相同断面上反复发生,这一现象说明锅炉爆管的根本问题还未被解决。
因此,了解过热器爆管事故的直接原因和根本原因,搞清管子失效的机理,并提出预防措施,减少过热器爆管的发生是当前的首要问题。
同时,随着火电厂运行时间的逐年增长,超期服役的老龄机组也在不断增加,高温部件蠕变损伤和材料老化程度也日趋严重,高温部件损坏事故也时有发生。
因此,解决火电厂老龄机组的寿命评估和运行安全性问题已迫在眉睫。
火电厂对锅炉设备实行状态检修,需要有一个可靠的寿命评估方法,对高温部件剩余寿命作出正确的评估。
2 过热器爆管原因过热器和再热器是工质温度和金属温度最高的部件,受热面管材过热后管材金属温度超过许用的极限温度,内部组织发生变化,降低了许用应力,管子在内压力下产生塑性变形,最后导致过热爆管。
假如某管子在540℃时可以持续工作100000h,那么,长期在550℃下工作,它的寿命可能只有50000h,即寿命缩短一半。
因此过热就意味着降低安全系数或减少寿命,所以应该严格控制蒸汽温度的上限。
2.1 过热器爆管的根本原因根本原因:①长期过热,长期过热是指管壁温度长期处于设计温度以上而低于材料的下临界温度,超温幅度不大但时间较长,锅炉管子发生碳化物球化,管壁氧化减薄,持久强度下降,蠕变速度加快,使管径均匀胀粗,最后在管子的最薄弱部位导致脆裂的爆管现象。
这样,管子的使用寿命便短于设计使用寿命。
超温程度越高,寿命越短。
长时超温爆管根据工作应力水平可分为三种:高温蠕变型、应力氧化裂纹型、氧化减薄型[3];②短期过热;③磨损使管壁减薄爆管;④腐蚀疲劳;⑤应力腐蚀裂纹,应力腐蚀裂纹是指在介质含氯离子和高温条件下,由于静态拉应力或残余应力作用产生的管子破裂现象;⑥热疲劳,热疲劳是指炉管因锅炉启停引起的热应力、汽膜的反复出现和消失引起的热应力和由振动引起的交变应力作用而发生的疲劳损坏。
⑦异种金属焊接;⑧质量控制失误,质量控制失误是指在制造、安装、运行中由于外界失误的因素所造成的损坏。
加强电厂运行、检修及各种制度的管理是防止质量控制失误出现的有效手段。
2.2 超温原因超温原因有以下九种:①燃料特性的变化,如灰分和水分增加,燃料发热量降低,则到达同样的负荷必须增加燃料消耗量,水分蒸发也使烟气容积增大,导致流经过热器的烟气流速增加,对流换热加强;从而使出口汽温升高。
②火焰中心上移时,炉内辐射吸热比例减少。
对流式过热器的对流吸热份额增加,使出口汽温增加。
③炉膛设计高度偏低,火焰中心的相对位置提高,从而提高了炉膛出口烟温,引起管壁超温。
④过量空气系数增大使燃烧生成的烟气量增多,烟气流速增大,对流换热加强,使对流过热器出口汽温升高。
⑤给水温度降低,则加热给水所需热量增加,为维持负荷,必须增加入炉燃料量,炉内烟气量和炉膛出口烟温增加,导致对流式过热器出口蒸汽温度增加。
⑥切向燃烧引起烟温偏差,使实际的受热面吸热产生了偏差。
因此,烟气温度场和速度场的分布偏差是过热器管超温的重要原因。
⑦锅炉受热面沾污结渣会降低炉内受热面的传热能力,并引起炉内火焰中心向后推移,炉膛出口烟温相应升高,导致过热汽温偏高。
⑧升负荷速率过快使升负荷过程中的壁温峰值过大。
⑨其它方面的原因,如:选材余度不够;受热面偏多,蒸汽质量流速偏低;结构设计原因造成的热偏差;壁温测点温度失真;焊接质量问题[3]。
解决高温受热面超温问题的对策:①削弱残余气流旋转;②注意减少三通区域内涡流的影响和同屏间的热偏差;③壁温测量尽量准确;④做好运行调整工作。
2.3 高温腐蚀高温腐蚀是导致受热面失效、爆管、引起火力发电厂事故停机的主要原因之一。
锅炉受热面腐蚀根据腐蚀部位和环境不同可分为烟气侧腐蚀和水汽侧腐蚀两大类。
火电厂锅炉的过热器的烟气侧存在的高温腐蚀与部件工作环境的温度、气体成分、煤质成分和煤粒的运动状况等因素有关,具有腐蚀速度快、腐蚀区域相对集中以及突发性的特点。
锅炉烟气侧发生的高温腐蚀主要为硫腐蚀、氯腐蚀和钒腐蚀。
当蒸汽温度高于565℃时,燃料灰分中含有较多的S、V及碱性物质等成分时,往往在覆盖有熔盐或积灰层下的管壁上发生烟灰腐蚀。
燃料中含有的S、V及碱性物质越多,炉管金属的耐蚀性、耐热性越差,腐蚀越易发生;管壁温度越高,腐蚀越严重。
飞灰也是造成高温腐蚀的主要因素[4]。
烟气侧高温腐蚀还与低熔点的沉积物有关。
过热器管高温腐蚀的防治措施:在燃煤锅炉中,如燃料中K、Na、S含量较高时就应注意防止或减轻过热器和再热器的高温腐蚀问题。
此时要避免在这些受热面管子上积结引起腐蚀的复合硫酸盐是困难的,主要应降低受热面的壁温,应使这些受热面的蒸汽出口段布置在烟温较低区,因为高的烟温和高的管壁温度均能使管子金属的腐蚀速度增加。
如壁温低于550℃,则腐蚀速度将大为减小,一般应保持壁温不超过600~620℃,以免这些受热面管子受到严重腐蚀。