机械伤害的原因分析
常见普通车床机械伤害的原因分析

常见普通车床机械伤害的原因分析普通车床机械伤害是车床操作时常见的安全隐患之一,它可能会导致工人的伤亡和车床的损害。
常见的机械伤害包括手指被卡住、物体掉落、碰撞等。
以下分析了常见普通车床机械伤害的原因。
一、个人操作错误普通车床的操作需要一定的技能和认真的态度,如果操作不当,就会出现安全事故。
例如,工人没有穿戴防护用具、未戴手套、操作时把手置于危险区域、误触开关等操作错误都可能导致机械伤害。
二、设备故障车床是一种精密的机械设备,长期使用后容易出现故障,例如电机损坏、传动系统故障、刀架失调等。
如果未能及时检修和维护车床,将会增加车床故障和安全事故的发生几率。
三、工作环境车床操作的工作环境对机械伤害的发生也有影响。
例如,工作区域的狭小、工作台离地过高或过低、工作场所的光线不足等都会增加机械伤害的风险。
四、不当的材料或工件车床加工需要使用材料或工件,不当的材料或工件也会增加机械伤害的风险。
例如,材料不稳定、工件超出车床能力范围、工件未加固等情况都可能导致危险的机械伤害。
五、行为不端在车床操作时,如果操作者心情不好或者匆忙时就会增加机械伤害的风险。
例如,操作者过于着急和匆忙时就容易疏忽,出现机械伤害的风险。
六、未进行良好的培训车床操作是一项技能活动,如果未经过专业培训的工人随意操作车床会增加机械伤害的风险。
因此,厂家和相关机构应在购置车床时,确保工人接受过一定的培训和考试,从而了解车床的操作规程。
最后,机械伤害的发生也有一定的运气成分。
出现机械伤害并不是出现了以上任何一种原因就一定会发生,因此,需要在前期做好防范措施、在操作过程中遵守指导,提高安全意识和技能,做好车床的安全保护措施,避免机械伤害的发生。
分析建筑施工行业机械伤害

分析建筑施工行业机械伤害在建筑施工行业中,机械伤害是一种常见且严重的安全隐患。
由于建筑施工过程中涉及到众多类型的机械设备,如起重机、挖掘机、装载机、搅拌机等,一旦操作不当或防护措施不到位,就容易引发机械伤害事故,给施工人员的生命安全和身体健康带来威胁,同时也会影响工程进度和企业的经济效益。
因此,深入分析建筑施工行业中的机械伤害问题,采取有效的预防措施,具有重要的现实意义。
一、建筑施工行业机械伤害的类型建筑施工行业中的机械伤害类型多种多样,常见的主要有以下几种:1、卷入和绞伤这是较为常见的机械伤害类型。
当施工人员的身体部位,如衣物、头发、手臂等接触到旋转的机械设备部件,如皮带轮、齿轮、传动轴等,就容易被卷入或绞伤。
例如,在操作搅拌机时,如果施工人员的手臂靠近正在运转的搅拌轴,就可能被卷入其中,造成严重的伤害。
2、碰撞和挤压在施工现场,机械设备在运行或移动过程中,可能会与施工人员发生碰撞,或者将施工人员挤压在设备与固定物体之间。
比如,起重机吊运物料时,如果操作失误,可能会撞到下方的施工人员;挖掘机在作业时,如果回转半径内有施工人员,可能会将其挤压受伤。
3、切割和刺伤一些机械设备配备有锋利的切割部件或突出的尖锐物,如电锯、切割机、钻床等,如果施工人员在操作时不慎接触到这些部件,就容易被切割或刺伤。
4、飞出物打击机械设备在运行过程中,其零部件可能会因松动、断裂等原因飞出,对附近的施工人员造成打击伤害。
例如,砂轮片在高速旋转时破裂飞出,可能会击中施工人员的身体。
二、建筑施工行业机械伤害的原因导致建筑施工行业机械伤害事故发生的原因是多方面的,主要包括以下几个方面:1、人的不安全行为(1)施工人员缺乏必要的安全意识和操作技能,违规操作机械设备。
例如,未经培训就上岗操作,不按照操作规程进行操作,盲目蛮干等。
(2)施工人员在操作机械设备时注意力不集中,疲劳作业,或者在设备运行时进行维修、保养等危险行为。
(3)施工人员未正确佩戴个人防护用品,如安全帽、工作服、手套等,导致在发生机械伤害时无法有效保护身体。
造成机械伤害事故的原因分析

造成机械伤害事故的原因分析
从安全系统工程学的角度来看,造成机械伤害的原因可以从人、机、环境三个方面进行分析。
人、机、环境三个方面中的任何一个出现缺陷,都有可能引起机械伤害事故的发生。
一、人的不安全行为
1.误触开关或违章开机。
操作者操作时注意力不集中或思想过紧张而发生误操作或误动作或操作者业务技术素质低,操作不熟练,缺乏正规的专业培训以及监督检查不够。
2.违章作业,操作者不按规程进行操作。
违章作业一般都是因作业人员缺乏安全知识,心存侥幸造成的认为一次违章不一定会造成事故。
检修、检查机械时,忽视安全措施。
在线检修时,未采取必要的预防措施,如未断电作业、电源处未悬挂警示牌等。
不小心进入机械危险部位或是未与操作人员联系,盲目接触机械危险部位。
3.安全生产意识淡薄,安全管理机制不健全
二、物的不安全因素
1.设计不当致机械不符合安全要求,机械故障,防护及安全装置失灵等。
2.安全防护设施不健全或形同虚设。
主要有以下几种情况:一是无安全防护设施;二是机械设备安全防护设施损坏;三是解除了机械
设备安全防护设施;四是作业人员未按要求使用安全防护设施。
三、环境的不安全因素
噪声干扰、照明光线不良、无通风、温湿度不当、场地狭窄、布局不合理等。
机械安全事故案例分析

机械安全事故案例分析机械安全事故是生产过程中经常发生的问题,对企业和员工的安全带来极大的威胁。
本篇文章通过对一些典型的机械安全事故案例进行分析,以提高大家对机械安全问题的认识,并找出防止类似事故发生的措施。
案例一:机械伤害某工厂的一名工人在操作一台冲压机时,不慎将手卷入机器中,造成严重伤害。
经过调查分析,事故发生的原因有以下几点:1.工人未按照操作规程操作,伸手进入危险区域。
2.冲压机缺少必要的防护装置,如防护栏、警示标志等。
3.工厂对员工的安全培训不足,导致员工对安全风险认识不足。
案例二:物体打击在某建筑工地上,一名工人在操作塔吊时,吊装的货物突然脱落,将地面上的一名工人击中,导致重伤。
事故原因分析如下:1.工人操作塔吊时,未对货物进行稳固,导致货物脱落。
2.塔吊的监控系统不完备,无法实时监控货物状态。
3.现场安全管理不到位,缺乏对作业现场的安全监督。
案例三:触电事故一家电器生产厂家的员工在维修一台电动机时,未切断电源,直接进行维修,导致触电事故发生。
事故原因分析如下:1.员工在进行设备维修时,未按照操作规程切断电源。
2.企业对设备维修的安全管理不严格,未对员工进行充分的安全教育。
3.设备本身存在缺陷,如缺乏漏电保护装置等。
通过对以上三个案例的分析,我们可以总结出一些防止机械安全事故发生的措施:1.加强员工的安全培训,提高员工的安全意识,使员工熟练掌握安全操作规程。
2.企业应完善设备的安全防护设施,如防护栏、警示标志、漏电保护装置等。
3.企业应建立健全的安全管理制度,加强对作业现场的安全监督,确保各项安全措施得到有效执行。
4.加强设备的日常维护和检修,确保设备处于良好的工作状态。
以上是本文对机械安全事故案例的分析,希望对大家有所启示。
在今后的生产过程中,我们要时刻警惕机械安全风险,确保企业和员工的安全。
案例四:火灾爆炸在某化工厂,由于操作人员未严格遵守操作规程,在搬运易燃物品时引发了火灾,火势蔓延导致爆炸事故。
机械伤害常见原因分析
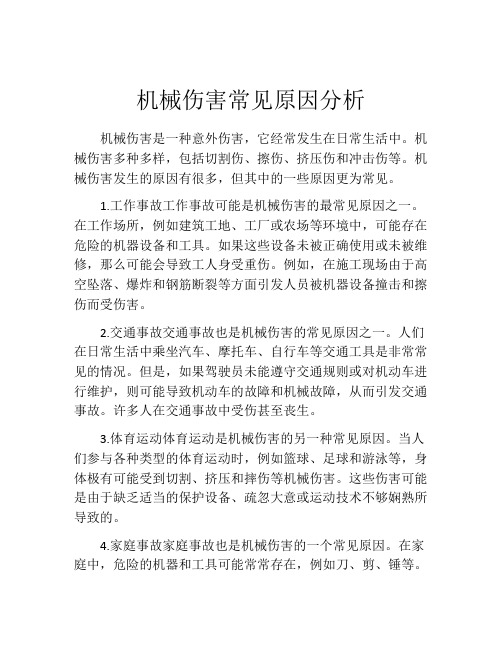
机械伤害常见原因分析机械伤害是一种意外伤害,它经常发生在日常生活中。
机械伤害多种多样,包括切割伤、擦伤、挤压伤和冲击伤等。
机械伤害发生的原因有很多,但其中的一些原因更为常见。
1.工作事故工作事故可能是机械伤害的最常见原因之一。
在工作场所,例如建筑工地、工厂或农场等环境中,可能存在危险的机器设备和工具。
如果这些设备未被正确使用或未被维修,那么可能会导致工人身受重伤。
例如,在施工现场由于高空坠落、爆炸和钢筋断裂等方面引发人员被机器设备撞击和擦伤而受伤害。
2.交通事故交通事故也是机械伤害的常见原因之一。
人们在日常生活中乘坐汽车、摩托车、自行车等交通工具是非常常见的情况。
但是,如果驾驶员未能遵守交通规则或对机动车进行维护,则可能导致机动车的故障和机械故障,从而引发交通事故。
许多人在交通事故中受伤甚至丧生。
3.体育运动体育运动是机械伤害的另一种常见原因。
当人们参与各种类型的体育运动时,例如篮球、足球和游泳等,身体极有可能受到切割、挤压和摔伤等机械伤害。
这些伤害可能是由于缺乏适当的保护设备、疏忽大意或运动技术不够娴熟所导致的。
4.家庭事故家庭事故也是机械伤害的一个常见原因。
在家庭中,危险的机器和工具可能常常存在,例如刀、剪、锤等。
如果这些危险物品被不慎使用或放置不当,那么可能导致人与机器设备的不慎碰撞和切割,从而引发机械伤害。
5.军事作战军事作战也是机械伤害的一种原因。
在战争中,人们常常在离爆炸不远的地方战斗,这可能会导致机体受到机器的击打和爆炸波的冲击所带来的机械伤害。
另外,敌方战斗机、坦克等重型装备的作用下也可能导致机械伤害。
6.环境灾害环境灾害,如地震、龙卷风和火灾,也是机械伤害的一个常见原因。
当这些自然力量降临时,建筑物和设备可能遭到破坏,从而造成机械伤害。
例如,在地震后,由于建筑物的倒塌和散落的碎片,许多人可能会受到切割和挤压伤害。
总的来说,机械伤害的原因多种多样,无处不在,人们要保持谨慎和警觉,避免不必要的危险。
常见普通车床机械伤害的原因分析

常见普通车床机械伤害的原因分析随着车床机的广泛应用,车床机械伤害的问题也日益突出。
车床机械伤害的发生原因多种多样,主要包括人为和机械两种原因。
本文将结合实际案例,对车床机械伤害的原因分析进行探讨。
一、人为原因1.操作不当操作不当是导致车床机械伤害的最主要原因之一。
操作人员对设备的操作流程不熟悉或不遵守安全操作规程,以及对车床机的操作技能掌握不到位,将导致车床机械伤害的发生。
例如,操作人员在操作车床机时,未能按要求进行锁定及解锁操作,或者因操作失误而造成工件车刀、车刀碰撞等。
2.装配不当车床机的安装是关键的一步,在车床机安装过程中,如未能严格按照厂家提供的操作说明进行,或者在安装过程中疏忽大意,将导致车床机械伤害的发生。
例如,未能按照操作说明进行设备的固定、连接电源等环节,或者在设备安装时未能认真检查设备的稳定性、电缆的连接情况等。
3.维护不及时车床机维护不及时也是人为原因导致的车床机械伤害的主要原因之一。
操作人员未能出色维护车床机,包括设备的保养、清洁和检验等工作,将直接影响到车床机设备的安全运行能力。
二、机械原因1.老化损坏车床机的老化问题在使用过程中随时存在。
由于车床机在使用过程中承受着长期的高强度负荷,因此,在机器老化后,其自身的安全性和稳定性将会下降,从而导致车床机械伤害的发生。
2.设备损坏车床机械伤害的契机就是设备损坏。
设备损坏可以由许多因素引起,例如机器磨损、实验负荷、外部环境等等。
如果设备损坏对应的修理工作未能得到及时的处理,将有可能导致车床机械伤害的发生。
3.设备选用问题车床机的选用是至关重要的一步,选用适合设备的前提是了解自身行业和业务的需要。
如果在选用车床机设备时没有考虑到实际使用情况和将来的业务需求,将可能导致车床机械伤害的发生,从而影响企业生产的正常运转。
总结来看,车床机械伤害的发生原因多种多样,操作不当、装配不当、维护不及时、老化损坏、设备损坏和设备选用问题等是车床机械伤害的主要原因。
造成机械伤害的原因及其预防措施

造成机械伤害的原因及预防机械, 预防, 伤害日常工作中,由于机械伤害常常给员工带来痛苦,甚至终身残疾。
怎样才能有效地防止机械伤害事故呢?首先要正确分析产生机械伤害事故的原因,然后采取相应的安全防范措施。
形成机械伤害事故的原因:1、修理、检查机械时,忽视安全措施。
线路检修时,未采取必要预防措施;断电作业,电源处未挂警示牌。
2、安全防护装置不健全或形同虚设。
3、电源布局混乱,不利于紧急停车。
4、违章作业,随便进入危险作业区。
5、不熟悉操作规程,遇有紧急情况,发生判断错误。
有针对性的预防措施:1、线路检修时,必须采取严格的安全预防措施;断电作业时,电源处应悬挂标志明显的警示牌,并确认机械惯性消失后,再开始作业。
2、机械设备各传动部位必须有可靠的防护装置,不能为了图省事而任意拆除。
3、电源开关布局要合理,不要将多台设备的开关无规则地放在一起。
4、非操作人员严禁进入有危险因素的作业区域;进入时,必须有安全措施。
5、操作人员上岗前,须经过专业培训,考试合格后,持证上岗。
此外,还要正确使用劳保用品,严格落实有关规章制度,切实保障安全防范措施的到位。
只有这样,才能有效预防各类机械伤害事故的发生,确保平安、健康。
1、不懂电器和机械的人员严禁使用和摆弄机电设备。
2、机电设备应完好,必须有可靠有效的安全防护装置。
3、机电设备停电、停工休息时必须拉闸关机,电箱按要求上锁。
4、机电设备应做到定人操作、定人保养、检查。
5、机电设备应做到定机经管、定期保养。
6、机电设备应做到定岗位和岗位职责。
7、机电设备不准带病运转。
8、机电设备不准确超负荷运转。
9、机电设备不准在运转时维修保养。
10、机电设备运行时,操作人员严禁将头、手、身伸入运转的机械行程范围内。
收藏分享评分①通过培训来提高人们辨别危险的能力;②通过对机器的重新设计,使危险更加醒目(或者使用警示标志);③通过培训,提高避免伤害的能力;④增强采取必要的行动来避免伤害的自觉性。
培训教材-机械伤害成因分析及防汇范措施

机械伤害成因分析及防汇范措施1、机械伤害的特点1).什么是机械伤害机械伤害是指机械做出强大的功能作用于人体的伤害。
2).机械伤害事故有什么特点机械伤害死亡事故的形式惨重,如搅死、挤死、压死、碾死、被弹出物体打死、磨死等。
当发现有人被机械伤害的情况时,虽及时紧急停车,但因设备惯性作用,仍可将受害造成致使性伤害,乃至身亡。
一般性工伤事故表现为:职工手指、胳膊、腿、脚趾骨骨折、挫伤,皮肤裂伤等。
3).常见伤害人体的机械设备有哪些有皮带运输机、行车、车床、磨床、铣床、砂轮机、泵、空压机等。
2.形成机械伤害的事故主要原因分析形成机械伤害的事故其主要原因有:1)检修、检查机械忽视安全措施。
如人进入设备检修、检查作业,不切断电源,未挂不准合闸警示牌,未设专人监护等措施而造成严重后果。
也有的因当时受定时电源开关作用或发生临时停电等因素误判而造成事故。
也有的虽然对设备断电,但因未等至设备惯性运转彻底停住就下手工作,同样造成严重后果。
2)缺乏安全装置。
如有的机械传动带、齿轮、接近地面的或人手能够着的联轴节、皮带轮、飞轮等易伤害人体部位没有完好防护装置;还有的人孔等部位缺护栏及盖板,无警示牌,人一疏忽误接触这些部位,就会造成事故。
3)电源开关布局不合理,一种是有了紧急情况不立即停车;另一种是好几台机械开关设在一起,开关位号未标识清楚,极易造成误开机械引发严重后果。
4)机械线路安装不规范,私拉乱接。
临时线路多,线路跨起、拖起、磨起。
5)自制或任意改造机械设备,不符合安全要求。
6)在机械运行中进行清理、卡料、上皮带蜡,加油等作业。
7)任意进入机械运行危险作业区(采样、干活、借道、拣物等)。
8)物件乱堆乱放,物件堆放不安全,堆放过高,车床床头、小刀架、床面、滑道面上随便放置工、量具,物件占压安全通道。
9)体力劳动强度大,易疲劳。
或用手工代替机械操作。
10)操作人员未经培训考核上岗或其他人员乱动机械。
3.防止机械伤害事故的防范措施防止机械伤害事故的防范措施有:1)检修机械必须严格执行断电挂禁止合闸警示牌和设专人监护的制度。
- 1、下载文档前请自行甄别文档内容的完整性,平台不提供额外的编辑、内容补充、找答案等附加服务。
- 2、"仅部分预览"的文档,不可在线预览部分如存在完整性等问题,可反馈申请退款(可完整预览的文档不适用该条件!)。
- 3、如文档侵犯您的权益,请联系客服反馈,我们会尽快为您处理(人工客服工作时间:9:00-18:30)。
整理范本
机械伤害的原因分析:
一、人的不安全行为
1、操作失误的主要原因有:
1)机械产生的噪声使操作者的知觉和听觉麻痹,导致不易判断或判断错误;
2)依据错误或不完整的信息操纵或控制机械造成失误;
3)机械的显示器、指示信号等显示失误使操作者误操作;
4)控制与操纵系统的识别性、标准化不良而使操作者产生操作失误;
5)时间紧迫致使没有充分考虑而处理问题;
6)缺乏对动机械危险性的认识而产生操作失误;
7)技术不熟练,操作方法不当;
8)准备不充分,安排不周密,因仓促而导致操作失误;
9)作业程序不当,监督检查不够,违章作业;
10)人为的使机器处于不安全状态,如取下安全罩、切除联锁装置等。
走捷径、图方便、忽略安全程序。
如不盘车、不置换分析等。
2、误入危区的原因主要有:
1)操作机器的变化,如改变操作条件或改进安全装置时;
2)图省事、走捷径的心理,对熟悉的机器,会有意省掉某些程序而误入危区;
3)条件反射下忘记危区;
4)单调、的操作使操作者疲劳而误入危区;
5)由于身体或环境影响造成视觉或听觉失误而误入危区;
6)错误的思维和记忆,尤其是对机器及操作不熟悉的新工人容易误入危区;
7)指挥者错误指挥,操作者未能抵制而误入危区;
8)信息沟通不良而误入危区;
9)异常状态及其它条件下的失误。
二、机械的不安全状态
机械的不安全状态,如机器的安全防护设施不完善,通风、防毒、防尘、照明、防震、防噪声以及气象条件等安全卫生设施缺乏等均能诱发事故。
动机械所造成的伤害事故的危险源常常存在于下列部位:
1、旋转的机件具有将人体或物体从外部卷入的危险;机床的卡盘、钻头、铣刀等、传动部件和旋转轴的突出部分有钩挂衣袖、裤腿、长发等而将人卷入的危险;风翅、叶轮有绞碾的危险;相对接触而旋转的滚筒有使人被卷入的危险。
2、作直线往复运动的部位存在着撞伤和挤伤的危险。
冲压、剪切、锻压等机械的模具、锤头、刀口等部位存在着撞压、剪切的危险。
3、机械的摇摆部位又存在着撞击的危险。
4、机械的控制点、操纵点、检查点、取样点、送料过程等也都存在着不同的潜在危险因素。
.。