DCS在柳钢2号高炉上的应用
DCS自动控制系统在冶金制氧中的应用

DCS自动控制系统在冶金制氧中的应用1.工业仪表最早出现在20世纪30年代,最初只用于热能动力和冶金等连续性的热力生产过程,因此当时称为热工仪表。
50年代我国出现DDZ-Ⅱ型仪表,就是当时四线制仪表;70年代我国出现DDZ-Ⅲ型仪表,这是仪表一个里程碑的发展,二线制仪表,就是既有电源又可以传输信号的工业仪表。
80年代初期我国在冶金制氧出现了“集散控制系统”DCS系统。
2 集散控制系统集散控制系统DCS可以解释为在模拟量回路控制较多的行业中,尽量将控制所造成的危险性分散,而将管理和显示功能集中的一种自动化高技术产品。
DCS系统一般由五部份组成:控制器、I/O板、操作站、通讯网络和图形及编程软件。
控制器:控制站是DCS的核心,直接与生产过程相连接,对过程变量进行检测和处理,并产生控制信号驱动现场的执行机构,实现生产过程的闭环控制。
流量的闭环控制系统DCS通常采用若干个控制器(过程站)对一个生产过程中的众多控制点进行控制,各控制器间通过网络连接并可进行数据交换。
操作采用计算机操作站,通过网络与控制器连接,收集生产数据,传达操作指令。
3 冶金制氧用DCS控制系统冶金制氧通常采用一个控制器的DCS控制系?y ,I/O:I/O板根据仪表在控制系统中所起的不同作用,将电动仪表的八大单元,即变送、调节、执行、运算、显示、转换、给定、辅助单元,直接进行检测,集成。
所有信号经控制器处理,发出控制信号驱动现场的执行机构,实现生产过程的闭环控制(1)空分温度、热电阻、热电偶等接触式温度检测仪表的测温元件,应安装在能准确反映介质温度的地方;安装在工艺管道上的测温元件应与管道中心线垂直或倾斜45°,插入深度应大于250mm或处在管道中心,插入方向宜与被测介质逆向或垂直。
管道公称直径小于80mm时可安装在弯头处或加扩大管;双金属温度计安装时,刻度盘面应便于观察;测温元件用连接头的螺纹应与测温元件螺纹相匹配;当水平安装时其插入深度大于1m或被测温度大于700℃时,应采取防弯曲措施。
DCS系统在钢铁行业中的应用案例分享
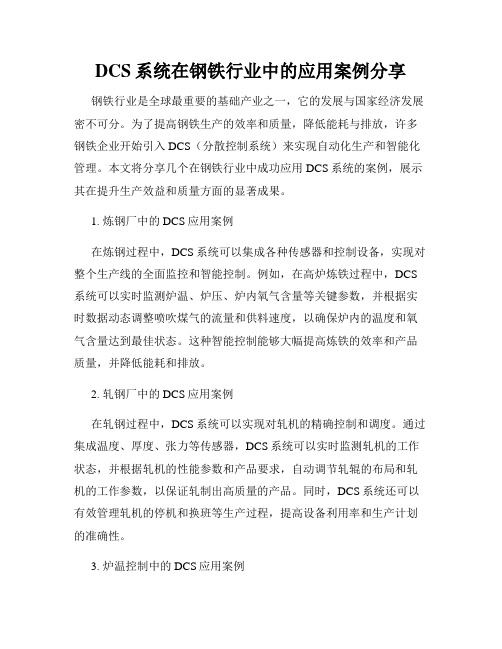
DCS系统在钢铁行业中的应用案例分享钢铁行业是全球最重要的基础产业之一,它的发展与国家经济发展密不可分。
为了提高钢铁生产的效率和质量,降低能耗与排放,许多钢铁企业开始引入DCS(分散控制系统)来实现自动化生产和智能化管理。
本文将分享几个在钢铁行业中成功应用DCS系统的案例,展示其在提升生产效益和质量方面的显著成果。
1. 炼钢厂中的DCS应用案例在炼钢过程中,DCS系统可以集成各种传感器和控制设备,实现对整个生产线的全面监控和智能控制。
例如,在高炉炼铁过程中,DCS 系统可以实时监测炉温、炉压、炉内氧气含量等关键参数,并根据实时数据动态调整喷吹煤气的流量和供料速度,以确保炉内的温度和氧气含量达到最佳状态。
这种智能控制能够大幅提高炼铁的效率和产品质量,并降低能耗和排放。
2. 轧钢厂中的DCS应用案例在轧钢过程中,DCS系统可以实现对轧机的精确控制和调度。
通过集成温度、厚度、张力等传感器,DCS系统可以实时监测轧机的工作状态,并根据轧机的性能参数和产品要求,自动调节轧辊的布局和轧机的工作参数,以保证轧制出高质量的产品。
同时,DCS系统还可以有效管理轧机的停机和换班等生产过程,提高设备利用率和生产计划的准确性。
3. 炉温控制中的DCS应用案例炉温是钢铁生产中非常重要的参数,它直接影响到钢材的质量和生产效益。
DCS系统在炉温控制中的应用可以帮助钢铁企业实现更加精确和稳定的温度控制。
通过采集炉温数据和环境数据,DCS系统可以根据事先设定的温度曲线,自动调节燃烧系统、送风系统等设备的工作参数,以实现最佳的炉温控制效果。
这种智能化控制不仅提高了产品的一致性和质量稳定性,还减少了人工干预和能耗浪费。
总结:DCS系统在钢铁行业中的应用案例丰富多样,从炼钢到轧钢,从生产线的控制到炉温的调节,都能发挥重要作用。
通过引入DCS系统,钢铁企业可以实现生产过程的智能化和自动化,提高生产效率,降低能耗和排放,提升产品质量稳定性和一致性。
DCS系统在金属加工中的应用效果
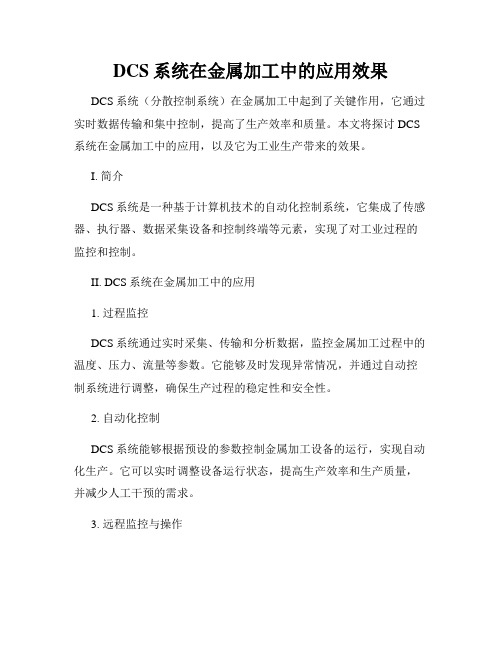
DCS系统在金属加工中的应用效果DCS系统(分散控制系统)在金属加工中起到了关键作用,它通过实时数据传输和集中控制,提高了生产效率和质量。
本文将探讨DCS 系统在金属加工中的应用,以及它为工业生产带来的效果。
I. 简介DCS系统是一种基于计算机技术的自动化控制系统,它集成了传感器、执行器、数据采集设备和控制终端等元素,实现了对工业过程的监控和控制。
II. DCS系统在金属加工中的应用1. 过程监控DCS系统通过实时采集、传输和分析数据,监控金属加工过程中的温度、压力、流量等参数。
它能够及时发现异常情况,并通过自动控制系统进行调整,确保生产过程的稳定性和安全性。
2. 自动化控制DCS系统能够根据预设的参数控制金属加工设备的运行,实现自动化生产。
它可以实时调整设备运行状态,提高生产效率和生产质量,并减少人工干预的需求。
3. 远程监控与操作DCS系统通过网络连接,实现对金属加工设备的远程监控与操作。
工作人员可以通过电脑或移动设备监视生产过程,同时进行参数调整和设备控制,减少了人力资源的消耗,提高了工作效率。
III. DCS系统在金属加工中的效果1. 提高生产效率DCS系统能够根据实时数据对生产过程进行优化调整,提高了生产效率。
通过自动化控制和远程监控,减少了生产过程中的停机时间,提高了设备利用率。
2. 保证生产质量DCS系统能够准确监测生产参数,保证金属加工过程的稳定性和一致性,有效避免了人为操作带来的误差。
这样,生产出的金属制品质量更加可靠,符合客户的需求。
3. 提高安全性DCS系统能够实时监测金属加工设备的工作状态,及时发现并解决潜在的安全问题。
它可以自动控制设备的运行,避免人为操作引起的事故风险,保障生产过程的安全性。
4. 减少人力成本DCS系统的自动化控制和远程监控功能减少了对人力资源的需求。
相比传统的人工操作模式,DCS系统能够集中管理和控制多个设备,节省了人力成本,提高了工作效率。
IV. 结论DCS系统在金属加工中的应用效果显著。
DCS系统在钢铁工业中的应用效果
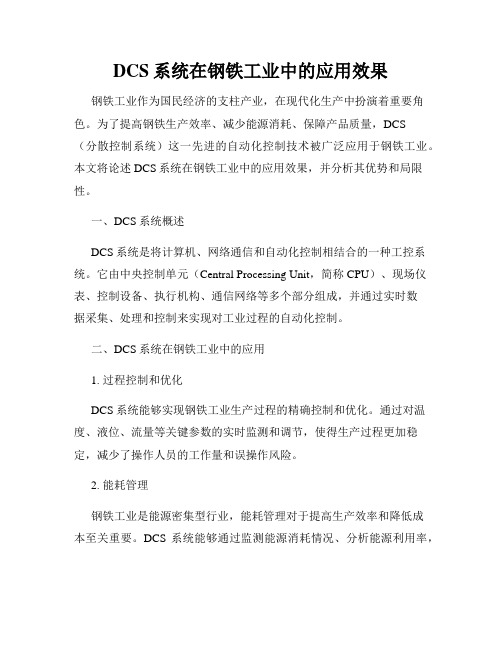
DCS系统在钢铁工业中的应用效果钢铁工业作为国民经济的支柱产业,在现代化生产中扮演着重要角色。
为了提高钢铁生产效率、减少能源消耗、保障产品质量,DCS(分散控制系统)这一先进的自动化控制技术被广泛应用于钢铁工业。
本文将论述DCS系统在钢铁工业中的应用效果,并分析其优势和局限性。
一、DCS系统概述DCS系统是将计算机、网络通信和自动化控制相结合的一种工控系统。
它由中央控制单元(Central Processing Unit,简称CPU)、现场仪表、控制设备、执行机构、通信网络等多个部分组成,并通过实时数据采集、处理和控制来实现对工业过程的自动化控制。
二、DCS系统在钢铁工业中的应用1. 过程控制和优化DCS系统能够实现钢铁工业生产过程的精确控制和优化。
通过对温度、液位、流量等关键参数的实时监测和调节,使得生产过程更加稳定,减少了操作人员的工作量和误操作风险。
2. 能耗管理钢铁工业是能源密集型行业,能耗管理对于提高生产效率和降低成本至关重要。
DCS系统能够通过监测能源消耗情况、分析能源利用率,并提供相应的节能建议。
通过实施节能措施和优化能源配置,有效降低了能源消耗。
3. 质量控制DCS系统能够实时监测和控制生产过程中的关键参数,并根据设定的标准进行判断和调整,确保产品质量的稳定和达标。
同时,DCS系统还能够对产品进行追溯,便于排查和解决质量问题。
4. 故障诊断和预测DCS系统通过集成大量传感器和设备,能够实时获取设备运行信息,并通过数据分析,及时发现设备故障和异常情况。
同时,DCS系统还能够对设备的寿命进行预测,提前进行维护和更换,避免了因设备故障导致的生产中断和损失。
三、DCS系统的优势和局限性1. 优势(1)高度自动化:DCS系统能够实现对钢铁生产过程的全面自动化控制,大幅减少了人工干预,提高了生产效率。
(2)实时监测和反馈:DCS系统能够实时监测各个关键参数,及时反馈到中央控制单元,使得生产过程更加精确和稳定。
DCS系统在冶金行业中的应用及其关键技术
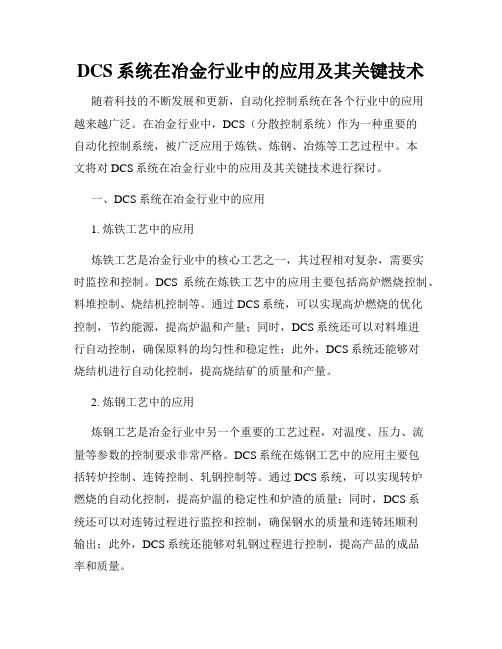
DCS系统在冶金行业中的应用及其关键技术随着科技的不断发展和更新,自动化控制系统在各个行业中的应用越来越广泛。
在冶金行业中,DCS(分散控制系统)作为一种重要的自动化控制系统,被广泛应用于炼铁、炼钢、冶炼等工艺过程中。
本文将对DCS系统在冶金行业中的应用及其关键技术进行探讨。
一、DCS系统在冶金行业中的应用1. 炼铁工艺中的应用炼铁工艺是冶金行业中的核心工艺之一,其过程相对复杂,需要实时监控和控制。
DCS系统在炼铁工艺中的应用主要包括高炉燃烧控制、料堆控制、烧结机控制等。
通过DCS系统,可以实现高炉燃烧的优化控制,节约能源,提高炉温和产量;同时,DCS系统还可以对料堆进行自动控制,确保原料的均匀性和稳定性;此外,DCS系统还能够对烧结机进行自动化控制,提高烧结矿的质量和产量。
2. 炼钢工艺中的应用炼钢工艺是冶金行业中另一个重要的工艺过程,对温度、压力、流量等参数的控制要求非常严格。
DCS系统在炼钢工艺中的应用主要包括转炉控制、连铸控制、轧钢控制等。
通过DCS系统,可以实现转炉燃烧的自动化控制,提高炉温的稳定性和炉渣的质量;同时,DCS系统还可以对连铸过程进行监控和控制,确保钢水的质量和连铸坯顺利输出;此外,DCS系统还能够对轧钢过程进行控制,提高产品的成品率和质量。
3. 冶炼工艺中的应用冶炼工艺是冶金行业中的另一个重要环节,其过程涉及到多个工序和设备的协同运行。
DCS系统在冶炼工艺中的应用主要包括矿石破碎、矿石浮选、冶炼反应、尾渣处理等。
通过DCS系统,可以对矿石破碎过程进行监控和控制,确保矿石的粒度和质量符合冶炼工艺要求;同时,DCS系统还可以对矿石浮选过程进行自动控制,提高选矿的效率和回收率;此外,DCS系统还能够对冶炼反应进行实时监控,确保反应的稳定性和产品质量;最后,DCS系统还能够对尾渣处理过程进行控制,减少环境污染。
二、DCS系统在冶金行业中的关键技术1. 数据采集和处理技术DCS系统需要采集大量的数据,并对数据进行实时处理和分析。
柳钢2号高炉实现智能喷吹的研究

151管理及其他M anagement and other柳钢2号高炉实现智能喷吹的研究王绪鹏,刘 敏,朱国铭,黄华钢,林俊贤(广西柳州钢铁集团有限公司,广西 柳州 545002)摘 要:高炉喷吹煤粉是从高炉风口向炉内直接喷吹磨细了的无烟煤粉或烟煤粉或这两者的混合煤粉,以替代焦炭起提供热量和还原剂的作用,从而降低焦比,降低生铁成本。
随着煤粉均匀输送到风口,煤粉的燃烧效率提高,对改善高炉的炉况、保证高炉顺行有利,起到了增产的作用。
因此将高炉的煤粉喷吹工艺控制过程由手动控制、半自动控制改造为自动控制,解决煤粉喷吹控制过程存在的动态性、非线性、滞后性的问题是很有必要的。
关键词:喷煤;智能;自动控制中图分类号:TF325.6 文献标识码:A 文章编号:11-5004(2020)12-0151-2收稿日期:2020-06作者简介:王绪鹏,男,生于1986年,汉族,广西玉林人,工程师,研究方向:冶金行业。
1 目前现状柳钢2号高炉喷煤喷吹系统采用半自动人工作。
存在喷煤速率波动大、输送煤粉不均匀,影响煤粉燃烧率、增加氮气消耗。
喷吹压力不稳定,影响高炉热风压力波动、换罐断煤、系统不连续。
依靠人工操作,喷煤量的准确性难以保证。
主要存在以下问题。
(1)喷吹量调节主要以罐压调整作为主要手段,调压过程金对分配器压力产生影响,对均匀喷吹不利。
(2)喷吹速率波动大,瞬时速率偏差可达6t/h。
(3)在人工操作的情况下,往往只关注保证整点煤量,对小时时段内各个更小时间段,例如按小时设定量计算每3min 该喷煤量,实际喷煤量,缺乏精细控制,小时时段内喷煤量偏差达到lt。
(4)倒罐期间喷煤波动大且断流,导致现场喷煤不均匀,不稳定,不连续。
(5)同时由于喷煤速率波动大、不稳定而增加了气量消耗,增加了操作人员的劳动强度。
(6)喷吹速率不稳,煤焦置换比降低,煤粉在高炉回旋区的燃烧率降低,使更多的未燃尽煤随煤气移出炉外,对除尘工艺负荷加大,能耗严重。
DCS系统在钢铁行业中的关键作用和效益
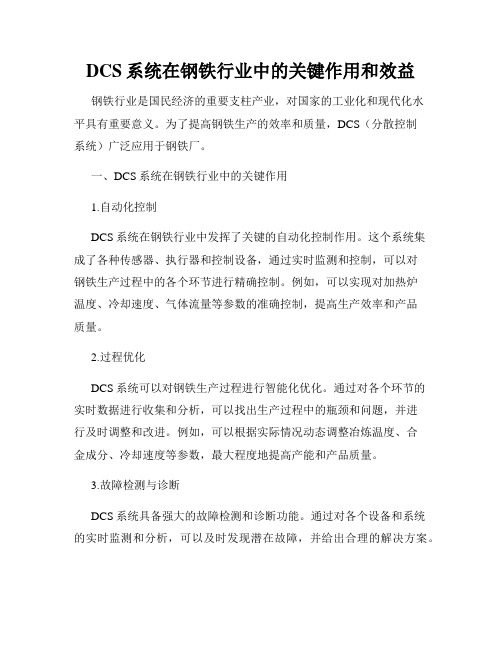
DCS系统在钢铁行业中的关键作用和效益钢铁行业是国民经济的重要支柱产业,对国家的工业化和现代化水平具有重要意义。
为了提高钢铁生产的效率和质量,DCS(分散控制系统)广泛应用于钢铁厂。
一、DCS系统在钢铁行业中的关键作用1.自动化控制DCS系统在钢铁行业中发挥了关键的自动化控制作用。
这个系统集成了各种传感器、执行器和控制设备,通过实时监测和控制,可以对钢铁生产过程中的各个环节进行精确控制。
例如,可以实现对加热炉温度、冷却速度、气体流量等参数的准确控制,提高生产效率和产品质量。
2.过程优化DCS系统可以对钢铁生产过程进行智能化优化。
通过对各个环节的实时数据进行收集和分析,可以找出生产过程中的瓶颈和问题,并进行及时调整和改进。
例如,可以根据实际情况动态调整冶炼温度、合金成分、冷却速度等参数,最大程度地提高产能和产品质量。
3.故障检测与诊断DCS系统具备强大的故障检测和诊断功能。
通过对各个设备和系统的实时监测和分析,可以及时发现潜在故障,并给出合理的解决方案。
例如,可以在设备出现过载、过热等异常情况时及时警示并采取相应的措施,防止设备损坏和生产事故的发生。
二、DCS系统在钢铁行业中的效益1.提高生产效率DCS系统的应用使得钢铁生产过程更加高效和精确。
通过自动化控制和智能化优化,可以最大程度地减少人为因素的干预,提高生产效率和效益。
同时,DCS系统的实时监测和数据分析功能,可以帮助企业及时发现生产过程中的问题,并采取相应措施,减少生产线停机和损失。
2.提高产品质量DCS系统的精确控制和优化功能,使得钢铁产品的质量更加稳定和可靠。
通过对各个参数的实时监测和调整,可以确保产品的成分和性能达到设计要求。
此外,DCS系统的故障检测和诊断功能,可以帮助企业及时修复设备故障,减少产品次品率和废品率。
3.降低能耗和成本DCS系统的智能化优化功能,可以帮助企业降低能耗和成本。
通过对能耗和成本的实时监测和分析,可以找出能耗高、成本大的环节,并制定相应的节能和降本措施。
DCS系统在热电厂锅炉中的应用

DCS系统在热电厂锅炉中的应用摘要DCS系统在热电厂锅炉中的应用,可以使控制更加易于实现,可靠和方案优化。
便于故障的查找,分析和处理。
提升企业的信息化,便于管理。
关键词DCS系统;控制方案;系统配置;监视;管理所谓集散控制系统(即DCS,英文名称为Distributed Control System),其含义是利用微处理机或微型计算机技术对生产过程进行集中管理和分散控制。
是4C技术的产物。
4C技术就是控制技术(Control),计算机(Computer)技术,通讯(Communication)技术和CRT(Cathode Ray Tube)显示技术。
整个装置继承了常规仪表控制系统和计算机集中控制系统的优点,克服了单微机控制系统危险性高度集中以及常规仪表控制功能单一,人/机联系差的缺点,可以方便地用于工业装置的生产控制和经营管理,在电厂锅炉流程自动化领域的应用已经十分普及。
1 锅炉控制方案锅锅炉控制方案:常用的有燃烧自动控制,汽包水位自动控制。
1)锅炉燃烧系统控制可分散成:给煤控制,送风控制,炉膛负压控制(1)给煤控制原理说明:采用三冲量单级调节,以锅炉出口蒸汽压力为被调节变量,主汽流量信号和汽包压力信号为补充信号,PID调节作用为反作用。
即锅炉出口蒸汽压力大于给定值时,减少给煤量,汽包压力经分流后正方向接入。
主汽流量信号经分流后反向接入。
(2)送风控制原理说明:采用串级调节。
以烟气含氧量信号为主调变量,经主调节器运算后作为副调节器的给定信号。
主汽流量信号为补充信号,从而改变送风量以适应氧量及主汽流量的变化。
(3)炉膛负压原理说明:采用单冲量调节。
以炉膛负压为被调节变量。
锅炉燃烧自动控制在以往二型,三型仪表时代在实际应用中很难投入,利用集散控制系统强大的控制功能和灵活的组态方式,超前及延时功能。
在实际应用得以实现。
方便了锅炉的运行调整。
提高了锅炉运行的稳定性燃烧经济性。
2)汽包液位控制锅炉给水自动调节的任务是使给水量跟踪锅炉的蒸发量,并使汽包液位保持在工艺允许的范围内。
- 1、下载文档前请自行甄别文档内容的完整性,平台不提供额外的编辑、内容补充、找答案等附加服务。
- 2、"仅部分预览"的文档,不可在线预览部分如存在完整性等问题,可反馈申请退款(可完整预览的文档不适用该条件!)。
- 3、如文档侵犯您的权益,请联系客服反馈,我们会尽快为您处理(人工客服工作时间:9:00-18:30)。
( 3 )气密箱温度高于 7c。 0= 【 ( 4 )炉顶温度高于50 。 0 ̄ C
()炉 顶压力 高 于 2 0 P 。 5 2 K a
3 历史 数据查 询 . 4
4结
语
()过 程参 数 的集 中显示 为 高炉全 局控 制和 1
分析 炉况 、指导 冶炼 提供 了有利 条件 。 () 控制 系统利 用梯 型 图编程 简 单清晰 ;同 2 可 以制作 数 据 趋 势 图 ,通 过 趋 势 图 可 以 观 察 炉况 ,一 旦 出现 异 常 极 易 发 现 ,而 且 可 以 调
定之后才能正常工作 ,否则在 R Lg 0 0 Soi 50 的 x
硬 件 结 构上 ,远 程 机 架 的所 有 模 块 前 会 出现 黄
上位机编写公式计算出的_艺参数数值无法存 丁 储 ,切换画面后历史数据无法查询 ;在下位机 编程计算 出来的工艺参数值 可以赋给一个变量
名 ,可 以保 存历史 数据 并查 询 。
力系数 、高炉全压差 、理论燃烧温度 、富氧率 、
鼓 风动 能 、标 准 风速 、实 际 风 速 、鼓 风 湿度 等 参数 的计 算 。在 C nrl oi控 制 系统 中 ,有两 ot g oL x 种 方式 进 行 数 学 运 算 ,一 种 是 通 过 上 位 机 直接
编 写公 式 ,另 一 种 是 通过 下 位 机 编 程 实 现 。在
■l
D S在 柳钢 2号 高炉上 的应 用 C
l 前 言
麓
对各过程参数和 R Lg 0 0 S oi 50 进行链接等。 x
() 程 序 编 写 。在 R Lg 50 6 Soi 00中编 写相 x
柳 钢 炼铁 厂 2号 高 炉 ( 0 m) 的仪 表 过 200
程检测与控制系统采用 了 C n o Lg 作为集成 关 程序 ,如 流 量 的计 算 、数 学 模 型 的 建立 、系 ot l oi r x 架构。下位机使用 R L g 50 n rreSr s 统时间的调用等 ,并设置通道量程等 。 S oi 00E t p s e e x e i i
32 数学公 式运 算 .
2 系统调试
高炉 系统 的过 程监 控 数据 较 多 ,和辅 助 系统
之间存 在很多数据交换 。系统调试 的主要步骤
如下:
() R Ln 1 Si x及 l 址 设 置 。 在 R Ln P地 S ix中 添 加 了 通讯 网卡 之 后 ,设 置 电脑 T PI ,然 后 C/ P 通 过 R N toxf o t le v . 件 为 1 5 一 S ew r o cnr n t 8 r o 0软 7 6
设定重要 参数异常 的相 关报警 ,报警值可
根据工艺要求手动设定 ,一 旦出现异常 ,画面
相 应 参 数不 断 闪烁 ,同 时 声 音 报警 器 发 出声 音 报 警 ,直 至 恢 复 正 常 ,报警 自动取 消பைடு நூலகம்。报 警 值
Ve t i S 5 制作生产工艺流程图,制作实 i S d E . w uo 0 时和历史趋势 图 ,设置历史数据保存路径 ,并
C nrl oi 控 制 系统 的 主要 功能包 括 过程 o t gx oL
3 功能实现
通讯软件为 R Ln 2 2 S i V . ,并利用 它所 提供的 x 5 O C接 口进行数据采集 。该控制 系统具有强大 P
的控制功 能 ,控制器 支 持 的数 字 量 I / 多 可达 O最 到 1800点 ,模拟量 I 2 0 / 多可 达到 40 0点 。 O最 0
一
数 据 的大 量 采 集 和集 中显 示 、数 学 公 式运 算 功 能 、报 警功 能等 。 31 过 程参数 集 中显 示 .
整 个 系统 工 艺 流 程 分 6大 系 统 :本 体测 温
个 控制器 支持 3 任务 。 2个
系 统 、冷 却 水 系 统 、送 风 系统 、报 警 系统 、炉 顶系统 、设定 系统 等 。通 过 C nrl oi控 制系 ot g oL x 统 ,可 以将 分 散 的 过程 数 据 集 中在 操作 室 的计 算 机 上 显 示 。值班 工 长 在 计 算 机 前操 作 ,可 以 全 面地 掌 握 高 炉 冶炼 过 程 中 的实 时 状况 ,充 分 体现 了集 中控 制 的理念 。
33 报 警 系统 .
色的感叹号 ,只有将 网络整定 成功 以后 ,感叹 号才会消除,模块才能正常工作 。
()T g的 建立 。T g的 建 立 有 3个 途 径 , 4 a a 可 以分 别 在上 位 机 、下 位 机 控制 器 和 下位 机 主
程 序 中创 建 。建议 在下 位机 中创 建 。 () 工 艺 流 程 图 制 作 。 利 用 Fc rTl 5 at y a o k
V1. 60 行 编程 ;上 位 机 使用 FcoyakVe 3进 at T l iw r Su i S 50制 作 画面 及运 行 画 面 ;通 过 R N t tdo E . Se — W F r ot le v . OXo nr nt 80软件 进行 网络 优化 ;网络 f c o
幔I
设定 主要包括 :
()采 用屏 蔽 电缆 ,并 专 门埋 设仪 表地 线 , 3
() 中压水压 力低 于 07 a 1 .MP 。
保 证 可靠接 地 。
()高 压水压 力低 于 1 a 2 . MP 。 5
()系统 间的网络传输 ,距离超过 10 4 0 m,
全部 采用光 纤通讯 。
EB N T设置地址。设置成功后 , 计算机即可和模
块进 行通讯 。 () 硬件 组态 。按照 R Ln 显示 的模 块 2 S ix里 顺 序 ,在 R Lgx50 组态 。 Soi 00里
() 网络 整定 。远 程 机 均 需 要 经 过 网络 整 3
数学 公 式 运 算 包 括 高 炉 透 气 性 、透 气性 阻