焊管调整技术教程
电焊焊管操作方法

电焊焊管操作方法
电焊焊管操作方法如下:
1. 准备工作:
- 将焊管清洁干净,去除表面的油脂和污垢。
- 确保电焊机和其他工具正常工作。
2. 切割焊管:
- 使用管钳固定焊管。
- 使用锯片或切割机等工具将焊管根据需要的尺寸切割成所需的长度。
3. 准备焊接接头:
- 使用砂纸或钢丝刷清洁焊管的两端,确保没有锈蚀或腐蚀。
- 在焊管的两端涂抹焊接剂。
4. 安装连接件:
- 根据需要的连接方式,选择合适的连接件,如弯头、三通等。
- 使用砂纸或钢丝刷清洁连接件的内部和外部。
5. 连接管道:
- 将焊管与连接件对齐,确保完全插入。
- 使用管钳将焊管紧固在连接件上。
6. 进行电焊焊接:
- 打开电焊机,调整合适的电流和焊接速度。
- 使用焊剂预热管道焊缝。
- 使用焊条或焊丝进行焊接,确保焊条或焊丝充满焊缝。
7. 完成焊接:
- 等待焊缝冷却。
- 使用砂纸或钢丝刷清除焊接残渣和焊缝周围的锈蚀或腐蚀。
- 检查焊缝的质量,并进行必要的修补。
请注意,以上步骤仅为基本操作方法,具体操作步骤可能因实际情况有所不同。
在进行电焊焊管操作时,务必严格遵守相关安全规定,佩戴个人防护设备,如焊接手套、面罩和防护镜等,以确保操作安全。
如果不熟悉电焊操作或缺乏相关经验,建议寻求专业人士的帮助或培训。
高频焊管机的调试技巧
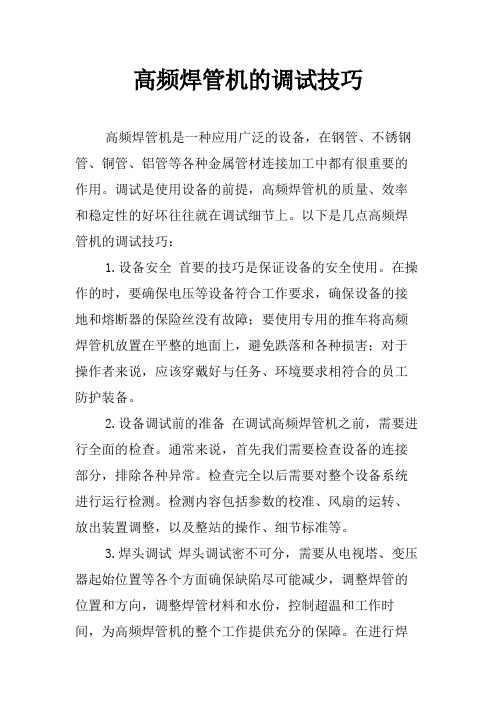
高频焊管机的调试技巧高频焊管机是一种应用广泛的设备,在钢管、不锈钢管、铜管、铝管等各种金属管材连接加工中都有很重要的作用。
调试是使用设备的前提,高频焊管机的质量、效率和稳定性的好坏往往就在调试细节上。
以下是几点高频焊管机的调试技巧:1.设备安全首要的技巧是保证设备的安全使用。
在操作的时,要确保电压等设备符合工作要求,确保设备的接地和熔断器的保险丝没有故障;要使用专用的推车将高频焊管机放置在平整的地面上,避免跌落和各种损害;对于操作者来说,应该穿戴好与任务、环境要求相符合的员工防护装备。
2.设备调试前的准备在调试高频焊管机之前,需要进行全面的检查。
通常来说,首先我们需要检查设备的连接部分,排除各种异常。
检查完全以后需要对整个设备系统进行运行检测。
检测内容包括参数的校准、风扇的运转、放出装置调整,以及整站的操作、细节标准等。
3.焊头调试焊头调试密不可分,需要从电视塔、变压器起始位置等各个方面确保缺陷尽可能减少,调整焊管的位置和方向,调整焊管材料和水份,控制超温和工作时间,为高频焊管机的整个工作提供充分的保障。
在进行焊接操作的过程中,不仅需要控制操作的时间,还需要调整其他属性。
例如,焊接的速度不能太快或太慢,以避免焊接出现不均匀等问题,同时需要确保服务器了高频焊管机的工作要求,以充分满足操作要求。
4.采用合适的电源在调试高频焊管机时,我们需要根据设备的具体情况选择合适的电源,并确保电源稳定,工作正常。
根据设备版本、工作要求和功能需求等方面进行选择。
5.焊接机本身的工作环境高频焊管机的操作和质量还与工作环境有关。
要保持空气干燥、整洁,避免各种影响焊接工作的因素干扰,比如粉尘、霉菌等。
为此,我们需要将高频焊管机移动到干燥、无霉虫环境中工作,避免在一些恶劣环境下工作。
6.值得关注的测试仪器高频焊管机的调试还需要使用一些测试仪器,比如电缆测试仪等。
我们需要充分利用这些测试仪器进行各种测量,准确分析设备的工作情况。
高频焊管成型调整技术方法
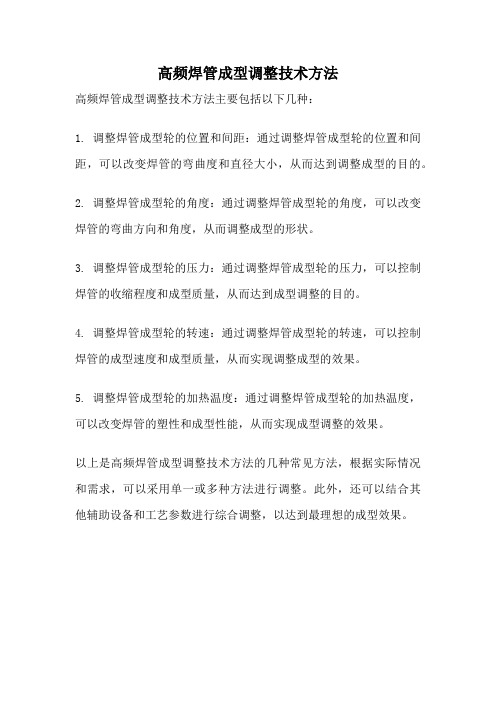
高频焊管成型调整技术方法
高频焊管成型调整技术方法主要包括以下几种:
1. 调整焊管成型轮的位置和间距:通过调整焊管成型轮的位置和间距,可以改变焊管的弯曲度和直径大小,从而达到调整成型的目的。
2. 调整焊管成型轮的角度:通过调整焊管成型轮的角度,可以改变焊管的弯曲方向和角度,从而调整成型的形状。
3. 调整焊管成型轮的压力:通过调整焊管成型轮的压力,可以控制焊管的收缩程度和成型质量,从而达到成型调整的目的。
4. 调整焊管成型轮的转速:通过调整焊管成型轮的转速,可以控制焊管的成型速度和成型质量,从而实现调整成型的效果。
5. 调整焊管成型轮的加热温度:通过调整焊管成型轮的加热温度,可以改变焊管的塑性和成型性能,从而实现成型调整的效果。
以上是高频焊管成型调整技术方法的几种常见方法,根据实际情况和需求,可以采用单一或多种方法进行调整。
此外,还可以结合其他辅助设备和工艺参数进行综合调整,以达到最理想的成型效果。
焊管调整技术教程
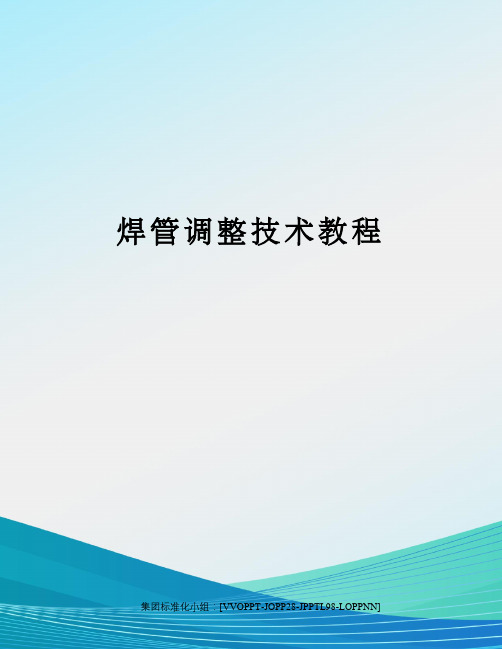
焊管调整技术教程集团标准化小组:[VVOPPT-JOPP28-JPPTL98-LOPPNN]一:换辊:1,基准面距离:轴瓦一端有一固定端,此固定端有一基准面,或在牌坊架上,或在轴瓦上,以此确定轧制中心基准面与轧制中心的垂直距离。
2,为保证轧辊预装位置正确,必须保证各水平机架的基准面在同一平面内,不得松动。
3,水平下轴的水平高度各架应严格一致,以保证轧辊水平位置准确。
4,机架组装的注意事项。
A,开口机架下轴瓦注意方向,避免装反,上下轴不准装反。
B,各调整部位保证滑动,调整方便。
C,各紧固部件不得松动。
D, 检查轧辊尺寸和表面.检查各封闭孔导向环的尺寸和表面.E, 轧辊安装固定要紧固,不允许有轴向串动和径向跳动,检查轴承是否损坏,松动.二:换辊后的调整:1, 校验轧制中心线:A,以水平下辊为基准面校验轧制中心线是调整机组的原则。
B, 拉一中心细线通过成型第一架到定径最后一架,保持一定张力,并靠合孔型槽底,注意中心线不得与水平下辊外的任何部件接触。
C,各架水平下辊的孔型中心均与中心线位置相符。
D,各架水平下辊孔型槽底均与中心线靠合。
E,正确调整轧辊的水平位置.从横向检查成型机各架水平辊的上下辊轴的中心线是否水平,是否有一头高一头低的倾斜现象,通过压下装置调整水平.F,正确调整各架的辊缝.按照孔型图和工艺规程调整各水平辊和立辊的辊缝,一般为带钢的厚度.辊缝过大则照成变形不充分,带钢在孔型内左右滑动和扭转,辊缝过小使成型负荷增加,机架损坏.2, 立辊调整:A, 与轧制中心对称。
B, 端面水平。
C, 成型2,3,4架立辊下沿高于轧制中心线。
D, 其他的按椭圆到圆应略底于轧制中心线。
3, 调整原则:A, 立辊偏高:使变形带钢头部上翘,严重的造成跑头,还将使运行带钢在立辊间构成弓型,使孔型下部磨损增大,边缘刻伤带钢。
B, 立辊偏低:对变形带钢进入孔型不利,易跑头,并刻伤带钢边缘或出现横向墩粗,造成焊接质量缺陷。
螺旋焊管数据调型方法

业 环节 , 节省 了大量 劳动力 。
【 成 松 。 杂 , 洪 洋 等 . 业 工程 学 报 》2 1 ,1 ) 李 坎 谭 《 农 。0 2 (0 】
・
企业天地 ・
新疆农机化
2 1 年第 3 02 期
成型角计算 :
C S t B 'D=1 5 / . 4 7 0 0 5 2 O O /r = r 2 0 31  ̄ 2 = .5 9
6号 辊 尺 寸距 离 即 为所 需 管 径 , 、 辊 均 与 滑 5号 7号 轨平行 , 与 6 辊 相切 , 且 号 画一管 径后 即可绘 出。在 实 际工 作 中 , 还发 现一 种 函数 关 系 , 以不 用 绘 图 , 可
2 1 年第 3 02 期
新疆农机化
・ 业天 地 ・ 企
螺旋焊管数据调型方 法
赵 艺
( 疆 八 钢 金 圆 钢 管 有 限 公 司 , 疆 乌 鲁木 齐 8 0 2 ) 新 新 3 0 6
摘 要 : 绍 了螺 旋 焊 管 成 型 器 不 同 结 构采 用 的 不 同数 据 调 型 方 法 介 关 键 词 : 管 ; 据 调 型 ; 法 焊 数 方
号、 3号辊 支撑 、 2号辊 压下 , 完成 由卷 板到 钢管 冷弯
1 前 言
螺 旋 焊 管一 般 用 于输水 、 气 、 力 管 网建 设 、 输 热 农 田灌 溉 、水利 管 网建设 中。八 钢 金 圆钢管 有 限公 司是生 产螺旋 焊 管 的专业 厂家 ,生 产 的管 径 尺寸从 (29 25 0 m 约 有 3 2 1~ 4 m j O多种 。调 型技 术 是 螺旋 焊 管机 组 的关 键 技术 , 19 从 9 7年建 厂开始 公 司就一 直 采用 样 筒调 型方 法 ,即将样 筒放 置 在成 型 器 的 1 号、 3号辊 上 , 筒落 稳后 按 照样 筒外 形 尺 寸分 别调 样 整 4号 、 5号 、 6号 、 7号 、 外 控 辊 的位 置 及 参 数 8号 ( 1 , 外控辊 和样 筒相 接触 。 图 )使 这种 方法 生产 时每
焊接参数调整方法介绍课件
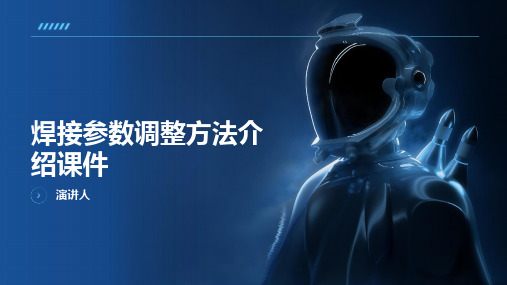
01
焊接参数影 响焊接质量, 进而影响生 产效率
02
焊接参数影 响焊接速度, 进而影响生 产效率
03
焊接参数影 响焊接成本, 进而影响生 产效率
04
焊接参数影 响焊接工艺, 进而影响生 产效率
影响成本控制
焊接参数影响 焊接质量,质 量不佳会增加 返工成本
01
焊接参数影响 能源消耗,能 源浪费会增加 能源成本
调整电压时,可以通过试验和经验来确定最佳电压值, 以保证焊接质量和效率。
速度参数的调整
01
速度参数是焊接 过程中非常重要 的参数之一,它 决定了焊接的速
度和效率。
02
速度参数的调整 需要根据焊接材 料的特性、焊接 工艺的要求以及 焊接设备的性能 等因素进行综合
考虑。
03
速度参数的调整 可以通过调整焊 接设备的速度控 制旋钮或者通过 焊接设备的控制 系统进行设置。
04
气体保护:影响 焊缝质量和焊接
效率
05
焊丝直径:影响 熔化速度、焊缝 成形和焊接效率
06
焊接位置:影响 熔化速度、焊缝 成形和焊接效率
07
焊接材料:影响 焊缝质量和焊接
效率
08
焊接工艺:影响 焊缝质量和焊接
效率
09
焊接设备:影响 焊接速度和焊接
效率
10
环境因素:影响 焊接质量和焊接
效率
影响生产效率
01
生产环境的温度和湿度:选择适合生产环境 的焊接参数,以保证焊接质量
02
生产环境的通风和照明:选择适合生产环境 的焊接参数,以保证焊接安全和效率
03
生产环境的噪音和振动:选择适合生产环境 的焊接参数,以保证焊接精度和稳定性
氩弧焊制管入门
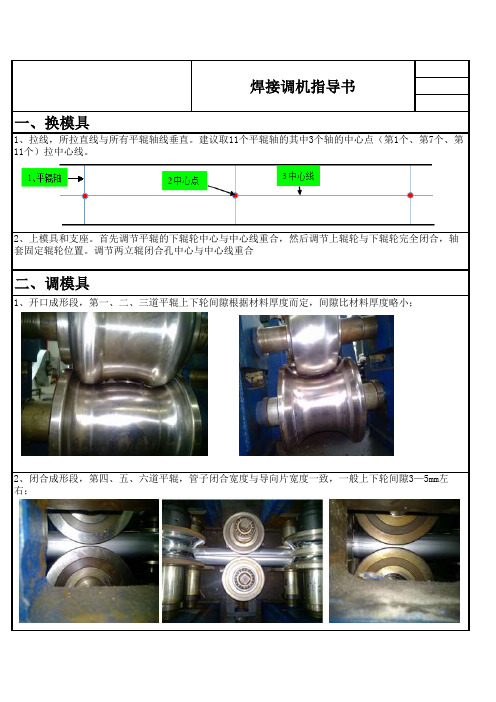
1-2mm 2-3mm
四、焊接常见问题
原因 解决方法
①无保护气体流出,没有打开气阀或气管堵塞; ①打开气阀,保证气管畅通 1、不能引弧 ②焊接方式选择开关设成了手工焊方式 2、焊偏 ①钨针偏离管子闭合缝隙中心; ①焊接电流过小或转速过快; 3、未焊透 ②钨针烧损: ③钨针到管子距离过远 ②焊接方式设置为自动焊 ①调节焊枪使管子两边缘熔化宽度一样 ①根据熔透程度相应的增加电流或减小 速度 ②更换钨针 ③适当向下调节焊枪
焊接调机指导书 一、换模具
1、拉线,所拉直线与所有平辊轴线垂直。建议取11个平辊轴的其中3个轴的中心点(第1个、第7个、第 11个)拉中心线。
2、上模具和支座。首先调节平辊的下辊轮中心与中心线重合,然后调节上辊轮与下辊轮完全闭合,轴 套固定辊轮位置。调节两立辊闭合孔中心与中心线重合
二、调模具
1、开口成形段,第一、二、三道平辊上下轮间隙根据材料厚度而定,间隙比材料厚度略小;
2、闭合成形段,第四、五、六道平辊,管子闭合宽度与导向片宽度一致,一般上下轮间隙3—5mm左 右;
3、立辊保证两平辊之间材料边缘平直,平滑过渡,自然成形(钢带边缘与导向片所成俯视图为等腰梯 形)
三、焊枪
1、两把焊枪焊接,前枪为直柄枪,后枪 2、钨针磨削方向为竖直方向,钨 3、钨针伸出磁嘴长度1— 为Y柄枪;两枪向前倾斜角度α 为60°— 针顶部直径0.2—0.3mm; 2mm,钨针到管子距离2— 70°,焊枪对中,焊接后管子缝隙两边 3mm; 熔化宽度一样,固定焊枪;
4、错边
①焊接轮的两个轮子高度不一致;
①调节焊接轮使两个轮子高度一致
①管子边缘成型不好,有褶皱现象,可能是前两 ①适当向上调节平辊或调节立辊增大间 个平辊压的太紧或立辊收缩太紧; 距,使边缘平直无褶皱 5、焊穿 ②焊接轮松动; ③钨针到管子距离太近 6、焊缝过高 ①焊接轮两个轮子距离过近,电流偏大 ①钨针烧损,电流偏大; 7、焊缝过宽 ②钨针距节焊枪 ①调节焊接轮距离,适当减小电流 ①更换钨针,适当减小电流
焊管调整技术教程

焊管调整技术教程一:换辊:1,基准面距离:轴瓦一端有一固定端,此固定端有一基准面,或在牌坊架上,或在轴瓦上,以此确定轧制中心基准面与轧制中心的垂直距离。
2,为保证轧辊预装位置正确,必须保证各水平机架的基准面在同一平面内,不得松动。
3,水平下轴的水平高度各架应严格一致,以保证轧辊水平位置准确。
4,机架组装的注意事项。
A,开口机架下轴瓦注意方向,避免装反,上下轴不准装反。
B,各调整部位保证滑动,调整方便。
C,各紧固部件不得松动。
D, 检查轧辊尺寸和表面.检查各封闭孔导向环的尺寸和表面.E, 轧辊安装固定要紧固,不允许有轴向串动和径向跳动,检查轴承是否损坏,松动.二:换辊后的调整:1, 校验轧制中心线:A,以水平下辊为基准面校验轧制中心线是调整机组的原则。
B, 拉一中心细线通过成型第一架到定径最后一架,保持一定张力,并靠合孔型槽底,注意中心线不得与水平下辊外的任何部件接触。
C,各架水平下辊的孔型中心均与中心线位置相符。
D,各架水平下辊孔型槽底均与中心线靠合。
E,正确调整轧辊的水平位置.从横向检查成型机各架水平辊的上下辊轴的中心线是否水平,是否有一头高一头低的倾斜现象,通过压下装置调整水平.F,正确调整各架的辊缝.按照孔型图和工艺规程调整各水平辊和立辊的辊缝,一般为带钢的厚度.辊缝过大则照成变形不充分,带钢在孔型内左右滑动和扭转,辊缝过小使成型负荷增加,机架损坏.2, 立辊调整:A, 与轧制中心对称。
B, 端面水平。
C, 成型2,3,4架立辊下沿高于轧制中心线。
D, 其他的按椭圆到圆应略底于轧制中心线。
3, 调整原则:A, 立辊偏高:使变形带钢头部上翘,严重的造成跑头,还将使运行带钢在立辊间构成弓型,使孔型下部磨损增大,边缘刻伤带钢。
B, 立辊偏低:对变形带钢进入孔型不利,易跑头,并刻伤带钢边缘或出现横向墩粗,造成焊接质量缺陷。
C, 导向辊:按中心线高度将下辊孔型槽底调至略高与中心线。
作用:消皱,电流集中增大。
- 1、下载文档前请自行甄别文档内容的完整性,平台不提供额外的编辑、内容补充、找答案等附加服务。
- 2、"仅部分预览"的文档,不可在线预览部分如存在完整性等问题,可反馈申请退款(可完整预览的文档不适用该条件!)。
- 3、如文档侵犯您的权益,请联系客服反馈,我们会尽快为您处理(人工客服工作时间:9:00-18:30)。
一:换辊:
1,基准面距离:轴瓦一端有一固定端,此固定端有一基准面,或在牌坊架上,或在轴瓦上,以此确定轧制中心基准面与轧制中心的垂直距离。
2,为保证轧辊预装位置正确,必须保证各水平机架的基准面在同一平面内,不得松动。
3,水平下轴的水平高度各架应严格一致,以保证轧辊水平位置准确。
4,机架组装的注意事项。
A,开口机架下轴瓦注意方向,避免装反,上下轴不准装反。
B,各调整部位保证滑动,调整方便。
C,各紧固部件不得松动。
D, 检查轧辊尺寸和表面.检查各封闭孔导向环的尺寸和表面.
E, 轧辊安装固定要紧固,不允许有轴向串动和径向跳动,检查轴承是否损坏,松动.
二:换辊后的调整:
1, 校验轧制中心线:
A,以水平下辊为基准面校验轧制中心线是调整机组的原则。
B, 拉一中心细线通过成型第一架到定径最后一架,保持一定张力,并靠合孔型槽底,注意中心线不得与水平下辊外的任何部件接触。
C,各架水平下辊的孔型中心均与中心线位置相符。
D,各架水平下辊孔型槽底均与中心线靠合。
E,正确调整轧辊的水平位置.从横向检查成型机各架水平辊的上下辊轴的中心线是否水平,是否有一头高一头低的倾斜现象,通过压下装置调整水平.
F,正确调整各架的辊缝.按照孔型图和工艺规程调整各水平辊和立辊的辊缝,一般为带钢的厚度.辊缝过大则照成变形不充分,带钢在孔型内左右滑动和扭转,辊缝过小使成型负荷增加,机架损坏.
2, 立辊调整:
A, 与轧制中心对称。
B, 端面水平。
C, 成型2,3,4架立辊下沿高于轧制中心线。
D, 其他的按椭圆到圆应略底于轧制中心线。
3, 调整原则:
A, 立辊偏高:使变形带钢头部上翘,严重的造成跑头,还将使运行带钢在立辊间构成弓型,使孔型下部磨损增大,边缘刻伤带钢。
B, 立辊偏低:对变形带钢进入孔型不利,易跑头,并刻伤带钢边缘或出现横向墩粗,造成焊接质量缺陷。
C, 导向辊:按中心线高度将下辊孔型槽底调至略高与中心线。
作用:消皱,电流集中增大。
D, 八辊调整:将一段成品管插入八辊尽量使辊子对中,调整适当压力。
调整孔型位置,使钢管与轧制线平行,推动钢管可准确插入定径。
E, 挤压辊调整:
(1)出口管成扁圆状,即立面小于平面。
(2) 管缝在辊缝中,不得埋入孔型中。
(3)管筒边缘对接良好,不得错位。
(4)头部运行稳定,不准上下左右偏离转缝。
三,生产过程中的调整:
(一)错位和扭转
1,平辊
A,轧辊对中性良好,但上下辊平行度稍差,将造成轴间距小的带钢一侧压力稍大,使其向反方向偏转,应增加带钢偏转侧的压力。
(为正调法,调整量小)
B,上下轴平行度好,但轧辊对中性差,上辊偏向内侧,则带钢内侧压力大,使其向外侧偏转,应减少带钢偏转侧的牙力。
(为反调法,调整量大)
此故障在四五架出现较多,应首先检查上下轴的平行度!
C, 封闭孔各架上辊导向环的两侧片辊严重磨损或导向环损坏.
2,立辊
A, 归圆前立辊错动方向与钻缝方向一致。
B, 闭口立辊错动较大,将造成管缝一侧帖紧前架导环运行,使管筒反向转缝。
C, 立辊多方向错位将造成管缝不规则转缝,使管筒运行极不稳定。
D, 水平辊的磨损将造成轧制中心线的下降,使立辊相对增高,翘头,顶管入缝。
E, 规圆前立辊压力不够,管头入辊缝。
F, 各架两侧立辊不对称或有高低串动.
3,挤压辊
A,轻微错动,按管缝方向将导向辊反向旋转。
B,错动较大,因挤压辊中心错动使管筒边缘一侧紧贴导向片运行,此时将造成焊口的反向转缝,即错动方向与转缝方向相反。
C,采用挤压辊的扁孔型设计。
D,保持水平,不得出现仰角。
E, 适当保持挤压力。
4, 带钢有镰刀弯.
5, 如果带钢走得稍微不平稳,可用增大压下量的办法来消除.
(二)鼓包
1, 轧制底线是否合理,各架下辊底径是否合理,轧辊孔型设计是否合理
2, 调整时适当加大封闭孔前力辊组压力,适当加大封闭孔压下量,适当加大预成型开口孔的压下量.
3,鼓包起因是板材在成型过程中的边缘拉伸,调整的一般做法是把封闭孔逐渐上山消除。
(三)压痕和划伤
1, 轧辊有缺陷,轧辊碎裂,掉块或轧辊上粘住铁皮等杂物.
2, 管坯运动速度和轧辊圆周速度不相等,出现相对滑动.可拆除传动轴使轧辊自由转动.
3, 辊径不合理,轴承损坏,轧辊表面不光滑,辊环倒角不好.
四,操作对焊接质量的影响
A, 感应器
1,感应器与钢管的距离为3---5毫米.
2,多匝感应器应为二到四匝,用圆形或方形铜管缠成圆桶状,当中通水冷却.
3,单匝感应器的宽度: 焊1,5寸以下管时为管直径的1.5倍,
焊2—3寸管时,为管直径的1.2倍;
焊4寸以上时,与管直径相等.
多匝感应器的宽度: 参照单匝选取,比单匝稍窄即可.
4,放置位置: 感应器与管同心放置,其应尽量靠近挤压辊.为提高效率,可将感应器斜放与焊缝成一个角度.
B, 阻抗器(磁棒)
1,间隙:与管子的间隙为6—15毫米
2,长度: 焊1.5寸以下管时150—200毫米.
焊2—3寸管时250—300毫米.
焊四寸以上时350---400毫米.
3,放置位置: 其头部应与挤压辊中心线重合,尾部到感应器的中心距离应大于头部到感应器的中心长度.
4,为增加效率可在感应器的两侧加附加阻抗器.
C, 焊接制度
1,固相塑性压焊
这种方式是把管坯边缘加热到1300~1350摄氏度的高温,但还未达到溶化状态,由于挤压辊强大的压力,将边缘部分的氧化物薄膜挤出焊缝,在高温下固相在结晶,使两边缘焊在一起.这种方式要求挤压辊的挤压力较大,应不低于4~5公斤/毫米².其内毛刺高度小,但表面平整均匀.其特征是焊接时没有火花喷溅.
2,半熔化焊接
这种方式是把管坯边缘在交点处加热至半熔化状态,其焊接温度高于第一种固相塑性压焊,约为1350~1400摄氏度.借助于挤压辊的压力,便可容易的将带氧化物的液体金属挤出焊缝,并在半熔化状态下实现焊接.这种方式要求较小,约为2~3公斤/毫米².其内毛刺高度较小,但表面不太平整均匀.其特点是焊接时在交点处有轻微的火花喷溅.
3,熔化焊接
这种方式是把管坯边缘在通向交点的途中即被加热至熔化状态,,其焊接温度约在1400摄氏度以上.由于边缘金属熔化的早,在交点处(挤压辊中心)之前的位置,即发生边缘过梁,电流在此高度集中,使过梁处发生局部汽化,在挤压辊压力作用下,发生强烈的火花喷溅.其特征是焊接时在交点处之前有周期性的强烈的火花喷溅.这种方式的挤压力与第二种相似,但内毛刺和外毛刺都要大一些,成周期性的丘陵壮.
D, 开口角
1, 开口角增大:电流降低不明显,而焊接质量容易得到保证。
2, 开口角小:产生大颗粒闪光喷溅,热损失增大,溶渣不易排除,焊口产生缺陷。
3, 薄壁管时,开口角适当增大。
4, 厚壁管时,焊速是主要矛盾,开口角应适当减小。
5, 焊大管时,环路阻抗大,开口角应大些。
6, 焊小管时,开口角应小些。
7, 开口角通常为2—6度.
E, 焊接速度: 在焊管机组的机械设备和焊接装置所允许的最大速度下进行焊接较为合适. F, 管坯边缘形状: 边缘形状影响金属流动上升角,影响内外毛刺,影响整个焊接断面的焊接强度. 应为X行.其次为I行,。