微细电火花加工技术
精密及微细电火花加工(一)

() 2 高精度旋转主轴, 振摆小 , 动态精度高。最好
不用附加旋转轴型式 。转速为 0— 0 mn 1 0r i; 0 /
标电火花成 型机床 , 结合具体加工 对象 , 开展试验研
究, 取得了重要成果。本文 以研究报告为基础 , 结合近 几年国外在微精及微细 电火花加工 中的新成果 , 着重
内, 可以方便地用作 电极制作 、 修整 以及 多电极 的加
工。
损耗量即尽快地 制作 出成形 电极 , 通常 选用 T —R r c 即晶体管驰张式电路 。被加工 电极接正极 , 反拷块接 负极 。间隙并联 电容量按加工要求选定。若反拷加工
1 3 2 细 丝 电极法 . .
面积较大 , 如反拷加工电极端面时 , 可利用晶体管脉冲
子器件上的微孔 、 光阑等。 ‘
量对电加工性 能有很大影响。还应消除材料 的 内应
力, 以免加工后产生弯 曲。 12 精密微细孔的加工条件要求 .
为了探求精密及微 细孔 电火花加工的工艺特点 ,
北京机床研究所利用本所研制生产的 D 53 A型坐 G 42
() 1 机床工作台定位精度在 2I 以内; m x
计量 , 制造电极的尺寸控制具有一定特殊性。
1 1 电极 材料 .
近年来 , 瑞典 3 R公司和瑞士 E O R WA公司制作 出
紫铜电极价廉易得 , 用于孔径小 、 相同直径孔数少 且深度不大的工件 的加工 。铜 钨合金 电极用于加工 : 孔径更小、 要求更高的孔 ; 同直径孔数较多或深度大 相
1 电极
精密加工中, 了直径 0 1m 以下的微孔加工 除 . m
外, 一般都按照电火花加工 的常规 , 通过转换 加工规 准, 以达到所需的尺寸精度及表面粗糙度要求 。这时 , 中、 精规准加工时的加工余量很小 , 因而对各档加工电
微细电火花加工技术在组合加工中的应用
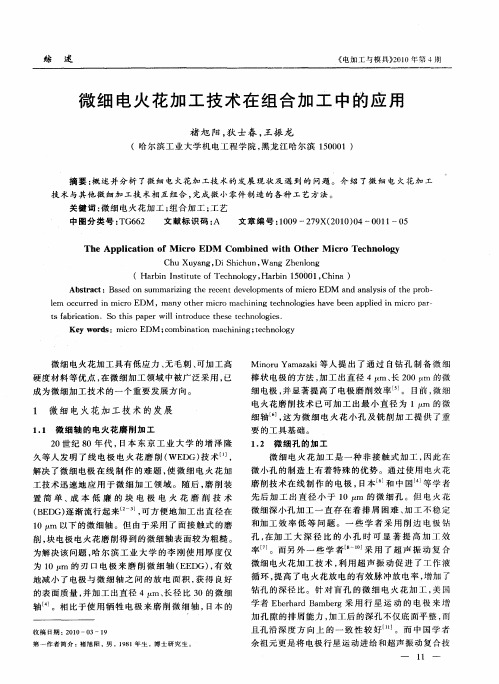
Th p i a i n o i r e A plc to fM c o EDM m b n d wih Ot e i r c n l g Co i e t h r M c o Te h o o y
Ch y n Di hc u W a g Z e ln u Xu a g, ih n, n h no g S
棒 状 电 极 的 方 法 , 工 出 直 径 4t 、 2 0 m 的 微 加 m 长 0 *
细 电极 , 并显 著提 高 了 电极磨 削效 率 。 目前 , 细 微
电火花磨 削 技术 已 可加 工 出最 小 直径 为 1 m 的微
1 微 细 电 火 花 加 工 技 术 的发 展
1 2 微 细 孔 的加 工 . 微 细 电火 花 加 工 是 一 种非 接 触式 加 工 , 因此 在 微 d 的制 造上 有 着特 殊 的优势 。通 过 使用 电火 花 qL 磨 削技 术在 线 制 作 的 电极 , 日本 和 中 国 等 学 者 先 后加 工 出 直 径 小 于 1 m 的 微 细 孔 。但 电 火 花 0 微细 深小 孔加 工 一 直 存 在 着 排 屑 困难 、 工 不 稳 定 加 和加 工 效 率 低 等 问 题 。 一 些 学 者 采 用 削 边 电 极 钻
微 细 电火花 加工 技 术 , 利用 超 声 振 动 促 进 了工 作 液
循 环 , 高 了 电火 花放 电 的有效 脉 冲放 电率 , 提 增加 了
钻孔 的 深径 比。针 对 盲 孔 的微 细 电火 花 加 工 , 国 美
轴 。相 比于使 用 牺 牲 电极 来 磨 削 微 细 轴 , 1 的 1本 7
综 述
《 电加工与模具》I0年第 4 21 ) 期
微 细 电火 花 加 工 技 术 在 组 合 加 工 中的 应 用
微细加工技术概述及其应用

2011 年春季学期研究生课程考核(读书报告、研究报告)考核科目:微细超精密机械加工技术原理及系统设计学生所在院(系):机电工程学院学生所在学科:机械设计及理论学生姓名:杨嘉学号:10S008214学生类别:学术型考核结果阅卷人微细加工技术概述及其应用摘要微细加工原指加工尺度约在微米级范围的加工方法,现代微细加工技术已经不仅仅局限于纯机械加工方面,电、磁、声等多种手段已经被广泛应用于微细加工,从微细加工的发展来看,美国和德国在世界处于领先的地位,日本发展最快,中国有很大差距。
本文从用电火花加工方法加工微凹坑和用微铣削方法加工微小零件两方面描述了微细加工技术的实际应用。
关键词:微细加工;电火花;微铣削1微细加工技术简介及国内外研究成果1.1微细加工技术的概念微细加工原指加工尺度约在微米级范围的加工方法。
在微机械研究领域中,从尺寸角度,微机械可分为1mm~10mm的微小机械,1μm~1mm的微机械,1nm~1μm的纳米机械,微细加工则是微米级精细加工、亚微米级微细加工、纳米级微细加工的通称。
广义上的微细加工,其方式十分丰富,几乎涉及现代特种加工、微型精密切削加工等多种方式,微机械制造过程又往往是多种加工方法的组合。
从基本加工类型看,微细加工可大致分为四类:分离加工——将材料的某一部分分离出去的加工方式,如分解、蒸发、溅射、切削、破碎等;接合加工——同种或不同材料的附和加工或相互结合加工方式,如蒸镀、淀积、生长等;变形加工——使材料形状发生改变的加工方式,如塑性变形加工、流体变形加工等;材料处理或改性和热处理或表面改性等。
微细加工技术曾广泛用于大规模集成电路的加工制作,正是借助于微细加工技术才使得众多的微电子器件及相关技术和产业蓬勃兴起。
目前,微细加工技术已逐渐被赋予更广泛的内容和更高的要求,已在特种新型器件、电子零件和电子装置、机械零件和装置、表面分析、材料改性等方面发挥日益重要的作用,特别是微机械研究和制作方面,微细加工技术已成为必不可少的基本环节。
微细电火花加工技术

微细电火花加工技术微细电火花加工技术是一种高精度加工方法,它通过利用电火花放电的瞬间高温和高压能量,将工件表面的金属材料溶解、熔化、蒸发和喷射等效应,实现对工件进行微细加工的一种技术。
微细电火花加工技术具有加工精度高、表面质量好、加工效率高等优点,在模具制造、航空航天、医疗器械等领域有着广泛的应用。
微细电火花加工技术的原理是利用电火花放电过程中产生的高温等效应来加工工件。
在微细电火花加工过程中,工件和电极通过一个电解液隔开,当施加足够的电压时,电极上会产生高频率的电火花放电。
电火花放电瞬间产生的高温和高压能量会使电解液中的金属离子快速聚集在工件表面,形成微小的气泡,同时气泡瞬间爆破产生的压力将工件表面的金属材料冲击下来。
通过不断重复这个过程,就可以实现对工件表面的微细加工。
微细电火花加工技术的加工精度非常高,可以达到亚微米级别。
这是因为在电火花放电过程中,由于高温和高压能量的局部聚集作用,使得工件表面的金属材料局部熔化和蒸发,从而实现微细加工。
此外,微细电火花加工技术还可以实现对工件表面的复杂形状、小孔和细槽等微细结构的加工,具有很高的灵活性。
微细电火花加工技术的应用非常广泛。
在模具制造领域,微细电火花加工技术可以用于制造高精度的模具零件,如模具芯、模具腔等。
在航空航天领域,微细电火花加工技术可以用于制造航空发动机的涡轮叶片、航天器的结构零件等。
在医疗器械领域,微细电火花加工技术可以用于制造高精度的医疗器械零件,如人工关节、牙科种植体等。
微细电火花加工技术虽然有很多优点,但也存在一些限制。
首先,由于加工过程中电火花放电会产生高温,工件表面容易产生热应力,从而导致表面质量下降。
其次,微细电火花加工技术只适用于导电材料的加工,对于非导电材料的加工效果不佳。
此外,微细电火花加工技术的加工效率相对较低,加工速度较慢。
微细电火花加工技术是一种高精度加工方法,具有广泛的应用前景。
随着科技的不断进步和发展,微细电火花加工技术将会进一步提高加工精度和效率,为各个领域的微细加工需求提供更好的解决方案。
微细电火花加工关键技术及工艺研究
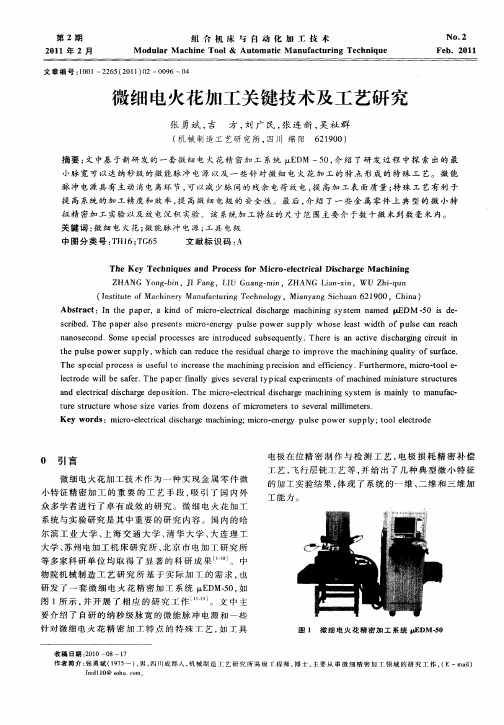
ZHANG Yo g bn,J a g,LI Gu n — i n —i IF n U a g r n,Z ANG a xn,W U Zh — u a H Lin— i iq n
( n tueo c iey Ma ua tr g T c n lg ,Min a gSc u n6 0 Isi t fMa hn r n fcui e h oo y t n a y n ih a 2 0,C ia 1 9 hn )
Absr c :I h pe ,a k n ir - lcrc ldic r e m a hnig s t m a e EDM 一 0 s e ta t n t e pa r i d ofm co ee tia s hag c i n ys e n m d o 5 i d - s rb d.Th pe lo prs nt co・n r y pule po r s p y wh e la tw it fpus a e c c ie e pa ras e e s mir e e g s we u pl os e s d h o le c n ra h n n s c n S m e s ca o e s s ae i to uc d s bs q e ty.Th r s ala tv ic agn ic i i a o e o d. o pe il pr c s e r n r d e u e u n l e e i l c ie ds h r ig cru t n t e p s w e u h ule po rs ppl whih c n r d et er sd lc ag o i pr v h c ii gq l y o u f c . y, c a e uc h e iua h r et m o e t e ma hn uai fs ra e n t Th pe il oc s sus f lt n r a et em a h n gpr cso n f ce y. rh r o e m ir -o le e s ca pr e si eu o ic e s h c i i e iin a d e n i inc Fu t em r , c o t o -
微细电火花加工设备技术研究
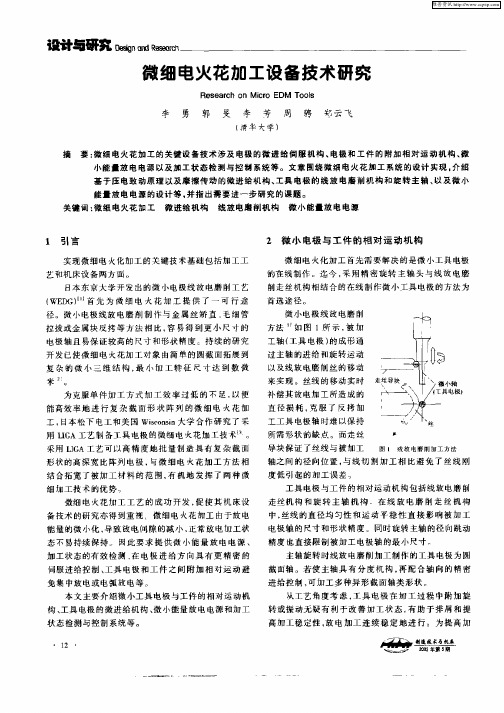
设计与研究
位移 分辨 率 的同时 实现 大位移 行程 的优 点 。其基 本结 构 和运动 原理 见 图 3所示 , 主要 构件 包括 主轴 、 向压 轴键设 备技 术涉及 电极 的 微进 给 伺服 机构 、 微 电极和 工 件 的 附加 相 对运 动机 构 、 微 小能 ■放 电电源 以及 加工状 态检 测与控 制 系统 等。 文章 围绕 微细 电火花 加 工系统 的设计 实现 . 介绍
基 于压 电致动原 理 以及摩 擦传 动 的微进 给机 构 、 具 电极 的 线放 电磨 削机 构 和旋 转 主 轴 、 工 以及 微 小
转 或振动无 疑有 利 于改 善 加 工 状 态 , 助于 排 屑 和提 有
高加 工稳定 性 , 电 加工 连续 稳 定 地 进 行。 为 提高 加 放
维普资讯
Di。 e d sn g
工 效 率 , 必要 进一 步开 发电极 丝连 续进 给补偿 机 构。 有 图 2为微 细 电极旋 转进 丝机构 原 理 示意 图 。由 进 给 活塞 、 常闭式 夹 丝机 构 、 开式 夹丝 机构 和导 向头 常 等构 成 , 机构 与穿 于 其 中 的 电极 丝 被 置 于 旋 转套 筒 该
电极 轴 的尺 寸和形 状精 度 。同时 旋转 主轴 的径 向跳动 精度 也直接 限制 被加工 电极 轴 的最小尺 寸 。 主轴旋 转时 线放 电磨 削加工 制作 的工具 电极 为圆
截面轴 。若 使主轴 具 有 分 度 机构 , 配台 轴 向的 精 密 再 进 给控 制 , 可加工 多种 异 形截面 轴类形 状 。 从工艺 角度考 虑 , 具 电极 在 加 工 过程 中附加 旋 工
能量 放 电电源 的设计 等 , 并指 出需要 进 一步研 究 的课题 。 关键词 : 微细 电火花加 工 微进 绐机构 线 放 电磨削机 构 微小 能■ 放 电电源
超声辅助等离子体中微细电火花加工技术研究
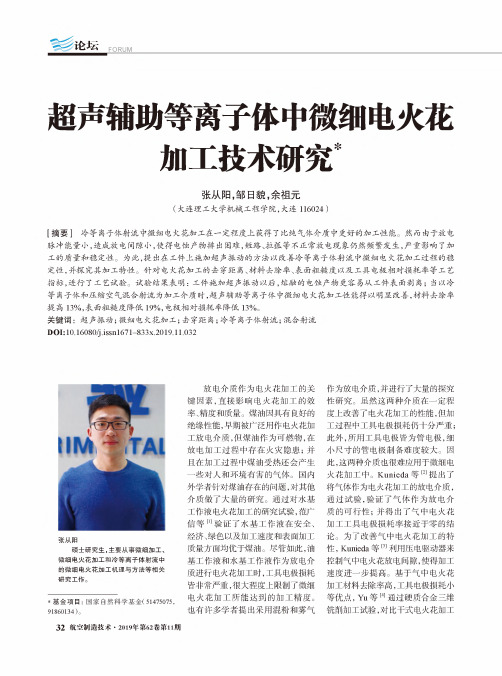
工特性发现,氮气等离子体加压缩空 气射流中微细电火花加工的质量更 好。有研究结果表明:等离子体射流 中微细电火花加工和气中微细电火 花加工相比,前者的放电间隙更大,
性能。因此,为改善等离子射流中微 细电火花加工存在的不足,本文提出 了采用超声振动辅助等离子体中微细 电火花加工的新方法,并通过工艺试 验对该方法的加工特性进行了研究。
试验及方法
1试验装置
试验采用自主研制的超声振动 辅助等离子体中微细电火花加工机
床,如图1和2所示,分别为试验
装置示意图和实物图。该机床主要 由机床主体部分、伺服运动平
论坛FORUM
超声辅助等离子体中微细电火花
加工技术研究
张从阳,邹日貌,余祖元
(大连理工大学机械工程学院,大连116024)
[摘要]冷等离子体射流中微细电火花加工在一定程度上获得了比纯气体介质中更好的加工性能。然而由于放电 脉冲能量小,造成放电间隙小,使得电蚀产物排出困难,短路、拉弧等不正常放电现象仍然频繁发生,严重影响了加 工的质量和稳定性。为此,提出在工件上施加超声振动的方法以改善冷等离子体射流中微细电火花加工过程的稳 定性,并探究其加工特性。针对电火花加工的击穿距离、材料去除率、表面粗糙度以及工具电极相对损耗率等工艺 指标,进行了工艺试验。试验结果表明:工件施加超声振动以后,熔融的电蚀产物更容易从工件表面剥离;当以冷 等离子体和压缩空气混合射流为加工介质时,超声辅助等离子体中微细电火花加工性能得以明显改善,材料去除率
提高13%,表面粗糙度降低19%,电极相对损耗率降低13%。
微细电火花加工的底面轮廓模型及定长补偿方法
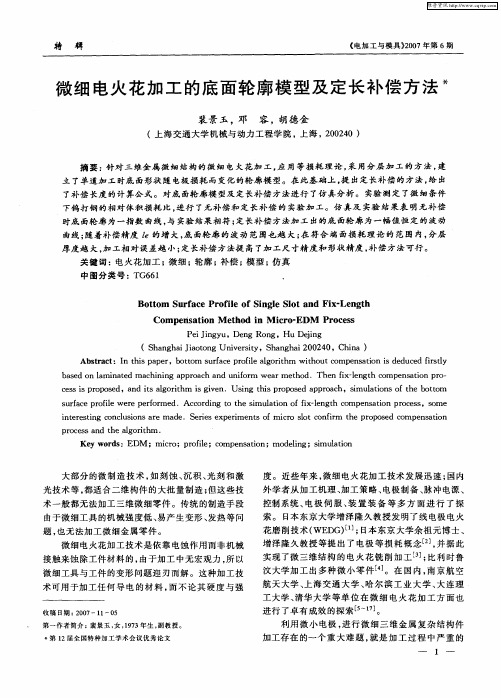
摘要 : 对 三维金 属微 细 结构 的微 细 电 火花加 工 , 用等 损耗 理论 , 用 分层 加 工 的方 法 , 针 应 采 建 立 了单道 加工 时底 面形状 随 电极损 耗 而 变化 的轮 廓模 型 。在此 基础 上 , 出定长补 偿 的方 法 , 出 提 给 了补 偿 长度 的计算公 式 。对 底 面轮 廓模 型及 定 长补偿 方 法进行 了仿 真分 析 。 实验 测 定 了微 细条 件 下钨 打钢 的相 对体 积损耗 比 , 进行 了无补偿和 定 长补 偿 的 实验 加 工 。仿 真及 实验 结 果表 明无 补偿 时底 面轮 廓为 一指数 曲线 , 实验 结果 相符 ; 长补偿 方 法加 工 出的底 面轮 廓 为一 幅值 恒定 的 波动 与 定 曲线 ; 着补偿精 度 的增 大 , 面轮 廓 的 波动 范 围也越 大 ; 符 合 端 面损 耗 理 论 的 范 围 内 , 层 随 底 在 分
花磨 削技 术 ( D … ; WE G) 日本 东 京大 学余 祖元博 士 、
增泽 隆久 教授 等 提 出 了 电极 等 损 耗 概 念[ 并据 此 , 实现 了微 三维 结构 的 电火 花 铣 削 加 工 ; 比利 时鲁
接 触来蚀 除 工件材 料 的 , 由于加 工 中无宏 观力 , 以 所
s ra e p o i r e o m e u fc r fl we ep r r d.Ac o d n o t e smu a i n o i - n t o e s t n p o e s o e f c r ig t h i l t f f l g h c mp n a i r c s ,s me o x e o i t r s ig c n l s n r d .S r s e p r e t fmir l tc n i h r p s d c mp n t n n e e t o cu i s a e ma e e i x e i n s o c o s o f n o e m o m r t ep o oe o e s i a o p o e sa d t e ag rt . r c n h l o ihm s
- 1、下载文档前请自行甄别文档内容的完整性,平台不提供额外的编辑、内容补充、找答案等附加服务。
- 2、"仅部分预览"的文档,不可在线预览部分如存在完整性等问题,可反馈申请退款(可完整预览的文档不适用该条件!)。
- 3、如文档侵犯您的权益,请联系客服反馈,我们会尽快为您处理(人工客服工作时间:9:00-18:30)。
微细电火花加工技术
微细电火花加工技术的简要及背景
随着世界范围产品日益的小型化和精密化,作为非接触式精微制造方法之一的微细及小孔电火花加工技术以其超精细和高精度的加工特点倍受学术界和工业界关注,目前已经成为微机械制造领域的重要组成部分之一,在制造业中得以广泛应用。
电火花加工是利用浸在工作液中的两极间脉冲放电时产生的电蚀作用,蚀除导电材料的特种加工方法,又称放电加工或电蚀加工。
主要用于加工具有复杂形状的型孔和型腔的模具和零件;加工各种硬、脆材料,如硬质合金和淬火钢等;加工深细孔、异形孔、深槽、窄缝和切割薄片等;加工各种成形刀具、样板和螺纹环规等工具和量具。
20世纪50年代初期,我国开始研究和试制电火花镀敷设备,即把硬质合金用电火花工艺镀敷在高速钢金属切削刀具和冷冲模刃口上,提高金属切削刀具和模具的使用寿命。
同时我国还成功研制了电火花穿孔机,并广泛应用于柴油机喷嘴小孔的加工。
60年代初,上海科学院电工研究所成功研制了我国第一台靠模仿形电火花线切割机床。
随后又出现了具有我国特色的冷冲模工艺,即直接采用凸模打凹模的方法,使凸凹模配合的均匀性得到了保证,大大简化了工艺过程。
60年代末,上海电表厂张维良工程师在阳极切割的基础上发明了我国独有的高速走丝线切割机床。
上海复旦大学研制出电火花线切割数控系统。
70年代随着电火花工艺装备的不断进步,电火花型腔模具成型加工工艺已经成熟。
线切割工艺也从加工小型冷冲模发展到可以加工中型和较大型模具。
切割厚度不断增加,加工精度也不断提高。
80年代以来计算机技术飞速发展,电火花加工也引进了数控技术和电脑编程技术,数控系统的普及,使人们从繁重、琐碎的编程工作中解放出来,极大的提高了效率。
目前计算机技术广泛应用于工业领域,电火花加工实现了数控化和无人化。
美国、日本的一些电火花加工设备生产公司依靠其精密机械制造的雄厚实力,通过两轴、三轴和多轴数控系统、自动工具交换系统及采用多方向伺服的平动、摇动方案,解决了电火花加工技术中一系列实质性的问题。
随着具有高精度、高刚度、高自动化、高加工表面粗糙度的机床不断出现,使加工的功能及范围不断扩大。
如今,在国际上,电火花加工可以加工大至数十吨重的模具和零件,小至只有几微米的微孔。
微细电火花加工技术的原理
电火花加工基于电火花腐蚀原理,是在工具电极与工件电极相互靠近时,极间形成脉冲性火花放电,在电火花通道中产生瞬时高温,使局部金属融化,甚至汽化,从而将金属蚀除下来。
(1)极间介质的电离、击穿,形成放电通道
放电通道是有大量带正电和负电的粒子以及中型粒子组成,带电粒子高速运动,相互碰撞,产生大量热能,使通道温度升高,通道中心温度可达到10000摄氏度以上。
由于放电开始阶段通道截面很小,而通道内有高温热膨胀形成的压力高达几万帕,高温高压的放电通道急速扩展,产生一个强烈的冲击波向四周传播。
在放电的同时还伴随着光效应和声效应,这就形成了肉眼所能看到的电火花。
(2)电极材料的融化,汽化热膨胀
液体介质被电离、击穿,形成放电通道后,通道间带负电的粒子奔向正极,带正电的粒子奔向负极,粒子间相互撞击,产生大量的热能,使通道瞬间达到很高的温度。
通道高温首先使工作液汽化,进而气化,然后高温向四周扩散,使两电极表面的金属材料开始融化直至沸腾气化。
气化后的工作液和金属蒸汽瞬间体积猛增,形成了爆炸的特性。
所以在观察电火花加工时,可以看到工件与工具电极间有冒烟现象并听到轻微的爆炸声。
(3)电极材料的抛出
正负电极间产生的电火花现象,使放电通道产生高温高压。
通道中心的压力最高,工作液和金属汽化后不断向外膨胀,形成内外瞬间压力差,高压力处的熔融金属液体和蒸汽被排挤,抛出放电通道,大部分被抛入到工作液中。
加工中看到的桔红色火花就是被抛出的高温金属熔滴和碎屑。
(4)极间介质的消电离
在电火花放电加工过程中产生的电蚀产物如果来不及排除和扩散,那么产生的热量将不能及时传出,使该处介质局部过热,局部过热的工作液高温分解,结碳,使加工无法进行,并烧坏电极。
因此为了保证电火花加工过程的正常进行,在两次放电之间必须有足够的时间间隔让电蚀产物充分排除,恢复放电通道的绝缘性,使工作液介质消电离实际上,电火花加工的过程远比上述复杂,它是电力、磁力、热力、流体动力、电化学和胶体化学等综合作用的过程。
到目前为止,
人们对电火花加工过程的了解还有限,需要进一步研究。
微细电火花加工技术的应用
1.陶瓷
为查明放电能量的有效性,对拥有优越绝缘性材料的机械零件化曾经是一个重要的课题。
这是一项与陶瓷相关技术研制发端。
作为材料的陶瓷,价格低,到手较为容易,除了绝缘性能之外,陶瓷的特点可以举出的是,拥有重量轻、刚度高、耐磨损性以及热环境状态下的稳定性优异。
达到如此优越程度的材料没有被积极当作机械零件来使用的原因是,一般的常识认为韧性较低的缘故。
所谓“热压件”的陶瓷确实拥有裂纹的缺点,但通过充分观察、分析、验证其加工过程有可能作为机械零件来使用不会有什么问题。
在沙迪克公司电火花机床的实际生产中除了外部因素之外,陶瓷发生裂纹的机率为零。
实际上,把该陶瓷作为机械零件材料,对发挥直线电机驱动的优越性却变成了一种重要的技术基础,也就是陶瓷本身的特点能最大限度的发挥出作为直线电机驱动优越性的高速、高加速、高响应的特性,同时,为了获得高精度特性在实施有成效的热对策方面带来了有效的成果。
2.直线电机驱动
旋转电机被分类成板极的直线电机驱动是一种直接驱动,无需所谓传递动力的进给丝杠,所以没有进给丝杠引起的间隙、爬行、扭曲和滞后等影响,从而确立了极为平滑的运动特性,能使优异的响应性产生高精度的轴驱动。
由于采用高精度、高分辨率的直线光栅作为位置检测装置,恰好是在控制着自身的驱动。
所以能成为在连续的时间轴上进行高精度位置
控制。
对于电火花加工而言,高响应需要的伺服特性是支配加工性能的一个重要的因素,直线电机驱动的确是一种理想的执行元件。
使用传统的进给丝杠,通过高精度的控制技术,并非不能实现一定程度的定位精度,但在纳米这种非常微小的领域中为保证优异的加工性能则需要在极高频率条件下的控制特性。
因此,在进给丝杠摩擦状态中,除了磨损产生的时效变化问题之外,不能保持初期性能的这一缺点也是难以回避的。
如果从一般的不利印象来看,还存在若干有关生产率、热效率和怀疑受磁力影响的声音。
然而,沙迪克公司的直线电机是由自行研制的,所以对其基本性能进行了完整无缺的验证,并将每种机床所配置的控制特性皆确立了最优条件。
所以,这类担心的事项一概不成问题,技术开发已全部完成。
实际上,在确立停止、开动、停止这种不连续的简单动作中的安全性等方面,把不损害性能的性价比达到极限的机械构成品当作具体的事项也是重要的课题。
除性能之外,应解决的众多课题皆被克服掉了,沙迪克公司已集聚了独家的技术窍门。
微细电火花加工技术在将来的应用前景
未来数控电火花加工技术的发展空间是十分广阔的。
由于电火花加工过程本身的复杂性,迄今对电火花加工的机理尚未完全弄清楚,大多研究成果是建立在大量系统的工艺实验基础上完成的,所以对电火花加工机理的深入研究,并以此直接指导和应用于实践加工是数控电火花加工技术发展的根本。
在现有技术水平的基础上,不断开发新工艺将是数控电火花加工技术发展方向。
如数控电火花铣削加工是一种还不成熟的技术,值得继续研究的新工艺。
数控电火花机床在结构设计、脉冲电源的开发方面将朝更合理、更具优势化的方向全面发展,提高加工性能,同时考虑降低机床制造的成本。
数控电火花加工在控制技术上将朝自动化、智能化方面的更高层次发展,数控电火花加工的网络管理技术在高档机床上已有
应用,将逐步推广及应用,获取更好的系统管理效果。
总之数控电火花技术以提高加工质量、提高加工效率、扩大加工范围、降低加工成本等为目标在模具工业中不断发展。
在模具工业技术快速发展的新形势下,数控电火花加工技术已取得了突破性的进展,其不仅在过去及和现在的模具制造中被广泛应用,相信在今后的模具加工中其也必将发挥重要作用。
量、提高加工效率、扩大加工范围、降低加工成本等为目标在模具工业中不断发展。