(槽控机操作知识课件)铝电解智能控制系统培训_16671215
铝电解预焙槽生产管理与控制PPT课件

6 0.66 976 0.009 0.009 0.002 0.38 0.041 5.50 4.30
第一部分:业翔浓度控制原理介绍 第二部分:沉淀的形成与溶解原理 第三部分:电流效率的主要影响因素
1
影响浓度控制的主要因素
1. 电压和电流信号不稳定使控制信号失真; 2.过热度、温度和分子比变化造成电阻曲线漂移; 3.异常操作的影响,如换极、出铝、抬母线、阳极效应, 堵料、冒料、槽外添加氟化铝、手动下料、频繁升降 阳极等造成物料和热平衡大幅度波动操作; 4.当过热度升高时,炉底沉淀或炉帮的溶化进入电解质, 增加了氧化铝的实际投入量,使氧化铝浓度升高,当 过热度偏低时,炉底沉淀或炉帮的形成使氧化铝沉入 炉底,减少了氧化铝的实际投入量,降低氧化铝浓度 而诱发效应;
3 0.72 971 0.011 0.009 0.002 0.38 0.041 8.00 4.20
0.9 52 75
4 0.76 980 0.011 0.009 0.003 0.39 0.039 6.00 4.50
1.00 82 73
批号 5
0.67 976 0.01 0.009 0.002 0.038 0.038 3.60 6.00
8
其亚铝业142#槽历史曲线
9
南平铝业240KA系列电解槽日报表
10
第二部分:沉淀的形成与溶解原理
邱竹贤先生的研究认为氧化铝在冰晶石中的溶解过程可 以分为两步:第一步是Al2O3晶体受F离子侵蚀而生成Al2O3 溶质,第二步是Al2O3溶质在溶剂作用下生成铝氧氟络合离 子。在低Al2O3浓度条件下主要生成Al2OF62-离子,在高 Al2O3浓度条件下主要生成Al2O2F42-离子。我们笼统地认 为Al2O3在冰晶石中的溶解度和溶解速率主要取决于冰晶石 中游离F离子的数量和活度,取决于冰晶石熔体中AlF63-离 子的离解度。熔体中凡是占用游离F离子的因素都会降低电 解质对氧化铝的溶解度,凡是降低F离子活度的因素都必将 降低电解质对氧化铝的溶解速率,而凡是提高电解质中F离 子浓度和活度的因素虽然提高了电解质对氧化铝的溶解能力 ,但必然同时提高电解质熔体对阴极铝的溶解损失,因此努 力降低铝液和氧化铝在电解质体系的溶解度并保持平稳生产 是我们铝电解工艺和控制的重要内容。
铝电解槽控机操作使用说明

铝电解槽智能模糊控制系统槽控机操作使用说明1 内部结构简介每一台槽控机由左右两个部分组成,右半部分叫做逻辑部分,是槽控机的核心部分,左半部分叫做动力部分,是槽控箱的供电部分和控制阳极升降的执行单元。
左右两边都有一些连线和电解槽的其它设备相连。
1.槽控机的动力电源(三相、其相电压为380V):该电源的作用提供电解槽上提升电机的动力380V电源,该电源由专用的供电回路提供。
2.槽控机的动力电源(单相、电压交流220V):该电源的作用是用于控制打壳下料电磁阀的线包用电,各种接触器动作线包用电等。
3.槽控机逻辑电源(单相、电压交流220V):该电源经过槽控机的开关电源变换后,提供给槽控机的逻辑单元用电。
4.提升电机动力电源线(三相、相电压为380V):该动力线由槽控机输出,连接到电解槽上的提升电机,当需要进行阳极升降时,经过槽控机的空气开关,主接触器,正转接触器或反转接触器(统称为辅助接触器)将槽控机的动力电源接通,使提升电机正转或反转,带动电解槽上的提升机构达到阳极升降的目的。
5.打壳下料电磁阀连接线(单相、电压为交流220V):该动力线由槽控机输出,连接到电解槽的打壳下料电磁阀的动作线包上,当需要进行打壳下料动作时,经过槽控机固态继电器和槽控机的动力电源接通,使打壳下料电磁阀得电动作,达到向电解槽内补充氧化铝的作用。
6.槽控机避雷接地线(目前未接):该线通过电解厂房的接地母线直接和大地连接,每个槽控机都和这条线相连,该线连接到槽控机的避雷装置的地线上。
该线的作用是使槽控机防雷电袭击和抗电干扰,保证槽控机正常工作,但也是造成槽控机产生相对直流电位差比较高,使维修人员易直流触电的原因,因此,该接地线有利有弊。
7.槽电压采样线:为了控制电解槽,槽控机每0.5秒要对被控电解槽的槽电压进行一次采样,槽电压采样线是槽控机与电解槽直流大母线的连接线。
进入槽控机的槽电压采样线一方面连到槽控机的槽电压表上,进行槽电压瞬时值显示,另一方面经过熔断器连接到槽控机上的V/F转换板上,进行电压频率转换,实现对槽电压的采样。
铝电解槽控制系统
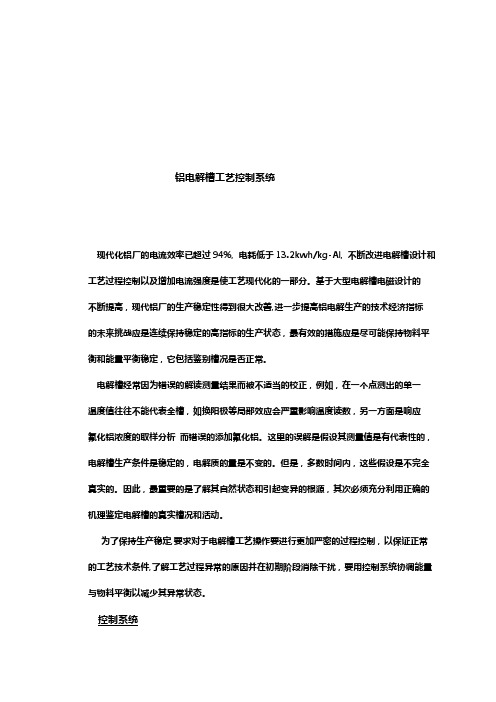
铝电解槽工艺控制系统现代化铝厂的电流效率已超过94%, 电耗低于13.2kwh/kg-Al, 不断改进电解槽设计和工艺过程控制以及增加电流强度是使工艺现代化的一部分。
基于大型电解槽电磁设计的不断提高,现代铝厂的生产稳定性得到很大改善,进一步提高铝电解生产的技术经济指标的未来挑战应是连续保持稳定的高指标的生产状态,最有效的措施应是尽可能保持物料平衡和能量平衡稳定,它包括鉴别槽况是否正常。
电解槽经常因为错误的解读测量结果而被不适当的校正,例如,在一个点测出的单一温度值往往不能代表全槽,如换阳极等局部效应会严重影响温度读数,另一方面是响应氟化铝浓度的取样分析而错误的添加氟化铝。
这里的误解是假设其测量值是有代表性的,电解槽生产条件是稳定的,电解质的量是不变的。
但是,多数时间内,这些假设是不完全真实的。
因此,最重要的是了解其自然状态和引起变异的根源,其次必须充分利用正确的机理鉴定电解槽的真实槽况和活动。
为了保持生产稳定,要求对于电解槽工艺操作要进行更加严密的过程控制,以保证正常的工艺技术条件,了解工艺过程异常的原因并在初期阶段消除干扰,要用控制系统协调能量与物料平衡以减少其异常状态。
控制系统当前铝厂的控制系统主要是氧化铝浓度控制,控制策略是控制氧化铝浓度保持在一定范围内,控制办法是按加料量分成3个加料期,正常加料期,减量加料期和增量加料期。
电解槽上部结构上带有定容加料器,它是一个容积一定的容器,在氧化铝堆积比重一定的条件下重量一定,加料量多少由定容器开放的间隔时间来决定.正常加料期的定容加料时间根据额定电流和预定的电流效率计算的氧化铝消耗量确定,减量加料期延长定容加料的间隔时间,意味着降低电解质中的氧化铝浓度,增量加料期缩短加料间隔时间,意味着降低电解质中氧化铝浓度,控制系统所根据的信号也是以生产条件稳定为基础。
氧化铝在电解质中的溶解度是电解质总量,电解质温度,电解质化学成分,氧化铝的物理性能等的函数,在这些条件一定时,氧化铝的溶解度就是它的饱和浓度,任一条件的改变都会引起氧化铝溶解度的变化。
(槽控机操作知识课件)铝电解智能控制系统培训_16671215
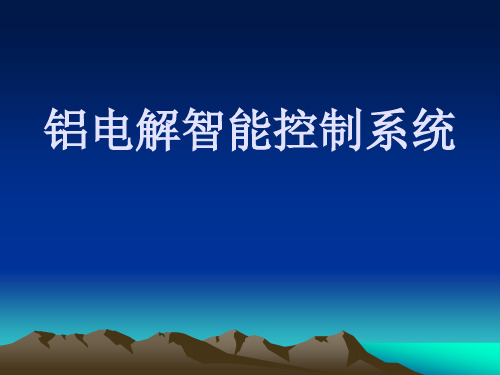
尽早建立(过渡期内形成) 高分子比( CR≥ 2.9,结永久性坚硬炉帮) 降CR同时 1、降过热度
2、降AE系数 3、降电压 4、保温 5、降温度
四、铝电解工艺技术条件的选择
稳定是铝电解生产的第一要务,铝电解生产中的 主要干扰因素 1、效应(5分钟,25V,温度升高30℃)
2、大计量投料(加料前后温降2℃) ,产生 沉淀
2、 有利于提高电解质与阳极的界面张力,降低阳极 气体表面积,加速气体逸出,从而提高电流效率。
四、铝电解工艺技术条件的选择
铝水平的保持
高铝水作用主要有以下几个方面: 1、高铝水能增大水平电流与铝液表面的距离和缩小水平电流 的夹角,减弱水平电流产生的电磁力,减小铝液变形,提高铝 液的安定性,从而降低极距和电压。
二、槽控机下料控制基本原理
激励—反馈机制
3.
低浓度槽:
二、槽控机下料控制基本原理
状态转换依据:斜率、累斜
高浓度槽
二、槽控机下料控制基本原理
•槽稳定性判据:
• 针振:高频波动信号,产生原因集中在阳极底部。 • 摆动:低频波动信号,产生原因在槽膛不规整。 • 槽控机处理措施:附加电压。
•特殊作业处理: • 物料平衡:停料,有新的观点。
• 显示和管理各种生产数据,为电解生产管理提供依据。 • 控制系统不是万能的。原因:铝电解是一个复杂的、缺乏精
确模型和解析算法的控制系统,而且不是闭环控制,因此需 要人机配合才能充分发挥他的作用。铝电解控制系统的输入: 电压及系列电流;输出:下料间隔(氧化铝浓度)及阳极动 作(设定电压)。
二、槽控机下料控制基本原理
8.分子比调整必须坚持快升慢降的原则,要在实践中逐步掌握分子 比变化与温度变化滞后的时间差,分析变化趋势;
电解槽控制系统讲义共16页
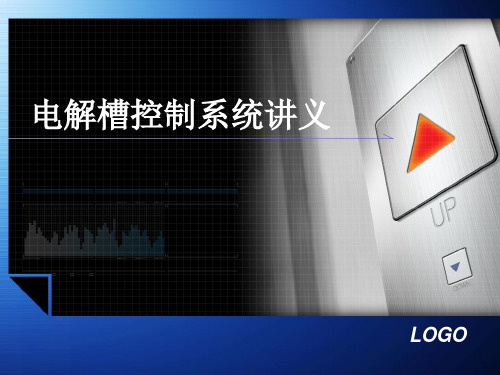
规则库说明
采用“if<条件>then<结论>”(条件和结论都可含
模糊子句)的模糊产生式表示法来统一地表达由推 理机使用的各种规则。为了简化推理机的构造, 我们仅采用简单规则和“AND”类型的复合规则来 表达全部规则,这是因为其他类型的规则均可以 拆分为这两种类型的规则。“AND”类型的复合规 则的表达形式如下:
紧急停电开关检查
当按紧急停电开关时,脱扣线圈跳起,起到断开380V电 源的作用,说明功能正常。
themegallery LOGO
槽控系统保护
缺相保护检查
当槽控机进行阳极升降时,三相保护器进行检查,起到缺相 保护功能。
自诊断
(1)软件自诊断功能:每8个时,槽控机便可以进行一次自诊断检 查,如果没有故障,说明槽控机正常,若有故障显示故障编号。 (2)人工自诊断:将CPU板上JP1的1与2短接且CPU板上K3的第8 位设为OFF时,CPU通电或CPU通电情况按一下复位时,便自动 运行位于27C512中的调试软件进行自检。
信号分配器的说明
系列电流的模/数转换(A/D转换)及系列电流数字量的分配
将整流所送来的系列电流模拟量信号经1#VFC模块转换为0--10Khz
的脉冲信号,并将此脉冲信号送上位主机各通讯板;同时对此脉冲 进行分别隔离后送各区的槽控机。
输入模拟量信号可以为电流信号(4--20MA或0--20MA)也可为电
themegallery LOGO
SV INPUT SPD
SV INPUT
VP 2#VFC
1#VFC
IP
VP
PC104
VP
IP SIP
TO COMMUNICATION CARD
铝电解教程.ppt
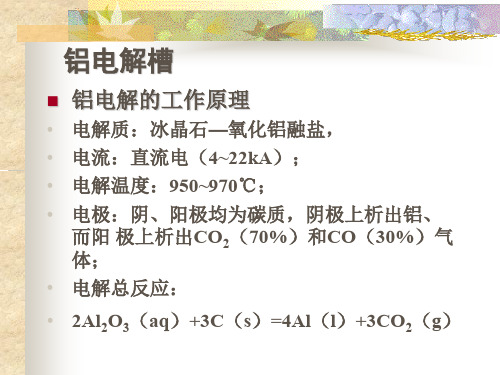
• 电解槽排布方式:
• 横向排列 l 纵向排列
单行排列 双行排列
铝电解槽配置图
铝电解槽的母线配置
图4-2-8
未来铝电解槽的改进
•
目前的铝电解槽尚存在一些问题:生产过程能量
利用率较低,电流效率不太理想,单位产品的投资费
用较高,控制污染的设备费用也很贵。
• 4.2.4.1 原有电解槽的改造
•
原有电解槽的改造包括阴极材料、阳极材料及槽
⑷炭阳极对阳极糊的要求
阳极糊要求有一定的塑性(或流动性),以便 填满拔棒后留下的孔洞;但流动时不能引起焦 粒偏析,孔洞不能被富含沥青的糊所填充,以 免此处焦化后孔隙率过高;
流动性与糊中沥青配比、沥青的软化点、阳极 上部温度等因素有关。
阳极糊的质量主要取决于固定炭粒的粒度组成, 沥青配比由粒度组成确定。
化作用,基本上同旁插棒槽。在焦化过程
中,也形成了烧结锥体。阳极棒通过上层
的液体糊,一直插到阳层的
阳极糊来充填,结果生成所谓“二次阳
极”。这对于阳极的质量有一定的影响。
自焙阳极上插棒式电解槽简图
图4-2-5
(3) 连续预焙阳极电解槽
相对于非连续式有如下特点: • 优点: 无阳极残极,预焙炭块消耗量小; 阳极电流分布均匀,故阳极消耗均匀; 生产的连续性。 • 缺点: 阳极不能用氧化铝保温,热损失大; 炭块之间接缝存在接触电压降,故槽电
铝电解工业初期的小型预焙电解槽; 20世纪20~40年代,相继采用旁插棒式 自焙阳极和上插棒式自焙阳极; 50年代后大型预焙阳极。
铝电解槽的发展从19世纪末至今已经有了一百多 年的历史。
ã 初期:电流强度为4~8kA的小型预焙阳极电 解槽,产铝量为20~40kg/d;电能消耗为 42kW·h。
铝电解计算机智能控制技术—讲座
• 自动连续的高速运算功能
微型计算机的发展
• 1946年首次提出原理:“存储程序”原理 并诞生第一台电子计算机。 • 1971年在美国Intel公司诞生第一台微型计算机 • 1971~1973年 为第一阶段 • 1973~1975年 为第二阶段
• 1975~1978年 为第三阶段
• 1978~1981年 为第四阶段
智能控制理论与技术的发展趋势
目前的发展趋势是,综合运用多种智能控制
理论与技术,构成集成型智能控制。
计算机控制系统的发展
• 集中式控制系统
• 集-散式控制系统(分布式控制系统)
• 全分布式控制系统(网络型控制系统、现
场总线型控制系统)
管理信息系统
MIS局域网
过程监控级
(上位机)
1#工控微机 通信线
M#工控微机
直接控制级 (槽控机)
1号 槽控机
2号 槽控机
n号
槽控机
铝 电 解 计 算 机 控 制 系 统 配 置 示 意 图
1号电解槽
2号电解槽
n号电解槽
局域网(MIS)
工控微机
工控微机
键盘输入
网络接口 通 通 迅 接 口
键盘输入
槽况诊断 子 系 统
组织与监视 子 系 统 通讯接口
迅 接 口
在线仿真 子 系 统
计算机智能控制技术
中南大学 李劼
计算机结构原理
数据 数据
输入设备 输出设备
数据
运算器
存储器
控制信号
控制器
指令
微型计算机系统基本构成
微型计算机
微 型 计 算 硬件 电 源
辅助电路
输入/输出外围设备 系统软件 软件 应用软件
《铝电解技师培训》课件
铝电解设备的维护与保养
设备维护保养的重要性
阐述铝电解设备维护保养对生产效率和设备寿命的影响。
日常维护保养
介绍日常维护保养的要点,如清洁、检查、紧固等。
定期维护保养
讲解定期维护保养的步骤和注意事项,如更换易损件、检查设备性 能等。
04
CATALOGUE
铝电解生产中的安全与环保
铝电解生产中的安全风险与防范措施
铝电解生产中的事故应急处理
应急处理原则
及时报告、迅速响应、科学救援、减少损失。
应急处理措施
启动应急预案、组织救援队伍、调配救援资源、开展现场救援等。
05
CATALOGUE
铝电解技师培训计划与实施
铝电解技师培训的目标与内容
目标
培养具备铝电解技术知识和实践能力的技师,提高其在铝电解行业的技能水平和 工作能力。
02
CATALOGUE
铝电解技师的职责与要求
铝电解技师的岗位职责
操作和维护铝电解设备
监控生产过程
铝电解技师需要熟练掌握铝电解设备的操 作和维护,确保设备正常运行,提高设备 的使用寿命和稳定性。
铝电解技师需要密切监控生产过程,及时 发现并解决生产过程中的问题,确保生产 安全、高效地进行。
优化生产工艺
安全风险
高温、高压、腐蚀、触电、机械伤害 等。
防范措施
穿戴个人防护用品、定期检查设备维 护、严格执行安全操作规程、加强员 工安全培训等。
铝电解生产中的环保要求与处理方法
环保要求
减少污染物的排放、降低能耗和资源消耗、提高资源利用效 率等。
处理方法
采用环保设备和技术、加强废水废气治理、合理利用废弃物 资源等。
THANKS
感谢观看
槽控系统培训
槽控系统培训电解厂电解车间职工技能培训电解槽计算机控制铝电解计算机控制作用及意义:1、减轻了电解工的劳动强度,提高了劳动生产率。
2、自动把各种技术参数控制在设定的理想范围内,使电解槽在最佳条件下运行,大大的提高了生产经济指标。
3、使管理者及时掌握槽子的运行情况,及时作出正确的分析、判断,调整槽子的运行参数。
铝电解槽计算机控制的基本原理:利用测量到的槽电压和系列电流,采用控制槽内电阻保持平衡的数学模型,自动按设定周期投入氧化铝,以控制电解槽的物料平衡,自动调整极距,以控制电解槽的热平衡。
铝电解计算机控制系统的构成:我公司200KA、90KA、宝川90KA 都采用中南大学业翔公司的铝电解智能模糊控制系统。
控制系统采用“槽控机——上位机——管理机”三级全分布式控制,采用CAN通信协议和以太网TCP/IP通信协议构成网络体系,形成管控一体化系统。
每一台电解槽配备一台槽控机作为直接控制级,槽控机具有独立进行槽电压和系列电流采样的能力,并对槽子的物料平衡和热平衡的快速变化过程实时进行控制。
微机站的上位机作为过程监控级,通过CAN通信网络与槽控机相连,对槽控机的运行过程监视并完成生产管理功能。
各工控机和管理机,通过交换机连接。
各级管理人员通过管理机可观察电解槽的曲线,了解槽子的运行。
槽控机的功能:1、控制槽电压槽控机采集到的槽电压是跟随系列电流的波动而时刻变动的。
因此,采集到的电压作为调整槽电压的根据毫无意义,而且电流低落时,将出现大量的提升阳极,使系列电压过高,过高的电压又使电流低落,从而出现恶性循环。
因此,槽电压的控制以不受电流波动影响的槽电阻为依据。
R=(U-E)/ I槽控机采集到电流、电压以后,首先进行解析,算出槽电阻值,然后分成效应电阻、异常电阻、正常电阻。
对于正常电阻,槽控机自动控制。
当电阻异常、发生效应、电流异常时,不进行槽电阻控制,只发出报警信息,通知人工处理。
由设定电压加上附加电压,求出目标电压。
槽控机操作控制内容_苏源
铝电解控制系统操作说明中铝国际贵阳分公司1目录一.槽控机显示面板及操作面板 (4)1.1显示面板示意 (4)1.2数码显示管布局及常规显示 (5)1.2.1数码显示布局: (5)1.2.2数码管常规显示 (6)1.3操作面板布局示意 (6)1.4参数显示 (6)二.槽控机故障显示说明 (7)1号故障(提升机主电源信号应有效时却无效) (7)2号故障(提升机主电源信号应无效时却有效) (7)3号故障(提升机动作信号应有效时却无效): (7)4号故障(提升机动作信号应无效时却有效): (7)5号故障(无阳极脉冲或阳极脉冲太少): (8)6号故障(提升机动作输入信号无效后仍有阳极脉冲): (8)7号故障(控制电源无效): (8)8号故障(交流定时器超时保护动作): (8)9号故障(直流定时器失效或时间太长): (8)10号故障(直流定时器超时动作后不能切断提升机主电源): (8)11号故障(直流定时器超时信号不能复位): (8)12号故障(直流定时器超时复位后提升机主电源信号无效): (8)13号故障(行程装置与阳极实际动作方向相反): (9)14号故障(直流定时器超时保护动作): (8)15号故障(阳极升降按钮粘连):........................................................... 错误!未定义书签。
16号故障(电流通道故障):.. (9)17号故障(掉电保护故障): (9)18号故障(电压通道故障): (9)三、电解槽工艺管理与控制 (9)3.1电解槽状态与槽控机设定命令 (9)3.1.1非正常期 (9)3.1.2正常期: (10)23.2 效应管理模式 (10)3.3工艺控制 (11)3.3.1、电流异常 (11)3.3.2、电压异常 (11)3.3.3、自动电压控制(RC) (12)3.3.4、电压波动(SHK): (13)3.3.5、效应检测及处理 (14)3.3.6、出铝控制 (15)3.3.7、换极 (16)3.3.8、扎边部 (17)3.3.9、抬母线 (17)四、槽控机操作: (20)4.1、正常加工(NB) (20)4.2、效应加工(AEB) (20)4.3、升阳极(AU) (20)4.4、降阳极(AD) (20)4.5、更换阳极(AC) (21)4.6、出铝(TAP) (21)4.7、抬母线(ABR) (21)4.8、边部加工(SB) (21)4.9、效应预报加工(AEPB) (22)4.10、氟化盐加工ALF (22)五、特征曲线分析: (23)5.1曲线变化有规律 (23)5.2炉帮形成不好 (24)5.3换极后电压出现波动,调极后恢复正常 (25)5.4效应后出现长时间的欠加工 (25)5.5出铝后噪声增大 (27)5.6短时间内按多次出铝键(出铝操作不当) (28)5.7出铝后噪声降低 (28)5.8效应前噪声大,效应后噪声降低,恢复正常 (29)5.9连续多次发生效应 (29)5.10电解质水平低效应多发 (30)5.11效应后出现低电压 (31)5.12过欠加工时,电压变化大,时常出现电压尖峰。
- 1、下载文档前请自行甄别文档内容的完整性,平台不提供额外的编辑、内容补充、找答案等附加服务。
- 2、"仅部分预览"的文档,不可在线预览部分如存在完整性等问题,可反馈申请退款(可完整预览的文档不适用该条件!)。
- 3、如文档侵犯您的权益,请联系客服反馈,我们会尽快为您处理(人工客服工作时间:9:00-18:30)。
4、分子比、电流与电压调整过程
四、铝电解工艺技术条件的选择
保持下料点火眼畅通的必要性
1、下料点的火眼有利于加强局部的热交换能力,提 高下料点的电解质流速,有利于氧化铝的预热和溶解。
2、下料点的火眼能使氧化铝在电解质表面铺展和 分散,扩大氧化铝在电解质中接触界面,扩大了热交换界 面,甚至以单个颗粒溶解,从而提高了氧化铝的溶解速率 并减弱了冷料对电解质过热度的影响。
一、铝电解控制系统结构与用途
数据为中心的新型上位机监控系统——铝电解企业控制信息私有云的实现
新型监控系统采用 以服务为中心的企 业分布式架构;提 供历史数据的两级 分布式备份机制; 将整个与铝电解控 制相关的信息组织 成企业控制信息私 有云。
一、铝电解控制系统结构与用途 — 控制系统作用
• 控制铝电解生产的下料及阳极动作,保持氧化铝浓度和设定 电压的稳定。
1.“U”型曲线: 任何控制系统都需要存在输入和输出间的对应关系。
注意高、中、低三个浓度区 的氧化铝浓度的变化规律: • 低浓度区:氧化铝浓度增 加,槽电阻下降;氧化铝浓 度减低,电阻上升; • 中浓度区:氧化铝浓度不 管怎么变化,槽电阻没有明 显的变化; • 高浓度区:氧化铝浓度增 加,槽电阻上升;氧化铝浓 度降低,电阻下降。
动力单元
采集板
多CPU网络型槽控机逻辑单元的基本构成
一、铝电解控制系统结构与用途
以现场总线互联 采用多个微控制器协同工作方式
操作模块
主模块
采集板
采样模块
外部 CAN 总线
槽电压 系列电流
采样模块 内部 CAN 总线 操作模块
主模块
触摸开关
动作信号
手动信号
动力单元
采集板
全分布式(网络式)智能槽控机 逻辑单元的基本构成
2、 有利于提高电解质与阳极的界面张力,降低阳极 气体表面积,加速气体逸出,从而提高电流效率。
四、铝电解工艺技术条件的选择
铝水平的保持
高铝水作用主要有以下几个方面: 1、高铝水能增大水平电流与铝液表面的距离和缩小水平电流 的夹角,减弱水平电流产生的电磁力,减小铝液变形,提高铝 液的安定性,从而降低极距和电压。
铝电解智能控制系统
一、铝电解控制系统结构与用途
槽控机硬件体系升级——强化运算功能
外部 CAN 总线(至上位机)
槽电压 系列电流
采样模块
内部 CAN 总线
主模块
操作模块
触摸开关
槽控机为3-CPU网络体系结构,内含三 个智能模块,CPU升级强化运算功能, 主板CPU采用Arm9系列处理器。
动作信号
手动信号
4、减少火眼不畅通时的每次打壳下料量,弥补低过 热度电解质对氧化铝溶解能力的不足。
四、铝电解工艺技术条件的选择
低氧化铝浓度的主要作用是:
1、有利于氧化铝和炉底沉淀的溶解 主要是提高铝氧氟离子的扩散动力,提高氧化铝
的溶解速率,从而有利于溶解炉底沉淀而保持炉底洁 净,有利于降低炉底水平电流改善槽内磁场和铝液运 动,为电解生产连续进行提供一个稳定的工作环境。 由于低分子比和低过热度工艺都降低电解质的氧化铝 饱和浓度,因此,低氧化铝浓度显得格外重要。
2、 高铝水有利于加强边部散热,降低电解质过热度,促进炉 帮和伸腿的发育。
• 怎样建立炉膛:
尽早建立(过渡期内形成) 高分子比( CR≥ 2.9,结永久性坚硬炉帮) 降CR同时 1、降过热度
2、降AE系数 3、降电压 4、保温 5、降温度
四、铝电解工艺技术条件的选择
稳定是铝电解生产的第一要务,铝电解生产中的 主要干扰因素 1、效应(5分钟,25V,温度升高30℃)
2、大计量投料(加料前后温降2℃) ,产生 沉淀
• 显示和管理各种生产数据,为电解生产管理提供依据。 • 控制系统不是万能的。原因:铝电解是一个复杂的、缺乏精
确模型和解析算法的控制系统,而且不是闭环控制,因此需 要人机配合才能充分发挥他的作用。铝电解控制系统的输入: 电压及系列电流;输出:下料间隔(氧化铝浓度)及阳极动 作(设定电压)。
二、槽控机下料控制基本原理
控制的特色是:充分利用电 解槽运行在“临界状态”附近时 阳极气膜电阻对物料平衡、热平 衡及极距的变化十分敏感这一特 点,设计出新一代功能强大的
“槽电阻噪声分析器”
(用软件实现)。
四、铝电解工艺技术条件的选择
• 炉膛作用:
• 绝缘保护层,延长槽寿命 • 减少水平电流分量,稳定槽况 • 改善热平衡自调能力 • 提高电流效率
二、槽控机下料控制基本原理
激励—反馈机制
3.
低浓度槽:
二、槽控机下料控制基本原理
状态转换依据:斜率、累斜
高浓度槽
二、槽控机下料控制基本原理
•槽稳定性判据:
• 针振:高频波动信号,产生原因集中在阳极底部。 • 摆动:低频波动信号,产生原因在槽膛不规整。 • 槽控机处理措施:附加电压。
•特殊作业处理: • 物料平衡:停料,有新的观点。
3、有利于碳渣从火眼喷出,保持电解质洁净。
四、铝电解工艺技术条件的选择
怎样在低过热度条件下保持下料点火眼畅通
1、要保证打击头的直径。
2、还要设计科学的打壳深度,合理的打壳深度应该 是距离铝液表面8~10cm,使氧化铝直接进入快速 流动的电解质内,提高其扩散能力,
3、增加打壳次数,破碎电解质表面结壳并加强搅拌,
• 能量平衡:附加电压。
三、槽控机阳极控制基本原理
三、槽控机阳极控制基本原理
阳极调整的整体思路:
• 计算机是趋势调整,比人工瞬时调整要好,尽量不要人工干 预。 • 电压过高时,“过量处理”优先。 • 电压过低时,判断标准适当放宽,尽量走“低端”。 • 阳极调整过多影响效率,特别是“压极距”; • 阳极调整主要是考虑几个保护,效应期间禁止自动阳移,更 换程序半小时内禁止阳移,电流和电压越限禁止阳移,出铝 期间禁止阳升,电压快速攀升不超过100MV则暂时不降,欠
量和过量周期初期适当提高控制上限30MV。。
四、铝电解工艺技术条件的选择
➢ 低电压:3.85~3.95V(数据仅供参考,依槽型和原料等条件不同而调整,下同)
➢ 低电解温度:930~940℃ ➢ 低过热度:8~10 ℃
“五低三窄一高”
➢ 低氧化铝浓度:1.8~2.5%
➢ 低阳极效应系数:≤0.02 ➢ 窄物料平衡工作区 ➢ 窄热平衡工作区 ➢ 窄磁流体稳定性调节区 ➢ 高电流密度:0.80A/cm2