直齿轮、斜齿轮、圆锥齿轮、蜗杆蜗轮计算
齿轮计算公式大全
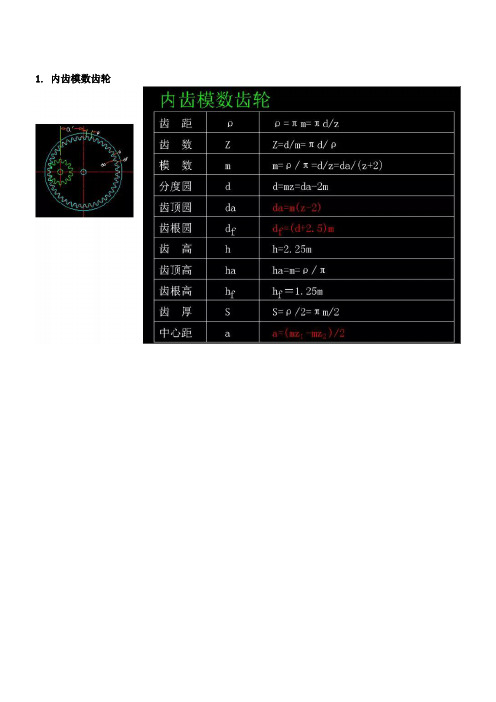
1. 内齿模数齿轮5. 变位模数齿轮8. 齿条节圆柱上的螺旋角:基圆柱上的螺旋角:齿厚中心车角:销子直径:中心距离增加系数:标准正齿轮的计算(小齿轮①,大齿轮②)1.齿轮齿标准2.工齿齿形直齿3.模数 m4.压力角5.齿数6.有效齿深7.全齿深8.齿顶隙9.基础节圆直径10.外径11.齿底直径12.基础圆直径13.周节14.法线节距15.圆弧齿厚16.弦齿厚17.齿轮油标尺齿高18.跨齿数19.跨齿厚20.销子直径21.圆柱测量尺寸(偶数齿)(奇数齿)其中,22.齿隙标准螺旋齿的计算公式(齿直角方式)(小齿轮①,大齿轮②)1.齿轮齿形标准2.齿形基准断面齿直角3.工具齿形螺旋齿4. 模数5.压力角6.齿数 Z17.螺旋角方向β0(左或右)8.有效齿深9.全齿深10.正面压力角11.中心距离12.基准节圆直径13.外径14.齿底圆直径15.基圆直径16.基圆上的螺旋角17.导程18.周节(齿直角)19.法线节距(齿直角)20.圆弧齿厚(齿直角)21.相当正齿轮齿数22.弦齿厚23.齿轮游标尺齿深24.跨齿数25.跨齿厚26.梢子直径其中,27.圆柱测量尺寸(偶数齿)(奇数齿)28.齿隙移位正齿轮计算公式(小齿轮①,大齿轮②)1.齿轮齿形转位2.工具齿形直齿3.模数m4.压力角5.齿数Z6.有效齿深7.全齿深或8.齿隙 C9.转位系数10.中心距离11.基准节圆直径12.啮合压力角13.啮合节圆直径14.外径15.齿顶圆直径16.基圆直径17.周节18.法线节距19.圆弧齿厚20.弦齿厚21.齿轮游标尺齿高22.跨齿数23.跨齿厚24.梢子直径25.圆柱测量尺寸(偶数齿)(奇数齿)移位螺旋齿的计算公式(齿直角方式)(小齿轮①,大齿轮②)1.齿轮齿形移位2.齿形基准断面齿直角3.工具齿形螺旋齿4.模数(齿直角)5.压力角(齿直角)6.齿数Z17.螺旋方向β08.有效齿深9.全齿深10.移位系数11.中心距离12.正面模数13.正面压力角14.相当正齿轮齿数15.齿直角啮齿压力角16.基准节圆直径17.外径18.啮齿节圆直径19.基圆直径20.基础圆柱上的螺旋角21.圆弧齿厚22.弦齿厚23.齿轮游标尺齿高24.跨齿数25.跨齿厚26.销子直径27.圆柱测量尺寸(偶数齿)(偶数齿)注:齿隙f=m 1.25以下 0.025-0.075m 1.25-2.5 0.05-0.10蜗轮、蜗杆的计算公式:1、传动比=蜗轮齿数÷蜗杆头数2、中心距=(蜗轮节径+蜗杆节径)÷23、蜗轮吼径=(齿数+2)×模数4、蜗轮节径=模数×齿数5、蜗杆节径=蜗杆外径-2×模数6、蜗杆导程=π×模数×头数7、螺旋角(导程角)tgB=(模数×头数)÷蜗杆节径。
蜗轮蜗杆计算

2、根据齿面形状不同分为:
普通蜗杆传动
圆弧圆柱蜗杆传动
3、阿基米德蜗杆
在轴剖面:直线齿廓 法剖面:凸曲线 垂直轴剖面:阿基米德螺线 车削加工,不能磨削,精度低。
蜗轮滚刀:与蜗杆尺寸相同 在中间平面上可看成直齿齿条与渐开线齿轮啮合
9.2 普通圆柱蜗杆传动的主要参数和几何尺寸计算
中间平面上的参数作为设计基准
单位时间由箱体外壁散发到空气中的热量为
H 2 K s A(t t0 )
W
式中 Ks—散热系数 A—散热面积 t—达到平衡时,箱体内的 油温,t在800以内 t0—周围空气温度, t0=200
根据热平衡条件H1=H2可求得既定工作条件下 的油温
t
t0
1000 P1 (1 )
Ks A
C
在既定工作条件下,保持正常油温所需要的 散热面积
一、蜗杆传动的特点和应用
1、特点:
单级传动比大; 结构紧凑; 传动平稳,无噪音; 可自锁; 传动效率低; 成本高。
2、应用:
机床:数控工作台、分度 汽车:转向器 冶金:材料运输 矿山:开采设备 起重运输:提升设备、电梯、 自动扶梯
二、蜗杆传动的类型
1、按蜗杆形状分
圆柱蜗杆传动
环面蜗杆传动 锥蜗杆传动
A 1000 P1 (1 )
K s (t t0 )
m2
一般应使t在80℃以下
若t>80℃或有效的散热面积不足时,则必须
采取措施,以提高其散热能力
常用措施: 1 、合理设计箱体结构,铸 出或焊上散热片,以增大散 热面积
2 、在蜗轮轴上装置风扇, 进行人工通风,以提高散 热系数
3 、在箱体油池内装 设蛇形冷却水管
[ ]H —蜗轮材料的许用接触应力,MPa
过程装备基础 第11章 齿轮传动与蜗杆传动

rb2 ’
ra2
2 OO 2 2
24
啮合线
点击图标播放
25
11.5
斜齿圆柱齿轮传动
11.5.1 斜齿圆柱齿轮的形成及其传动特点
(1)齿廓曲面的形成 基圆柱上的螺旋角: b 分度圆柱上的螺旋角:
发生面 K K A 发生面 发生面 K
渐开线 ?端面齿形
b
K
A
B
A B
A
直齿轮齿廓曲面的形成
40
(5)齿面塑性变形
原因:用软钢或其它较软的材料制造的齿轮在重 载下工作。 条件:低速、起动频繁和瞬时过载。 现象:渐开线形状被破坏,瞬时传动比不恒定。 措施:提高齿面硬度,采用油性好的润滑油。
41
11.6.2 齿轮材料及热处理 (1)齿轮材料
45号钢 中碳合金钢 金属材料 低碳合金钢 最常用,经济、货源充足 40Cr、40MnB、35SiMn等 20Cr、20CrMnTi等
* 齿根圆直径 d f d 2hf ( z 2ha 2c* )m
基圆直径 db d cos mzcos
p m 齿距 齿厚与槽宽 s e m / 2
基圆齿厚
pb db / z mzcos / z m cos p cos
43
(3)按齿面硬度分类
软齿面( HBS≤350)齿轮:
主要失效形式:齿面点蚀。 应用:多用于中、低速传动。 热处理:调质或正火处理,热处理后再进行轮齿的精切。
硬齿面( HBS>350)齿轮:
主要失效形式:齿根弯曲疲劳折断。 应用:高速、中载、无猛烈冲击的重要齿轮。
热处理:中碳钢经表面淬火处理或用低碳钢经表面渗碳淬火处理。
机械设计基础第七章齿轮传动
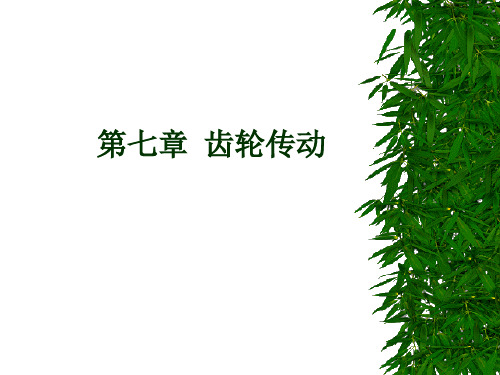
§7-7 直齿圆锥齿轮传动的强度计
算 方向: Ft——主反从同
Fr——指向各自的轴线
一、直F齿a—圆—锥指齿向轮大传端 动的受力分析
Fr1 Fa2
Fa1 Fr 2
Ft1=-Ft2
二、强度计算
1、齿面接触强度的计算 2、齿根弯曲强度的计算
P120
§7-8 蜗杆传动强度计算
一、蜗杆传动的失效形式、设计准则及常用材料
2T1 d1
Fa2
பைடு நூலகம்Ft 2
2T2 d2
Fa1
Fr1 Fr2 Ft2tg
力的方向和蜗轮转向的判别
蜗轮转向的判别 : Fa1的反向即为蜗轮的角速度w2方向
圆周力
Ft——主反从 同
径向力
Fr——指向各自 的轴线
轴向力 Fa1——蜗杆左右
手螺旋定则
三、蜗杆传动强度计算
1、蜗轮齿面接触强度的计算 2、蜗轮齿根弯曲强度的计算
(2)铸钢 用于尺寸较大齿轮,需正火和退火以消除 铸造应力。 强度稍低 。
2、铸铁 脆、机械强度,抗冲击和耐磨性较差, 但抗胶合和点蚀能力较强,用于工作平 稳、低速和小功率场合。
常用铸铁:灰铸铁;球墨铸铁(有较好
的机械性能和耐磨性 )
3、非金属材料——工程塑料(ABS、尼 龙)、夹布胶木
适于高速、轻载和精度不高的传动中, 特点是噪音较低,无需润滑;
四、蜗杆传动热平衡计算
1、原因 效率低,发热大,温升高,润滑油粘度 下降润滑油在齿面间被稀释,加剧磨损 和胶合。
2、冷却措施 加散热片以增大散热面积;风扇;
冷却水管;循环油冷却
§7-9 齿轮、蜗杆和蜗轮的构造 一、结构
1、齿轮轴 2、实体式 3、辐板式(孔板式) 4、轮辐式 5、镶圈齿轮
《机械设计手册》之蜗杆锥齿轮

αx1 = αt2 = α β1 + β 2 = 90° (γ1 = β 2 ) 旋向相同 °
结束
§ 10-8 蜗杆传动
四、主要参数和几何尺寸 (一) 主要参数
1、 齿数 、 蜗杆齿数 z1 亦称为头数 一般 z1=1 ~ 10 要求自锁时,取z1=1 z1 → γ1 2、 模数 m 、 推荐 z1=1、2、4、6
R=
d mz = 2 sin δ 2 sin δ
结束
§ 10 - 9 圆锥齿轮传动
三、几何参数和尺寸计算
1、几何尺寸 、 大端的参数为标准值,计算大端的尺寸
d = mz
d a = d + 2 ha cos δ
d f = d − 2 h f cos δ
δ f = δ −θ f
⇐ tan θ f = h f / R
6. 成本 → 蜗轮材料贵重
结束
§ 10-8 蜗杆传动
一、蜗杆传动的类型介绍 圆柱蜗杆 蜗杆的形状 环面蜗杆 圆锥蜗杆
圆柱蜗杆— 设计、制造简单
常用
环面蜗杆、圆锥蜗杆— 啮合性能好,承载能力、效率高, 但设计、制造复杂
少用
结束
§ 10-8 蜗杆传动
一、蜗杆传动的类型介绍
按照蜗杆齿廓形状不同
阿基米德蜗杆 蜗杆 渐开线蜗杆 圆弧齿蜗杆
m m a = r1 + r2 = (q + z 2 ) ≠ ( z1 + z 2 ) 2 2
结束
§ 10-8 蜗杆传动
五、蜗杆传动的运动学参数
1. 传动比 啮合传动 2. 转向的判定
i=
ω1 n1 z 2 d 2 = = ≠ ω 2 n2 z1 d1
P
v 2 = v 1 + v 21
直齿轮、斜齿轮、圆锥齿轮、蜗杆蜗轮计算
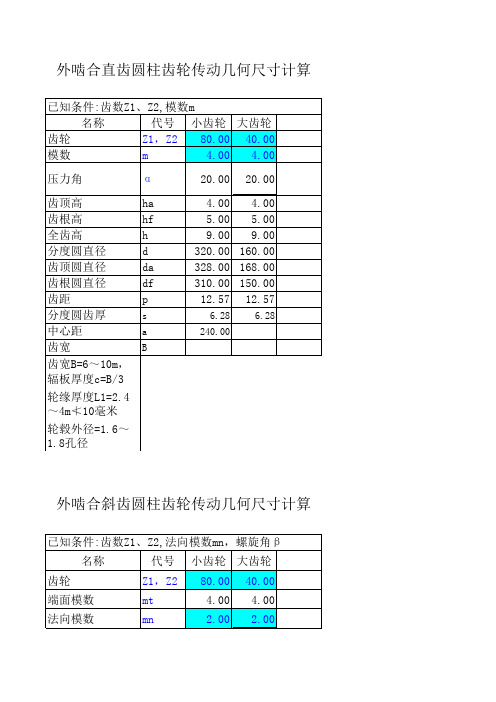
Sz1=0.45πMdu Sf1=Sz1cosλ h~=Mdu Z2=iZ1 Dfe2=MduZ2 Dje2=Dfe2=MduZ2 Dg2=Mdu(Z2-2.4) Ddi2=Mdu(Z2+2)
Dw2=Ddi2+Mdu(根据注:及时改)
b=0.65Ddi1 R1=0.5Dfe1-Mdu R1=0.5Ddi1+1.2Mdu
注:蜗杆特性系数q 为 14,13,12,11,10,9, 8
注:☆蜗杆螺纹长度 L:当Z=1~2时取大于 (11+0.06Z2)Mdu, 当Z=3~4时取大于 (12.5+0.09Z2)Mdu
注:蜗杆在分度圆 上的轴向齿厚 =1.498m,分度圆上 的法向齿厚 =1.498mcosλ
切制螺纹部分长度L
A
模数
Mdu
轴截面齿形角
α
传动比
i
变位系数 径向间隙
蜗
杆
蜗 轮
ξ
c
头数
Z1
特性系数
q
齿顶高
hdi
齿根高
hg
分度圆直径
Dfe1
节圆直径
Dje1
齿顶圆直径
Ddi1
齿根圆直径
Dg1
分度圆螺旋导角(弧度)
λ
法向模数
mf
螺旋长度
L☆
轴截面齿距
P
螺旋导程
PZ
螺牙沿分度圆柱上的轴向齿厚 Sz1 螺牙沿分度圆柱上的法向齿厚 Sf1
备注
ξ=(A/Mdu)-0.5(q+z2) C=0.25Mdu Z1=1,2,4 q=Dfe1/Mdu hdi=Mdu hg=1.2Mdu Dfe1=qMdu Dje1=Dfe1+2Mduξ=Mdu(q+2ξ) Ddi1=Mdu(q+2) Dg1=Mdu(q-2.4) λ=arctgZ1/q mf=Mducosλ L=(12+0.1z2)Mdu L=(13+0.1z2)Mdu P=πMdu
《齿轮传动设计》PPT课件

三、渐开线齿轮的啮合特性
渐开线齿轮符合齿廓啮合基本定 律,即能保证定传动比传动 由齿廓啮合基本定律知
i12
1 2
O2P O1P
❖ 由渐开线性质知,
❖ 啮合点公法线与二基圆内公切
线重合
N2
❖ 二基圆为定圆,N1N2为定直线, 则节点P为定点
i12 12
O2Pr2'rb2 O1P r1' rb1
co
n. st
机械设计基础 ——齿轮传动
例题2
❖已知:一渐开线直齿圆柱齿轮,用卡尺测量出齿顶圆直径 da=208mm, 齿根圆直径df=172mm, 数得齿数z=24.
❖求:该齿轮的模数m,齿顶高系数ha*和顶隙系数c*
解:
da(z2ha *)m208 mm
df(z2h a *2c*)m 17m 2 m
m 8 mm
O1
1 rb1
P K’
N1 K
C1
C2
2 rb2
O2
机械设计基础 ——齿轮传动
三、渐开线齿轮的啮合特性
机械设计基础 ——齿轮传动
5-4 渐开线标准齿轮的基本尺寸
一、外齿轮 二、内齿轮 三、齿条
机械设计基础 ——齿轮传动
一、外齿轮
1 各部分名称和符号 2 基本参数 3 几何尺寸 4 例题
机械设计基础 ——齿轮传动
h
* a
1
c
*
0 .25
正常齿: 短齿:
m 1mm h a *1,c*0.25 m 1mm h a *1,c*0.35
ha*0.8,c*0.3
机械设计基础 ——齿轮传动
例题3
❖已知: 法向距离〔即公法线长度〕分别为 :W3 = 61.84mm,
齿轮传动设计计算实例(114)

解:
cos
mn 2a
z1
z2
4 30 60
2 190
0.9474
所以
1840
tan t
tan n cos
tan 20 cos1840
0.3640 0.9474
0.3842
d1
mn cos
z1
4 30 0.9474
mm 126.662mm
F2
2KT1 bm 2 z 2
YFa2YSa2
F1
YFa 2 YSa 2 YFa1YSa1
82.76 2.2881.734 MPa 2.52 1.625
80.18MPa< F 2
故轮齿齿根弯曲疲劳强度足够。
(4)计算齿根传动的中心距 a
a
m 2
z1
z2
2 2
db2 d 2 cos t 253.325 0.9335mm 236.479mm
例 3 试设计带式运输机减速器的高速级圆柱齿轮传动。已知输入功率 P 40kW ,小齿轮转速 n1 970r / min ,传动比 i 2.5 ,使用寿命为 10a(年)(设每年工作 300d(天)),单班制,电动机驱动,
(3)校核齿面接触疲劳强度
由式(8.45)
H 3.17Z E
KT u 1
bd 12 u
H
确定有关参数和系数:
1)分度圆直径
d1
mn z1 cos
3 24 cos1415
mm 74.29mm
- 1、下载文档前请自行甄别文档内容的完整性,平台不提供额外的编辑、内容补充、找答案等附加服务。
- 2、"仅部分预览"的文档,不可在线预览部分如存在完整性等问题,可反馈申请退款(可完整预览的文档不适用该条件!)。
- 3、如文档侵犯您的权益,请联系客服反馈,我们会尽快为您处理(人工客服工作时间:9:00-18:30)。
外啮合直齿圆柱齿轮传动几何尺寸计算
外啮合斜齿圆柱齿轮传动几何尺寸计算
压力角α20.0020.00
齿顶高ha 2.00 2.00
齿根高hf 2.50 2.50
全齿高h 4.50 4.50
分度圆直径d320.00160.00
齿顶圆直径da324.00164.00
齿根圆直径df315.00155.00
分度圆齿厚s 6.28 6.28
中心距a240.00
齿宽
计算m n=(da-df)/4.5
计算螺旋角cosβ =m n z/(da-2mn)
注
注:☆蜗杆齿宽:当
注:☆最大外圆直
注:☆蜗轮齿宽:当
注:模数为12,10
注:蜗杆特性系数
注:☆蜗杆螺纹长
注
外啮合直齿锥齿轮传动几何尺
齿顶高h di 齿根高hg 分度圆直径
D fe1节圆直径D je1齿顶圆直径D di1齿根圆直径
D g1分度圆螺旋导角(弧度)λ法向模数m f 轴截面齿距P 螺旋导程
P Z 螺牙沿分度圆柱上的轴向齿厚S z1螺牙沿分度圆柱上的法向齿厚S f1齿厚测量高度h~齿数Z 2分度圆直径
D fe2节圆直径D je2齿根圆直径D g2齿顶圆直径D di2最大外圆直径Dw 2轮缘宽度b 齿顶圆弧半径R 1齿根圆弧半径
R 2
注:☆磨削蜗杆需加长:Mdu≤10时,加长25MM;10≤Mdu≤16时,加长35M 注:☆蜗杆齿宽:当Z=1~2时取(13~16)Mdu, 当Z=3~4时取(15~21)Mdu
注:☆最大外圆直径:当Z=1取≤Ddi2+2Mdu,当Z=2~3取≤Ddi2+1.5Mdu,当Z=4取≤Ddi2+Mdu 注:☆蜗轮齿宽:当Z≤3时取≤0.75Ddi1, 当Z=4时取≤0.67Ddi1,包角2θ=45°~130°注:模数为12,10,8,6,5,4,3,2.5,2,1.5,1注:蜗杆特性系数q为14,13,12,11,10,9,8
注:☆蜗杆螺纹长度L:当Z=1~2时取大于(11+0.06Z2)Mdu, 当Z=3~4时取大于(12.5+0.09Z2)
蜗 轮
蜗 杆
螺旋长度L☆齿根圆弧半
注:蜗杆在分度圆上的轴向齿厚=1.498m,分度圆上的法向齿厚=1.498λ
轴向齿形
h 齿顶高h 齿根高轴向齿距 3:1
a
压力角齿根圆弧半
d 齿顶圆直径d 齿根圆直径d 分度圆直径2
1
f 1
a 1
P x
a 1
f 1
(a )蜗杆
(b
几何尺寸计算
长35MM;Mdu>16时,加长40-50MM 15~21)Mdu
Ddi2+1.5Mdu,当Z=4取≤Ddi2+Mdu 67Ddi1,包角2θ=45°~130°
当Z=3~4时取大于(12.5+0.09Z2)Mdu
齿顶圆弧半径R 齿根圆弧半径R a
向齿厚=1.498mcosλ
齿顶圆弧半径
齿根圆弧半径R
R a 2
(b)蜗轮。