3.3.3物料平衡计算的方法和步骤
物料平衡的计算方法
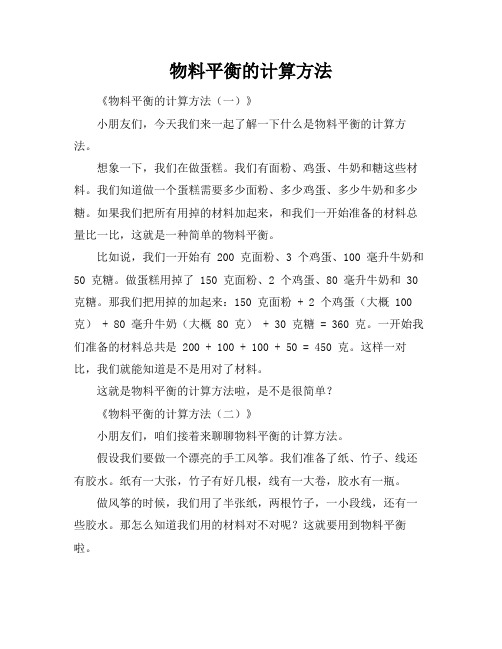
物料平衡的计算方法《物料平衡的计算方法(一)》小朋友们,今天我们来一起了解一下什么是物料平衡的计算方法。
想象一下,我们在做蛋糕。
我们有面粉、鸡蛋、牛奶和糖这些材料。
我们知道做一个蛋糕需要多少面粉、多少鸡蛋、多少牛奶和多少糖。
如果我们把所有用掉的材料加起来,和我们一开始准备的材料总量比一比,这就是一种简单的物料平衡。
比如说,我们一开始有 200 克面粉、3 个鸡蛋、100 毫升牛奶和50 克糖。
做蛋糕用掉了 150 克面粉、2 个鸡蛋、80 毫升牛奶和 30 克糖。
那我们把用掉的加起来:150 克面粉 + 2 个鸡蛋(大概 100 克) + 80 毫升牛奶(大概 80 克) + 30 克糖 = 360 克。
一开始我们准备的材料总共是 200 + 100 + 100 + 50 = 450 克。
这样一对比,我们就能知道是不是用对了材料。
这就是物料平衡的计算方法啦,是不是很简单?《物料平衡的计算方法(二)》小朋友们,咱们接着来聊聊物料平衡的计算方法。
假设我们要做一个漂亮的手工风筝。
我们准备了纸、竹子、线还有胶水。
纸有一大张,竹子有好几根,线有一大卷,胶水有一瓶。
做风筝的时候,我们用了半张纸,两根竹子,一小段线,还有一些胶水。
那怎么知道我们用的材料对不对呢?这就要用到物料平衡啦。
我们先看看用掉的东西。
半张纸大概是原来那张纸的一半,两根竹子,线用了大概 1 米(假设原来有 10 米),胶水用了四分之一瓶。
把这些加起来,和我们一开始准备的比一比。
如果差不多,那就说明我们用得刚刚好,这就是物料平衡哟!你们明白了吗?《物料平衡的计算方法(三)》小朋友,今天再给你讲讲物料平衡的计算方法。
比如说我们要搭一个积木城堡。
我们有好多好多的积木块,有大的、小的、方的、圆的。
我们开始搭城堡啦,用了 20 个大积木块,30 个小积木块,10 个方积木块,还有 5 个圆积木块。
那我们来算算用掉了多少。
把这些数字加起来,一共是 65 个积木块。
物料衡算的基本方法

西南科技大学
§3-6 化工过程的物料衡算 (一)物料衡算的基本方法
2、物料衡算式 物料衡算是研究某一个体系内进、出物料量及组成的变化 所谓体系就是物料衡算的范围,它可以根据实际需要人为 的选定。体系可以是一个设备或几个设备,也可以是一个单
schoolofmaterialsscienceandengineeringswust化工工艺设计chemicalprocessdesign西南科技大学第6节物料衡算一物料衡算的基本方法二无化学反应的物料衡算三反应过程的物料衡算四过程的物料衡算36化工过程的物料衡算一物料衡算的基本方法1物料衡算进行的步骤2物料衡算式3物料衡算的基准36化工过程的物料衡算一物料衡算的基本方法1物料衡算进行的步骤画出物料衡算示意图如方框图写出化学反应方程式包括主反应和副反应列出已知数据和由物料平衡所需要求解的问题决定系统的边界
体系中积累=输入-输出+生成-消耗
式中生成或消耗是因反应而生成或消耗的量 ; 积累项
可正可负 .当积累项不为零时,称为非稳定过程 ;积累
项+消耗 输入=输出
对无反应的稳定过程:
化工工艺设计(Chemical Process Design)
总质量平衡式 总物质的量平衡式 组分质量平衡式 组分物质的量平衡式
无化学反应 有化学反应
是 是 是 是 是 非 非 非
组分平衡式
元素原子 平衡式
元素原子质量平衡式
元素原子物质的量平衡式
是 是
是 是
西南科技大学
化工工艺设计(Chemical Process Design)
§3-6 化工过程的物料衡算 (一)物料衡算的基本方法
制药厂物料平衡计算的方法及流程

制药厂物料平衡计算的方法及流程英文回答:Material balance calculation is an important process in the pharmaceutical industry to ensure the accuracy and efficiency of production. It involves tracking and accounting for all the materials that enter and exit the manufacturing process, including raw materials, intermediates, and final products. The purpose of material balance calculation is to identify any discrepancies or losses in the production process and to optimize the use of materials.The method and procedure for material balance calculation in a pharmaceutical factory can be summarized as follows:1. Define the system boundaries: The first step is to define the boundaries of the system, which includes identifying the inputs and outputs of the process. Thishelps in determining the scope of the material balance calculation.2. Gather data: The next step is to collect all the necessary data related to the materials used in the process. This includes the quantity and quality of raw materials, intermediates, and final products. It is important toensure that the data is accurate and reliable.3. Calculate the material inventory: Once the data is collected, the material inventory at each stage of the process needs to be calculated. This involves determining the quantity of materials present at the beginning and endof each stage, as well as any additions or withdrawals during the process.4. Analyze material losses: After calculating the material inventory, it is important to analyze any material losses that may have occurred during the process. This can be done by comparing the expected material usage with the actual material usage. Any discrepancies should be investigated and addressed.5. Optimize material usage: Based on the analysis of material losses, steps can be taken to optimize the use of materials. This can include identifying areas of high material consumption and implementing measures to reduce waste or improve efficiency.6. Verify the results: Finally, the results of the material balance calculation should be verified to ensure their accuracy. This can be done by conducting regular audits and reconciling the calculated material balances with actual physical inventories.In conclusion, material balance calculation is acrucial process in the pharmaceutical industry to ensure the efficient and accurate use of materials. By following a systematic approach and analyzing the data, pharmaceutical factories can identify and address any material losses, leading to improved productivity and cost savings.中文回答:制药厂物料平衡计算是制药行业中一个重要的过程,用于确保生产的准确性和效率。
3.3.3物料平衡计算的方法和步骤
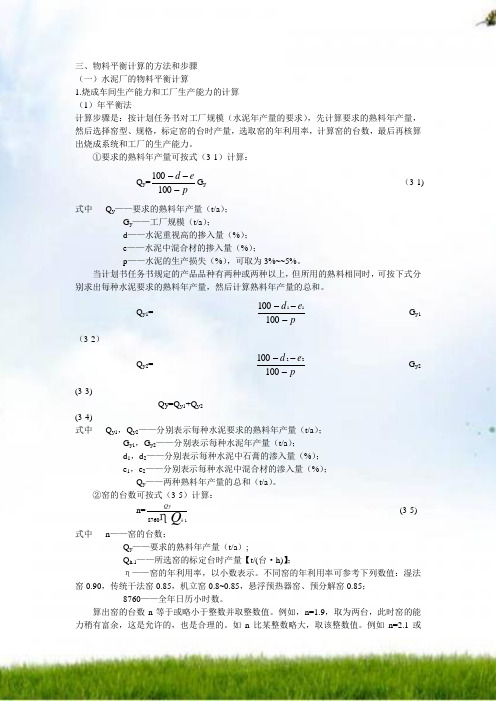
三、物料平衡计算的方法和步骤 (一)水泥厂的物料平衡计算1.烧成车间生产能力和工厂生产能力的计算 (1)年平衡法计算步骤是:按计划任务书对工厂规模(水泥年产量的要求),先计算要求的熟料年产量,然后选择窑型、规格,标定窑的台时产量,选取窑的年利用率,计算窑的台数,最后再核算出烧成系统和工厂的生产能力。
①要求的熟料年产量可按式(3-1)计算: Q y =ped ---100100G y (3-1)式中 Q y ——要求的熟料年产量(t/a );G y ——工厂规模(t/a );d ——水泥重视高的掺入量(%);e ——水泥中混合材的掺入量(%); p ——水泥的生产损失(%),可取为3%~~5%。
当计划书任务书规定的产品品种有两种或两种以上,但所用的熟料相同时,可按下式分别求出每种水泥要求的熟料年产量,然后计算熟料年产量的总和。
Q y1=pe d ---10010011G y1(3-2)Q y2=pe d ---10010022G y2(3-3)Qy=Q y1+Q y2(3-4)式中 Q y1,Q y2——分别表示每种水泥要求的熟料年产量(t/a );G y1,G y2——分别表示每种水泥年产量(t/a ); d 1,d 2——分别表示每种水泥中石膏的渗入量(%); e 1,e 2——分别表示每种水泥中混合材的渗入量(%); Q y ——两种熟料年产量的总和(t/a )。
②窑的台数可按式(3-5)计算:n=1.8760h QQyη (3-5)式中 n ——窑的台数;Q y ——要求的熟料年产量(t/a );Q h.1——所选窑的标定台时产量【t/(台·h)】;η——窑的年利用率,以小数表示。
不同窑的年利用率可参考下列数值:湿法窑0.90,传统干法窑0.85,机立窑0.8~0.85,悬浮预热器窑、预分解窑0.85;8760——全年日历小时数。
算出窑的台数n 等于或略小于整数并取整数值。
例如,n=1.9,取为两台,此时窑的能力稍有富余,这是允许的,也是合理的。
制药厂物料平衡计算的方法及流程
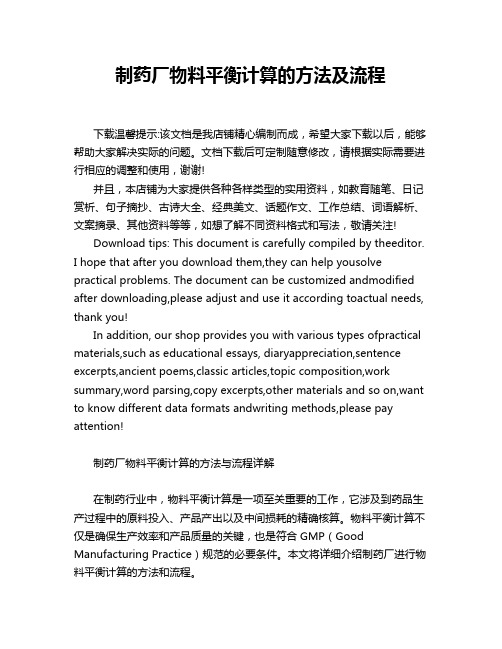
制药厂物料平衡计算的方法及流程下载温馨提示:该文档是我店铺精心编制而成,希望大家下载以后,能够帮助大家解决实际的问题。
文档下载后可定制随意修改,请根据实际需要进行相应的调整和使用,谢谢!并且,本店铺为大家提供各种各样类型的实用资料,如教育随笔、日记赏析、句子摘抄、古诗大全、经典美文、话题作文、工作总结、词语解析、文案摘录、其他资料等等,如想了解不同资料格式和写法,敬请关注!Download tips: This document is carefully compiled by theeditor.I hope that after you download them,they can help yousolve practical problems. The document can be customized andmodified after downloading,please adjust and use it according toactual needs, thank you!In addition, our shop provides you with various types ofpractical materials,such as educational essays, diaryappreciation,sentence excerpts,ancient poems,classic articles,topic composition,work summary,word parsing,copy excerpts,other materials and so on,want to know different data formats andwriting methods,please pay attention!制药厂物料平衡计算的方法与流程详解在制药行业中,物料平衡计算是一项至关重要的工作,它涉及到药品生产过程中的原料投入、产品产出以及中间损耗的精确核算。
物料衡算的步骤与方法(一)

物料衡算的步骤与方法(一)物料衡算的步骤与方法1. 引言物料衡算是生产和供应链管理中重要的环节,它涉及到对物料数量和价值的准确计算和管理。
本文将介绍物料衡算的步骤与方法,以帮助读者更好地理解和应用。
2. 步骤2.1 确定衡算目标在进行物料衡算前,首先需要明确衡算的目标。
这可以包括衡算物料的成本、库存价值、销售数量等。
明确目标可以帮助确定后续的衡算方法和指标。
2.2 收集数据收集相关的数据是进行物料衡算的基础。
这包括物料的进货价格、销售价格、销售数量、库存数量等。
可以通过内部系统、供应商提供的信息或者实地调查等方式获得所需的数据。
2.3 确定衡算方法根据衡算目标和所需数据,选择合适的衡算方法。
常见的衡算方法包括加权平均法、先进先出法、后进先出法等。
不同的方法适用于不同的情况,需要根据具体情况进行选择。
2.4 进行衡算计算使用选择的衡算方法,对所收集到的数据进行计算。
这包括计算物料的成本、库存价值、销售金额等指标。
可以借助计算软件或者自行编写程序来进行计算,提高效率和准确性。
2.5 分析和解读结果完成衡算计算后,需要对结果进行分析和解读。
将所得指标与目标进行对比,了解物料衡算的情况。
对衡算结果进行解读,可以发现潜在问题、改进机会以及优化方案等。
3. 方法3.1 加权平均法加权平均法是一种常用的物料衡算方法。
它根据不同批次物料的进货价格和数量,计算出平均成本。
通过平均成本可以得出物料的价值和库存成本。
3.2 先进先出法先进先出法是一种常用的库存管理方法,也可以用于物料衡算。
它假设先进入库存的物料也是先被销售出去,根据这个假设,可以得到物料的成本和库存价值。
3.3 后进先出法后进先出法和先进先出法相反,它假设最后进入库存的物料先被销售出去。
根据这个假设,可以计算出物料的成本和库存价值。
结论物料衡算是生产和供应链管理中重要的环节,它可以帮助企业准确计算物料的成本、库存价值等指标。
本文介绍了物料衡算的步骤和常用方法,希望能对读者有所帮助。
物料平衡管理规程
依据:《GMP》与药品生产质量管理的要求目的:实施物料平衡管理,防止差错和混药范围:每个批次产品生产过程的关键工序、物料1.在每个关键工序进行物料平衡是避免或及时发现差错与混药的有效方法之一,因此,每个品种各关键生产工序的批生产记录(批包装记录)都必须明确规定物料平衡的计算方法,以及根据验证结果确定各工序物料平衡的合格范围。
2.物料平衡计算的基本要求实际值2.1 计算公式:物料平衡= ────×100%理论值2.2 理论值:为按照所用的原料(包装材料)量,在生产中无任何损失或差错的情况下得出的最大数量。
2.3 实际值:为生产过程中实际产出量,包括本工序产出量、收集的废品量、生产中的取样品量(检品)、丢弃的不合格物料(如捕尘系统、真空系统、管理系统收集的残余物)3.在生产过程中如有跑料现象,应及时通知车间管理人员及质检员,并详细记录跑料过程及数量,跑料数量也应计入物料平衡之中,加在实际值的范围之内。
4.确定需进行物料平衡计算的主要工序4.1 提取车间:前处理、中药材提取后、浓缩后4.2口服液车间:配制、灌装(分装)、灭菌、灯检、内外包装材料等5.需进行物料平衡的物料、产品5.1 提取车间:前处理的各种原料、提取的液体物料(中间产品) 、提取浓缩液。
5.2 口服液车间:主要原料、半成品、关键内外包材、产成品6.物料平衡时计算单位:提取(前处理)以重量或体积进行计算、液体制剂以体积(或数量支、瓶、个等)计算、包装材料以数量计算。
7.物料平衡的管理7.1 每批产品在相关生产作业完成后,操作人员应根据物料的领用量、结存量、污损量等实际数量(计量必须准确)进行平衡计算,经车间质检员复核。
7.1.1 凡物料平衡在合格范围之内,经车间质检员检查签发“半成品递交许可证”后,才可以递交下工序。
7.1.2凡高于或低于合格范围,应立即贴示“待查”标志,不能递交,并填写偏差处理记录中相应项目,通知车间管理人员及车间质检员按“生产过程偏差管理规程”进行调查,采取处理措施,并详细记录。
第三章物料平衡计算
第三章物料平衡计算物料平衡计算是工程中的一项重要工作,其主要目的是通过对物料的输入、输出和转化过程进行分析和计算,确保工艺流程的稳定和可行性。
物料平衡计算需要考虑物料的质量、能量和动量方面的平衡,以及相应的测试和测量方法。
在进行物料平衡计算之前,首先需要了解和收集有关工艺流程的物料参数,如输入物料的质量流量、组成和温度,以及输出物料的质量流量、组成和温度等信息。
这些信息通常可以从实验、数据手册和现场测量获得。
接下来,进行物料平衡计算时需要考虑物料的输入、输出和转化过程。
输入物料可以是原料、能源或辅助材料等,输出物料可以是产品、废弃物或副产物等。
转化过程可以是化学反应、物理转化或传递过程等。
在计算过程中,需要将输入物料的质量流量、组成和温度与输出物料的质量流量、组成和温度进行对比和平衡,确保它们之间的一致性。
物料平衡计算的方法包括输入输出法和进退法。
输入输出法是通过累积分析输入物料和输出物料的质量和能量变化,计算物料的转化率和能量效率。
进退法是通过分析物料在不同过程中的流动和转化情况,计算各物料之间的平衡关系。
在进行物料平衡计算时,还需要考虑物料的测试和测量方法。
常用的测试方法包括采样、化验和仪器测量等。
采样是获取物料样本的过程,化验是通过实验室测试获取物料组成和性质的过程,仪器测量是通过使用各种仪器设备对物料进行质量、温度和压力等性质的测量。
物料平衡计算在实际工程中有着广泛的应用。
它可以帮助工程师了解和优化工艺流程,改进生产效率和产品质量。
在化工工程中,物料平衡计算可以用于计算化学反应的反应物和产物之间的转化率和收率。
在环境工程中,物料平衡计算可以用于衡量废水处理过程中的污染物去除效率。
在能源工程中,物料平衡计算可以用于优化能源利用和能源消耗。
总之,物料平衡计算是工程中不可或缺的一项工作,通过对物料的输入、输出和转化过程进行分析和计算,确保工艺流程的稳定和可行性。
它需要考虑物料的质量、能量和动量方面的平衡,以及相应的测试和测量方法。
物料平衡计算的方法及流程
物料平衡计算的方法及流程下载温馨提示:该文档是我店铺精心编制而成,希望大家下载以后,能够帮助大家解决实际的问题。
文档下载后可定制随意修改,请根据实际需要进行相应的调整和使用,谢谢!并且,本店铺为大家提供各种各样类型的实用资料,如教育随笔、日记赏析、句子摘抄、古诗大全、经典美文、话题作文、工作总结、词语解析、文案摘录、其他资料等等,如想了解不同资料格式和写法,敬请关注!Download tips: This document is carefully compiled by theeditor. I hope that after you download them,they can help yousolve practical problems. The document can be customized andmodified after downloading,please adjust and use it according toactual needs, thank you!In addition, our shop provides you with various types ofpractical materials,such as educational essays, diaryappreciation,sentence excerpts,ancient poems,classic articles,topic composition,work summary,word parsing,copy excerpts,other materials and so on,want to know different data formats andwriting methods,please pay attention!物料平衡计算是指根据质量守恒定律,对生产过程中的物料进行定量分析,以确定物料的输入、输出和损失情况。
第3章_物料衡算
适等,同时及时发现和解决流程设计中存在的问题。
工厂设计概论 Conspectus of Manufactory-design
§3.2 连续生产过程的物料衡算
第 3 章
直接求算法 对反应比较简单或仅有一个反应且只有一个未知数 的情况可直接求算;对反应比较复杂,物料衡算应依物 料流动顺序分步进行。 利用结点进行衡算 在化工生产中常有某些产品的组成需要用旁路调节才 能送往下一个工序的情况,可采用结点进行衡算如图3-1
物 料 衡 算
率、单程收率、回收率等) 、质量标准(原料、助剂、
中间产物和产品规格、组成及相关物理化学常数) 、化 学变化及物理化学变化的变化关系。 选择计算基准及计算单位 整个计算过程应保持计算基准与计算单位一致,避免
出错。有时根据特殊需要局部工序或设备可另设计算
基准及单位,最后要求进行单位换算建立各工序或各设 备之间正确的物料时间平衡关系。
② 物理化学变化(相变化)。在各酯化釜中,由于反应
第 3 章
温度高于水和EG的沸点,酯化生成的水被蒸出反应体系。
根据气液平衡关系,反应液中仍含有少量的水,水蒸出时 夹带出一定比例的EG, 蒸出的EG经分离后全部返回到反 应器中,因此各酯化反应器中原料配比不变,即Mr=Mr0 。 在缩聚反应釜中,为了使缩聚反应向生成聚合物的方 向移动,需尽量降低反应液中EG的含量,因此,缩聚阶段 特别是反应后期,需在高真空的条件下进行, 各缩聚釜中 生成的EG大部分被蒸出,使Mr< Mr0 。
物 料 衡 算
工厂设计概论 Conspectus of Manufactory-design
第 3 章
3.1.2 物料衡算的基本概念
进入生产装臵的各种原料 之间的比例关系,如质量比、 摩尔比 反应物参加反应的百分率 生成目标产物的反应物数 量占参加反应的反应物数 量的百分比 生产为目标产物的反应物
- 1、下载文档前请自行甄别文档内容的完整性,平台不提供额外的编辑、内容补充、找答案等附加服务。
- 2、"仅部分预览"的文档,不可在线预览部分如存在完整性等问题,可反馈申请退款(可完整预览的文档不适用该条件!)。
- 3、如文档侵犯您的权益,请联系客服反馈,我们会尽快为您处理(人工客服工作时间:9:00-18:30)。
三、物料平衡计算的方法和步骤 (一)水泥厂的物料平衡计算1.烧成车间生产能力和工厂生产能力的计算 (1)年平衡法计算步骤是:按计划任务书对工厂规模(水泥年产量的要求),先计算要求的熟料年产量,然后选择窑型、规格,标定窑的台时产量,选取窑的年利用率,计算窑的台数,最后再核算出烧成系统和工厂的生产能力。
①要求的熟料年产量可按式(3-1)计算: Q y =ped ---100100G y (3-1)式中 Q y ——要求的熟料年产量(t/a );G y ——工厂规模(t/a );d ——水泥重视高的掺入量(%);e ——水泥中混合材的掺入量(%); p ——水泥的生产损失(%),可取为3%~~5%。
当计划书任务书规定的产品品种有两种或两种以上,但所用的熟料相同时,可按下式分别求出每种水泥要求的熟料年产量,然后计算熟料年产量的总和。
Q y1=pe d ---10010011G y1(3-2)Q y2=pe d ---10010022G y2(3-3)Qy=Q y1+Q y2(3-4)式中 Q y1,Q y2——分别表示每种水泥要求的熟料年产量(t/a );G y1,G y2——分别表示每种水泥年产量(t/a ); d 1,d 2——分别表示每种水泥中石膏的渗入量(%); e 1,e 2——分别表示每种水泥中混合材的渗入量(%); Q y ——两种熟料年产量的总和(t/a )。
②窑的台数可按式(3-5)计算:n=1.8760h QQyη (3-5)式中 n ——窑的台数;Q y ——要求的熟料年产量(t/a );Q h.1——所选窑的标定台时产量【t/(台·h)】;η——窑的年利用率,以小数表示。
不同窑的年利用率可参考下列数值:湿法窑0.90,传统干法窑0.85,机立窑0.8~0.85,悬浮预热器窑、预分解窑0.85;8760——全年日历小时数。
算出窑的台数n 等于或略小于整数并取整数值。
例如,n=1.9,取为两台,此时窑的能力稍有富余,这是允许的,也是合理的。
如n 比某整数略大,取该整数值。
例如n=2.1或2.2,而取为两台时,则必须采取提高窑的台时产量的措施,或者相应增大窑的年利用率,否则便不能达到要求的设计能力。
如确因设备系列的限制而无合适规格的窑可选,使工厂设计能力略小于计划书规定的数值时,则应在初步设计说明书中加以说明。
当n 与整数值相差较大,例如n=1.2,1.5,1.6时,则一台窑达不到要求的设计能力,而两台窑又超过需求的设计能力太多,在此情况下,必须另行选择窑的规格,重新计算和标定窑的产量。
如因设备选型所限,使工厂设计能力比要求的能力超过较多时(例如n=1.6,1.7,而取为两台时),也应在初步设计说明书中加以论述。
窑的台数一般可考虑1~2台,不宜太多,故应尽可能采用效能高、规格较大的窑。
③烧成系统的生产能力可按下列各式计算:熟料小时产量 Q h =nQ h.1 (t/h ) (3-6) 熟料日产量 Q d =24Q h (t/d ) (3-7) 熟料年产量 Q y =8760ηQ h (t/a ) (3-8) ④工厂的生产能力可按下列各式由烧成车间的生产能力求得:水泥小时生产 h h Q ed pG ---=100100 (t/h ) (3-9)水泥日产量 G d =24G h (t/d ) (3-10) 水泥年产量 G y =8760ηG h (t/a ) (3-11) (2)周平衡法计算步骤是:按计划任务书对工厂规模(熟料日产量)的要求,选择窑型和规格,标定窑的台时产量,计算窑的台数,然后再核算出烧成系统和工厂的每周生产能力。
①窑的台数可按下式计算:1.24h dQ Q n =(3-12)式中 n ——窑的台数;Q d ——要求的熟料日产量(t/d ); 24——每日小时数。
②计算烧成系统的生产能力熟料小时产量和日产量的计算与年平衡法相同,见式(3-6)和式(3-7)。
熟料周产量:Q w =168Q h (t/周) (3-13) 式中 168——每周小时数。
③水泥厂小时产量和日产量的计算与年平衡法相同,见式(3-9)和式(3-10)。
水泥周产量:Q w =168Q h (t/周) (3-14) 2、原料、燃料、材料消耗定额的计算 (1)原料消耗定额①考虑煤灰掺入量时,1t 熟料的干生料理论消耗量:I sK --=100100干(3-15)式中 K 干——干生料理论消耗量(t/t 熟料); I ——干生料的烧失量(%);s ——煤灰掺入量,以熟料百分数表示(%)。
②考虑煤灰掺入量时,1t 熟料的干生料消耗定额:生干生P K K -100100=(3-16)式中 K 生——干生料消耗定额(t/t 熟料);P 生——生料的生产损失(%),一般3%~~5%。
③各种干原料消耗定额K 原=K 生·x (3-17) 式中 K 原——某种干原料的消耗定额(t/t 熟料); x ——干生料中该原料的配合比(%)。
(2)干事高消耗定额 ed dK d --=100 (3-18)式中 K d ——干石膏消耗定额(t/t 熟料);d 、e ——分别表示水泥中石膏、混合材的掺入量(%)。
(3)干混合材消耗定额e d ee K --=100 (3-19)式中 Ke ——干混合材消耗定额(t/t 熟料)。
(4)烧成用干煤消耗定额)100(1001f f p Q qK -=(3-20)式中 K f1——烧成用干煤消耗定额(t/t 熟料);q ——熟料烧成消耗(kJ/kg 熟料); Q ——干煤低位热值(kJ/kg 干煤); P f ——煤的生产损失(%),一般取3%。
(5)烘干用干煤消耗定额 )(ωωω烘烧湿f 221-100100q -100-2P Q Q M K f ⨯⨯⨯=(3-21)式中 K f2——烘干用干煤消耗定额(t/t 熟料);M 湿——需烘干的湿物料量,用年平衡法时以t/a 表示,用周平衡法时以t/周表示; Q 烧——烧成系统生产能力,用年平衡法时以熟料年产量表示,用周平衡法时以熟料周产量表示;ω1,ω2——分别表示烘干前、后物料的含水量; Q 烘——蒸发1kg 水分的耗热量(kJ/kg 水分),可参考烘干机经验数据,而准确的数据应通过具体烘干机的热工计算求得。
上述各种干物料消耗定额换算为含天然水分的湿物料消耗定额时,可用下式计算:0-100100ω湿干K K = (3-22)式中 K 湿,K 干——分别表示湿物料、干物料消耗定额(kg/kg 熟料);Ω0——该湿物料的天然水分(%)。
3.原料、燃料、材料需要量的计算和物料平衡表的编制将各种物料消耗定额乘以烧成系统生产能力,可求出各种物料的需要量。
例如,将湿石灰石消耗定额乘以熟料周产量,便得出湿石灰石每周需要量;乘以熟料年产量,便得出湿石灰石每年需要量。
将计算结果汇总成物料平衡表,其格式见表3-2。
表3-2 水泥厂物料平衡表物料名称天然水分生产损失消耗定额(t/t熟料)物料平衡量(t)备注干料含天然水分料干料含天然水分料1 2 3 4 5 6 7 8 9 10 11 12 13 14 石灰石粘土铁粉生料石膏混合材熟料水泥烧成用煤烘干用煤燃煤合计注:1.采用年平衡法时,可不列第8栏和第12栏;采用周平衡法时,可不列第9栏和第13栏。
2.备注中可列:生料组分、物料配合比、生产熟料消耗定额、烧成热耗和烘干热耗、煤的热值等。
(二)陶瓷厂的物料平衡计算1.衡算步骤(1)根据生产工艺流程,选择衡算的项目。
凡具有主机设备的工序必须立项衡算,而只有辅助设备或非重要设备的工序,可以不单独列项,此外上下加工量相差不大的工序如原料的粗碎、中碎工序,可以并项计算。
(2)确定与衡算项目密切相关的工艺参数,如损失率、废品率、回坯率和烧失率等。
(3)根据计划任务书中的设计产量及损失率、废品率,逆着生产流程的工序,计算各工序的加工任务,一般从包装→检验(装配)→焙烧→上釉→干燥→成型→制泥,逐项进行计算。
(4)编制物料衡算表,把计算结果列入表中。
在进行物料衡算时,要注意基准的统一。
如:时间均以年为单位;废品率指加工100件制品时,报废件数的百分数,以制品的件数为基准,如要换算成质量时,可将半成品按不同加工工序中的单件制品质量乘以件数;半成品在生产过程中会产生物理、化学变化,如干燥脱水;焙烧时,灼烧损失等,为了计算方便,物料衡算中常采用瓷坯基准及干坯基准。
2.衡算过程以一次烧成工艺为例:(1)检验、包装废品率工厂年产量年出窑量(烧成量)-1=(2)烧成废品率年出窑量年装窑量-1=(3)干燥废品率年施釉量年干燥量-1=(4)施釉废品率年装窑量年施釉量-1=(5)成型、修坯废品率年干燥量年成型量-1=(6)练泥损失率)切削损失率)((年成型量年坯料需要量-1-1=以上过程均未考虑烧失率,系采用瓷坯基准(灼烧率),下面过程为换算成干坯基准(干基)。
即烧失率年坯料需要量干基年坯料需要量-1)(=(7)年泥料破碎、粉碎加工量=球磨、过筛损失率)粗、中碎损失率)((废坯泥回收量(干基)年坯料需要量(干基)-1-1-(t/a )废坯泥回收量(干基)=(年干燥量×干燥废品率+年成型量×成型废品率+年成型量×成型余泥率)×坯泥回收利用率 (t/a )(8)各种原料处理量(干基)=年泥料粉碎加工量(干基)×该原料在配料中的百分比(%) (t/a )(9)各种原料年进厂量(湿基) =自然含水率)洗选损失率)(储存损失率)(()各种原料处理量(干基-1-1-1 (t/a )(10)各种原料年购入量(湿基)=运输损失率各种原料年进厂量-1 (t/a )【例】某厂年产100万m 2釉面砖,产品规格152mm ×152mm ×5mm ,物料平衡计算的主要参数及结果见表3-3和表3-4.表3-3 主要生产工序半成品数量变化 产品名称规格(mm)单位面积质量(kg/m 2)年产量 釉烧 (万m 2)(t)损失率(万m 2/a )(t/a)装窑、施釉素烧、干燥损失率(万m2/a)(t/a)坯:釉灼减(%)损失率(%)(万m2/a)(t/a)1 109.8 10980 94:6 8 15 129.2 13198成型喷雾干燥新坯料加工量(干基)损失率(%)(万m2/a)(万m2/a)(t/a)损失率(%)(t/a)成型回坯率(%)喷干回坯率(%)(t/a)10 143.5 6314 14665 5 15437 8 3 13800 注:1.素烧、干燥量计算已考虑灼烧减量,故后部分计算为干基;2.年新坯加工率=年喷雾干燥量-年回坯量=年喷雾干燥量-年成型量×成型回坯率+年喷雾干燥量×喷干回坯率;3.干燥、素烧采用一次码烧工艺,故二工序合并计算;4.年釉料需要量=10980×6%=658.8t,釉用原料加工量计算方法同坯料计算;5.规格152mm×152mm×5mm的釉面砖,以44片/m2计算成型产量(万片/a)。