风扇压气机设计技术
航空发动机风扇 压气机叶片激光冲击强化技术的发展与应用
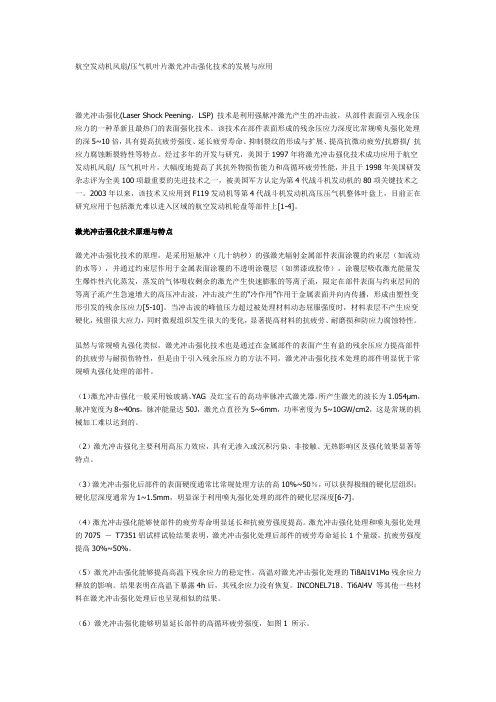
航空发动机风扇/压气机叶片激光冲击强化技术的发展与应用激光冲击强化(Laser Shock Peening,LSP) 技术是利用强脉冲激光产生的冲击波,从部件表面引入残余压应力的一种革新且最热门的表面强化技术。
该技术在部件表面形成的残余压应力深度比常规喷丸强化处理的深5~10倍,具有提高抗疲劳强度、延长疲劳寿命、抑制裂纹的形成与扩展、提高抗微动疲劳/抗磨损/ 抗应力腐蚀断裂特性等特点。
经过多年的开发与研究,美国于1997年将激光冲击强化技术成功应用于航空发动机风扇/ 压气机叶片,大幅度地提高了其抗外物损伤能力和高循环疲劳性能,并且于1998年美国研发杂志评为全美100项最重要的先进技术之一,被美国军方认定为第4代战斗机发动机的80项关键技术之一。
2003年以来,该技术又应用到F119发动机等第4代战斗机发动机高压压气机整体叶盘上,目前正在研究应用于包括激光难以进入区域的航空发动机轮盘等部件上[1-4]。
激光冲击强化技术原理与特点激光冲击强化技术的原理,是采用短脉冲(几十纳秒)的强激光辐射金属部件表面涂覆的约束层(如流动的水等),并通过约束层作用于金属表面涂覆的不透明涂覆层(如黑漆或胶带),涂覆层吸收激光能量发生爆炸性汽化蒸发,蒸发的气体吸收剩余的激光产生快速膨胀的等离子流,限定在部件表面与约束层间的等离子流产生急速增大的高压冲击波,冲击波产生的“冷作用”作用于金属表面并向内传播,形成由塑性变形引发的残余压应力[5-10]。
当冲击波的峰值压力超过被处理材料动态屈服强度时,材料表层不产生应变硬化,残留很大应力,同时微观组织发生很大的变化,显著提高材料的抗疲劳、耐磨损和防应力腐蚀特性。
虽然与常规喷丸强化类似,激光冲击强化技术也是通过在金属部件的表面产生有益的残余压应力提高部件的抗疲劳与耐损伤特性,但是由于引入残余压应力的方法不同,激光冲击强化技术处理的部件明显优于常规喷丸强化处理的部件。
(1)激光冲击强化一般采用钕玻璃、YAG 及红宝石的高功率脉冲式激光器。
动力风扇实验报告总结(3篇)
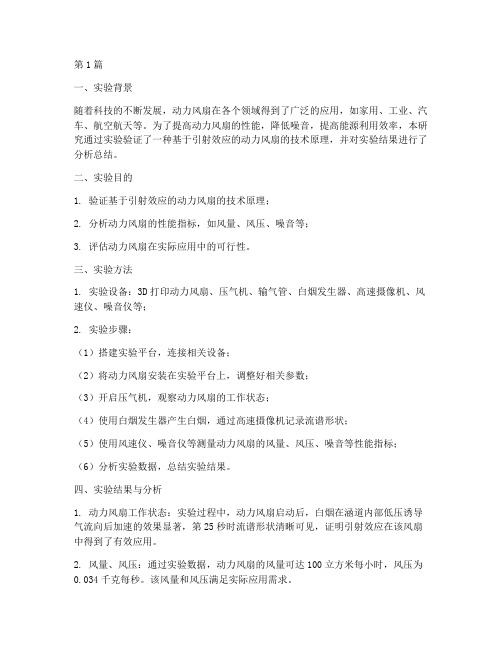
第1篇一、实验背景随着科技的不断发展,动力风扇在各个领域得到了广泛的应用,如家用、工业、汽车、航空航天等。
为了提高动力风扇的性能,降低噪音,提高能源利用效率,本研究通过实验验证了一种基于引射效应的动力风扇的技术原理,并对实验结果进行了分析总结。
二、实验目的1. 验证基于引射效应的动力风扇的技术原理;2. 分析动力风扇的性能指标,如风量、风压、噪音等;3. 评估动力风扇在实际应用中的可行性。
三、实验方法1. 实验设备:3D打印动力风扇、压气机、输气管、白烟发生器、高速摄像机、风速仪、噪音仪等;2. 实验步骤:(1)搭建实验平台,连接相关设备;(2)将动力风扇安装在实验平台上,调整好相关参数;(3)开启压气机,观察动力风扇的工作状态;(4)使用白烟发生器产生白烟,通过高速摄像机记录流谱形状;(5)使用风速仪、噪音仪等测量动力风扇的风量、风压、噪音等性能指标;(6)分析实验数据,总结实验结果。
四、实验结果与分析1. 动力风扇工作状态:实验过程中,动力风扇启动后,白烟在涵道内部低压诱导气流向后加速的效果显著,第25秒时流谱形状清晰可见,证明引射效应在该风扇中得到了有效应用。
2. 风量、风压:通过实验数据,动力风扇的风量可达100立方米每小时,风压为0.034千克每秒。
该风量和风压满足实际应用需求。
3. 噪音:实验过程中,动力风扇的噪音水平较高,需进一步优化设计以降低噪音。
4. 性能评估:基于引射效应的动力风扇在风量和风压方面表现良好,但在噪音方面有待改进。
综合考虑,该风扇在实际应用中具有较高的可行性。
五、实验结论1. 基于引射效应的动力风扇技术原理得到验证,具有较好的应用前景;2. 该风扇的风量和风压满足实际应用需求,但在噪音方面有待改进;3. 实验结果表明,解耦的设计降低了系统设计复杂度,有利于提高动力风扇的性能。
六、实验展望1. 优化动力风扇的设计,降低噪音,提高能源利用效率;2. 研究不同工况下动力风扇的性能,为实际应用提供理论依据;3. 探索新型动力风扇材料,提高风扇的稳定性和耐久性。
第3章 压气机
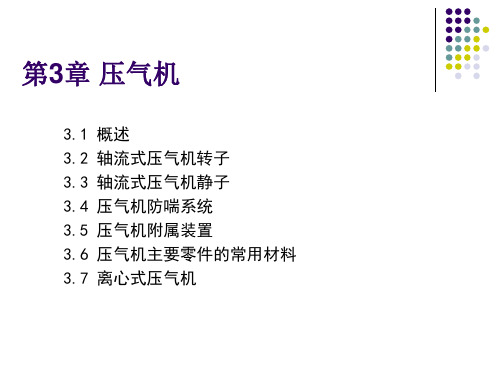
3.4 压气机防喘系统
3.4.1 压气机的喘振 基元级 攻角 落后角 失速:攻角过大时,气流从叶背分离,导致压气机效率降
低、工作不稳定、旋转失速、喘振。 旋转失速:失速区向叶片旋转相反方向移动的现象。 喘振:在非设计状态下,压气机前面增压级和后面增加级
不匹配,导致气流的攻角变大,所产生的脉冲型的气流分 离和堵塞。
3.4 压气机防喘系统
3.4.1 压气机的喘振 对于多级轴流式压气机,容易出现喘振的情况
➢ 在一定转速下工作时,若出口反压增大,使空气流量降 低到一定程度时,就会产生共振。因为空气流量降低时, 各级叶片上的气流攻角增加,容易产生气流分离和堵塞。
➢ 当发动机偏离设计工作状态而降低转速时容易发生喘振。
装配紧度研究
恰当半径内:鼓径向变形小,盘大;盘压入鼓 恰当半径外:盘径向变形小,鼓大;鼓压入盘
3.2.2 鼓盘式转子 1. 不可拆卸的鼓盘式转子
装配定心:径向销钉原理
3.2.2 鼓盘式转子
2. 可拆卸的鼓盘式转子 在转配以后可以根据使用和维修的要求进行可以进行无
损分解的转子。 分类 (1)用拉杆联接 JT3D (2)短螺栓联接 JT9D高压 (3)长轴螺栓联接 30KY低压
(2) 特点 端部过弯叶身的叶片
为了减少叶片两端壁附面层所造成的损失,而将叶身(包括静子叶 片)尖端和根部前、后缘特别地加以弯曲,提高压气机效率。
3.2 轴流式压气机转子
3.2.3 工作叶片及其与轮盘的联接 2、榫头的构造
(1) 要求
3.2 轴流式压气机转子
3.2.3 工作叶片及其与轮盘的联接 2、榫头的构造
(2) 特点 减震凸台
较长叶片为避免发生危险共振或颤震在叶身中部的凸台
开题报告(CFM-56航空发动机风扇结构强度与噪声分析)

XX大学毕业设计(论文)开题报告题目发动机CMF-56航空发动机风扇结构强度与噪声分析专业名称飞行器动力工程班级学号xx学生姓名 xx指导教师xx填表日期年月日一、选题的依据及意义:1. 选题的依据:现代人生活中有三大污染:空气污染、噪声污染和水污染。
前面两项都与航空发动机有关。
噪声污染是伴随着近代工业革命和航空喷气时代的到来而到来的。
现今,噪声污染已是一个全世界都十分关注的环境问题,过量的环境噪声对人的生理和心理都有影响。
长期暴露在高噪声环境下对人的听力和身体健康将造成严重的危害,一般性的噪声干扰则会影响人们的正常工作和生活。
在人们的生活中,噪声无处不在。
噪声的等级由声强级的单位“分贝”数表示大小。
我国国家标准(GB 3096-1982)中规定:居民生活区白天的允许值为50dB,晚上则为40dB。
根据生理健康测定:一般环境声音在30至50分贝时,不会影响人们正常的起居;声音达到60分贝以上时,人们便会有较大的感觉,导致失眠;在噪声级70分贝的环境下,人与人之间正常的沟通交流就会感到困难;80至90分贝时会觉得很吵,长期在这种环境下学习和生活,会使人体神经细胞逐渐受到破坏;若是在噪声级85至90分贝的环境下长期工作若干年,造成耳聋的几率达26%;长期生活在90分贝以上的环境中,听力会受到严重影响并产生神经衰弱头疼高血压等疾病;大于100分贝会使耳朵发胀疼痛,这样的声响达到人耳的痛阈。
痛阈以上的噪声危害更大,超过115分贝,大脑皮层的功能便严重衰退。
如果超过175分贝,可能引发心脏共振,导致死亡。
可见,噪声对人体的损害非常之大。
电风扇噪声为30分贝,洗衣机为50分贝,空调为70分贝,一个人声嘈杂、生意兴隆的餐厅噪声为75~80分贝,车水马龙的大街上可达85~90分贝,机声隆隆、马达轰鸣的生产车间大约为90分贝。
螺旋桨飞机附近的噪声约为105~110分贝,涡轮喷气发动机在中间状态工作时约为110~130分贝,加力状态可达180~192分贝。
风扇压气机结构设计

将材料进行切割和成型处理,满足产品尺寸 和形状要求。
组装和调试阶段
包装和运输阶段
将各部件按照一定的顺序和步骤组装在一起 ,并进行调试和检验。
对成品进行包装,确保在运输过程中不受损 伤,并按照客户要求进行运输。
制造工艺中的关键问题
精度控制
保证各部件的制造精度, 确保组装时的配合精度和 质量。
组装工艺
风扇压气机结构设计
xx年xx月xx日
目录
• 风扇压气机设计总述 • 风扇压气机总体方案及结构设计 • 风扇压气机性能分析与优化 • 风扇压气机制造工艺及质量控制 • 风扇压气机设计的工程应用及效果 • 风扇压气机设计的经验总结与进一步研究
01
风扇压气机设计总述
风扇压气机概述
风扇压气机是一种将电能转化 为空气动能,同时增加空气压
随着航空航天、能源、环保等领域 的不断发展,风扇压气机的应用前 景将更加广阔。
06
风扇压气机设计的经验总结与进一步 研究
设计经验总结
风扇压气机是航空发动机的关键部件之一,其设计需考虑多个因素,如气动性能 、强度、可靠性等。
在设计过程中,需要对压气机的性能参数进行反复迭代和优化,以达到最佳性能 。
优化方案二
通过增加风扇压气机的高压侧和低压侧的壁面附 面层,减少流动损失,提高效率。
对比结果
对三种优化方案进行CFD模拟和实验测试,对比 各种方案的性能提升效果和经济性表现,为风扇 压气机的优化设计提供参考。
04
风扇压气机制造工艺及质量控制
制造工艺流程
设计和准备阶段
切割和成型阶段
根据产品要求进行详细设计,准备所需材料 和工具。
时输出轴功。
工业领域应用
在工业领域,风扇压气机被广泛 应用于各种空气压缩、通风和排 放系统中,如冶炼厂、化工厂等 。
涡扇15发动机原理

涡扇15发动机原理以涡扇15发动机原理为标题,我们将详细介绍涡扇15发动机的工作原理。
涡扇15发动机是一种高性能的喷气式发动机,广泛应用于民用和军用飞机中。
涡扇15发动机是一种涡轮风扇发动机,它采用了涡轮增压器和风扇两个级别的压气机。
其工作原理如下:1. 压气机部分:涡扇15发动机的压气机由多个级别组成,每个级别都有一组转子和定子。
当发动机启动后,压气机的转子开始旋转,通过离心力将空气压缩并推向下一个级别。
这样逐级压缩的过程使得空气的压力和温度不断增加。
2. 燃烧室部分:在压气机的末级,空气被引导进入燃烧室。
在燃烧室中,燃料被喷射进入高温和高压的空气中,然后燃烧产生高温高压的燃气。
这些燃气通过喷嘴喷出,产生推力。
3. 高压涡轮部分:燃气喷出后,通过高压涡轮的作用,将其中一部分能量转化为机械能,驱动压气机的转子旋转。
高压涡轮的转子与压气机的转子通过轴连在一起,共同组成了一个整体。
4. 低压涡轮部分:燃气通过高压涡轮后,流经燃气发生器,再通过低压涡轮。
低压涡轮的转子则驱动着风扇转子的旋转。
风扇是涡扇15发动机的重要组成部分,它通过产生大量的气流来提供额外的推力。
5. 喷管部分:经过低压涡轮后,燃气流向喷管。
喷管的设计有助于加速燃气排出,产生更大的推力。
喷管还能改变喷气流的方向,从而提供飞行中所需的推力调整和机动性。
涡扇15发动机的工作原理可以总结为:通过压气机将空气压缩,然后在燃烧室中与燃料混合并燃烧产生高温高压的燃气,燃气通过高压涡轮和低压涡轮的作用驱动压气机和风扇旋转,最后通过喷管排出产生推力。
涡扇15发动机具有高效、可靠和推力大的特点,广泛应用于各类飞机中。
它的工作原理基于涡轮增压和风扇的组合,能够提供足够的推力和燃料效率,满足飞机在不同飞行阶段的需求。
不断的技术创新使得涡扇15发动机在性能和可靠性上得到了进一步的提升,为航空工业的发展做出了重要贡献。
风扇压气机结构设计ppt课件

3.防外来物打伤〔FOD)
❖大涵道比风扇及涡轮轴发动机尤为重要
3.防外来物打伤〔FOD)
❖防止外物打伤的措施: ❖叶片上加凸台,带冠; ❖小展弦比叶片 ❖进气锥及增压级气路形状 ❖中介机匣位置 ❖防尘网 ❖粒子分离器
3.防外来物打伤〔FOD)
3.防外来物打伤〔FOD)
RB211-535E4
GE90
盘缘上。 ❖ 轴向燕尾型--广泛采用于风扇、压气机中。 ❖ 环形燕尾槽--用于高压后几级中。 ❖ 榫树型榫头--在压气机中较少使用。 ❖叶片在轮盘槽内的固定 ❖卡圈、锁片、锁板、销钉
2.压气机工作叶片结构
❖根部 (榫头)
❖销钉连接
2.压气机工作叶片结构
❖根部 (榫头) ❖锁片槽向固定
2.压气机工作叶片结构
混合式转子
1. 转子的基本结构
❖二、转子的连结形式: ❖短螺栓连接 ❖焊接的盘鼓混合式转子 ❖销钉连接转子 ❖长螺栓连接转子
短螺栓连接转子
二、转子的连结形式
❖发动机转子应力分布
焊接的盘鼓混合式转子
销钉连接 转子
长螺栓连接转子
长螺栓连接转子
❖AL-31F
2.压气机工作叶片结构
❖ 叶身 ❖ 叶型: ❖ 亚音、超音 ❖ 叶尖切速: ❖ 决定叶片的加功量 ❖ 宽弦: ❖ 提高抗外物打伤能力,减振
❖作用 ❖固定叶片并使叶片对气
体作功。 ❖负荷很大是重要零件。 ❖剖面形状 ❖外缘:视叶片尺寸定 ❖内部:由强度而定。 ❖中心:开孔大加厚。
3.压气机轮盘结构
❖盘~轴作成一体简化结构
❖盘~叶片做成一体 ❖ (Blade+Disk=Blisk) ❖整体叶环 ❖ (Blade+Ring=Bling)
风扇压气机结构设计

优化方法
几何优化
调整风扇压气机的叶片形状、角 度和位置等几何参数,以提高其
性能表现。
流动控制
采用适当的流动控制措施,如安装 导流叶片、使用湍流模型等,改善 风扇压气机的内部流场结构。
多学科优化
综合考虑结构、热力学和气动力学 等多个学科因素,进行多学科优化 设计,提高整体性能。
优化实例
某型风扇压气机通过改进叶片形状,减少了流动 损失,提高了效率。
轻量化
风扇压气机的设计应尽可能减 轻其重量,以减小发动机的总
重,提高飞行器的性能。
维护性
风扇压气机的设计应便于维护 和修理,降低维护成本,提高
发动机的经济性。
03 风扇压气机的设计方法
设计方法概述
理论设计
基于压气机气动理论和结 构力学原理,进行风扇压 气机的设计。
实验设计
通过实验测试和数据分析, 对风扇压气机进行优化设 计。
风扇压气机结构设计
目录
CONTENTS
• 引言 • 风扇压气机的基本原理 • 风扇压气机的设计方法 • 风扇压气机的结构设计 • 风扇压气机的性能仿真与优化 • 结论与展望
01 引言
研究背景和意义
随着航空工业的快速发展,风扇压气机作为航空发动机的关 键部件,其性能和效率对整个发动机的性能有着重要影响。 因此,研究风扇压气机的结构设计具有重要的实际意义。
04 风扇压气机的结构设计
风扇叶轮设计
总结词:高效低阻
详细描述:风扇叶轮设计应注重提高空气流动效率,降低流动阻力,以达到更高的压缩效率。叶轮的形状、叶片的数目、角 度以及材料选择都是关键因素。
机匣设计
总结词
刚度与强度
详细描述
机匣作为风扇压气机的外壳,需要承受内部的气体压力和旋转力矩。因此,机匣设计应注重提高刚度 和强度,防止变形和振动。同时,机匣的冷却设计也是关键。
- 1、下载文档前请自行甄别文档内容的完整性,平台不提供额外的编辑、内容补充、找答案等附加服务。
- 2、"仅部分预览"的文档,不可在线预览部分如存在完整性等问题,可反馈申请退款(可完整预览的文档不适用该条件!)。
- 3、如文档侵犯您的权益,请联系客服反馈,我们会尽快为您处理(人工客服工作时间:9:00-18:30)。
b. 方案评估 采用二维气动计算程序对一维计算筛选后的方案进行分析。通过调整流道和设计参数轴向压力分布,对径向和轴向载荷分布进行优化;
c. 确定初始结构方案设计。
风扇是涡轮风扇发动机的重要部件之一,它的作用与压气机的相同。风扇后面的空气分为两路,一路是外涵道,一路是内涵道。风扇一般为一级,使结构简单。
风扇/压气机设计技术主要包括气动设计技术、全三元计算技术、间隙控制技术、旋转失速和喘振控制技术、结构设计技术、材料与工艺技术等方面。
国外概况:目前,战斗机发动机的推重比在不断提高,因此要求风扇/压气机级压比不断提高但又保持效率在可接受范围内,这始终是风扇/压气机设计所追求的目标。美国80年代中期开始实施的"综合高性能涡轮发动机技术"计划(即IHPTET计划)的目标是在下世纪初验证推重比为20的战斗机发动机技术,风扇结构最终实现单级化,压气机也由9级减为3级。俄罗斯的风扇/压气机的研制计划与美国IHPTET计划相类似。也就是说,研制高压比风扇/压气机已经成为风扇/压气机的发展趋势。美国、俄罗斯等国家都已制订研究计划并已取得阶段性成果。
A、 机匣处理
机匣处理对于转子叶尖为临界失速区的转子非常成功。实验表明,压气机失速时,叶尖首先达到失速区,经转子机匣处理后,其失速裕度有显著改善,且增压比、效率也有一定改善。美国NASA刘易斯研究中心采用了一个5级跨音速压气机的进口级进行机匣处理的试验研究,试验了以下三种不同结构:
N-S方程解得的叶片排内流场与实际测得的更吻合,这使得压气机设计又向前迈进了一大步。
3、间隙控制技术
现代航空发动机先进的气动设计与试验方法已使压气机效率高达88%以上。再要进一步提高发动机性能,就要尽量减小气流泄漏,减少流道中的端壁损失。叶尖间隙损失是通道端壁损失的重要组成部分,这种损失是由动叶和机匣间的间隙造成的。中等推力、中等增压比的发动机,叶片高度较大,由叶尖间隙造成的损失还不很严重。随着增压比的增加,叶片高度显著缩短,高压压气机后几级的叶高有的已缩短到20-30mm,这样叶尖间隙造成的损失变得非常显著。根据实测,叶尖间隙相对值(即间隙/叶片高度)增加1%,效率约降低1%;而效率降低1%,耗油率约增加2%。因此,为了保持发动机在主要工作状态下间隙最小,在其它状态不发生干扰摩擦,提出了间隙控制问题。
4、旋转失速和喘振控制技术
旋转失速是一种限制在压气机叶片排附近的流动扰动现象。也就是说,它不影响压气机远处的上下游。旋转失速发生在压气机转速一定而空气流量减少时。当空气流量减少到一定程度就能观察到不稳定流动,同时压气机发出特殊叫声,振动也增大。在动叶后测得的流场表明,有一个或多个扰动流或称失速团以低于转子的速度围绕着压气机旋转,这种非稳定工况即称之为旋转失速。此时,压气机压比突然下降,气动性能明显恶化,有时还会导致压气机着火。另外,每个叶片在进入和退出失速区时还会承受脉动载荷,容易引起疲劳断裂。统计表明,旋转失速是使压气机叶片疲劳断裂的主要原因之一。旋转失速时,其气流的脉动频率较高(约40-120Hz)、脉动的幅值比喘振时小。
1、风扇/压气机的气动设计技术
压气机的气动设计又可分为:
初始方案设计
初始方案设计主要是根据空战战斗机飞行任务和设计约束条件及其先进气动布局的技术特点,确定发动机的总压比、流量、效率、裕度等设计条件,选择合适的风扇或压气机设计方案,并根据确定的气动方案设计初始结构方案。通常,初始方案设计又分为以下几个阶段:
风扇单级压比在目前最先进战斗机发动机F119上已达1.7;在预研的试验件上,美国达2.2,叶尖速度475m/s;而俄罗斯试验件单级压比达2.4和3.2,叶尖速度则分别为577m/s和630m/s。转子叶片展弦比则减小到1.0左右。
对于核心压气机,也呈现大致相同的发展趋势。核心压气机平均级压比从50年代的1.16提高到90年代的1.454,而叶尖速度从291m/s提高到455.7m/s。目前,美国现役战斗机发动机和正处于工程和制造发展阶段的90年代先进战斗机(ATF),其核心压气机基本上是70年代研制成功的。GE公司下一代核心压气机正处于研究起步阶段,目标是比目前最高级压比再提高25%。由此可见,追求更高的级压比一直是各国研制风扇/压气机的发展方向。
风扇/压气机的级压比的提高主要有以下途径:一是进一步发展传统的跨音级风扇/压气机。传统的跨音级风扇/压气机是指转子相对来流叶尖超音、叶根亚音,静子绝对来流亚音。目前各国现役发动机风扇/压气机进口级均属此类型。进一步发展传统的跨音级风扇/压气机即进一步提高叶尖切线速度,如采用小展弦比前缘后掠式叶片,将叶片设计成掠式几何形状以合理控制通道激波的强度,在利用气流跨越激波产生压比突跃的同时控制激波的损失。二是研制超音通流风扇。80年代后期NASA 刘易斯研究中心开始实施一项超音通流风扇计划,研制出的此类风扇进出口轴向气流速度均超音。与传统跨音风扇相比,当叶尖切线速度相同时,超音通流风扇可实现更高的级增压比。
此外,采用更先进的刷式封严取代传统的篦齿封严能有效减少径向间隙的漏气量,提高发动机效率达4%-6%。目前,EJ200、V2500、XG40发动机都已采用刷式封严。近年,NASA兰利研究中心又开始研制一种新的叶尖间隙自适应控制法--形状记忆合金法。它是将形状记忆合金环放置在压气机每级的凸肩上,当每级达到自身的工作温度时形状记忆合金环径向收缩,将运转间隙降低到某一预定值。实验发现,装上这种形状记忆合金环能提高压气机效率0.8%,耗油率将下降0.2-0.4%。
叶尖间隙控制的方法可以分为被动控制和主动控制两种。
被动间隙控制
被动间隙控制,即不随发动机工作状况调节的间隙控制技术。主要对转子和静子在不同工作状态下的受力状况进行认真分析,尤其是对机匣在各种工况下的热变化进行精心设计,以求转、静子之间的热配合恰当,使间隙保持在允许的范围内。一般过去研制的发动机都采用这种方法。主要是通过减小装配间隙、采用双层机匣或低线膨胀系数的合金做机匣等途径来减小发动机工作时的径向间隙。美国GE公司的CF6在前安装节处增加一个切向连杆,使压气机机匣最大局部变形由1.8mm减小到1mm,从而减小压气机间隙。美国普?惠公司的JT9D在外封气环上喷覆陶瓷涂层,在叶尖上敷以碳化硅涂层,以改善环与叶片之间的可磨合性。在JT8D高压压气机外环上喷涂镍铬聚酯易磨材料,使转子叶片旋转时,利用叶片在外环上磨出环槽,以减小间隙。英国罗?罗公司的RB211采用双层结构机匣,保持气流通道的内层机匣仅承受气动载荷,外层机匣则承受并传递结构载荷,刚性较好的外层机匣变形小,可以使RB211在飞行时保持均匀的叶尖间隙。在设计机匣时,应使机匣在不同的发动机工作状态下直径的变化与转子叶尖的径向膨胀尽可能一致,从而保证巡航状态间隙较小。另外,还可以采用低线膨胀系数材料做压气机机匣,由于稳态下可以得到更小的间隙,而瞬态下压气机机匣与转子能更好地配合,预计效率能改进0.4%。在压气机机匣上开槽,使叶尖间隙伸入一矩形槽或沟中,也是控制叶尖间隙、提高压气机性能的有效方法之一。目前,CF6-80C2、CFM56-5、RB211-524G/H、PW4000发动机都在压气机机匣上开有斜槽。
求解N-S方程
欧拉方程加上粘性项就是纳维尔斯托克斯(N-S)方程。求解N-S方程所需要的条件比求解欧拉方程更高,电子计算机计算速度每秒高达亿次或几亿次,并且需要有大的内存和外存设备。因为计算粘性流,沿壁面计算站之间距离非常小(一般在0.1-0.2mm左右),计算站和计算结点非常多,计算工作量巨大。
计算粘性流需要解决的另一个问题就是紊流计算模型。目前,计算紊流采用零方程、一方程和双方程。普遍认为双方程模型与混合长度模型(计算分离点)相结合,效果更好。
d. 对叶身进行应力和振动分析,根据分析结果修改叶型;
e. 对叶片进行颤振分析,并修改叶型;
f. 进行非设计点性能计算;
g. 机匣处理设计;
h. 编写最终气动设计报告。
ቤተ መጻሕፍቲ ባይዱ2、全三元计算技术
在上述设计高性能的风扇或压气机的过程中,采用何种数值计算方法是评估设计方法好坏的一个关键因素。传统的、忽略粘性或对粘性进行简化处理的分析设计方法不能真实反映风扇或压气机三维流场的复杂流动。目前世界上有能力设计航空发动机的国家,都在研究压气机全三元计算,以求更精确地反映风扇或压气机中的复杂流场,有效地提高设计精度,但这必须以高速大型电子计算机为前提条件。全三元计算又分无粘和有粘两类。无粘计算都采用解欧拉动量方程,有粘计算是直接求解N-S方程。
主动间隙控制
主动间隙控制是根据发动机的工作状态,人为地控制机匣或转子的膨胀量,使转子和静子的热响应达到较好的匹配,在高空巡航状态间隙尽可能小,而在其它状态又不致发生干扰摩擦。英国罗?罗公司的RB211发动机的叶尖间隙的主动控制是根据叶尖间隙传感器信号使封严环前后移动,将间隙保持在±0.25mm。美国GE公司为高效节能发动机E3的压气机设计的主动控制系统,是通过调节压气机后机匣上的第5级放气量来实现对第6级到第10级压气机的间隙控制。美国普?惠公司的PW4000发动机的高压压气机采用了"热效"转子(Thermoticsrotor),即在起飞和巡航过程中,将压气机第9级和第15级的空气引入转子内腔,以保持较小的径向间隙。
喘振是一种与系统相关的流动扰动现象。也就是说,整个压气机系统被包含在不稳定过程中,而不仅仅是压气机叶片排,即压气机发生失速,而系统发生喘振。喘振一般发生在发动机的非设计状态或发动机工作状态发生变化的过程中,尤其是发动机遇到恶劣的工作条件时,如飞机机动飞行引起进气道畸变,发动机吸进发射武器产生的废气等,都可能引发发动机喘振。喘振具有突发性,如处理不当,能在很短时间内损坏发动机,甚至导致严重后果。当发动机偏离设计状态时,压气机通道中气流受到扰动,压气机叶片会因气流冲角变大,叶背产生气流分离,分离较强时便损害这些叶片的工作性能而发生失速,当失速扩大到一定程度时,造成压气机流道的堵塞,压气机出口压力急剧下降,空气流量也随之下降甚至出现回流,燃烧室温度迅速超过允许值,在叶轮的不断旋转下,气流参数出现周期性低频脉动(频率在20Hz以下),通常还伴随有低沉的轰鸣声并能程度不同地观察到有火舌从喷口喷出,这是喘振的主要特征。