离心压气机设计方法综述--
燃气轮机离心压气机的设计与优化
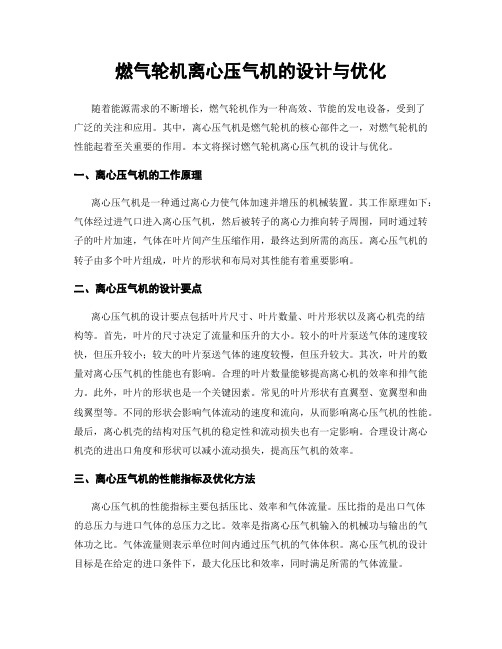
燃气轮机离心压气机的设计与优化随着能源需求的不断增长,燃气轮机作为一种高效、节能的发电设备,受到了广泛的关注和应用。
其中,离心压气机是燃气轮机的核心部件之一,对燃气轮机的性能起着至关重要的作用。
本文将探讨燃气轮机离心压气机的设计与优化。
一、离心压气机的工作原理离心压气机是一种通过离心力使气体加速并增压的机械装置。
其工作原理如下:气体经过进气口进入离心压气机,然后被转子的离心力推向转子周围,同时通过转子的叶片加速,气体在叶片间产生压缩作用,最终达到所需的高压。
离心压气机的转子由多个叶片组成,叶片的形状和布局对其性能有着重要影响。
二、离心压气机的设计要点离心压气机的设计要点包括叶片尺寸、叶片数量、叶片形状以及离心机壳的结构等。
首先,叶片的尺寸决定了流量和压升的大小。
较小的叶片泵送气体的速度较快,但压升较小;较大的叶片泵送气体的速度较慢,但压升较大。
其次,叶片的数量对离心压气机的性能也有影响。
合理的叶片数量能够提高离心机的效率和排气能力。
此外,叶片的形状也是一个关键因素。
常见的叶片形状有直翼型、宽翼型和曲线翼型等。
不同的形状会影响气体流动的速度和流向,从而影响离心压气机的性能。
最后,离心机壳的结构对压气机的稳定性和流动损失也有一定影响。
合理设计离心机壳的进出口角度和形状可以减小流动损失,提高压气机的效率。
三、离心压气机的性能指标及优化方法离心压气机的性能指标主要包括压比、效率和气体流量。
压比指的是出口气体的总压力与进口气体的总压力之比。
效率是指离心压气机输入的机械功与输出的气体功之比。
气体流量则表示单位时间内通过压气机的气体体积。
离心压气机的设计目标是在给定的进口条件下,最大化压比和效率,同时满足所需的气体流量。
离心压气机的优化方法主要有以下几种:首先,可以通过改变叶片的形状和布局来改善离心机的性能。
例如,采用曲线翼型叶片可以提高离心机的效率和压比。
其次,可以通过增加叶片数量和合理设置叶片的进出口角度来改善离心机的性能。
离心压缩机设计
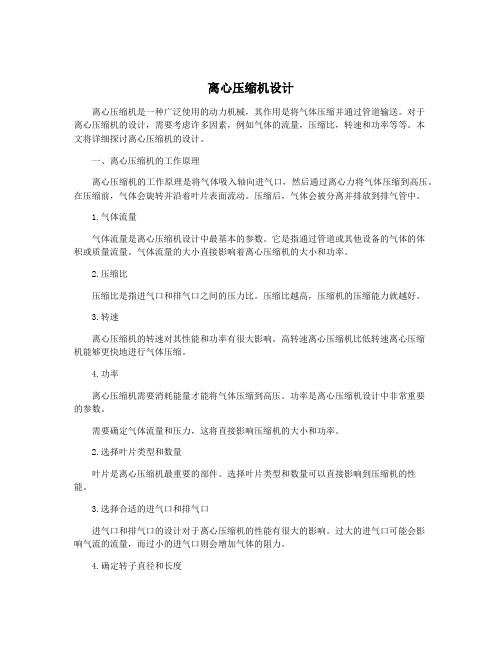
离心压缩机设计离心压缩机是一种广泛使用的动力机械,其作用是将气体压缩并通过管道输送。
对于离心压缩机的设计,需要考虑许多因素,例如气体的流量,压缩比,转速和功率等等。
本文将详细探讨离心压缩机的设计。
一、离心压缩机的工作原理离心压缩机的工作原理是将气体吸入轴向进气口,然后通过离心力将气体压缩到高压。
在压缩前,气体会旋转并沿着叶片表面流动。
压缩后,气体会被分离并排放到排气管中。
1.气体流量气体流量是离心压缩机设计中最基本的参数。
它是指通过管道或其他设备的气体的体积或质量流量。
气体流量的大小直接影响着离心压缩机的大小和功率。
2.压缩比压缩比是指进气口和排气口之间的压力比。
压缩比越高,压缩机的压缩能力就越好。
3.转速离心压缩机的转速对其性能和功率有很大影响。
高转速离心压缩机比低转速离心压缩机能够更快地进行气体压缩。
4.功率离心压缩机需要消耗能量才能将气体压缩到高压。
功率是离心压缩机设计中非常重要的参数。
需要确定气体流量和压力,这将直接影响压缩机的大小和功率。
2.选择叶片类型和数量叶片是离心压缩机最重要的部件。
选择叶片类型和数量可以直接影响到压缩机的性能。
3.选择合适的进气口和排气口进气口和排气口的设计对于离心压缩机的性能有很大的影响。
过大的进气口可能会影响气流的流量,而过小的进气口则会增加气体的阻力。
4.确定转子直径和长度转子直径和长度会直接影响到离心压缩机的大小和性能。
根据气体流量和压力确定适当的转子直径和长度。
5.选择适当的驱动方式离心压缩机的驱动方式可以是电机,蒸汽涡轮或燃气涡轮等。
需要根据工作条件和需求选择适当的驱动方式。
6.调整和优化设计设计完成后,需要进行调整和优化,以确保离心压缩机运行平稳,性能达到最优。
离心压缩机广泛应用于空气压缩机,制冷空调,涡轮增压器和火箭发动机等领域。
离心压缩机的优点是机械结构简单,性能稳定,可靠性高,并且能够满足各种气体的压缩需求。
离心压缩机设计涉及到许多参数和步骤。
离心压气机设计方法综述--

离心压气机设计方法综述压缩机是把原动机的机械能转变为气体能量的一种机械,分为容积式和透平式两种。
透平式压缩机是一种叶片式旋转机械,其中气体压力的提高是利用叶片和气体的相互作用来实现的,按照结构分为离心式压气机和轴流式压气机两种。
离心式压气机中气体压力的提高,是由于气体流经叶轮时,由于叶轮旋转,使气体受到离心力的作用而产生压力,与此同时气体获得速度,而气体流过叶轮,扩压器等扩张通道时,气体的流动速度又逐渐减慢从而使气体压力得到提高。
设计一台离心压气机包括多方面的内容,主要有:结构设计;通流部分的选择和计算;强度与振动计算;工艺设计;自动控制和调节;以及驱动型式等问题。
这里主要讨论前两项。
在离心压气机设计方法上,先后出现了几何设计方法,二维气动设计方法,准三维气动设计方法,全三维气动设计方法。
以这些方法为理论基础,建立了离心压气机计算机辅助集成设计系统。
这种设计系统的建立,为高性能离心压气机设计提供了有效工具。
最早用于离心压气机叶轮叶片的成形方法是几何成型方法,这是一种比较简单的成型方法。
国内增压器研究领域在50年代从前苏联引进的径向叶片的“双回转中心法”是几何成型方法中的代表,并在国内涡轮增压器领域得到广泛的应用。
该方法成型规律比较简单,使用该方法设计前倾后弯曲线不太可能。
于是产生了离心压气机叶轮的“骨架成型法”,这种方法可以弥补“双补转中心法”的不足。
但是,成型后弯叶片时,需要数控铣床。
早期设计离心压气机叶轮时,设计人员认为叶片型线是由二次曲线组成的,如使用圆弧线,抛物线等代表叶型、轮缘、轮毂型线形状。
使用二次曲线表示的叶片型线形状的一般表达式为f ez dr cz brz ar +++++=22222γθ式中,r 为半径,z 为叶轮轴向坐标,a,b,c,d,e,f 为系数。
系数决定叶轮进口角度和叶型型线。
Eckerdt 即采用上式设计了Eckerdt 叶轮。
Whitfield 等人认为叶轮型线可由下式表示:(){}(){}1//=+++f e d e z b a ϕ式中,ϕ既可代表半径r 也可代表周向角度θ。
离心压气机理论-第一部分-2010
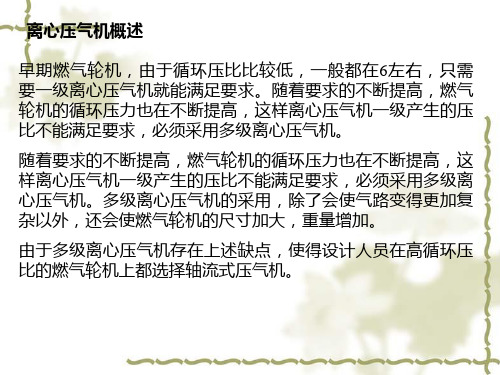
离心压气机基本理论
离心压气机叶轮可分为带叶冠叶轮和不带叶冠叶轮两种两种, 前者又叫闭式叶轮,后者又叫开式叶轮。图2和图3给出了这两 种叶轮形式。
图2 不带叶冠叶轮
图3 带叶冠叶轮
离心压气机基本理论
燃气轮机和涡轮增压器由于转速很高,通常使用开式叶轮。因 为增加叶冠会增加叶轮质量,使转子惯性增加,从而导致整机 性能恶化。
5级轴流+1级离心 5.30
3级轴流+1级离心 5.73
1级离心
1.60
2级离心
3.2-3.4
4级轴流+1级离心 4.2
2级离心
4.0
总增压比 17.00 14.72 8.0-8.30 13.14 14.38 15.00
为什么采用离心压气机? 因为单级压比大,由于流量小,可以保证出口端压气机末级叶 片高度在合适的范围内,不会过小。
离心压气机概述
涡轮增压器是径流式叶轮机械应用的最为广泛的一个领域。 如果说燃气轮机是改进叶轮机械设计和制造技术的驱动力,那 么涡轮增压技术和涡轮增压器的广泛使用为径流式叶轮机械的 发展提供了广阔的市场。
废气涡轮增压的设想首先由瑞士人波希在1905年提出,当时获 得了德国和美国的专利。 1911年波希在单缸机上首次完成涡轮增压的台架试验。 1925年,波希又提出了脉冲增压的设想。 到1940年代,涡轮增压在船用和陆用大型发动机上得到了大量 推广使用。 直到1950年,涡轮增压器才在大型柴油机上得到广泛使用。
16 PWC
14
Байду номын сангаас
PWC
12
10
PWC&Boeing
PWC209
&319
离心式压气机的原理与设计(1)
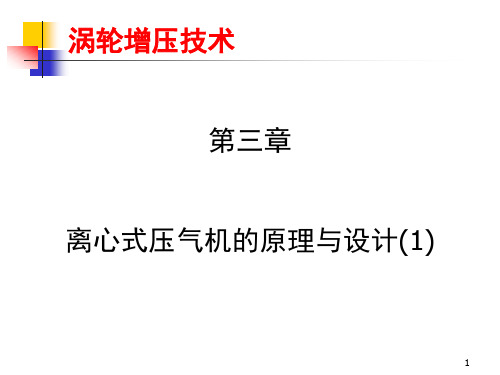
n1 n1 −1
ξin为损失系数,可取 0.05 ~ 0.10
23
空气在进口段中的流动
---进口气流角 ---进口气流角
以叶轮旋转轴为中心轴, 作圆柱面切割叶轮,然后 展开,可以得到如左所示 的叶轮进口处的速度三角 形的图。 叶片安装角βg1,30-35° 进口气流角β1 气流冲角i,3-5° i=βg1- β1
---叶轮的结构(1) ---叶轮的结构(1) 叶轮的结构
铸造叶轮毛坯, 带长短叶片
26
空气在叶轮内的流动
---叶轮的结构(2) ---叶轮的结构(2) 叶轮的结构
五轴铣床铣削叶轮,一般用于大直径的叶轮制造
27
空气在叶轮内的流动
---叶轮的结构(3) ---叶轮的结构(3) 叶轮的结构
叶轮平衡去重位置
28
空气在叶轮内的流动
---导风轮与工作叶轮 ---导风轮与工作叶轮
离心式压气机叶轮由导风轮和工作叶轮两部分 组成。导风轮将流入气体由轴向转为径向;工 作叶轮使气体由内向外作径向流动。通常将直 径方向尺寸基本不变的一段叫做导风轮。 车辆用增压器由于压气机叶轮小型化及采用精 密铸造工艺,而将导风轮和工作叶轮铸成一个 整体,并统称压气机叶轮。
n k Wr = − n − 1 k − 1 R T4* − T1*
(
)
(3-6)
20
空气在进口段中的流动
---进口的形式(1) ---进口的形式(1) 进口的形式
车辆用增压器的进口型式一般为圆锥形或圆柱形,图 3-6(a)。极少部分的进口采用预扭叶片,以扩大压气 机的流量范围。
21
空气在进口段中的流动
前弯叶片,工作叶轮可将较多的能量传递给空气, 但是,这部分多出来的能量是以增加叶轮出口处的 气流速度的方式,即增加动能的方式传递给空气, 因而必须经过叶轮之后的扩压段,和涡壳通道才能 转变为气体的压力能。由于扩压段及涡壳中的效率 较低,这种形式的叶轮降低了压气机的级效率。 目前用的极少。
离心式压气机任意型叶型设计方法

离心式压气机任意型叶型设计方法
任柏森
【期刊名称】《内燃机学报》
【年(卷),期】1992(010)001
【总页数】8页(P69-76)
【作者】任柏森
【作者单位】无
【正文语种】中文
【中图分类】TK474.8
【相关文献】
1.低雷诺数下二维扩压叶型设计方法研究 [J], 张乃昌;侯安平
2.基于目标压力分布的压气机叶型黏性反问题设计方法 [J], 张小玉;耿少娟;张宏武
3.某型轴流压气机高压第16级叶型气动特性的试验研究 [J], 张宇; 韩万金
4.径流及斜流压气机任意曲面叶型长短叶片的造型设计方法 [J], 王琦;单鹏
5.轴流压气机超音叶片叶型几何设计方法的研究 [J], 肖敏;刘波;仲永兴
因版权原因,仅展示原文概要,查看原文内容请购买。
离心压气机设计
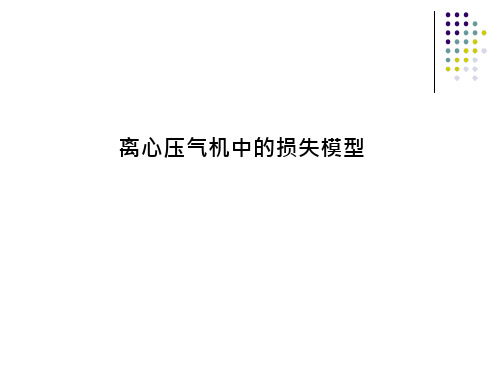
离心压气机内损失特点
根据上面的分析得出的结论,在叶轮旋转速度和焓变相同情况 下,径流式叶轮机械相对速度的变化小于相应轴流式叶轮机械 相对速度的变化。
由这样的结论我们或许推断出径流式叶轮机械比相应的轴流式 叶轮机械的效率更高一些,而实际上径流式叶轮机械的效率更 低一些。
这种矛盾主要是由于径流式叶轮机械通道形状比较复杂造成的, 工质在径流式叶轮机械内部流动时要流过90 弯曲通道,其哥氏 力的方向近似沿周向方向(轴流式叶轮机械哥氏力方向近似沿径 向),这就产生比轴流式叶轮机械中更加强烈的二次流动。
各种损失模型 离心压气机内主要损失:叶型损失、端壁损失、泄漏损失 在很多情况下,这三种损失大小基本相当,每一种损失大约占总损失的三分之一。
叶片表面摩擦损失 叶片载荷损失
叶片尾迹混合损失 轮盘摩擦损失
有叶扩压器内损失 扩压器出口损失 泄漏损失
初步设计中的性能分析
初步设计最开始是以设计点进行的,必须要使用分析模式对非 设计点的性能进行预测。因此需要使用分析程序获得压气机的 性能。
叶片剖面的设计
使用Bezier曲线可以对叶片形状进行描述,这种方法非常灵活。 通过端点的相邻点就可以对端点处的斜率进行控制。在一个交 互性较好的系统上可以非常容易地确定轮缘和轮毂形状以及叶 片形状。
叶片中线上环量rC 分布方式分析
rC 沿s分布规律可以有多种形式,它可以是线性变化,也可以 是非线性变化;可以是单段曲线,也可以是分段曲线。对于非 线性变化,可以为二次曲线分布,也可以为三次曲线分布。
叶片设计
叶轮叶片设计过程中包含一系列气动上的选择和避免出现一些问 题,包括:
• 对叶片角在子午面上的分布进行选择 • 对叶片通道内平均相对马赫数的分布进行选择 • 设计的叶轮要满足轮毂轮缘处所要求的气动载荷 • 避免叶片槽道内出现局部气动分离,尤其要尽量避免轮缘处出
第二章 离心式压气机的原理与设计
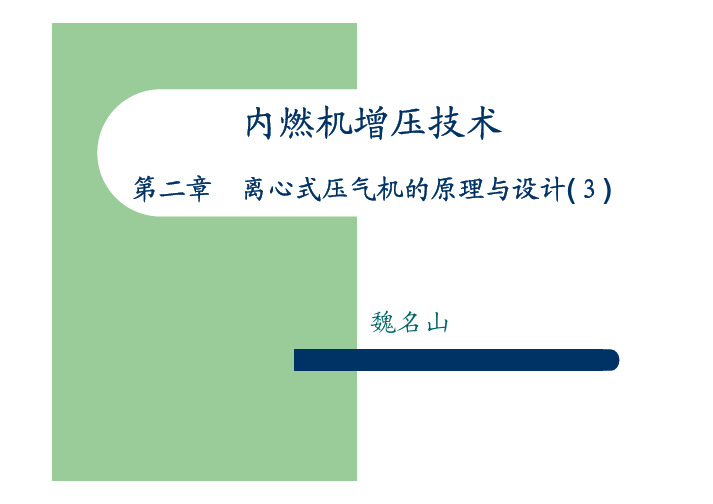
内燃机增压技术第二章离心式压气机的原理与设计(3)魏名山第二章离心式压气机的原理与设计(3)z集气器(涡壳)z离心式压气机计算示例z压气机特性集气器---形状(2)集气器---形状(3)z涡壳截面的形状可以有很多种,以梨形的损失最小,但各种形状相差不大,所以在设计时更多地是考虑尺寸上的小型化。
近年来逐渐多采用的鸭蛋形截面涡壳能得到最小的外形尺寸。
集气器---流道计算(4)z将某一个确定的R H值代入上式,就可以求出一个对应的φ值。
如此变更不同的R值,就H可得到相应的不同的φ值。
将一系列φ值与它对应的R值制成表格或曲线后,再反过来由H表格或曲线用插值法,求出各所需的指定整数φ值及对应的R值。
离心式压气机计算示例---命题z 试为6150柴油机设计一台废气涡轮增压器。
增压前发动机的功率N e =184kW ,转速为2000RPM ,比油耗g e 为250g/kWh ,机械效率ηM =0.75。
增压后功率要求提高100%,环境压力P 0=98066.5Pa ,环境温度T 0=303K 。
离心式压气机计算示例---某些系数的选取z选定发动机的充气系数z过量空气系数z 扫气系数05.17.19.0===H H v H ϕαη离心式压气机计算示例---功率z 增压后发动机的功率N eHkW368%)1001(=+=e e N N H离心式压气机计算示例(1)z压气机具体的结构尺寸,可按照王延生、黄佑生著《车辆发动机废气涡轮增压》或朱大鑫著《涡轮增压与涡轮增压器》上所列的表格进行计算。
z其基本思路为:根据前述发动机计算,算出压比、流量后,按经验值假设压气机叶轮的出口直径,和压气机的绝热效率。
同时对计算过程中所涉及到的一些系数如各处的流动损失系数设值。
离心式压气机计算示例(2)z根据压比算出压气机绝热功,根据压气机绝热功和压头系数算出叶轮出口圆周速度,然后算出叶轮旋转速度。
z根据流量算进口面积和进口直径。
z然后根据前述的计算公式,从进口开始算到出口。
- 1、下载文档前请自行甄别文档内容的完整性,平台不提供额外的编辑、内容补充、找答案等附加服务。
- 2、"仅部分预览"的文档,不可在线预览部分如存在完整性等问题,可反馈申请退款(可完整预览的文档不适用该条件!)。
- 3、如文档侵犯您的权益,请联系客服反馈,我们会尽快为您处理(人工客服工作时间:9:00-18:30)。
离心压气机设计方法综述压缩机是把原动机的机械能转变为气体能量的一种机械,分为容积式和透平式两种。
透平式压缩机是一种叶片式旋转机械,其中气体压力的提高是利用叶片和气体的相互作用来实现的,按照结构分为离心式压气机和轴流式压气机两种。
离心式压气机中气体压力的提高,是由于气体流经叶轮时,由于叶轮旋转,使气体受到离心力的作用而产生压力,与此同时气体获得速度,而气体流过叶轮,扩压器等扩张通道时,气体的流动速度又逐渐减慢从而使气体压力得到提高。
设计一台离心压气机包括多方面的内容,主要有:结构设计;通流部分的选择和计算;强度与振动计算;工艺设计;自动控制和调节;以及驱动型式等问题。
这里主要讨论前两项。
在离心压气机设计方法上,先后出现了几何设计方法,二维气动设计方法,准三维气动设计方法,全三维气动设计方法。
以这些方法为理论基础,建立了离心压气机计算机辅助集成设计系统。
这种设计系统的建立,为高性能离心压气机设计提供了有效工具。
最早用于离心压气机叶轮叶片的成形方法是几何成型方法,这是一种比较简单的成型方法。
国内增压器研究领域在50年代从前苏联引进的径向叶片的“双回转中心法”是几何成型方法中的代表,并在国内涡轮增压器领域得到广泛的应用。
该方法成型规律比较简单,使用该方法设计前倾后弯曲线不太可能。
于是产生了离心压气机叶轮的“骨架成型法”,这种方法可以弥补“双补转中心法”的不足。
但是,成型后弯叶片时,需要数控铣床。
早期设计离心压气机叶轮时,设计人员认为叶片型线是由二次曲线组成的,如使用圆弧线,抛物线等代表叶型、轮缘、轮毂型线形状。
使用二次曲线表示的叶片型线形状的一般表达式为f ez dr cz brz ar +++++=22222γθ式中,r 为半径,z 为叶轮轴向坐标,a,b,c,d,e,f 为系数。
系数决定叶轮进口角度和叶型型线。
Eckerdt 即采用上式设计了Eckerdt 叶轮。
Whitfield 等人认为叶轮型线可由下式表示:(){}(){}1//=+++f e d e z b a ϕ式中,ϕ既可代表半径r 也可代表周向角度θ。
Krain 提出了一个更为复杂的表达式来定义离心压气机叶片型线。
随着设计、制造技术的进步,离心压气机几何设计中广泛采用的一种成型方法是Bezier 多项式法。
对于离心压气机叶轮的几何成型方法,由于在叶片成型过程中没有考虑叶片表面上载荷分布等气动问题,不可避免的会对离心压气机的性能产生一定的影响。
使用这种方法很难设计出高性能的离心压气机。
随着设计人员研究的深入及技术上的进步,离心压气机几何成型方法正逐步被气动成型方法所代替,并相继出现了二维气动设计方法,准三维气动设计方法和全三维气动设计方法。
和轴流式叶轮机械相比,径流式叶轮机械的气动设计方法更为成熟。
国外很多叶轮机械研究机构已经对离心压气机气动设计研究了几十年,推出了离心压气机计算机辅助集成设计系统。
目前设计的离心压气机大部分是借助种工具完成的。
离心压气机的设计主要是叶轮叶片设计,叶轮叶片设计中不可缺少的两个步骤是叶轮初步设计和详细设计。
离心压气机设计系统一般应包括初步设计及性能优化计算,性能仿真数学模型,叶片成型计算,叶轮应力分析计算。
各部分的具体功能如下。
一.离心压气机叶轮初步设计及优化部分:采用优化方法获得叶轮主要性能参数及主要几何尺寸,性能参数主要有叶轮进出口速度、进出口气流角、叶轮旋转速度、压气机效率等;结构参数有进口轮毂、轮毂大小、叶轮轴向长度、叶轮直径大小等。
二.离心压气机性能仿真部分:使用完善的损失模型对离心压气机在设计工况和非设计工况下的性能进行模拟三.离心压气机叶片成型:根据给定的叶片在轮缘、轮毂、中间流线上的载荷分布规律计算叶片在这几个位置上的叶型角β、周向角θ,通过迭代计算获得叶片叶型坐标。
四.叶轮内部流场流动分析:对成型的叶轮内部流场进行计算,根据计算结果判定吸力面和压力面上的速度分布和压力分布是否合理。
五.离心压气机叶轮应力分析:采用有限元方法计算所设计叶轮的应力分布,进行振动分析。
六.3D结构模型:确定叶轮几何形状和尺寸,进口端部几何形状和尺寸。
对离心压气机叶轮计算机辅助集成设计系统的基本要求是有良好用户界面的交互式图像系统。
这一系统应易于使用,易于掌握,并且有很好的前处理和后处理程序。
计算输入数据最好在图形界面上以填空方式完成。
这样做的好处是非常直观,设计人员知道输入数据之间的几何关系。
这种方法利于设计人员对设计系统的正确使用,进而提高工作效率。
计算获得的叶轮几何数据应输入到图形处理软件中,使用这一软件完成叶轮的三维造型。
后处理程序中一个很重要的功能是尽可能多的提供各个参数的计算曲线,设计人员通过这些曲线判定叶轮是否满足设计要求。
如设计人员可以根据这些曲线判断叶片表面压力分布是否合理,速度分布是否有突越现象等。
同时,一个好的集成系统还应具有交互性功能。
设计人员可以通过改变一些参数分布来改变叶片形状,如通过改变输出的叶片叶型角β分布曲线或叶片周向角θ分布曲线,使系统重新设计叶片形状,从而获得新叶轮并输出新叶轮的计算结果。
一个集成系统还应具有项目管理功能,这一过程要尽可能的减少设计人员的工作,它应该具有自动地为一个项目的输入输出文件命名的功能。
对于任意一条曲线,设计人员通过鼠标按图形界面上的存储键,即可生成这条曲线的存储文件,供以后设计时参考。
一些离心压气机叶轮计算机辅助集成设计系统已经在实际中得到应用,比较有代表性的有Bruce和Masme介绍的集成系统和Nojima等人介绍的设计系统。
这个系统的结构如下图1所示。
使用这一集成系统,Nojima等人设计出一系列高性能离心压气机,其设计性能已经得到实验验证。
有实例如下所述,使用上文介绍的离心压气机叶轮计算机辅助集成设计系统设计一个离心压气机叶轮。
这个叶轮设计参数如下:质量流量为19kg/s,叶轮转m/s,速为10000 r/min,入口旋度为零,出口旋度为1782m/s,另一出口旋度为1832入口滞止压力为98 kPa,入口滞止温度为303 K,叶片数目为15,叶片前缘倾角30,给定叶片轮缘、轮毂型线形状。
计算中使用40个直为零,叶片尾缘倾角为线元定义叶片中型面形状,每次设计计算中规定对流线位置计算的迭代次数最大为20次,规定在叶片弦长65% 处出现滑移现象。
最终获得的叶轮主要尺寸是入口轮缘直径为0.542 m ,入口轮毂直径为0.26 m ,叶轮直径为0.976 m ,设计效率为0.82,设计压比为2.8。
图 2 和图 3 分别是吸力面和压力面上的相对速度分布等值线图的计算结果。
从图 2 吸力面上相对速度的计算结果可以发现轮缘处相对速度均大于相同位置上轮毂处速度,未发现叶轮出口会出现“射流-尾迹”流动现象,这主要是由于采用的流场计算方法比较粗糙所造成的。
这种流场计算方法无法获得真实的叶轮槽道内流动现象,这是今后应该改进的。
图 4 在叶片出口分别为前倾() 30不倾() 0和后倾() 30-三种情况下,保持轮缘型线不变,改变轮毂型线位置情况下叶轮叶片中型面的设计结果,以这种方式设计的叶轮可以更容易比较叶轮载荷分布的变化情况。
图5 和图6 分别给出了三种叶片出口倾角下叶片在轮缘和轮毂处速度分布的计算结果,从图中可以看出,叶片表面速度分布变化不大,叶片在轮缘轮毂处的载荷分布基本相同。
上述结论还有待于进一步进行大量的计算进行验证。
径流式叶轮机械设计的全三维反问题设计方法在最近的十年里,径流式叶轮机械全三维反问题设计方法取得了飞速的发展,相继有一些学者发表文章论述这个问题。
他们采用规定叶片表面环量rC分布方法。
这一方法的大致过程是:在叶片表面各个点的环量获得后,流体速度被分解为平均速度(按叶片节距平均,下同)和周期速度,这样可采用Stokes 流函数方法求得轴向和径向平均速度,三个方向上的周期速度采用Clebsch公式计算。
开始计算叶片型线前,除了规定叶片环量分布外,还规定轮缘、轮毂型线形状,叶片数目,叶片前缘和叶片尾缘坐标,叶片叠加位置,叶片旋转速度等参数,叶片型线通过迭代计算完成。
第一次迭代计算前首先给定初始叶片形状,接着计算流场,根据计算的流场重新计算叶片型线。
这个过程一直进行下去,直至获得收敛的计算结果。
最后的计算结果不仅给出了叶片形状,而且还规除了叶片表面压力分布和整个内部流场速度分布。
最早提出这种方法的人是Tan等。
他们使用这种方法设计了不可压流动情况下的环型叶栅,设计过程中认为叶片为无限薄。
计算过程中依靠光滑特征函数方法把三个方向上的流场变量进行展开,其中径向采用Bessel函数,切向使用Fourier级数,轴向使用Chebyshev多项式。
随后,Dang和Mccune把这种方法用于有限厚度叶片设计。
Borges进一步发展了这种方法并成功设计了一台低速径流涡轮,计算中采用二阶精度差分格式和多重网格技术。
通过对采用环量分布方法设计的径流涡轮和原有涡轮的性能进行了对比,发现新叶轮的性能在大部分工作范围内都优于原始叶轮。
Ghaly、Yang、Zangeneh和Hawthorne把环量分布方法用于高速径流式涡轮的设计。
设计结果表明,新叶轮的性能均明显好于旧叶轮的性能。
上述设计中都没有考虑粘性影响,而在设计离心压气机叶轮时,应尽量考虑粘性影响。
Zangeneh使用有粘-无粘迭代方法设计了一台离心压气机叶轮,为了考虑粘性影响,在设计过程中引入了一个漩涡强度分量代表熵增影响。
Zangeneh和GoTo等人还发展了一种抑制叶轮内部二次流动的设计方法,他们把这种方法用于一个混流泵叶轮的设计。
从试验结果和计算结果来看,他们设计的叶轮有效地减弱了叶轮槽道内二次流动现象,也即减轻了叶轮出口“射流-尾迹”流动现象。
后来Zangeneh把这一方法用于离心泵的设计。
使用全三维反问题方法设计径流式叶轮机械的还有Yiu和Zangeneh,把优化设计方法用于高速离心压气机叶轮的反设计中,Zangeneh和Tjohroaminata分别对带有分流叶片的离心压气机和向心涡轮的设计方法进行了研究。
由以上叙述可以看出,癸巳能够叶片表面环量分布是径流式叶轮机械三维反设计中的一种有效方法。
这种方法比较直观,因为环量分布决定叶片加功量分布。
通过规定环量分布设计叶片的做法是比较合理的。
英国剑桥大学和美国麻省理工学院以及两校培养的博士在径流式叶轮机械设计方面的研究居于国际领先地位。
目前,离心压气机叶轮设计已经发展到了一个很高水平,如有的离心压气机叶轮绝热效率高达95% 。
但决定离心压气机效率高低的因素绝不仅仅只是叶轮一个因素,而是由很多因素。
这些因素包括扩压器、涡壳等。
因此,要想进一步改善离心压气机性能,除了要改进离心压气机叶轮设计方法外,还要进一步改善与压气机性能密切相关的一些部件的设计方法。