基于MATLAB的塑料模具浇注系统的优化设计-
基于MATLAB的塑料模具浇注系统的优化设计
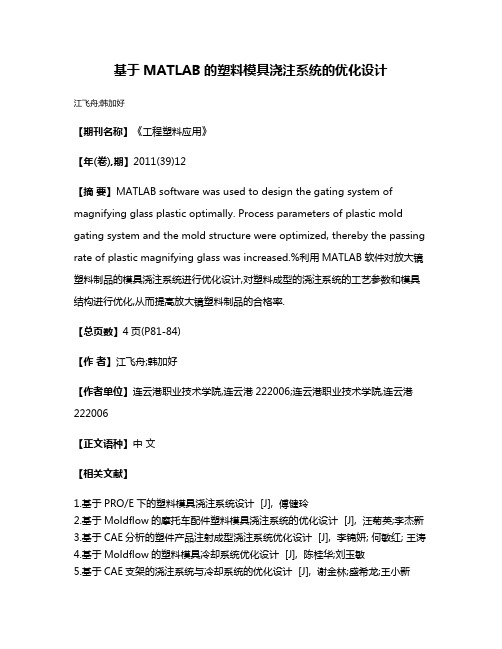
基于MATLAB的塑料模具浇注系统的优化设计
江飞舟;韩加好
【期刊名称】《工程塑料应用》
【年(卷),期】2011(39)12
【摘要】MATLAB software was used to design the gating system of magnifying glass plastic optimally. Process parameters of plastic mold gating system and the mold structure were optimized, thereby the passing rate of plastic magnifying glass was increased.%利用MATLAB软件对放大镜塑料制品的模具浇注系统进行优化设计,对塑料成型的浇注系统的工艺参数和模具结构进行优化,从而提高放大镜塑料制品的合格率.
【总页数】4页(P81-84)
【作者】江飞舟;韩加好
【作者单位】连云港职业技术学院,连云港222006;连云港职业技术学院,连云港222006
【正文语种】中文
【相关文献】
1.基于PRO/E下的塑料模具浇注系统设计 [J], 傅健玲
2.基于Moldflow的摩托车配件塑料模具浇注系统的优化设计 [J], 汪菊英;李杰新
3.基于CAE分析的塑件产品注射成型浇注系统优化设计 [J], 李锦妍; 何敏红; 王涛
4.基于Moldflow的塑料模具冷却系统优化设计 [J], 陈桂华;刘玉敏
5.基于CAE支架的浇注系统与冷却系统的优化设计 [J], 谢金林;盛希龙;王小新
因版权原因,仅展示原文概要,查看原文内容请购买。
塑料注射模具浇注系统的优化设计

文献 标 识 码 :A
文 章 编 号 :1 0 0 5—5 7 7 0( 2 0 1 3 )1 1 — 0 0 4 0— 0 5
Op t i ma l D e s i g n o f P l a s t i c I n j e c t i o n Mo u l d Ga t i n g S y s t e m
注射成 型 是 塑 料 制 品 生 产 中 的一 种 重 要 加 _ 丁方 法 ,世界上 注 射 模 的产 量 占塑 料 成 型模 具 总 产 量 的 5 0 % 以上 。传统 的塑料 注射模 设计 主要 是靠经 验 、直 觉或 反复试 模来 进行 ,很难 得 到较佳 的 工艺参数 ,甚 至有 些模具 由于难 以确定改 进方 法 ,在 试模 、修 模过 程 中变 成 了废 品 ,造 成 了 很 大 浪 费 。利 用 注 射 模
p r o g r a m S i f l l i n g t i m e ,t e mp e r a t u r e ,s h e a r i n g r a t e ,me l t i n g w i r i n g a n d a i r p o c k e t ,i n j e c t i n g p r e s s u r e a n d t h e
di s t r i b u t i o n ma p o f l o c ki n g s t r e n g t h. Th r o u g h c o mpa r i ng a n d a na l y z i n g, t h e r e l a t i v e l y g o o d p r o g r a m wa s
s i mu l a t i o n a n d a n a l y s i s o f t h e f il l i n g mo u l d p r o c e s s f o r t h r e e gn p r o g r a ms, i t g o t e a c h
基于PRO/E下的塑料模具浇注系统设计
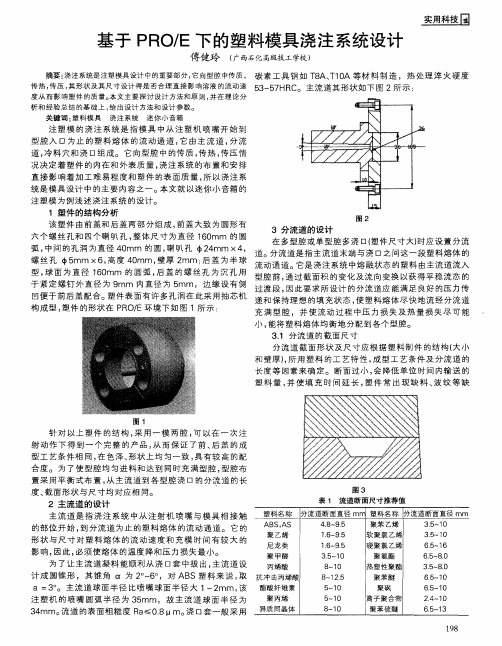
表 1 流 道 断 面 尺 寸 推荐 值
塑 料名 称 分流 道 断 面直 径 mm 塑 料名 称 分流道 断 面 直径 mm AB S, AS 4 . 8 ~ 9 . 5 聚 苯 乙烯 3 与一 1 O
聚 乙烯
尼 龙类
聚 甲醛
1 . 6 N 9 . 5
1 . 6 ~ 9 . 5
3 . 5 ~1 O
软 聚 氯 乙烯
硬 聚氯 乙烯
聚氨 酯
3 5 ~1 0
6 . 5 ~1 6
6 . 5 ~8 . 0
丙 烯 酸
8 ~ 1 O
8 ~ 1 2 与
计成 圆锥 形 ,其 锥 角 o c为 2 。 ~ 6 。 ,对 AB S塑 料来 说 , 取 抗 冲 击 丙烯 酸 a=3 。 。主 流 道球 面半 径 比喷嘴 球面 半径 大 1—2 mm , 该 醋酸 纤 维 素 聚 丙 烯 注 塑机 的喷 嘴 圆 弧半 径 为 3 5 a m,故主 流 道 球 面 半 径 为 r 异质 同晶体 3 4 mm。 流道 的表 面粗 糙度 R a ≤O . 8 L l m。 浇 口套一般 采 用
ห้องสมุดไป่ตู้
注 塑模 的浇 注 系统 是 指 模 具 中从 注 塑机 喷嘴 开 始 到 型腔 入 口为 止 的 塑料 熔 体 的流 动 通 道 , 它 由主 流 道 , 分 流 道, 冷 料 穴和 浇 口组 成。 它向型腔 中 的传 质 , 传热 , 传 压 情 况决 定着 塑件 的 内在 和 外表 质量 , 浇注 系统 的布 置和 安 排 直接 影 响着加 工难 易程 度和 塑件 的表面 质量 , 所 以浇注 系 统 是模 具 设计 中 的主要 内容 之一 。 本 文就 以迷你 小 音箱 的 注 塑模 为例浅 述浇 注系 统 的设计 。 1塑 件 的结构 分析 该塑 件 由前 盖和 后 盖两 部 分组 成 , 前 盖 大致 为 圆形 有 六个 螺丝 孔和 四个 喇叭 孔 , 整体 尺 寸 为直 径 1 6 O mm 的 圆 弧, 中 间的孔 洞 为直 径 4 0 mm 的 圆 , 喇 叭 孔 2 4 mm ×4,
基于cae分析的塑件产品注射成型浇注系统优化设计
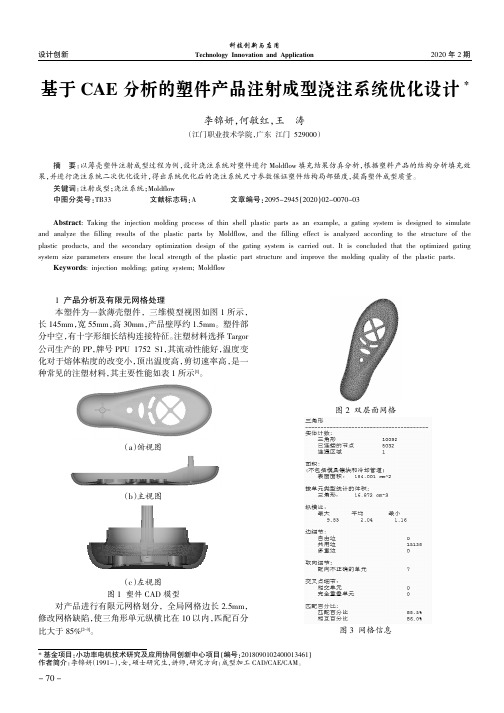
2020年2期设计创新科技创新与应用Technology Innovation andApplication基于CAE 分析的塑件产品注射成型浇注系统优化设计*李锦妍,何敏红,王涛(江门职业技术学院,广东江门529000)1产品分析及有限元网格处理本塑件为一款薄壳塑件,三维模型视图如图1所示,长145mm ,宽55mm ,高30mm ,产品壁厚约1.5mm 。
塑件部分中空,有十字形细长结构连接特征。
注塑材料选择Targor 公司生产的PP ,牌号PPU 1752S1,其流动性能好,温度变化对于熔体粘度的改变小,顶出温度高,剪切速率高,是一种常见的注塑材料,其主要性能如表1所示[1]。
(a )俯视图(b )主视图(c )左视图图1塑件CAD 模型对产品进行有限元网格划分,全局网格边长2.5mm ,修改网格缺陷,使三角形单元纵横比在10以内,匹配百分比大于85%[2-3]。
图2双层面网格图3网格信息摘要:以薄壳塑件注射成型过程为例,设计浇注系统对塑件进行Moldflow 填充结果仿真分析,根据塑料产品的结构分析填充效果,并进行浇注系统二次优化设计,得出系统优化后的浇注系统尺寸参数保证塑件结构局部强度,提高塑件成型质量。
关键词:注射成型;浇注系统;Moldflow中图分类号:TB33文献标志码:A文章编号:2095-2945(2020)02-0070-03Abstract :Taking the injection molding process of thin shell plastic parts as an example,a gating system is designed to simulateand analyze the filling results of the plastic parts by Moldflow,and the filling effect is analyzed according to the structure of the plastic products,and the secondary optimization design of the gating system is carried out.It is concluded that the optimized gating system size parameters ensure the local strength of the plastic part structure and improve the molding quality of the plastic parts.Keywords :injection molding;gating system;Moldflow*基金项目:小功率电机技术研究及应用协同创新中心项目(编号:2018090102400013461)作者简介:李锦妍(1991-),女,硕士研究生,讲师,研究方向:成型加工CAD/CAE/CAM。
基于CAE技术的注塑模浇口优化设计

第25卷第6期2004年11月 江苏大学学报(自然科学版)Journal of Jiangsu University(Natural Science Edition) V ol.25N o.6N ov.2004基于CAE技术的注塑模浇口优化设计袁国定1,胡曙光2,韩阳飞1,俞春明1(1.江苏大学机械工程学院,江苏镇江212013;2.江苏大学京江学院,江苏镇江212013)摘要:注塑模浇口位置的设定是塑料注塑成型模具设计中的关键技术之一,决定了聚合物流动方向和流动平衡性,通过浇口位置的优化可以显著提高产品的质量.基于C AE技术,利用M old flow软件对塑料制件在注塑成型中浇口位置和数量的选择进行分析,对不同浇口位置进行流动模拟分析,预测可能存在的气泡位置和熔接痕的位置,以确定最佳浇口位置和数量,可避免在模具上进行试模、修模的繁琐过程,从而为模具设计人员优化模具设计提供依据.关键词:注塑模;最佳浇口位置;C AE;模拟分析中图分类号:T Q320 文献标识码:A 文章编号:1671-7775(2004)06-0477-05Design of gate position for plastic injection moldingby CAE techniqueYUAN Guo2ding1,HU Shu2guang2,H AN Yang2fei1,YU Chun2ming1 (1.School of M echanical Engineering,Jiangsu University,Zhenjiang,Jiangsu212013,China;2.Jingjiang C ollege,Jiangsu University,Zhenjiang,Jiangsu212013,China)Abstract:G ate location analysis is the key technology in injection m olding.Flow direction and balanced flow of polymer depend on gate location whose optimization can prom ote product quality.G ate location and number of plastic parts in the injection m olding were analyzed with C AE s oftware M old flow.The location of air traps and weld lines were predicted by simulation of fillings from different gates to decide the optimum gate location.It can av oid the traditional repeated adjustment and die repairing,thus providing foundations for designing op2 timum m old.K ey w ords:injection m ould;optimum injection location;C AE;simulation analysis 传统的注塑模设计和制造很大程度上依赖于设计者的经验和制造工人的技巧,设计的正确性只有通过试模才能知道,制造的缺陷主要靠修模来纠正,有时还可能导致整套模具的报废,特别是对复杂的中高档模具,问题更为突出.C AE(C om puter Aided Engineering)技术采用有限元计算方法,根据高分子流变学和传热学的基本理论,建立塑料熔体在模具型腔中的流动、传热的物理数学模型,利用数值分析工具来分析和预测生产中注塑产品和注塑工艺可能存在的问题,定量地给出成型过程的状态参数,及时判断如何修改制件的形状以获得较理想的状态,避免了在模具上进行试模、修模的繁琐过程.作者基于C AE技术,利用M old flow/MPI分析软件,对某数码相机的前盖和手机的前面壳体注塑成型中浇口位置和数量进行选择.对不同浇口位置进行流动模拟分析,预测可能存在的气泡位置和熔接痕的位置,确定最佳浇口位置和数量,从而为模具设计人员进行模具设计提供科学的依据.收稿日期:2004-02-16基金项目:镇江市产学研基金资助项目(2002152)作者简介:袁国定(1948-),女,江苏南通人,副教授(ygd@),主要从事模具CAD/CAE/CAM一体化制造的研究.1 注塑过程的数字描述基于C AE技术进行注塑模设计时,应充分了解塑料熔体在流道和型腔中的流动、传热情况,并进行定量计算,求得压力、温度、剪应变力及冷却时间等参数.通过数学模型,求得各参数,从而预测流动特点、温度分布、冷却时间、锁模力大小等.注塑过程的数字描述是注塑成型分析和优化设计的理论基础.塑料熔体充填过程被认为是粘性非等温不可压缩流动与传热过程,可采用粘性不可压缩流动的基本方程来描述.鉴于大多数塑料制件都是薄壁件,故可以认为熔体是在扁平型腔内流动,并引入一些假设和简化,在此基础上,根据连续介质力学和热力学理论,可得到充填过程的数学模型.(1)连续性方程5u 5t+5(bv)5γ=0(1)式中u、v为x、y方向的平均速度.(2)动量方程5P 5x-55zη5u5z=0(2)5P 5y-55zη5v5z=0(3)式中P为熔体的压力.(3)能量方程 ρc p 5T5t+u5T5x+v5T5y=k52T5z2+ηγ2(4)式中,ρ为密度;c p为比热容;k为传热系数;T为熔体的温度.(4)粘度模型根据计算精度和计算时间等方面的不同需要,可以选择幂律型或者CROSS粘度模型.CROSS粘度模型中,粘度对温度和压力的依赖性,间接地通过零剪切度η0来表示,η0有两种形式,分别为5参数的EXP模型和7参数的W LF模型.(5)边界条件5u5z=5v5z=05T5z=0(5)z=0 u=v=0 T=T w z=±b 式中T w为薄壁温度;b为型腔半厚.在流动前沿C m(t)上 P=0在型腔边界C0和型芯C i边界上 P=0 5P5n=0在熔体入口处 T=T e式中T e为熔体入口温度.2 CAE在模具浇口优化设计中应用浇口是熔体流进型腔的最后通道,对于制件的质量影响很大.浇口在流道中的断面积最小,长度最短,起着控制熔体流速、保压补缩、使熔体温度升高、粘度下降、熔体变稀等的作用.浇口的设计主要包括浇口的数目、位置、形状和尺寸.浇口的数目和位置主要影响浇口的充填模式;而浇口的形状与尺寸决定了聚合物流动方向和平衡.当流动不平衡时容易造成不均匀的收缩和翘曲变形,影响气泡和熔接痕的位置,并影响内应力的取向和制件的质量;不适当的浇口位置常造成型腔内的气体在注塑成形过程中无法逃逸,造成短射、气穴、烧焦痕迹等注塑缺陷.为得到最合适的浇口位置和数量就必须对塑料件的外形和注塑过程中的流动情况进行模拟和分析.211 数码相机前盖模拟分析过程21111 数模的预处理要对制件进行分析,首先要在数模表面生成三角形网格来覆盖整个工件表面,为以后的MPI/flow分析提供一个基础平台.因此首先在Pro/Engineer中创建实体模型,并将其通过M D L(M old flow DesginLink)导入到MPI模块中.由于网格生成成功与否直接影响到后面的分析工作,所以在生成网格后要用网格状态统计表工具来检查网格生成中产生的缺陷和不足,并用相应的网格编辑工具来修复网格,消除缺陷.要注意的是在修复时会破坏其他已经修复好的实体区域,从而产生新的缺陷和不足,如在修复自由边时可能会产生元素的重叠等新缺陷,所以修复是循环往复进行的,直到得到满意的网格覆盖为止.作者在分析中采用中性面网格,有限元分析模型数据为:面单元数=13636,节点数=6792,匹配率为9017%.因此对MPI/流量-溶解分析是可接受的.如果网目匹配百分率太低,应该重新运用网格生成工具来修改网格,直到其匹配率大于85%.21112 浇口位置的初步确定MPI模块提供了最佳浇口位置分析功能,进行该分析有助于选定浇口位置.通过软件对工件的初步分析,结合实际制件的技术要求和生产方式,得出如图1和图2两种浇口的布置方式.874 江苏大学学报(自然科学版) 第25卷图1 单浇口填充压力变化Fig.1 S ingle gatepressure图2 双浇口填充压力变化Fig.2 T w o gates pressure 塑件所用材料为ABS ,相关参数为:塑料熔融温度为230℃;模具温度为60℃;最大充填压力为100MPa.212 流动模拟分析结果比较21211 不同浇口位置的冲型压力变化在充填的时候,对于不同浇口位置的冲型压力变化如图1、图2所示,应该避免压力范围的大变化.大多数的注射成型过程中压力的变化范围应在100~150MPa.在保压的时候,压力的变化将影响体积收缩率,因此在保压时模腔中的压力变化要小.图1是单浇口冲型压力变化图,其中1区、2区是低压区,它的压力变化范围是32142MPa.图2是双浇口冲型压力变化图,其中3区是低压区,它的压力变化范围是26191MPa.从以上初步分析可知,双浇口的低压区小且压力变化范围比单浇口的小.也就是说双浇口对塑件的体积收缩率影响小,更有利于保证塑件的成型质量.21212 不同浇口位置产生的气泡在塑料熔体注射充填过程中,模腔内除了原有空气外,还有塑料含有的水分在注射温度下蒸发而成的水蒸气,塑料局部过热分解产生的低分子挥发性气体等.这些气体若不能通过排气系统顺利排出模腔,将会影响制品成型以及脱模后的质量.图3、图4表明,注塑件在浇注结束后会在两股低温流头相遇处或流动末尾处产生气体.两种方案出现气泡的情况是单浇口多于双浇口,且单浇口有些气泡出现在表面,不易于排除.图3 单浇口方案的气泡分布Fig.3 Air traps distrbution of singlegate图4 双浇口方案的气泡分布Fig.4 Air traps distribution of tw o gates21213 不同浇口位置产生的熔接痕熔接痕产生于两股低温流头相遇的位置,熔接痕的出现对制品强度有一定的影响,熔接痕会削弱制品的结构强度并在制品的表面产生缺陷,且在对制品进行涂漆等后处理时,熔接痕位置较难处理.所以应尽量缩短熔接痕的长度和避免出现在制品的主要受力部位.图5、图6分别给出了两种浇口位置熔接痕的数量及分布,从分析结果中可知单浇口的熔接痕少,溶体流动较均匀.双浇口的熔接痕相对多一点,在熔接痕处的力学性能差,有可能会影响制品的质量.但双浇口中的塑料在充型时,其易产生熔接痕的地方有较高的温度,从而可以保证熔接痕的产生机率很小,基本上不会影响塑件的使用性能和外观质量.974第6期 袁国定等:基于C AE 技术的注塑模浇口优化设计图5 单浇口方案的熔接痕分布Fig.5 Weld line distrbution of singlegate图6 双浇口方案的熔接痕分布Fig.6 Weld line distribution of tw o gates213 手机前壳体浇口的优化设计某款手机的前面壳体,材料为PC +ABS ,产品长86mm ,宽45mm ,平均厚度为112mm ,是手机中的重要外观件之一.外观件对注塑成型质量要求较高,所以模具设计时,首先需要对浇口的位置进行优化分析以得到较好的制件质量.根据实际经验,浇口数设计为2个,浇口位置初始方案设置在液晶显示屏(LC D )窗口的上下两个对角,如图7箭头所示.对该方案进行充填分析,结果如图7所示.从图7a 充填时间上看,最后充填区域右上角和下角的充填时间不一致,所以该方案充填不平衡,充填不平衡容易引起局部过保压,使制件的密度不均匀,导致质量不一致.从图7b 看出,所需的注塑压力约为78MPa 左右,这是因为充填不平衡导致所需的注射压力比较高.由于该制件的孔眼比较多,所以在制件上产生的熔接痕和气穴也比较多,如图7c 、d 所示.通过上面的分析,为了使流动达到较为平衡的状态,降低注塑压力,提高产品质量,需要对浇口的位置重新进行选择.将浇口位置设置在LC D 窗口的左角和下角两处(图8).对该改进方案进行充填分析,得到的充填时间、注塑压力、熔接痕、气穴等分析结果见图8.从图8a 充填时间可以看出,最后充填区域右上角和下角的两处的充填时间较为一致,所需的注射压力(图8b )比初始方案减小,降至68MPa 左右,有利于保证制件的质量,熔接痕(图8c )在强度要求相对较低的区域,气穴(图8d )的分布和初始方案差不多.总的来说,改进后的方案较合理,所以该模具的浇口位置设计应采用改进后的方案.图7 初始方案的模拟分析图8 改进方案的模拟分析Fig.8 S imulation of improved project84 江苏大学学报(自然科学版) 第25卷3 结 论(1)利用注塑C AE 分析软件,可在模具设计的初始阶段,分析比较不同方案的注塑压力、充填状态等参数,预测设计中潜在的缺陷,突破了传统的在注塑机上反复试模、修模的束缚,为设计人员修改设计提供科学的依据.C AE 技术的应用带来的直接好处是优化模具设计,省时省力,减少试模、修模次数和模具报废率,缩短模具设计制造周期,降低成本,提高产品质量.(2)随着C AE 技术的深入研究,人们正在致力于将优化技术与C AE 技术有机结合起来,利用现有的模拟结果,借助于优化理论,开发智能化的分析系统,给出明确的改进方向和尺度,实现注塑模的自动、优化设计,从根本上解决依赖经验和技巧的问题.参考文献(R eferences)[1] 申长雨.塑料模具计算机辅助工程[M].郑州:河南科学技术出版社,1998.[2] 张佑生.塑料模具计算机辅助设计[M].北京:机械工业出版社,1998.[3] 吴崇峰.实用注射模C AD/C AM/C AE 技术[M].北京:轻工业出版社,2000.[4] 申长雨.注射模充模过程C AE 技术I :理论与算法[J ].模具工业,2001(2):51-56.SHE N Chang 2yu.C AE I theory and arithmetic of the fil 2ling course of injection m ould[J ].Mould Industry ,2001(2):51-56.(in Chinese )[5] Apellmann R C ,Haberstroh E.Three 2dimensional simula 2tion of the udder injection m olding process [R ],ANTE ’2000,SPE con ference ,2000.[6] 芦亚萍.大圆角洗衣机箱体成型模具主要参数计算方法分析[J ].江苏理工大学学报(自然科学版)2001122(3):41-44.LU Y a 2ping.An analysis on the calculation of the main pa 2rameters of the shaping m ould for washing machine boxes with a big arc[J ].Journal o f Jiangsu Univer sity o f Science and Technology (Natural Science Edition ),2001,22(3):41-44.(in Chinese )(责任编辑 陈持平)旋转导向管喷动床装置日前江苏大学研发的“旋转导向管喷动床装置”被授予实用新型专利,该专利采用喷动床反应器的新型结构,主要用于物料干燥、热解、造粒等.其特点在于导向管的上部为旋转部分,借助于物料喷出导向管端口时的反作用力驱动旋转部分.该结构可实现物料离开导向管后全部落在环形区内,当导向管直径增大后仍能保证喷动床的正常运转.该实用新型专利的应用突破传统导向管的局限性,可显著提高喷动床生产能力.(科技处 唐 恒)184第6期 袁国定等:基于C AE 技术的注塑模浇口优化设计。
基于CAD_CAE技术注塑模优化设计

第29卷第7期Vol.29NO.7重庆工商大学学报(自然科学版)J Chongqing Technol Business Univ.(Nat Sci Ed )2012年7月Jul.2012文章编号:1672-058X (2012)07-0062-07基于CAD /CAE 技术注塑模优化设计*林权(武夷学院电子工程系,福建武夷山354300)收稿日期:2011-11-12;修回日期:2011-12-27.*基金项目:福建省教育厅科技计划专项项目(JK2011059);武夷学院青年教师专项科研基金(XQ201105).作者简介:林权(1980-),男,福建福州人,硕士,从事塑料模具设计与制造研究.摘要:改变以往依靠经验、直觉或反复试模的模具设计方法,采用计算机辅助设计软件UG 、数据转换软件CAD Doctor 、有限元分析软件MoldFlow 相结合的方法进行注塑模优化设计;结果表明:通过对成型压力、填充时间、最大锁模力等指标测试,可知网格划分的疏密程度不能作为塑件分析准确度的标准依据;通过对注射过程中充填分析、冷却分析及翘曲分析模拟,得到了塑件的最佳的浇注系统和冷却系统设计参数,获取了气穴、熔接线、翘曲变形等分布特性,为优化模具结构设计提供了重要参考;最后通过实践证明,运用CAD /CAE 技术创建的模具结构灵活可靠,产品质量满足使用要求,模具设计可供同行参考。
关键词:CAD /CAE 技术;模流分析;注塑模具;优化设计中图分类号:TQ320文献标志码:A在产品不断的推陈出新,技术不断的在进步的时代,越来越多的塑料产品,开发时间的周期越来越短,为了提高企业的竞争力,各制造商从概念设计、产品设计、模具设计、开模、试模的过程中,不断地在寻求缩短时间周期的方法,发现模具试模的部份是很大的关键,而传统依靠经验、直觉或反复试模才能修正模具的设计方法已不能满足现代生产和集成技术的需求[1-3]。
现代以模具CAD /CAE 技术在计算机上对模具设计方案进行分析和模拟来代替实际的试模,不仅可以检验各种产品生产可行性,而且在设计阶段就预知可能发生的情形,并加以修正将问题降到最低[4]。
基于MATLAB和CATIA的注塑模具零件库的参数化设计

Excel、MATLAB和CATIA V5R20等软件,实现了注塑模具的带肩推杆零件库的参数化设计,达到了改变基本参数就可以得
到相应的三维模型的驱动化设计。
关键词:CATIA;参数化设计;注塑模具;计算机辅助设计;MATLAB;零件库
中图分类号:TH 122;TP 391.7
文献标志码:粤020原园3
Parametric Design of Parts Library of Injection Mold Based on MATLAB and CATIA
YE Shuang, WANG Jie, HUANG Sisi, LIU Jiange
(School of Manufacturing Science and Engineering, Sichuan University, Chengdu610065, China)
基金项目:中国制造 2025 数字出版知识挖掘与服务创新平 台及产业化 - 子项目:注塑模具与管接头三维图 库研究与建设(17H1172)
在前人的基础上,更加提高了建模人员的建模效率,减轻 了建模人员的工作负担。 1 CATIA参数化和MATLAB编程的介绍及应用
CATIA (Computer Aided Tri -Dimensional Interface Application)是IBM和法国达索系统公司共同设计的一款 集计算机辅助设计和制造以及分析于一体的功能强大的 CAD软件。MATLAB是Matrix、Laboratory两个词的前缀组 合,是由美国的MathWorks公司于1984年发布的一种功能 强大的高级技术计算语言和交互式环境[3]。MATLAB程序 运行MATLAB自己的语言,它拥有一个覆盖领域宽广的 预先定义的函数库,还有各种各样的函数,这样就使得技 术工作变得方便高效。
基于数值模拟技术的塑料弯管注塑模优化设计
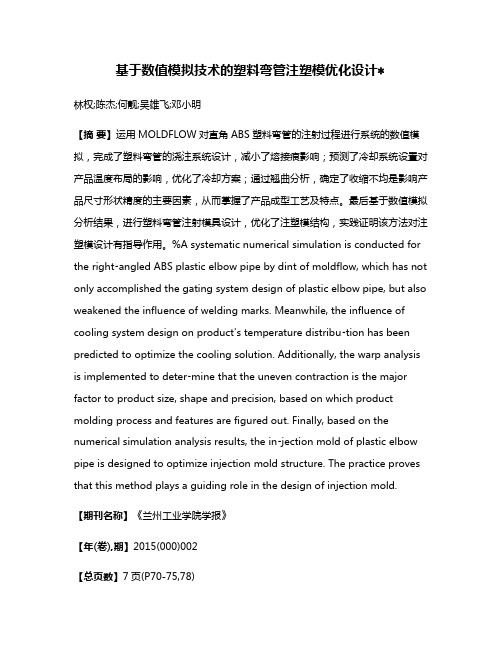
基于数值模拟技术的塑料弯管注塑模优化设计∗林权;陈杰;何靓;吴雄飞;邓小明【摘要】运用MOLDFLOW对直角ABS塑料弯管的注射过程进行系统的数值模拟,完成了塑料弯管的浇注系统设计,减小了熔接痕影响;预测了冷却系统设置对产品温度布局的影响,优化了冷却方案;通过翘曲分析,确定了收缩不均是影响产品尺寸形状精度的主要因素,从而掌握了产品成型工艺及特点。
最后基于数值模拟分析结果,进行塑料弯管注射模具设计,优化了注塑模结构,实践证明该方法对注塑模设计有指导作用。
%A systematic numerical simulation is conducted for the right⁃angled ABS plastic elbow pipe by dint of moldflow, which has not only accomplished the gating system design of plastic elbow pipe, but also weakened the influence of welding marks. Meanwhile, the influence of cooling system design on product's temperature distribu⁃tion has been predicted to optimize the cooling solution. Additionally, the warp analysis is implemented to deter⁃mine that the uneven contraction is the major factor to product size, shape and precision, based on which product molding process and features are figured out. Finally, based on the numerical simulation analysis results, the in⁃jection mold of plastic elbow pipe is designed to optimize injection mold structure. The practice proves that this method plays a guiding role in the design of injection mold.【期刊名称】《兰州工业学院学报》【年(卷),期】2015(000)002【总页数】7页(P70-75,78)【关键词】数值模拟;注塑模具;塑料弯管;优化设计【作者】林权;陈杰;何靓;吴雄飞;邓小明【作者单位】武夷学院机电工程学院,福建武夷山 354300;武夷学院机电工程学院,福建武夷山 354300;武夷学院机电工程学院,福建武夷山 354300;武夷学院机电工程学院,福建武夷山 354300;武夷学院机电工程学院,福建武夷山354300【正文语种】中文【中图分类】TQ320.66由于石化工业的不断发展,塑料注塑产品占据市场的份额越来越大,工业上和生活中都离不开注塑产品,其中注塑模具设计是注塑产品成型最关键的部分,因此如何提高注塑模具设计质量,缩短产品生产周期,降低生产成本己成为塑料成型技术领域研究的重要课题[1-2].传统的模具设计方法存在周期长、出错率高等缺陷[3],已经无法满足客户的需求.在此以塑料直角弯管为例,提出将先进的计算机数值模拟技术应用于注塑模具设计的全过程,预测并消除可能发生的问题,实现对模具设计过程的优化,确保模具生产质量.塑料直角弯管长73 mm,宽57 mm ,内孔直径为32 mm,内部拐角处为90°,壁厚约3.5 mm,两端管头处均有台阶接口,其结构尺寸如图1所示.其生产技术要求如下:① 未注圆角为R0.5;② 未注脱模斜度为0.5°;③ 浇口处理要求平整去除;④ 未注尺寸公差依照GB1800—1987,IT9级要求;⑤ 不允许有注射缺陷,如缩水,流痕,波纹,表面剥离,气泡等;⑥ 分模面优先考虑图示平面;⑦ 产品头部带锥面与凹槽部分长25 mm,为密封连接段,模具结构中不允许设置顶针;⑧ 批量生产,材料收缩率为0.5%.该塑件为90°的塑料连接弯头,主要用于液体输送管道安装,因此常受到液体压力的冲击,而且端部有连接密封的需要,要求塑件有良好的机械强度,不易变形,以及耐磨、耐腐蚀等,根据各类塑料的性能特点选用ABS工程塑料(丙烯腈、丁二烯、苯乙烯三种单体的共聚物)作为塑件的生产原料.在此选用奇美公司生产的注塑级ABS\PA757,密度:1.2 g/cm3,成型收缩率:0.4%~0.7%,成型温度:200~240 ℃,干燥条件:80~90 ℃/2 h.从零件图可以看出产品结构不复杂,壁厚相对均匀,成型工艺性好,易于采用注塑成型,只是产品存在一个垂直内孔,需要侧向抽芯机构,而且抽芯距比较大,两个方向都需要.在有限元数值模拟分析前,先要对产品建立模型,使计算机能了解产品所有几何特性[4].在此利用UGNX8.0对产品进行建模,然后导入Moldflow模流分析软件并进行网格划分,高质量的网格是数值模拟分析结果准确性的保证[5].网格模型是由点(point)与面(surface)所组成,每一点在空间上都有惟一坐标值,面由点所联结而成,但需注意同一个面上所有点需为共平面,不可以歪斜,否则元素切割会有错误.面则包含一些属性,例如几何厚度等,用以辅助建立程序与数值计算进行,图2为塑料弯管有限元分析模型.通过利用MPI(Moldflow Plastics In-sight)对产品有限元模型进行充填、保压、冷却及翘曲变形等注射成型模拟分析,可以获知产品在成型过程中的各种状态,获取各种问题和缺陷的“数据流”,如最佳浇口位置、熔接线、成型过程温度压力、气穴分布、翘曲变形等,最后再参考这些数据进行模具结构设计.最佳浇口位置分析是MOLDFLOW模流分析中重要环节,通过对塑胶充填过程进行数值模拟计算,可以很容易的搜索到最佳的进浇位置,再结合产品实际生产工艺环境,分析出来的最佳浇口位置是模具结构设计的重要参考依据.但在进行注射浇口最佳化分析前,先要确定注塑工艺参数,在此采用MOLDFLOW成型窗口中推荐的数据与实际经验相结合的办法,选择的奇美\ABS\PA757注塑工艺参数如表1所示.图3为最佳浇口位置分析云图,图中弯管体现蓝颜色的地方表示最佳浇口选择区域,绿色黄色次之,而最差的浇口选择区用最显目的红颜色表示.从图中可以看出,蓝色区域集中在直角弯管的直角拐弯处的圆环带上,即图中A到B的圆环带上,最佳的位置处在直角拐弯接近凹槽A处.图4为流动阻力分析云图,由于直角塑料弯管一端头部有凹槽,另一端头部有台阶,都会导致充填流动的阻力增加,且两端距离最佳的蓝色直角拐弯A处也最远,图中CD两处分别用最显目的红颜色波纹来表示,它们的流动阻力最大.为了缓和两端的流动阻力,也为了模具成型结构设计的方便性,选择B处为该产品的进浇口位置.浇注系统设计合理与否对塑件的质量、尺寸、性能、模具结构、废料率等等都有较大影响[6].在此根据产品的技术要求,分模面优先考虑图1产品零件图所在的平面,即产品水平截面作为分型面.接着就需要确定型腔数量,由于产品尺寸较小,比较适合一模多腔,但从模具制造方面考虑,开设的型腔不易多,由图1产品结构可知,成型一个产品就需要增加两根互相垂直的侧抽芯,侧向抽芯机构和镶件都会增加模具制造难度,但产品又需要具备一定的生产效率,因此决定在模具的四个方向都设置抽芯机构,采用一模四腔,对称布置,如图5所示,总体上结构简单紧凑,又能保证各个型腔的平衡流动成形和脱模需要.由于注塑材料ABS\PA757流动性好,根据模具浇注系统的设计原则,再结合最佳浇口位置分析结果,以及产品生产技术要求,决定采用侧浇口的变异形式扇形浇口,浇口开设在塑件的圆弧面B处. 注塑模冷却系统的设计没有固定的模式和规则,冷却系统设计主要包括模具冷却方式、冷却介质流道尺寸大小和位置等[6].在此根据直角弯管形状以及相关成型部件结构,设定冷却系统如图5所示,从图中可以看出,首先冷却水道在产品成型型腔上下各开通直通式水道4条,分别冷却动定模型腔,外部用冷却软管连接,冷却水道直径为8 mm,冷却水道与产品成型表面距离为20 mm,冷却水道间距为40 mm,并均匀的分布在注塑模具横截面上进行均衡冷却.其次,为了保证型芯与型腔的温差不能太大,所以在两垂直侧抽芯上也需要开设水道.在此选用隔板式冷却水路,详见图5.图中隔板式冷却系统采用管道直径为12 mm,板式冷却管道直径为20 mm,内部包含分隔水路的铜质镶片,厚约2 mm,每个侧抽芯内部均设置隔板冷却水路,同一侧隔板共用一条冷却水路进行降温,东西南北四个方向总共添加4条冷却水路.注塑成型时间的设定包含了充填时间、保压时间与冷却时间等.其中充填时间的设定主要会影响产品是否发生短射,若充填时间过长则流速越慢,容易造成产品短射.由于数值模拟与实际现场生产不同,现场实际的充填时间为注塑机台的输出值,其值除了包含充填所需的时间外,也包含保压所需的时间,而数值模拟分析充填时间与保压时间是分别设定,若直接输入注塑机台输出的充填时间,则会造成充填时间过长而导致产品短射.图6为产品充填时间分析云图,从图中获知直角弯管充填完毕需要的时间是1.08 s,蓝颜色表示最早充填到达的位置,绿色黄色次之,而红色区域主要分布在弯管带凹槽的一端,表示熔体最后充填位置,也就是需要最长的注射时间.图7为流动前沿温度分布云图,该云图不仅可以观察熔体在模腔中各时段的充填情形,来判断产品是否存在短射,是否存在局部区域流动阻力过大而产生迟滞,而且能预测熔接线及气穴的位置,将作为模具结构设计的重要参考依据.在此通过分析流动波前充填的40%(图7a)到流动波前的100%(图7b),获知塑料熔体流动前沿温度一直保持在熔融状态,整体分布基本为230 ℃,获知浇注系统的设计方案使得各模腔充填均匀以及达到熔体流动平衡.结合图6与图7还可以看出塑料弯管填充情况良好,没有出现局部区域流动阻力过大而迟滞,没有产生短射现象,充填熔体的温度与注射压力也满足需求. 从图7中还可以看出,充填结束阶段的流动波前处于塑料弯管的直角转弯处与两端面,是最容易产生气穴的地方,也是熔接线最可能产生的位置,如图8所示.熔接线不但影响外观,而且产品容易在此线位置产生应力集中而有断裂的问题产生,但对于本产品而言,从图6~7可知,充填过程中塑料熔体流动前沿温度一直保持在熔融状态,直角转弯处与两端面的熔体温度无明显降低,熔接温度较高且温差很小,属于热熔接线,热熔接线的熔合性好且痕迹不明显,保证了产品机械强度和表观质量.对于气穴,本产品属于中小型塑件,型腔所包容的空气总量小,且型芯型腔属于组合式,气体可以通过成型零件间的配合间隙予以排除.图7 流动前沿温度分布云图另外,本产品最大注射压力23 MPa发生在速度/压力控制转换的时候,填充量约为总体积的99%,且最大注射压力也低于注射机最大注射压力的80%,因此该浇注系统填充时间短、效率高、填充完全.图8 熔接痕分布3.2 冷却成型模拟分析模具冷却回路设计是否合理,主要考核以下几点:首先是冷却后的产品零件温度达到或者小于零件设置的顶出温度,其次是冷却液出入口处温度差要控制在规定范围之内,最后是冷却是否存在不均衡,引起的变形在允许范围之内.通过MPI\COOL 分析获知,冷却后产品的零件温度为78 ℃,而分析设置的顶出温度为88 ℃,零件温度明显低于顶出温度,符合设计要求;其次,冷却液出入口温度差最大为1.2 ℃,而由根据参考文献4可知,一般认为冷却液温升不高于3 ℃即满足设计原则,可以看出该冷却系统冷却效果较好;最后对冷却不均引起的产品翘曲变形进行分析,获知最大的变形量为0.008 7 mm,且呈线条状分布在端面边缘处,产品其余部分变形量很微小,普遍都在0.005 mm以下.因此模具的冷却系统设计合理,符合冷却系统简单而实用的原则.3.3 翘曲变形与体积收缩模拟分析在模流分析中,产品的翘曲变形因素主要有3种,分别为冷却不均引起的变形,分子取向不一样引起的变形,以及收缩不均引起的变形[7].其中由冷却不均引起的变形在已经分析过,变形幅度很小不是引起产品变形的主要因素,另外通过模拟分析后获知分子取向不一致引起的变形为零,因此引起本产品变形的主要因素就是收缩不均,产品收缩不均引起的总变形如图9所示.通过计算变形幅度最大为0.2737 mm,位于弯管带凹槽一端的端面处,由于凹槽位置是熔体最后填充的地方,流程较长,并且通过凹槽这个变截面的地方,熔体压力损失也比较大,因而熔体不易补充和压实造成收缩.产品其他大部分位置的翘曲变形量均小于0.2 mm,是由于保压压力都可以直接作用,补缩容易.但总体上塑料熔体流动情况良好,且具备一致性和均衡性,变形量较小,满足使用要求.图9 产品收缩不均引起的变形图10为产品顶出时体积收缩率分布云图,从图中可以获知,产品的浇注系统中主流道顶部与底部收缩率最大,都显示为红色达到了5.7%左右,底部是由于该处塑料体积最大为产品的热节之处,顶部是由于靠近注塑机的喷嘴,熔体冷却最慢造成,其余部分都显示为蓝色、绿色、黄色.黄色表示体积收缩率在4.6%左右,主要分布在弯管带凹槽的一端与产品进浇口附件的圆弧面处,其他部位都小于4 %.根据文献[5]可知,ABS工程塑料的收缩率一般在0.4%~0.7%之间,根据以上的数值模拟分析情况,除主流道外其收缩值率不到0.5%,符合ABS的基本收缩率,同时也符合产品的生产技术要求.图10 顶出时产品体积收缩率4 注塑模具结构设计利用MOLDFLOW对塑料弯管进行较为详细的注射成型分析模拟,确定了最佳浇口位置,建立了浇注系统和冷却系统,再通过填充、流动、保压、冷却、翘曲等环节分析,获得了ABS熔体通过扇形浇口进入模具型腔后的流动行为及其温度、压力分布状况,评估了熔接痕和气穴可能出现的位置及其模具结构、成型工艺设置提出的要求,测试了模具冷却系统对注塑产品质量的影响以及成型过程中产品温度分布状况,另外还模拟计算了塑料弯管可能产生的翘曲状况和变形分布,揭示了本产品收缩不均是引起尺寸变化的重要因素.图11 模具结构最后基于数值模拟分析结果,对模具结构进行设计.首先从取得弯管产品的 CAD 原始模型与结构开始,根据生产技术要求评估开模形式以及分模面,再根据数值模拟的分析结果,设计流道浇口、斜导柱与侧向分型与抽芯机构、成型零件、脱模机构、结构模板支架、冷却系统以及模具刚度强度设计等,最后模具结构如图11所示.从图中获知模具一模四腔,主流道位于模具中心位置,以塑料弯管水平截面为分型面,采用组合式型芯型腔布局,公模仁与母模仁属于碰穿式分型面分别固定在动定模板上,熔体流道和冷却系统正如数值模拟所示,属于单分型面两板式注塑模. 塑料弯管注塑模设计的重点是成型直角内通孔,在此采用两个互相垂直的侧型芯1与侧型芯2穿插来成型直角内孔,侧型芯固定在侧滑块上,同个方向的两个侧型芯共用一个侧滑块,侧滑块中间设置导向孔,由固定在定模板的斜导柱驱动其完成侧分型运动,为了避免侧型芯与公母模仁接触拉毛磨损,在侧型芯与模仁间有个滑块挡板,由滑块挡板承受注射成型侧压力,避免侧隙流胶和封胶面的损伤.此外为了保证塑料弯管成型不错位,具备一定的同轴度,要避免发生侧型芯侧移,所以必须加强侧滑块的定位与导向.本模具采用双边T型槽导向,锁紧块与侧滑块22度斜面配合并设计锁位,斜导杆与侧滑块20度配合,且斜导柱与导向孔双边只留间隙1 mm,防止开合模过程中发生侧移.脱模采用加工与设计都比较简单的推杆,并设置复位杆复位,由流动成型模拟分析可知弯管直角拐弯处外缘是冷却最慢的位置,应该避开在该处设置推杆,另外弯管带锥面与凹槽部分长25 mm,为密封连接段不允许设置顶针,因此在距离端面约30 mm的位置设置带凹槽端的推杆,其它结构如图11所示.5 结语本课题基于数值模拟分析技术,通过利用MPI对塑料弯管进行充填、保压、冷却及翘曲变形等注射成型模拟分析,获知产品在成型过程中的各种状态,获取各种问题和缺陷,掌握了产品注塑成型过程及其工艺特点,并为模具结构设计提供了重要的参考设计信息,最后很好的完成了塑料弯管的模具设计.模具制造与产品生产实践证明,该模具结构合理,塑件侧抽运动灵活可靠,顶出质量符合设计要求,各项指标满足客户需求.因此利用数值模拟技术进行注塑模具结构优化设计的方法可靠有效,具备经济效益与参考价值.(责任编辑:曾贤灏)Optimal Design for the Injection Mold of Plastic Elbow Pipe Based on Numerical SimulationLIN Quan, CHEN Jie, HE Jing, WU Xiong-fei, DENG Xiao-ming(College of Mechanical and Electrical Engineering, WuyiUniversity,Wuyishan 354300, China)Abstract: A systematic numerical simulation is conducted for the right-angled ABS plastic elbow pipe by dint of moldflow, which has not only accomplished the gating system design of plastic elbow pipe, but also weakened the influence of welding marks. Meanwhile, the influence of cooling system design on product's temperature distribution has been predicted to optimize the cooling solution. Additionally, the warp analysis is implemented to determine that the uneven contraction is the majorfactor to product size, shape and precision, based on which product molding process and features are figured out. Finally, based on the numerical simulation analysis results, the injection mold of plastic elbow pipe is designed to optimize injection mold structure. The practice proves that this method plays a guiding role in the design of injection mold.Key words: numerical simulation; injection mold; plastic elbow pipe; optimal design作者简介:林权(1980-), 男,福建福州人,讲师,硕士.基金项目:福建省教育厅A类科技项目(JA13323);国家级大学生创新创业训练计划项目(201310397014 );南平市科技计划项目(N2013X01-7)*收稿日期:2014-11-01中图分类号: TQ320.66文献标志码:A文章编号:1009-2269(2015)02-0070-06图7为流动前沿温度分布云图,该云图不仅可以观察熔体在模腔中各时段的充填情形,来判断产品是否存在短射,是否存在局部区域流动阻力过大而产生迟滞,而且能预测熔接线及气穴的位置,将作为模具结构设计的重要参考依据.在此通过分析流动波前充填的40%(图7a)到流动波前的100%(图7b),获知塑料熔体流动前沿温度一直保持在熔融状态,整体分布基本为230 ℃,获知浇注系统的设计方案使得各模腔充填均匀以及达到熔体流动平衡.结合图6与图7还可以看出塑料弯管填充情况良好,没有出现局部区域流动阻力过大而迟滞,没有产生短射现象,充填熔体的温度与注射压力也满足需求. 从图7中还可以看出,充填结束阶段的流动波前处于塑料弯管的直角转弯处与两端面,是最容易产生气穴的地方,也是熔接线最可能产生的位置,如图8所示.熔接线不但影响外观,而且产品容易在此线位置产生应力集中而有断裂的问题产生,但对于本产品而言,从图6~7可知,充填过程中塑料熔体流动前沿温度一直保持在熔融状态,直角转弯处与两端面的熔体温度无明显降低,熔接温度较高且温差很小,属于热熔接线,热熔接线的熔合性好且痕迹不明显,保证了产品机械强度和表观质量.对于气穴,本产品属于中小型塑件,型腔所包容的空气总量小,且型芯型腔属于组合式,气体可以通过成型零件间的配合间隙予以排除.另外,本产品最大注射压力23 MPa发生在速度/压力控制转换的时候,填充量约为总体积的99%,且最大注射压力也低于注射机最大注射压力的80%,因此该浇注系统填充时间短、效率高、填充完全.模具冷却回路设计是否合理,主要考核以下几点:首先是冷却后的产品零件温度达到或者小于零件设置的顶出温度,其次是冷却液出入口处温度差要控制在规定范围之内,最后是冷却是否存在不均衡,引起的变形在允许范围之内.通过MPI\COOL 分析获知,冷却后产品的零件温度为78 ℃,而分析设置的顶出温度为88 ℃,零件温度明显低于顶出温度,符合设计要求;其次,冷却液出入口温度差最大为1.2 ℃,而由根据参考文献4可知,一般认为冷却液温升不高于3 ℃即满足设计原则,可以看出该冷却系统冷却效果较好;最后对冷却不均引起的产品翘曲变形进行分析,获知最大的变形量为0.008 7 mm,且呈线条状分布在端面边缘处,产品其余部分变形量很微小,普遍都在0.005 mm以下.因此模具的冷却系统设计合理,符合冷却系统简单而实用的原则.在模流分析中,产品的翘曲变形因素主要有3种,分别为冷却不均引起的变形,分子取向不一样引起的变形,以及收缩不均引起的变形[7].其中由冷却不均引起的变形在已经分析过,变形幅度很小不是引起产品变形的主要因素,另外通过模拟分析后获知分子取向不一致引起的变形为零,因此引起本产品变形的主要因素就是收缩不均,产品收缩不均引起的总变形如图9所示.通过计算变形幅度最大为0.2737 mm,位于弯管带凹槽一端的端面处,由于凹槽位置是熔体最后填充的地方,流程较长,并且通过凹槽这个变截面的地方,熔体压力损失也比较大,因而熔体不易补充和压实造成收缩.产品其他大部分位置的翘曲变形量均小于0.2 mm,是由于保压压力都可以直接作用,补缩容易.但总体上塑料熔体流动情况良好,且具备一致性和均衡性,变形量较小,满足使用要求.图10为产品顶出时体积收缩率分布云图,从图中可以获知,产品的浇注系统中主流道顶部与底部收缩率最大,都显示为红色达到了5.7%左右,底部是由于该处塑料体积最大为产品的热节之处,顶部是由于靠近注塑机的喷嘴,熔体冷却最慢造成,其余部分都显示为蓝色、绿色、黄色.黄色表示体积收缩率在4.6%左右,主要分布在弯管带凹槽的一端与产品进浇口附件的圆弧面处,其他部位都小于4 %.根据文献[5]可知,ABS工程塑料的收缩率一般在0.4%~0.7%之间,根据以上的数值模拟分析情况,除主流道外其收缩值率不到0.5%,符合ABS的基本收缩率,同时也符合产品的生产技术要求.利用MOLDFLOW对塑料弯管进行较为详细的注射成型分析模拟,确定了最佳浇口位置,建立了浇注系统和冷却系统,再通过填充、流动、保压、冷却、翘曲等环节分析,获得了ABS熔体通过扇形浇口进入模具型腔后的流动行为及其温度、压力分布状况,评估了熔接痕和气穴可能出现的位置及其模具结构、成型工艺设置提出的要求,测试了模具冷却系统对注塑产品质量的影响以及成型过程中产品温度分布状况,另外还模拟计算了塑料弯管可能产生的翘曲状况和变形分布,揭示了本产品收缩不均是引起尺寸变化的重要因素.最后基于数值模拟分析结果,对模具结构进行设计.首先从取得弯管产品的 CAD 原始模型与结构开始,根据生产技术要求评估开模形式以及分模面,再根据数值模拟的分析结果,设计流道浇口、斜导柱与侧向分型与抽芯机构、成型零件、脱模机构、。
- 1、下载文档前请自行甄别文档内容的完整性,平台不提供额外的编辑、内容补充、找答案等附加服务。
- 2、"仅部分预览"的文档,不可在线预览部分如存在完整性等问题,可反馈申请退款(可完整预览的文档不适用该条件!)。
- 3、如文档侵犯您的权益,请联系客服反馈,我们会尽快为您处理(人工客服工作时间:9:00-18:30)。
基于MATLAB的塑料模具浇注系统的优化设计江飞舟韩加好(连云港职业技术学院,连云港 222006摘要利用MATLAB软件对放大镜塑料制品的模具浇注系统进行优化设计,对塑料成型的浇注系统的工艺参数和模具结构进行优化,从而提高放大镜塑料制品的合格率。
关键词 MATLAB 塑料模具浇注系统优化设计塑料浇注的制造系统主要包括塑料成型工艺、机械加工制造、修饰及装配。
目前塑料成型最常见的方法是注射成型技术,注射成型技术具有生产效率高、尺寸精度高、易于批量生产及能制造多种塑料制品等优点。
塑料的注射成型工艺对浇注系统的工艺参数和塑料模具的结构合理性具有较高的要求,如果浇注系统的工艺参数和模具结构不合理,塑料制品就会产生缺陷,严重的塑料无法成型。
因此,应对塑料模具浇注系统的工艺参数进行优化,浇注系统的工艺参数主要有注射温度、注塑压力和注射速率;影响塑料制品的模具结构主要有分型面的确定、浇口的尺寸和位置设定;另外,加热系统、冷却系统及注塑机的性能也是影响塑料成型的主要工艺参数。
塑料制品通常比较复杂,塑料模具设计人员的经验有限,因此无法直接设计出成本低、塑料制品质量好的模具,一般需要反复试验和修改设计多次才能投入生产。
因此,利用MATLAB软件对塑料模具进行优化设计,掌握浇注系统对塑料成型的影响,找出模具浇注系统存在的缺陷,从而能提高塑料模具浇注系统设计的合理性,可以有效地降低塑料成型的成本,提高生产效率。
笔者以放大镜为例,利用MATLAB软件对放大镜塑料制品的模具浇注系统进行优化设计,对塑料成型的浇注系统的工艺参数和模具结构进行优化,从而提高放大镜塑料制品的合格率。
1塑料放大镜模具浇注系统的概述如果塑料放大镜模具浇注系统设计不合理将导致熔体温度和压力发生改变,使其质量降低,也会降低塑料放大镜模具的力学性能。
塑料放大镜模具浇注系统主要包括浇口的位置、数目、形状及流道的尺寸。
在设计塑料放大镜的浇注系统的过程中需充分地考虑塑料放大镜的力学性能,熔体的流程比,且要确保所有的浇口中的熔体同时充满。
为了满足塑料放大镜透光的需要,塑料的材料选择聚乙烯,塑料模具三面有斜导柱抽芯机构,中间利用镶嵌式结构。
塑料模具有较高的耐磨性,可利用经过淬火的耐磨钢。
2塑料放大镜模具浇注系统基本结构参数和工艺参数塑料放大镜的几何形状和主要尺寸如图1所示。
图1塑料放大镜的结构图塑料放大镜的形状比较复杂,通常情况下塑料放大镜在注射成型以后由于收缩会紧紧地包在型芯上,所以需要非常大的脱模力。
同时,塑料放大镜的镜杆厚度比较小,如果利用推杆使塑料放大镜顶出,一般可以选择的推杆直径约为0.6 mm,塑料放大镜所受到的顶出压力非常大,有可能使塑料放大镜被顶穿,这样就使塑料放大镜破坏,甚至不能脱模,因此顶出塑料放大镜时,可以利用推板来完成。
塑料放大镜浇注系统的三维模型由UG软件绘制,为了能够提高分析效率,可以忽略塑料放大镜的局部细节,浇注系统设计时主要考虑注射成型的效率,因此利用一个注射模具和两个注射腔体配合使用的方式,利用侧向浇口进行浇注,塑料放大镜浇注系统的三维模型如图2所示。
收稿日期:2011-10-14图2塑料放大镜浇注系统的三维图塑料放大镜浇注系统的主要参数见表1。
表1塑料放大镜浇注系统的主要参数项目数据塑料放大镜的体积/m3 3.2×10–5塑料放大镜的质量/kg 3.46×10–2浇注系统的体积/m37.1×10–6浇注系统的质量/kg7.8×10–3根据塑料放大镜材料的浇注系统的经验值,结合经验公式确定浇注系统流道的几何尺寸见表2。
表2塑料放大镜浇注系统的几何尺寸 mm浇口浇口的几何尺寸分流道的几何尺寸主流道的几何尺寸侧浇口长度 1.25.0 4.5宽度 5.5高度 2.0塑料放大镜模具的整体结构如图3所示。
1—推杆固定板; 2—拉料杆; 3—动模垫板; 4—动模型腔固定板; 5—定位销; 6—定模型腔固定板; 7—定模板; 8—定位环; 9—主浇套;10—定模型腔块; 11—动模型腔块; 12—型腔杆图3塑料放大镜模具的总体结构利用螺杆和复位杆连接推杆,注塑机的顶杆可以使塑料放大镜模具的推杆固定板向前运动,从推板可以通过复位杆顶出塑料制品。
推板设置冷料穴,当拉料杆固定在推杆安装板上,推板和拉料杆将不会产生相对运动,不能使浇注系统流道内的凝料和拉料杆脱离。
将拉料杆和动模板固定,在塑料件被推板顶出时,将流道内的凝料推出。
在推板上加工出一个椭球状的凹坑,从而有利于浇注系统流道附着的凝料能被顺利推出。
3优化前放大镜模具浇注系统注射成型工艺参数注塑机开模时使复位杆和动模板靠紧,在推板和定模板上将模具分开,动模和动模安装板同时向后运动。
由于塑料放大镜紧紧地包在动模型芯上可以脱出定模型腔,浇口将被拉断,塑料放大镜处于动模侧;当注塑机顶出时,在复位杆的带动下顶杆使推板向前运动,进而使浇注流道内的凝料和塑料放大镜从拉料杆和型芯脱离。
注射成型设备利用德国BOY公司生产的注塑机,需较大的注射速率,且要求模具温度较高,所采用的注射成型工艺参数见表3。
表3塑料放大镜模具浇注系统注射成型的工艺参数表工艺参数数据工艺参数数据熔体温度/℃240注射速率/cm3·s–150保压压力/MPa85注塑压力/MPa36保压时间/s10冷却时间/s40模具温度/℃75成型周期/s95在塑料放大镜模具浇注系统注射成型阶段,模具运行不够流畅。
另外,塑料制品和流道凝料应该保证可以顺利脱模,从而能够使塑料放大镜质量得到提高,达到设计标准。
为了能够确保浇注系统成型工艺顺利进行,使塑料熔料能够在最短的时间内充满型腔,注射成型腔体内的压力必须保证均匀分布,从而能够使塑料熔料可以均匀填充在流道内。
保压曲线和熔料在流道内的填充过程关系非常密切,因此要想了解熔料在流道内的填充情况,应该确定浇注系统的保压曲线,塑料放大镜浇注系统的保压曲线如图4所示。
图4塑料放大镜模具浇注系统的保压曲线根据保压曲线,利用MATLAB软件编制塑料放大镜浇注系统的有限元仿真程序,将塑料放大镜划分为183945个四面体单元,浇注系统的流道被划分为548个四面体单元,进行仿真计算,通过对仿真结果的分析,可以发现优化前放大镜的浇注系统注射成型存在着如下的缺陷。
(1充模平衡性较差从仿真计算结果可以发现塑料放大镜注射成型浇注系统各部分的填充时间不相同,镜面所需要的熔体填充时间为8.36 s,而镜柄所需要的填充时间为9.34 s,所以,塑料放大镜各部分不能保证同时填充完毕,由此可以判断出塑料放大镜制品充模平衡较差。
(2最大注塑压力过大仿真结果为优化前的最大注塑压力为36 MPa,该注塑压力值超出了注塑机的最大性能,因此需要增加投资以获得性能更高的注塑机,从而提高了塑料放大镜注射成型的成本,因此,必须对其浇注系统的工艺进行优化。
(3温度分布不够均匀当塑料熔体填充完毕后,温度范围大概在196~220℃,最大的温度差为19℃,因此可以确定塑料放大镜填充结束后内部的温差不够均匀。
4优化后塑料放大镜模具浇注系统注射成型工艺参数针对以上缺陷,对塑料放大镜浇注系统的工艺参数进行优化设计,优化后结果见表4。
表4优化后塑料放大镜注射成型的工艺参数表工艺参数数据工艺参数数据熔体温度/℃260注射速率/cm3·s–160保压压力/MPa80注塑压力/MPa23.4保压时间/s8冷却时间/s35模具温度/℃70成型周期/s90经过浇注系统的优化,注射成型的效果有明显的提高,主要体现在以下几个方面:(1充模平衡性提高对优化后的浇注系统进行仿真计算,可以发现优化后塑料放大镜浇注系统各部分所需要的熔体填充时间一致,均在7.64 s左右,和优化前的8.36 s相比,减少了0.72 s,因此,可以保证塑料放大镜各部分同时被充满,并且使塑料放大镜制品处于良好的平衡状态,另外由于填充时间的减少,注射成型周期也相应减少。
(2最大注塑压力降低经过浇注系统优化后,放大镜注射成型的最大注塑压力为23.4 MPa,这样最大注塑压力降低了,注塑机的性能可以完全满足目前注射成型需求,从而提高放大镜注射成型的经济效益。
(3温度分布比较均匀经过浇注系统的优化后,经过MATLAB软件仿真计算,获得最大的温度差小于15℃,从而能够确保塑料放大镜填充结束后内部的温度差比较均匀。
因此,经过对浇注系统的优化,可以提高放大镜注射成型的质量和效率。
5优化前后注射成型效果对比经过放大镜浇注系统的优化后,注射成型的性能获得了较好的提高。
主要体现在以下几个方面:(1降低最大剪切力。
最大剪切力可以体现熔体在流道中的流动流畅性,根据MATLAB仿真结果可知,浇注系统优化前后的最大剪切力分别为0.45 MPa和0.25 MPa,剪切力降低了很多,表明熔体流动所需要的压力降低了,从而确保熔体能够更加容易地充满浇注系统的整个腔体。
(2降低最大收缩率。
最大收缩率可以体现塑料放大镜在冷却阶段能否均匀收缩,经仿真分析可以得出最大体积的收缩率在浇注系统的优化前后分别为19.8%和10.2%,表明经过优化后,塑料放大镜制品在冷却阶段可均匀收缩,有效地提高了塑料放大镜注射成型的质量。
(3降低整体翘曲变形量。
仿真结果表明,优化前后整体翘曲变形量分别为5.434 mm和3.245 mm,总体翘曲变形量得到了降低,使塑料放大镜制品的各个区域收缩比较均匀,从而能够提高成型放大镜的尺寸精度。
综上所述,经过对浇注系统工艺参数的优化,塑料放大镜成型质量得到较大的提高。
6结论综合塑料放大镜制品的使用需求和塑料成型特点,利用MATLAB软件对浇注系统进行优化设计。
通过对工艺参数的进一步优化,从而使塑料熔体能够具有较好的平衡性,最终提高塑料制品的性能。
参考文献[1]丛穆,江梅.CAE技术在汽车塑料件生产中的应用[J].汽车工艺与材料,2002 (8/9:83–87.[2]张维合.注塑模具设计实用教程[M].北京:化学工业出版社,2007.[3]曹阳根,傅意蓉.IC封装模流道平衡CAE应用[J].模具工业,2004(5:34–37.[4]陆如辉,訾炳涛,孙福良,等.镁合金齿轮箱压铸模设计与压铸工艺[J].特种铸造及有色合金,2005,25(9:544–545.OPTIMAL DESIGN FOR GATING SYSTEM OF PLASTICS MOLD BASED ON MATLABJiang Feizhou , Han Jiahao(Lianyungang V ocational Technical School Electrical and Mechanical Engineering College, Lianyungang222006, China ABSTRACT MATLAB software was used to design the gating system of magnifying glass plastic optimally. Process parameters of plastic mold gating system and the mold structure were optimized, thereby the passing rate of plastic magnifying glass was increased.KEYWORDS MATLAB, plastic mold, gating system, optimal design帝人推CFRP大规模生产技术及中间材料日本帝人公司宣布,该公司已拥有了一项用于碳纤维增强塑料(CFRP的大规模生产技术,使得一次生产循环所用的时间不到1 min。