先进航空发动机关键制造技术研究
航空发动机效率提升研究及优化措施分析

航空发动机效率提升研究及优化措施分析航空发动机效率的提升是航空产业发展的重要课题之一。
随着对环境保护和能源效率的需求不断增加,航空发动机的效率优化成为了关键的研究领域。
本文将讨论航空发动机效率的相关概念、研究方法以及现有的优化措施,并对未来的发展进行前瞻性展望。
首先,我们需要明确航空发动机效率的概念。
航空发动机效率是指在单位时间内产生的动力输出与所消耗的燃料能量之间的比值。
通过提高航空发动机的效率,可以减少燃料的消耗量,降低航空运输对能源的依赖,同时也能减少对环境的污染。
目前,航空发动机效率提升的研究主要集中在以下几个方面:1. 燃料燃烧效率的提高:通过改进燃烧室的设计和燃料注入系统,优化燃料与空气的混合过程,可以提高燃料的燃烧效率。
此外,采用燃料增压系统和高效的压缩机,可以提高整个燃烧过程中的压缩比,进一步提高燃烧效率。
2. 减少内部损失:航空发动机内部存在着多种损失,如摩擦损失、冷却损失、机械损失等。
通过改进涡轮机的结构和材料,减少叶轮和导叶之间的摩擦损失;优化冷却系统,提高冷却效率,减少冷却损失;采用先进的机械设计和材料,降低机械损失。
这些措施可以显著减少内部损失,提高航空发动机的效率。
3. 废气再利用:航空发动机在燃烧过程中会产生大量废气。
通过在废气排放中回收能量,如采用废气涡轮增压、废气余热回收等技术,可以提高发动机的能量利用率,进一步提高效率。
除了以上的研究领域,航空发动机效率提升还面临着一些挑战。
首先,高效率往往伴随着高温和高压,在设计和制造方面会面临更高的要求;其次,航空发动机的能效提升需要综合考虑安全性、可靠性和经济性等方面的因素,需要协调各种技术和指标的平衡。
未来,航空发动机效率提升的发展方向是多方面的。
一方面,随着新材料、新工艺的出现,航空发动机的设计和制造将更加先进和精细化,进一步提高效率;另一方面,航空发动机将更加智能化,通过数据分析和预测,实现优化运行和维护,进一步提升效率。
航空发动机叶片关键技术发展现状分析
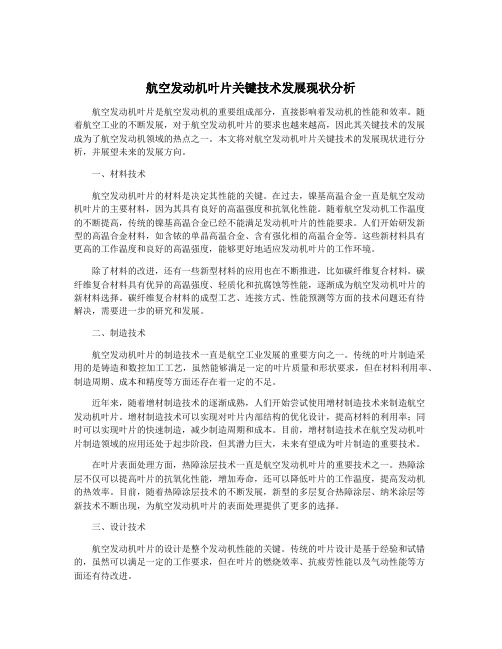
航空发动机叶片关键技术发展现状分析航空发动机叶片是航空发动机的重要组成部分,直接影响着发动机的性能和效率。
随着航空工业的不断发展,对于航空发动机叶片的要求也越来越高,因此其关键技术的发展成为了航空发动机领域的热点之一。
本文将对航空发动机叶片关键技术的发展现状进行分析,并展望未来的发展方向。
一、材料技术航空发动机叶片的材料是决定其性能的关键。
在过去,镍基高温合金一直是航空发动机叶片的主要材料,因为其具有良好的高温强度和抗氧化性能。
随着航空发动机工作温度的不断提高,传统的镍基高温合金已经不能满足发动机叶片的性能要求。
人们开始研发新型的高温合金材料,如含铱的单晶高温合金、含有强化相的高温合金等。
这些新材料具有更高的工作温度和良好的高温强度,能够更好地适应发动机叶片的工作环境。
除了材料的改进,还有一些新型材料的应用也在不断推进,比如碳纤维复合材料。
碳纤维复合材料具有优异的高温强度、轻质化和抗腐蚀等性能,逐渐成为航空发动机叶片的新材料选择。
碳纤维复合材料的成型工艺、连接方式、性能预测等方面的技术问题还有待解决,需要进一步的研究和发展。
二、制造技术航空发动机叶片的制造技术一直是航空工业发展的重要方向之一。
传统的叶片制造采用的是铸造和数控加工工艺,虽然能够满足一定的叶片质量和形状要求,但在材料利用率、制造周期、成本和精度等方面还存在着一定的不足。
近年来,随着增材制造技术的逐渐成熟,人们开始尝试使用增材制造技术来制造航空发动机叶片。
增材制造技术可以实现对叶片内部结构的优化设计,提高材料的利用率;同时可以实现叶片的快速制造,减少制造周期和成本。
目前,增材制造技术在航空发动机叶片制造领域的应用还处于起步阶段,但其潜力巨大,未来有望成为叶片制造的重要技术。
在叶片表面处理方面,热障涂层技术一直是航空发动机叶片的重要技术之一。
热障涂层不仅可以提高叶片的抗氧化性能,增加寿命,还可以降低叶片的工作温度,提高发动机的热效率。
目前,随着热障涂层技术的不断发展,新型的多层复合热障涂层、纳米涂层等新技术不断出现,为航空发动机叶片的表面处理提供了更多的选择。
激光加工工艺在航空发动机叶片制造中的应用研究
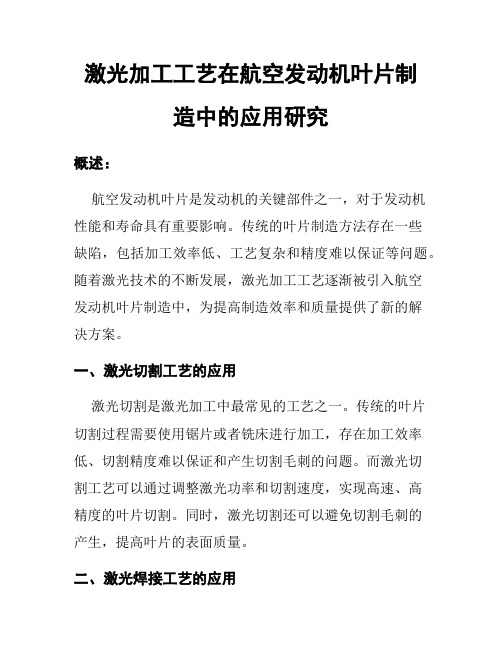
激光加工工艺在航空发动机叶片制造中的应用研究概述:航空发动机叶片是发动机的关键部件之一,对于发动机性能和寿命具有重要影响。
传统的叶片制造方法存在一些缺陷,包括加工效率低、工艺复杂和精度难以保证等问题。
随着激光技术的不断发展,激光加工工艺逐渐被引入航空发动机叶片制造中,为提高制造效率和质量提供了新的解决方案。
一、激光切割工艺的应用激光切割是激光加工中最常见的工艺之一。
传统的叶片切割过程需要使用锯片或者铣床进行加工,存在加工效率低、切割精度难以保证和产生切割毛刺的问题。
而激光切割工艺可以通过调整激光功率和切割速度,实现高速、高精度的叶片切割。
同时,激光切割还可以避免切割毛刺的产生,提高叶片的表面质量。
二、激光焊接工艺的应用叶片的制造过程中需要进行各部件的焊接,传统的焊接方法往往存在焊接接头强度不高、焊接变形严重和焊接精度难以控制等问题。
而激光焊接工艺具有高能量密度、小熔区和热影响区、焊缝宽度可控等优势,可以有效解决传统焊接方法存在的问题。
通过激光焊接技术,可以实现叶片各部件的高质量焊接,提高叶片的整体强度和稳定性。
三、激光打孔工艺的应用叶片在制造过程中需要进行各种孔的加工,传统的孔加工方法往往存在加工精度难以保证、孔壁质量差等问题。
激光打孔工艺可以通过调整激光功率和加工参数,实现高精度的叶片孔加工。
激光打孔具有加工速度快、孔壁质量好和无需后续加工等优势,可以提高叶片的加工效率和质量。
四、激光刻蚀工艺的应用激光刻蚀是一种通过激光束直接蚀刻叶片表面的工艺。
传统的刻蚀方法往往存在加工时间长、刻蚀深度难以控制和操作复杂等问题。
而激光刻蚀工艺可以通过调整激光功率和刻蚀参数,实现高精度、高效率的叶片表面刻蚀。
激光刻蚀具有加工速度快、刻蚀深度可控和操作简单等优势,可以实现叶片表面的纹理加工和功能性图案的刻蚀。
五、激光熔化成形工艺的应用激光熔化成形是通过激光束对叶片材料进行熔化,并利用表面张力和气流的作用实现材料的流动和成形。
航空发动机关键制造技术

件 制 造 过 程 的 专 业 化 成 套 制 造 技 术
等 。 本 期 主 题 策 划 了 复 合 材 料 加 工
技 术 、 整 体 叶 盘 制 造 技 术 、 以 及 新 技 术 新 工 艺 新装 备 希 期 读 者对 这
,
些 关 键 技 术 能 有 所 了 解 。 策 划 人 : 李 华 翔
造 中 主 要 用 于 压 气 机 及 涡 轮 机 的 各
类 机 匣 、 压 气 机 盘 及 涡 轮 盘 、 涡 轮
轴 和 压 气 机 轴 等 复 杂 构 件 的 加 工 。 高 效 精 密 切 削 、 变 形 补 偿 、 自 适 应
加工 ,
以 及 抗 疲 劳 制 造 等 技 术 的 研
特 别 策 划 航空 发 动机 关键制 造技 术 :
先进 航 空 发 动 机关 键 制 造 技 术 包 括 轻 量 化 整 体 化新 型 冷 却 结 构
、
件 制 造 技 术 新 材 料 构 件 制 造 技 ,
术 航 空 发 动 机 制 造 新 技 术 新 工 ,
艺 航空 发 动 机零 部件 的 无 损 检 测 ,
技 术 , 以 及 造 技 术 。
轻量 化 、 整 体 化 新 型 冷 却 结 构 件 制 造 技 术 包 括 : 整 体 叶 盘 制 造 技 术 , 整 体 叶 环 ( 无 盘 转 子)制 造 技 术 , 大 小 叶 片 转 子 制 造 技 术 , 发 动 机 机 匣 制 造 技 术 , 宽 弦 风 扇 叶 片 制 造 技
究 和 应 用 在 新 代 一 发 动 机 的 加 工 中
需 求 迫 切 。
另 外 还 有 特 种 加 工 技 术 特 种 ,
焊 接 技 术 热 障 涂 层 技 术 快 速 原
用于航空发动机的涡轮叶片材料及制造技术研究
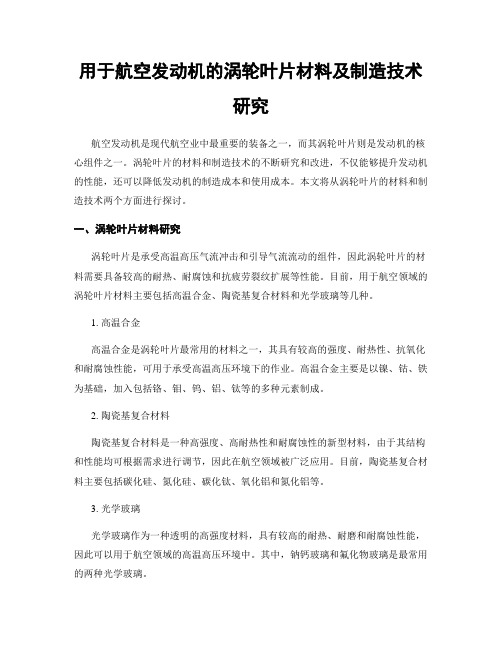
用于航空发动机的涡轮叶片材料及制造技术研究航空发动机是现代航空业中最重要的装备之一,而其涡轮叶片则是发动机的核心组件之一。
涡轮叶片的材料和制造技术的不断研究和改进,不仅能够提升发动机的性能,还可以降低发动机的制造成本和使用成本。
本文将从涡轮叶片的材料和制造技术两个方面进行探讨。
一、涡轮叶片材料研究涡轮叶片是承受高温高压气流冲击和引导气流流动的组件,因此涡轮叶片的材料需要具备较高的耐热、耐腐蚀和抗疲劳裂纹扩展等性能。
目前,用于航空领域的涡轮叶片材料主要包括高温合金、陶瓷基复合材料和光学玻璃等几种。
1. 高温合金高温合金是涡轮叶片最常用的材料之一,其具有较高的强度、耐热性、抗氧化和耐腐蚀性能,可用于承受高温高压环境下的作业。
高温合金主要是以镍、钴、铁为基础,加入包括铬、钼、钨、铝、钛等的多种元素制成。
2. 陶瓷基复合材料陶瓷基复合材料是一种高强度、高耐热性和耐腐蚀性的新型材料,由于其结构和性能均可根据需求进行调节,因此在航空领域被广泛应用。
目前,陶瓷基复合材料主要包括碳化硅、氮化硅、碳化钛、氧化铝和氮化铝等。
3. 光学玻璃光学玻璃作为一种透明的高强度材料,具有较高的耐热、耐磨和耐腐蚀性能,因此可以用于航空领域的高温高压环境中。
其中,钠钙玻璃和氟化物玻璃是最常用的两种光学玻璃。
二、涡轮叶片制造技术研究合适的涡轮叶片材料是涡轮叶片的基础,而制造技术则直接决定着叶片的质量和性能。
目前,涡轮叶片的常见制造技术包括精密铸造技术、热等静压成型技术、超声波焊接技术等。
1. 精密铸造技术精密铸造技术是现代涡轮叶片制造中最常见的一种技术,其主要原理是在对模具进行预处理和设计后,在高温下将熔融金属注入模具中,并通过精密控制形成叶片的整体结构。
精密铸造技术能够在保证叶片性能的同时,大大降低叶片制造的成本。
2. 热等静压成型技术热等静压成型技术是一种通过将原料放入容器中直接加热处理以制造高质量涡轮叶片的技术。
在加热的过程中,原料将保持某种特定的形状和结构,并在以后的冷却过程中形成较高质量的叶片。
大型飞机用发动机的特点及关键制造技术.
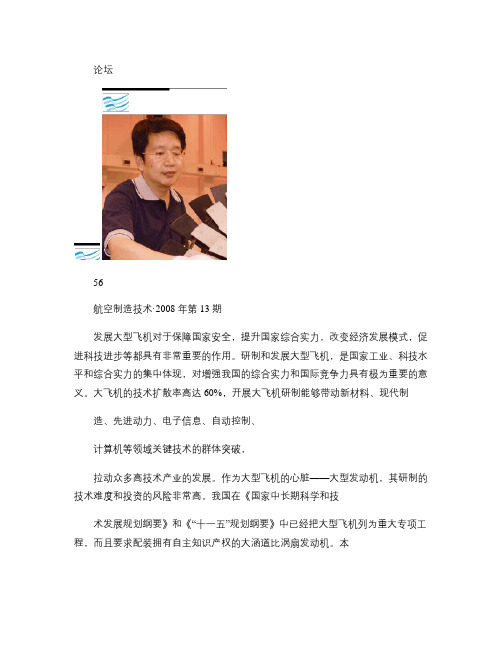
论坛56航空制造技术·2008 年第13 期发展大型飞机对于保障国家安全,提升国家综合实力,改变经济发展模式,促进科技进步等都具有非常重要的作用。
研制和发展大型飞机,是国家工业、科技水平和综合实力的集中体现,对增强我国的综合实力和国际竞争力具有极为重要的意义。
大飞机的技术扩散率高达60%,开展大飞机研制能够带动新材料、现代制造、先进动力、电子信息、自动控制、计算机等领域关键技术的群体突破,拉动众多高技术产业的发展。
作为大型飞机的心脏——大型发动机,其研制的技术难度和投资的风险非常高。
我国在《国家中长期科学和技术发展规划纲要》和《“十一五”规划纲要》中已经把大型飞机列为重大专项工程,而且要求配装拥有自主知识产权的大涵道比涡扇发动机。
本文结合大飞机用发动机的特点对其关键制造技术作了初步探讨和分析,并对我国研制和生产大飞机用发动机提出了几点参考建议。
大飞机用发动机的性能特点所谓大飞机,是指起飞总重量超过100t 的运输类飞机,包括军用和民用大型运输机,也包括150座以上的干线客机。
大飞机的发动机应该具备高可靠性、长寿命、节能环保以及低成本运行等基本要求,在发动机的结构上,具有大涵道比、零件整体化、轻量化等特点并尽可能多地采用复合材料。
与军用战斗机发动机相比,大飞机用发动机的主要特点具体表现为:(1)安全可靠性高。
安全性主要指低的空中停车率(现已降至0.002~0.005次/1000飞行小时)。
为满足这一要求,大飞机用发动机普遍采用了较大的核心机尺寸和较低的涡轮前工作温度。
大型飞机用发动机的特点及关键制造技术Characteristics of Aeroengine for Large Aircraft and Its ManufacturingTechnology西安航空发动机(集团)有限公司马建宁西北工业大学现代设计与集成制造技术教育部重点实验室张定华王增强李山吴宝海国外的成功经验和先进制造技术的发展表明,我国大飞机用航空发动机的研制必须将专业的制造技术与信息技术、管理技术进行有机地结合,并将计算机技术综合应用于设计、制造、检测、管理、销售、使用、服务等发动机研制的全过程。
先进航空发动机关键制造技术研究

先进航空发动机关键制造技术研究摘要:航空发动机是飞机的核心部分。
在21世纪,航空发动机的设计和制造技术体现出了国家的科技发展水平,随着科学技术的不断发展,国家对航空领域的重视程度越来越高,所以通过对我国现有的发动机制造水平进行研究,能够对先进的航空发动机制造技术进行分析,研究出先进的发动机制造技术,促进我国航空领域的不断发展。
关键词:航空发动机;关键技术;制造研究引言:航空发动机技术具有高技术、高投入、高风险的特性,一般来说,单台发动机的研发时间一般在十年到二十年左右,所耗费的资金大约是10亿到20亿。
从这些数据就能够看出航空发动机的重要性和难度。
我国的航空发动机技术的发展与先进国家相比,仍然存在着很大的距离,因此,要想令我国的发动机技术水平得到提升,就需要投入大量的经费去进行技术方面的研究,只有这样才能够令先进航空发动机关键制造技术得到更好的发展。
一、我国航空发动机的发展我国航空发动机经历了一个非常漫长的过程,航空发动机的作用就是为飞机提供推动力,在所有航空器进行工作的过程当中,航空发动机都是一个非常核心的部位,自从飞机研发成功之后,飞机的发动机也得到了飞速的发展,我国的航空业逐渐形成了各种各样、多种类、大范围的特点。
从我国航空发动机的发展历程来看,发动机经历了两个时期,一个是活塞发动机时期,另外一个是燃气涡轮发动机时期,从活塞发动机时期到燃气涡轮发动机十期,可以看出航空领域发生了质的飞跃。
我国进行航空发动机的研制工作是在新中国成立之后,新中国刚刚成立的时候,我国的科学技术水平简直就是一张白纸,从最初的模仿、改造到现在可以独立研发出高水平的航空发动机,我国的科技人员经历了一个非常漫长且坎坷的过程。
我国是世界上最大的发展中国家,航空发动机的事业直接体现出一个国家的国力标准和经济发展程度,如果一个国家没有先进的航空发动机事业,那么这个国家的航空事业便不会有大的成就,航空工业也不会得到迅速的发展。
二、航空发动机的制造工艺特点航空发动机的制造工艺特点主要有以下几个方面,分别是材料难加工,切除率大、形状与结构复杂、加工精度高。
航空航天先进制造技术与研发方案设计

航空航天先进制造技术与研发方案设计第1章先进制造技术概述 (3)1.1 航空航天工业背景 (3)1.2 先进制造技术发展现状 (4)1.3 航空航天先进制造技术的挑战与机遇 (4)第2章材料科学与航空航天制造 (5)2.1 高功能金属材料 (5)2.1.1 钛合金 (5)2.1.2 镍基高温合金 (5)2.1.3 金属基复合材料 (5)2.2 复合材料及其制造技术 (5)2.2.1 碳纤维增强复合材料 (5)2.2.2 玻璃纤维增强复合材料 (5)2.2.3 复合材料制造技术 (5)2.3 新型航空航天材料发展趋势 (6)2.3.1 陶瓷基复合材料 (6)2.3.2 纳米材料 (6)2.3.3 智能材料 (6)2.3.4 生物基复合材料 (6)第3章高精度加工技术 (6)3.1 数控加工技术 (6)3.1.1 数控铣削加工 (6)3.1.2 数控车削加工 (6)3.1.3 数控磨削加工 (6)3.2 激光加工技术 (7)3.2.1 激光切割 (7)3.2.2 激光焊接 (7)3.2.3 激光打标与雕刻 (7)3.3 电火花加工技术 (7)3.3.1 精密电火花成形加工 (7)3.3.2 电火花线切割加工 (7)3.3.3 多轴联动电火花加工 (7)第4章高效自动化装配技术 (7)4.1 自动化装配系统 (7)4.1.1 自动化装配系统组成 (8)4.1.2 自动化装配原理 (8)4.1.3 航空航天制造业应用案例 (8)4.2 技术在装配中的应用 (8)4.2.1 分类及特点 (8)4.2.2 路径规划与控制 (8)4.2.3 航空航天装配应用案例 (8)4.3 虚拟现实与增强现实技术在装配中的应用 (8)4.3.1 虚拟现实与增强现实技术原理 (8)4.3.2 虚拟现实与增强现实在装配中的应用 (9)4.3.3 航空航天装配应用案例 (9)第5章铸造与锻造技术 (9)5.1 铸造技术及其在航空航天领域的应用 (9)5.1.1 铸造技术概述 (9)5.1.2 航空航天领域铸造技术的应用 (9)5.2 锻造技术及其在航空航天领域的应用 (9)5.2.1 锻造技术概述 (9)5.2.2 航空航天领域锻造技术的应用 (9)5.3 高温合金锻造技术 (10)5.3.1 高温合金锻造技术概述 (10)5.3.2 高温合金锻造工艺 (10)5.3.3 高温合金锻造技术在航空航天领域的应用 (10)第6章焊接与连接技术 (10)6.1 激光焊接技术 (10)6.1.1 激光焊接原理与特点 (10)6.1.2 激光焊接在航空航天领域的应用 (10)6.1.3 激光焊接技术的发展趋势 (10)6.2 电子束焊接技术 (11)6.2.1 电子束焊接原理与特点 (11)6.2.2 电子束焊接在航空航天领域的应用 (11)6.2.3 电子束焊接技术的发展趋势 (11)6.3 超声波焊接技术 (11)6.3.1 超声波焊接原理与特点 (11)6.3.2 超声波焊接在航空航天领域的应用 (11)6.3.3 超声波焊接技术的发展趋势 (11)6.4 气动连接技术 (11)6.4.1 气动连接原理与特点 (11)6.4.2 气动连接在航空航天领域的应用 (11)6.4.3 气动连接技术的发展趋势 (12)第7章表面处理与涂层技术 (12)7.1 表面处理技术 (12)7.1.1 机械表面处理技术 (12)7.1.2 化学表面处理技术 (12)7.1.3 激光表面处理技术 (12)7.2 涂层技术 (12)7.2.1 热喷涂技术 (12)7.2.2 物理气相沉积技术 (12)7.2.3 化学气相沉积技术 (12)7.3 防腐蚀与耐磨涂层技术 (13)7.3.1 防腐蚀涂层技术 (13)7.3.2 耐磨涂层技术 (13)7.3.3 复合涂层技术 (13)第8章检测与质量控制技术 (13)8.1 无损检测技术 (13)8.1.1 超声波检测技术 (13)8.1.2 射线检测技术 (13)8.1.3 磁粉检测技术 (13)8.1.4 涡流检测技术 (14)8.2 在线监测与故障诊断技术 (14)8.2.1 振动监测技术 (14)8.2.2 声学监测技术 (14)8.2.3 温度监测技术 (14)8.2.4 油液监测技术 (14)8.3 质量控制与管理技术 (14)8.3.1 统计过程控制技术 (14)8.3.2 质量管理体系 (14)8.3.3 数字化质量监控技术 (14)8.3.4 智能化质量控制技术 (15)第9章绿色制造与可持续发展 (15)9.1 航空航天工业绿色制造概述 (15)9.2 低碳制造技术 (15)9.3 循环经济与资源再利用技术 (15)第10章研发方案设计与案例分析 (15)10.1 研发方案设计流程与方法 (15)10.1.1 研发方案设计概述 (15)10.1.2 研发方案设计流程 (16)10.1.3 研发方案设计方法 (16)10.2 航空航天先进制造技术集成与应用案例 (16)10.2.1 高功能复合材料制造技术 (16)10.2.2 高精度加工技术 (16)10.2.3 数字化制造与智能制造技术 (16)10.2.4 绿色制造技术 (16)10.3 航空航天制造企业研发战略与未来展望 (16)10.3.1 航空航天制造企业研发战略 (16)10.3.2 航空航天先进制造技术的未来发展趋势 (16)10.3.3 航空航天制造业面临的挑战与机遇 (16)10.3.4 航空航天制造企业研发方向与布局 (16)第1章先进制造技术概述1.1 航空航天工业背景航空航天工业是国家战略性高技术产业,具有极高的技术含量和综合集成能力。
- 1、下载文档前请自行甄别文档内容的完整性,平台不提供额外的编辑、内容补充、找答案等附加服务。
- 2、"仅部分预览"的文档,不可在线预览部分如存在完整性等问题,可反馈申请退款(可完整预览的文档不适用该条件!)。
- 3、如文档侵犯您的权益,请联系客服反馈,我们会尽快为您处理(人工客服工作时间:9:00-18:30)。
先进航空发动机关键制造技术研究
作者:霍羿达王志东马文浩
来源:《科学与财富》2020年第21期
摘要:航空发动机是飞机的核心部分。
在21世纪,航空发动机的设计和制造技术体现出了国家的科技发展水平,随着科学技术的不断发展,国家对航空领域的重视程度越来越高,所以通过对我国现有的发动机制造水平进行研究,能够对先进的航空发动机制造技术进行分析,研究出先进的发动机制造技术,促进我国航空领域的不断发展。
关键词:航空发动机;关键技术;制造研究
引言:
航空发动机技术具有高技术、高投入、高风险的特性,一般来说,单台发动机的研发时间一般在十年到二十年左右,所耗费的资金大约是10亿到20亿。
从这些数据就能够看出航空发动机的重要性和难度。
我国的航空发动机技术的发展与先进国家相比,仍然存在着很大的距离,因此,要想令我国的发动机技术水平得到提升,就需要投入大量的经费去进行技术方面的研究,只有这样才能够令先进航空发动机关键制造技术得到更好的发展。
一、我国航空发动机的发展
我国航空发动机经历了一个非常漫长的过程,航空发动机的作用就是为飞机提供推动力,在所有航空器进行工作的过程当中,航空发动机都是一个非常核心的部位,自从飞机研发成功之后,飞机的发动机也得到了飞速的发展,我国的航空业逐渐形成了各种各样、多种类、大范围的特点。
从我国航空发动机的发展历程来看,发动机经历了两个时期,一个是活塞发动机时期,另外一个是燃气涡轮发动机时期,从活塞发动机时期到燃气涡轮发动机十期,可以看出航空领域发生了质的飞跃。
我国进行航空发动机的研制工作是在新中国成立之后,新中国刚刚成立的时候,我国的科学技术水平简直就是一张白纸,从最初的模仿、改造到现在可以独立研发出高水平的航空发动机,我国的科技人员经历了一个非常漫长且坎坷的过程。
我国是世界上最大的发展中国家,航空发动机的事业直接体现出一个国家的国力标准和经济发展程度,如果一个国家没有先进的航空发动机事业,那么这个国家的航空事业便不会有大的成就,航空工业也不会得到迅速的发展。
二、航空发动机的制造工艺特点
航空发动机的制造工艺特点主要有以下几个方面,分别是材料难加工,切除率大、形状与结构复杂、加工精度高。
材料难加工,切除率大主要指的是航空发动机核心的转子部分,通常采用的是钛合金高温合金等非常难以加工的材料,在切削的过程当中,会加剧刀具切削刃的磨损程度。
另外,在加工的过程当中,很有可能有绝大部分的材料都会被切除掉,因此,如何在航空发动机核心转子部件的加工过程当中提高加工精度,令加工表面的更加完整就十分的重要[1]。
形状与结构复杂主要指的是在发动机中采用的是宽弦空心风扇叶片,这些结构非常的复杂,所以现有的制造工艺方法无法满足实际生产发动机的需要,因此必须针对不同的零件结构来进行工作,只有这样才能够探索新的工艺和新技术,不斷提高复杂构件的制作水平,从而降低航空发动机的成本。
加工精度高主要指的是航空发动机是航空器的核心组成部分,因此,航空发动机的精度直接决定了航空器的运行安全,因此,我国发动机零部件的生产过程中应该注重加工精度,只有这样才能够令航空发动机的研制水平得到提高,从而不断促进航空发动机研发水平的进步。
三、对我国先进发动机制造技术的建议
(一)不断提高发动机制造技术的技术水平
在航空发动机发展的过程当中,应该加大技术研究,只有这样才能够令先进的发动机技术被应用到航空发动机的研发过程当中,国家已经对先进的发动机技术研发进行了支持,通过这种方式能够促进我过高性能发动机的制造技术水平的不断提升,有利于促进我国高性能发动机制造技术的持续发展。
在高性能发动机研发的过程当中,需要科研人员吸收国外先进的制造业技术,并且脚踏实地,依据我国航空业发展的国情去发展我国的航空制造业技术。
我国的航空制造业技术与发达国家相比仍然存在着一定的差距,所以这就需要我国的科研人员以科学发展观为导向,学习先进的理论知识,不断提高自己的专业实践能力,从而令发动机制造的技术决定性掌握在自己的手里,不断形成我国特色的航空制造业体系,在航空制造业发展的过程当中发挥出自身的力量,不断促进我国航空发动机的设计与制造水平,从而改进在制造过程当中存在的不足现象,提高发动机制造技术含量[2]。
(二)探索航空发动机的研究项目
在航空发动机发展的过程当中,相应的科研人员一定要对未来的发展前景和创新环境条件进行探索,不断探索航空发动机的研究项目,在国家的大力支持下,和科研人员的不断努力中,在最短的时间内突破在航空发动机发展的过程当中面临的一系列的问题,从而令我国发动机制造技术能够实现质的飞跃。
在不断探索航空发动机的研究项目过程当中,以我国的工业技
术发展为基础,从而进行深入的剖析与研讨,航空发动机制造技术进行分析,令发动机制造的技术探索性能得到提高,从而令新一代的发动机性能得到改进。
(三)采用先进的航空发动机制造技术新工艺
在航空发动机制造技术发展的过程当中,新型结构件精密制胚技术、先进的切削技术、特种加工技术、特种焊接技术等技术都得到了一定的发展,因此,需要将这些技术应用到航空发动机制造的过程当中,只有这样才能够令航空发动机制造当中的关键技术水平得到更好的提升。
采用新型结构件精密支配技术,能够有效地避免毛坯件发生损坏的现象,从而令精铸件、精锻件、单晶和定向凝固精筑建以及快速凝固,令制胚毛胚在航空发动机的制造过程当中发挥出重要的作用[3]。
采用先进的切削技术,能够令典型的难加工材料——钛合金高温合金及金属基复合材料等新材料进行加工,通过先进的切削技术,能够确定加工的精度和表面完整性,所以在新一代航空发动机的切削加工的工作当中,利用先进的切削技术,能够提高加工效率和加工质量,令加工的自动化水平得到提高,从而能够研制出高精度、高刚性的磨削加工技术,不断促进航空发动机制造技术新工与水平的提升。
采用特种加工技术,能够避免外力因素的影响,从而为形成技术创新而开阔新的途径。
采用特种焊接技术,能够确保航空发动机的结构完整性,特种焊接技术能够令航空发动机制造当中的成本降低,同时也能够满足可靠性的要求,所以摩擦焊接技术在航空发动机制造过程当中已经成为了非常关键的一种技术。
采用热障涂层技术能够进行高温防护隔热,所以在航空发动机制造业发展的过程当中,热障涂层技术得到了广泛的应用。
四、结束语
在先进航空发动机关键技术制造研究的过程当中,一定要令发动机制造的技术决定性、技术探索性、技术突破性和技术发展性得到凸显,从而令我国航空发动机的技术水平能够得到提升。
航空发动机的技术水平直接影响着我国科研研发的方向以及科研研发的动力,因此,制造高性能的发动机是我国制造业未来发展的一个大方向,在发动机制造的研发过程当中,一定要投入大量的资金,国家应该要给予大力的支持,通过吸收国外先进的技术理念,脚踏实地,结合我国的国情,令我国现代化的航空技术水平能够得到提升,推动我国航空行业的发展,在经济社会发展的过程当中,航空发动机的设计与制造水平能够令我国航空领域的发展水平越来越高,从而不断提高我国的国际竞争力。
参考文献:
[1] 黄维,黄春峰,王永明,等. 先进航空发动机关键制造技术研究[J]. 国防制造技术,2009(03):42-48.
[2] 兰明亮,杨吉祥,徐和,等. 先进航空发动机关键制造技术研究[J]. 华东科技:学术版,2015(9):16-16.
[3] 张定华,黄新春. 航空发动机关键构件制造可靠性技术研究[J]. 航空制造技术,2015(17):26-29.。