有害物质风险评估程序通用版
危害识别和风险评估程序

危害识别和风险评价管理程序一、目的二、范围三、职责HSE管理者代表:对危害识别与风险评价工作直接负责,确定及审批管理程序、危害识别及风险评价的结果。
安全环保部门和HSE管理人员:组织开展危害识别和风险评价工作,负责对各单位的工作进行指导、控制和更新。
省公司安全环保部门负责编制发布和危害识别和风险评价管理程序,对全省工作进行指导,负责组织相关专业技术人员对全省的识别和评价结果进行总的分析和认证。
各市地分公司的安全环保部门及HSE管理人员负责本公司各项工作的开展。
其它各部门:参与开展危害识别与风险评价的查找、分析、控制和更新工作。
所有员工:接受安全环保部门组织的培训,参与危害识别和风险控制的查找、分析、控制和更新工作。
四、定义危害:可能造成人员伤害、职业病、财产损失、环境破坏或其组合的根源或状态。
危害识别:认知危害的存在并确定其特征的过程。
风险:特定危害事件发生的可能性及后果严重性的结合。
风险评价:依照现有的专业经验、评价标准和准则,评价风险程度并确定风险是否可容忍的全过程。
事故:造成死亡、职业病、财产损失、环境破坏的事件。
事件:导致或可能导致事故的事情。
五、工作程序危害识别及风险评估程序流程,参照附录1,具体步骤概括如下:1、成立评估小组省、市、县公司及所属部门应成立有专业技术人员和操作人员参加的评估小组,所有评估人员需经过专门培训并有能力、资格开展职业安全健康的危害识别、风险评估和指导工作,同时各部门也应要求其他员工参与危害的确定。
2、选择和确定评估范围和对象评估小组应首先识别出公司从事的经营活动、产品或服务范围,包括规划、设计、建设、投用、采购、销售、产品、储运、设备、设施、服务、检维修、消防、合约商的服务和设备,以及行政和后勤等活动的全过程。
所有可能导致重要危害的活动,包括非常规活动如检维修等都必须充分得到识别。
在确定评估范围后,评估小组可按下列方法,确定评估对象:——按地理区域或部门;——按装置、设备、设施;——按作业任务。
危害风险评估程序

XXX-SOP-036
危害风险评估管理规范
版本/版次
A/0
页次
2/6
2008年10月6日制订
核准
审查
制订
2008年10月8日生效
(2)危害是指必须预以控制的、可能发生的、会对消费者健康造成损害的危害。风险评分≥5分的,可判为显著危害。
总在发生
高
4
5
6
7
经常发生
中等
3
4
5
6
偶尔发生
低
2
3
4
5
历史上未发生
产品在流水线上依次过紫外灯,然后入胶袋
紫外线消毒灯
15.包装
注意外箱注明日期,包装合格后,按照包装的顺序摆放在卡板上.
流水线
18.QA:
按抽样计划进行抽检,按照成品检验规范进行检验,
19.成品仓
按照客户、订单、ITEM进行分类摆放。
20装箱
按照要求装箱
文件编号
XXX-SOP-036
危害风险评估管理规范
版本/版次
A/0
页次
5/6
2008年10月6日制订
核准
审查
制订
2008年10月8日生效
6、危害风险分析
(1)
成分及加工步骤
(2)
确定在此步骤出现的潜在危害
(3)危害风险评估
(4)
对第(3)列判断提出理由和依据
(5)
防止显著危害的措施
危害发生的可能性
对人体危害程度
是否为显著危害
1美
耐皿粉
验收
生物性
无
化学性
3.2风险分析评估标准
根据产品安全危害造成不良健康后果的严重性及发生的可能性,对每种产品安全危害进行评价和分类,应指明在原料、加工和分销中哪个环节每种食品安全危害可能被引入、产生或增加程度。
hsf有害物质管理风险评估表

无 无 直接接触 无 直接接触
直接接触
低 低 高 低 低 高 低 低 高 低 中等 中等 中等 中等 中等 中等
中等 中等 高 低
中等
中等
注意防止破袋预防污染 检查卡板防止刺坏的包装袋 每批取样用XRF测试确认 注意防止破袋预防污染 注意防止破袋预防污染
1 注意防止破袋预防污染 注意防止破袋预防污染
直接接触 无
16
工程检
工程検査
XFR检测仪器
无
缝袋机
无
17
包装袋印字
包装
插车/卡板
无
18
出货
出货
货车
无
备注: ➀ 生产□ 移动 信息流♀ 储存◇ 检査☐
中等 中等 中等
中等 中等 中等 低风险 中等 中等 中等 中等 低 中等 中等 低 中等 中等 中等 中等 低 中等
中等
中等 中等 低
高
低
低
低
采用金属材料耐磨 采用金属材料耐磨
有害物质管理风险评估
批准
颜色:所有
歩骤 生产流程与流程图 受注/订单
1 评审
过程描述
机器/设备装置、 是否与材料、 易耗品、材料 中间物料、成 ROHS管理风险等级 管理要求与措施
品直接接触
传真机
无
受 注 / 订 单 评 电子邮件/电脑 审
无
打印机
无
中等
准确接受客户要求,并进行内部评审,及时 将客户要求转化内部管控要求
采用耐磨型金属材料
上一页
9 材料/颜料/添
加剂定量
挤出
8
冷却
9
10
沥水干燥
11
切粒
12
有害物质风险评估工作程序

有害物质风险评估工作程序引言随着人类对环保意识的提高以及工业化进程的不断加速,涉及到人类生产和生活的各种有害物质的种类和数量不断增多,与之相关的风险也在不断增加。
因此,对有害物质的风险评估工作成为了当前环境保护和工业安全领域面临的一个重要问题。
本文将介绍有害物质风险评估工作的基本流程和注意事项。
有害物质风险评估的基本流程第一步:确定目标人群和暴露途径有害物质的危险性与其接触方式和接触量密切相关,因此在评估有害物质的风险时必须首先确定有哪些人群会接触这种有害物质以及接触途径。
例如,某些有害物质可能只对从事相关工作的人员有危害,而对于普通消费者则没有影响;有些有害物质只有通过食入或者呼吸等途径才会对人体产生影响,因此要评估其风险必须明确相关的暴露途径。
第二步:收集有害物质的毒理学数据和流行病学数据评估有害物质风险的过程中需要收集有害物质的毒理学数据和流行病学数据。
毒理学数据通常包括各种动物的实验数据和人体研究数据,主要用来确定有害物质的毒性程度、剂量-效应关系等参数;流行病学数据主要通过流行病学调查等方式获取,用来确定在实际人群中有害物质暴露所导致的健康影响。
第三步:确定曝露水平在评估有害物质的风险时还需要确定人体实际接触到有害物质的水平,通常包括内源性曝露和外源性曝露两种形式。
内源性曝露是指人体自身产生有害物质,外源性曝露则是指从环境或者饮食等途径摄入有害物质。
确定曝露水平是评估有害物质风险的重要一步,因为只有明确了实际曝露水平,才能正确评估风险。
第四步:风险特征描述和剂量-反应关系建立在确定了有害物质暴露水平后,还需要描述该物质的风险特征和建立其剂量-反应关系。
风险特征描述包括出现的健康影响的种类和程度等,而剂量-反应关系建立则是指根据毒理学数据建立有害物质对不同剂量的反应程度等数据,这些数据有助于评估不同曝露水平下的风险。
第五步:基于风险特征和剂量-反应关系进行风险评价在第四步确定了有害物质的风险特征和剂量-反应关系后,可以基于这些参数进行风险评价,以确定实际曝露水平下人体健康风险。
限制性物质污染风险评估程序
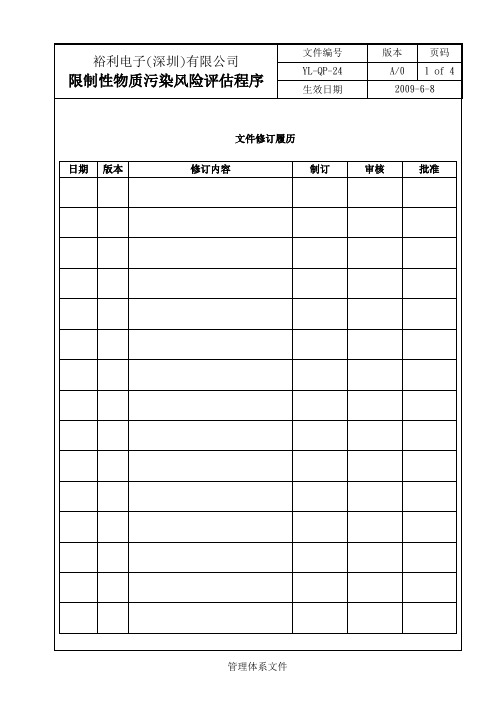
日期
版本
修订内容
制订
审核
批准
1.目的
通过对本司制程、供应商所提供的原材料及委托加工的产品(包括其加工的制程等)进行环境有害物质使用的风险性评估,对制程所使用的工治具,供应商所提供的原材料、委托外加工等进行选择,从而有效的防止本司制程及供应商所提供的原材料、委托加工过程中出现HSF不符合因素,达到逐步禁用或消减使用环境有害物质的目的。
6.1.2制程添加物供应商必须提供:真实有效并符合标准的相关物质的含量测试报告、MSDS(化学品必须)、有害物质不使用保证书及添加物本身的风险自评。
6.1.3辅助材料供应商必须提供:真实有效并符合标准的相关物质的含量测
试报告、有害物质不使用保证书、及其材料本身的风险评估。
6.1.4加工供应商必须提供:加工处理结果(如电镀)及处理过程中使用添加物、辅助材料的真实有效并符合标准的相关物质的含量测试报告、MSDS(化学品必须)、有害物质不使用保证书及其对自身(包括其处理结果与处理过程)的风险自评。
6.2.2制程添加物风险评估:
6.2.2.1包括制程中所有使用到的去渍油、除油、洗模水等添加物。
6.2.2.2根据供应商提供的相关物质的含量测试报告及MSDS等资料对添加物进行有害物质风险评估.此类物质对产品本身的化学性质并无影响,但对人体可能造成其他伤害,所以对其评估时除对其四项有害物质的评估外,必须根据MSDS对其伤害性进行评估,采购时优先选择对人体无伤害添加物。
4.2风险:指一种遭受损失的可能性。本司具体指制程或委托供应商加工处理过程中使用某种可能不符合客户环保要求的原材料、工治具及辅料而对公司造成损失的可能性。
4.3高风险:以危害物质控制标准为依据,产品中某项有害物质的含量与HSF要求标准值的百分比在71%以上者为高风险物料.(如:实测钢材料的含铅量为2800ppm、HSF要求标准值钢合金为3500ppm,2800:3500*% =80%;>71%,此物料则为高风险物料)。
有害物质风险评估工作程序
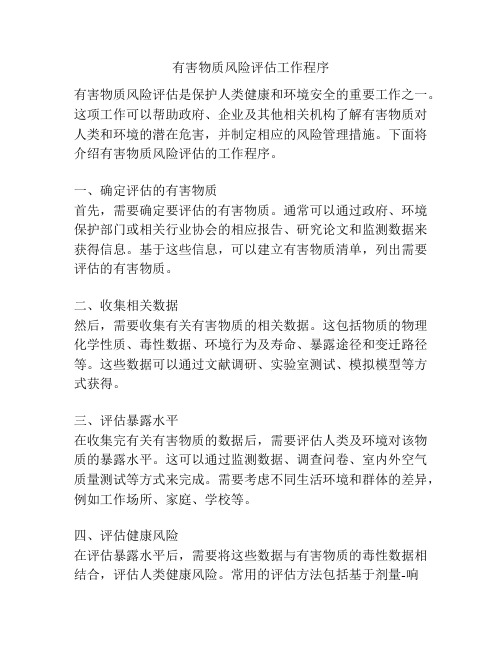
有害物质风险评估工作程序有害物质风险评估是保护人类健康和环境安全的重要工作之一。
这项工作可以帮助政府、企业及其他相关机构了解有害物质对人类和环境的潜在危害,并制定相应的风险管理措施。
下面将介绍有害物质风险评估的工作程序。
一、确定评估的有害物质首先,需要确定要评估的有害物质。
通常可以通过政府、环境保护部门或相关行业协会的相应报告、研究论文和监测数据来获得信息。
基于这些信息,可以建立有害物质清单,列出需要评估的有害物质。
二、收集相关数据然后,需要收集有关有害物质的相关数据。
这包括物质的物理化学性质、毒性数据、环境行为及寿命、暴露途径和变迁路径等。
这些数据可以通过文献调研、实验室测试、模拟模型等方式获得。
三、评估暴露水平在收集完有关有害物质的数据后,需要评估人类及环境对该物质的暴露水平。
这可以通过监测数据、调查问卷、室内外空气质量测试等方式来完成。
需要考虑不同生活环境和群体的差异,例如工作场所、家庭、学校等。
四、评估健康风险在评估暴露水平后,需要将这些数据与有害物质的毒性数据相结合,评估人类健康风险。
常用的评估方法包括基于剂量-响应关系的风险评估、无效剂量的测量、比较各种敏感性人群的风险等。
评估结果通常以急性和慢性风险比值、致癌风险等形式报告。
五、评估环境风险除了人类健康风险评估外,还需要评估有害物质对环境的潜在危害。
这涉及到有害物质在环境中的分布、降解和寿命等因素。
可以通过建立模拟模型、环境监测和生态学调查等来评估环境风险。
六、制定风险管理措施基于评估结果,需要制定相应的风险管理措施。
这可以包括禁止使用有害物质、限制使用量、改进生产工艺、提供个人防护用具等。
此外,还需要制定相应的监测计划,以跟踪有害物质的使用和暴露水平变化。
七、风险沟通与信息公开风险评估的结果需要及时向相关利益相关者沟通,包括政府、企业、公众和媒体等。
重要的是要使用易于理解的语言和形式向他们传达风险信息,以便他们能够正确理解和采取相应的行动。
有害物质管理程序(流程)

xxxXXXXXXXXXXXXXXXXXXXX 有限公司程序文件文件名称:有害物质管理程序文件编号:生效日期:版本号:适用范围:编制:审核:批准:文件制订/修改情况记录明确有害物质的管理标准,规范有害物质的识别、评价及控制,以确保高风险的物料、工艺、器具能得到有效的管制,减少其污染 HSF 产品的可能。
2适用范围:限公司内的各相关单位的有害物质管理过程。
3定义:3.1HS 物料/产品/器具(有害物质): 指的是相关的环保法规(如:RoHS、WEEE、REACH、食品卫生等)及其它适用标准或客户要求中禁止使用的材料(包括:物料、产品、工治具、机器设备、测试仪器、包装包器等);3.2HSF(有害物质减免): 指的是相关的环保法规(如:RoHS、WEEE、REACH、食品卫生等)及其它适用标准或客户要求中规定的任何材料对有害物质的减少或消除。
3.3有害物质的识别:是指对产品的提供过程及相关的物料产品器具等进行调查分析,明确其是否含有或可能会含有有害物质的过程。
4职责:4.1产品验证中心理化分析部:对相关部门申请的原材料,零部件及成品进行有害物质测试, 并负责对《RoHS 物料定期送检及监控方案》的维护更新。
4.2社会责任管理部负责HSF 标准及法律法规评价,形成《HSF 适用法规评价表》,并定期更新;有害物质管理标准的制定、修订及组织对含有害物质的物料及过程的识别和评价,形成《有害物质识别及评价总表》;负责有害物质管理体系内审及协助管理者代表组织有害物质管理评审。
4.3各分公司体系管理人员及品管部负责协助对本公司内有害物质的识别和评价。
4.4公司相关部门负责依管理标准对高风险物料、产品或过程的制定相应的管控方案来实施管控。
4.5物流管理中心及相关采购部门:负责评估和确认供应商对有害物质管控的能力及结果,监督供应商对有害物质的管控;负责从供应商处索取有害物质测试报告以及相关保证书,并负责对供应商进行有害物质控制的能力教育和培训。
危害辨识和风险评价控制程序范本(二篇)
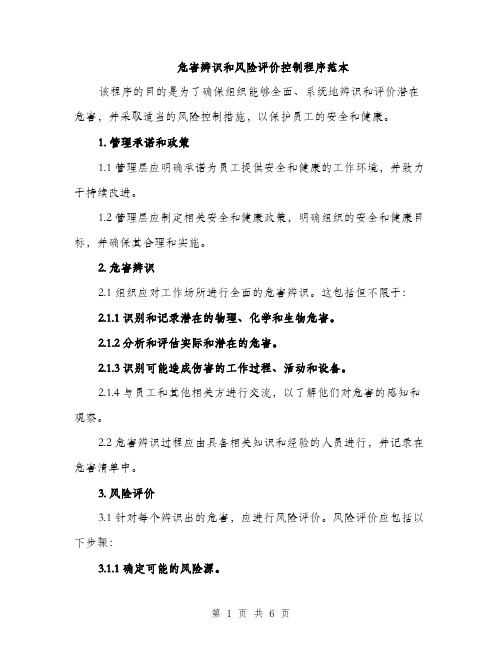
危害辨识和风险评价控制程序范本该程序的目的是为了确保组织能够全面、系统地辨识和评价潜在危害,并采取适当的风险控制措施,以保护员工的安全和健康。
1. 管理承诺和政策1.1 管理层应明确承诺为员工提供安全和健康的工作环境,并致力于持续改进。
1.2 管理层应制定相关安全和健康政策,明确组织的安全和健康目标,并确保其合理和实施。
2. 危害辨识2.1 组织应对工作场所进行全面的危害辨识。
这包括但不限于:2.1.1 识别和记录潜在的物理、化学和生物危害。
2.1.2 分析和评估实际和潜在的危害。
2.1.3 识别可能造成伤害的工作过程、活动和设备。
2.1.4 与员工和其他相关方进行交流,以了解他们对危害的感知和观察。
2.2 危害辨识过程应由具备相关知识和经验的人员进行,并记录在危害清单中。
3. 风险评价3.1 针对每个辨识出的危害,应进行风险评价。
风险评价应包括以下步骤:3.1.1 确定可能的风险源。
3.1.2 评估员工可能的接触程度和频率。
3.1.3 评估潜在的伤害情况和可能的后果。
3.1.4 评估现有的控制措施和管理措施,以确定其有效性和可行性。
3.1.5 确定风险等级和优先级。
3.2 风险评价应由具备相关知识和经验的人员进行,并记录在风险评估表中。
4. 风险控制4.1 通过建立和实施适当的控制措施来降低风险至可接受范围。
4.2 控制措施应根据风险评估结果制定,并尽可能遵循以下原则:4.2.1 优先选择技术性控制措施,如工程控制,以消除或降低危害。
4.2.2 采取行政控制措施,如工作和操作规程,以保证员工遵守安全操作规范。
4.2.3 提供个人防护装备,并确保其正确使用和维护。
4.3 控制措施的实施应经过充分的培训和沟通,确保员工理解和遵守。
4.4 控制措施的有效性应定期进行检查和评估,并采取必要的改进措施。
5. 安全文化和员工参与5.1 组织应建立积极的安全文化,鼓励员工主动参与危害辨识和风险评价。
5.2 组织应定期举行安全培训和会议,提高员工对危害和风险的认识和理解。
- 1、下载文档前请自行甄别文档内容的完整性,平台不提供额外的编辑、内容补充、找答案等附加服务。
- 2、"仅部分预览"的文档,不可在线预览部分如存在完整性等问题,可反馈申请退款(可完整预览的文档不适用该条件!)。
- 3、如文档侵犯您的权益,请联系客服反馈,我们会尽快为您处理(人工客服工作时间:9:00-18:30)。
管理制度编号:YTO-FS-PD127
有害物质风险评估程序通用版
In Order T o Standardize The Management Of Daily Behavior, The Activities And T asks Are Controlled By The Determined Terms, So As T o Achieve The Effect Of Safe Production And Reduce Hidden Dangers.
标准/ 权威/ 规范/ 实用
Authoritative And Practical Standards
有害物质风险评估程序通用版
使用提示:本管理制度文件可用于工作中为规范日常行为与作业运行过程的管理,通过对确定的条款对活动和任务实施控制,使活动和任务在受控状态,从而达到安全生产和减少隐患的效果。
文件下载后可定制修改,请根据实际需要进行调整和使用。
1.0目的
本程序在于全面有效的识别与评估RSC-MS产品生産中的物料、供应商和生产过程中所产生的风险,从而更好的预防、降低和控制可能産生的交叉污染;
2.0范围
适用于公司ROHS管理的活动过程、子过程与ROHS 产品相关之各部门及场所;
3.0定义
无
4.0职责
4.1各部门调查和识别本部门接受的物料、服务或活动过程等所有可能存在的风险,并书面报告给风险评估小组;
4.2 管理代表负责召集各组员对各部门之报告进行评估,制定出所需的控制措施,并跟进控制措施的完成情况;
5.0 作业程序
5.1风险分类
1>风险评估小组成立:本公司之风险评估小组为环境推进小组兼任;
2>风险评估中风险类别分为三大类:物料风险、供应商/加工商风险、过程风险;
3>风险等级分为高风险与低风险两种类型;
4>物料风险评估包括:a> ROHS产品BOM所列的物料;b> 生産过程使用之物料;
5.2物料的风险评估
1> 满足以下条件之一即被评定为高风险物料;
a>有多种物料构成,物料中较易带有受限物质:如COB、马达等含有多种材料的元器件等;
b>为增强某种功能、用途、外观效果等而在物料或制作工艺中有意增加受限物质(需由相关技术人员判定),紧固件中的螺丝/螺母等,因电镀/钝化行业中的三价铬工艺目前不够成熟,多数厂家采用六价铬处理工艺;
c>物料的成份复杂或不纯(需由相关技术人员判定),含有多种成份或成份不清楚,如线材/化工原料等;
d>含有回收再用的物料,且难以被追溯;如塑胶制品生产须添加适当之PBB/PBDE阻燃剂,如果重新回收使用的塑料中阻燃剂无法衡量或控制,容易造成交叉污染;使PBB/PBDE含量超标;
2> 满足以下条件之一的物料被判定为低风险物料;
a>间接物料未直接用在产品上,如包裝用的周转容器/工夾具等;
b>沒有使用回收再用的物料;
c>物料成份组合中沒有混合的机会;
d>由单一物料构成,受限制物质影响的几率低;
5.3供应商/加工商的风险评估
1>满足以下条件之一即被评定为高风险供应商/加工商:
a>新供应商/加工商或持续一年未有任何ROHS产品业务往来的供应商/加工商;
b>以往两年物料供应或加工曾经出现过严重的问题;
c> 完全沒有ROHS概念的供应商;
2>满足以下条件之一即被评定为低风险供应商/加工商:
a>在以往供应的两年中都未出现过严重问题的供应商/加工商;
b>已经建立了有关ROHS产品之管理系统或有关ROHS产品的管理体系;
c>世界级跨国公司或行业内声誉超卓的公司,如菲利浦、索尼等;
5.4工序的风险评估
过程的风险包括生产过程中所有生产设备、工/夹具、测试仪器、工作环境、操作人员等在正常、异常、紧急的状况下所有可能导致交叉污染产生的风险状况;
1> 满足以下条件之一即被评定为高风险:
a> 该过程使用的设备、工/夹具、测试仪器等并非ROHS控制生产工序专用,且将直接接触产品,若不经过相应的处理措施,将对ROHS物料或产品造成极大的交叉污染;
b>该过程导致ROHS物料与非ROHS物料的混料机会极大,如领料时ROHS物料与非ROHS物料无明显的区分,操作人员未受过专门ROHS培训,将导致混料;
2>满足以下条件之一即被评定为低风险:
a>该过程所使用的设备、工/夹具、测试仪器等属于ROHS产品生产专用,(或虽非ROHS产品专用,但并不直接与产品接触)且有有效的清洁措施;
b>该过程导致ROHS物料和非ROHS物料的混料机会很小;
5.5物料风险控制措施:
a>要求供应商/加工商提供由认可机构检验的ROHS 测试报告;
b>提供合格ROHS检测报告的频率暂定为1年1次;
c>要求供应商/加工商在更改设计或工艺时須重新提供
ROHS检测报告;
b>要求供应商同我司签署“环保物料供应协议保证书”
5.6工序风险控制
a) 购买/加工新的及符合ROHS要求的工/夹具、使用设备、辅助材料,并且須保证是ROHS产品专用;
b) 所有与ROHS产品相关工序之区域、设备、工/夹具、辅助材料、容器等都必须有明显之标识;
c) 对所有专用工/夹具、设备进行清洁后方可使用;
e) 工人必须经过ROHS相关知识培训并经考核合格方给予上岗;
5.7风险评估的频率
a> 对物料的风险评估在设计初期或有任何设计或物料更改的阶段进行;
b>对供应商的风险评估为一年一次或有新供应商加入时进行;
c>工序的风险评估在生产前或有任何工艺更改时进行,高风险工序最少每年一次
6.0 引用文件
无
7.0 表单/记录
7.1 物料风险评估表
7.2 供应商风险评估表
7.3 制程风险评估表
该位置可输入公司/组织对应的名字地址
The Name Of The Organization Can Be Entered In This Location。