油气储运毕业论文翻译原文
油气储运专业英语reading部分翻译

Petroleum and Its Modern Uses[1] Petroleum, coal, and natural gas are the most widely used sources of energy in the m odern world. They are of primary importance in the industrialized countries, where vast am ounts of energy are consumed to operate the different kinds of machines used today. The se three energy sources are collectively referred to as fossil fuels.石油、煤炭和天然气是现代世界最广泛使用的能源。
它们在工业化国家中最为重要,在这些国家,人们消耗大量的能源来操作今天使用的各种机器。
这三种能源统称为化石燃料。
[2] At various depths beneath land and sea, there are accumulations of hydrocarbons form ed millions and even hundreds of millions of years ago by decomposition of animal and v egetable remains. They were covered by sand or mud, which in time was itself covered by the water of the seas. Hydrocarbons are compounds of hydrogen and carbon which, at n ormal temperatures and pressures, may be gaseous, liquid or solid according to their mole cular complexity. The natural deposits are correspondingly gaseous, liquid or solid, dependi ng on the relative proportion of the various hydrocarbons present in mixture. Petroleum is composed largely of the remains of these tiny marine animals and plants that lived so lo ng ago.在陆地和海洋的不同深处,有数百万年甚至数亿年前由于动物和植物残骸的分解而形成的碳氢化合物的积聚。
(完整版)油气储运专业英语(英汉互译)
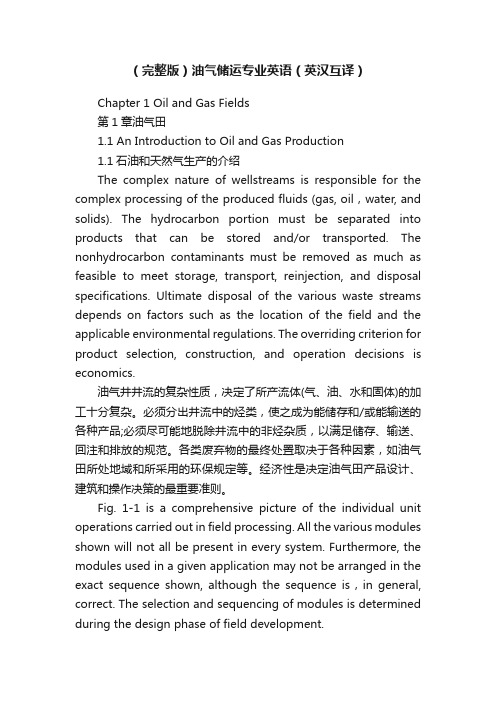
(完整版)油气储运专业英语(英汉互译)Chapter 1 Oil and Gas Fields第1章油气田1.1 An Introduction to Oil and Gas Production1.1石油和天然气生产的介绍The complex nature of wellstreams is responsible for the complex processing of the produced fluids (gas, oil,water, and solids). The hydrocarbon portion must be separated into products that can be stored and/or transported. The nonhydrocarbon contaminants must be removed as much as feasible to meet storage, transport, reinjection, and disposal specifications. Ultimate disposal of the various waste streams depends on factors such as the location of the field and the applicable environmental regulations. The overriding criterion for product selection, construction, and operation decisions is economics.油气井井流的复杂性质,决定了所产流体(气、油、水和固体)的加工十分复杂。
必须分出井流中的烃类,使之成为能储存和/或能输送的各种产品;必须尽可能地脱除井流中的非烃杂质,以满足储存、输送、回注和排放的规范。
油气储运 毕业论文

油气储运毕业论文油气储运随着全球经济的快速发展和人们对能源需求的不断增长,油气储运成为了一个备受关注的话题。
油气储运是指将天然气和石油从产地运输到消费地的过程,它涉及到各种设备、技术和管理方法。
在这篇文章中,我们将探讨油气储运的重要性、挑战以及未来的发展方向。
首先,油气储运对于全球能源供应的稳定至关重要。
石油和天然气是世界上最重要的能源资源之一,它们在工业、交通和生活中发挥着不可替代的作用。
然而,大部分油气资源都分布在地理位置偏远的地区,如海底、沙漠和北极地区。
因此,如何将这些资源安全、高效地运输到消费地成为了一个重要的问题。
油气储运系统的建设和运营,能够确保能源供应的稳定性,维持全球经济的正常运行。
然而,油气储运也面临着一些挑战。
首先,安全问题是最重要的考虑因素之一。
油气的储存和运输过程中存在着爆炸、泄漏和污染等风险,一旦发生事故,将对环境和人类健康造成巨大的损害。
因此,油气储运企业必须制定严格的安全标准和操作规程,并采取相应的措施来预防和应对事故的发生。
其次,油气储运还面临着环境问题。
石油和天然气的开采和运输过程会产生大量的温室气体和其他污染物,对气候变化和生态环境造成不可忽视的影响。
因此,油气储运企业需要采取可持续发展的方法,减少对环境的负面影响。
为了应对这些挑战,油气储运行业正在不断发展和创新。
首先,技术的进步为油气储运提供了更多的选择。
例如,液化天然气(LNG)技术的发展使得天然气能够以液体形式储存和运输,从而解决了长距离运输的问题。
此外,自动化和智能化技术的应用,能够提高油气储运的安全性和效率。
其次,油气储运企业也在积极探索可持续发展的路径。
他们正在研究和应用新的能源储存和转换技术,如电动汽车和可再生能源,以减少对传统石油和天然气的依赖。
在未来,油气储运行业将继续面临新的挑战和机遇。
一方面,全球能源需求的不断增长将推动油气储运的发展。
另一方面,可再生能源的快速发展和环境保护的呼声也将促使油气储运行业转型。
化学工程 油气运输 外文翻译 外文文献 英文文献
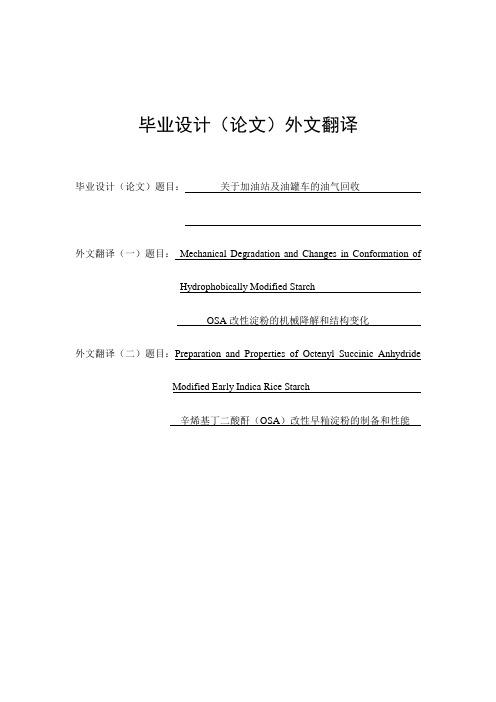
毕业设计(论文)外文翻译毕业设计(论文)题目:关于加油站及油罐车的油气回收外文翻译(一)题目:Mechanical Degradation and Changes in Conformation ofHydrophobically Modified StarchOSA改性淀粉的机械降解和结构变化外文翻译(二)题目:Preparation and Properties of Octenyl Succinic AnhydrideModified Early Indica Rice Starch辛烯基丁二酸酐(OSA)改性早籼淀粉的制备和性能低成本和高可靠的喷射压缩机采用油气回收领域,以解决生态问题,在开发节能技术。
一定的技术困难,但是,这个操作复杂设备在最佳条件下,即:有效的参数范围狭窄喷气熟悉设计压缩机遇到喷射压缩机启动和稳定运行的复杂性液体收益访问接收室。
血压波动也使自己感到液体喷射压缩机的运作产生负面影响。
在同时,压力和流量的变化是恢复,积累就业的运作系统的特点,石油和天然气的加工。
在这方面,要研究液体喷射压缩机的操作下变条件,包括该设备的监管。
OAO跟Orenburgneft “液体喷射压缩机的设计,开发与双流量喷嘴集结合可调驱动电源泵,使人们有可能以不同的尺寸和无量纲特征喷射装置。
液体喷射压缩机的实验研究进行了在一条长凳上安装的IM Gubkin俄罗斯石油和天然气的州立大学。
在这些调查过程中,添置介绍了液体喷射压缩机相似理论[1]。
喷射压缩机的基本组件如下:- 直接流喷嘴组,以确保工作液喷射形成与调节的可能性射流压缩部分,科里奥利和Boussienesq系数的直径;- 一个环形接收室的入口和出口之间的部分,以确保交付的介质转移到工作液喷射;- 在第一套可互换组件(不同的入口和出口之间的混合室内部的直径和长度),确保工作与正在传输介质液体混合,- 扩散器与一组可互换组件(不同的入口部分的内部直径),从而确保在气液混合物的流速减少。
关于油气储运技术毕业论文

关于油气储运技术毕业论文油气储运技术是石油与天然气工程的重要组成部分,对于油气资源的开发和生产具有至关重要的意义。
油气储运技术通过一系列的工艺和设备,将原油、天然气等能源资源从油田或天然气田输送到相应的加工厂、储罐或终端用户,保证了能源资源的安全、有效和高效供应。
本文将对油气储运技术的概念、发展、现状以及未来发展进行探讨。
油气储运技术的概念是指油田或天然气田开采后,将其产出的原油、天然气等能源资源通过管道、船舶、铁路等方式输送到储罐、加工厂或终端用户的技术。
油气储运技术主要包括输送系统、储存系统和控制系统三个方面。
输送系统包括管道输送、海上输送和铁路输送等方式,以满足不同需求的能源输送。
储存系统包括储罐、储气库等设施,用于存储原油、天然气等能源资源。
控制系统利用先进的控制技术,对油气储运过程进行监控和控制,确保输送的安全和高效。
油气储运技术的发展经历了多年的积累和创新。
在20世纪初,由于石油和天然气资源的发现和开采,油气储运技术开始得到重视和应用。
当时主要采用的是海上输送和铁路输送方式,由于技术和设备的限制,输送效率较低。
随着科技的进步和设备的更新,油气管道的建设和使用成为油气储运的主要方式,输送效率大大提高。
同时,在储罐、储气库等储存设施方面也进行了很多创新,提高了能源资源的储存和分配效率。
控制系统也逐渐应用于油气储运过程中,实现了自动化、智能化的管理。
目前,油气储运技术已经取得了重大的发展和进步。
在油气管道方面,中国已经建成了世界上最长和最大规模的输送管道网,有效地解决了能源输送的问题。
在储存设施方面,储罐、储气库等设施的建设和管理水平不断提高,能源资源的储存能力和分配能力得到了大幅度提升。
控制系统方面,通过先进的监控和控制技术,实现了对油气储运过程的远程监控和智能控制,大大提高了运行效率和安全性。
未来,随着能源需求的不断增长和能源资源的进一步开采,油气储运技术仍将面临一些挑战和发展机遇。
一方面,油气储运技术需要进一步提高能源输送的效率和安全性,采用更先进的技术和设备,实现能源资源的最优配置。
油气储运外文翻译(腐蚀类)【范本模板】

重庆科技学院学生毕业设计(论文)外文译文学院石油与天然气工程学院专业班级油气储运10级3班学生姓名汪万茹学号2010440140NACE论文富气管道的腐蚀管理Faisal Reza,Svein Bjarte Joramo—Hustvedt,Helene Sirnes Statoil ASA摘要运输网的运行为挪威大陆架(NCF)总长度接近1700千米的富气管道的运行和整体完整性提供了技术帮助。
根据标准以一种安全,有效,可靠的方式来操作和维护管道是很重要的。
天然气在进入市场之前要通过富气管道输送至处理厂.在对这些富气进行产品质量测量和输送到输气管道之前要在平台上进行预处理和脱水处理。
监测产物是这些管线腐蚀管理的一个重要部分。
如果材料的表面没有游离水管道就不会被腐蚀。
因此,在富气管道的运行过程中监测水露点(WDP)或水分含量具有较高的优先性,并且了解含有二氧化碳(CO2)和硫化氢(H2S)的水在管道中析出过程中的腐蚀机制对全面控制管道腐蚀很重要.本文将详细介绍生产监测的项目,例如讨论生产流量,压力,温度,气体组成和水露点。
一个全面的内部评估应该包括对富气管道中三甘醇(TEG)和水作用机理的详细阐述.关键词:富气管道,产品监控,内部腐蚀,腐蚀产物,二氧化碳(CO2),硫化氢(H2S),三甘醇(TEG),水露点(WDP),液体滞留。
引言从海上生产设施输送富气所使用的碳钢管线需要可靠的控制装置将水控制在气相中,以避免在管道内表面上凝结水和产生游离水。
全面腐蚀不仅仅是和腐蚀产物本身有关,沉淀产物有可能会促使一个更高的腐蚀速率[1].液体滞留在管道中可以引起腐蚀,然而为了保证管道内部完整性仅仅评估腐蚀速度是不够的。
在管道中腐蚀产物可能会导致进一步的问题;增加表面粗糙度和减少直径可以导致压力降的增加,同时也会引起接收终端设备的一些问题,比如腐蚀和堵塞[3]。
管道系统可能由主运输干线连接一些输送支线组成,这样一个复杂的海底管道系统的完整性管理不是很简单的。
油气储运毕业论文
油气储运毕业论文油气储运毕业论文近年来,随着全球能源需求的增长,油气储运成为了一个备受关注的话题。
作为能源行业的重要环节,油气储运对于能源供应的稳定性和经济发展起着至关重要的作用。
本文将从油气储运的意义、技术发展和环境影响等方面进行论述。
一、油气储运的意义油气储运是指将原油、天然气等能源资源从产地运输到加工厂、储存设施或终端用户的过程。
它不仅是能源供应链的重要环节,也是能源市场稳定运行的基础。
油气储运的意义主要体现在以下几个方面:首先,油气储运保障了能源供应的稳定性。
能源是现代社会发展的基石,而能源供应的稳定性对于国家的经济发展和社会稳定至关重要。
通过建设完善的油气储运系统,可以确保能源资源的安全输送,避免因供应中断而导致的能源危机。
其次,油气储运促进了能源资源的优化配置。
不同地区的能源资源分布不均,通过建设高效的油气储运系统,可以将能源资源从产地输送到需求地,实现资源的优化配置。
这不仅有助于提高能源利用效率,还能够促进地区经济的发展。
最后,油气储运推动了能源技术的创新与发展。
油气储运是一个高技术含量的领域,涉及到管道输送、海上运输、储存技术等多个方面。
通过对油气储运技术的研发和应用,可以推动能源技术的创新与发展,提高能源资源的利用效率和环境友好性。
二、油气储运的技术发展随着能源需求的不断增长,油气储运技术也在不断发展和创新。
在油气储运领域,涉及到的技术包括管道输送、海上运输、储存技术等。
以下是几个重要的技术发展趋势:首先,管道输送技术的发展是油气储运的重要方向之一。
管道输送是目前最常用的油气储运方式,具有输送量大、输送距离长、安全可靠等优点。
随着技术的不断进步,管道输送技术在输送效率、安全性和环保性方面都有了显著的提高。
其次,海上运输技术的发展也是一个重要的趋势。
海上运输是一种灵活、高效的油气储运方式,尤其适用于远离陆地的油气资源开发。
随着深海油气勘探开发的不断深入,海上运输技术的发展将成为油气储运的重要方向。
油气储运工程英文作文
油气储运工程英文作文英文:As a professional in oil and gas transportation engineering, I have been involved in various projects related to the storage and transportation of these resources. One of the key challenges in this field is ensuring the safety and efficiency of the operations.To achieve this, we use advanced technologies and equipment, such as pipeline monitoring systems, leak detection systems, and remote control systems. These tools help us to detect and prevent potential hazards, as well as to optimize the flow of resources.In addition to technology, communication and teamwork are also crucial in oil and gas transportation engineering. For example, when working on a pipeline project, we need to coordinate with various stakeholders, including landowners, government agencies, and local communities. Effectivecommunication and collaboration can help us to address concerns and ensure that the project is completed successfully.Another important aspect of oil and gas transportation engineering is sustainability. We need to consider the environmental impact of our operations and take measures to minimize it. For example, we may use renewable energy sources to power our equipment or implement measures to reduce greenhouse gas emissions.Overall, oil and gas transportation engineering is a challenging and rewarding field that requires a combination of technical expertise, communication skills, and a commitment to sustainability.中文:作为一名油气储运工程专业人士,我参与了许多与这些资源储存和运输有关的项目。
(完整版)油气储运专业英语(英汉互译)
Chapter 1 Oil and Gas Fields第1章油气田1.1 An Introduction to Oil and Gas Production1.1石油和天然气生产的介绍The complex nature of wellstreams is responsible for the complex processing of the produced fluids (gas, oil,water, and solids). The hydrocarbon portion must be separated into products that can be stored and/or transported. The nonhydrocarbon contaminants must be removed as much as feasible to meet storage, transport, reinjection, and disposal specifications. Ultimate disposal of the various waste streams depends on factors such as the location of the field and the applicable environmental regulations. The overriding criterion for product selection, construction, and operation decisions is economics.油气井井流的复杂性质,决定了所产流体(气、油、水和固体)的加工十分复杂。
必须分出井流中的烃类,使之成为能储存和/或能输送的各种产品;必须尽可能地脱除井流中的非烃杂质,以满足储存、输送、回注和排放的规范。
各类废弃物的最终处置取决于各种因素,如油气田所处地域和所采用的环保规定等。
油气储运专业英语
油气储运专业英语The oil and gas industry is a cornerstone of modern energy infrastructure, requiring a specialized understanding of the processes involved in the transportation and storage of hydrocarbons.From the extraction site to the refinery, the journey of oil and gas is complex, involving pipelines, tankers, and storage facilities. Each stage demands precision and adherence to safety protocols to prevent leaks and environmental damage.The language of oil and gas storage and transportation is technical and specific, with terms like "pipeline integrity" and "tank farm management" becoming second nature to those in the field. Communication in this industry is crucial for ensuring operations run smoothly and efficiently.In the classroom, students of oil and gas storage and transportation learn the fundamentals of fluid dynamics, material science, and engineering principles that underpin the industry. They also become familiar with the regulatory frameworks that govern these operations.As technology advances, so too does the language of the industry. Terms like "digital twins" and "smart pipelines" are now part of the lexicon, reflecting the integration of digital technology into traditional oil and gas operations.The global nature of the oil and gas industry means that professionals must be fluent in English, the lingua franca of international business. This proficiency enablescollaboration across borders and the sharing of best practices worldwide.Continuing education is essential for those in the field, as new methods and technologies are constantly emerging. This includes staying abreast of the latest in English-language literature on topics like offshore drilling and LNG shipping.In summary, mastering the English language in the context of oil and gas storage and transportation is not just about understanding technical jargon; it's about being able to communicate effectively in an ever-evolving global industry.。
- 1、下载文档前请自行甄别文档内容的完整性,平台不提供额外的编辑、内容补充、找答案等附加服务。
- 2、"仅部分预览"的文档,不可在线预览部分如存在完整性等问题,可反馈申请退款(可完整预览的文档不适用该条件!)。
- 3、如文档侵犯您的权益,请联系客服反馈,我们会尽快为您处理(人工客服工作时间:9:00-18:30)。
( 1of6 )United States Patent Application20050205157 Kind Code A1 Hutchinson, Ray J. September 22, 2005Service station leak detection and recovery systemAbstractA fueling environment that distributes fuel from a fuel supply to fuel dispensers in a daisy chain arrangement with a double walled piping system. Fuel leaks that occur within the double walled piping system are returned to the underground storage tank by the outer wall of the double walled piping. This preserves the fuel for later use and helps reduce the risk of environmental contamination. Leak detectors may also be positioned in fuel dispensers detect leaks and provide alarms for the operator and help pinpoint leak detection that has occurred in the piping system proximate to a particular fuel dispenser or in between two consecutive fuel dispensers.Inventors:Hutchinson, Ray J.; (Houma, LA)Correspondence Name and Address: WITHROW & TERRANOVA, P.L.L.C. P.O. BOX 1287CARYNC27512USAssignee Name and Adress:GILBARCO INC. GreensboroNCSerial No.: 131823Series Code: 11Filed: May 18, 2005U.S. Current Class:141/311A U.S. Class at Publication:141/311.00A Intern'l Class: B65B 001/04Claims1-20. (canceled)21. A method of detecting a leak in a fueling environment's fueling distribution system with a fuel dispenser, said method comprising: dispensing fuel throughout a fueling environment in an inner conduit of a double walled conduit; capturing a leak from the inner conduit with an outer conduit of the double walled conduit; returning fluid leaked into the outer conduit to an underground storage tank through a submersible turbine pump.22. The method of claim 21, wherein returning fluid leaked into the outer conduit through the submersible turbine pump comprises allowing fluid to pass into a casing construction of the submersible turbine pump.23. The method of claim 21, wherein returning fluid leaked into the outer conduit through the submersible turbine pump comprises opening a valve associated with the submersible turbine pump to allow fluid to pass into a casing construction of the submersible turbine pump.24. The method of claim 21, wherein returning fluid leaked into the outer conduit to the underground storage tank through the submersible turbine pump comprises connecting the fluid to a double walled pipe connecting the submersible turbine pump to the underground storage tank.25. The method of claim 21, wherein dispensing fuel throughout the fueling environment comprises dispensing fuel with a main and branch piping arrangement.26. The method of claim 21, wherein dispensing fuel throughout the fueling environment comprises dispensing fuel with a daisy-chained piping arrangement.27. The method of claim 21, further comprising detecting the leak.28. The method of claim 27, further comprising reporting the leak.29. The method of claim 28, wherein reporting the leak comprises reporting the leak to an element selected from the group consisting of: a site controller, a tank monitor, a site communicator, and a location remote from the fueling environment.30. The method of claim 27, wherein detecting the leak comprises detecting the leak with a leak detection probe positioned in the outer conduit.31. The method of claim 27, wherein detecting the leak comprises detecting the leak with a leak detection probe positioned in a fuel dispenser manifold.32. The method of claim 21, wherein returning fluid leaked into the outer conduit comprises assisting the returning with a vacuum.33. The method of claim 21, wherein returning fluid leaked into the outer conduit comprises using gravity to bring fluid to the submersible turbine pump.34. A fueling environment, comprising: a fuel storage tank; a submersible turbine pump associated with the fuel storage tank; at least one fuel dispenser; a double walled piping network fluidly coupling the fuel storage tank to the at least one fuel dispenser such that fuel is dispensed throughout the fueling environment in an inner conduit and leaks from the inner conduit are captured in an outer conduit and returned to the fuel storage tank through the submersible turbine pump.35. The fueling environment of claim 34, wherein the at least one fuel dispenser comprises fuel handling components.36. The fueling environment of claim 34, wherein the submersible turbine pump comprises a casing construction and fluid returned to the fuel storage tank through the submersible turbine pump passes into the casing construction.37. The fueling environment of claim 34, wherein the submersible turbine pump comprises a valve adapted to open to return fluid leaked into the outer conduit through the submersible turbine pump.38. The fueling environment of claim 34, further comprising a double walled pipe connecting the submersible turbine pump to the fuel storage tank, said double walled pipe returning fluid from the submersible turbine pump to the fuel storage tank.39. The fueling environment of claim 34, wherein the fuel storage tank comprises an underground storage tank.40. The fueling environment of claim 34, wherein the double walled piping network comprises a main and branch piping arrangement.41. The fueling environment of claim 34, wherein the double walled piping network comprises adaisy-chained piping arrangement.42. The fueling environment of claim 34, further comprising a leak detector adapted to detect leaks.43. The fueling environment of claim 42, wherein the leak detector is further adapted to report any leaks.44. The fueling environment of claim 42, wherein the leak detector reports any leaks to an element selected from the group consisting of: a site controller, a tank monitor, a site communicator, and a location remote from the fueling environment.45. The fueling environment of claim 42, wherein the leak detector is positioned in the outer conduit.46. The fueling environment of claim 42, wherein the leak detector is positioned in a fuel dispenser manifold.47. The fueling environment of claim 34, further comprising a vacuum source adapted to assist the return of fluid leaked into the outer conduit.48. The fueling environment of claim 34, wherein the double walled piping network is arranged such that fluid leaked into the outer conduit returns to the submersible turbine pump at least in part via gravity.DescriptionFIELD OF THE INVENTION[0001] The present invention relates to a fuel recovery system for recovery leaks that occur in fuel supply piping in a retail fueling environment.BACKGROUND OF THE INVENTION[0002] Managing fuel leaks in fueling environments has become more and more important in recent years as both state and federal agencies impose strict regulations requiring fueling systems to be monitored for leaks. Initially, the regulations required double walled tanks for storing fuel accompanied by leak detection for the tanks. Subsequently, the regulatory agencies have become concerned with the piping between the underground storage tank and the fuel dispensers and are requiring double walled piping throughout the fueling environment as well.[0003] Typically, the double walled piping that extends between fuel handling elements within thefueling environment terminates at each end with a sump that is open to the atmosphere. In the event of a leak, the outer pipe fills and spills into the sump. The sump likewise catches other debris, such as water and contaminants that contaminate the fuel caught by the sump, thereby making this contaminated fuel unusable. Thus, the sump is isolated from the underground storage tank, and fuel captured by the sump is effectively lost.[0004] Coupled with the regulatory changes in the requirements for the fluid containment vessels are requirements for leak monitoring such that the chances of fuel escaping to the environment are minimized. Typical leak detection devices are positioned in the sumps. These leak detection devices may be probes or the like and may be connected to a control system for the fueling environment such that the fuel dispensing is shut down when a leak is detected.[0005] Until now, fueling environments have been equipped with elements from a myriad of suppliers. Fuel dispensers might be supplied by one company, the underground storage tanks by a second company, the fuel supply piping by a third company, and the tank monitoring equipment by yet a fourth company. This makes the job of the designer and installer of the fueling environment harder as compatibility issues and the like come into play. Further, it is difficult for one company to require a specific leak detection program with its products. Interoperability of components in a fueling environment may provide economic synergies to the company able to effectuate such, and provide better, more integrated leak detection opportunities.[0006] Any fuel piping system that is installed for use in a fueling environment should advantageously reduce the risk of environmental contamination when a leak occurs and attempt to recapture fuel that leaks for reuse and to reduce excavation costs, further reducing the likelihood of environmental contamination. Still further, such a system should include redundancy features and help reduce the costs of clean up.SUMMARY OF THE INVENTION[0007] The present invention capitalizes on the synergies created between the tank monitoring equipment, the submersible turbine pump (STP), and the fuel dispenser in a fueling environment.A fluid connection that carries a fuel supply for eventual delivery to a vehicle is made between the underground storage tank and the fuel dispensers via double walled piping. Rather than use the conventional sumps and low point drains, the present invention drains any fuel that has leaked from the main conduit of the double walled piping back to the underground storage tank. This addresses the need to recapture the fuel for reuse and to reduce fuel that is stored in sumps which must later be retrieved and excavated by costly service personnel.[0008] The fluid in the outer conduit may drain to the underground storage tank by gravity coupled with the appropriately sloping piping arrangements, or a vacuum may be applied to the outer conduit from the vacuum in the underground storage tank. The vacuum will drain the outer conduit. Further, the return path may be fluidly isolated from the sumps, thus protecting the fuel from contamination.[0009] In an exemplary embodiment, the fuel dispensers are connected to one another via a daisy chain fuel piping arrangement rather than by a known main and branch conduit arrangement. Fuel supplied to a first fuel dispenser by the STP and conduit is carried forward to other fuel dispensers coupled to the first fuel dispenser via the daisy chain fuel piping arrangement. The daisy chain is achieved by a T-intersection contained within a manifold in each fuel dispenser. Fuel leaking in the double walled piping is returned through the piping network through each downstream fuel dispenser before being returned to the underground storage tank.[0010] The daisy chain arrangement allows for leak detection probes to be placed within each fuel dispenser so that leaks between the fuel dispensers may be detected. The multiplicity of probes causes leak detection redundancy and helps pinpoint where the leak is occurring. Further, the multiple probes help detect fuel leaks in the outer conduit of the double walled piping. This is accomplished by verifying that fuel dispensers downstream of a detected leak also detect a leak. If they do not, a sensor has failed or the outer conduit has failed. A failure in the outer piping is cause for serious concern as fuel may be escaping to the environment and a corresponding alarm may be generated.[0011] Another possibility with the present invention is to isolate sumps, if still present within the fuel dispenser, from this return path of captured leaking fuel such that contaminants are precluded from entering the leaked fuel before being returned to the underground storage tank. In this manner, fuel may potentially be reused since it is not contaminated by other contaminants, such as water, and reclamation efforts are easier. Since the fuel is returned to the underground storage tank, there is less danger that a sump overflows and allows the fuel to escape into the environment.[0012] Those skilled in the art will appreciate the scope of the present invention and realize additional aspects thereof after reading the following detailed description of the preferred embodiments in association with the accompanying drawing figures.BRIEF DESCRIPTION OF THE DRAWING FIGURES[0013] The accompanying drawing figures incorporated in and forming a part of this specification illustrate several aspects of the invention, and together with the description serve to explain the principles of the invention.[0014] FIG. 1 illustrates a conventional communication system within a fueling environment in the prior art;[0015] FIG. 2 illustrates a conventional fueling path layout in a fueling environment in the prior art;[0016] FIG. 3 illustrates, according to an exemplary embodiment of the present invention, a daisy chain configuration for a fueling path in a fueling environment;[0017] FIG. 4 illustrates, according to an exemplary embodiment of the present invention, a fueldispenser;[0018] FIG. 5 illustrates a first embodiment of a fuel return to underground storage tank arrangement;[0019] FIG. 6 illustrates a second embodiment of a fuel return to underground storage tank arrangement; and[0020] FIG. 7 illustrates a flow chart showing the leak detection functionality of the present invention.DETAILED DESCRIPTION OF THE PREFERRED EMBODIMENTS[0021] The embodiments set forth below represent the necessary information to enable those skilled in the art to practice the invention and illustrate the best mode of practicing the invention. Upon reading the following description in light of the accompanying drawing figures, those skilled in the art will understand the concepts of the invention and will recognize applications of these concepts not particularly addressed herein. It should be understood that these concepts and applications fall within the scope of the disclosure and the accompanying claims.[0022] Fueling environments come in many different designs. Before describing the particular aspects of the present invention (which begins at the description of FIG. 3), a brief description of a fueling environment follows. A conventional exemplary fueling environment 10 is illustrated in FIGS. 1 and 2. Such a fueling environment 10 may comprise a central building 12, a car wash 14, and a plurality of fueling islands 16.[0023] The central building 12 need not be centrally located within the fueling environment 10, but rather is the focus of the fueling environment 10, and may house a convenience store 18 and/ora quick serve restaurant 20 therein. Both the convenience store 18 and the quick serve restaurant20 may include a point of sale 22, 24, respectively. The central building 12 may further house a site controller (SC) 26, which in an exemplary embodiment may be the G-SITE.RTM. sold by Gilbarco Inc. of Greensboro, N.C. The site controller 26 may control the authorization of fueling transactions and other conventional activities as is well understood. The site controller 26 may be incorporated into a point of sale, such as point of sale 22 if needed or desired. Further, the site controller 26 may have an off-site communication link 28 allowing communication with a remote location for credit/debit card authorization, content provision, reporting purposes or the like, as needed or desired. The off-site communication link 28 may be routed through the Public Switched Telephone Network (PSTN), the Internet, both, or the like, as needed or desired.[0024] The car wash 14 may have a point of sale 30 associated therewith that communicates with the site controller 26 for inventory and/or sales purposes. The car wash 14 alternatively may be a stand alone unit. Note that the car wash 14, the convenience store 18, and the quick serve restaurant 18 are all optional and need not be present in a given fueling environment.[0025] The fueling islands 16 may have one or more fuel dispensers 32 positioned thereon. The fuel dispensers 32 may be, for example, the ECLIPSE.RTM. or ENCORE.RTM. sold by Gilbarco Inc. of Greensboro, N.C. The fuel dispensers 32 are in electronic communication with the site controller 26 through a LAN or the like.[0026] The fueling environment 10 also has one or more underground storage tanks 34 adapted to hold fuel therein. As such the underground storage tank 34 may be a double walled tank. Further, each underground storage tank 34 may include a tank monitor (TM) 36 associated therewith. The tank monitors 36 may communicate with the fuel dispensers 32 (either through the site controller 26 or directly, as needed or desired) to determine amounts of fuel dispensed and compare fuel dispensed to current levels of fuel within the underground storage tanks 34 to determine if the underground storage tanks 34 are leaking.[0027] The tank monitor 36 may communicate with the site controller 26 and further may have an off-site communication link 38 for leak detection reporting, inventory reporting, or the like. Much like the off-site communication link 28, off-site communication link 38 may be through the PSTN, the Internet, both, or the like. If the off-site communication link 28 is present, the off-site communication link 38 need not be present and vice versa, although both links may be present if needed or desired. As used herein, the tank monitor 36 and the site controller 26 are site communicators to the extent that they allow off site communication and report site data to a remote location.[0028] For further information on how elements of a fueling environment 10 may interact, reference is made to U.S. Pat. No. 5,956,259, which is hereby incorporated by reference in its entirety. Information about fuel dispensers may be found in commonly owned U.S. Pat. Nos. 5,734,851 and 6,052,629, which are hereby incorporated by reference in their entirety. Information about car washes may be found in commonly owned U.S. patent application Ser. No. 10/______ filed 6 May 2002, entitled IMPROVED SERVICE STA TION CAR W ASH, which is hereby incorporated by reference in its entirety. An exemplary tank monitor 36 is the TLS-350R manufactured and sold by Veeder-Root. For more information about tank monitors 36 and their operation, reference is made to U.S. Pat. Nos. 5,423,457; 5,400,253; 5,319,545; and 4,977,528, which are hereby incorporated by reference in their entireties.[0029] In addition to the various conventional communication links between the elements of the fueling environment 10, there are conventional fluid connections to distribute fuel about the fueling environment as illustrated in FIG. 2. Underground storage tanks 34 may each be associated with a vent 40 that allows over-pressurized tanks to relieve pressure thereby. A pressure valve (not shown) is placed on the outlet side of each vent 40 to open to atmosphere when the underground storage tank 34 reaches a predetermined pressure threshold. Additionally, under-pressurized tanks may draw air in through the vents 40. In an exemplary embodiment, two underground storage tanks 34 exist--one a low octane tank (87) and one a high octane tank (93). Blending may be performed within the fuel dispensers 32 as is well understood to achieve an intermediate grade of fuel. Alternatively, additional underground storage tanks 34 may be provided for diesel and/or an intermediate grade of fuel (not shown).[0030] Pipes 42 connect the underground storage tanks 34 to the fuel dispensers 32. Pipes 42 may be arranged in a main conduit 44 and branch conduit 46 configuration, where the main conduit 44 carries the fuel to the branch conduits 46, and the branch conduits 46 connect to the fuel dispensers 32. Typically, pipes 42 are double walled pipes comprising an inner conduit and an outer conduit. Fuel flows in the inner conduit to the fuel dispensers, and the outer conduit insulates the environment from leaks in the inner conduit. For a better explanation of such pipes and concerns about how they are connected, reference is made to Chapter B13 of PIPING HANDBOOK, 7.sup.th edition, copyright 2000, published by McGraw-Hill, which is hereby incorporated by reference.[0031] In a typical service station installation, leak detection may be performed by a variety of techniques, including probes and leak detection cables. More information about such devices can be found in the previously incorporated PIPING HANDBOOK. Conventional installations do not return to the underground storage tank 34 fuel that leaks from the inner conduit to the outer conduit, but rather allow the fuel to be captured in low point sumps, trenches, or the like, where the fuel mixes with contaminants such as dirt, water and the like, thereby ruining the fuel for future use without processing.[0032] While not shown, vapor recovery systems may also be integrated into the fueling environment 10 with vapor recovered from fueling operations being returned to the underground storage tanks 34 via separate vapor recovery lines (not shown). For more information on vapor recovery systems, the interested reader is directed to U.S. Pat. Nos. 5,040,577; 6,170,539; and Re. 35,238, and U.S. patent application Ser. No. 09/783,178 filed 14 Feb. 2001, all of which are hereby incorporated by reference in their entireties.[0033] Now turning to the present invention, the main and branch supply conduit arrangement of FIG. 2 is replaced by a daisy chain fuel supply arrangement as illustrated in FIG. 3. The underground storage tank 34 provides a fuel delivery path to a first fuel dispenser 32, via a double walled pipe 48. The first fuel dispenser 32, is configured to allow the fuel delivery path to continue onto a second fuel dispenser 32.sub.2 via a daisy chaining double walled pipe 50. The process repeats until an nth fuel dispenser 32.sub.n is reached. Each fuel dispenser 32 has a manifold 52 with an inlet aperture and an outlet aperture as will be better explained below. In the nth fuel dispenser 32.sub.n, the outlet aperture is terminated conventionally as described in the previously incorporated PIPING HANDBOOK.[0034] As better illustrated in FIG. 4, each fuel dispenser 32 comprises a manifold 52 with a T-intersection housed therein. The T-intersection 54 allows the fuel line conduit 56 to be stubbed out of the daisy chaining double walled pipe 50 and particularly to extend through the outer wall 58 of the daisy chaining double walled pipe 50. This T-intersection 54 may be a conventional T-intersection such as is found in the previously incorporated PIPING HANDBOOK. The manifold 52 comprises the aforementioned inlt aperture 60 and outlet aperture 62. While shown on the sides of the manifold 52's housing, they could equivalently be on the bottom side of the manifold 52, if desired. Please note that the present invention is not limited to a manifold 52 witha T-joint, and that any other suitable configuration may be used that allows fuel to be supplied to a fuel dispenser 32 and allows to continue on as well to the next fuel dispenser 32 until the last fuel dispenser 32 is reached.[0035] A leak detection probe 64 may also be positioned within the manifold 52. This leak detection probe 64 may be any appropriate liquid detection sensor as needed or desired. The fuel dispenser 32 has conventional fuel handling components 66 therein, such as fuel pump 68, a vapor recovery system 70, a fueling hose 72, a blender 74, a flow meter 76, and a fueling nozzle 78. Other fuel handling components 66 may also be present as is well understood in the art.[0036] With this arrangement, the fuel may flow into the fuel dispenser 32 in the fuel line conduit 56, passing through the inlet aperture 60 of the manifold 52. A check valve 80 may be used if needed or desired as is well understood to prevent fuel from flowing backwards. The fuel handling components 66 draw fuel through the check valve 80 and into the handling area of the fuel dispenser 32. Fuel that is not needed for that fuel dispenser 32 is passed through the manifold 52 upstream to the other fuel dispensers 32 within the daisy chain. A sump (not shown) may still be associated with the fuel dispenser 32, but it is fluidly isolated from the daisy chaining double walled pipe 50.[0037] A first embodiment of the connection of the daisy chaining double walled pipe 50 to the underground storage tank 34 is illustrated in FIG. 5. The daisy chaining double walled pipe 50 connects to a casing construction 82, which in turn connects to the double walled pipe 48. A submersible turbine pump 84 is positioned within the underground storage tank 34, preferably below the level of the fuel 86 within the underground storage tank 34. For a more complete exploration of the casing construction 82 and the submersible turbine pump 84, reference is made to U.S. Pat. No. 6,223,765 assigned to Marley Pump Company, which is incorporated herein by reference in its entirety and the product exemplifying the teachings of the patent explained in Quantum Submersible Pump Manual: Installation and Operation, also produced by the Marley Pump Company, also incorporated by reference in its entirety. In this embodiment, fuel captured by the outer wall 58 is returned to the casing construction 82 such as through a vacuum or by gravity feeds. A valve (not shown) may allow the fuel to pass into the casing construction 82 and thereby be connected to the double walled pipe 48 for return to the underground storage tank 34. The structure of the casing construction in the '765 patent is well suited for this purpose having multiple paths by which fuel may be returned to the outer wall of the double walled pipe that connects the casing construction 82 to the submersible turbine pump 84.[0038] A second embodiment of the connection of the daisy chaining double walled pipe 50 to the underground storage tank 34 is illustrated in FIG. 6. The casing construction 82 is substantially identical to the previously incorporated U.S. Pat. No. 6,223,765. The daisy chaining double walled pipe 50 however comprises a fluid connection 88 to the double walled pipe 48. This allows the fuel in the outer wall 58 to drain directly to the underground storage tank 34, instead of having to provide a return path through the casing construction 82. Further, the continuous fluid connection from the underground storage tank 34 to the outer wall 58 causes any vacuum present in the underground storage tank 34 to also be existent in the outer wall 58 of the daisy chaining doublewalled pipe 50. This vacuum may help drain the fuel back to the underground storage tank 34. In an exemplary embodiment, the fluid connection 88 may also be double walled so as to comply with any appropriate regulations.[0039] FIG. 7 illustrates the methodology of the present invention. During new construction of the fueling environment 10, or perhaps when adding the present invention to an existing fueling environment 10, the daisy chained piping system according to the present invention is installed (block 100). The pipe connection between the first fuel dispenser 32.sub.1 and the underground storage tank 34 may, in an exemplary embodiment, be sloped such that gravity assists the drainage from the fuel dispenser 32 to the underground storage tank 34. The leak detection system, and particularly, the leak detection probes 64, are installed in the manifolds 52 of the fuel dispensers 32 (block 102). Note that the leak detection probes 64 may be installed during construction of the fuel dispensers 32 or retrofit as needed. In any event, the leak detection probes 64 may communicate with the site communicators such as the site controller 26 or the tank monitor 36 as needed or desired. This communication may be for alarm purposes, calibration purposes, testing purposes or the like as needed or desired. Additionally, this communication may pass through the site communicator to a remote location if needed. Further, note that additional leak detectors (not shown) may be installed for redundancies and/or positioned in the sumps of the fuel dispensers 32. Still further, leak detection programs may be existent to determine if the underground storage tank 34 is leaking. These additional leak detection devices may likewise communicate with the site communicator as needed or desired.[0040] The fueling environment 10 operates as is conventional, with fuel being dispensed to vehicles, vapor recovered, consumers interacting with the points of sale, and the operator generating revenue (block 104). At some point a leak occurs between two fuel dispensers 32.sub.x and 32.sub.x+1. Alternatively, the leak may occur at a fuel dispenser 32.sub.x+1 (block 106). The leaking fuel flows towards the underground storage tank 34 (block 108), as a function of the vacuum existent in the outer wall 58, via gravity or the like. The leak is detected at the first downstream leak detection probe 64 (block 110). Thus, in the two examples, the leak would be detected by the leak detection probe 64 positioned within the fuel dispenser 32.sub.x. This helps in pinpointing the leak. An alarm may be generated (block 112). This alarm may be reported to the site controller 26, the tank monitor 36 or other location as needed or desired.[0041] A second leak detection probe 64, positioned downstream of the first leak detection probe 64 in the fuel dispenser 32.sub.x-1, will then detect the leaking fuel as it flows past the second leak detection probe 64 (block 114). This continues, with the leak detection probe 64 in each fuel dispenser 32 downstream of the leak detecting the leak until fuel dispenser 32.sub.1 detects the leak. The fuel is then returned to the underground storage tank 34 (block 116).[0042] If all downstream leak detection probes 64 detect the leak at query block 118, that is indicative that the system works (block 120). If a downstream leak detection probe 64 fails to detect the leak during the query of block 118, then there is potentially a failure in the outer wall 58 and an alarm may be generated (block 122). Further, if the leak detection probes 64 associated with fuel dispensers 32.sub.x+1 and 32.sub.x-1 both detect the leak, but the leak detection probe。