氢气吸附原理
变压吸附制氢原理
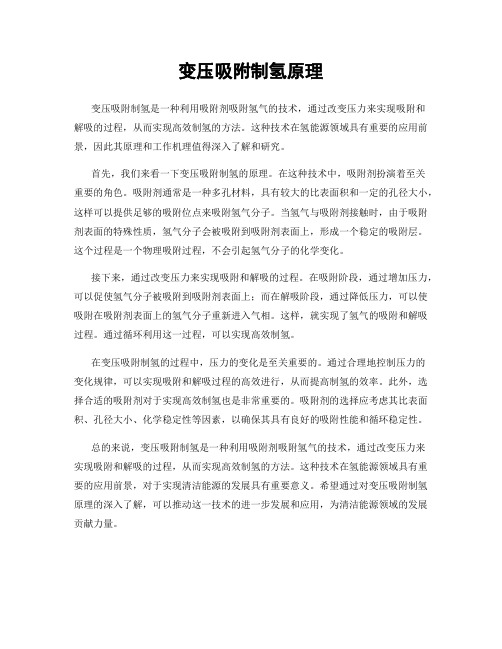
变压吸附制氢原理变压吸附制氢是一种利用吸附剂吸附氢气的技术,通过改变压力来实现吸附和解吸的过程,从而实现高效制氢的方法。
这种技术在氢能源领域具有重要的应用前景,因此其原理和工作机理值得深入了解和研究。
首先,我们来看一下变压吸附制氢的原理。
在这种技术中,吸附剂扮演着至关重要的角色。
吸附剂通常是一种多孔材料,具有较大的比表面积和一定的孔径大小,这样可以提供足够的吸附位点来吸附氢气分子。
当氢气与吸附剂接触时,由于吸附剂表面的特殊性质,氢气分子会被吸附到吸附剂表面上,形成一个稳定的吸附层。
这个过程是一个物理吸附过程,不会引起氢气分子的化学变化。
接下来,通过改变压力来实现吸附和解吸的过程。
在吸附阶段,通过增加压力,可以促使氢气分子被吸附到吸附剂表面上;而在解吸阶段,通过降低压力,可以使吸附在吸附剂表面上的氢气分子重新进入气相。
这样,就实现了氢气的吸附和解吸过程。
通过循环利用这一过程,可以实现高效制氢。
在变压吸附制氢的过程中,压力的变化是至关重要的。
通过合理地控制压力的变化规律,可以实现吸附和解吸过程的高效进行,从而提高制氢的效率。
此外,选择合适的吸附剂对于实现高效制氢也是非常重要的。
吸附剂的选择应考虑其比表面积、孔径大小、化学稳定性等因素,以确保其具有良好的吸附性能和循环稳定性。
总的来说,变压吸附制氢是一种利用吸附剂吸附氢气的技术,通过改变压力来实现吸附和解吸的过程,从而实现高效制氢的方法。
这种技术在氢能源领域具有重要的应用前景,对于实现清洁能源的发展具有重要意义。
希望通过对变压吸附制氢原理的深入了解,可以推动这一技术的进一步发展和应用,为清洁能源领域的发展贡献力量。
psa变压吸附制氢原理

psa变压吸附制氢原理变压吸附技术(PSA)是一种用于制备高纯度氢气的重要技术。
它是一种基于压力变化的吸附分离技术,利用吸附剂对不同组分气体的选择性吸附能力,使得气体在不同压力下被吸附和解吸,从而实现气体的分离和纯化。
PSA技术在制氢领域具有广泛的应用,其制氢原理主要包括吸附、脱附和再生三个过程。
本文将从PSA制氢的基本原理、吸附剂的选择、操作参数的优化以及工业应用等方面进行详细介绍。
第一部分:PSA制氢的基本原理PSA制氢的基本原理是基于吸附和脱附的分离过程。
在PSA制氢系统中,通常包括两个吸附塔,其中一个用于吸附,另一个用于脱附和再生。
制氢的流程包括吸附、脱附和再生三个主要过程。
首先,原料气混合物通过吸附塔,在吸附剂上进行吸附,其间不同气体在吸附剂上的亲和力不同,会导致气体组分的分离。
其次,通过调整压力和温度等操作参数,实现吸附剂的脱附,将所需的氢气从吸附剂上解吸出来。
最后,通过再生操作,使吸附剂再次恢复吸附能力,为下一轮吸附脱附过程做准备。
通过不断循环这一流程,可以实现高纯度氢气的制备。
第二部分:吸附剂的选择吸附剂的选择对于PSA制氢过程非常重要。
在PSA制氢系统中,吸附剂的选择要考虑其吸附容量、选择性、热稳定性以及再生性等因素。
常用的吸附剂包括活性炭、分子筛和铜铁氧体等,它们在吸附和脱附过程中有不同的性能表现。
活性炭具有较大的比表面积和吸附能力,适用于吸附大分子量气体;分子筛具有较强的分子筛分离能力,适用于吸附小分子量气体;铜铁氧体具有较好的热稳定性和选择性,适用于高温条件下的制氢过程。
在实际应用中,要根据原料气的成分和制氢的工艺条件,选择合适的吸附剂,以实现高效的PSA制氢。
第三部分:操作参数的优化在PSA制氢系统中,操作参数的优化对于提高制氢效率和氢气纯度非常重要。
操作参数包括吸附压力、脱附压力、再生温度等。
首先,吸附压力是决定气体吸附量的关键参数,要合理选择吸附压力,以实现高效的气体吸附。
氢气干燥器的原理
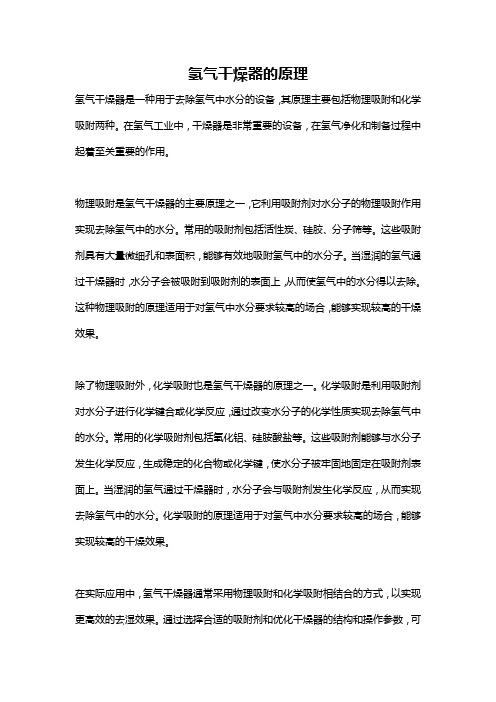
氢气干燥器的原理氢气干燥器是一种用于去除氢气中水分的设备,其原理主要包括物理吸附和化学吸附两种。
在氢气工业中,干燥器是非常重要的设备,在氢气净化和制备过程中起着至关重要的作用。
物理吸附是氢气干燥器的主要原理之一,它利用吸附剂对水分子的物理吸附作用实现去除氢气中的水分。
常用的吸附剂包括活性炭、硅胶、分子筛等。
这些吸附剂具有大量微细孔和表面积,能够有效地吸附氢气中的水分子。
当湿润的氢气通过干燥器时,水分子会被吸附到吸附剂的表面上,从而使氢气中的水分得以去除。
这种物理吸附的原理适用于对氢气中水分要求较高的场合,能够实现较高的干燥效果。
除了物理吸附外,化学吸附也是氢气干燥器的原理之一。
化学吸附是利用吸附剂对水分子进行化学键合或化学反应,通过改变水分子的化学性质实现去除氢气中的水分。
常用的化学吸附剂包括氧化铝、硅胺酸盐等。
这些吸附剂能够与水分子发生化学反应,生成稳定的化合物或化学键,使水分子被牢固地固定在吸附剂表面上。
当湿润的氢气通过干燥器时,水分子会与吸附剂发生化学反应,从而实现去除氢气中的水分。
化学吸附的原理适用于对氢气中水分要求较高的场合,能够实现较高的干燥效果。
在实际应用中,氢气干燥器通常采用物理吸附和化学吸附相结合的方式,以实现更高效的去湿效果。
通过选择合适的吸附剂和优化干燥器的结构和操作参数,可以实现对氢气中水分的高效去除,确保氢气的干燥度符合工艺要求。
除了吸附原理外,氢气干燥器还需要考虑到干燥器本身的稳定性、可靠性和运行成本。
在选择吸附剂时,需要考虑到吸附剂的稳定性和循环再生性能,以确保干燥器的长期稳定运行。
在设计干燥器结构和操作参数时,需要考虑到氢气的流速、压力、温度等因素,以确保干燥器能够在不同工况下都能够保持良好的干燥效果。
在运行维护方面,需要考虑到干燥器的再生方式、再生周期、再生能耗等因素,以确保干燥器的运行成本能够得到控制。
总之,氢气干燥器是一种通过物理吸附和化学吸附原理去除氢气中水分的设备,其干燥效果受到吸附剂选择、干燥器结构设计和操作参数等多种因素的影响。
制氢吸附原理

制氢吸附原理
制氢吸附原理是利用微孔吸附材料在气液或气体中的一种或几种组分上的选择性吸附原理,把氢气分离出来。
一般情况下,吸附物的吸引比化学分子小,所以升高温度或降低吸附物的局部压力都可能使吸附物消失。
氢气分离常用的吸附剂是沸石和活性炭,变压吸附制氢的基本原理是利用吸附剂对不同气体的吸附能力、吸附力、吸附量随压力的不同而不同的性质,当吸附剂选择吸附时,压力吸附混合物中的易吸组分(一般为物理吸附),在吸附床减压时,将这两种吸附组分分离,这样,吸附剂得以再生,使用二塔或多塔交替循环操作,连续生产。
制氢吸附有如下优点:产品纯度高;一般可在室温和不高的压力下工作,床层再生时不用加热,产品纯度高;设备简单,操作、维护简便;连续循环操作,可完全达到自动化。
因此,当这种新技术问世后,就受到各国工业界的关注,竞相开发和研究,发展迅速,并日益成熟。
氢气吸附原理

第一章前言本装置是采用变压吸附(简称PSA)法从富氢气流中回收或提纯氢气。
改变操作条件可生产出不同纯度的氢气,氢气纯度最高可达99.999%以上。
本装置采用气相吸附工艺,因此,原料气不应含有任何液体或固体。
本说明中涉及到的压力均为表压,组成浓度为摩尔百分数,流量除专门标注外均为标准状态下的流量。
第二章工艺说明本装置为四塔二次均压工艺流程,它的关键部分由四个吸附塔(以下简称A、B、C、D塔)和十八个气动角座阀和二只梭阀组成。
另外在原料气输入管路上配置一个原料气缓冲罐(以下简称为E),在产品气输出管路上配置一个氢缓冲罐(以下简称F),使产品气能稳定地输出。
一、工作原理和过程实施本装置采用变压吸附(PSA)分离气体的工艺,其原理是利用所采用的吸附剂对不同吸附质的选择性吸附和吸附剂对吸附质的吸附容量随压力变化而有差异的特性,在吸附剂选择吸附条件下,高压吸附除去原料中杂质组分,低压下脱附这些杂质而使吸附剂获得再生。
整个操作过程是在环境温度下进行的。
吸附剂的再生是通过三个基本步骤来完成的:1.吸附塔压力降至低压首先是顺着吸附的方向进行降压(以下简称为顺向放压),接着是逆吸附的方向进行降压(以下简称为逆向放压)。
顺向放压时,有一部分吸附剂仍处于吸附状态。
逆向放压时,被吸附的部分杂质从吸附剂中解吸出来,并被排除出吸附塔。
2.用产品气在低压下冲洗吸附剂,以清除尚残留于吸附剂中的杂质。
3.吸附塔升压到吸附压力,以准备再次分离原料气。
本装置采用四塔二次均压变压吸附过程,即每个吸附塔在一次循环中均需要经历吸附(A)、一次均压(1ED),顺向放压(PP),二次均压(2ED),逆向放压(D)、一次升压(2ER),二次升压(1ER),以及最终升压(FR)等九个步骤,四个吸附塔在执行程序的安排上相互错开,构成一个闭路循环,以保证原料连续输入和产品不断输出。
整个过程主要由十八只气动角座阀和二只梭阀来实现。
氢气提纯工艺流程图)程控阀的功能说明如下:(见PSA-H2高选阀——A、B、C、D塔出料和二次均压高选阀KV e,f——A、B塔产品输出,以C、D塔终充,对A、B塔均压,冲洗阀KV g,h——C、D塔产品输出,以A、B塔终充,对C、D塔均压,冲洗阀KV a,b,c,d——A、B、C、D塔进料阀KV –e,-f——二次均压阀 KVi,j,k,l—逆向放压,冲洗排放切换阀KV m ——二均阀 KV -m ——逆向排放阀A、B、C、D——吸附塔 E——原料气缓冲罐F——氢缓冲罐现以A塔为例对工作过程进行说明:1.吸附(A)原料气通过气动角座阀KV a进入A塔,A塔在工作压力下吸附流入原料通过气动角座阀KV e和高选阀气中的杂质组分,未被吸附的产品组分H2流出,其中大部分作为产品从本系统中输出。
氢气吸附塔的原理和作用

氢气吸附塔的原理和作用
氢气吸附塔的原理是基于吸附剂对氢气的选择性吸附能力。
在氢气吸附塔中,通常使用吸附剂填充塔体,当混合气体通过吸附塔时,吸附剂会选择性地吸附氢气,而不吸附其他气体成分。
这样就可以实现氢气的分离和纯化。
氢气吸附塔的作用主要包括两个方面,一是氢气的分离,二是氢气的纯化。
首先,氢气吸附塔可以用于氢气的分离。
在许多工业生产和实验室研究中,需要从混合气体中分离出纯净的氢气。
通过氢气吸附塔,可以将混合气体中的氢气与其他气体成分分离开来,实现氢气的提纯和纯净氢气的获取。
其次,氢气吸附塔可以用于氢气的纯化。
在一些需要高纯度氢气的工业生产过程中,需要对氢气进行纯化处理,以满足生产工艺的要求。
氢气吸附塔通过选择性吸附氢气,可以有效去除混合气体中的杂质气体成分,从而实现氢气的纯化。
总的来说,氢气吸附塔通过选择性吸附氢气的原理,可以实现
氢气的分离和纯化,具有重要的应用价值。
在氢能源和化工领域,氢气吸附塔的原理和作用将继续发挥重要作用,为氢气的生产和利用提供技术支持。
氢气变压吸附原理
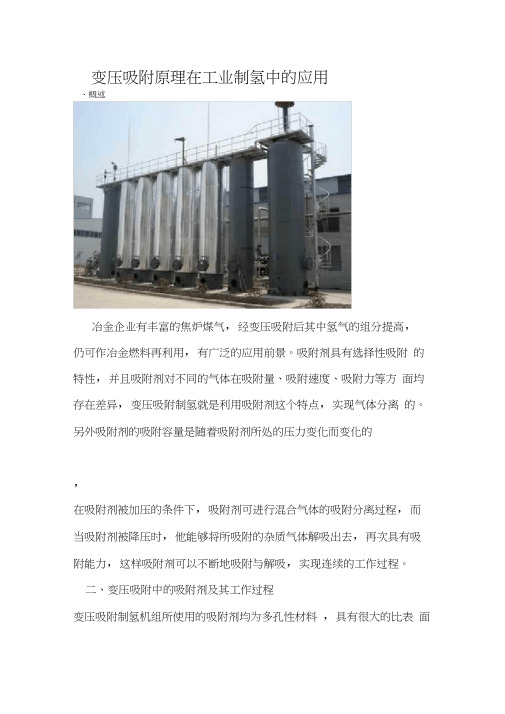
变压吸附原理在工业制氢中的应用、概述冶金企业有丰富的焦炉煤气,经变压吸附后其中氢气的组分提高,仍可作冶金燃料再利用,有广泛的应用前景。
吸附剂具有选择性吸附的特性,并且吸附剂对不同的气体在吸附量、吸附速度、吸附力等方面均存在差异,变压吸附制氢就是利用吸附剂这个特点,实现气体分离的。
另外吸附剂的吸附容量是随着吸附剂所处的压力变化而变化的,在吸附剂被加压的条件下,吸附剂可进行混合气体的吸附分离过程,而当吸附剂被降压时,他能够将所吸附的杂质气体解吸出去,再次具有吸附能力,这样吸附剂可以不断地吸附与解吸,实现连续的工作过程。
二、变压吸附中的吸附剂及其工作过程变压吸附制氢机组所使用的吸附剂均为多孔性材料,具有很大的比表面积。
常用吸附剂的比表面积见表1。
表1 常用吸附剂的比表面积(米2/ 克)吸附剂细孔硅胶活性氧化铝活性炭A型分子筛X、丫型分子筛合成丝光沸石比表面积500 〜600 230〜380 800 〜1050 750 〜800 800〜1000 300〜500由于分子运动学说可知,当吸附剂与吸附介质相接触时,在一定的运行条件下,单位时间内到达吸附剂表面的分子数与离开吸附剂表面的分子数存在一个动态的平衡关系,并且有一些分子还会浓聚或停留在吸附剂表面上,此种现象就称为吸附。
吸附过程是一个非常复杂的过程,一般可分为三个阶段: (1) 外扩散—气体分子从外界空间到吸附剂颗粒外表面; (2) 内扩散—气体分子沿着吸附剂的微孔深入其吸附表面; (3) 吸附在内吸附表面上。
而解吸脱附(再生) 过程与吸附过程相同,只是经过(3) 、(2) 、(1) 的运行步骤,反向从吸附剂表面向外界空间扩散。
评价一种吸附剂的性能优劣,是从吸附剂对某一纯组分的静吸附量a0 来考核的,a0 是温度( T) 与气体分压(Pi) 的函数,见式(1) 。
a0 = f ( T ,Pi) (1)在工业生产中,由于诸多因素,吸附剂往往不能达到完全的吸附平衡为此要引入动吸附量 a 的概念。
原理为氢键吸附的是

氢键吸附原理及应用
氢键是一种化学键,其原理是氢原子与其他原子的电负性差形成
的电荷分布不均。
因此,氢原子便带有一定的正电荷,可以与其他原
子中的负电荷形成静电相互作用。
氢键吸附是指氢原子与石墨烯等表
面上的氧原子形成氢键,从而吸附在表面上的现象。
氢键吸附在许多材料的表面上应用广泛,比如用于氢气储存、催
化反应等。
氢气储存是目前很多国家研究的课题之一,其难点在于氢
气分子小、分散性强,储存成本高昂。
氢键吸附材料可以将氢气吸附
在表面上,从而大大降低储存成本。
此外,氢键吸附还可以用于催化反应。
通过改变材料表面的结构,使得其具有更强的活性,从而提高催化反应效率。
最近研究表明,氢
键吸附可以在催化反应中发挥重要作用,为提高反应速率和降低催化
剂的使用量提供了新思路。
综上所述,氢键吸附原理应用广泛,对于提高能源利用效率和环
境保护有重要意义。
未来,我们还需要更多的研究和探索,从而发现
更多氢键吸附材料,实现氢气储存和催化反应的更高效率和更广泛应用。
- 1、下载文档前请自行甄别文档内容的完整性,平台不提供额外的编辑、内容补充、找答案等附加服务。
- 2、"仅部分预览"的文档,不可在线预览部分如存在完整性等问题,可反馈申请退款(可完整预览的文档不适用该条件!)。
- 3、如文档侵犯您的权益,请联系客服反馈,我们会尽快为您处理(人工客服工作时间:9:00-18:30)。
第一章前言本装置是采用变压吸附(简称PSA)法从富氢气流中回收或提纯氢气。
改变操作条件可生产出不同纯度的氢气,氢气纯度最高可达99.999%以上。
本装置采用气相吸附工艺,因此,原料气不应含有任何液体或固体。
本说明中涉及到的压力均为表压,组成浓度为摩尔百分数,流量除专门标注外均为标准状态下的流量。
第二章工艺说明本装置为四塔二次均压工艺流程,它的关键部分由四个吸附塔(以下简称A、B、C、D塔)和十八个气动角座阀和二只梭阀组成。
另外在原料气输入管路上配置一个原料气缓冲罐(以下简称为E),在产品气输出管路上配置一个氢缓冲罐(以下简称F),使产品气能稳定地输出。
一、工作原理和过程实施本装置采用变压吸附(PSA)分离气体的工艺,其原理是利用所采用的吸附剂对不同吸附质的选择性吸附和吸附剂对吸附质的吸附容量随压力变化而有差异的特性,在吸附剂选择吸附条件下,高压吸附除去原料中杂质组分,低压下脱附这些杂质而使吸附剂获得再生。
整个操作过程是在环境温度下进行的。
吸附剂的再生是通过三个基本步骤来完成的:1.吸附塔压力降至低压首先是顺着吸附的方向进行降压(以下简称为顺向放压),接着是逆吸附的方向进行降压(以下简称为逆向放压)。
顺向放压时,有一部分吸附剂仍处于吸附状态。
逆向放压时,被吸附的部分杂质从吸附剂中解吸出来,并被排除出吸附塔。
2.用产品气在低压下冲洗吸附剂,以清除尚残留于吸附剂中的杂质。
3.吸附塔升压到吸附压力,以准备再次分离原料气。
本装置采用四塔二次均压变压吸附过程,即每个吸附塔在一次循环中均需要经历吸附(A)、一次均压(1ED),顺向放压(PP),二次均压(2ED),逆向放压(D)、一次升压(2ER),二次升压(1ER),以及最终升压(FR)等九个步骤,四个吸附塔在执行程序的安排上相互错开,构成一个闭路循环,以保证原料连续输入和产品不断输出。
整个过程主要由十八只气动角座阀和二只梭阀来实现。
程控阀的功能说明如下:(见PSA-H2氢气提纯工艺流程图)高选阀——A、B、C、D塔出料和二次均压高选阀KV e,f——A、B塔产品输出,以C、D塔终充,对A、B塔均压,冲洗阀KV g,h——C、D塔产品输出,以A、B塔终充,对C、D塔均压,冲洗阀KV a,b,c,d——A、B、C、D塔进料阀KV –e,-f——二次均压阀 KVi,j,k,l—逆向放压,冲洗排放切换阀KV m ——二均阀 KV -m ——逆向排放阀A、B、C、D——吸附塔 E——原料气缓冲罐F——氢缓冲罐现以A塔为例对工作过程进行说明:1.吸附(A)原料气通过气动角座阀KV a进入A塔,A塔在工作压力下吸附流入原料气中的杂质组分,未被吸附的产品组分H2通过气动角座阀KV e和高选阀流出,其中大部分作为产品从本系统中输出。
剩余部分通过调节针阀和气动角座阀KV h向D塔进行最终级升压。
吸附过程直至输出产品杂质浓度超过规定值时结束。
2.一次降压平衡(1ED),简称:一次均压操纵气动角座阀KVa,切断进A塔原料气,同时操纵气动角座管阀KV f,使A塔与刚结束一次升压步骤的B塔以出口端相连,实行一次压力平衡,一次均压后A、B塔压力基本相等。
回收了A塔的死空间的H2。
3.顺向放压(PP),简称:顺放A塔完成一次降压平衡(1ED)步骤后,又操纵气动角座阀KV f,使B塔最终升压;A塔内剩余气体顺着出口方向通过气动角座阀KV –e,再通过调节针阀限流,然后再通过气动角座阀KV-g向刚完成逆向放压的C塔进行冲洗。
当A塔压力降至规定值后,停止顺向放压,进行下一步骤。
4.二次降压平衡(2ED),简称:二次均压操纵气动角座阀KV –e和KV m,使A塔剩余的气体流过选择阀G2进入C塔底部,实现二次均压后A、C塔压力基本相等,又进一步的回收了A 塔的死空间的H2。
5.逆向放压(D),简称:逆放A塔二次均压(2ED)结束后,操纵气动角座阀KV i和KV –m,使A塔内剩余的气体从塔的入口端排出放空,A塔进行脱附。
6.冲洗(P)A塔逆放后,尚残留在踏内的杂质是利用D塔的顺放气,通过气动角座阀KV h,再通过调节针阀限流,然后再通过气动角座阀Kv e向刚完成逆向放压的A塔床层进行冲洗,塔内杂质进一步脱附,冲洗脱附气通过气动角座阀KV i排出放空。
7.一次升压平衡(2ER),简称:一次升压A塔冲洗步骤结束后,操纵气动角座阀KV m,使A塔排放处关闭,利用D 塔顺放后的剩余压力对A塔进行顺向压力平衡。
A塔压力升高直至两塔压力基本相等,此时回收D塔空间的H2。
8.二次升压平衡(1ER),简称:二次升压在一次升压步骤结束后,操纵气动角座阀KV e处于中通状态,同时操纵气动角座阀KV f处于中通状态利用B塔的一次均压气对A塔进行压力平衡,A塔压力进一步提高。
直至两塔压力基本相等,此时回收了B塔死空间的H2。
9.最终升压(FR),简称:终充A塔的最终升压是用产品气来升压的,操纵气动角座阀KV e,使其与调节针阀连通。
C塔通过气动角座阀KV g输出产品气,A塔的最终升压通过调节针阀与它连通,调节针阀是最终升压的限流阀,在规定时间内最终升压使A塔压力基本接近吸附压力。
通过这一步骤后,再生过程全部结束,紧接着便进行下一次循环。
其它三个塔的操作步骤与A塔相同,不过在时间上是相互错开的。
同一时间内各塔执行着不同的步骤。
调节针阀用于吸附塔的顺放流量调节,使塔内压力在切换时达到规定值;另一调节针阀用于最终升压的流量调节,使之在切换时,升压压力接近吸附压力。
两调节针阀,配合程序控制滑管阀按规定的程序操作及梭阀按逻辑关系动作,使变压吸附工艺过程能不断净化原料气,输出产品气。
二、工艺流程中主要设备1.吸附塔(A、B、C、D)四个吸附塔是装置中的关键设备,本吸附塔结构设计成隔套式,分内塔和外塔,内塔与外塔串联工作,原料气进和产品气出全部设置在下部,与传统的直通式吸附塔结构完全不同。
它的特点:不管在高速气流通过时,吸附塔的吸附剂基本上处于相对静止状态,大大地减小了吸附剂的磨损。
吸附塔进出口设置了对冲式和旋式分布气,使气流分布更均衡。
隔套式结构使吸附塔更加紧凑,在吸附工艺中,吸附时要产生吸附热,解吸时要吸收热,这种现象都将影响吸附效果,本隔套式结构在一定程度上解决了吸附热的平衡问题,提高了吸附剂的吸附能力。
本吸附塔结构已申报专利。
2.气动角座阀(KVa、KVb、KVc、KVd、KVe、KVf、KV-e、KV-f、KVg、KVhKV-g、KV-h、KVi、KVj、KVk、KVl)程控阀门是装置中又一种关键设备,整个制氢工艺过程要靠程控阀门的切换来完成。
目前国内外在四塔二次均压的工艺流程中用22只程控阀来完成制氢工艺过程,并带来工艺流程配管复杂等,只要其中有一只程控阀出故障,装置就得停下来处理,运行可靠性差。
现在我们采用了十八只气动角座阀组来替代22只程控阀,这样就减少了控制阀门,同时也简化了程控系统,提高装置的运行可靠性。
三、工艺流程(参见附图PSA制氢流程图)从外管网或压缩机送入装置的压力≤1.6Mpa的原料气(例如弛放气),经阀到原料气贮罐(E)进行缓冲,通过气动角座阀KVa,b,c,d四个阀的其中一个分别进入四个内装吸附剂的吸附塔(A、B、C、D)组成的变压吸附系统。
原料气在变压吸附系统内,从一个塔的内塔自下而上,然后从外塔自上而下通过其中一个正处于吸附步骤的吸附塔,经选择吸附后,产品气从吸附塔出口端流出,通过阀Kve、KVf、KVg或KVh和高选阀输出,产品气经过吸附塔压力调节阀进入产品气缓冲罐(F),又通过手动阀送往后续纯化装置。
吸附塔入口端排出的解吸气来自逆放和冲洗两个步骤,解吸气通过阀门Kvi KVj、KVk、KVl排出,再通过气动角座阀KV-m进入排放总管。
排出的解吸气通过阻火器排到大气中或回收利用。
在四个吸附塔的入口处,即原料贮罐顶部设置了超压安全保护。
当设定压力超过设定值时,安全阀启跳排入放空总管,然后通过阻火器排入大气中。
原料贮罐底部的球阀是置换时的排放阀,产品气贮罐置换时打开底部球阀排放阀,排放气都排到放空总管,然后通过阻火器排入大气中。
在运行过程中,由于种种原因导致产品纯度不合格时,通过产品连续分析仪发出低纯度报警,手动将不合格气由限流放空阀门排出,等产品合格后,手动关闭限流阀,将合格的产品气回到氢贮罐F。
系统设计了氮气置换阀,装置投运之前必须用氮气置换合格后,才能通入原料气。
第三章程序控制系统及工艺过程参数检测系统配有一套程序控制系统;二套流量检测;一套产品组分检测报警;一套压力调节系统,装置各点的压力指示为弹簧管压力表。
一、程序自动控制系统本装置共有十八只气动角座阀,均由程序控制器来控制和操纵。
程控机上右边设有PSA流程示意图,指示灯显示阀门的各种状态。
左边为西门子提供的控制操作面板,通过上面的操作键可以对工艺过程中每一步骤的工作时间任意设定,操作面板上方有液晶显示屏,显示四个吸附塔正在工作的各个状态,同时显示正在工作的时间。
在液晶显示屏上有一路压力过高报警,一个信号报警显示提供操作人员注意。
(一)面板下面操作键说明如下:F1启动开关:是本控制器的投入工作的开关;F2停止开关:是本控制器停止工作的开关;F3暂停开关:暂停和退出暂停的开关;F4步进(点动键):立即执行下一步程序;F5手动/自动(黑白开关):自动:按操作面板设定值输出信号;自动:流程中阀位显示黑色,由手控开关输出信号;1、手控开关(黑白开关):在手动状态时,由该开关控制输出,在自动状态时,手动开关无作用。
F6首页:立即恢复最初画面;(二)面板显示内容:1、阀位显示:由黑白两种颜色显示气动角座阀的开关阀位状态(液晶显示屏显示黑色表示阀门开在哪个位置)。
通过阀位指示操作人员可清楚地看出工艺流程中气体的流向。
2、报警信号指示:在液晶显示屏上有一路压力过高报警,一个信号报警显示。
3、吸附塔工作状态显示:在西门子的液晶显示屏上实时显示四个吸附塔的工作状态(中文显示)。
4、工作时间显示:在西门子的液晶显示屏上同时显示每个工艺步骤正在执行的时间。
每一步骤开始时从0到设定时间结束,切换到下一步骤后,又从0到设定时间结束。
(三)自动切换系统:程序控制器:是以它的切换时间为时间发信,切换时间由西门子提供的控制操作面板上的按键设定的时间来进行。
切换程序要满足二次均压或四塔一次均压工艺要求,其程序编制在西门子S7-200可编程序控制器内(S7-200安装在箱体内),然后再由S7-200可编程序控制器输出控制信号(电压DC24V)。
电气转换器:电气转换为电控滑阀,集中安装在现场的一只控制箱内,将电信号转换成气信号去控制程控阀。
控制器输出信号为14路,电控滑阀为14只,14只电控滑阀安装在控制箱内的集成底板上。