服装色差的识别成因与预防(可编辑修改word版)
浅谈色差产生的原因

浅谈色差产生的原因色差也叫色偏,在印刷中是不可避免的,只是大小的差异,一般要求△E*<3。
在这里主要从客观环境、印刷材料、印刷工艺、印刷设备四个方面分析色差产生的原因。
一、客观环境(一)照明光源。
我们一般说纯白才是标准的照明光源,但事实上并不是所有的照明光源都符合标准要求,或多或少都带有点偏色。
常见光源色偏情况如下表:偏色。
一般来说,光源偏色会导致印刷品往相应色偏色。
若光源偏黄,印刷品偏黄,光源偏蓝,印刷品偏蓝。
(二)环境色的影响。
环境色对人眼判断色彩影响很大。
同一绿色快置于红色环境中,它偏红。
如如将黑色60%置于实地和5%网点的环境中,可以明显的感受到它们的亮度有所差异。
因此辨别色差时必须注意消除环境色的影响。
二、印刷材料印刷材料主要是指纸张和油墨。
(一)纸张:1.纸张的白度,白度不同对印刷品颜色有重要影响,这是因为白度不同的纸张其效果就相当于在油墨中加入了不同程度的灰和黑,所以即使印刷时所用的墨量、色相都没有变化,由于白度也会造成色差。
2.纸张的吸收性,吸收性大的纸张,印迹不能很好地形成墨层,色彩不再鲜艳饱和。
3.纸张的光泽度和平滑度,如果纸张的光泽度和平滑度较高,我们观察到的颜色基本上是透过墨层反射出的颜色,主色光饱和度高。
如果纸张的表面粗糙、光泽度低,就会产生漫反射,就会降低主色光的饱和度,使我们人眼观察印刷品的颜色感觉变淡。
相同的墨量用密度计测量密度值。
平滑度光泽度高的纸张,密度值高。
平滑度光泽度低的纸张,密度值低。
(二)油墨:印刷墨层厚度和粘度不适容易产生印刷色差,印刷时,只有以适度而又均匀的印刷墨层,才能较好地保证印品的墨色质量,并有效防止印刷粘脏故障的产生。
若印刷墨层偏厚其粘度相应就增加,由此容易引起印刷中的纸面掉粉、拉毛现象,进而影响印品墨色均匀。
但若印刷墨层偏薄及油墨粘稠度过小,印品的墨色就显得偏淡,印品的视觉效果也就差。
随着印刷机转动时间的增长以及印刷速度的加快,摩擦系数增大,油墨温度升高,油墨的粘度会有所下降,所以调墨时必须考虑这些因素,以确保同批产品获得相对均衡的印刷墨色。
轧染色差的原因及预防措施
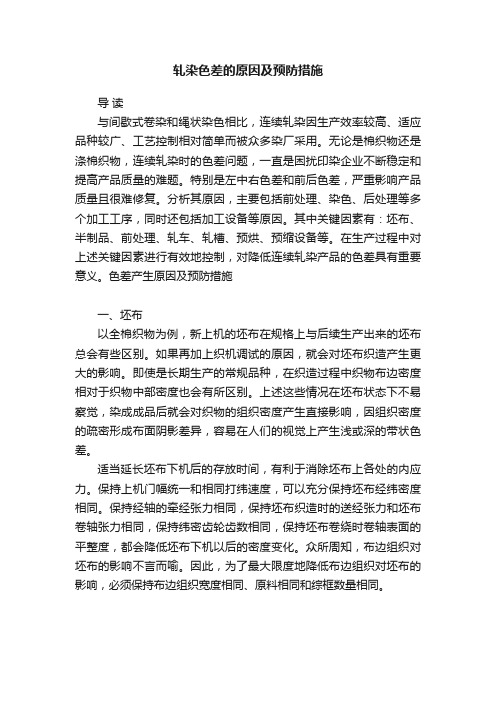
轧染色差的原因及预防措施导读与间歇式卷染和绳状染色相比,连续轧染因生产效率较高、适应品种较广、工艺控制相对简单而被众多染厂采用。
无论是棉织物还是涤棉织物,连续轧染时的色差问题,一直是困扰印染企业不断稳定和提高产品质量的难题。
特别是左中右色差和前后色差,严重影响产品质量且很难修复。
分析其原因,主要包括前处理、染色、后处理等多个加工工序,同时还包括加工设备等原因。
其中关键因素有:坯布、半制品、前处理、轧车、轧槽、预烘、预缩设备等。
在生产过程中对上述关键因素进行有效地控制,对降低连续轧染产品的色差具有重要意义。
色差产生原因及预防措施一、坯布以全棉织物为例,新上机的坯布在规格上与后续生产出来的坯布总会有些区别。
如果再加上织机调试的原因,就会对坯布织造产生更大的影响。
即使是长期生产的常规品种,在织造过程中织物布边密度相对于织物中部密度也会有所区别。
上述这些情况在坯布状态下不易察觉,染成成品后就会对织物的组织密度产生直接影响,因组织密度的疏密形成布面阴影差异,容易在人们的视觉上产生浅或深的带状色差。
适当延长坯布下机后的存放时间,有利于消除坯布上各处的内应力。
保持上机门幅统一和相同打纬速度,可以充分保持坯布经纬密度相同。
保持经轴的牵经张力相同,保持坯布织造时的送经张力和坯布卷轴张力相同,保持纬密齿轮齿数相同,保持坯布卷绕时卷轴表面的平整度,都会降低坯布下机以后的密度变化。
众所周知,布边组织对坯布的影响不言而喻。
因此,为了最大限度地降低布边组织对坯布的影响,必须保持布边组织宽度相同、原料相同和综框数量相同。
二、半制品半制品的加工质量对成品质量的影响远远大于染色工序本身。
所以,从坯布准备开始,翻布、打印、缝头等准备工序的每次加工都会影响棉织物练漂的加工质量。
烧毛、退浆、煮练、漂白、丝光、轧水和烘干工序都可以决定染色质量。
半制品质量问题通常会在染色才体现出来,因此,严格控制棉织物前处理加工各工序的工艺参数、工艺配方和工艺流程就显得非常重要。
【涤棉】涤棉混纺织物色差成因及解决方法

【纯干货】涤棉混纺织物色差成因及解决方法涤棉混纺织物热熔染色色差表现形式、产生原因及克服办法1.两边色差1)染液浸轧:两边带液量不一致;2)预烘和焙烘:烘干程度不均匀或不充分;2.边中色差及左中右色差1)轧辊轴心发生变形,产生轧余率不一致;2)在预烘或热熔时布幅中间和两边温度和风量不一致;a)在一般空车情况下,中间温度高于两边温度(焙烘箱)(热熔);b)散热时,两边易干,而中间慢,造成中间温度稍低(预烘);3)染料性能不同:由于温度中高边低,产生固色条件差异;低温型会发生中浅边深,高温型分散染料却相反;克服办法:第一,改善织物干燥的均匀性;第二,采用均匀轧车;第三,改善轧液的均匀性;第四,染色时要合理选用染料;3.正反面色差1)轧辊软硬度差异太大;2)预烘时正反面温度和风量不一致;3)热风预烘拔风效果差,湿度过度;4)克服办法:第一,合理选择软辊的硬度;第一,正反面烘燥力求均匀;第二,热风部分采用横导辊穿布方式;第三,预烘室拔风要充分,防止湿度过高;第四,在染料溶液中适当加入防泳移剂4.左右对角色差(实质上是局部性的正反面色差)1)预烘时左右热量不匀,辐射强度不一;2)喷风量左右不匀;3)金属导辊左右两头散热不一4)克服办法:从设备上找根源;5.前后色差1)坯布方面:纤维的种类、质量、配棉的变动;2)练漂前处理方面A.前处理采用设备不同,工艺条件不容易掌握一致,半制品染色后色泽有区别;B.退浆效果如有差别,也会形成色泽深浅;C.热定型速度和风速;D.丝光后的pH值:最显著的产生原因;3)染色方面A.进焙烘箱之前织物干潮不一致;B.热熔温度是染色过程中影响色差最显著的因素;C.车速、染液、显色液、还原液浓度掌握不一致,造成前后搭色不一;D.产地、批号不同的染料,色光有差异;4)后整理方面:树脂或高温焙烘可引起某些染料色光变化。
6.克服办法:第一,防止坯布因素,掌握纤维原料和上浆成分的变化情况;第二,练漂前处理机台要“三定”(定工艺、定机台、定人员);第三,要经常检查定型机、热风机运转情况;第四,染整加工的半制品,其退浆、丝光后织物上的pH值须“三查”;第五,染色用染料要按产地、批号分开堆放,控制好色光;第六,染料上车要研磨认真;第七,预烘后进入焙烘箱前布身要干;第八,在染色过程中,要严格控制工艺条件和操作规程;第九,染色机上装自控温装置;第十,出布处建贴样制度;第十一,染色后,成品检验按次序进行,分色成包;。
染整问题分析!原样、前后、左中右色差,色条、色花、色斑、破洞、风干印、皱条、压皱印!

染整问题分析!原样、前后、左中右色差,色条、色花、色斑、破洞、风干印、皱条、压皱印!平幅染整加工具有设备自动化程度高,各种工艺技术参数自动检测和控制手段、方法完备,连续化生产,生产效率高、劳动力成本低、产品质量稳定等独特优势。
是纤维素纤维及混纺、交织梭织物的首选印染加工手段。
但如果质量、工艺、技术、操作管理不到位,往往容易出现批量性质量问题,导致批量性返修,增加质量成本,重则造成次品无法返修无法交货,严重影响公司的生产进度、经济效益和信誉。
为此,仅就梭织物平幅连续化染整加工过程中经常出现的主要疵病产生原因、预防措施简述如下。
原样色差、前后色差一、产生原因:1.小样仿色时操作不规范、工艺参数控制不到位,仿色样不能反映染色配方的真实色光。
2.大车放样时称量不准、化料误差、各种工艺技术参数控制不到位,放样样品不能反映染色配方的正常颜色,影响对色人员的正常判断和配方调整偏差。
3.对客户来样没有进行仔细分析,染色配方选择的染料组合与客户来样使用的染料不同,存在同色异谱(跳灯)现象,在不同光源下呈现出不同的颜色。
4.调色人员的眼光误差,导致对色不准。
5.小样仿色、大车放样后没有按客户合同标准进行后整理,导致大货进行后整理时色光变化。
6.染色配方中染料性能差别太大,大车生产过程中工艺参数波动时织物颜色变化太大。
7.染前半成品毛效、白度、pH值、退浆、磨毛效果不一致。
8.染色时主要工艺技术参数波动,如轧槽染液液位波动、车速、予烘温度、焙烘温度、轧车压力、还原(固色)温度、时间、染料浓度、固色液、还原液浓度等的波动,导致颜色变化。
9.染料熨烫变色,导致对色不准。
10.坯布原因:不同厂家、同一厂家不同批次的坯布往往由于棉纤维品质不同、纱线的捻度不同、经纱上浆不同,经处理后织物的吸水性、上染性能存在差异导致染色时出现匹间色差。
11.染料原因:不同厂家、同一厂家不同批次的染料色光、力份存在差异。
二、预防措施:1.认真分析客户来样的纤维类别、使用染料类别、对色光源、后整理效果等内容,采用合同要求的同规格坯布、同类型染料、同样后整理工艺。
边中色差成因及预防论文等二篇

梭织物印染条花疵布成因及预防关键字:梭织物条花疵布成因措施梭织物所产生的各类条花染疵类别繁多,有织物去浆未净条花、煮练不透雨丝条花、烧毛条花、丝光去碱不匀条花、染色泳移条花和织造疏密不匀条花、灯芯绒割绒条花等,这是印染工作者经常遇到的质量问题。
随着目前纺织品国际竞争愈趋激烈,品质的要求也愈趋严格,各类条花染疵的存在影响织物外观,给企业带来的后遗症是不言而喻的。
染整过程为此返工改染甚至“全军覆没” 的事例不胜枚举,鉴于此,有必要对部分梭织物上呈现出来的各类条花染疵作出分析,提出纠正和预防措施。
1.各类条花疵布成因分析及预防办法1.1去浆未净条花1.1.1表现的形式中深色府绸薄织物纬向宽距为1.0 cm左右的经向条花。
1.1.2成因分析该类织物由于经纱纱支较细,织造时为减少断纱现象,一般给予该类织物经纱施加了大量的混合浆料(其成份复杂,有淀粉、PVA、石蜡、防腐剂等组成),这些高浓度混合浆料的存在增加了印染前处理的难度,若印染前处理过程中未将织物上浆料去净就转入后道生产,染色时就会不可避免地产生条花染疵(深色尤甚)。
1.1.3纠正、预防前处理工艺设计要着重考虑如何去除织物上浆料。
下面着重介绍享斯迈O、D、New高温裂解法。
(1)工艺流程:翻缝→高温裂解去浆煮练→烧毛→氧漂。
(2)高温裂解去浆煮练工艺条件:NaOH 56 g/ L;H2O21.3 g/L;O、D、New 8 g/L;H-982精练剂2 g/ L;工作液温度45℃;轧余率80%;履带箱堆置汽蒸50 min,温度100~102℃。
(3)效果:O、D、New高温裂解剂,其耐碱达300 g/L,是集润湿、乳化、分散、螯合、稳定为一体的复合化合物。
经该工艺处理的各类弹力府绸能有效消除条花染疵的产生。
另外,碱氧冷堆、短蒸复氧漂工艺;液下碱煮练、氧漂工艺;清棉师100 T前处理工艺亦可同样克服该类条花染疵的产生。
1.2 纬弹织物易出现的条花1.2.1表现形式纬弹类直贡、纱卡织物纬向宽距为0.5 cm左右的经向无规则条花。
服装染色工艺中色差控制与调整的智能化方法研究
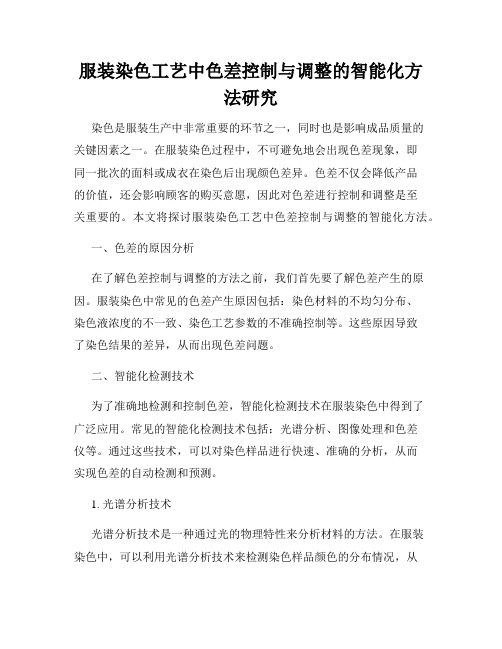
服装染色工艺中色差控制与调整的智能化方法研究染色是服装生产中非常重要的环节之一,同时也是影响成品质量的关键因素之一。
在服装染色过程中,不可避免地会出现色差现象,即同一批次的面料或成衣在染色后出现颜色差异。
色差不仅会降低产品的价值,还会影响顾客的购买意愿,因此对色差进行控制和调整是至关重要的。
本文将探讨服装染色工艺中色差控制与调整的智能化方法。
一、色差的原因分析在了解色差控制与调整的方法之前,我们首先要了解色差产生的原因。
服装染色中常见的色差产生原因包括:染色材料的不均匀分布、染色液浓度的不一致、染色工艺参数的不准确控制等。
这些原因导致了染色结果的差异,从而出现色差问题。
二、智能化检测技术为了准确地检测和控制色差,智能化检测技术在服装染色中得到了广泛应用。
常见的智能化检测技术包括:光谱分析、图像处理和色差仪等。
通过这些技术,可以对染色样品进行快速、准确的分析,从而实现色差的自动检测和预测。
1. 光谱分析技术光谱分析技术是一种通过光的物理特性来分析材料的方法。
在服装染色中,可以利用光谱分析技术来检测染色样品颜色的分布情况,从而判断是否存在色差。
通过这种方法,可以实时监测染色过程中的颜色变化,并进行相应的调整。
2. 图像处理技术图像处理技术可以将染色样品的图像输入计算机进行处理和分析。
通过图像处理技术,可以提取出染色样品的颜色信息,并进行比对和分析,从而得出色差的程度和分布情况。
这种方法可以辅助人工判断染色样品是否合格,并进行调整。
3. 色差仪色差仪是一种专门用于测量和分析色差的仪器。
它可以通过测量染色样品与标准颜色之间的差异,来评估色差的程度和种类。
色差仪具有测量精确、操作简便等特点,因此在服装染色中得到了广泛的应用。
三、智能化调整方法在检测到染色样品存在色差后,智能化调整方法可以自动进行调整,以降低色差的程度。
1. 自动控制染色液浓度染色液浓度的不一致是导致色差的重要原因之一。
智能化调整方法可以通过检测染色液浓度,调整染色液的配比和控制染色液的加入量,从而保证染料的均匀分布,减小色差的发生。
服装数码印花中产生色差的因素以及解决方法

38Technology网印工业Screen Printing Industry2020.06工艺技术服装数码印花的工序相比较传统的丝印等工艺已经简化很多,但还存在着制图、修图、导图、设置曲线等环节,才可以完成整个过程。
由于不同服装数码印花机在技术上有一定的限制、加之环境因素,从而影响服装数码印花品质量,那么产生色差的因素有哪些呢?客观存在的原因是:由于实际生产中有多方面的条件所限,并不可以完全消除颜色误差,只能通过调整来令颜色品质差别控制在合理的颜色标准中。
1.服装数码印花颜色与电脑显示器中的不一样电脑显示器会因不同品牌、型号及个别色值设定的参数,造成视觉上呈现颜色的不同。
基于显示器是以RGB色光成影像,而印刷品则是以CMYK 四色来调色。
两者原理大不同,会导致屏幕显示色与印刷成品产生严重色差,千万不可以用屏幕颜色来校对颜色。
2.服装数码印花环境影响因素环境因素也会对印刷颜色产生影响,印刷时间、服装数码印花墨水质量、温度、湿度、材质特性等,人为无法控制的因素均会对印刷颜色产生影响。
3.颜色色值问题颜色制作时,最浅的颜色色值勿低于8%,否则有可能无法印出。
请勿使用四色黑或四色灰,否则容易在印刷后呈现严重色差。
设计原稿上的图片颜色是RBG,而非CMYK。
服装数码印花中产生色差的因素以及解决方法39Technology 网印工业Screen Printing Industry2020.06工艺技术中暂停时间过长或者暂停的次数过于频繁,以上的操作都可能会导致画面不连续、图像输出有色差。
为了避免上述的情况发生,我们需要在打印前检查介质和墨水是否充分,发现问题,并及时进行补充。
需要注意,具备加热烘干装置的服装数码印花机,暂停时间过长时,在暂停前后打印的几PASS图像,色差有很大差异。
同一幅图,不同的机器或在不同的条件下完成打印(主要是对于需要拼接的大幅画面)即使是同一型号的不同服装数码印花机,其打印的效果(色差)都有不同的差别,打印完拼接后,在整体上就有色差。
布匹色差

布匹色差在线检测技术及应用前言预防和控制染色产品的色差, 并使其保持稳定, 一直是各印染企业和染整工作者所关注的重点。
尤其是随着制衣业工业化和连续化的高速发展, 人们对染色产品的色差提出了更高的标准和要求。
导致染色成品布产生色差的因素多且复杂, 要将色差严格控制在标准范围之内且使其长期保持稳定, 涉及到生产加工过程中的方方面面, 必须对各个要素和影响因素进行综合分析, 制定出相应的预防措施, 严格规范实施手段, 对染色织物的色差加以控制。
染色成品的色差一般分为: 原样色差、前后色差、左中右色差和正反面色差(俗称阴阳面) 四大类。
原样色差是指染色织物与客户来样或标准色卡样, 在色相、色光和色泽深度上存在的差异; 前后色差是指相同工艺先后染出的织物在色相、色光与深度上存在的差异; 左中右色差是指染色织物纬向左中右部分的色相、色光与色泽深度存在的差异; 正反面色差(阴阳面)是指平纹织物两面的色相与色泽深度存在的差异。
以下结合生产实践, 简要分析产生这四类色差的原因, 并提出预防和控制措施。
1 形成色差的主要因素1. 1 前处理随着印染生产加工技术的进步与发展, 前处理的处理能力、处理质量及处理效果对印染加工成品质量的影响越来越突出。
业内专家认为, 70% 左右的产品收稿日期: 2006 - 06- 19 质量应控制在前处理工序中。
在织物印染加工过程中, 前处理后的半成品所存在的疵病一般都具有一定的隐蔽性, 特别是对织物的内在质量指标有影响的疵病, 很难判断查明。
前处理中造成织物成品色差的影响因素主要有退浆除杂不匀、不净; 前后、左中右毛效不一致; 白度批差大; 丝光不匀透; 水洗效果差; 半成品布面碱性过大等。
1. 2半成品退浆除杂不匀、不净织物经过煮练、漂白工序后, 色素已被除去, 仅从织物布面很难发现其退浆及除杂不匀、不净的质量问题。
用这种半成品生产漂白和浅色品种, 容易产生泛黄、变色、色相不稳定(色萎、色暗)、艳度较差等问题; 此外还会影响织物的丝光和染色效果, 造成织物表面丝光和染色白芯等疵病。
- 1、下载文档前请自行甄别文档内容的完整性,平台不提供额外的编辑、内容补充、找答案等附加服务。
- 2、"仅部分预览"的文档,不可在线预览部分如存在完整性等问题,可反馈申请退款(可完整预览的文档不适用该条件!)。
- 3、如文档侵犯您的权益,请联系客服反馈,我们会尽快为您处理(人工客服工作时间:9:00-18:30)。
服装色差的识别成因与预防1.疵病特征:染色制品所得色泽深浅不一,色光有差别。
(1)同批色差:同批产品中.一个色号的产品箱与箱之间、件与件之间、包与包之间、匹与匹之间有色差。
(2)同匹色差:同匹产品中的左中有有色差或前后有色差或正反面有色差。
色差是染整厂常见疵病和多发性疵病之一,严重影响染色成品的质量。
2.产生原因各类织物的纤维组成不同,染色时采用的染料种类及工艺设备不同、加上染色加工中有不同的要求和特点,产生疵病的原因及表现就不一样。
色差在外观表现上多种多样,但究其原因,主要有以下几种。
(1)染料在织物上先期分布不均匀:染料在固着之前,如果在织物各部位上分布不匀,固色后必然形成色差。
造成这种现象的主要原因为:织物因素:由于纤维性能不同或前处理退、煮、漂、丝不够匀透,使染前半制品渗透性不匀而引起对染料吸收程度的差异。
吸液因素;由于机械结构上的原因或操作不当,使织物各部位的带液率不一致,因而造成色差。
轧辊压力不匀、加入染化料不匀等都会使织物吸收染料不匀。
预烘因素:在浸轧染液后预烘时,由于烘燥的速率和程度不一致,引起染料发生不同程度的泳移,使染料在织物上分布不匀。
(2)染料在织物上固着程度不同:尽管染料在织物上先期分布是均匀的,但在固着过程中.如条件控制不当(如温度、时间、染化料浓度等),使织物上某些部位的染料没有得到充分固色,在后处理皂洗时即被去除.从而产生色差。
例如,分散染料热溶温度两边或前后不一致、还原染料部分还原或氧化不充分、活性染料汽蒸条件不良等都会造成织物的前后或左右有色差。
(3)染料色光发生变异:这种差异不是由于织物上染料分布不均匀造成的.而是由于某些原因引起织物上的部分染料的色光发生变化,一般有以下几种原因:染前因素:半制品的白度不匀或pH 值有较大差异,在染色后往往造成色光差异。
染色因素:例如分散染料热溶温度过高,使某些染料的色光变得萎暗;还原染料的过度还原,也会使色光有差异。
染后因素:在后整理过程中.如树脂整理、高温拉幅以及织物上PH 值的不同等,都会引起染料色光有不同程度的变化。
皂洗:如皂洗不充分,会使发色不充足.色光不准。
实用服装跟单流程(精简版)一、前期跟单1、查阅订单资料服装接到订单资料后,仔细查看资料是否完整准确。
订单资料是跟单员跟进订单的唯一依据,只有完整的资料才能确保跟单的跟进工作。
核对分析资料的具体内容:a)资料是否完整b)文字描述是否与款式图一致c)确认面、辅料d)查看绣印花等其他设计要素e)了解客户特殊要求2、制作办单,查办,寄办。
跟单研究订单资料,制作出办单,列出所需的面辅料并配好,交给板房打纸样及做办,做好办后交洗水部洗水,洗回后交板房做后整及查验,技术部核查OK 后寄给客户批核。
同时根据办房报用料,整理出用料成本表一式二份,一份给香港跟单员,一份留底用于成本核算及订购物料作准备。
a)初办:目的是让客户确认服装的款式造型是否准确、设计风格是否一致,缝制工艺是否达到要求等。
生产办可以使用代用面料制作。
生产办的数量根据客户的需求而定。
b)大货办:是订单生产前客户最后一次确认的样衣,因此大货办制作的要求比较高,需要用订单中的面、辅料,要求制作的规格全色全码。
大货办得到客户的确认后才能进入大货的生产。
c)样办检验细则:主要检验样衣的面辅料材质和颜色、核对款式。
检验尺寸规格和包装等。
成品服装的各部分的规格范围必须符合客户的要求的公差范围,款式造型必须依照工艺文件中的款式图和款式描述来逐一核对,缝制工艺的检验。
3、定购大货面、辅料,报价、检验跟单依照客的定单数量及客提供的资料,计算清楚各物料的用量,并跟进客户直接提供的面,及物料尽快上厂。
香港供料时,跟单向香港方面索取价格,输进XXXX 系统;[没有使用系统的自己打单]除香港供料外,其他物料原则上由采购部统一采购,跟单员将详细资料交采购部门,由采购部门进行大货面辅料采购。
但某些物料由于货期紧等原因,将由跟单自己采购。
跟单自采购物料,选定、联系供应商,将价格输进系统,打出采购单,交给供应商,告知数量、交货期。
跟单将所有物料的价格输进系统,计算出总价,交组长及总经理批核,通过后,方可进行生产。
大货布料及物料回厂后,大货布由仓库验布员验布,提供验布报告,并需给一份给客。
跟单员根据验布报告进行跟进,同时剪疋头布和缩水布。
要洗水的要交由洗水部根据客要求去洗水。
回厂后由洗水部,分出LOT 色办交客批核(有些客是要求整个布封的疋头布,去批颜色的,并且要求洗前与洗后的,但有些是不用的,根据客人的要求来做,并且要留意布的正反面,中边色差,倒顺毛等等)然后根据做办的用料,初步计算该单的用布量,加裁或缩裁交客户确认,跟单员必须在大货生产前整理好制单资料和物料咭,在裁剪之前分发给相关部门。
物料管理控制:必须做一份物料跟进表,进行追踪。
每单物料回厂后,清楚地做好明细登记,并核查物料的规格,数量是否正确,要有处理物料质量和数量分配及物料差异,有物控的能力。
节约公司成本,并在大货物料发料前列出一份物料发放表,发给仓库及车间,以作为发料,用料参考,不足的物料,负责追补回,保证生产需要。
审批用料及通知开裁:核实大货物料是否跟报给客人的相同,计算用布量,是否够用.如在有多/少的情况下,问客人是否可缩裁/加裁.遇有绣/印花的,需整理好绣/印花样办,核对正确后,才可外发. 二、中期跟单客户批办OK 后,接下来生产大货,首先跟生产部排期,标准办样办返厂后,根据客人的评语,要求和样办,制作大货生产单,交技术部审查。
召集工厂管理人员、QC 以及客户QC 开产前会议。
核对工厂的生产工艺单是否与客户标准一致,核对的重点包括:面、辅料的材质、颜色是否正确;款式是否正确注意事项:生产过程中,将资料交QC,由QC 跟进生产质量监控跟进生产进度,及时做好客户要求与车间生产之间的协调和沟通,遇有客更改资料,需在第一时间传达到相关部门,并要保持资料的最新版本,做好签收记录。
能达到生产计划要求的情况,反映给上级部门,以督促解决,并了解和部门的生产实情,以求完成预定的任务,保证货期和质量.大货因客观问题需要延期,必需写出廷期原因及廷期后的交货期,与客户商讨,要求尽快回复,需客人出邮件/书面签回。
成品洗水时,必须要车间尽快做几件去洗水,以了解尺寸及洗水效果,同时给客人批核洗水颜色是否OK,确定接受后,方可洗大货。
当成品在总查后发现有太多次品需每件查看,如有轻微的次品挑出可给走货,严重的属于哪个部门的责任去追查该部门的当事人,通知生产厂长。
三、后期跟单核查包装办:大货包装前,核查包装的第一件包装办,确保物料齐备及包装方法正确后,方可进行包装,如有客要求要批核后再进行大货包装,就需提前包装一件样办给客去批办。
积极准备及配合客户初查,中查,尾查的查货,并且将客户查货信息反馈到各部门。
生产成品后按客要求挑船头办或收货办给客户,目的是让客户预先了解大货的生产情况和订单质量,样办的数量根据客人的要求而定。
并需走货前一星期做好商检资料交报关员做商检,商检需要什么资料,要问明报关员后提供。
客验货合格后,核实走货数量,整理装箱单及出货通知书,并向相关部门汇报可以安排出货。
资料整理及保存:出货后,整理并保存好有关的生产资料及标准样办,遇有次布及不合格的物料,整理好数据资料报客,以安排退回给客户,修正生产中的不足之处,以免翻单时不清楚。
注:很多问题都不是一成不变的,每个订单都有不同的做法,应根据实际的情况及客人要求来跟进。
一、首先跟单进入工作前需准备以下资料:1.颜色原样。
2.原手感样。
3.客人确认的小样(也就是工厂第一次打的色样)。
4.原品质样。
5.合同复印件(上面有对工厂的质量要求、标准、交期,数量等,跟单可参考)。
6.以及相关资料。
二、工厂打颜色小样:,跟单需做以下事情:1.按客供样(原色样)的颜色,要求工厂放小样,放小样必须有书面要求,也就是打色通知书,《打色通知书》的内容包括(对色光源、色牢度、染化料是否环保、打样版数、打样坯布及大小、打样坯布规格、完成时间)等。
2.打样坯布:打样坯布与大货一致,杜绝使用其它规格的坯布进行打样,针对大货生产特点,应考虑小样坯布是否进行砂洗或相关处理。
3.根据打样通知书,正确使用光源(如:D65、TL84、U3000 等)避免跳灯现象,提高打样准确率。
4.根据客人或市场部要求,《打样通知书》须注明小样大小和版数(印花和色织要注明循环问题,色织小样要附纱样,基本上化纤类染色布都是打A、B、C、D 四个样)。
5.时间要求:染色烧杯样3 天,印花样10 天,色织样10 天,特殊情况酌情解决处理。
6.文字说明:小样须贴在规定表格内(公司色样卡),根据打样通知书标明色号、色名、编号、送样日期等。
7.色样卡管理:妥善保管,防止腿色,编号放好,做到用的时候随时能找到。
三、中样或大货头缸样(也就是生产大货前的第一次生产试样):提供中样或大货头缸样(如品质样、手感样、样衣面料等)应同大货一致,在条件许可情况下,应尽量模仿大货生产工艺,对所使用的染化料、助剂以及工艺流程要有记录,特别是面料门幅,要按大货生产程序进行拉幅定型、拨水,对所提供的中样或头缸一定要要留样可查。
四、生产大货过程中:1.明确要求:明确订单合同的的各项要求,物别是内外质量的标准要求和交期。
2.制定生产计划:根据服装交期要求,制定面料生产计划以及分阶段的成品数量。
同时填写《面料组织生产进度表》每周或每次有新的变化要及时改动。
然后不定时间的向主管部门领导汇报。
以传真、邮件形式发给主管。
3.每道质量进行跟踪,主要注意:①是否在规定灯源下对色。
②小样、确认样或头缸样是否正确一致。
③色差控制:边中差、头尾色差、匹差、阴阳面色差、缸差等。
④经纬密、幅宽、色牢度、缩水率、手感、克重、气味等。
五、大货检验:4.检验标准和方式:按美国AATCC 国际标准,十分制与四分制检验方法或公司内部检验标准,而且须根据材料的用途进行不同的检验(比如:尼丝纺,有的客人是用作制雨伞的,这样就要求检验的时候一定要把底灯打开)。
5.在规定的光源下,以确认样为准,同时参考小样或原色样进行对色,色偏控制在4-5 级,不得低于4 级,如超标必须进行返修或投新坯重做。
3.外观质量:1.布面检验:重点检查污渍、纬斜、左中右色差、头尾色差、手感差、断经、断纬、经痕、油污、色花、粗纱、色污、并经并纬、胶条、胶痕、漏胶、胶粒等。
2.总体检验:幅宽(须量三次,头中尾)、克重(头尾)、经纬密、长度、色差、六、包装要求:根据不同的面料性质,可采用匹装或卷装或塑料袋或蛇皮便袋等包装。
而且唛头上一定要注明:款号、颜色、数量、缸号,色号,日期,订单号,卷号等。
七、测试样布3-5M带回公司进行相关物化性要求测试。
八、测试OK,方可发货(按公司程序要求发至相关工厂或本公司仓库)。