利用改进的遗传算法优化产品性能参数模型
基于改进多目标遗传算法的连铸二冷过程优化

基于改进多目标遗传算法的连铸二冷过程优化翟莹莹;厉英;敖志广【摘要】采用一种改进的多目标遗传算法对二冷工艺进行优化.改进的多目标遗传算法应用概率法选取选择算子,根据适应度值来动态计算交叉和变异概率,能够得到更好的全局最优解,提高算法精度和整体性能.在基于凝固传热模型的二冷优化过程中,采用变间距差分法离散求解传热方程,对比粒子群算法、多目标遗传算法,改进的多目标遗传算法搜索效率高,得到的价值函数最小.在实际生产中,采用优化后的二冷工艺,使得总用水量减少约10%,提高了铸坯质量,达到了节能降耗的要求.【期刊名称】《东北大学学报(自然科学版)》【年(卷),期】2019(040)005【总页数】5页(P658-662)【关键词】连铸;二冷工艺;凝固传热模型;多目标遗传算法;冶金准则【作者】翟莹莹;厉英;敖志广【作者单位】东北大学计算机科学与工程学院,辽宁沈阳 110169;东北大学冶金学院,辽宁沈阳 110819;东北大学计算机科学与工程学院,辽宁沈阳 110169【正文语种】中文【中图分类】T391.4连铸过程中,二次冷却工艺用于加速铸坯凝固进程,对出结晶器的带液芯的铸坯进行冷却,避免铸坯表面和内部产生缺陷,因此,合理控制各段水量是提高铸坯质量的重要因素.二次冷却工艺控制有静态和动态两种方式,目前,动态控制方式多处于理论研究阶段.国内外连铸生产中仍普遍采用静态控制方法.静态控制模式易于实现,在其他工艺参数变化不大,拉速较平稳时可以保证铸坯质量.连铸二冷过程优化既要使各段水量合理分配,又要使得铸坯凝固过程中的温度梯度和前沿速度在一定区间内,是典型的多目标优化问题.基于二维传热模型,应用冶金准则函数与先进的优化策略相结合的方法[1-2],建立稳定的二冷工艺优化模型能够提高连铸坯的质量.在优化模型中,需要分析数值求解传热模型的计算量,及基于冶金准则的价值函数的复杂性等问题,而传统的优化方法[3]求解该非线性优化问题的效率较低.为了合理控制工艺,提高铸坯质量,国内外学者做了大量研究工作,基于智能优化算法提出了多种二冷控制模式[4-8],如多目标优化[4]、粒子群算法[5]、遗传算法[7]等.但在优化过程中仍然存在很多问题,如基于凝固传热模型的求解优化过程中的收敛速度慢、搜索能力弱、优化时间长等.为了提高算法的收敛速度和局部搜索能力,本文提出一种基于改进的多目标遗传算法的二冷多目标优化方法,在建立铸坯凝固传热仿真模型的基础上,应用改进的多目标遗传算法,提高算法收敛精度,获取全局最优解,得到连铸二冷工艺的最优方案,使得铸坯均匀冷却,提高铸坯质量.1 多目标遗传算法及改进遗传算法是基于模拟生物进化过程与机制求解的自组织和自适应的人工智能技术,是一种从种群到种群的全局随机搜索和优化方法,广泛应用于多目标优化问题的求解.1.1 基本多目标遗传算法应用多目标遗传算法(MOGA)[9]求解,首先要找到Pareto最优解的评价方法,然后设计不同的选择、交叉和变异算子.在多目标算法优化设计过程中,利用优化关系,既可以独立地对每个子目标函数进行选择,也可以各个子目标函数进行个体选择.对于实际的多目标优化问题,如何选择算法,主要取决于决策者对问题的分析及算法的偏好.多目标遗传算法求解优化问题的步骤如下:步骤1 确定个体表现型及解空间,即决策变量和约束条件;步骤2 描述问题的数学形式及最终目标函数,构建优化模型;步骤3 确定个体表现型转换成基因型的编码方法及可行解的搜索空间;步骤4 确定个体基因型转换成表现型的解码方法;步骤5 确定适应度函数,明确目标函数与个体之间的映射规则;步骤6 设计选择、交叉、变异等算子的实现方法及遗传算法的运行参数.该算法在进化初期,能够保留适应度较好的个体,淘汰了种群中的其他个体,加快了种群的收敛速度.但是,在进化后期,种群中的个体处于停滞状态,很难收敛到全局最优解,易产生算法早熟收敛.1.2 改进的多目标遗传算法为了提高遗传算法的性能,克服求解问题中的困难,改善算法的早熟收敛性,本文提出了一种改进的多目标遗传算法(IMOGA),首先,为了降低算子的局部收敛性,本文采用概率法对选择算子进行筛选,在下一代中保留适应度较大的个体.具体步骤如下:步骤1 个体在下一代中的生存期望fiti根据群体中的个体适应度值来计算:(1)步骤2 计算个体的生存期望值Ni,取其整数部分[Ni]作为下一代的生存数目.步骤3 下一代个体的适应度值为(2)用基本比例法随机确定下一代中余下的个体.进一步地,根据适应度值来动态调整交叉概率、变异概率和基于概率法进行选择算子的选取.该方法降低了局部收敛性,提高全局搜索能力.交叉和变异概率公式为(3)(4)其中:fmax是种群的最大适应度值;favg是每代种群的平均适应度值;f′是交叉操作的两个个体中较大的适应度值;f是变异个体的适应度值;Pc3<Pc2<Pc1∈(0,1);Pm3<Pm2<Pm1∈(0,1).Pc和Pm随f呈阶段性线性变化,并且Pc和Pm在fmax的个体处均不为零,提高种群中优秀个体的Pc和Pm,使得这些个体一直处于运算过程中,算法不会局限于局部解,克服早熟收敛,从而得到全局最优解.2 连铸二冷工艺优化建模2.1 连铸坯凝固传热模型连铸凝固传热模型采用内热源的非稳态方程描述,根据不同的初始边界条件模拟铸坯的凝固过程,用于实际生产中的工艺参数优化.本文采用有限差分法求解凝固传热模型,得到铸坯的温度场分布、坯壳厚度及液芯长度等数据.1) 凝固传热建模.为了描述凝固传热模型,对具体的连铸过程进行假设:沿拉坯方向上铸坯的温度不随时间变化;忽略凝固冷却收缩引起的铸坯尺寸变化;在液相区中,采用增大导热系数法把对流传热等效成传导传热;忽略辊子的接触传热.采用薄片移动法,根据铸坯表面在不同冷却段的换热条件,建立热流与时间的函数关系,其中xy方向为铸坯的横截面;连铸过程的二维凝固传热控制方程:(5)其中:T为铸坯温度,K;ρ为密度,kg/m3;c为等效热容,J/(kg·℃);λ为导热系数,W/(m·℃);Q为内热源项.采用增大对流系数[10]的方式来处理二冷区不同传热方式带走的热量.对流传热方程:q=h(ts-ta)+σε[(ts+273)4-(ta+273)4].(6)其中:h为综合对流换热系数,W/(m2·℃);ts为铸坯表面温度,℃;ta为室温,℃;σ为斯蒂芬-玻耳兹曼常数,值为5.67×10-8W/(m2·K4);ε为铸坯表面黑度系数,值为0.8. 二冷区综合对流换热系数:h=[1 570W0.55(1-0.007 5tw)]/C.(7)其中:tw为二冷水温度,℃;W为水流密度,L/(m2s);C为常量,在不同的连铸过程中取值不同.2) 离散方法.凝固传热模型采用薄片移动法模拟,在空间上采用变间距有限差分法进行离散化处理,在时间上采用向后差分进行处理.为了保证差分计算精度和收敛性,采用变间距网格划分,圆坯横截面划分为外环部分和内环部分,在内外环划分大小不同的切向角网格,其交界位置可任意选择,在温度变化较大的外环区域,网格稠密,在温度较为平缓的内环区域,网格稀疏.2.2 基于冶金准则的多目标优化模型连铸坯在冷却过程中,水量分配不均,导致铸坯产生裂纹、疏松等缺陷.在二冷过程中应考虑冷却强度、水量分配、喷雾区的划分以及喷嘴的布置形式等冶金准则.基于传热模型,采用多目标遗传算法迭代计算各二冷段的传热系数,使价值函数的值最小,得到满足冶金准则的二冷区的工艺参数.1) 表面目标温度.根据钢的高温力学性能、冶金准则及生产工艺要求确定的铸坯表面目标温度tM,i,计算得到的表面温度tb,i应该充分接近目标温度,该函数尽量取最小值.f1,i(Qi)=(tM,i-tb,i)2.(8)2) 冷却水量消耗.从节能减排的角度考虑,整个二冷区的总冷却水量越少越好.即表示任一冷却段,n为总的冷却段数,该函数应取最小值,优化过程中,各个段的水量取为相应的目标水量:f2,i(Qi)=Qi.(9)3) 冶金长度限制.考虑到生产安全及连铸坯质量,液芯长度应该限制在某一区间内.为了减少应力作用下铸坯凝固前沿产生的裂纹,液芯LM在矫直点Ld之前完全凝固. f3,i(Qi)=(Max(0,LM-Ld))2.(10)4) 表面温度的最大冷却速度和回升速率限制.铸坯表面温度回升使得凝固前沿产生巨大的应力,铸坯内部易产生裂纹;铸坯沿拉坯方向的表面回温速率上限值Cp(℃·m)和冷却率上限为Cn(℃·m),表面回温速率和最大冷却速率满足限制条件:(11)(12)5) 其他约束性条件.矫直区温度应避开脆性温度区间,可以减少横裂纹的产生,脆性温度取值范围700 ℃<tBmin<900 ℃;铸坯鼓肚时,沿铸坯凝固前沿产生拉应力,使得凝固前沿发生断裂或者偏析.通常铸坯表面温度tBmax<1 100 ℃,即温度脆性区间温度取值范围为tBmax>ti,τ>tBmin,拉速根据实际生产状况,限定范围vmax>v貌一新i>vmin.由于以上各约束条件的单位不同,数量差异很大,为此需要将上述目标函数进行归一化处理fk,i∈[0,1],k=1,2,…,5.由于上述不同的约束条件对铸坯质量的影响程度不同,为此,选定不同加权系数对多目标价值函数进行评价:(13)其优化策略是通过寻找主控向量Q=[Q1,…,Qn]T(n为二冷区的分段个数),得到价值函数的最小值.3 现场应用及结果分析为了测试应用改进的多目标遗传算法的二冷优化模型的精确性,对石油套管钢26CrMoVTiB圆坯的二冷工艺进行优化分析.根据现场实际工艺条件,连铸机的主要设备参数为:圆坯直径为178 mm;结晶器长度0.9 m,足辊段长度为0.35 m,水雾冷却区分四段,长度分别为1.55,1.4,2.9,3.5 m,辐射区长度为5 m.浇注过程中拉速为1.9 m/min;浇铸温度为1 554 ℃;液相线温度为1 508 ℃,固相线温度为1 420 ℃;结晶器水流量为1 700 L/min,冷却水温差6.5 ℃.26CrMoVTiB的物性参数为:比热容为830 J/(kg·K);液态钢密度为ρl=6.9×103kg/m3, 固态钢密度ρs=7.5×103kg/m3;导热系数液态为kl=31.2 W/(m·K),固态为ks=37.4 W/(m·K).在传热模型及其他工艺条件相同的情况下,使用多目标遗传算法(MOGA)、粒子群算法(PSO)和改进的多目标遗传算法(IMOGA)对二冷工艺进行优化,其迭代搜索的优化过程如图1所示.IMOGA比其他两种算法的收敛效果更好,在经过35次迭代后,价值函数的取值最低,寻优效果最好.图1 二冷配水优化搜索过程的寻优曲线Fig.1 Optimization curve of water distribution in secondary cooling zone表1为优化前后二冷配水量对比.由表1可知,优化后的总用水量较优化前节省了10%左右,二冷各段的水量均有不同程度的降低,沿拉坯方向水量逐渐减少,减少铸坯应力的产生,不易产生内裂纹.表1 优化前后二冷配水量对比Table 1 Compare water distribution of secondary cooling scheme L/min二冷各段拉速 1.9m/min拉速2.1m/min拉速2.3m/min优化前优化后优化前优化前优化后优化前足辊段30.928.13431.162.259.31段45.941.147.544.268.466.32段28.925.527.325.739.337.93段20.718.522.719.337.236.94段16.815.917.715.629.127.6总水量143.2129.1149.2135.9236.2228.026CrMoVTiB钢优化前后的表面温度和液芯温度及坯壳厚度分布如图2所示.优化后26CrMoVTiB钢铸坯表面温度在结晶器出口处温度高于900 ℃,避开了低塑性区,不易在弯曲段出现裂纹;二冷区的铸坯表面温度低于1 100 ℃,符合防止铸坯鼓肚的要求;铸坯表面温度的回温速率低于100 ℃/m,表面温度降温速率小于200 ℃/m,温度变化平缓,有效地防止铸坯表面裂纹生成.二冷区三段、四段的铸坯表面温度波动幅度较小,均在奥氏体化温度以上,减小铸坯内的热应力及相变引起的组织应力,防止内裂纹的产生.图2 优化前后铸坯温度对比Fig.2 Comparison temperature distribution before and after optimization在实际生产中,分别抽取优化前和优化后的铸坯40块,铸坯质量缺陷等级分布如图3所示.水量优化后,温度变化更加平缓,温度梯度变小,铸坯质量较优化前提高较大.其中,中心疏松小于1.0级由49.45%上升到85.26%,中心缩孔小于1.0级由68.13%上升到80.17%,中心裂纹低于0.5级由44.84%上升到70.01%,且平均等轴晶率由28.42%上升到42.13%.二冷工艺优化后,铸坯低倍评级得到明显改善.图3 铸坯质量缺陷等级分布Fig.3 Grade distribution of various defects4 结论1) 本文提出了一种改进的多目标遗传算法,增强了全局搜索能力,避免过早陷入局部最优,解决了不可微、非线性优化问题,提高了算法的收敛精度.2) 采用改进的多目标遗传算法,优化连铸二冷工艺,其价值函数比改进前低0.1,比粒子群算法低0.05,得到了更优的全局解.3) 优化后的二冷工艺应用于生产实际中,铸坯表面温度和温度梯度趋势平缓,减少铸坯缺陷,二冷总用水量减少了约10%,既达到节能降耗的要求,又提高铸坯质量.参考文献:【相关文献】[1]Santos C A,Spim J A,Garcia A.Mathematical modeling and optimization strategies applied to the continuous casting of steel [J].Engineering Applications of Artificial Intelligence,2003,16(5/6):511-527.[2]Cheung N,Garcia A.The use of a heuristic search technique for the optimization of quality of steel billets produced by continuous casting [J].Engineering Applications of Artificial Intelligence, 2001,14(2):229-238.[3]Lotov A V,Kamenev G K,Berezkin V E,et al.Optimal control of cooling process in continuous casting of steel using a visualization-based multi-criteria approach [J].Applied Mathmatical Modeling,2005,29(7):653-672.[4]Imran M,Pambudi N,Farooq M.Thermal and hydraulic optimization of plate heat exchanger using multi objective genetic algorithm [J].Case Studies in Thermal Engineering,2017,10(9):570-578.[5]纪振平,马交成,谢植,等.基于混沌蚁群算法的连铸二冷参数多准则优化[J].东北大学学报(自然科学版),2008,29(6):782-785.(Ji Zhen-ping Ma Jiao-cheng,Xie Zhi,et al.Multi-criteria optimization based on chaos ant colony algorithm for secondary cooling parameters in continuous casting [J].Journal of Northeastern University(Natural Science),2008,29(6):782-785.)[6]Chakraborti N,Gupta R S P.Optimization of continuous casting process using genetic algorithms:studies of spray and radiation cooling regions [J].Ironmaking and Steelmaking,2003,30(4):273-278.[7]Zhai Y Y,Li Y,Ma B Y,et al.The optimisation of the secondary cooling water distributionwith improved genetic algorithm in continuous casting of steels [J].Materials Research Innovations,2015,19(1):26-31.[8]Wang X D,Wang Z F,Liu Y,et al.A particle swarm approach for optimization of secondary cooling process in slab continuous casting [J].International Journal of Heat and Mass Transfer,2016,93(1):250-256.[9]Fonseca C M,Fleming P J.Genetic algorithms for multiobjectiveoptimization:formulation,discussion and generalization [C]//Proceedings of the Fifth International Conference on Genetic Algorithms.San Mateo,1993:416-423.[10]Mosayebidorcheh S,Gorji-Bandpy M.Local and averaged-area analysis of steel slab heat transfer and phase change in continuous casting process [J].Applied Thermal Engineering,2017,118:724-733.。
基于改进双种群遗传算法的装配线平衡优化研究
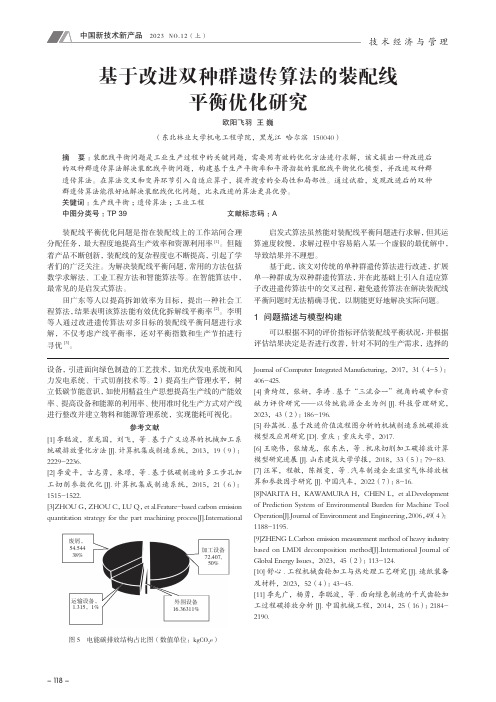
- 118 -设备,引进面向绿色制造的工艺技术,如光伏发电系统和风力发电系统、干式切削技术等。
2)提高生产管理水平,树立低碳节能意识,如使用精益生产思想提高生产线的产能效率、提高设备和能源的利用率、使用准时化生产方式对产线进行整改并建立物料和能源管理系统,实现能耗可视化。
参考文献[1]李聪波,崔龙国,刘飞,等.基于广义边界的机械加工系统碳排放量化方法[J].计算机集成制造系统,2013,19(9):2229-2236.[2]李爱平,古志勇,朱璟,等.基于低碳制造的多工步孔加工切削参数优化[J].计算机集成制造系统,2015,21(6):1515-1522.[3]ZHOU G,ZHOU C,LU Q,et al.Feature-based carbon emission quantitation strategy for the part machining process[J].InternationalJournal of Computer Integrated Manufacturing,2017,31(4-5):406-425.[4]黄绮煜,张妍,李涛.基于“三流合一”视角的碳中和贡献力评价研究——以传统能源企业为例[J].科技管理研究,2023,43(2):186-196.[5]孙菡悦.基于改进价值流程图分析的机械制造系统碳排放模型及应用研究[D].重庆:重庆大学,2017.[6]王晓伟,张绪龙,张东杰,等.机床切削加工碳排放计算模型研究进展[J].山东建筑大学学报,2018,33(5):79-83.[7]汪军,程敏,陈颖雯,等.汽车制造企业温室气体排放核算和参数因子研究[J].中国汽车,2022(7):8-16.[8]NARITA H,KAWAMURA H,CHEN L,et al.Development of Prediction System of Environmental Burden for Machine Tool Operation[J].Journal of Environment and Engineering,2006,49(4):1188-1195.[9]ZHENG L.Carbon emission measurement method of heavy industry based on LMDI decomposition method[J].International Journal of Global Energy Issues,2023,45(2):113-124.[10]舒心.工程机械齿轮加工与热处理工艺研究[J].造纸装备及材料,2023,52(4):43-45.[11]李先广,杨勇,李聪波,等.面向绿色制造的干式齿轮加工过程碳排放分析[J].中国机械工程,2014,25(16):2184-2190.图5 电能碳排放结构占比图(数值单位:kgCO 2e)废屑,54.544 38%外围设备 16.36311%运输设备,1.315,1%装配线平衡优化问题是指在装配线上的工作站间合理分配任务,最大程度地提高生产效率和资源利用率[1]。
遗传算法与模型预测控制的结合研究综述

遗传算法与模型预测控制的结合研究综述引言在现代科学和工程领域中,模型预测控制(Model Predictive Control, MPC)作为一种强大的控制方法,已经得到了广泛的应用。
然而,MPC的设计和优化过程往往是复杂且耗时的。
为了解决这一问题,研究人员开始探索将遗传算法(Genetic Algorithm, GA)与MPC相结合的方法,以提高控制系统的性能。
本文将对遗传算法与模型预测控制的结合研究进行综述。
遗传算法的基本原理遗传算法是一种模拟自然遗传和进化过程的优化算法。
它通过模拟自然选择、交叉和变异等过程,来搜索问题的最优解。
遗传算法的基本原理包括个体编码、适应度评价、选择、交叉和变异等步骤。
个体编码是将问题的解表示为一个染色体,适应度评价是根据问题的目标函数来评估染色体的优劣,选择是根据适应度值选择优秀的个体,交叉是将两个个体的染色体进行交换,变异是对染色体进行随机改变。
遗传算法在模型预测控制中的应用遗传算法在模型预测控制中的应用主要包括参数优化和约束处理两个方面。
参数优化是指通过遗传算法来寻找最优的控制参数,以使系统的性能指标达到最佳。
约束处理是指通过遗传算法来处理系统约束条件,以确保控制系统的稳定性和安全性。
在参数优化方面,研究人员通常将MPC的控制参数作为染色体的编码,以目标函数的最小化为优化目标,通过遗传算法来搜索最优的控制参数。
例如,某些研究将MPC的预测模型参数和控制权重作为染色体的编码,通过遗传算法来优化这些参数,以使系统的性能指标如稳定性、响应速度等达到最佳。
在约束处理方面,遗传算法可以用于处理MPC中的约束条件,例如状态变量的上下限、输入变量的变化率限制等。
通过将约束条件转化为适应度函数,遗传算法可以搜索满足约束条件的最优解。
一些研究还将遗传算法与其他优化方法相结合,以提高约束处理的效果。
结合研究的案例分析为了更好地理解遗传算法与模型预测控制的结合,我们将对一些相关的案例进行分析。
遗传算法优化模型训练过程及结果预测准确度比较

遗传算法优化模型训练过程及结果预测准确度比较遗传算法是一种模仿自然进化原理的优化算法,广泛应用于解决复杂的优化问题。
在机器学习领域,遗传算法也可以用于优化模型的训练过程,以提高模型的预测准确度。
本文将探讨遗传算法优化模型训练过程及结果预测准确度的比较。
首先,我们需要了解遗传算法的基本原理和步骤。
遗传算法通常包括初始化种群、选择、交叉、变异和替换等步骤。
在初始化种群阶段,通过随机生成一些初始解来构建一个初始的种群。
接下来,通过选择操作,根据某种适应度函数评估每个个体的适应度,并选择一部分适应度较高的个体作为父代。
然后,通过交叉操作,将父代个体的染色体信息进行随机组合生成新的个体。
最后,通过变异操作,在新个体的染色体上引入随机突变来提供种群的多样性。
重复上述步骤,直到达到终止条件。
在模型训练过程中,遗传算法可以用于优化模型的参数。
传统的机器学习算法通常使用梯度下降等优化方法来调整模型的参数,但这些方法对于复杂的模型和优化问题可能面临局部最优和收敛速度慢的困境。
遗传算法因其全局搜索和并行计算的特点,可以在一定程度上避免这些问题。
与传统的优化方法相比,遗传算法对初始解的选择更加灵活。
由于遗传算法具有较好的全局搜索能力,能够通过随机生成初始解的方式来探索更广阔的参数空间。
这对于模型的参数选择来说是非常重要的,因为良好的初始化可以使模型更快地收敛。
此外,遗传算法通过选择、交叉和变异等操作保持种群的多样性,以防止陷入局部最优解。
这种多样性维护使遗传算法更有可能找到更优的模型参数组合,并具有更好的泛化能力。
在优化模型训练过程时,我们可以将遗传算法与其他优化方法进行比较。
一种常用的方法是使用梯度下降法或其他传统的优化算法进行模型的参数调整,然后使用遗传算法对其进行进一步优化。
这种混合的优化策略可以充分利用遗传算法的全局搜索能力,并在较短的时间内获得更好的结果。
另一种方法是直接使用遗传算法进行模型的参数调整。
在这种情况下,我们可以通过比较使用遗传算法与传统优化方法得到的模型参数组合以及模型的预测准确度来评估遗传算法的效果。
基于改进遗传算法多体模型的汽车悬架参数优化

摘 要 :针对遗传算法普遍存在的概率参数主观选取问题、早熟问题以 及汽车悬架优化模型采用集中质量模型问题,提出了改进遗
传 算法 ,采 用 交叉 算子 和变 异算 子 分别 独立 作用 于父 代 个体 ,使 父代 所有 个 体都 进行 交叉 和 变异 来避 免概 率参 数 的选 取 问题 ;然 后按 父 子 混合杰 出者选 择策 略产 生子 代个 体 :使用 局 部多 次搜 索算 子和 替换 策略 来加 快遗 传算 法 的收敛 速度 :建立 遗传 算法 和 AD AMS软
维普资讯
第 2 卷第 3 6 期
、0 .6 ,1 2 No. 3
辽 宁工程技术大学学报
J ur a fLio n e h i a i e st o n lo a ni g T c n c lUn v riy
20 0 7年 6月
J n. u 2 7 00
He e Unv ri f n iern , n a 5 0 8 ia b i ie s yo gn i g Ha d n0 6 3 , n ) t E Ch
Abs r t Th p p r pr s n s al i r ve g n tc l ort m f r t r m erc p mi a on of mu tbo y t ac : e a e e e t l mp o d e e i ag i h o he pa a ti o t z t li d i i m o e — s d v h c es pe so I h sme o a n w og a s h me o e e i g rt msi e eo d Usn d lba e e i l us n i n. n t i t d, e pr r m c e fg n tca o h h l i sd v l pe . i g h sg n t orh t i e e c a g it m , r s v ra i l no c os o e nd mutto r t sa e ne d d. t rofs ing c mb n d lts c e d ai n ae r e e Fahe - fpr o i e ei ts h me a i n
基于改进遗传算法的计算机网络可靠性优化设计

计算机诞生之初,还不是计算机网络,只作为单机 工作。随着互联网普及到现在已经过了很久,而人们现在 所用的所有通信程序也无疑都是通过互联网来完成的 [1]。 ARPANET( 阿帕网 ) 是中国的主要互联网网络之一,它 也是因特网的创始人。ARPANET 是最先使用数据包交 换技术的计算机之一,利用包交换技术进行通信时的资 料都会被格式化成含有目标计算机地址的数据包,然后 再发送到互联网上供下一个目标计算机接受 [2]。数据包 一词是由 Donald Davies 于 1965 年创建的,用来形容经 过网络而在计算机系统内部传送的数据,因为数据包在 计算机网络中的地位至关重要,所以可以说数据包是整 个网络的主要主人公。在 1969 年,加州大学洛杉矶分校 (UCLA) 的教授 Steve Crocker 发布了第一个 RFC 论文, 这也被看作是现代网络的开始 [3]。同时,中国第一个网 络交换机也完成了在 ARPANET 上的首次传输,这也标
收稿日期 :2023-02-20 作者简介 :李继康(1982—),男,广西防城港人,本科,讲师,研究方向 :计算机多媒体技术、网络技术。
遗传算法参数的动态优化方案
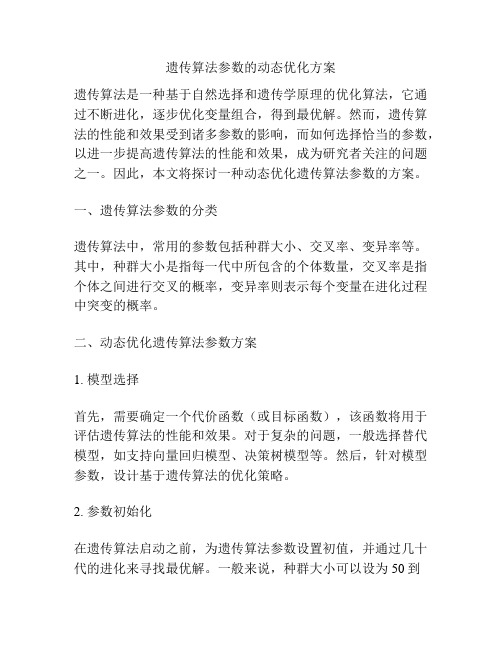
遗传算法参数的动态优化方案遗传算法是一种基于自然选择和遗传学原理的优化算法,它通过不断进化,逐步优化变量组合,得到最优解。
然而,遗传算法的性能和效果受到诸多参数的影响,而如何选择恰当的参数,以进一步提高遗传算法的性能和效果,成为研究者关注的问题之一。
因此,本文将探讨一种动态优化遗传算法参数的方案。
一、遗传算法参数的分类遗传算法中,常用的参数包括种群大小、交叉率、变异率等。
其中,种群大小是指每一代中所包含的个体数量,交叉率是指个体之间进行交叉的概率,变异率则表示每个变量在进化过程中突变的概率。
二、动态优化遗传算法参数方案1. 模型选择首先,需要确定一个代价函数(或目标函数),该函数将用于评估遗传算法的性能和效果。
对于复杂的问题,一般选择替代模型,如支持向量回归模型、决策树模型等。
然后,针对模型参数,设计基于遗传算法的优化策略。
2. 参数初始化在遗传算法启动之前,为遗传算法参数设置初值,并通过几十代的进化来寻找最优解。
一般来说,种群大小可以设为50到100左右,交叉率可以设为0.8到0.9,变异率可以设为0.005到0.01。
然后,将初值作为代价函数或目标函数的输入,以检验初值选择是否合理。
3. 优化策略基于上述的初值,开始进行动态优化遗传算法参数。
具体而言,在每次进化时,根据当前进化代数和遗传算法性能的变化情况,实时调整遗传算法参数。
如在前几代时,可以采用较小的交叉率和变异率,以保持种群多样性。
当进化代数较大时,应考虑加大交叉率和变异率,以加速收敛并求得最优解。
4. 优化终止当遗传算法达到预定的停止条件时,不再进行进化。
一般而言,停止条件包括代数足够、收敛到最优解等。
此时,通过对遗传算法参数的调整,得到优化后的遗传算法模型参数,以获取进一步的性能提升。
三、优化效果分析本方案将基于实验数据来验证其优化效果。
取50个连续函数优化问题和10个离散函数优化问题,分别采用传统的遗传算法(未设置动态优化参数)和本文所提出的动态优化方案进行比较。
基于机器学习与遗传算法的注塑产品工艺参数优化

基于机器学习与遗传算法的注塑产品工艺参数优化
龚川;项薇;陈昱
【期刊名称】《机械制造》
【年(卷),期】2024(62)5
【摘要】注塑成型工艺可以高效成型高精度产品,被广泛使用。
通过优化注塑产品工艺参数,可以获得更高的表面质量和尺寸精度。
为了获得最佳工艺参数组合,设计了基于关键工艺参数组合的极端梯度提升决策树模型。
为了解决训练数据不平衡问题,引入尺寸加权修正方法,提高对不合格产品尺寸的预测精度。
使用遗传算法对改进极端梯度提升决策树模型以产品尺寸误差最小为目标进行全局寻优,得到最佳工艺参数组合。
最佳工艺参数组合为模腔压力39.4 bar、切换压力33.8 bar、射嘴压力49.4 bar、回水温度72.6℃、模温机水流量58.7 cm^(3)/s。
【总页数】6页(P60-65)
【作者】龚川;项薇;陈昱
【作者单位】宁波大学机械工程与力学学院;浙江省零件轧制成形技术研究重点实验室;宁波大学先进储能技术与装备研究院
【正文语种】中文
【中图分类】TH162
【相关文献】
1.基于高斯过程机器学习的注塑过程建模及工艺参数优化设计
2.基于遗传算法的汽车复杂注塑件成形工艺参数优化
3.基于遗传算法的注塑成型工艺参数优化
4.基于
遗传算法的注塑成型工艺参数优化研究5.基于遗传算法和神经网络的注塑工艺参数优化
因版权原因,仅展示原文概要,查看原文内容请购买。
- 1、下载文档前请自行甄别文档内容的完整性,平台不提供额外的编辑、内容补充、找答案等附加服务。
- 2、"仅部分预览"的文档,不可在线预览部分如存在完整性等问题,可反馈申请退款(可完整预览的文档不适用该条件!)。
- 3、如文档侵犯您的权益,请联系客服反馈,我们会尽快为您处理(人工客服工作时间:9:00-18:30)。
硌 华 郡 力 新
( 华 侨 大学信 息科 学与 工程 学院 , 福建 厦门 3 6 1 0 2 1 )
摘
要 :借鉴 机械 优化设 计 的思想 。 以总费用 为 目标 函数 、 以零 件参 数 ( 标 定 值 和容 差 等级 ) 为 自变 量 , 建立 产 品性 能参 数 模 型 , 并提
a l g o r i t hm i s p r o p o s e d .I n t h i s a l g o it r h m ,t h e mut a t i o n pr o b a b i l i t y c h a n g i n g f o l l o ws t h e v a ia r t i o n o f n u mb e r s o f i t e r a t i o n s ,t he a d a p t i v e c r o s s o v e r
p r o b a b i l i t y,a s we l l a s t h e e l i t i s t s e l e c t i o n s t r a t e g y c o mb i n i n g r o u l e t t e wh e e l a l g o it r h m a r e a do p t e d. T h e s i mu l a t i o n e x pe ime r n t s v e if r y t h a t t h e i mp r o v e d g e n e t i c a l g o r i t h m i s b e t t e r t h a n t he s i mpl e g e n e t i c a l g o it r h m u p o n c o n v e r g e n c e s p e e d a nd s e a r c h i n g c a p a bi l i t y, a n d e fe c t i v e l y a v o i d l o c a l o p t i mi z a t i o n;i t i s a n e x c e l l e n t me t h o d f o r l a r g e — s c a l e p ra a me t e r o p t i mi z a t i o n. Ke y wo r d s: P a r a me t e r mo d e l Op t i ma l d e s i g n Ge n e t i c a l g o it r h m Cr o s s o v e r p r o b a b i l i t y Mu t a t i o n p r o b a bi l i t y No n l i ne r a pr o g r a mmi n g
出 了一种 改进 的遗 传算 法 。该 算法 运用 了随 迭代 次数 变化 的变 异概 率 、 自适 应 变化 的交 叉概 率 以及结 合 赌 轮算 法 的精 英 选 择策 略 。 仿真 试验 证 明 , 改进 的遗 传算 法不但 在 收敛 速度 和搜索 能力 上优 于 简单 的遗传 算法 , 而且 能够 较好 地 避免 局部 最 优 , 是较 好 的大 规模 参数 寻优 方法 。 关键 词 :参 数模 型 优化 设计 遗 传算 法 交叉 概率 变 异概 率 非 线性 规划
中 图分类 号 :T P 3 9 9
文献 标 志码 :A
A b s t r a c t :L e a r n f r o m t h e d e s i g n c o n c e p t o f m e c h a n i c l a o p t i m a l , w i t h t h e t o t a l c o s t a s t h e o b j e c t f u n c t i o n , a n d t h e p a r t p a r a m e t e r s( s c a l i n g
v a l u e s a n d t o l e r a n c e l e v e l s )a s i n d e p e n d e n t v a i r a b l e s , t h e p a r a me t e r mo d e l o f he t p r o d u c t p e f r o r ma n c e i s e s t a b l i s h e d 。a n d t h e i mp r o v e d g e n e t i c
利用改进的遗传算法优化进 的遗传算法优化产 品性 能参数模 型
Op t i mi z i n g t h e Pa r a me t e r Mo d e l o f P r o du c t P er f or ma n c e B a s e d o n I mp r o v e d Ge n e t i c Al g o r i t h m
0 引言
标志工业产 品性 能的参数 主要 取决 于零件的定值 与容差 。进行零件参 数 的设 计 . 就 是要 确定其 标定 值 和容差 。将零件组装成产 品时 , 若产 品参 数偏离 预先 设定的 目标值 , 就会 造成质 量损 失 , 偏 离越大 , 损失 越 大; 零件 的容差大小则决定 了制造成本 , 容差设计得 越 小, 成本越高 。正确有效地设计零件 的最优化参数 , 是