MLCC失效分析全面案例课件
MLCC质量控制与失效分析
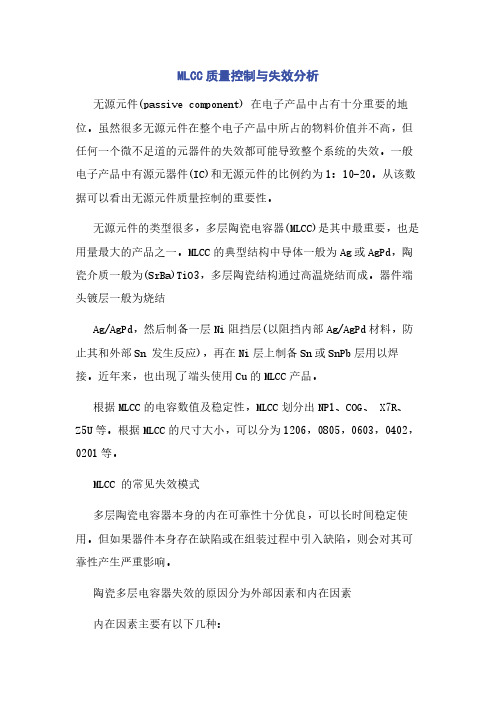
MLCC质量控制与失效分析无源元件(passive component)在电子产品中占有十分重要的地位。
虽然很多无源元件在整个电子产品中所占的物料价值并不高,但任何一个微不足道的元器件的失效都可能导致整个系统的失效。
一般电子产品中有源元器件(IC)和无源元件的比例约为1:10-20。
从该数据可以看出无源元件质量控制的重要性。
无源元件的类型很多,多层陶瓷电容器(MLCC)是其中最重要,也是用量最大的产品之一。
MLCC的典型结构中导体一般为Ag或AgPd,陶瓷介质一般为(SrBa)TiO3,多层陶瓷结构通过高温烧结而成。
器件端头镀层一般为烧结Ag/AgPd,然后制备一层Ni阻挡层(以阻挡内部Ag/AgPd材料,防止其和外部Sn发生反应),再在Ni层上制备Sn或SnPb层用以焊接。
近年来,也出现了端头使用Cu的MLCC产品。
根据MLCC的电容数值及稳定性,MLCC划分出NP1、COG、X7R、Z5U等。
根据MLCC的尺寸大小,可以分为1206,0805,0603,0402,0201等。
MLCC的常见失效模式多层陶瓷电容器本身的内在可靠性十分优良,可以长时间稳定使用。
但如果器件本身存在缺陷或在组装过程中引入缺陷,则会对其可靠性产生严重影响。
陶瓷多层电容器失效的原因分为外部因素和内在因素内在因素主要有以下几种:1.陶瓷介质内空洞(Voids)导致空洞产生的主要因素为陶瓷粉料内的有机或无机污染,烧结过程控制不当等。
空洞的产生极易导致漏电,而漏电又导致器件内部局部发热,进一步降低陶瓷介质的绝缘性能从而导致漏电增加。
该过程循环发生,不断恶化,严重时导致多层陶瓷电容器开裂、爆炸,甚至燃烧等严重后果。
2.烧结裂纹(firing crack)烧结裂纹常起源于一端电极,沿垂直方向扩展。
主要原因与烧结过程中的冷却速度有关,裂纹和危害与空洞相仿。
3.分层(delamination)多层陶瓷电容器的烧结为多层材料堆叠共烧。
烧结温度可以高达1000℃以上。
《失效分析案例》课件

02
失效分析的方法与技术
介绍了各种失效分析的方法和技术,如外观检查、化学分析、金相切片
、扫描电子显微镜等,以及它们在失效分析中的应用。
03
失效分析案例介绍
列举了一些典型的失效分析案例,包括电子产品、机械零件、复合材料
等,详细介绍了这些案例的失效模式、失效机理和失效原因。
失效分析的展望
失效分析技术的发展趋势
案例三:材料失效
总结词
材料检测、工艺优化、热处理
详细描述
针对材料失效,进行材料检测和工艺优化是关键。通过合理的热处理和加工工艺 ,可以改善材料的性能,提高其抗失效能力。同时,加强材料保护和使用合适的 涂层也是预防材料失效的重要手段。
案例四:结构失效
01 总结词
强度不足、失稳、疲劳
02
详细描述
结构失效通常表现为强度不足 、失稳和疲劳等问题。这些失 效原因可能导致建筑物、桥梁 等结构性能下降、功能丧失或 引发安全问题。
在产品维修和保障阶段,FMEA可以用于分析产品在使用过程中可能出现的问题, 预测产品的寿命和可靠性,为维修和保障计划提供依据。
05 预防与纠正措施
电子产品失效预防与纠正措施
总结词
电子产品失效预防与 纠正措施是确保电子 产品可靠性和性能的 关键。
元器件选择
选择质量稳定、可靠 性高的元器件,避免 使用次品或假冒伪劣 产品。
详细失效分析
采用各种技术和方法,深入分 析失效机制和根本原因。
验证与实施
对改进措施进行验证,并在实 际中实施,以改善产品的可靠 性和性能。
02 失效案例选择与 介绍
案例一:电子产品失效
总结词
详细描述
总结词
详细描述
MLCC漏电失效分析 (2)
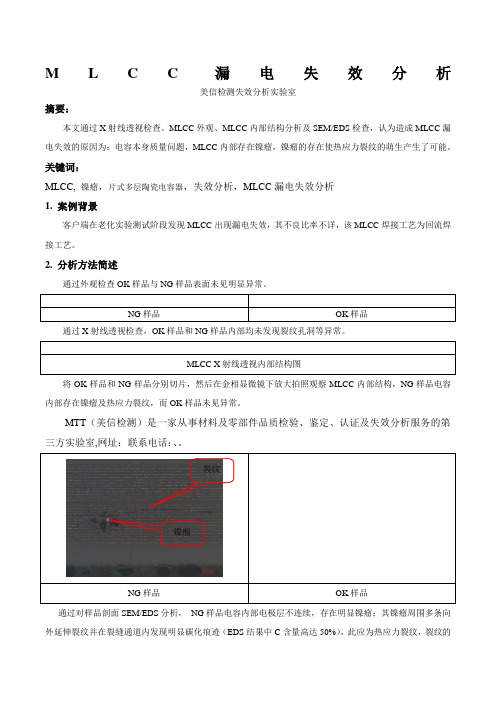
M L C C漏电失效分析美信检测失效分析实验室摘要:本文通过X射线透视检查、MLCC外观、MLCC内部结构分析及SEM/EDS检查,认为造成MLCC漏电失效的原因为:电容本身质量问题,MLCC内部存在镍瘤,镍瘤的存在使热应力裂纹的萌生产生了可能。
关键词:MLCC, 镍瘤,片式多层陶瓷电容器,失效分析,MLCC漏电失效分析1. 案例背景客户端在老化实验测试阶段发现MLCC出现漏电失效,其不良比率不详,该MLCC焊接工艺为回流焊接工艺。
2. 分析方法简述通过外观检查OK样品与NG样品表面未见明显异常。
NG样品OK样品通过X射线透视检查,OK样品和NG样品内部均未发现裂纹孔洞等异常。
MLCC X射线透视内部结构图将OK样品和NG样品分别切片,然后在金相显微镜下放大拍照观察MLCC内部结构,NG样品电容内部存在镍瘤及热应力裂纹,而OK样品未见异常。
MTT(美信检测)是一家从事材料及零部件品质检验、鉴定、认证及失效分析服务的第三方实验室,网址:联系电话:、。
裂纹镍瘤NG样品OK样品通过对样品剖面SEM/EDS分析,NG样品电容内部电极层不连续,存在明显镍瘤;其镍瘤周围多条向外延伸裂纹并在裂缝通道内发现明显碳化痕迹(EDS结果中C含量高达50%),此应为热应力裂纹,裂纹的存在直接导致电容性能异常;而OK样品电容内部电极层连续,陶瓷介质层致密未发现孔洞及镍瘤,电容性能良好。
镍瘤位置碳化痕迹位置NG样品电容内部局部形貌EDS能谱图(镍瘤位置)OK样品电容内部结构空白样品电容内部形貌和EDS能谱图(镍瘤位置)➢失效模式分析:多层陶瓷电容器(MLCC)本身的内在可靠性十分优良,可长时间稳定使用。
但如果器件本身存在缺陷或在组装过程中引入缺陷,则会对可靠性产生严重的影响。
陶瓷多层电容器(MLCC)失效的原因一般分为外部因素和内在因素。
内在因素包括: 陶瓷介质内空洞、介质层分层;外部因素包括:热应力裂纹及机械应力裂纹。
MLCC失效模式及分析手段知识分享
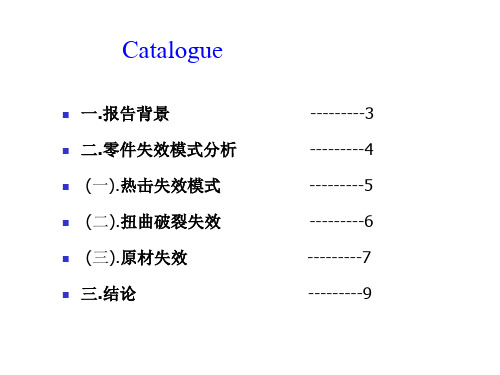
2.SMT之后生产阶段导致的破裂 失效
第三种是电路板切割﹑测试﹑背面组件和连接器安装﹑及 最后组装时,若焊锡组件受到扭曲或在焊锡过程后把电路 板拉直,都有可能造成‘扭曲破裂’这类的损坏。
2.SMT之后生产阶段导致的破裂 失效
在机械力作用下板材弯曲变形时,陶瓷的活动范围受端位 及焊点限制,破裂就会在陶瓷的端接界面处形成,这种破 裂会从形成的位置开始,从45°角向端接蔓延开来。
这些破裂现象一般为可见的表面裂缝,或2至3个电极间的内部破裂; 表面破裂一般会沿着最强的压力线及陶瓷位移的方向。(如图5)
1.SMT阶段导致的破裂失效
第二种是由真空检拾头导致的损坏或破裂﹐一般会在芯片 的表面形成一个圆形或半月形的压痕面积﹐并带有不圆滑 的边缘。此外﹐这个半月形或圆形的裂缝直经也和吸头相 吻合。
(1)热击失效模式:
第一种形如指甲狀或U-形的裂縫和第二种隐藏在内的 微小裂缝,两者的区别只是后者所受的张力较小,而 引致的裂缝也较轻微。第一种引起的破裂明显,一般 可以在金相中测出,第二种只有在发展到一定程度后 金相才可测。
(2)扭曲破裂失效
此种不良的可能性很多:按大类及表现可以分为两种: 1.SMT阶段导致的破裂失效 2.SMT之后生产阶段导致的破裂失效
(1)热击失效模式:
第一种是显而易见的形如指甲狀或U-形的裂縫(见图2)。
C A PA C ITO R
BO OY
端接
熱擎 裂縫
图2 热击破裂示意图
圖4 多層陶 瓷電容器所 出現的熱擎裂縫
(1)热击失效模式:
第二种是隐藏在内的微小裂缝(见图3)
在陶瓷端接介面形成的輕微破裂
電極
陶瓷
端接
图3 轻圖微5 輕热微击破 裂源自的纹位 置1.SMT阶段导致的破裂失效
MLCC电容环境失效案例解析
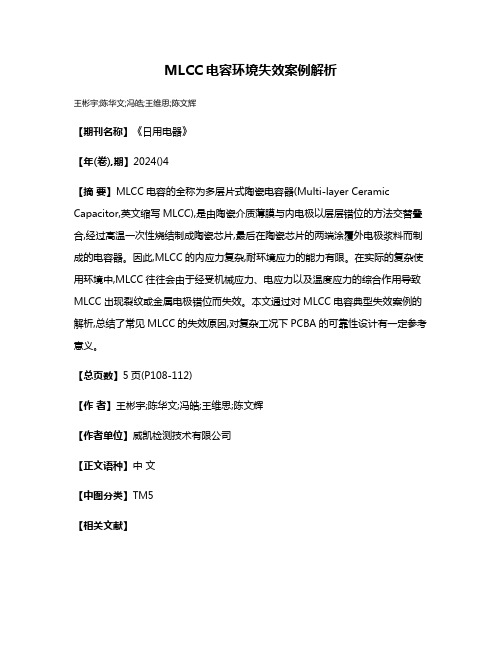
MLCC电容环境失效案例解析
王彬宇;陈华文;冯皓;王维思;陈文辉
【期刊名称】《日用电器》
【年(卷),期】2024()4
【摘要】MLCC电容的全称为多层片式陶瓷电容器(Multi-layer Ceramic Capacitor,英文缩写MLCC),是由陶瓷介质薄膜与内电极以层层错位的方法交替叠合,经过高温一次性烧结制成陶瓷芯片,最后在陶瓷芯片的两端涂覆外电极浆料而制成的电容器。
因此,MLCC的内应力复杂,耐环境应力的能力有限。
在实际的复杂使用环境中,MLCC往往会由于经受机械应力、电应力以及温度应力的综合作用导致MLCC出现裂纹或金属电极错位而失效。
本文通过对MLCC电容典型失效案例的解析,总结了常见MLCC的失效原因,对复杂工况下PCBA的可靠性设计有一定参考意义。
【总页数】5页(P108-112)
【作者】王彬宇;陈华文;冯皓;王维思;陈文辉
【作者单位】威凯检测技术有限公司
【正文语种】中文
【中图分类】TM5
【相关文献】
1.AP14可调电容器瞬间短路的典型失效案例分析
2.铅系多层陶瓷电容器(MLCCs)三层镀失效机理的研究
3.从铝电解电容典型失效案例分析看品质提升
4.MLCC电
容失效分析总结5.薄膜电容器在节能灯上的应用及失效案例分析
因版权原因,仅展示原文概要,查看原文内容请购买。
MLCC电容失效分析及对策ppt课件
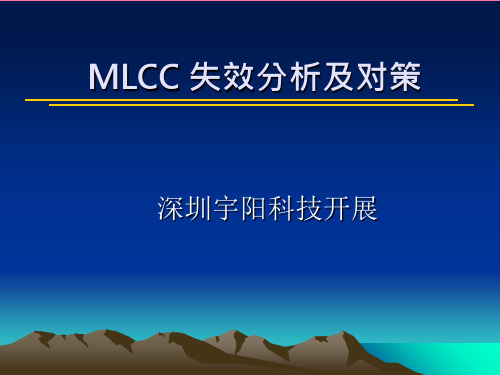
高,会引起PCB板过度分卷曲、脱层或烧损, 损害元件的完好性、瓷体裂纹和墓碑景象; 温度太低:焊膏不能彻底融化,会出现虚焊 等不良景象。
冷却区需求本卷须知
理想的冷却区曲线应该是和回流曲线成镜像 关系,焊点到达固态的构造越严密,得到 的焊接点质量越高,结合完好性越好。 冷却过快:快速的冷热变化,对组件呵斥暂时 的温度差,这使组件接受热-机械应力.当温差 过大时,导致组件的陶瓷与玻璃部分产生应 力裂纹 ;
c、吸嘴磨损过大、吸嘴外表不清洁;
d、吸嘴未校正不准确,吸料时发生偏移;
e 、X&Y轴定位不准确(环球设备自动拾取 校正)、Z轴高度调整,有的贴片机Z轴的 高度是根据元件的厚度而设定的;
f、PCB的外表平整度超出规范(印刷锡膏厚
㈡来料不良缘由 a、料孔太大或太窄; b、纸带偏薄,模具打孔磨损太大,纸带孔偏
相互交流 相互学习
With one’s help,Eyang will be successful.
零落、剥落实例
分板的实例
MLCC组装运用流程
• 废品工艺:
• SMT (Surface Mount Technology)
•
外表(组装)贴装技术
• Dipping 插件工段
• Packing 废品检测包装工段
抛料不良汇总
㈠ 设备不良缘由
a、Feeder料盘没上好;
b、吸嘴(buzzer)清洗不清洁,吸嘴真空压 力不到位;
率不平衡,严重时会出现微裂纹; 2、内电极金属层与陶瓷介质烧结时因热
膨胀系数不同,收缩不一致导致瓷体内部 产生了微裂。(MLCC质量隐患); 3、编织线裂纹
贴片电容失效分析
由于贴片电容的材质是高密度、硬质、易碎和研磨的MLCC,所以在使用过程中,需要十分谨慎。
经有关工程师分析,以下几种情况容易造成贴片电容的断裂及失效:1、贴片电容在贴装过程中,若贴片机吸嘴头压力过大发生弯曲,容易产生变形导致裂纹产生;2、如该颗料的位置在边缘部份或靠近边源部份,在分板时会受到分板的牵引力而导致电容产生裂纹最终而失效.建议在设计时尽可能将贴片电容与分割线平行排放.当我们处理线路板时,建议采用简单的分割器械处理,如我们在生产过程中,因生产条件的限制或习惯用手工分板时,建议其分割槽的深度控制在线路板本身厚度的1/3~1/2之间,当超过1/2时,强烈建议采用分割器械处理,否则,手工分板将会大大增加线路板的挠曲,从而会对相关器件产生较大的应力,损害其可靠性.3、焊盘布局上与金属框架焊接端部焊接过量的焊锡在焊接时受到热膨胀作用力,使其产生推力将电容举起,容易产生裂纹.4、在焊接过程中的热冲击以及焊接完后的基板变形容易导致裂纹产生:电容在进行波峰焊过程中,预热温度,时间不足或者焊接温度过高容易导致裂纹产生,5、在手工补焊过程中.烙铁头直接与电容器陶瓷体直接接触,容量导致裂纹产生。
焊接完成后的基板变型(如分板,安装等)也容易导致裂纹产生。
多层陶瓷电容(MLCC)应用注意事项一、储存为了保持MLCC的性能,防止对MLCC的不良影响储存时注意以下事项:1.室内温度5~40℃,温度20%~70%RH;2.无损害气体:含硫酸、氨、氢硫化合物或氢氯化合物的气体;3.如果MLCC不使用,请不要拆开包装。
如果包装已经打开,请尽可能地重新封上。
缩带装产品请避免太阳光直射,因为太阳光直射会使MLCC老化并造成其性能的下降。
请尽量在6个月内使用,使用之前请注意检查其可焊性。
二、物工操作MLCC是高密度、硬质、易碎和研磨的材质,使用过程中,它易被机械损伤,比如开裂和碎裂(内部开裂需要超声设备检测)。
MLCC在手持过程中,请注意避免污染和损伤。
MLCC在平板电源中的断裂分析和改进 ppt课件
容量计算公式:
C:容量值;
片式电容器的结构图
N:并联的电容器个数,相当于叠层介质的层数;
K:介质的介点常数,与介质的本身特性相关
d:平行板电容器两极板的间距,相当于介质厚度;
s:平行板电容器两极板的正对面积,相当于两层电极的正对面积;
因此, 凡是影响X、d、s、K的因数均能影响电容的容量值 .
电容器的作用
2、外因
主要包括在焊接和焊接后的操作过程中出现的热应力和机械应力。
MLCC的失效分析
分析手段:在失效的MLCC进行剖面分析、难点:需要剪板分析,直拆会加损 失效现象:失效的大部分样品经过DPA分析显示端电极呈现约45℃裂纹(图1) 典型特征:受力最大的部位呈现45℃裂纹(图2)
图1:MLCC弯曲开裂
1 滤波 2 耦合 3 隔直 4 交流取样 5 时间常数设定 6 IC工作频率调整
电容滤波电路 IC工作频率调整
MLCC的温度特性
不同材质电容Biblioteka 电容量以及介质损耗随温度变化的曲线
MLCC属于陶瓷电容器,常见的可分为以下几类: (1) I类电容器,线性温度特性,热稳定性
COG电容器(超稳定级):温度特性平稳、容值小、价值高 (2)II类电容器,非线性温度特性
BENGDING示意图
BENDGING实物图
目录 1 、 MLCC的介绍 2 、 MLCC的失效分析 3 、 MLCC的改善措施 4 、 结论
1、 MLCC材质选择
七
2、 MLCC尺寸选择
大
3、 优化MLCC安装方式
改
善
4、 改进PCB板设计
措 施
5、 改进贴装工艺
6、 优化焊接工艺
7、 改进检验方式
BME电极材料MLCC情况介绍(1)幻灯片PPT
Z5U:ΔC/C+22~-56%, (+10℃~+85℃)
Y5V:ΔC/C+22~-82%, (-30℃~+85℃)
1类瓷的标志代码
〔IEC60384-10、GB/T9324、JIS-C-
5101-10〕
标称温度系数α ppm/℃
温度系数允许偏差 ppm/℃
E6
1.0 1.5 2.2 3.3 4.7 6.8
优先精度
M ±20%
优先数系
E12
1.0 1.2 1.5 1.8 2.2 2.7 3.3 3.9 4.7 5.6 6.8 8.2
优先精度
K ±10%
优先数系 优先精度
E24
J
1.0
±5%
1.1
1.2
1.3
1.5
1.6
1.8
2.0
2.2
2.4
2.7
3.0
聚苯硫醚PPS〕 电解类:钽、铝电解液、有机半导体络合盐
TCNQ、导电聚合物阴极聚吡咯〔PPY〕\ 聚噻吩〔PTN〕
其他类〔云母、云母纸、空气〕
2、各类电容器的特点
• MLCC〔1类〕—微型化、高频化、超低损耗、低ESR、 高稳定、高耐压、高绝缘、高可靠、无极性、低容值、 低本钱、耐高温。
• MLCC〔2类〕—微型化、高比容、中高压、无极性、高 可靠、耐高温、低ESR 、低本钱。
ΔC/C极大值 %
±1.0 ±1.5 ±2.2 ±3.3 ±4.7 ±7.5 ±10.0 ±15.0 ±22.0 +22/-33 +22/-56 +22/-82
(a)
(e)行 的
贴片陶瓷电容失效机理分析
多层贴片陶瓷电容(MLCC)失效机理分析一.MLCC的应用及发展方向MLCC,广泛用于消费、通讯、信息类电子整机设备中,主要起到滤波、隔直、耦合、振荡等作用。
随着电子信息产业不断的发展,电子设备向薄、小、轻、便携式发展,MLCC也逐步向小型化、大容量化、高频率方向发展,MLCC在我们的HID及高端平板电视里有着极为广阔的应用,片状电容是增长速度最快的无源电子元器件之一,具有广阔的发展前景。
二.MLCC的基本结构MLCC有三大部分组成:1. 陶瓷介质 2.内部电极 3.外部电极其中电极一般为Ag或AgPd(钯),陶瓷介质一般为(SrBa)TiO3,多层陶瓷结构通过高温烧结而成。
器件端头镀层一般为烧结Ag/AgPd,然后制备一层Ni阻挡层(以阻挡内部Ag/AgPd材料,防止其和外部Sn发生反应),再在Ni层上制备Sn或SnPb层用以焊接。
近年来,也出现了端头使用Cu的MLCC产品。
三.MLCC的失效模式多层陶瓷电容器本身的内在可靠性十分优良,可以长时间稳定使用。
但如果器件本身存在缺陷或在组装过程中引入缺陷,则会对其可靠性产生严重影响。
陶瓷多层电容器失效的原因分为外部因素和内在因素。
内在因素主要包括以下三个方面: 1.陶瓷介质内空洞导致空洞产生的主要因素为陶瓷粉料内的有机或无机污染,烧结过程控制不当等。
空洞的产生极易导致漏电,而漏电又导致器件内部局部发热,进一步降低陶瓷介质的绝缘性能从而导致漏电增加。
该过程循环发生,不断恶化,严重时导致多层陶瓷电容器开裂、爆炸,甚至燃烧等严重后果。
2. 烧结裂纹烧结裂纹常起源于一端电极,沿垂直方向扩展。
主要原因与烧结过程中的冷却速度有关,裂纹和危害与空洞相仿。
3.分层多层陶瓷电容器的烧结为多层材料堆叠共烧。
烧结温度可以高达1000℃以上。
层间结合力不强,烧结过程中内部污染物挥发,烧结工艺控制不当都可能导致分层的发生。
分层和空洞、裂纹的危害相仿,为重要的多层陶瓷电容器内在缺陷。
- 1、下载文档前请自行甄别文档内容的完整性,平台不提供额外的编辑、内容补充、找答案等附加服务。
- 2、"仅部分预览"的文档,不可在线预览部分如存在完整性等问题,可反馈申请退款(可完整预览的文档不适用该条件!)。
- 3、如文档侵犯您的权益,请联系客服反馈,我们会尽快为您处理(人工客服工作时间:9:00-18:30)。
全面的M1CC失效分析案例课件
Q:M1CC电容是什么结构的呢?
A:多层陶瓷电容器是由印好电极(内电极)的陶瓷介质膜片以错位的方式叠合起来,经过一次性高温烧结形成陶瓷芯片,再在芯片的两端封上金属层(外电极)制成的电容。
Terminations
M1CC电容特点:
机械强度:硬而脆,这是陶瓷材料的机械强度特点。
热脆性:M1eC内部应力很复杂,所以耐温度冲击的能力很有限。
Q:M1CC电容常见失效模式有哪些?
A:
焊接锡量不当
r组装缺陷《
[墓碑效应
多层陶瓷J (陶瓷介质内空洞
电容器缺陷]f内在因素«电极内部分层
I本体缺陷1浆料堆积
(机械应力
【外在因素《热应力
I电应力
Q:怎么区分不同原因的缺陷呢?有什么预防措施呢?
当温度发生变化时,过量的焊锡在贴片电容上产生很高的张力,会使电容内部断裂或者电容器脱帽,裂纹一般发生在焊锡少的一侧;焊锡量过少会造成焊接强度不足,电容从PCB板上脱离,造成开路故障。
2、墓碑效应
(d)Norma1
图3墓碑效应示意图
在回流焊过程中,贴片元件两端电极受到焊锡融化后的表面张力不平衡会产生转动力矩,将元件一端拉偏形成虚焊,转动力矩较大时元件一端会被拉起,形成墓碑效应。
原因:本身两端电极尺寸差异较大;锡镀层不均匀;PCB板焊盘大小不等、有污物或水分、氧化以及焊盘有埋孔;锡膏粘度过高,锡粉氧化。
措施:
①焊接之前对PCB板进行清洗烘干,去除表面污物及水分;
②进行焊前检查,确认左右焊盘尺寸相同;
③锡膏放置时间不能过长,焊接前需进行充分的搅拌。
本体缺陷一内在因素
1、陶瓷介质内空洞
图4陶瓷介质空洞图
原因:
①介质膜片表面吸附有杂质;
②电极印刷过程中混入杂质;
③内电极浆料混有杂质或有机物的分散不均匀。
2、电极内部分层
图5电极内部分层
原因:多层陶瓷电容器的烧结为多层材料堆叠共烧。
瓷膜与内浆在排胶和烧结过程中的收缩率不同,在烧结成瓷过程中,芯片内部产生应力,使M1CC产生再分层。
预防措施:在M1CC的制作中,采用与瓷粉匹配更好的内浆,可以降低分层开裂的风
险。
3、浆料堆积
图6浆料堆积缺陷
原因:
①内浆中的金属颗粒分散不均匀;
②局部内电极印刷过厚;
③内电极浆料质量不佳。
本体缺陷一外在因素
1、机械应力裂纹
图7M1CC受机械应力开裂示意图
原因:多层陶瓷电容器的特点是能够承受较大的压应力,但抗弯曲能力比较差。
当PCB 板发生弯曲变形时,M1CC的陶瓷基体不会随板弯曲,其长边承受的应力大于短边,当应力超过M1CC的瓷体强度时,弯曲裂纹就会出现。
电容在受到过强机械应力冲击时,一般会形成45度裂纹和Y型裂纹。
常见应力源:工艺过程中电路板操作;流转过程中的人、设备、重力等因素;通孔元器件
插入;电路测试,单板分割;电路板安装;电路板点位钾接;螺丝安装等。
裂痕TK
图9流转过程受力开裂示意图
措施:
①选择合适的PCB厚度。
②设计PCBA弯曲量时考虑M1CC能承受的弯曲量。
比较重的元器件尽量均匀摆放,减少生产过程中由于重力造成的板弯曲。
③优化M1CC在PCB板的位置和方向,减小其在电路板上的承受的机械应力,M1CC应尽量与PCB上的分孔和切割线或切槽保持一定的距离,使得M1CC在贴装后分板弯曲时受到的拉伸应力最小。
D
/ ---- 切线孔
弯曲压力比较:A>B>C>D
④M1eC的贴装方向应与开孔、切割线或切槽平行,以确保M1eC在PCB分板弯曲时受到的拉伸应力均匀,防止切割时损坏。
⑤M1CC尽量不要放置在螺丝孔附近,防止锁螺丝时撞击开裂。
在必须放置电容的位置,可以考虑引线式封装的电容器。
图11合理使用支撑杆示意图
⑥测试时合理使用支撑架,避免板受力弯曲。
2、热应力裂纹
图12典型热应力开裂电容
电容在受到过强热应力冲击时,产生的裂纹无固定形态,可分布在不同的切面,严重时会导致在电容侧面形成水平裂纹。
原因:热应力裂纹产生和电容本身耐焊接热能力不合格与生产过程中引入热冲击有关。
可能的原因包括:烙铁返修不当、SMT炉温不稳定、炉温曲线变化速率过快等。
措施:①工艺方法应多考虑M1CC的温度特性和尺寸,1210以上的大尺寸M1CC容易造成受热不均匀,产生破坏性应力,不宜采用波峰焊接;
②注意焊接设备的温度曲线设置。
参数设置中温度跳跃不能大于150℃,温度变化不能大于2°C∕s,预热时间应大于2min,焊接完毕不能采取辅助降温设备,应自然随炉温冷却。
③手工焊接前,应增加焊接前的预热工序,手工焊接全过程中禁止烙铁头
直接接触电容电极或本体。
复焊应在焊点冷却后进行,次数不得超过2次
3、电应力裂纹
图13典型电应力开裂电容
过电应力导致产品发生不可逆变化,表现为耐压击穿,严重时导致多层陶瓷电容器开裂、爆炸,甚至燃烧等严重后果。
遭受过度电性应力伤害的M1CC,裂纹从内部开始呈爆炸状分散。
措施:①在器件选型时应注意实际工作电压不能高于器件的额定工作电压;
②避免浪涌、静电现象对器件的冲击。
Q:怎么进行M1CC失效分析呢?
A:整个过程分为5个大阶段:外观观察、电性测量分析、无损分析、破环性分析、成
分分析,过程中需要进行外观检查、电性测试、内部结构检查、失效点定位、失效原因分
析、失效点局部的成分分析,整个M1CC的失效分析的流程如图:
外观检查→电性能测试→X∙ray检杳—►切片分析→SEM/EDS
图15超景深数码显微镜立体外观观察
首先使用超景深数码显微镜进行外观立体观察,检查电容表面是否有开裂,多角度检查引脚侧面焊锡爬升情况。
电容外观完好,没有外部裂纹,焊锡爬升良好。
图16X-ray检查
对失效电容进行X射线检查,在电容右侧发现裂纹。
图17切片分析超景深数码显微镜观察截面
图18切片分析SEM观察截面裂纹形貌
对电容进行金相切片处理,可以清楚地看出,电容内部裂纹起源于焊端附近,呈Y字型,这是典型的机械应力裂纹形貌,对照可能的应力源排查,规范操作过程,最终解决电容开裂问题。