制动主缸设计计算共21页
制动主缸设计
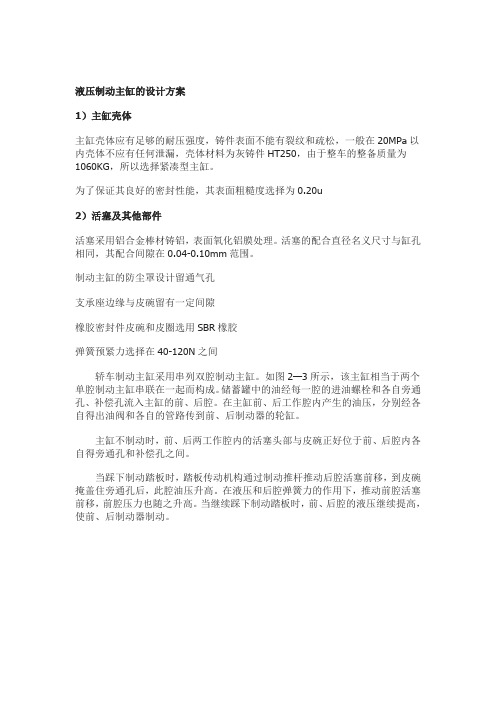
液压制动主缸的设计方案1)主缸壳体主缸壳体应有足够的耐压强度,铸件表面不能有裂纹和疏松,一般在20MPa以内壳体不应有任何泄漏,壳体材料为灰铸件HT250,由于整车的整备质量为1060KG,所以选择紧凑型主缸。
为了保证其良好的密封性能,其表面粗糙度选择为0.20u2)活塞及其他部件活塞采用铝合金棒材铸铝,表面氧化铝膜处理。
活塞的配合直径名义尺寸与缸孔相同,其配合间隙在0.04-0.10mm范围。
制动主缸的防尘罩设计留通气孔支承座边缘与皮碗留有一定间隙橡胶密封件皮碗和皮圈选用SBR橡胶弹簧预紧力选择在40-120N之间轿车制动主缸采用串列双腔制动主缸。
如图2—3所示,该主缸相当于两个单腔制动主缸串联在一起而构成。
储蓄罐中的油经每一腔的进油螺栓和各自旁通孔、补偿孔流入主缸的前、后腔。
在主缸前、后工作腔内产生的油压,分别经各自得出油阀和各自的管路传到前、后制动器的轮缸。
主缸不制动时,前、后两工作腔内的活塞头部与皮碗正好位于前、后腔内各自得旁通孔和补偿孔之间。
当踩下制动踏板时,踏板传动机构通过制动推杆推动后腔活塞前移,到皮碗掩盖住旁通孔后,此腔油压升高。
在液压和后腔弹簧力的作用下,推动前腔活塞前移,前腔压力也随之升高。
当继续踩下制动踏板时,前、后腔的液压继续提高,使前、后制动器制动。
图2—3 制动主缸工作原理图撤出踏板力后,制动踏板机构、主缸前、后腔活塞和轮缸活塞在各自的回位弹簧作用下回位,管路中的制动液在压力作用下推开回油阀流回主缸,于是解除制动。
若与前腔连接的制动管路损坏漏油时,则踩下制动踏板时,只有后腔中能建立液压,前腔中无压力。
此时在液压差作用下,前腔活塞迅速前移到活塞前端顶到主缸缸体上。
此后,后缸工作腔中的液压方能升高到制动所需的值。
若与后腔连接的制动管路损坏漏油时,则踩下制动踏板时,起先只有后缸活塞前移,而不能推动前缸活塞,因后缸工作腔中不能建立液压。
但在后腔活塞直接顶触前缸活塞时,前缸活塞前移,使前缸工作腔建立必要的液压而制动。
制动器的设计计算120080328162413270
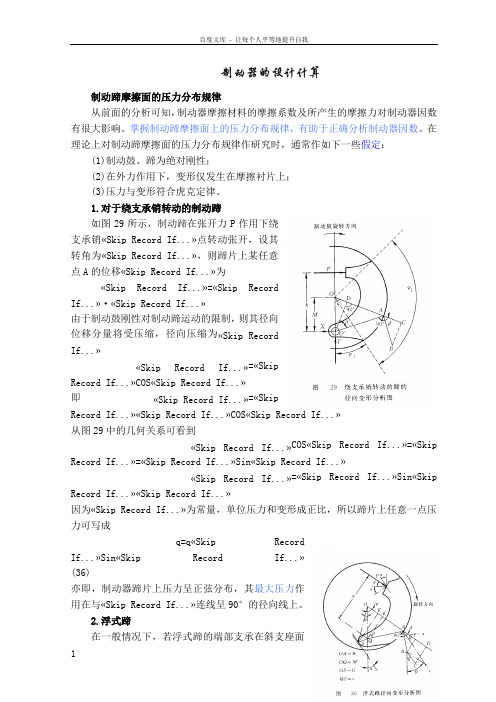
制动器的设计计算制动蹄摩擦面的压力分布规律从前面的分析可知,制动器摩擦材料的摩擦系数及所产生的摩擦力对制动器因数有很大影响。
掌握制动蹄摩擦面上的压力分布规律,有助于正确分析制动器因数。
在理论上对制动蹄摩擦面的压力分布规律作研究时,通常作如下一些假定:(1)制动鼓、蹄为绝对刚性;(2)在外力作用下,变形仅发生在摩擦衬片上;(3)压力与变形符合虎克定律。
1.对于绕支承销转动的制动蹄如图29所示,制动蹄在张开力P作用下绕支承销«Skip Record If...»点转动张开,设其转角为«Skip Record If...»,则蹄片上某任意点A的位移«Skip Record If...»为«Skip Record If...»=«Skip RecordIf...»·«Skip Record If...»由于制动鼓刚性对制动蹄运动的限制,则其径向位移分量将受压缩,径向压缩为«Skip RecordIf...»«Skip Record If...»=«SkipRecord If...»COS«Skip Record If...»即«Skip Record If...»=«SkipRecord If...»«Skip Record If...»COS«Skip Record If...»从图29中的几何关系可看到«Skip Record If...»COS«Skip Record If...»=«Skip Record If...»=«Skip Record If...»Sin«Skip Record If...»«Skip Record If...»=«Skip Record If...»Sin«Skip Record If...»«Skip Record If...»因为«Skip Record If...»为常量,单位压力和变形成正比,所以蹄片上任意一点压力可写成q=q«Skip RecordIf...»Sin«Skip Record If...»(36)亦即,制动器蹄片上压力呈正弦分布,其最大压力作用在与«Skip Record If...»连线呈90°的径向线上。
制动器的设计计算

§3 制动器的设计计算3.3制动蹄上的压力分布规律与制动力矩的简化计算1.沿蹄片长度方向的压力分布规律用解析方法计算沿蹄片长度方向的压力分布规律比较困难,因为除了摩擦衬片有弹性容易变形外,制动鼓、制动蹄以及支承也都有弹性变形。
通常在近似计算中只考虑衬片径向变形的影响,其他零件变形的影响较小,可以忽略不计。
制动蹄可设计成一个自由度和两个自由度的(见图37)形式。
首先计算有两个自由度的增势蹄摩擦衬片的径向变形规律。
为此,取制动鼓中心O点为坐标原点,如图37所示,并让y 1坐标轴通过制动蹄的瞬时转动中心A 1点。
制动时,由于摩擦衬片变形,制动蹄在绕瞬时转动中心A 1转动的同时,还顺着摩擦力作用方向沿支承面移动。
结果使制动蹄中心位于点,因而可以想象未变形的摩擦衬片的表面轮廓(EE 1O l 线)就沿方向移人制动鼓体内。
显然,衬片表面上所有点在这个方向上的变形是相同的。
例如,位于半径,上的任意点的变形就是线段。
因此,对于该点的径向变形为1OO 1OB 1B '11B B 1'11111cos Ψ≈=B B C B δ由于 和ο90)(111−+=Ψαϕmax 11'11δ==OO B B 于是得到增势蹄的径向变形1δ和压力为1q )sin(11max 11ϕαδδ+≈)sin(11max 1ϕα+=q q (43)式中 1α——任意半径1OB 和轴之间的夹角;1y 1ϕ——最大压力线与轴之间的夹角;1OO 1x 1ψ——半径和线之间的夹角。
1OB 1OO 下面再计算有一个自由度的增势蹄摩擦衬片的径向变形规律。
此时摩擦衬片在张开力和摩擦力的作用下,绕支承销中心A 1转动γd 角(见图37(b))。
摩擦衬片表面任意点沿制动蹄转动的切线方向的变形即为线段,其径向变形分量是线段,在半径延长线上的投影,即线段。
由于1B '11B B '11B B 1OB 1BB γd 角很小,可以认为,则所求的摩擦衬片径向变形为°=∠90'111B B Aγγγδd B A B B C B ⋅===sin sin 11'11111 考虑到,则由等腰三角形可知R OB OA =≈1111OB A γαsin /sin /11R B A = 代入上式,得摩擦衬片的径向变形和压力分别为γαδd R sin 1=αsin max 11q q = (44)综合上述可以认为:对于尚未磨合的新制动蹄衬片,沿其长度方向的压力分布符合正弦曲线规律,可用式(43)和式(44)计算。
气缸的设计计算

4.1纵向气缸的设计计算与校核:由设计任务可以知道,要驱动的负载大小位140N,考虑到气缸未加载时实际所能输出的力,受气缸活塞和缸筒之间的摩擦、活塞杆与前气缸之间的摩擦力的影响,并考虑到机械爪的质量。
在研究气缸性能和确定气缸缸径时,常用到负载率β:由《液压与气压传动技术》表11-1:/β=200N 运动速度v=30mm/s,取β=0.7,所以实际液压缸的负载大小为:F=F4.1.1气缸内径的确定D=1.27=1.27 =66.26mmF—气缸的输出拉力 N;P —气缸的工作压力Pa按照GB/T2348-1993标准进行圆整,取D=20 mm气缸缸径尺寸系列8 1 40 50 63 80 (90)100(110)125 (140)160 (180)200 (220)25 304.1.2活塞杆直径的确定由d=0.3D 估取活塞杆直径 d=8mm4.1.3缸筒长度的确定缸筒长度S=L+B+30L为活塞行程;B为活塞厚度活塞厚度B=(0.6 1.0)D= 0.720=14mm由于气缸的行程L=50mm ,所以S=L+B+30=886 mm导向套滑动面长度A:一般导向套滑动面长度A,在D<80mm时,可取A=(0.6 1.0)D;在D>80mm 时, 可取A=(0.6 1.0)d。
所以A=25mm最小导向长度H:根据经验,当气缸的最大行程为L,缸筒直径为D,最小导向长度为:H代入数据即最小导向长度H + =80 mm活塞杆的长度l=L+B+A+80=800+56+25+40=961 mm4.1.4气缸筒的壁厚的确定由《液压气动技术手册》可查气缸筒的壁厚可根据薄避筒计算公式进行计算:式中—缸筒壁厚(m);D—缸筒内径(m);P—缸筒承受的最大工作压力(MPa);—缸筒材料的许用应力(MPa);实际缸筒壁厚的取值:对于一般用途气缸约取计算值的7倍;重型气缸约取计算值的20倍,再圆整到标准管材尺码。
制动主缸DFMEA
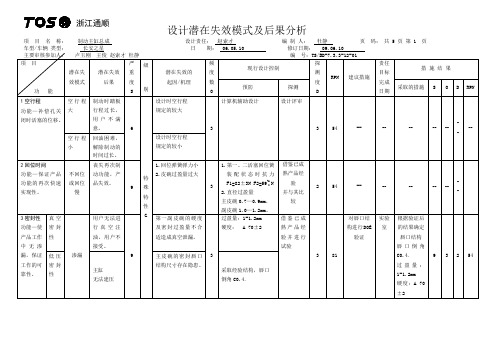
设计潜在失效模式及后果分析
项 目 名 称: 制动主缸总成 设计责任: 赵索才 编 制 人: 杜静 页 码: 共 5 页 第 1 页 车型/车辆 类型: 长安之星 日 期: 06.05.10 修订日期: 09.06.10
浙江通顺
设计潜在失效模式及后果分析
项 目 名 称: 制动主缸总成 设计责任: 赵索才 编 制 人: 杜静 页 码: 共 5 页 第 2 页 车型/车辆类型: 长安之星 日 期: 06.05.10 修订日期: 09.06.10
浙江通顺
设计潜在失效模式及后果分析
项 目 名 称: 制动主缸零部件 设计责任: 赵索才 编 制 人: 杜静 页 码: 共 5 页 第 3 页 车型/车辆类型: 长安之星 日 期: 06.05.10 修订日期: 09.06.10
浙江通顺
浙江通顺
设计潜在失效模式及后果分析
项目名称:制动主缸零部件设计责任:赵索才编制人:杜静页码:共5 页第 4 页车型/车辆类型:长安之星日期: 06.05.10 修订日期: 09.06.10
设计潜在失效模式及后果分析
项 目 名 称: 制动主缸零部件 设计责任: 赵索才 编 制 人: 杜静 页 码: 共 5 页 第 5 页 车型/车辆类型: 长安之星 日 期: 06.05.10 修订日期: 09.06.10
浙江通顺
设计潜在的失效模式及后果分析
(DFMEA)
产品名称:长安之星制动主缸
产品代号:0.02-2005.3B
浙江通顺科技集团有限公司
修订/日期:审核/日期:批准/日期:。
汽车制动主缸标准
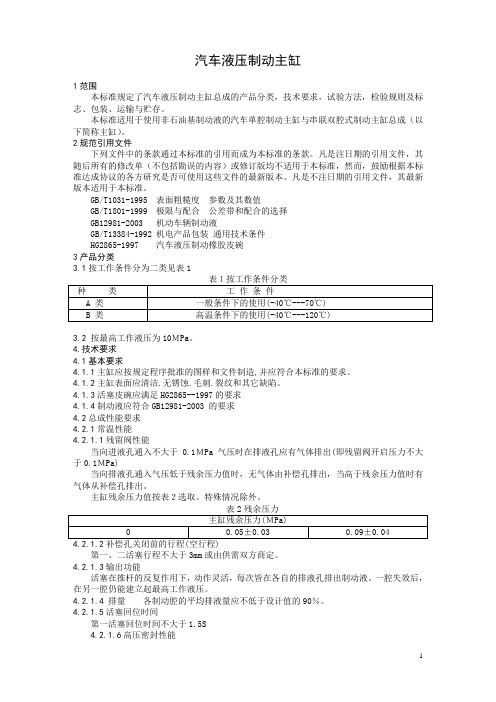
轮缸装置如图 1 所示,试验时将轮缸进液孔与主缸排液孔连接。
5.2 试验要求 5.2.1 试验样品应符合制造厂的技术要求,每次试验样品不少于 3 件,试验结束后才能解体 总成,特殊情况除外。 5.2.2 试验用制动液为非石油基制动液,应满足 12981-2003 的要求,具体牌号可以由供需双
2
方商定。 5.3 常温性能试验 5.3.1 试验条件
0
图 3 主缸第一活塞行程与液压关系曲线 5.5.2 试验方法
向主缸与储液室注满制动液,排净系统中的空气,确认液压系统无任何泄漏后,把主缸 试验装置安装在恒温箱中,在主缸下面放滤纸,开始试验。试验过程中每 2h 观察有无泄漏情 况。 5.5.3 高压密封性能检查
5.5.2 试验结束后,仍在恒温条件下重复 5.3.8 试验,但最高液压取 7.0MPa±0.3MPa, 如无条件也可以在 5min 内转入室温进行上述试验。 5.6 贮存耐腐蚀性试验 5.6.1 试验条件
a)压力表精度不低于 0.4 级 b)真空表 c)环境温度 10℃-32℃ 5.3.2 残留阀性能测量 向进液孔通入不大于 0.1MPa 气压,记录排液孔有气体排出时输入的最低气压值。 向排液孔通入不大于 0.15MPa 气压,观察补偿孔是否有气体排出,记录补偿孔有气体排 出时输入的最低气压值。 5.3.3 补偿孔关闭前的行程(空行程)测量 由排液孔通入残留阀开启的最低气压(对于无残留阀的主缸通入 0.05MPa-0.15MPa 气 压)空气由补偿孔排出后,缓慢地推动活塞,当气流停止从补偿孔排出时,记录活塞最小位移。 5.3.4 输出功能试验 主缸的排液孔与排量测量装置连接,如图 1 所示.向主缸与储液室注满制动液,排净系统 中的空气,连续反复地推动活塞制动液从排液孔断续地排出,在活塞返程时,关闭排液孔, 此项动作至少进行 5 次。试验中观察活塞动作的灵活性,并且模拟一腔失效在另一腔建立最 高工作液压。 5.3.5 排量测量 紧接上项试验,推动活塞到最大行程,关闭排液孔,活塞返回到初始位置后打开排液孔, 推动活塞到最大行程位置。用排量测量装置分别测出两制动腔排量,两次冲程间隔5S,每次 冲程速度约为 2 mm/S -5mm/S。 5.3.6 活塞回位时间测量 向主缸与储液室注满制动液,排净系统中的空气将活塞推至最大行程后,关闭各自的排 液孔,迅速撤消推杆力,记录第一活塞完全返回原位的时间。 5.3.7 高压密封性能试验 向主缸与储液室注满制动液,排净系统中的空气,推动活塞在制动腔中建立起最高工作 液压 10MPa,稳压后保持推杆位置不变,30S 后记录液压降。 5.3.8 耐压性能试验 试验装置同上,缓慢地推动活塞,经过 15S±5S 在制动腔中建立起最高工作液压的 130% (13MPa)稳压后保持推杆位置不变,5S 后记录液压降。 5.3.9 真空密封性试验 将主缸供液孔与真空源连接,使主缸处于工作状态,在供液孔内产生真空度为 0.026MPa ±0.004MPa,检测付皮碗与供液腔的密封性,5S 后记录变化量。 5.3.10 动态密封性
制动主缸毕业论文--汽车制动主缸的设计与优化
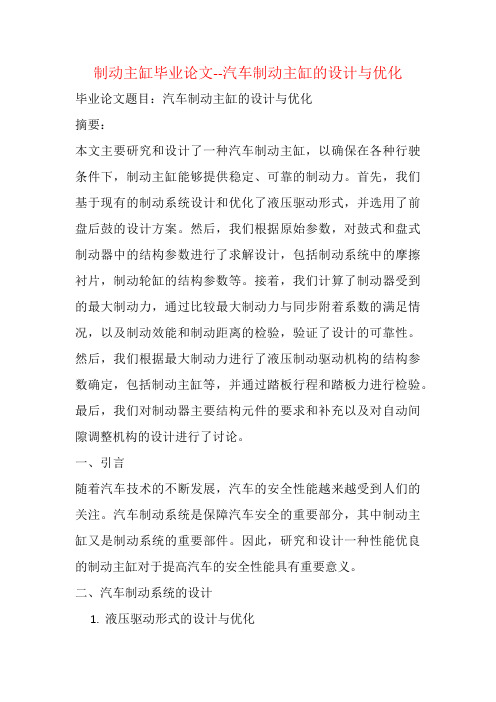
制动主缸毕业论文--汽车制动主缸的设计与优化毕业论文题目:汽车制动主缸的设计与优化摘要:本文主要研究和设计了一种汽车制动主缸,以确保在各种行驶条件下,制动主缸能够提供稳定、可靠的制动力。
首先,我们基于现有的制动系统设计和优化了液压驱动形式,并选用了前盘后鼓的设计方案。
然后,我们根据原始参数,对鼓式和盘式制动器中的结构参数进行了求解设计,包括制动系统中的摩擦衬片,制动轮缸的结构参数等。
接着,我们计算了制动器受到的最大制动力,通过比较最大制动力与同步附着系数的满足情况,以及制动效能和制动距离的检验,验证了设计的可靠性。
然后,我们根据最大制动力进行了液压制动驱动机构的结构参数确定,包括制动主缸等,并通过踏板行程和踏板力进行检验。
最后,我们对制动器主要结构元件的要求和补充以及对自动间隙调整机构的设计进行了讨论。
一、引言随着汽车技术的不断发展,汽车的安全性能越来越受到人们的关注。
汽车制动系统是保障汽车安全的重要部分,其中制动主缸又是制动系统的重要部件。
因此,研究和设计一种性能优良的制动主缸对于提高汽车的安全性能具有重要意义。
二、汽车制动系统的设计1.液压驱动形式的设计与优化液压驱动形式是制动系统的核心部分,其性能直接影响到制动的效能和稳定性。
我们采用前后式(Ⅱ式)双回路制动控制系统,以确保在任何一只车轮出现故障时,其他车轮仍能正常工作。
2.前盘后鼓的设计方案根据盘式和鼓式各自的性能特点,我们选用了前盘后鼓的设计方案。
这种设计方案可以充分发挥盘式制动器的高效性和稳定性,同时利用鼓式制动器在低速时的可靠性。
三、结构参数的设计与求解1.鼓式制动器的设计我们根据制动系统的原始参数,对鼓式制动器中的结构参数进行了求解设计,包括制动轮缸的结构参数等。
这些参数的确定需要考虑制动的效能、稳定性以及制造成本等多方面因素。
2.盘式制动器的设计同样地,我们对盘式制动器的结构参数也进行了求解设计,包括摩擦衬片的厚度、硬度等参数。
制动器的设计与计算(图片高清)

第四节制动器的设计与计算一、鼓式制动器的设计计算1.压力沿衬片长度方向的分布规律除摩擦衬片因有弹性容易变形外,制动鼓、蹄片和支承也有变形,所以计算法向压力在摩擦衬片上的分布规律比较困难。
通常只考虑衬片径向变形的影响,其它零件变形的影响较小而忽略不计。
制动蹄有一个自由度和两个自由度之分。
首先计算有两个自由度的紧蹄摩擦衬片的径向变形规律。
如图8—8a所示,将坐标原点取在制动鼓中心O点。
y I坐标轴线通过蹄片的瞬时转动中心A1点。
制动时,由于摩擦衬片变形,蹄片一面绕瞬时转动中心转动,同时还顺着摩擦力作用的方向沿支承面移动。
结果蹄片中心位于O1点,因而未变形的摩擦衬片的表面轮廓(E1E1线),就沿OO1方向移动进入制动鼓内。
显然,表面上所有点在这个方向上的变形是一样的。
位于半径OB l上的任意点B1的变形就是B1B’1线段,所以同样一些点的径向变形δ1为δ1=B1C1≈B1B’1cosψ1考虑到ψ1≈(φ1+α1—90º)和B1B’1=001=δ1max所以对于紧蹄的径向变形δ1和压力p1为:式中,α1为任意半径OB l和y1轴之间的夹角;Ψl为半径OBi和最大压力线001之间的夹角;φ1为х1轴和最大压力线001之间的夹角。
其次计算有一个自由度的紧蹄摩擦衬片的径向变形规律。
如图8—8b 所示,此时蹄片在张开力和摩擦力作用下,绕支承销A 1转动d γ角。
摩擦衬片表面任意点B l 沿蹄片转动的切线方向的变形就是线段B 1B ’1,其径向变形分量是这个线段在半径OB 1延长线上的投影,即为B 1C 1线段。
由于d γ很小,可认为∠A 1B 1B ’1=90º,故所求摩擦衬片的变形应为δ1=B 1C 1=B 1B’1sin γ1=A 1B 1sin γ1d γ考虑到OA l ~OB 1=R.那么分析等腰三角形A l OB 1,则有A 1月l /sin α=R /sin7,所以表面的径向变形和压力为γαδd R sin 1=αsin max 1p p = (8—2)综上所述可知,新蹄片压力沿摩擦衬片长度的分布符合正弦曲线规律,可用式(8—1)和式(8—2)计算。