回转支承承载能力
影响回转支承承载能力的四个参数

正比:由此 叮计算出 将要求 为4 m的淬硬层深度 a r 只淬到2 m 么 f将} 】 m 5 { 降至 l . j 15 6 ,由此而产 = J的 转支承失效形式为滚道剁落 .即使采取焊补 } 措施 也无济 于事
承蒗遭质量的因素较多,其中滚道淬火硬度、淬硬 层深度 、 滚道 曲率半径和接触角是最 重要的 个影
维普资讯
专 题 综 述
影 响 回转 支承 承 载 能 力的 四个 参数
Hale Waihona Puke 候 宁 【转支承的失效形式有两种 . 一 u ] 是滚道损坏 , 是断齿 . 而滚道损坏 占的比倒达9%以上 , 此 . 8 滚遭 质量是 转支承质量的核心问题。影u尉转支 向
数
不够极易造成心转支承失效 .从滚道表面点蚀开始
直至坍塌
滚道曲而是通过成型砂轮磨削得到的, 砂轮的 修整精度直接复制到滚道上 砂轮修正日 主要有 二 个 差源: 半径对刀误差 、 圆弧偏心距 差和修 上 F 正笔 回转 误差 .其 中前二 个 差 的大小除 与装备水 平有关外.很大程度上取决于操作工的责任心和操 作水平,P此有很大的不确定性 ,对刀误差影响着 , I 滚道半径 ,且它和偏心距 差共I影响着滚道接触
在 表面下 f4 a 1 7 深处 ,因此滚 遭淬硬 层 渫度须 大于
4滚 道 接触 角
接触角是指钢球在滚道上的接触点和钢球球心 连线与I转支承径向剖面( 水平面) 之问的夹角 [ 口 ] 转支承的额定静容量 与 s 成线性正比,一 i n 般原 始接触 角 取 4 。, 所 以称 为原 始接 触角 、 因它 5 之 是 是滚道没计i算和测量的角度, t ‘ 在回转支承轴向和径 向『隙为 ( .原始接触角和装配后的实际接触角 日 J ) 时
回转支承寿命载荷系数

2019/1/3
港口物流技术与装备教育部工程研究中心
9/32
Hale Waihona Puke 2.回转支承轮齿断齿分析2.1 齿轮断齿形式
轮齿受力后,在齿根部产生的弯曲应力很大,且在齿根过渡圆角处 有应力集中,由于轮齿的交变应力超过了材料的疲劳极限,在齿根圆角
处将产生疲劳裂纹,裂纹不断扩展,造成弯曲疲劳折断。过载折断通常
是由于受到短时过载或冲击载荷或轮齿磨薄,是轮齿应力超过其极限应 力所造成的。
2.2 静强度齿根弯曲应力 (2)静强度许用齿根弯曲应力
FPst F limYST YNT
S F min YrelT
(1-2)
式中: F lim —弯曲疲劳极限应力( N / m m2 ) ;
YST —试验齿轮的应力修正系数; YNT —弯曲强度的寿命系数;
YrelT —相对齿根圆角敏感系数;
2019/1/3
港口物流技术与装备教育部工程研究中心
10/32
2.回转支承轮齿断齿分析
2.2 静强度齿根弯曲应力 (1)静强度最大齿根弯曲应力
Fst KV K F K F
式中: K V —动载系数;
Fcal YF YS Y Y bmn
(1-1)
KF —弯曲强度计算的齿向载荷分布系数;
号。
承载能力曲线一般有两条,一条为极限静载曲线,一 条为疲劳寿命曲线。极限静载曲线用于初步选型,疲劳寿
命曲线用于校核。
2019/1/3
港口物流技术与装备教育部工程研究中心
3/32
1. 回转支承的疲劳计算
1.1 回转支承承载能力曲线
2019/1/3
港口物流技术与装备教育部工程研究中心
4/32
单排球式回转支承的承载能力分析

单排球式回转支承的承载能力分析I I I I I I J先进制 造技术杜 睿 吴志军 ( 清华大学 精密仪器与机械学系,北京 !"""#$ )!"#$%&’& () $(#* +#,#+’-% ’" # &’".$/ 0 1(2 &$/2’". 3/#1’".%& ’()* +& ,-) . /(0 1 %234567206 89 :52;)<)80 =0<65(7206 40> ?2;-40)<7* @<)0A -(4 &0)B25<)6C* D 2)/)0A !"""#$* E -)04 FEEEEEEEEEEEEEEEEEEEEEEEEEEEEEEEEEEEEEEEEEEEEEEEEEEEEEEEE E F【摘要】回转支承是工程机械行业的重要基础件。
通过运用赫兹的弹性接触理论对单排球式回转支承内部的接触问题进行计算,推导出了该类型回转支承承载能力的理论计算公式,进而分析了 回转支承的结构及工艺参数对其承载能力的影响,并给出了提高回转支承承载能力的方法,以供工 艺人员参考。
关键词J 回转支承;承载能力;影响因素【!"#$%&’$】!"#$%&’ (#)*%&’+ )*# ()+%, ,-./-&#&0+ $%1#"2 3+#1 %& ,-&+0*3,0%-& .),4%&#*2 %&13+0*25 64# "-)1 %& 04# *-""%&’ #"#.#&0+ -7 ) +%&’"# 8 *-$ +"#$%&’ (#)*%&’ $)+ ,)",3")0#1 (2 3+%&’ ^25K 9 + ,-&0),0 04#-*2: )&1 ) 04#-*#0%,)" 7-*.3") $)+ /*#+#&0#1 7-* 04# "-)1 ,)/),%02 -7 04%+ +"#$%&’ (#)*%&’5 !#;#*)" +0*3,03*)" )&1 0#,4&%,)" 7),0-*+ $#*# 7-3&1 0- +%’&%7%,)&0"2 )77#,0 04# "-)1 ,)/),%02 -7 04# +"#$%&’ (#)*%&’ +031%#15 <#04-1+ 0- %&,*#)+# "-)1 ,)/),%02 -7 +"#$%&’ (#)*%&’+ )*# /*-;%1#1 7-* 0#,4&-"-’%+0+5()* +,%-#. /0)+123 ")&%1234 5,&- ’&6&’1$*4 72809)2’123 8&’$,%中图分类号:@^!W ! 引言文献标识码:M车吊以及各类起重机配套外,还广泛应用于轻工机械、冶金机械、医疗机械、工业机器人、隧道掘进机、堆取料机、导弹发射架、雷达天线座、旋转舞台等。
回转支承轴承的介绍及应用

回转支承轴承的介绍及应用龙马轴承回转支承轴承又叫转盘轴承,有些人也称其为:旋转支承、回旋支承。
回转支承,是一种能够承受综合载荷的大型轴承,可以同时承受较大的轴向、径向负荷和倾覆力矩。
回转支承轴承一般带有安装孔、内齿轮或外齿轮、润滑油孔和密封装置,因而能使主机设计结构紧凑,引导简便,维护容易。
回转支承轴承有无齿式,外齿式和内齿式的四点接触球轴承、双排角接触式球轴承交叉圆柱滚子轴承、交叉圆锥滚子轴承和三排圆柱滚子复合轴承四个系列,其中四点接触球轴承具有较高的静负荷能力,交叉圆柱滚子具有较高的动负荷能力,交叉圆锥滚子轴承的预过盈能使轴承具有较大的支撑刚性和回转精度,三排圆柱滚子组合轴承由于承载能力的提高引向轴承高度,各种力量分别由不同滚道承受,所以同样受力情况下,其轴承直径可大大缩小,因而有使主机更加紧凑的特点是一种高承载能力的回转支承轴承。
回转支承轴承广泛用于起重机械、采掘机械、建筑机械、港口机械、船舶机具以及高精度的雷达机械和导弹发射架等设备的大型回转装置上。
同时也可以根据用户的具体要求设计、开发、生产各种特殊结构回转支承轴承。
回转支承在现实工业中应用很广泛,被人们称为:“机器的关节”,其主要应用在被广泛应用于:汽车起重机、铁路起重机、港口起重机、船用起重机、冶金起重机、集装箱起重机、挖掘机、灌装机、以及CT机驻波治疗仪、航海仪、雷达天线座、导弹发射架、坦克、机器人以及旋转餐厅等等方面。
工程机械回转支承应用广泛,工程机械是回转支承最初应用也是应用最广泛的地方,如土方机械、挖掘机、解体机、堆取料机、平地机、压路机、强夯机、凿岩机械、掘进机等。
其他的还有:混凝土机械:混凝土泵车、混凝土搅拌布料杆一体机、带式布料机给料机械:圆盘式给料机、混砂机起重机械:轮式起重机、履带式起重机、门座式起重机、塔式起重机、叉式起重机、随吊机、龙门起重机地基处理机械:冲击式反循环钻机、回转式钻机、冲击式回转式钻机、旋挖钻机、反循环回转钻机、正循环回转钻机、长螺旋工程钻机、潜水工程钻机、静压桩机、打桩机工程船舶:挖泥船专用车:桥梁检测车、消防车、擦窗机、平板运梁车、高空作业车、自行式高空作业平台轻工机械:饮料机械、吹瓶机、包装机械、灌装机、回转理瓶机、注塑机、船用起重机各种设备平台除了各种工程机械之外,回转支承的应用范围已经在逐渐扩大,目前类似港口设备、冶金设备、钻进平台等设备平台已经开始大范围使用回转支承代替原始轴承。
回转支承

回转支承回转支承是近四十年在世界范围内逐渐兴起的新型机械零部件,它有内外圈、滚动体等构成,目前,我国定型生产的回转支承,主要是80年代初由机械工业部指定天津工程机械研究所组织引进原联邦德国Rothe Erde公司的设计和制造技术。
1984年12月20日发布了中华人民共和国机械工业部标准:JB/2300-84《回转支承型式、基本参数和技术要求》,主要由机械电子工业部天津工程机械研究所、徐州海林回转支承厂负责起草,后来国家又在1991年发布了建筑机械标准:JB36.1-36.3-91,在1999年和2011年先后发布新的机械行业标准JB/2300-1999及JB/2300-2011。
回转支承定义回转支承是一种能够承受综合载荷的大型轴承,可以同时承受较大的轴向、径向负荷和倾覆力矩。
回转支承又叫转轴承,有些人也称其为:旋转支撑承、回旋支承。
英文名字分别叫: slewing bearing 、slewing ring bearing 、turntable bearing、slewing ring。
回转支承在现实工业中应用很广泛,被人们称为:“机器的关节”,是两物体之间需作相对回转运动,又需同时承受轴向力、径向力、倾翻力矩的机械所必需的重要传动部件。
随着机械行业的迅速发展,回转支承在船舶设备、工程机械、轻工机械、冶金机械、医疗机械、工业机械等行业得到了广泛的应用。
回转支承行业在我国已经经历了20余年的发展,自1984年首次发布的JB2300-84《回转支承形式、基本参数和技术要求》标准,以及在1999年修订的JB/T2300-1999《回转支承》标准,现我国已具备了完善的回转支承设计、制造和测试的综合开发能力。
回转支承的基本结构回转支承通常由蜗杆、回转支承、壳体、马达等部件构成。
由于核心部件采用回转支承,因此可以同时承受轴向力、径向力、倾翻力矩。
其形式很多,但结构组成基本大同小异。
由左及右分别是(上部分):1.外圈(有齿或无齿)2.密封带3.滚动体(滚球或滚柱)4.加油嘴由左及右分别是(下部分): 1.堵塞 2.堵塞销3.内圈(有齿或无齿)4.隔离块或保持架5.安装孔(丝孔或光孔)回转支承轴承型号及其结构特点回转支承轴承具有以下部分型号(参照XZWD):单排四点接触球式回转支承(01 系列)单排四点接触球式回转支承由两个座圈组成,结构紧凑、重量轻、钢球与圆弧滚道四点接触,能同时承受轴向力、径向力和倾翻力矩。
关于回转支承的现状及发展状况
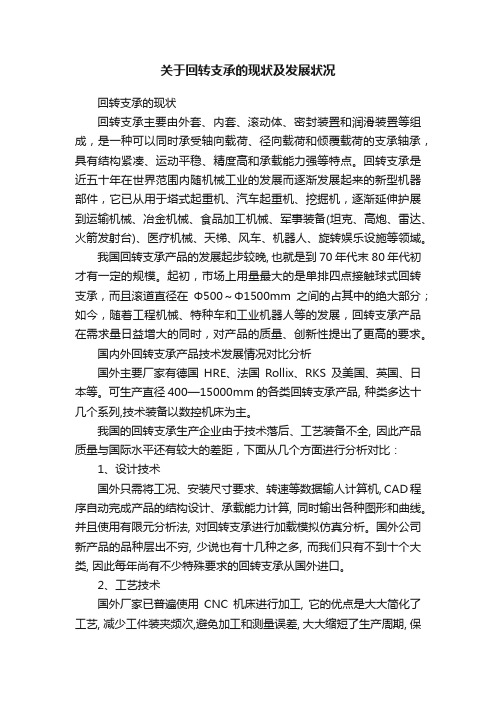
关于回转支承的现状及发展状况回转支承的现状回转支承主要由外套、内套、滚动体、密封装置和润滑装置等组成,是一种可以同时承受轴向载荷、径向载荷和倾覆载荷的支承轴承,具有结构紧凑、运动平稳、精度高和承载能力强等特点。
回转支承是近五十年在世界范围内随机械工业的发展而逐渐发展起来的新型机器部件,它已从用于塔式起重机、汽车起重机、挖掘机,逐渐延伸护展到运输机械、冶金机械、食品加工机械、军事装备(坦克、高炮、雷达、火箭发射台)、医疗机械、天梯、风车、机器人、旋转娱乐设施等领域。
我国回转支承产品的发展起步较晚, 也就是到70年代末80年代初才有一定的规模。
起初,市场上用量最大的是单排四点接触球式回转支承,而且滚道直径在Φ500~Φ1500mm之间的占其中的绝大部分;如今,随着工程机械、特种车和工业机器人等的发展,回转支承产品在需求量日益增大的同时,对产品的质量、创新性提出了更高的要求。
国内外回转支承产品技术发展情况对比分析国外主要厂家有德国HRE、法国Rollix、RKS及美国、英国、日本等。
可生产直径400—15000mm的各类回转支承产品, 种类多达十几个系列,技术装备以数控机床为主。
我国的回转支承生产企业由于技术落后、工艺装备不全, 因此产品质量与国际水平还有较大的差距,下面从几个方面进行分析对比:1、设计技术国外只需将工况、安装尺寸要求、转速等数据输人计算机, CAD程序自动完成产品的结构设计、承载能力计算, 同时输出各种图形和曲线。
并且使用有限元分析法, 对回转支承进行加载模拟仿真分析。
国外公司新产品的品种层出不穷, 少说也有十几种之多, 而我们只有不到十个大类, 因此每年尚有不少特殊要求的回转支承从国外进口。
2、工艺技术国外厂家已普遍使用CNC机床进行加工, 它的优点是大大简化了工艺, 减少工件装夹频次,避免加工和测量误差, 大大缩短了生产周期, 保证了内外圈装配的合套率, 同时提高了产品质量的保证能力。
回转支承选型计算
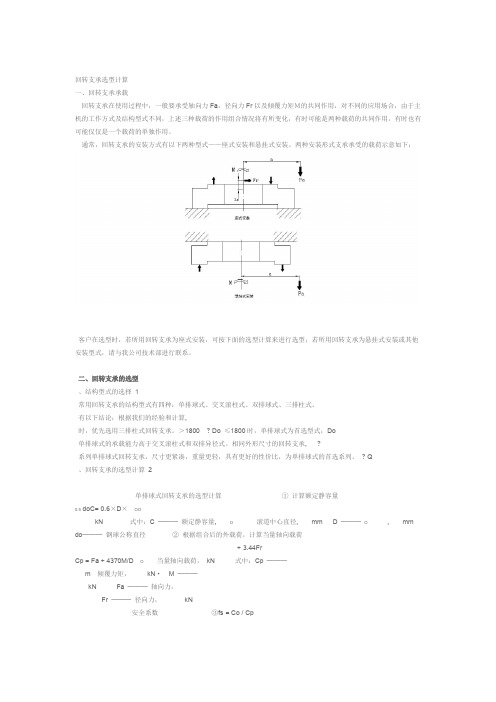
回转支承选型计算一、回转支承承载回转支承在使用过程中,一般要承受轴向力Fa,径向力Fr以及倾覆力矩M的共同作用,对不同的应用场合,由于主机的工作方式及结构型式不同,上述三种载荷的作用组合情况将有所变化,有时可能是两种载荷的共同作用,有时也有可能仅仅是一个载荷的单独作用。
通常,回转支承的安装方式有以下两种型式——座式安装和悬挂式安装。
两种安装形式支承承受的载荷示意如下:客户在选型时,若所用回转支承为座式安装,可按下面的选型计算来进行选型;若所用回转支承为悬挂式安装或其他安装型式,请与我公司技术部进行联系。
二、回转支承的选型、结构型式的选择1常用回转支承的结构型式有四种:单排球式、交叉滚柱式、双排球式、三排柱式。
有以下结论:根据我们的经验和计算,时,优先选用三排柱式回转支承。
>1800? Do ≤1800时,单排球式为首选型式;Do单排球式的承载能力高于交叉滚柱式和双排异径式。
相同外形尺寸的回转支承, ?系列单排球式回转支承,尺寸更紧凑,重量更轻,具有更好的性价比,为单排球式的首选系列。
? Q、回转支承的选型计算2单排球式回转支承的选型计算①计算额定静容量0.5 doC= 0.6×D×OOkN 式中:C ───额定静容量, O滚道中心直径, mm D ───O, mm do───钢球公称直径②根据组合后的外载荷,计算当量轴向载荷+ 3.44FrCp = Fa + 4370M/D O当量轴向载荷,kN 式中:Cp ───m 倾覆力矩,kN·M ───kN Fa ───轴向力,Fr ───径向力,kN安全系数③fs = Co / Cpfs值可按下表选取三排柱式回转支承的选型计算①计算额定静容量0.75×do Co= 0.534×D O kN ───式中:C 额定静容量, O滚道中心直径D ───, mm O上排滚柱直径, mm do ───②根据组合后的外载荷,计算当量轴向载荷Cp = Fa + 4500M/D O kN 当量轴向载荷,C p───式中:M ───倾覆力矩,kN·mFa ───轴向力,kN③安全系数fs = Co / Cpfs值可按下表选取回转支承安全系数f s3、利用静载曲线选型静态承载曲线表示回转支承保持静止状态时所能承受的最大负荷。
回转支承承载能力的探析与提高
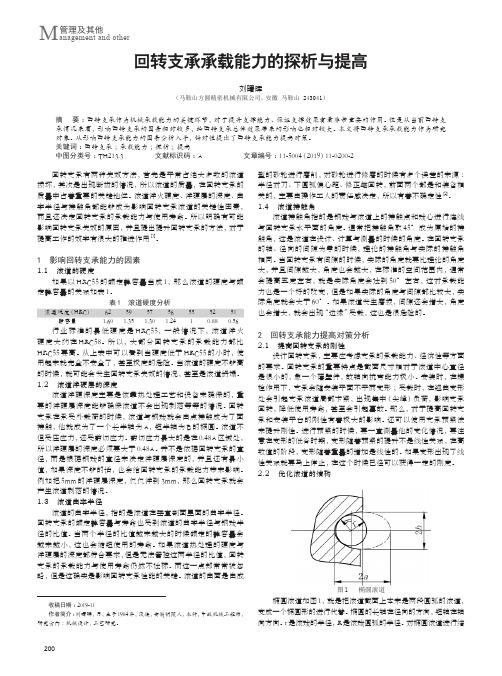
1 影响回转支承能力的因素
1.1 滚道的硬度
如果以 HRC55 的额定静容量当成 1,那么滚道的硬度与额
定静容量的关系如表 1。
表 1 滚道硬度分析
滚道硬度(HRC) 62 59 57 56 55 52 51
静容量
1.60 1.35 1.30 1.24 1 0.88 0.56
行 业 标 准 的 最 低 硬 度 是 HRC55,一 般 情 况 下,滚 道 淬 火
- 1、下载文档前请自行甄别文档内容的完整性,平台不提供额外的编辑、内容补充、找答案等附加服务。
- 2、"仅部分预览"的文档,不可在线预览部分如存在完整性等问题,可反馈申请退款(可完整预览的文档不适用该条件!)。
- 3、如文档侵犯您的权益,请联系客服反馈,我们会尽快为您处理(人工客服工作时间:9:00-18:30)。
影响回转支承承载能力的四个参数回转支承的失效形式有两种,一是滚道损坏,二是断齿,而滚道损坏占的比例达98%以上,因此我们说,滚道质量是回转支承质量的核心问题,影响回转支承滚道质量的因素较多,其中滚道淬火硬度、淬硬层深度、滚道曲率半径和接触角无疑是最重要的四个影响因素,它们以不同的方式影响着滚道质量,并决定了回转支承的承载能力和使用寿命。
•滚道硬度回转支承滚道淬火硬度对其额定静容量影响较大,如以HRC55时额定静容量为标准1,则滚道硬度与额定静容量有下列对应关系:标准规定的最低硬度为HRC55,通常实际平均淬火硬度在HRC57左右,因此绝大多数回转支承实际承载能力均高于按HRC55计算的理论值。
从上表也可看出当硬度低于HRC53时,即使留有1.2的安全系数,使用也不安全了,特别当硬度只有HRC50时,1.7倍的安全系数也形同虚设,非常危险。
硬度不够极易造成回转支承失效,从滚道表面点蚀开始到坍塌结束。
•滚道淬硬层深度滚道淬硬层深度目前尚无无损检测的方法,主要靠工艺和装备来保证,必要的淬硬层深度是回转支承滚道不产生剥落的保证。
当回转支承受外负荷作用时,钢球与滚道的点接触就变成了面接触,是一个长半轴为a,短半轴为b的椭圆面,滚道除受压应力外,还受到剪切应力作用,最大剪切应力发生在表面下0.47a深处,因此滚道淬硬层深度须大于0.47a(一般取0.6a),这也是标准中根据钢球直径大小,而不是根据回转支承直径大小来规定淬硬层深度的原因,同时给出了具体最小保证值。
深度不够又会对回转支承的承载能力产生什么样的影响呢?它定量化的描述是:额定静容量CO与淬硬层深度H0.908成正比,由此可计算出,将要求为4mm的淬硬层深度只淬到2.5mm,那么CO将由1降至0.65,由此而产生的回转支承失效形式为滚道剥落,即使采取焊补措施也无济于事。
•滚道曲率半径这里的滚道曲率半径是指滚道在垂直剖面内的曲率半径,它与钢球半径的比值t(一般为1.04~1.08)的大小也显著影响着回转支承的额定静容量和动容量(寿命Lh),设t=1.04时为额定静容量和寿命均为1,则有下列对比关系:从表中可看出半径比越大额定静容量越低,使用寿命越短,即使滚道热处理硬度和淬硬层深度都符合标准要求,而不能有效控制该半径比,回转支承的承载能力和使用寿命仍达不到标准值,而这一点往往被忽视,但它却是影响回转支承性能的重要参数。
滚道曲面是通过成型砂轮磨削得到的,砂轮的修整精度直接复印到滚道上,砂轮修正时主要有三个误差源:半径对刀误差,上、下圆弧偏心距误差和修正笔回转误差,其中前二个误差的大小除与装备水平有关外,很大程度上取决于操作工的责任心和操作水平,因此有很大的不确定性,对刀误差影响着滚道半径,且它和偏心距误差共同影响着滚道接触角。
•滚道接触角α该接触角是指钢球在滚道上的接触点和钢球球心连线与回转支承径向剖面(水平面)之间的夹角。
回转支承的额定静容量CO与sinα成线性正比,一般原始接触角α取45o,之所以称之谓原始接触角,是因它是滚道设计计算和测量的角度,在回转支承轴、径向间隙为0时,原始接触角和装配后的实际接触角一致,当回转支承有间隙时,实际接触角大于原始接触角,间隙越大,实际接触角越大,在标准规定的间隙范围内一般将增加2o~10o,即实际接触角将达到47o~55o,这是一个对承载能力有利的变化,如果原始接触角和间隙都较大,实际接触角超过60o,随着滚道的磨损间隙将进一步加大,实际接触角也将增大,也就是钢球的落点向滚道边缘靠近,这时将出现接触椭圆面超出滚道边缘,滚道实际受力将高于理论计算应力,而造成滚道边缘压溃,回转支承失效。
因此控制好原始接触角和装配间隙已不是一个简单的精度问题,而是保证承载能力和使用寿命的大事。
影响原始接触角的因素是滚道半径误差和上、下半弧偏心距的误差,而实际接触角以原始接触角为最小值,随着间隙的加大而加大,当钢球与滚道的曲率比不同时,同样的滚道半径和上、下弧偏心距误差对原始接触角误差大小的影响程度不同.同样,装配间隙对实际接触角的影响也与曲率比有关,曲率比越小,实际接触角越大,换言之曲率比越小,原始接触角越难控制,间隙对实际接触角影响越大。
轴向间隙对接触角的从提高滚道的承载能力角度考虑,我们希望滚道与钢球的半径比越小越好,然从控制接触角角度考虑,又不希望太小。
目前国内大多数回转支承厂普遍使用的砂轮修整方式都很难兼顾两者。
顾此失彼,而这往往被一些制造厂有意无意地忽视了。
不是接触角失控就是采用增大滚道半径牺牲滚道承载能力来控制接触角,不管哪种情况出现都是用户所不愿接受的。
解决这一矛盾的有效办法是采用数控装置修整砂轮。
数控三坐标联动自动修整,从原理上避免了半径对刀和偏心距调整而产生的误差,滚道半径和原始接触角得到有效保证。
如果我们把滚道的淬火硬度和淬硬层深度称之谓滚道的“硬件”,那么滚道的半径和接触角就是滚道的“软件”,只“硬”不“软”事倍功半,只有“软、硬”兼备的滚道才是回转支承品质的保证。
数控三坐标联动修整砂轮,有效地保证了滚道的“软件”水平,而滚道在热处理之前的数控车削,则为“硬件”提供了重要保证,这种保证体现在两个方面,其一:数控车削的滚道曲面、形状规则、表面粗糙度低、滚道边口圆弧倒角半径一致,且与滚道面平滑连接。
规则的滚道曲面,使淬硬层深度均匀成为可能,平滑连接的倒角避免了淬火时的“尖角效应”,根除了滚道边口易淬裂的缺陷。
一致的倒角半径解决了过大的倒角造成的滚道有效承载区域的缩小,使钢球在滚道上的接触面过早地到达边口,而影响使用寿命。
其二:数控车削的滚道曲面,除表面粗糙度外,其余尺寸与磨削后的滚道曲面完全一致,因此滚道的磨削量很小(为普通方法加工的1/2~1/3),最大限度地保留了淬硬层深度和表面硬度,同时数控车削滚道使内、外圈的滚道中心直径的一致性得到了很好的保证,避免了因配磨而损失的淬硬层深度和表面硬度,进一步提高了回转支承的承载能力和使用寿命。
综上所述,只有“软、硬”兼备的滚道,才是回转支承承载能力的有效保证,而数控化加工是目前最有效和最可靠的手段。
造成挖掘机用回转支承早期失效的主要原因有二条:一是断齿;二是滚道破坏。
其中,断齿是主要原因,占90%以上,且绝大多数发生在挖掘机出厂后六个月以内。
这不但严重困扰着回转支承制造厂产品质量信誉,同时也对主机厂产品市场造成不利影响,因此认真解决好这一问题是回转支承制造厂和主机厂的共同的目标和责任,也是双方进一步合作共同发展的根本保证。
因断齿而使回转支承早期失效的根本原因是什么呢?设计问题;制造问题,材质问题;装配问题还是使用问题。
透过下列现象不难发现问题的本质之所在:①在过去的十二年里,马鞍山回转支承厂共为各类主机配套回转支承二万余套,除挖掘机行业外,仅有一起回转支承断齿记录,而且是发生在晚期。
当然,挖掘机的工况较塔吊、汽车吊等其它大部分使用回转支承的行业的主机工况要恶劣,回转速度较快,冲击负荷也较大,断齿的可能性相应地也大些,这也是不争的事实。
因此,挖掘机用回转支承的模数较同一滚道直径的其它行业主机用回转支承要大一档,而且是硬齿面(一般在47HRC~58HRC之间选取不同的硬度段),基本满足了挖掘机对回转支承齿轮的要求。
虽然统计资料表明挖掘机用回转支承早期断齿的概率大于其它主机,但也仅限于极少的二、三种挖掘机上,大部分机种极少有回转支承早期断齿事故发生。
②从我们掌握的资料分析,国内外绝大多数20~22吨级的挖掘机使用的回转支承齿轮模数都为10mm (或径节 =2.5),热处理和精度等级基本一致,国产挖掘机一般采用标准齿高和标准压力角。
回转支承齿轮周向许用力P可按下式计算:P=Kz*m*b/78 (吨)式中 Kz=(z/150)^(±0.09)外齿取+;内齿取-z-齿数m-模数mmb-齿宽mm若设齿宽b=80;齿数z=90~110;且为内啮合,则齿轮周向许用力为:p=(90~110/150)^(-0.09)*10*80/78=10.74~10.55(吨)可见齿轮的周向许用力能够满足该吨级的挖掘机对回转支承齿轮负荷要求,但在该级别中个别机型出现的回转支承早期断齿率却高达2%,其它绝大部分机型无此现象发生。
③通过对多起早期断齿实物的分析研究发现,大部分断齿发生在沿齿宽方向的上半部,一半以上的断裂面与轮齿的上端面相交,并成45°~60°左右的夹角,即使全齿脱落其裂纹也是自上而下扩张所致。
齿轮受挤压而产生的塑性变形也相当明显,且上部较下部严重得多,整圈齿槽宽都有不同程度变化,从下至上、从根至顶齿槽宽递增。
我们是否可以认为:造成挖掘机回转支承早期断齿的作用力并非是周向回转驱动力,而是与之啮合的小齿轮对其施加的径向挤压力,且挤压时小齿轮的轴线与回转支承齿轮轴线不平行。
该力产生于挖掘过程中地面对斗的反作用力,由于回转支承有间隙的原故,与回转支承内外圈分别联接的上下两部分在倾覆力矩的作用下,将发生在回转支承通过大臂的轴向剖面上的相对倾斜,同时产生沿回转支承径向与大臂反方向的相对位移,位移量与回转支承径向间隙相当。
因与回转支承啮合的小齿轮安装在大臂的相反方向,当两者齿侧间隙过小时,位移尚未完成,小齿轮便压上大齿轮,这种情况下本应由回转支承滚道承担的负荷却由齿轮担当了,由于小齿轮是悬臂安装原本倾斜的轴线在挤压力的反作用下进一步加剧,致使作用在大齿轮上的挤压力集中在齿宽的上部。
开始齿轮由塑性变形来补偿齿侧间隙的不足,随着回转支承滚道的进一步磨合,其径向间隙渐渐加大,而变形量却是有限的。
通过受力分析可以看到:小齿轮对大齿轮的挤压力是地面对斗的反作用力的几倍甚至十几倍,并且作用在齿廓上的力将被再一次放大,压力角越小放大系数越大。
这一经过两次放大的力足以造成大小齿轮断齿。
以上分析的结论与第③条现象是吻合的。
因此,笔者认为:回转支承早期断齿的根本原因是与小齿轮的配合侧隙过小。
建议侧隙值不小于回转支承径向间隙的1.25倍。
值得参改的是,我厂近期为加拿大制造的四种型号的挖掘机用回转支承的齿轮压力角分别为25°和27°,国内合资厂也有采用。
这对提高齿轮抗径向挤压能力是有效的。
当然,诸如回转支承材质缺陷;齿淬后残余内应力较大、内部有裂纹;因回转支承滚道失效回转卡滞;挖掘机违章操作等也可导致回转支承齿轮早期失效,但应该分布面较广且离散。
一、单排球式回转支承的选型计算1、计算额定静容量C0 = f ·D·d式中:Co ——额定静容量,kNf ——静容量系数,0.108 kN / mm2D ——滚道中心直径,mmd ——钢球公称直径,mm2、根据组合后的外载荷,计算当量轴向载荷式中:Cp ——当量轴向载荷,kNM ——总倾覆力矩,kN·mFa ——总轴向力,kNFr ——总倾覆力矩作用平面的总径向力,kN3、计算安全系数fs = Co / Cpfs值可按下表选取。