毕业设计-中英文翻译模板
毕业论文英文翻译模板【范本模板】
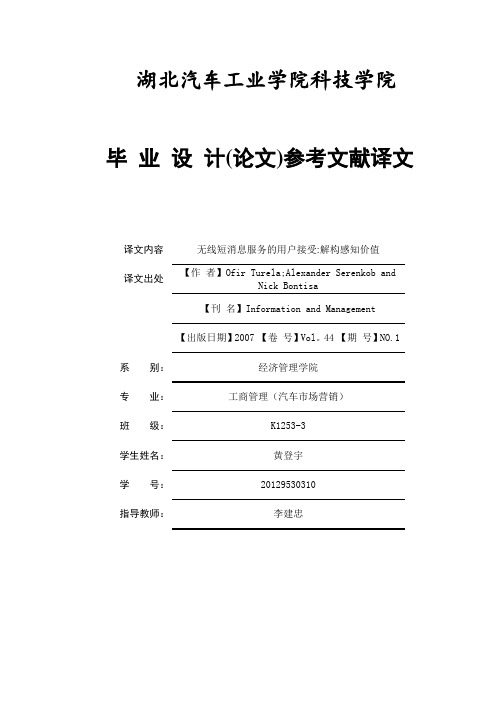
湖北汽车工业学院科技学院毕业设计(论文)参考文献译文译文内容无线短消息服务的用户接受:解构感知价值译文出处【作者】Ofir Turela;Alexander Serenkob andNick Bontisa【刊名】Information and Management【出版日期】2007 【卷号】Vol。
44 【期号】NO.1系别:经济管理学院专业:工商管理(汽车市场营销)班级:K1253-3学生姓名:黄登宇学号:20129530310指导教师:李建忠题目Information & Management 44 (2007) 63–73www.elsevier。
com/locate/imUser acceptance of wireless short messagingservices:Deconstructing perceivedvalueOfir Turel a,*, Alexander Serenko b, Nick Bontis aa DeGroote School of Business, McMaster University, Hamilton, Ontario L8S 4M4, Canadab Faculty of Business Administration, Lakehead University, Thunder Bay, Ontario P7B 5E1, CanadaReceived 22 June 2005; received in revised form 12 April 2006; accepted 26 October 2006Available online 28 November 2006译文原文:译文内容:无线短消息服务的用户接受:解构感知价值无线增值服务,每使用服务,如短消息服务(短信),近年来吸引了越来越多的关注。
然而,现存的文献提供了一些洞察技术采用无线支付,每使用服务.我们的研究探讨了这一采用相结合的营销和观点的222个年轻的,成人短信用户的实证调查.这是假设知觉价值将是一个关键的多维行为意向的决定因素。
毕业设计中英文翻译【范本模板】
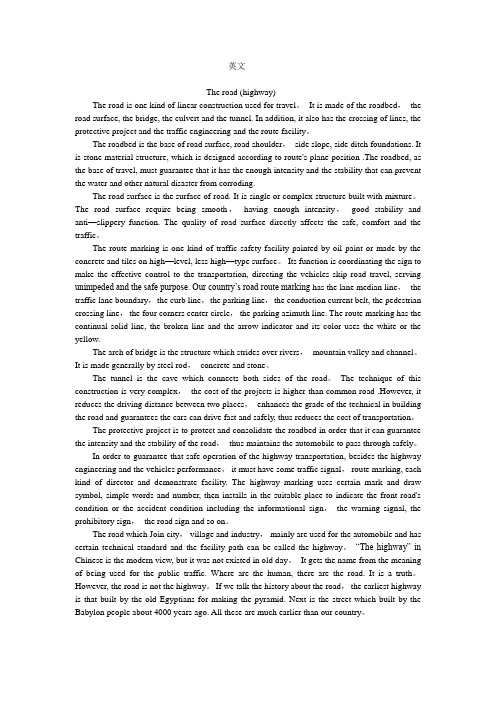
英文The road (highway)The road is one kind of linear construction used for travel。
It is made of the roadbed,the road surface, the bridge, the culvert and the tunnel. In addition, it also has the crossing of lines, the protective project and the traffic engineering and the route facility。
The roadbed is the base of road surface, road shoulder,side slope, side ditch foundations. It is stone material structure, which is designed according to route's plane position .The roadbed, as the base of travel, must guarantee that it has the enough intensity and the stability that can prevent the water and other natural disaster from corroding.The road surface is the surface of road. It is single or complex structure built with mixture。
The road surface require being smooth,having enough intensity,good stability and anti—slippery function. The quality of road surface directly affects the safe, comfort and the traffic。
毕业设计英语翻译全文
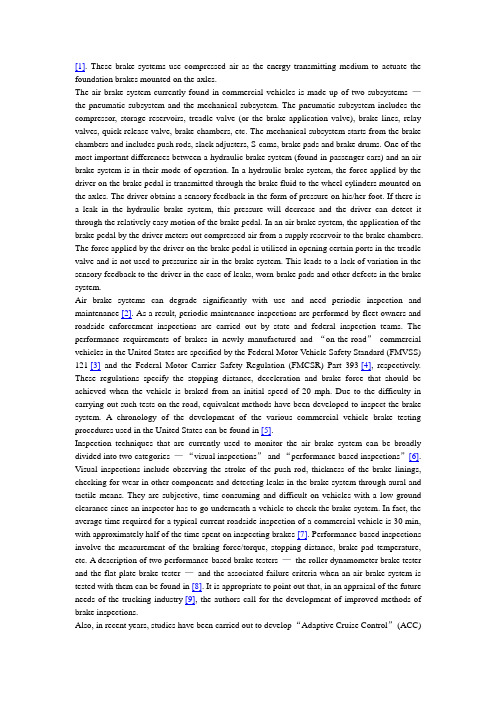
[1]. These brake systems use compressed air as the energy transmitting medium to actuate the foundation brakes mounted on the axles.The air brake system currently found in commercial vehicles is made up of two subsystems —the pneumatic subsystem and the mechanical subsystem. The pneumatic subsystem includes the compressor, storage reservoirs, treadle valve (or the brake application valve), brake lines, relay valves, quick release valve, brake chambers, etc. The mechanical subsystem starts from the brake chambers and includes push rods, slack adjusters, S-cams, brake pads and brake drums. One of the most important differences between a hydraulic brake system (found in passenger cars) and an air brake system is in their mode of operation. In a hydraulic brake system, the force applied by the driver on the brake pedal is transmitted through the brake fluid to the wheel cylinders mounted on the axles. The driver obtains a sensory feedback in the form of pressure on his/her foot. If there is a leak in the hydraulic brake system, this pressure will decrease and the driver can detect it through the relatively easy motion of the brake pedal. In an air brake system, the application of the brake pedal by the driver meters out compressed air from a supply reservoir to the brake chambers. The force applied by the driver on the brake pedal is utilized in opening certain ports in the treadle valve and is not used to pressurize air in the brake system. This leads to a lack of variation in the sensory feedback to the driver in the case of leaks, worn brake pads and other defects in the brake system.Air brake systems can degrade significantly with use and need periodic inspection and maintenance [2]. As a result, periodic maintenance inspections are performed by fleet owners and roadside enforcement inspections are carried out by state and federal inspection teams. The performance requirements of brakes in newly manufactured and “on-the-road”commercial vehicles in the United States are specified by the Federal Motor V ehicle Safety Standard (FMVSS) 121 [3]and the Federal Motor Carrier Safety Regulation (FMCSR) Part 393 [4], respectively. These regulations specify the stopping distance, deceleration and brake force that should be achieved when the vehicle is braked from an initial speed of 20 mph. Due to the difficulty in carrying out such tests on the road, equivalent methods have been developed to inspect the brake system. A chronology of the development of the various commercial vehicle brake testing procedures used in the United States can be found in [5].Inspection techniques that are currently used to monitor the air brake system can be broadly divided into two categories —“visual inspections”and “performance-based inspections”[6]. Visual inspections include observing the stroke of the push rod, thickness of the brake linings, checking for wear in other components and detecting leaks in the brake system through aural and tactile means. They are subjective, time-consuming and difficult on vehicles with a low ground clearance since an inspector has to go underneath a vehicle to check the brake system. In fact, the average time required for a typical current roadside inspection of a commercial vehicle is 30 min, with approximately half of the time spent on inspecting brakes [7]. Performance-based inspections involve the measurement of the braking force/torque, stopping distance, brake pad temperature, etc. A description of two performance-based brake testers —the roller dynamometer brake tester and the flat plate brake tester —and the associated failure criteria when an air brake system is tested with them can be found in [8]. It is appropriate to point out that, in an appraisal of the future needs of the trucking industry [9], the authors call for the development of improved methods of brake inspections.Also, in recent years, studies have been carried out to develop “Adaptive Cruise Control”(ACC)systems or “Autonomous Intelligent Cruise Control”(AICC) systems. The objective of these systems is to maintain a constant distance between two consecutive vehicles by mainly controlling the engine throttle and the brake system. While most of the research on ACC systems has focused on passenger cars, the benefits of implementing such systems on heavy trucks are significant [10].A typical ACC system for heavy trucks controls the engine throttle, the transmission and the brake system and will be interfaced with existing systems like the Antilock Braking System (ABS), Traction Control System (TCS), etc. A typical truck ABS monitors the speed of the wheels and modulates the brake system pressure in the event of an impending wheel lock-up [11]. The ABS consists of an Electronic Control Unit (ECU) that receives signals from the wheel speed sensors and processes this information to regulate the brake system pressure through modulator valves. It should be noted that ABS does not control the treadle valve to regulate the pressure in the brake system. It reduces the brake system pressure that is “commanded”by the driver when it senses an impending wheel lock-up. It cannot provide a higher pressure than that corresponding to the pedal input from the driver.It is important to note that the ABS modulates the brake system pressure only under conditions when a wheel lock-up is impending. The ABS is disengaged during “normal”braking operations. In fact, it has been pointed out in [12] that ABS is “passive during the vast majority of braking operations”. During such braking operations, the pressure of air in the brake system is the level that is commanded by the driver through the motion of the brake pedal. Hence, in order to implement ACC systems on commercial vehicles it is necessary to develop control schemes that will automatically regulate the brake system pressure during all braking operations.Motivated by the above issues, our overall objective is to develop model-based control and diagnostic systems for air brake systems. Such a model of the air brake system should correlate the pressure transients in all the brake chambers of the air brake system with the treadle valve plunger displacement (i.e., the displacement of the brake pedal) and the supply pressure of air provided from the reservoirs to the treadle and relay valves. We have already developed a model [13], and control and diagnostic schemes [14] and [15]based on this model, for the configuration of the air brake system where the primary circuit of the treadle valve is directly connected to one of the two front brake chambers. This model predicts the pressure transients in a front brake chamber during a given brake application with the input data being the treadle valve plunger displacement and the supply pressure to the treadle valve. In order to extend these control and diagnostic schemes, a model should be developed to predict the response of all the brake chambers in the air brake system. One of the steps involved in obtaining a model for the entire air brake system is to develop a model to predict the response of the relay valve, and this is the focus of this article.We will show in the subsequent sections that a relay valve has three phases (or modes) of operation and the evolution of pressure in each of the modes is different. The transition from one mode to another depends primarily on the pressure in the brake chamber and for this reason, it can be naturally modeled as a hybrid system.This article is organized as follows. In Section 2, we present a brief description of the air brake system and the experimental setup that has been constructed at Texas A&M University. A hybrid dynamical model of the relay valve to predict its pressure response is derived in Section 3. We present the equations governing the motion of the mechanical components in the relay valve and the flow of air in the system. This model is corroborated against experimental data and the resultsare provided in Section 4.2. A brief description of the air brake system and the experimental setupA layout of the air brake system found in a typical tractor is presented in Fig. 1. An engine-driven air compressor is used to compress air and the compressed air is collected in storage reservoirs. The pressure of the compressed air in the reservoirs is regulated by a governor. Compressed air is supplied from these reservoirs to the treadle and relay valves. The driver applies the brake by pressing the brake pedal on the treadle valve. This action meters the compressed air from the supply port of the treadle valve to its delivery port. Then, the compressed air travels from the delivery port of the treadle valve through air hoses to the relay valve (referred to as the service relay valve in Fig. 1) and the quick release valve and finally to the brake chambers mounted on the axles.Fig. 1. A general layout of a truck air brake system.View thumbnail imagesThe S-cam foundation brake, found in more than 85% of the air-braked vehicles in the United States [1], is illustrated in Fig. 2. Compressed air metered from the storage reservoirs enters the brake chamber and acts against the diaphragm, generating a force resulting in the motion of the push rod. The motion of the push rod serves to rotate, through the slack adjuster, a splined shaft on which a cam in the shape of an ‘S’is mounted. The ends of two brake shoes rest on the profile of the S-cam and the rotation of the S-cam pushes the brake shoes outwards so that the brake pads make contact with the rotating drum. This action results in the deceleration of the rotating drum. When the brake pedal is released by the driver, air is exhausted from the brake chamber and the push rod strokes back into the brake chamber thereby rotating the S-cam in the opposite direction. The contact between the brake pads and the drum is now broken and the brake is thus released.Fig. 2. The S-cam foundation brake.View thumbnail imagesA schematic of the experimental setup at Texas A&M University is provided in Fig. 3. Two “Type-20”brake chambers (having an effective cross-sectional area of 20 in2) are mounted on a front axle of a tractor and two “Type-30”brake chambers (having an effective cross-sectional area of 30 in2) are mounted on a fixture designed to simulate the rear axle of a tractor. The air supply to the system is provided by means of two compressors and storage reservoirs. The reservoirs are chosen such that their volume is more than twelve times the volume of the brake chambers that they provide air to, as required by the Federal Motor V ehicle Safety Standard (FMVSS) 121 [3]. Pressure regulators are mounted at the delivery ports of the reservoirs to control the supply pressure to the treadle valve and the relay valve. A cross-sectional view of the treadle valve used in the experiments is illustrated in Fig. 4. The treadle valve consists of two circuits —the primary circuit and the secondary circuit. The delivery port of the primary circuit is connected to the control port of the relay valve and the delivery ports of the relay valve are connected to the two rear brake chambers. The relay valve has a separate port for obtaining compressed air supply from the reservoir. The delivery port of the secondary circuit is connected to the Quick Release V alve (QRV) and the delivery ports of the QRV are connected to the two front brake chambers.Fig. 3. A schematic of the experimental facility.View thumbnail imagesFig. 4. A sectional view of the treadle valve.View thumbnail imagesThe treadle valve is actuated by means of a pneumatic actuator and compressed air is supplied to this actuator from the storage reservoirs through a pressure regulator. The displacement of the treadle valve plunger is measured by means of a displacement transducer. A pressure transducer is mounted at the entrance of each of the four brake chambers by means of a custom designed and fabricated pitot tube fixture. A displacement transducer is mounted on each of the two front brake chamber push rods through appropriately fabricated fixtures in order to measure the push rod stroke. All the transducers are interfaced with a connector block through shielded cables. The connector block is connected to a PCI-MIO-16E-4 Data Acquisition (DAQ) board [16] (mounted on a PCI slot inside a desktop computer) that collects the data during brake application and release. An application program is used to collect and store the data in the computer.3. Modeling the response of the relay valveIn this section, we shall present a description of the model of the relay valve. We adopt a lumped parameter approach in the development of this model. Friction at the sliding surfaces in the treadle and relay valves is neglected since they are well lubricated. The springs present in these valves have been experimentally found to be nearly linear in the range of their operation (except the rubber graduating spring used in the treadle valve, see Fig. 4) and the spring constants have been determined from experimental data. Other parameters such as areas, initial deflections, etc., are measured and used in the model.In this article, our objective is to develop a model for predicting the pressure transients in the rear brake chambers actuated by the relay valve during the brake application process. The relay valve is controlled by means of the compressed air delivered by the primary circuit of the treadle valve during a brake application. We shall consider the configuration of the brake system where the delivery port of the primary circuit of the treadle valve is connected to the control port of the relay valve. Compressed air is provided from the storage reservoirs to the relay valve at its supply port and one of the delivery ports of the relay valve is connected to a rear brake chamber. We shall measure the pressure transients at the primary delivery port of the treadle valve and in the rear brake chamber in our experiments. The pressure measured at the primary delivery port of the treadle valve will be provided as input to the numerical scheme that solves the model equations developed to predict the pressure transients in the rear brake chamber.When the driver presses the brake pedal, the primary piston in the treadle valve (see Fig. 4) first closes the primary exhaust port (by moving a distance equal to xpt) and then opens up the primary inlet port (xpp>xpt, xpp being the displacement of the primary piston from its initial position). This action serves to meter the compressed air from the reservoir to the primary delivery port. We shall refer to this phase as the “apply phase”. When the pressure in the primary circuit increases to a level such that it balances the force applied by the driver, the primary piston closes the primary inlet port with the exhaust port also remaining closed (xpp=xpt). We shall refer to this phase as the “hold phase”. When the driver releases the brake pedal, the primary piston return spring forces the primary piston to its initial position. This action opens the exhaust port (xpp<xpt) and air is exhausted from the primary delivery port to the atmosphere. We shall refer to this phase as the “exhaust phase”. A detailed derivation of the model of the treadle valve can be foundin [13].A schematic of the cross-sectional view of the relay valve used in our experimental setup is presented in Fig. 5. The compressed air from the delivery port of the primary circuit of the treadle valve enters the control port of the relay valve. The resulting force pushes the relay valve piston and the exhaust port of the relay valve is closed when the relay valve piston moves a distance equal to xrpt. Once the pre-loads on the relay valve assembly gasket are overcome, the inlet port of the relay valve is opened (xrpp>xrpt, xrpp being the displacement of the relay valve piston from its initial position). Compressed air is now metered from the supply port of the relay valve to its delivery port and subsequently to the rear brake chambers. This is the apply phase associated with the operation of the relay valve. When the pressure in the delivery port of the relay valve increases to a level such that it balances the forces acting on the relay valve piston due to the compressed air from the treadle valve, the inlet port of the relay valve is closed with its exhaust port also remaining closed (xrpp=xrpt). This is the hold phase associated with the operation of the relay valve. When the brake pedal is released by the driver, air is exhausted from the primary circuit of the treadle valve and consequently from the control port of the relay valve. Due to the presence of compressed air in the delivery port of the relay valve, the relay valve piston is pushed back to its initial position and this opens the exhaust port of the relay valve (xrpp<xrpt). Thus, air is exhausted from the delivery port of the relay valve to the atmosphere. This is the exhaust phase associated with the operation of the relay valve.Fig. 5. A sectional view of the relay valve.View thumbnail imagesThe equation of motion governing the mechanics of the operation of the relay valve piston and the relay valve assembly gasket during the apply and the hold phases is given by(1)where Mrpp and Mrv denote respectively the mass of the relay valve piston and the relay valve assembly gasket, xrpp denotes the displacement of the relay valve piston from its initial position, xrpt is the distance traveled by the relay valve piston before it closes the relay valve exhaust port, Krv is the spring constant of the relay valve assembly return spring, Fkrvi is the pre-load on the same, Arpp is the net area of the relay valve piston exposed to the pressurized air at the control port of the relay valve, Arpp1 is the net area of the relay valve piston exposed to the pressurized air at the delivery port of the relay valve, Arpp2 is the net area of the relay valve piston exposed to the exhaust port of the relay valve, Arv1 is the net cross-sectional area of the relay valve assembly gasket exposed to the pressurized air at the supply port of the relay valve, Arv2 is the net cross-sectional area of the relay valve assembly gasket exposed to the pressurized air at the delivery port of the relay valve, Ppd is the pressure of air at the delivery port of the primary circuit of the treadle valve, Prs is the pressure of air being supplied to the relay valve, Prd is the pressure of air at the delivery port of the relay valve and is the atmospheric pressure.The mass of the relay valve piston is of the order of around 0.1 kg and the magnitude of the spring and pressure forces is found to be of the order of 102 N. Thus, the acceleration required for the inertial forces to be comparable with the spring force and the pressure force terms has to be of theorder of 102–103 m/s2, which is not the case. Hence the inertial forces are neglected and the above equation reduces to(2)The equation of motion of the relay valve piston during the exhaust phase is given by(3)Neglecting inertial forces, the above equation reduces to(4)PpdArpp=Prd(Arpp1+Arpp2).Next, we will consider the flow of air in the portion of the brake system under study. The relay valve opening is modeled as a nozzle. For the flow through a restriction, if the ratio of the cross-sectional area of the upstream section to the cross-sectional area of the restriction is 4.4 or higher, the approach velocity to this restriction can be neglected and the upstream properties (such as pressure, enthalpy, temperature, etc.) can be taken to be the upstream total or stagnation properties [17]. In our case, the minimum ratio of the cross-sectional area of the supply chamber of the relay valve to the cross-sectional area of the relay valve opening (the restriction) is found to be more than this value. Hence, we can consider the valve opening as a nozzle and take the properties in the supply chamber of the valve as the stagnation properties at the inlet section of the nozzle. The flow through the nozzle is assumed to be one-dimensional and isentropic. We also assume that the fluid properties are uniform at all sections in the nozzle. Air is assumed to behave like an ideal gas with constant specific heats. Under the above assumptions, the part of the pneumatic subsystem under consideration can be visualized as illustrated in Fig. 6.Fig. 6. The simplified visualization of the pneumatic subsystem under consideration.View thumbnail imagesThe energy equation for the flow of air through the nozzle under the above assumptions can be written as [18](5)where ho is the specific stagnation enthalpy at the entrance section of the nozzle, h is the specific enthalpy at the exit section of the nozzle and u is the magnitude of the velocity of air at the exit section of the nozzle.For isentropic flow of an ideal gas with constant specific heats, the pressure (P), density (ρ) and temperature (T) are related by(6)where γis the ratio of specific heats.The mass flow rate of air from the relay valve opening at any instant of time (denoted by ) isgiven bywhere Ap is the cross-sectional area of the valve opening. This is the rate at which air is accumulating in the hoses and the brake chamber once the relay valve is actuated. Since we lump the properties of air inside the hose and the brake chamber, the mass of air in the brake chamber at any instant of time is obtained from the ideal gas equation of state as(8)where Vb is the volume of air in the brake chamber and Trd is the temperature of air in the brake chamber at that instant of time.Let us now consider the mechanics of the operation of the brake chamber. A cross-sectional view of the brake chamber is shown in Fig. 7. When the brake is applied, the brake chamber diaphragm starts to move only after a minimum threshold pressure is reached. This pressure is required to overcome the pre-loads on the diaphragm. When this pressure is attained in the brake chamber, the diaphragm moves such that the push rod is pushed out of the brake chamber. Once the brake pads contact the brake drum and steady state is reached, the volume of air in the brake chamber will be the maximum during that particular brake application. Thus, the volume of air in the brake chamber at any instant of time during the brake application process is given by(9)where V o1 is the initial volume of air in the brake chamber before the application of the brake, V o2 is the maximum volume of air in the brake chamber, Ab is the cross-sectional area of the brake chamber, xb is the displacement of the brake chamber diaphragm, i.e., the stroke of the push rod, and xbmax is the maximum stroke of the push rod.Fig. 7. A sectional view of the brake chamber.View thumbnail imagesIn our current experimental setup, the rear brake chambers are mounted on a fixture and the end of the push rod outside the brake chamber is not connected to a slack adjuster. The push rod is brought to rest during a given brake application when it strikes a plate mounted with its face perpendicular to the direction of motion of the push rod. The position of this plate can be adjusted to vary the push rod stroke. Hence, a reasonable model for the brake chamber is given by(10)where Mb is the mass of the brake chamber diaphragm, Kb is the spring constant of the brake chamber return spring and Fkbi is the pre-load on the brake chamber diaphragm return spring. It should be noted that the pressure of air in the rear brake chamber at any instant of time is assumed to be the same as the pressure of air at the delivery port of the relay valve at that instant of time. Neglecting inertial forces when compared to the force due to the pressure and spring forces, the above equation reduces toIn the case of a brake chamber mounted on an actual axle, the relationship between the push rod stroke and the brake chamber pressure has been found to be different than the one given by Eq.(11) due to the presence of additional components such as the slack adjuster, S-cam, brake pads and brake drum [15]. Thus, the model relating the push rod stroke and the brake chamber pressure for a rear brake chamber mounted on an actual rear axle should be developed as described in [15]. Differentiating Eq. (8) with respect to time and comparing the result with Eq. (7), and using Eqs.(5), (6), (9) and (11), we obtain the equation describing the pressure response of the relay valve during the apply and hold phases as(12)where Trs is the temperature of the air being supplied to the relay valve, CD is the discharge coefficient, R is the specific heat of air, γis the ratio of specific heats of air (both R and γare assumed to be constants) and(13)Ap=2πrrv(xrpp−xrpt),with rrv being the external radius of the relay valve inlet section. The discharge coefficient (CD) is used in order to compensate for the losses during the flow. Due to the complexity involved in calibrating the valve to determine the value of the discharge coefficient, we assumed a value of 0.82 for CD as recommended in [17]. The pressure transients in the brake chamber during the apply and hold phases are obtained by solving Eqs. (2) and (12) along with the initial condition that at the start of a given brake application, the brake chamber pressure is equal to the atmospheric pressure.4. Corroboration of the modelIn this section, we corroborate the model for the relay valve by comparing its predictions against experimental data obtained from various test runs carried out over a range of supply pressures. It should be noted that the typical supply pressure in air brake systems is usually between 825.3 kPa (105 psig) and 928.8 kPa (120 psig) and this is the pressure range provided by the compressor used in our experimental setup. Eqs. (2) and (12) are solved numerically to obtain the pressure transients in the rear brake chamber during the apply and hold phases of a given brake application. The pressure measured at the delivery port of the primary circuit of the treadle valveis given as the input data to the numerical scheme. The prediction of the model for a test run is compared with the data collected during that test run and the results from various test runs are presented in Fig. 8, Fig. 9, Fig. 10, Fig. 11 and Fig. 12. In these figures, time (in seconds) and brake chamber pressure (in Pa) have been plotted on the abscissa and the ordinate respectively. The value corresponds to that instant of time at which the computer program for collecting the data is started.Fig. 8. Pressure transients at 653 kPa (80 psig) supply pressure —apply phase.View thumbnail imagesFig. 9. Pressure transients at 722 kPa (90 psig) supply pressure —apply phase.View thumbnail imagesFig. 10. Pressure transients at 584 kPa (70 psig) supply pressure —apply and exhaust phases. View thumbnail imagesFig. 11. Pressure transients at 653 kPa (80 psig) supply pressure —apply and exhaust phases. View thumbnail imagesFig. 12. Pressure transients at 584 kPa (70 psig) supply pressure —repeated application.View thumbnail imagesIt can be observed from these figures that the model is able to predict the beginning and end of each brake application reasonably well. The steady state brake chamber pressure is also predicted well by the model in all the cases. The model has also captured the pressure transients well in the exhaust phase during a complete brake application and release cycle as shown in Fig. 10 and Fig. 11. It has also predicted the pressure transients well in the case of repeated brake applications as can be observed from Fig. 12.5. ConclusionsIn this article, we have developed a hybrid model for predicting the response of the relay valve used in air brake systems of commercial vehicles. The relay valve is actuated by the compressed air from the delivery port of the primary circuit of the treadle valve. We have presented the main governing equations for the pressure transients in a rear brake chamber attached to a delivery port of the relay valve. We have corroborated this model using data obtained from experimental test runs performed over a range of supply pressures. We plan to incorporate this model of the relay valve into an overall model of the air brake system which can be used in control and diagnostic applications.References[1]S.F. Williams, R.R. Knipling, Automatic slack adjusters for heavy vehicle air brake systems, Tech. Rep. DOT HS 807 724, National Highway Traffic Safety Administration, Washington, D. C., February 1991。
毕业设计中英文翻译

Programmable logic controllerA programmable logic controller (PLC) or programmable controller is a digital computer used for automation of electromechanical processes, such as control of machinery on factory assembly lines, amusement rides, or lighting fixtures. PLCs are used in many industries and machines. Unlike general-purpose computers, the PLC is designed for multiple inputs and output arrangements, extended temperature ranges, immunity to electrical noise, and resistance to vibration and impact. Programs to control machine operation are typically stored in battery-backed or non-volatile memory. A PLC is an example of a real time system since output results must be produced in response to input conditions within a bounded time, otherwise unintended operation will result.1.HistoryThe PLC was invented in response to the needs of the American automotive manufacturing industry. Programmable logic controllers were initially adopted by the automotive industry where software revision replaced the re-wiring of hard-wired control panels when production models changed.Before the PLC, control, sequencing, and safety interlock logic for manufacturing automobiles was accomplished using hundreds or thousands of relays, cam timers, and drum sequencers and dedicated closed-loop controllers. The process for updating such facilities for the yearly model change-over was very time consuming and expensive, as electricians needed to individually rewire each and every relay.In 1968 GM Hydramatic (the automatic transmission division of General Motors) issued a request for proposal for an electronic replacement for hard-wired relay systems. The winning proposal came from Bedford Associates of Bedford, Massachusetts. The first PLC, designated the 084 because it was Bedford Associates' eighty-fourth project, was the result. Bedford Associates started a new company dedicated to developing, manufacturing, selling, and servicing this new product: Modicon, which stood for MOdular DIgital CONtroller. One of the people who worked on that project was Dick Morley, who is considered to be the "father" of the PLC. The Modicon brand was sold in 1977 to Gould Electronics, and later acquired by German Company AEG and then by French Schneider Electric, the current owner.One of the very first 084 models built is now on display at Modicon's headquarters in North Andover, Massachusetts. It was presented to Modicon by GM,when the unit was retired after nearly twenty years of uninterrupted service. Modicon used the 84 moniker at the end of its product range until the 984 made its appearance.The automotive industry is still one of the largest users of PLCs.2.DevelopmentEarly PLCs were designed to replace relay logic systems. These PLCs were programmed in "ladder logic", which strongly resembles a schematic diagram of relay logic. This program notation was chosen to reduce training demands for the existing technicians. Other early PLCs used a form of instruction list programming, based on a stack-based logic solver.Modern PLCs can be programmed in a variety of ways, from ladder logic to more traditional programming languages such as BASIC and C. Another method is State Logic, a very high-level programming language designed to program PLCs based on state transition diagrams.Many early PLCs did not have accompanying programming terminals that were capable of graphical representation of the logic, and so the logic was instead represented as a series of logic expressions in some version of Boolean format, similar to Boolean algebra. As programming terminals evolved, it became more common for ladder logic to be used, for the aforementioned reasons. Newer formats such as State Logic and Function Block (which is similar to the way logic is depicted when using digital integrated logic circuits) exist, but they are still not as popular as ladder logic.A primary reason for this is that PLCs solve the logic in a predictable and repeating sequence, and ladder logic allows the programmer (the person writing the logic) to see any issues with the timing of the logic sequence more easily than would be possible in other formats.2.1ProgrammingEarly PLCs, up to the mid-1980s, were programmed using proprietary programming panels or special-purpose programming terminals, which often had dedicated function keys representing the various logical elements of PLC programs. Programs were stored on cassette tape cartridges. Facilities for printing and documentation were very minimal due to lack of memory capacity. The very oldest PLCs used non-volatile magnetic core memory.More recently, PLCs are programmed using application software on personal computers. The computer is connected to the PLC through Ethernet, RS-232, RS-485 or RS-422 cabling. The programming software allows entry and editing of theladder-style logic. Generally the software provides functions for debugging and troubleshooting the PLC software, for example, by highlighting portions of the logic to show current status during operation or via simulation. The software will upload and download the PLC program, for backup and restoration purposes. In some models of programmable controller, the program is transferred from a personal computer to the PLC though a programming board which writes the program into a removable chip such as an EEPROM or EPROM.3.FunctionalityThe functionality of the PLC has evolved over the years to include sequential relay control, motion control, process control, distributed control systems and networking. The data handling, storage, processing power and communication capabilities of some modern PLCs are approximately equivalent to desktop computers. PLC-like programming combined with remote I/O hardware, allow a general-purpose desktop computer to overlap some PLCs in certain applications. Regarding the practicality of these desktop computer based logic controllers, it is important to note that they have not been generally accepted in heavy industry because the desktop computers run on less stable operating systems than do PLCs, and because the desktop computer hardware is typically not designed to the same levels of tolerance to temperature, humidity, vibration, and longevity as the processors used in PLCs. In addition to the hardware limitations of desktop based logic, operating systems such as Windows do not lend themselves to deterministic logic execution, with the result that the logic may not always respond to changes in logic state or input status with the extreme consistency in timing as is expected from PLCs. Still, such desktop logic applications find use in less critical situations, such as laboratory automation and use in small facilities where the application is less demanding and critical, because they are generally much less expensive than PLCs.In more recent years, small products called PLRs (programmable logic relays), and also by similar names, have become more common and accepted. These are very much like PLCs, and are used in light industry where only a few points of I/O (i.e. a few signals coming in from the real world and a few going out) are involved, and low cost is desired. These small devices are typically made in a common physical size and shape by several manufacturers, and branded by the makers of larger PLCs to fill out their low end product range. Popular names include PICO Controller, NANO PLC, and other names implying very small controllers. Most of these have between 8 and12 digital inputs, 4 and 8 digital outputs, and up to 2 analog inputs. Size is usually about 4" wide, 3" high, and 3" deep. Most such devices include a tiny postage stamp sized LCD screen for viewing simplified ladder logic (only a very small portion of the program being visible at a given time) and status of I/O points, and typically these screens are accompanied by a 4-way rocker push-button plus four more separate push-buttons, similar to the key buttons on a VCR remote control, and used to navigate and edit the logic. Most have a small plug for connecting via RS-232 or RS-485 to a personal computer so that programmers can use simple Windows applications for programming instead of being forced to use the tiny LCD and push-button set for this purpose. Unlike regular PLCs that are usually modular and greatly expandable, the PLRs are usually not modular or expandable, but their price can be two orders of magnitude less than a PLC and they still offer robust design and deterministic execution of the logic.4.PLC TopicsFeaturesThe main difference from other computers is that PLCs are armored for severe conditions (such as dust, moisture, heat, cold) and have the facility for extensive input/output (I/O) arrangements. These connect the PLC to sensors and actuators. PLCs read limit switches, analog process variables (such as temperature and pressure), and the positions of complex positioning systems. Some use machine vision. On the actuator side, PLCs operate electric motors, pneumatic or hydraulic cylinders, magnetic relays, solenoids, or analog outputs. The input/output arrangements may be built into a simple PLC, or the PLC may have external I/O modules attached to a computer network that plugs into the PLC.System scaleA small PLC will have a fixed number of connections built in for inputs and outputs. Typically, expansions are available if the base model has insufficient I/O. Modular PLCs have a chassis (also called a rack) into which are placed modules with different functions. The processor and selection of I/O modules is customised for the particular application. Several racks can be administered by a single processor, and may have thousands of inputs and outputs. A special high speed serial I/O link is used so that racks can be distributed away from the processor, reducing the wiring costs for large plants.User interfacePLCs may need to interact with people for the purpose of configuration, alarm reporting or everyday control.A simple system may use buttons and lights to interact with the user. Text displays are available as well as graphical touch screens. More complex systems use a programming and monitoring software installed on a computer, with the PLC connected via a communication interface.CommunicationsPLCs have built in communications ports, usually 9-pin RS-232, but optionally EIA-485 or Ethernet. Modbus, BACnet or DF1 is usually included as one of the communications protocols. Other options include various fieldbuses such as DeviceNet or Profibus. Other communications protocols that may be used are listed in the List of automation protocols.Most modern PLCs can communicate over a network to some other system, such as a computer running a SCADA (Supervisory Control And Data Acquisition) system or web browser.PLCs used in larger I/O systems may have peer-to-peer (P2P) communication between processors. This allows separate parts of a complex process to have individual control while allowing the subsystems to co-ordinate over the communication link. These communication links are also often used for HMI devices such as keypads or PC-type workstations.ProgrammingPLC programs are typically written in a special application on a personal computer, then downloaded by a direct-connection cable or over a network to the PLC. The program is stored in the PLC either in battery-backed-up RAM or some other non-volatile flash memory. Often, a single PLC can be programmed to replace thousands of relays.Under the IEC 61131-3 standard, PLCs can be programmed using standards-based programming languages. A graphical programming notation called Sequential Function Charts is available on certain programmable controllers. Initially most PLCs utilized Ladder Logic Diagram Programming, a model which emulated electromechanical control panel devices (such as the contact and coils of relays) which PLCs replaced. This model remains common today.IEC 61131-3 currently defines five programming languages for programmable control systems: FBD (Function block diagram), LD (Ladder diagram), ST(Structured text, similar to the Pascal programming language), IL (Instruction list, similar to assembly language) and SFC (Sequential function chart). These techniques emphasize logical organization of operations.While the fundamental concepts of PLC programming are common to all manufacturers, differences in I/O addressing, memory organization and instruction sets mean that PLC programs are never perfectly interchangeable between different makers. Even within the same product line of a single manufacturer, different models may not be directly compatible.DDER LOGIC FUNCTIONSTopics:• Functions for data handling, mathematics, conversions, array operations, statistics,comparison and Boolean operations.• Design examplesObjectives:• To understand basic functions that allow calculations and comparisons• To understand array f unctions using memory files5.1INTRODUCTIONLadder logic input contacts and output coils allow simple logical decisions. Functionsextend basic ladder logic to allow other types of control. For example, the addition oftimers and counters allowed event based control. A longer list of functions is shown inFigure 5.1. Combinatorial Logic and Event functions have already been covered. Thischapter will discuss Data Handling and Numerical Logic. The next chapter will coverLists and Program Control and some of the Input and Output functions. Remaining functionswill be discussed in later chapters.Combinatorial Logic- relay contacts and coilsEvents- timer instructions- counter instructionsData Handling- moves- mathematics- conversionsNumerical Logic- boolean operations- comparisonsLists- shift registers/stacks- sequencersProgram Control- branching/looping- immediate inputs/outputs- fault/interrupt detectionInput and Output- PID- communications- high speed counters- ASCII string functionsFigure 5.1 Basic PLC Function CategoriesMost of the functions will use PLC memory locations to get values, store values and track function status. Most function will normally become active when the input is true. But, some functions, such as TOF timers, can remain active when the input is off. Other functions will only operate when the input goes from false to true, this is known as positive edge triggered. Consider a counter that only counts when the input goes from false to true, the length of time the input is true does not change the function behavior. A negative edge triggered function would be triggered when the input goes from true to false. Most functions are not edge triggered: unless stated assume functions are not edge triggered.NOTE: I do not draw functions exactly as they appear in manualsandprogramming software.This helps save space and makes the instructionssomewhat easier to read. All of the necessary information is given.5.2 DATA HANDLING5.2.1 Move FunctionsThere are two basic types of move functions;MOV(value,destination) - moves a value to a memory locationMVM(value,mask,destination) - moves a value to a memory location, but with a mask to select specific bits.The simple MOV will take a value from one location in memory and place it inanother memory location. Examples of the basic MOV are given in Figure 5.2. When A is true the MOV function moves a floating point number from the source tothe destination address. The data in the source address is left unchanged. When B is true the floating point number in the source will be converted to an integer and storedin the destination address in integer memory. The floating point number will be rounded up or down to the nearest integer. When C is true the integer value of 123will be placed in the integer file N7:23.NOTE: when a function changes a value, except for inputs and outputs, the value is changed immediately. Consider Figure 15.2, if A, B and C are all true, then the value in F8:23 will change before the next instruction starts. This is different than the input and output scans that only happen before and after the logic scan.Figure 5.2 Examples of the MOV FunctionA more complex example of move functions is given in Figure 5.3. When Abecomes true the first move statement will move the value of 130 into N7:0. And, the second move statement will move the value of -9385 from N7:1 to N7:2. (Note: The number is shown as negative because we are using 2s compliment.) For the simple MOVs the binary values are not needed, but for the MVM statement the binary values are essential. The statement moves the binary bits from N7:3 to N7:5, but only those bits that are also on in the mask N7:4, other bits in the destination will be left untouched. Notice that the first bit N7:5/0 is true in the destination address before and after, but it is not true in the mask. The MVM function is very useful for applications where individual binary bits are to be manipulated, but they are less useful when dealing with actual number values.5.2.2 Mathematical FunctionsMathematical functions will retrieve one or more values, perform an operation andstore the result in memory. Figure 15.4 shows an ADD function that will retrieve values from N7:4 and F8:35, convert them both to the type of the destination address, add the floating point numbers, and store the result in F8:36. The function has two sources labelled source A and source B. In the case of ADD functions the sequence can change, but this is not true for other operations such as subtraction and division. A list of other simple arithmetic function follows. Some of the functions, such as the negative function are unary, so there is only one source.Figure 5.4 Arithmetic FunctionsAn application of the arithmetic function is shown in Figure 5.5. Most of theoperations provide the results we would expect. The second ADD function retrieves avalue from N7:3, adds 1 and overwrites the source - this is normally known as an increment operation. The first DIV statement divides the integer 25 by 10, the result is rounded to the nearest integer, in this case 3, and the result is stored in N7:6. The NEG instruction takes the new value of -10, not the original value of 0, from N7:4 inverts the sign and stores it in N7:7.Figure 5.5 Arithmetic Function ExampleA list of more advanced functions are given in Figure 15.6. This list includes basictrigonometry functions, exponents, logarithms and a square root function. Thelast function CPT will accept an expression and perform a complex calculation.Figure 5.6 Advanced Mathematical FunctionsFigure 5.7 shows an example where an equation has been converted to ladderlogic. The first step in the conversion is to convert the variables in the equation to unused memory locations in the PLC. The equation can then be converted using the most nested calculations in the equation, such as the LN function. In this case the results of the LN function are stored in another memory location, to be recalled later. The other operations are implemented in a similar manner. (Note: This equation could have been implemented in other forms, using fewer memory locations.)Figure 5.7 An Equation in Ladder LogicThe same equation in Figure 5.7 could have been implemented with a CPT function as shown in Figure 5.8. The equation uses the same memory locations chosen in Figure 5.7. The expression is typed directly into the PLC programmingsoftware.Figure 5.8 Calculations with a Compute FunctionMath functions can result in status flags such as overflow, carry, etc. care mustbetaken to avoid problems such as overflows. These problems are less commonwhen using floating point numbers. Integers are more prone to these problemsbecause they are limited to the range from -32768 to 32767.5.2.3 ConversionsLadder logic conversion functions are listed in Figure 5.9. The example function will retrieve a BCD number from the D type (BCD) memory and convert it to a floating point number that will be stored in F8:2. The other function will convert from 2s compliment binary to BCD, and between radians and degrees.Figure 5.9 Conversion FunctionsExamples of the conversion functions are given in Figure 5.10. The functionsload in a source value, do the conversion, and store the results. The TOD conversion to BCD could result in an overflow error.Figure 5.10 Conversion Example5.2.4 Array Data FunctionsArrays allow us to store multiple data values. In a PLC this will be a sequential series of numbers in integer, floating point, or other memory. For example, assume we are measuring and storing the weight of a bag of chips in floating point memory starting at #F8:20 (Note the ’#’ for a data file). We could read a weight value every 10 minutes, and once every hour find the average of the six weights. This section will focus on techniques that manipulate groups of data organized in arrays, also called blocks in the manuals.5.2.4.1 - StatisticsFunctions are available that allow statistical calculations. These functions arelisted in Figure 5.11. When A becomes true the average (AVE) conversion will start at memory location F8:0 and average a total of 4 values. The control word R6:1 is used to keep track of the progress of the operation, and to determine when the operation is complete. This operation, and the others, are edge triggered. The operation may require multiple scans to be completed. When the operation is done the average will be stored in F8:4 and the R6:1/DN bit will be turned on.Figure 5.11 Statistic FunctionsExamples of the statistical functions are given in Figure 5.12 for an array of data that starts at F8:0 and is 4 values long. When done the average will be stored in F8:4, and the standard deviation will be stored in F8:5. The set of values will also be sorted in ascending order from F8:0 to F8:3. Each of the function should have their own control memory to prevent overlap. It is not a good idea to activate the sort and the other calculations at the same time, as the sort may move values during the calculation, resulting in incorrect calculations.5.2.4.2 - Block OperationsA basic block function is shown in Figure 5.13. This COP (copy) function will copy an array of 10 values starting at N7:50 to N7:40. The FAL function will perform mathematical operations using an expression string, and the FSC function will allow two arrays to be compared using an expression. The FLL function will fill ablock of memory with a single value.Figure 5.13 Block Operation FunctionsFigure 5.14 shows an example of the FAL function with different addressingmodes. The first FAL function will do the following calculations N7:5=N7:0+5, N7:6=N7:1+5, N7:7=N7:2+5, N8:7=N7:3+5, N7:9=N7:4+5. The second FAL statement does not have a file ’#’ sign in front of the expression value, so the calculations will be N7:5=N7:0+5, N7:6=N7:0+5, N7:7=N7:0+5, N8:7=N7:0+5,N7:9=N7:0+5. With a mode of 2 the instruction will do two of the calculations for every scan where B is true. The result of the last FAL statement will be N7:5=N7:0+5, N7:5=N7:1+5,N7:5=N7:2+5, N7:5=N7:3+5, N7:5=N7:4+5. The last operation would seem to be useless, but notice that the mode is incremental. This mode will do one calculation for each positive transition of C. The all mode will perform all five calculations in a single scan. It is also possible to put in a number that will indicate the number of calculations per scan. The calculation time can be long for large arrays and trying to do all of the calculations in one scan may lead to a watchdog time-out fault.5.3 LOGICAL FUNCTIONS5.3.1 Comparison of ValuesComparison functions are shown in Figure 15.15. Previous function blocks were outputs, these replace input contacts. The example shows an EQU (equal) function that compares two floating point numbers. If the numbers are equal, the output bit B3:5/1 is true, otherwise it is false. Other types of equality functions are also listed.Figure 5.15 Comparison FunctionsThe example in Figure 15.16 shows the six basic comparison functions. To the right of the figure are examples of the comparison operations.Figure 5.16 Comparison Function ExamplesThe ladder logic in Figure 5.16 is recreated in Figure 5.17 with the CMP function that allows text expressions.Figure 5.17 Equivalent Statements Using CMP StatementsExpressions can also be used to do more complex comparisons, as shown in Figure 5.18. The expression will determine if F8:1 is between F8:0 and F8:2.Figure 5.18 A More Complex Comparison ExpressionThe LIM and MEQ functions are shown in Figure 5.19. The first three functions will compare a test value to high and low limits. If the high limit is above the low limit and the test value is between or equal to one limit, then it will be true. If the low limit is above the high limit then the function is only true for test values outside the range. The masked equal will compare the bits of two numbers, but only those bits that are true in the mask.Figure 5.19 Complex Comparison FunctionsFigure 5.20 shows a numberline that helps determine when the LIM function willbe true.Figure 5.20 A Number Line for the LIM FunctionFile to file comparisons are also permitted using the FSC instruction shown in Figure 5.21. The instruction uses the control word R6:0. It will interpret the expression 10 times, doing two comparisons per logic scan (the Mode is 2). The comparisons will be F8:10<F8:0, F8:11<F8:0 then F8:12<F8:0, F8:13<F8:0 then F8:14<F8:0,F8:15<F8:0 then F8:16<F8:0, F8:17<F8:0 then F8:18<F8:0,F8:19<F8:0. The function will continue until a false statement is found, or the comparison completes. If the comparison completes with no false statements the output A will then be true. The mode could have also been All to execute all the comparisons in one scan, or Increment to update when the input to the function is true - in this case the input is a plain wire, so it will always be true.Figure 5.21 File Comparison Using Expressions5.3.2 Boolean FunctionsFigure 5.22 shows Boolean algebra functions. The function shown will obtain data words from bit memory, perform an and operation, and store the results in a new location in bit memory. These functions are all oriented to word level operations. The ability to perform Boolean operations allows logical operations on more than a single bit.Figure 5.22 Boolean FunctionsThe use of the Boolean functions is shown in Figure 15.23. The first three functions require two arguments, while the last function only requires one. The AND function will only turn on bits in the result that are true in both of the source words. The OR function will turn on a bit in the result word if either of the source word bits is on. The XOR function will only turn on a bit in the result word if the bit is on in only one of the source words. The NOT function reverses all of the bits in the source word.6.PLC compared with other control systemsPLCs are well-adapted to a range of automation tasks. These are typically industrial processes in manufacturing where the cost of developing and maintaining the automation system is high relative to the total cost of the automation, and where changes to the system would be expected during its operational life. PLCs contain input and output devices compatible with industrial pilot devices and controls; little electrical design is required, and the design problem centers on expressing the desired sequence of operations. PLC applications are typically highly customized systems so the cost of a packaged PLC is low compared to the cost of a specific custom-built controller design. On the other hand, in the case of mass-produced goods, customized control systems are economic due to the lower cost of the components, which can be optimally chosen instead of a "generic" solution, and where the non-recurring engineering charges are spread over thousands or millions of units.For high volume or very simple fixed automation tasks, different techniques are used. For example, a consumer dishwasher would be controlled by an electromechanical cam timer costing only a few dollars in production quantities.。
毕业设计外文翻译模板
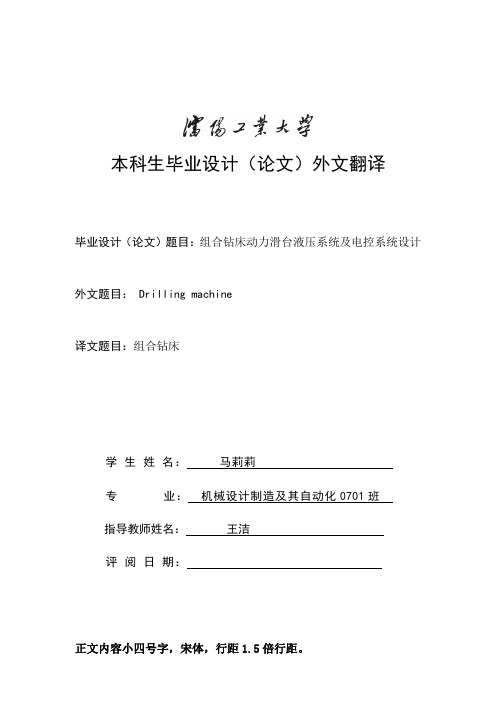
本科生毕业设计(论文)外文翻译毕业设计(论文)题目:组合钻床动力滑台液压系统及电控系统设计外文题目: Drilling machine译文题目:组合钻床学生姓名:马莉莉专业:机械设计制造及其自动化0701班指导教师姓名:王洁评阅日期:正文内容小四号字,宋体,行距1.5倍行距。
The drilling machine is a machine for making holes with removal of chips and it is used to create or enlarge holes. There are many different types of drilling machine for different jobs, but they can be basically broken down into two categories.The bench drill is used for drilling holes through raw materials such as wood, plastic and metal and gets its name because it is bolted to bench for stability so that larger pieces of work can be drilled safely. The pillar drill is a larger version that stands upright on the floor. It can do exactly the same work as the bench drill, but because of its size it can be used to drill larger pieces of materials and produce bigger holes. Most modern drilling machines are digitally automated using the latest computer numerical control (CNC) technology.Because they can be programmed to produce precise results, over and over again, CNC drilling machines are particularly useful for pattern hole drilling, small hole drilling and angled holes.If you need your drilling machine to work at high volume, a multi spindle drill head will allow you to drill many holes at the same time. These are also sometimes referred to as gang drills.Twist drills are suitable for wood, metal and plastics and can be used for both hand and machine drilling, with a drill set typically including sizes from 1mm to 14mm. A type of drill machine known as the turret stores tools in the turret and positions them in the order needed for work.Drilling machines, which can also be referred to as bench mounted drills or floor standing drills are fixed style of drills that may be mounted on a stand or bolted to the floor or workbench. A drilling machine consists of a base, column, table, spindle), and drill head, usually driven by an induction motor.The head typically has a set of three which radiate from a central hub that, when turned, move the spindle and chuck vertically, parallel to the axis of the column. The table can be adjusted vertically and is generally moved by a rack and pinion. Some older models do however rely on the operator to lift and re clamp the table in position. The table may also be offset from the spindles axis and in some cases rotated to a position perpendicular to the column.The size of a drill press is typically measured in terms of swing which can be is defined as twice the throat distance, which is the distance from the centre of the spindle to the closest edge of the pillar. Speed change on these drilling machines is achieved by manually moving a belt across a stepped pulley arrangement.Some drills add a third stepped pulley to increase the speed range. Moderndrilling machines can, however, use a variable-speed motor in conjunction with the stepped-pulley system. Some machine shop drilling machines are equipped with a continuously variable transmission, giving a wide speed range, as well as the ability to change speed while the machine is running.Machine drilling has a number of advantages over a hand-held drill. Firstly, it requires much less to apply the drill to the work piece. The movement of the chuck and spindle is by a lever working on a rack and pinion, which gives the operator considerable mechanical advantage.The use of a table also allows a vice or clamp to be used to position and restrain the work. This makes the operation much more secure. In addition to this, the angle of the spindle is fixed relative to the table, allowing holes to be drilled accurately and repetitively.Most modern drilling machines are digitally automated using the latest computer numerical control (CNC) technology. Because they can be programmed to produce precise results, over and over again, CNC drilling machines are particularly useful for pattern hole drilling, small hole drilling and angled holes.Drilling machines are often used for miscellaneous workshop tasks such as sanding, honing or polishing, by mounting sanding drums, honing wheels and various other rotating accessories in the chuck. To add your products click on the traders account link above.You can click on the links below to browse for new, used or to hire a drilling machine.Drilling machines are used for drilling, boring, countersinking, reaming, and tapping. Several types are used in metalworking: vertical drilling machines, horizontal drilling machines, center-drilling machines, gang drilling machines, multiple-spindle drilling machines, and special-purpose drilling machines.Vertical drilling machines are the most widely used in metalworking. They are used to make holes in relatively small work-pieces in individual and small-lot production; they are also used in maintenance shops. The tool, such as a drill, countersink, or reamer, is fastened on a vertical spindle, and the work-piece is secured on the table of the machine. The axes of the tool and the hole to be drilled are aligned by moving the workpiece. Programmed control is also used to orient the workpiece and to automate the operation. Bench-mounted machines, usually of the single-spindle type, are used to make holes up to 12 mm in diameter, for instance, in instrument-making.Heavy and large workpieces and workpieces with holes located along a curved edge are worked on radial drilling machines. Here the axes of the tool and the hole to be drilled are aligned by moving the spindle relative to the stationary work-piece.Horizontal drilling machines are usually used to make deep holes, for instance, in axles, shafts, and gun barrels for firearms and artillery pieces.Center-drilling machines are used to drill centers in the ends of blanks. They are sometimes equipped with supports that can cut off the blank before centering, and in such cases they are called center-drilling machines. Gang drilling machines with more than one drill head are used to produce several holes at one time. Multiple-spindle drilling machines feature automation of the work process. Such machines can be assembled from several standardized, self-contained heads with electric motors and reduction gears that rotate the spindle and feed the head. There are one-, two-, and three-sidedmultiple-spindle drilling machines with vertical, horizontal, and inclined spindles for drilling and tapping. Several dozen such spindles may be mounted on a single machine. Special-purpose drilling machines, on which a limited range of operations is performed, are equipped with various automated devices.Multiple operations on workpieces are performed by various combination machines. These include one- and two-sided jig boring machines,drilling-tapping machines (usually gang drilling machines with reversible thread-cutting spindles), milling-type drilling machines and drilling-mortising machines used mainly for woodworking, and automatic drilling machines.In woodworking much use is made of single- and multiple-spindle vertical drilling machines, one- and two-sided, horizontal drilling machines (usually with multiple spindles), and machines equipped with a swivel spindle that can be positioned vertically and horizontally. In addition to drilling holes, woodworking machines may be used to make grooves, recesses, and mortises and to remove knots.英文翻译指导教师评阅意见。
毕业设计中英文翻译
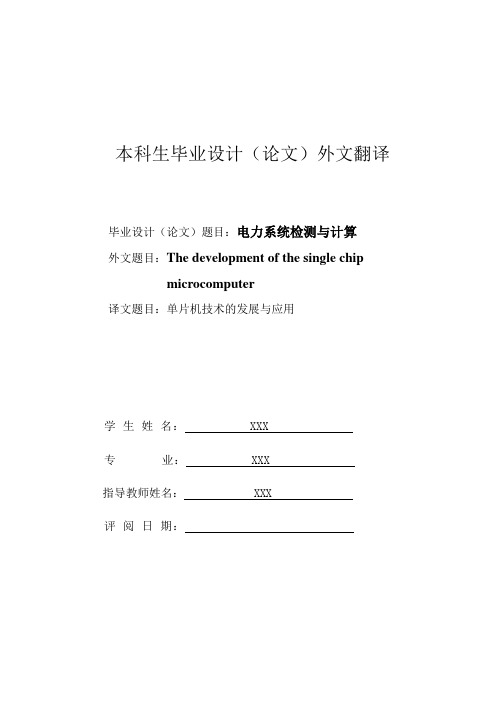
本科生毕业设计(论文)外文翻译毕业设计(论文)题目:电力系统检测与计算外文题目:The development of the single chipmicrocomputer译文题目:单片机技术的发展与应用学生姓名: XXX专业: XXX指导教师姓名: XXX评阅日期:单片机技术的发展与应用从无线电世界到单片机世界现代计算机技术的产业革命,将世界经济从资本经济带入到知识经济时代。
在电子世界领域,从 20 世纪中的无线电时代也进入到 21 世纪以计算机技术为中心的智能化现代电子系统时代。
现代电子系统的基本核心是嵌入式计算机系统(简称嵌入式系统),而单片机是最典型、最广泛、最普及的嵌入式系统。
一、无线电世界造就了几代英才。
在 20 世纪五六十年代,最具代表的先进的电子技术就是无线电技术,包括无线电广播,收音,无线通信(电报),业余无线电台,无线电定位,导航等遥测、遥控、遥信技术。
早期就是这些电子技术带领着许多青少年步入了奇妙的电子世界,无线电技术展示了当时科技生活美妙的前景。
电子科学开始形成了一门新兴学科。
无线电电子学,无线通信开始了电子世界的历程。
无线电技术不仅成为了当时先进科学技术的代表,而且从普及到专业的科学领域,吸引了广大青少年,并使他们从中找到了无穷的乐趣。
从床头的矿石收音机到超外差收音机;从无线电发报到业余无线电台;从电话,电铃到无线电操纵模型。
无线电技术成为当时青少年科普、科技教育最普及,最广泛的内容。
至今,许多老一辈的工程师、专家、教授当年都是无线电爱好者。
无线电技术的无穷乐趣,无线电技术的全面训练,从电子学基本原理,电子元器件基础到无线电遥控、遥测、遥信电子系统制作,培养出了几代科技英才。
二、从无线电时代到电子技术普及时代。
早期的无线电技术推动了电子技术的发展,其中最主要的是真空管电子技术向半导体电子技术的发展。
半导体电子技术使有源器件实现了微小型化和低成本,使无线电技术有了更大普及和创新,并大大地开阔了许多非无线电的控制领域。
毕业设计中英文翻译
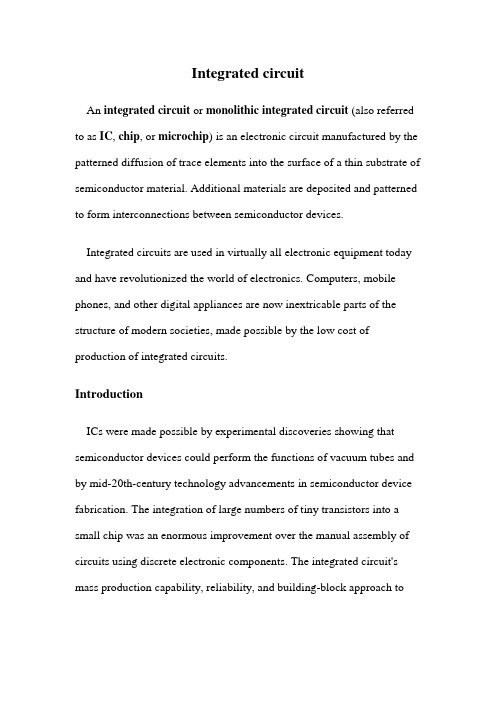
Integrated circuitAn integrated circuit or monolithic integrated circuit (also referred to as IC, chip, or microchip) is an electronic circuit manufactured by the patterned diffusion of trace elements into the surface of a thin substrate of semiconductor material. Additional materials are deposited and patterned to form interconnections between semiconductor devices.Integrated circuits are used in virtually all electronic equipment today and have revolutionized the world of electronics. Computers, mobile phones, and other digital appliances are now inextricable parts of the structure of modern societies, made possible by the low cost of production of integrated circuits.IntroductionICs were made possible by experimental discoveries showing that semiconductor devices could perform the functions of vacuum tubes and by mid-20th-century technology advancements in semiconductor device fabrication. The integration of large numbers of tiny transistors into a small chip was an enormous improvement over the manual assembly of circuits using discrete electronic components. The integrated circuit's mass production capability, reliability, and building-block approach tocircuit design ensured the rapid adoption of standardized ICs in place of designs using discrete transistors.There are two main advantages of ICs over discrete circuits: cost and performance. Cost is low because the chips, with all their components, are printed as a unit by photolithography rather than being constructed one transistor at a time. Furthermore, much less material is used to construct a packaged IC than to construct a discrete circuit. Performance is high because the components switch quickly and consume little power (compared to their discrete counterparts) as a result of the small size and close proximity of the components. As of 2006, typical chip areas range from a few square millimeters to around 350 mm2, with up to 1 million transistors per mm2.TerminologyIntegrated circuit originally referred to a miniaturized electronic circuit consisting of semiconductor devices, as well as passive components bonded to a substrate or circuit board.[1] This configuration is now commonly referred to as a hybrid integrated circuit. Integrated circuit has since come to refer to the single-piece circuit construction originally known as a monolithic integrated circuit.[2]InventionEarly developments of the integrated circuit go back to 1949, when the German engineer Werner Jacobi (Siemens AG) filed a patent for an integrated-circuit-like semiconductor amplifying device showing five transistors on a common substrate arranged in a 2-stage amplifier arrangement. Jacobi disclosed small and cheap hearing aids as typical industrial applications of his patent. A commercial use of his patent has not been reported.The idea of the integrated circuit was conceived by a radar scientist working for the Royal Radar Establishment of the British Ministry of Defence, Geoffrey W.A. Dummer (1909–2002). Dummer presented the idea to the public at the Symposium on Progress in Quality Electronic Components in Washington, D.C. on May 7, 1952.[4] He gave many sympodia publicly to propagate his ideas, and unsuccessfully attempted to build such a circuit in 1956.A precursor idea to the IC was to create small ceramic squares (wafers), each one containing a single miniaturized component. Components could then be integrated and wired into a tridimensional or tridimensional compact grid. This idea, which looked very promising in 1957, was proposed to the US Army by Jack Kilby, and led to the short-lived Micro module Program. However, as the project was gaining momentum, Jack Kilby came up with a new, revolutionary design: the IC.Newly employed by Texas Instruments, Jack Kilby recorded his initial ideas concerning the integrated circuit in July 1958, successfully demonstrating the first working integrated example on September 12, 1958.In his patent application of February 6, 1959, Jack Kilby described his new device as ―a body of semiconductor material ... wherein all the components of the electronic circuit are completely integrated.‖Jack Kilby won the 2000 Nobel Prize in Physics for his part of the invention of the integrated circuit.Jack Kilby's work was named an IEEE Milestone in 2009.Noyce also came up with his own idea of an integrated circuit half a year later than Jack Kilby. His chip solved many practical problems that Jack Kilby's had not. Produced at Fairchild Semiconductor, it was made of silicon, whereas Jack Kilby chip was made of germanium. GenerationsIn the early days of integrated circuits, only a few transistors could be placed on a chip, as the scale used was large because of the contemporary technology, and manufacturing yields were low by today's standards. As the degree of integration was small, the design was done easily. Over time, millions, and today billions of transistors could be placed on one chip, and to make a good design became a task to be planned thoroughly. This gave rise to new design methods.SSI, MSI and LSIThe first integrated circuits contained only a few transistors. Called "small-scale integration" (SSI), digital circuits containing transistors numbering in the tens for example, while early linear ICs such as the Plessey SL201 or the Philips TAA320 had as few as two transistors. The term Large Scale Integration was first used by IBM scientist Rolf Landauer when describing the theoretical concept, from there came the terms for SSI, MSI, VLSI, and ULSI.SSI circuits were crucial to early aerospace projects, and aerospace projects helped inspire development of the technology. Both the Minuteman missile and Apollo program needed lightweight digital computers for their inertial guidance systems; the Apollo guidance computer led and motivated the integrated-circuit technology,while the Minuteman missile forced it into mass-production. The Minuteman missile program and various other Navy programs accounted for the total $4 million integrated circuit market in 1962, and by 1968, U.S. Government space and defense spending still accounted for 37% of the $312 million total production. The demand by the U.S. Government supported the nascent integrated circuit market until costs fell enough to allow firms to penetrate the industrial and eventually the consumer markets. The average price per integrated circuit dropped from $50.00 in1962 to $2.33 in 1968.[13] Integrated circuits began to appear in consumer products by the turn of the decade, a typical application being FMinter-carrier sound processing in television receivers.The next step in the development of integrated circuits, taken in the late 1960s, introduced devices which contained hundreds of transistors on each chip, called "medium-scale integration" (MSI).They were attractive economically because while they cost little more to produce than SSI devices, they allowed more complex systems to be produced using smaller circuit boards, less assembly work (because of fewer separate components), and a number of other advantages.Further development, driven by the same economic factors, led to "large-scale integration" (LSI) in the mid 1970s, with tens of thousands of transistors per chip.Integrated circuits such as 1K-bit RAMs, calculator chips, and the first microprocessors, that began to be manufactured in moderate quantities in the early 1970s, had under 4000 transistors. True LSI circuits, approaching 10,000 transistors, began to be produced around 1974, for computer main memories and second-generation microprocessors.VLSIThe final step in the development process, starting in the 1980s and continuing through the present, was "very large-scale integration" (VLSI). The development started with hundreds of thousands of transistors in the early 1980s, and continues beyond several billion transistors as of 2009. Multiple developments were required to achieve this increased density. Manufacturers moved to smaller design rules and cleaner fabrication facilities, so that they could make chips with more transistors and maintain adequate yield. The path of process improvements was summarized by the International Technology Roadmap for Semiconductors (ITRS). Design tools improved enough to make it practical to finish these designs in a reasonable time. The more energy efficient CMOS replaced NMOS and PMOS, avoiding a prohibitive increase in power consumption. Better texts such as the landmark textbook by Mead and Conway helped schools educate more designers, among other factors.In 1986 the first one megabit RAM chips were introduced, which contained more than one million transistors. Microprocessor chips passed the million transistor mark in 1989 and the billion transistor mark in 2005.[14] The trend continues largely unabated, with chips introduced in 2007 containing tens of billions of memory transistors.[15]ULSI, WSI, SOC and 3D-ICTo reflect further growth of the complexity, the term ULSI that stands for "ultra-large-scale integration" was proposed for chips of complexityof more than 1 million transistors.Wafer-scale integration (WSI) is a system of building very-large integrated circuits that uses an entire silicon wafer to produce a single "super-chip". Through a combination of large size and reduced packaging, WSI could lead to dramatically reduced costs for some systems, notably massively parallel supercomputers. The name is taken from the term Very-Large-Scale Integration, the current state of the art when WSI was being developed.A system-on-a-chip (SoC or SOC) is an integrated circuit in which all the components needed for a computer or other system are included on a single chip. The design of such a device can be complex and costly, and building disparate components on a single piece of silicon may compromise the efficiency of some elements. However, these drawbacks are offset by lower manufacturing and assembly costs and by a greatly reduced power budget: because signals among the components are kept on-die, much less power is required (see Packaging).A three-dimensional integrated circuit (3D-IC) has two or more layers of active electronic components that are integrated both vertically and horizontally into a single circuit. Communication between layers useson-die signaling, so power consumption is much lower than in equivalent separate circuits. Judicious use of short vertical wires can substantially reduce overall wire length for faster operation.Advances in integrated circuitsAmong the most advanced integrated circuits are the microprocessors or "cores", which control everything from computers and cellular phones to digital microwave ovens. Digital memory chips and ASICs are examples of other families of integrated circuits that are important to the modern information society. While the cost of designing and developing a complex integrated circuit is quite high, when spread across typically millions of production units the individual IC cost is minimized. The performance of ICs is high because the small size allows short traces which in turn allows low power logic (such as CMOS) to be used at fast switching speeds.ICs have consistently migrated to smaller feature sizes over the years, allowing more circuitry to be packed on each chip. This increased capacity per unit area can be used to decrease cost and/or increase functionality—see Moore's law which, in its modern interpretation, states that the number of transistors in an integrated circuit doubles every two years. In general, as the feature size shrinks, almost everything improves—the cost per unit and the switching power consumption godown, and the speed goes up. However, ICs with nanometer-scale devices are not without their problems, principal among which is leakage current (see subthreshold leakage for a discussion of this), although these problems are not insurmountable and will likely be solved or at least ameliorated by the introduction of high-k dielectrics. Since these speed and power consumption gains are apparent to the end user, there is fierce competition among the manufacturers to use finer geometries. This process, and the expected progress over the next few years, is well described by the International Technology Roadmap for Semiconductors (ITRS).In current research projects, integrated circuits are also developed for sensoric applications in medical implants or other bioelectronic devices. Particular sealing strategies have to be taken in such biogenic environments to avoid corrosion or biodegradation of the exposed semiconductor materials.[16] As one of the few materials well established in CMOS technology, titanium nitride (TiN) turned out as exceptionally stable and well suited for electrode applications in medical implants.[17][18] ClassificationIntegrated circuits can be classified into analog, digital and mixed signal (both analog and digital on the same chip).Digital integrated circuits can contain anything from one to millions of logic gates, flip-flops, multiplexers, and other circuits in a few square millimeters. The small size of these circuits allows high speed, low power dissipation, and reduced manufacturing cost compared with board-level integration. These digital ICs, typically microprocessors, DSPs, and micro controllers, work using binary mathematics to process "one" and "zero" signals.Analog ICs, such as sensors, power management circuits, and operational amplifiers, work by processing continuous signals. They perform functions like amplification, active filtering, demodulation, and mixing. Analog ICs ease the burden on circuit designers by having expertly designed analog circuits available instead of designing a difficult analog circuit from scratch.ICs can also combine analog and digital circuits on a single chip to create functions such as A/D converters and D/A converters. Such circuits offer smaller size and lower cost, but must carefully account for signal interference.ManufacturingFabricationRendering of a small standard cell with three metal layers (dielectric has been removed). The sand-colored structures are metal interconnect, with the vertical pillars being contacts, typically plugs of tungsten. The reddish structures are poly-silicon gates, and the solid at the bottom is the crystalline silicon bulk.Schematic structure of a CMOS chip, as built in the early 2000s. The graphic shows LDD-Misfit's on an SOI substrate with five materialization layers and solder bump for flip-chip bonding. It also shows the section for FEOL (front-end of line), BEOL (back-end of line) and first parts of back-end process.The semiconductors of the periodic table of the chemical elements were identified as the most likely materials for a solid-state vacuum tube. Starting with copper oxide, proceeding to germanium, then silicon, the materials were systematically studied in the 1940s and 1950s. Today, silicon monocrystals are the main substrate used for ICs although someIII-V compounds of the periodic table such as gallium arsenide are used for specialized applications like LEDs, lasers, solar cells and the highest-speed integrated circuits. It took decades to perfect methods of creating crystals without defects in the crystalline structure of the semiconducting material.Semiconductor ICs are fabricated in a layer process which includes these key process steps:∙Imaging∙Deposition∙EtchingThe main process steps are supplemented by doping and cleaning.∙Integrated circuits are composed of many overlapping layers, each defined by photolithography, and normally shown in different colors.Some layers mark where various dopants are diffused into thesubstrate (called diffusion layers), some define where additional ions are implanted (implant layers), some define the conductors(poly-silicon or metal layers), and some define the connectionsbetween the conducting layers (via or contact layers). All components are constructed from a specific combination of these layers.∙In a self-aligned CMOS process, a transistor is formed wherever the gate layer (poly-silicon or metal) crosses a diffusion layer.∙Capacitive structures, in form very much like the parallel conducting plates of a traditional electrical capacitor, are formedaccording to the area of the "plates", with insulating material between the plates. Capacitors of a wide range of sizes are common on ICs.∙Meandering stripes of varying lengths are sometimes used to form on-chip resistors, though most logic circuits do not need any resistors.The ratio of the length of the resistive structure to its width, combined with its sheet resistivity, determines the resistance.∙More rarely, inductive structures can be built as tiny on-chip coils, or simulated by gyrators.Since a CMOS device only draws current on the transition between logic states, CMOS devices consume much less current than bipolar devices.A random access memory is the most regular type of integrated circuit; the highest density devices are thus memories; but even a microprocessor will have memory on the chip. (See the regular array structure at the bottom of the first image.) Although the structures are intricate – with widths which have been shrinking for decades – the layers remain much thinner than the device widths. The layers of material are fabricated much like a photographic process, although light waves in the visible spectrum cannot be used to "expose" a layer of material, as they would be too large for the features. Thus photons of higher frequencies (typically ultraviolet) are used to create the patterns for each layer. Because each feature is so small, electron microscopes are essential tools for a process engineer who might be debugging a fabrication process.Each device is tested before packaging using automated test equipment (ATE), in a process known as wafer testing, or wafer probing. The wafer is then cut into rectangular blocks, each of which is called a die. Each good die (plural dice, dies, or die) is then connected into a package using aluminum (or gold) bond wires which are welded and/or thermosonic bonded to pads, usually found around the edge of the die. After packaging, the devices go through final testing on the same or similar ATE used during wafer probing. Industrial CT scanning can also be used. Test cost can account for over 25% of the cost of fabrication on lower cost products, but can be negligible on low yielding, larger, and/or higher cost devices.As of 2005, a fabrication facility (commonly known as a semiconductor fab) costs over $1 billion to construct,[19] because much of the operation is automated. Today, the most advanced processes employ the following techniques:∙The wafers are up to 300 mm in diameter (wider than a common dinner plate).∙Use of 32 nanometer or smaller chip manufacturing process. Intel, IBM, NEC, and AMD are using ~32 nanometers for their CPU chips.IBM and AMD introduced immersion lithography for their 45 nmprocesses[20]∙Copper interconnects where copper wiring replaces aluminium for interconnects.∙Low-K dielectric insulators.∙Silicon on insulator (SOI)∙Strained silicon in a process used by IBM known as strained silicon directly on insulator (SSDOI)∙Multigate devices such as trin-gate transistors being manufactured by Intel from 2011 in their 22 nim process.PackagingIn the late 1990s, plastic quad flat pack (PQFP) and thin small-outline package (TSOP) packages became the most common for high pin count devices, though PGA packages are still often used for high-end microprocessors. Intel and AMD are currently transitioning from PGA packages on high-end microprocessors to land grid array (LGA) packages.Ball grid array (BGA) packages have existed since the 1970s. Flip-chip Ball Grid Array packages, which allow for much higher pin count than other package types, were developed in the 1990s. In an FCBGA package the die is mounted upside-down (flipped) and connects to the packageballs via a package substrate that is similar to a printed-circuit board rather than by wires. FCBGA packages allow an array of input-output signals (called Area-I/O) to be distributed over the entire die rather than being confined to the die periphery.Traces out of the die, through the package, and into the printed circuit board have very different electrical properties, compared to on-chip signals. They require special design techniques and need much more electric power than signals confined to the chip itself.When multiple dies are put in one package, it is called SiP, for System In Package. When multiple dies are combined on a small substrate, often ceramic, it's called an MCM, or Multi-Chip Module. The boundary between a big MCM and a small printed circuit board is sometimes fuzzy. Chip labeling and manufacture dateMost integrated circuits large enough to include identifying information include four common sections: the manufacturer's name or logo, the part number, a part production batch number and/or serial number, and a four-digit code that identifies when the chip was manufactured. Extremely small surface mount technology parts often bear only a number used in a manufacturer's lookup table to find the chip characteristics.The manufacturing date is commonly represented as a two-digit year followed by a two-digit week code, such that a part bearing the code 8341 was manufactured in week 41 of 1983, or approximately in October 1983. Legal protection of semiconductor chip layoutsLike most of the other forms of intellectual property, IC layout designs are creations of the human mind. They are usually the result of an enormous investment, both in terms of the time of highly qualified experts, and financially. There is a continuing need for the creation of new layout-designs which reduce the dimensions of existing integrated circuits and simultaneously increase their functions. The smaller an integrated circuit, the less the material needed for its manufacture, and the smaller the space needed to accommodate it. Integrated circuits are utilized in a large range of products, including articles of everyday use, such as watches, television sets, washing machines, automobiles, etc., as well as sophisticated data processing equipment.The possibility of copying by photographing each layer of an integrated circuit and preparing photomasks for its production on the basis of the photographs obtained is the main reason for the introduction of legislation for the protection of layout-designs.A diplomatic conference was held at Washington, D.C., in 1989, which adopted a Treaty on Intellectual Property in Respect of Integrated Circuits (IPIC Treaty). The Treaty on Intellectual Property in respect of Integrated Circuits, also called Washington Treaty or IPIC Treaty (signed at Washington on May 26, 1989) is currently not in force, but was partially integrated into the TRIPs agreement.National laws protecting IC layout designs have been adopted in a number of countries.Other developmentsIn the 1980s, programmable logic devices were developed. These devices contain circuits whose logical function and connectivity can be programmed by the user, rather than being fixed by the integrated circuit manufacturer. This allows a single chip to be programmed to implement different LSI-type functions such as logic gates, adders and registers. Current devices called field-programmable gate arrays can now implement tens of thousands of LSI circuits in parallel and operate up to 1.5 GHz (Anachronism holding the speed record).The techniques perfected by the integrated circuits industry over the last three decades have been used to create very small mechanical devices driven by electricity using a technology known asmicroelectromechanical systems. These devices are used in a variety of commercial and military applications. Example commercial applications include DLP projectors, inkjet printers, and accelerometers used to deploy automobile airbags.In the past, radios could not be fabricated in the same low-cost processes as microprocessors. But since 1998, a large number of radio chips have been developed using CMOS processes. Examples include Intel's DECT cordless phone, or Atheros's 802.11 card.Future developments seem to follow the multi-coremulti-microprocessor paradigm, already used by the Intel and AMD dual-core processors. Intel recently unveiled a prototype, "not for commercial sale" chip that bears 80 microprocessors. Each core is capable of handling its own task independently of the others. This is in response to the heat-versus-speed limit that is about to be reached using existing transistor technology. This design provides a new challenge to chip programming. Parallel programming languages such as theopen-source X10 programming language are designed to assist with this task.集成电路集成电路或单片集成电子电路(也称为IC、集成电路片或微型集成电路片)是一种电子电路制作的图案扩散微量元素分析在基体表面形成一层薄的半导体材料。
毕业设计中英文翻译

Bridge Waterway OpeningsIn a majority of cases the height and length of a bridge depend solely upon the amount of clear waterway opening that must be provided to accommodate the floodwaters of the stream. Actually, the problem goes beyond that of merely accommodating the floodwaters and requires prediction of the various magnitudes of floods for given time intervals. It would be impossible to state that some given magnitude is the maximum that will ever occur, and it is therefore impossible to design for the maximum, since it cannot be ascertained. It seems more logical to design for a predicted flood of some selected interval ---a flood magnitude that could reasonably be expected to occur once within a given number of years. For example, a bridge may be designed for a 50-year flood interval; that is, for a flood which is expected (according to the laws of probability) to occur on the average of one time in 50 years. Once this design flood frequency, or interval of expected occurrence, has been decided, the analysis to determine a magnitude is made. Whenever possible, this analysis is based upon gauged stream records. In areas and for streams where flood frequency and magnitude records are not available, an analysis can still be made. With data from gauged streams in the vicinity, regional flood frequencies can be worked out; with a correlation between the computed discharge for the ungauged stream and the regional flood frequency, a flood frequency curve can be computed for the stream in question. Highway CulvertsAny closed conduit used to conduct surface runoff from one side of a roadway to the other is referred to as a culvert. Culverts vary in size from large multiple installations used in lieu of a bridge to small circular or elliptical pipe, and their design varies in significance. Accepted practice treats conduits under the roadway as culverts. Although the unit cost of culverts is much less than that of bridges, they are far more numerous, normally averaging about eight to the mile, and represent a greater cost in highway. Statistics show that about 15 cents of the highway construction dollar goes to culverts, as compared with 10 cents for bridge. Culvert design then is equally as important as that of bridges or other phases of highway and should be treated accordingly.Municipal Storm DrainageIn urban and suburban areas, runoff waters are handled through a system of drainage structures referred to as storm sewers and their appurtenances. The drainage problem is increased in these areas primarily for two reasons: the impervious nature of the area creates a very high runoff; and there is little room for natural water courses. It is often necessary to collect the entire storm water into a system of pipes and transmit it over considerable distances before it can be loosed again as surface runoff. This collection and transmission further increase the problem, since all of the water must be collected with virtually no ponding, thus eliminating any natural storage; and though increased velocity the peak runoffs are reached more quickly. Also, the shorter times of peaks cause the system to be more sensitive to short-duration, high-intensity rainfall. Storm sewers, like culverts and bridges, are designed for storms of various intensity –return-period relationship, depending upon the economy and amount of ponding that can be tolerated.Airport DrainageThe problem of providing proper drainage facilities for airports is similar in many ways to that of highways and streets. However, because of the large and relatively flat surface involved the varying soil conditions, the absence of natural water courses and possible side ditches, and the greater concentration of discharge at the terminus of the construction area, some phases of the problem are more complex. For the average airport the overall area to be drained is relatively large and an extensive drainage system is required. The magnitude of such a system makes it even more imperative that sound engineeringprinciples based on all of the best available data be used to ensure the most economical design. Overdesign of facilities results in excessive money investment with no return, and underdesign can result in conditions hazardous to the air traffic using the airport.In other to ensure surfaces that are smooth, firm, stable, and reasonably free from flooding, it is necessary to provide a system which will do several things. It must collect and remove the surface water from the airport surface; intercept and remove surface water flowing toward the airport from adjacent areas; collect and remove any excessive subsurface water beneath the surface of the airport facilities and in many cases lower the ground-water table; and provide protection against erosion of the sloping areas. Ditches and Cut-slope DrainageA highway cross section normally includes one and often two ditches paralleling the roadway. Generally referred to as side ditches these serve to intercept the drainage from slopes and to conduct it to where it can be carried under the roadway or away from the highway section, depending upon the natural drainage. To a limited extent they also serve to conduct subsurface drainage from beneath the roadway to points where it can be carried away from the highway section.A second type of ditch, generally referred to as a crown ditch, is often used for the erosion protection of cut slopes. This ditch along the top of the cut slope serves to intercept surface runoff from the slopes above and conduct it to natural water courses on milder slopes, thus preventing the erosion that would be caused by permitting the runoff to spill down the cut faces.12 Construction techniquesThe decision of how a bridge should be built depends mainly on local conditions. These include cost of materials, available equipment, allowable construction time and environmental restriction. Since all these vary with location and time, the best construction technique for a given structure may also vary. Incremental launching or Push-out MethodIn this form of construction the deck is pushed across the span with hydraulic rams or winches. Decks of prestressed post-tensioned precast segments, steel or girders have been erected. Usually spans are limited to 50~60 m to avoid excessive deflection and cantilever stresses , although greater distances have been bridged by installing temporary support towers . Typically the method is most appropriate for long, multi-span bridges in the range 300 ~ 600 m ,but ,much shorter and longer bridges have been constructed . Unfortunately, this very economical mode of construction can only be applied when both the horizontal and vertical alignments of the deck are perfectly straight, or alternatively of constant radius. Where pushing involves a small downward grade (4% ~ 5%) then a braking system should be installed to prevent the deck slipping away uncontrolled and heavy bracing is then needed at the restraining piers.Bridge launching demands very careful surveying and setting out with continuous and precise checks made of deck deflections. A light aluminum or steel-launching nose forms the head of the deck to provide guidance over the pier. Special teflon or chrome-nickel steel plate bearings are used to reduce sliding friction to about 5% of the weight, thus slender piers would normally be supplemented with braced columns to avoid cracking and other damage. These columns would generally also support the temporary friction bearings and help steer the nose.In the case of precast construction, ideally segments should be cast on beds near the abutments and transferred by rail to the post-tensioning bed, the actual transport distance obviously being kept to the minimum. Usually a segment is cast against the face of the previously concerted unit to ensure a good fit when finally glued in place with an epoxy resin. If this procedure is not adopted , gaps of approximately 500mm shold be left between segments with the reinforcements running through andstressed together to form a complete unit , but when access or space on the embankment is at a premium it may be necessary to launch the deck intermittently to allow sections to be added progressively .The correponding prestressing arrangements , both for the temporary and permanent conditions would be more complicated and careful calculations needed at all positions .The pricipal advantage of the bridge-launching technique is the saving in falsework, especially for high decks. Segments can also be fabricated or precast in a protected environment using highly productive equipment. For concrete segment, typically two segment are laid each week (usually 10 ~ 30 m in length and perhaps 300 to 400 tonnes in weight) and after posttensioning incrementally launched at about 20 m per day depending upon the winching/jacking equipment.Balanced Cantiulever ConstructionDevelopment in box section and prestressed concrete led to short segment being assembled or cast in place on falsework to form a beam of full roadway width. Subsequently the method was refined virtually to eliminate the falsework by using a previously constructed section of the beam to provide the fixing for a subsequently cantilevered section. The principle is demonsrated step-by-step in the example shown in Fig.1.In the simple case illustrated, the bridge consists of three spans in the ratio 1:1:2. First the abutments and piers are constructed independently from the bridge superstructure. The segment immediately above each pier is then either cast in situ or placed as a precast unit .The deck is subsequently formed by adding sections symmetrically either side.Ideally sections either side should be placed simultaneously but this is usually impracticable and some inbalance will result from the extra segment weight, wind forces, construction plant and material. When the cantilever has reached both the abutment and centre span,work can begin from the other pier , and the remainder of the deck completed in a similar manner . Finally the two individual cantilevers are linked at the centre by a key segment to form a single span. The key is normally cast in situ.The procedure initially requires the first sections above the column and perhaps one or two each side to be erected conventionally either in situ concrete or precast and temporarily supported while steel tendons are threaded and post-tensioned . Subsequent pairs of section are added and held in place by post-tensioning followed by grouting of the ducts. During this phase only the cantilever tendons in the upper flange and webs are tensioned. Continuity tendons are stressed after the key section has been cast in place. The final gap left between the two half spans should be wide enough to enable the jacking equipment to be inserted. When the individual cantilevers are completed and the key section inserted the continuity tendons are anchored symmetrically about the centre of the span and serve to resist superimposed loads, live loads, redistribution of dead loads and cantilever prestressing forces.The earlier bridges were designed on the free cantilever principle with an expansion joint incorporated at the center .Unfortunately,settlements , deformations , concrete creep and prestress relaxation tended to produce deflection in each half span , disfiguring the general appearance of the bridge and causing discomfort to drivers .These effects coupled with the difficulties in designing a suitable joint led designers to choose a continuous connection, resulting in a more uniform distribution of the loads and reduced deflection. The natural movements were provided for at the bridge abutments using sliding bearings or in the case of long multi-span bridges, joints at about 500 m centres.Special Requirements in Advanced Construction TechniquesThere are three important areas that the engineering and construction team has to consider:(1) Stress analysis during construction: Because the loadings and support conditions of the bridge are different from the finished bridge, stresses in each construction stage must be calculated to ensurethe safety of the structure .For this purpose, realistic construction loads must be used and site personnel must be informed on all the loading limitations. Wind and temperature are usually significant for construction stage.(2) Camber: In order to obtain a bridge with the right elevation, the required camber of the bridge at each construction stage must be calculated. It is required that due consideration be given to creep and shrinkage of the concrete. This kind of the concrete. This kind of calculation, although cumbersome, has been simplified by the use of the compiters.(3) Quality control: This is important for any method construction, but it is more so for the complicated construction techniques. Curing of concrete, post-tensioning, joint preparation, etc. are detrimental to a successful structure. The site personnel must be made aware of the minimum concrete strengths required for post-tensioning, form removal, falsework removal, launching and other steps of operations.Generally speaking, these advanced construction techniques require more engineering work than the conventional falsework type construction, but the saving could be significant.大桥涵洞在大多数情况中桥梁的高度和跨度完全取决于河流的流量,桥梁的高度和跨度必须能够容纳最大洪水量.事实上,这不仅仅是洪水最大流量的问题,还需要在不同时间间隔预测不同程度的水灾。
- 1、下载文档前请自行甄别文档内容的完整性,平台不提供额外的编辑、内容补充、找答案等附加服务。
- 2、"仅部分预览"的文档,不可在线预览部分如存在完整性等问题,可反馈申请退款(可完整预览的文档不适用该条件!)。
- 3、如文档侵犯您的权益,请联系客服反馈,我们会尽快为您处理(人工客服工作时间:9:00-18:30)。
毕业设计(论文)外文资料
原文及译文
专业计算机科学与技术班级05104000
学号0510400000
姓名学生姓名
指导教师教师姓名
原文出处:建议按照参考文献的格式填写到此处。
原文标题
原文作者
[原文一般应是一篇文章或书中连续的内容,不能挑着译。
原文给出译文部分的原文即可。
]
译文:
译文标题
原文作者
[译文写在此处]
[译文5页左右即可。
图、表、程序代码等一般可不译,译文中可略去。
]
[如译文篇幅不足,可将原文、译文部分重复1~2次(注意页眉),翻译2~3篇文献。
] 指导教师意见:
指导教师:
年月日。