CRH车轮磨耗分析
铁道机车车辆轮轨的摩擦磨损与节能降耗情况分析

铁道机车车辆轮轨的摩擦磨损与节能降耗情况分析在铁路运输过程中,机车车轮与铁轨之间产生的制动力和牵引力导致二者之间存在巨大的摩擦力,长时间的摩擦会导致轮毂及铁轨的寿命大大降低,车辆的牵引力及制动力下降,对列车的运行稳定性十分不利。
因此,在平时列车运营的过程中需要加强对车辆轮毂及铁轨的维护,采取有效方法减少轮毂的磨损,降低车辆能耗,为铁路行业创造更多收益。
1 铁道机车车辆轮轨的摩擦磨损情况分析铁路机车车辆的磨损是目前影响铁道机车使用寿命的关键因素之一。
列车行驶的过程中,由于列车轮毂与铁轨之间产生较大的牵引力和制动力,导致车轮轮毂造成较大的磨损,从而增加了铁路部门对铁路及机车的运营维护费用。
据有关部门统计,我国目前的铁路中,磨损程度十分严重的约占到总数的30%左右,其他铁路均有不同程度的磨损。
铁路的严重磨损导致铁路运行安全受到了严重威胁,此外,每年铁路部门在维修铁路等方面的花销更高,给铁路运营部门造成了较大的经济负担。
1.1 运行过程中车轮的摩擦磨损车轮是铁路车辆的重要组成部分,在实际运营过程中,铁路机车的彻骨会出现:轮缘损伤、热损伤、车轮踏面断裂等现象。
因摩擦而产生的热量主要集中于车轮与轨道的接触面,造成表面过度磨损的主要原因在于表面聚集了过多的制动热应力及内部应力存在缺陷。
目前,我国铁路机车中出现上述几种问题的数量众多,企鹅车损状况十分严重。
车轮的严重消耗导致车辆在维修时必须要更换车轮,我国每年在更换车轮方面的开销高达三十亿以上,年均更换车轮数为七十万只左右。
1.2 钢轨的摩擦磨损我国现在的铁路运输行业发展势头十分迅猛。
近年来,随着铁路总里程量的增加,铁路运输量也随着增大,这也为铁路部门带来了巨大的铁路运营压力。
我国铁路轨道磨损情况是目前给铁路运输部门造成压力主要方面,铁路轨道磨损严重,导致铁路运输安全性无法得到有效保证,容易造成铁路运输事故。
另外,随着我国铁路运输网络的不断建设及完善,每年在钢轨建设及维护等方面的成本呈现快速上升趋势,不但会造成铁路运输部门经济负担增加,而且需要大量的钢材来进行轨道维护,造成了基础资源浪费的情况。
CRH2动车组拖车车轮滚动接触疲劳分析
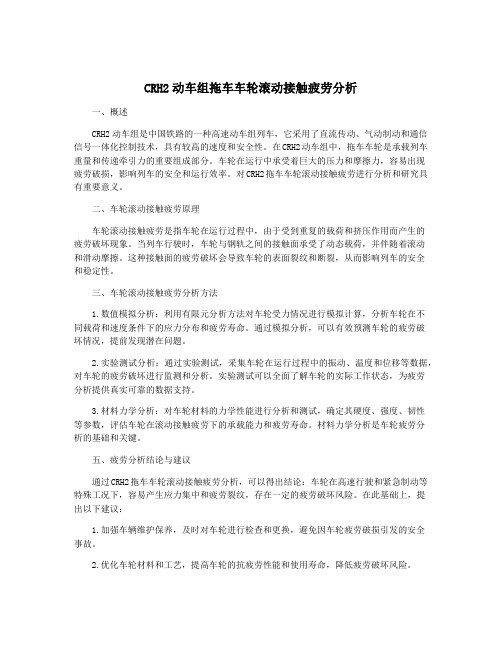
CRH2动车组拖车车轮滚动接触疲劳分析一、概述CRH2动车组是中国铁路的一种高速动车组列车,它采用了直流传动、气动制动和通信信号一体化控制技术,具有较高的速度和安全性。
在CRH2动车组中,拖车车轮是承载列车重量和传递牵引力的重要组成部分。
车轮在运行中承受着巨大的压力和摩擦力,容易出现疲劳破损,影响列车的安全和运行效率。
对CRH2拖车车轮滚动接触疲劳进行分析和研究具有重要意义。
二、车轮滚动接触疲劳原理车轮滚动接触疲劳是指车轮在运行过程中,由于受到重复的载荷和挤压作用而产生的疲劳破坏现象。
当列车行驶时,车轮与钢轨之间的接触面承受了动态载荷,并伴随着滚动和滑动摩擦。
这种接触面的疲劳破坏会导致车轮的表面裂纹和断裂,从而影响列车的安全和稳定性。
三、车轮滚动接触疲劳分析方法1.数值模拟分析:利用有限元分析方法对车轮受力情况进行模拟计算,分析车轮在不同载荷和速度条件下的应力分布和疲劳寿命。
通过模拟分析,可以有效预测车轮的疲劳破坏情况,提前发现潜在问题。
2.实验测试分析:通过实验测试,采集车轮在运行过程中的振动、温度和位移等数据,对车轮的疲劳破坏进行监测和分析。
实验测试可以全面了解车轮的实际工作状态,为疲劳分析提供真实可靠的数据支持。
3.材料力学分析:对车轮材料的力学性能进行分析和测试,确定其硬度、强度、韧性等参数,评估车轮在滚动接触疲劳下的承载能力和疲劳寿命。
材料力学分析是车轮疲劳分析的基础和关键。
五、疲劳分析结论与建议通过CRH2拖车车轮滚动接触疲劳分析,可以得出结论:车轮在高速行驶和紧急制动等特殊工况下,容易产生应力集中和疲劳裂纹,存在一定的疲劳破坏风险。
在此基础上,提出以下建议:1.加强车辆维护保养,及时对车轮进行检查和更换,避免因车轮疲劳破损引发的安全事故。
2.优化车轮材料和工艺,提高车轮的抗疲劳性能和使用寿命,降低疲劳破坏风险。
3.优化列车运行参数和控制策略,减少车轮的应力集中和疲劳破坏,提高列车的安全和稳定性。
CRH1型动车组轮缘异常磨耗研究及解决方案

王 开 团 ,张 现 锋 ,周 海 廷 ,姜 靓 (青岛四方庞巴迪铁路运输设备有限公司,山东青岛 266111)
摘 要 CRH1型动车组投入运营后,发现车轮轮缘有磨耗现象,部分 动 车 组 车 轮 出 现 偏 磨 等 异 常 现 象,特 别 是 福 州动车段动车组车轮偏磨比较严重,车轮旋修量 较 大,影 响 到 车 轮 寿 命。 通 过 对 运 行 线 路、线 路 条 件、车 轮 磨 耗 情 况的调查,进行理论分析和计算,提出对特殊线路进行 整 修、调 整 进 出 库 运 行 速 度、结 合 CRH1 转 向 架 综 合 加 改 方 案将 LMA 踏面更换为 LMD 踏面、调整一系定位节点 刚 度 等 解 决 方 案,有 效 解 决 了 车 轮 轮 缘 的 异 常 磨 耗,提 高 了 车 轮 寿 命 ,车 轮 平 均 寿 命 提 高 到 原 来 的 约 2.5 倍 。 关 键 词 动 车 组 ;轮 缘 磨 耗 ;线 路 ;踏 面 中 图 分 类 号 :U266.2 文 献 标 志 码 :A doi:10.3969/j.issn.1008-7842.2019.03.26
动车所和福州 南 动 车 所,主 要 运 行 线 路 为 上 海—南 京、 上海—福 州、福 州—厦 门 等 线 路,部 分 线 路 为 既 有 线 见 图 3~ 图 4。
通过对线 路 调 查,发 现 主 要 在 通 过 道 岔 及 小 曲 线 时,轨道侧面有与 轮 缘 磨 擦 痕 迹,在 各 动 车 所 的 小 曲 线 和 道 岔 处 轨 侧 均 有 磨 耗 情 况 ,在 轨 道 底 部 有 金 属 碎 屑 。
Байду номын сангаас
2.2 车 轮 磨 耗 调 查 BST 对上海和福州动车 组 车 轮 使 用 Miniprof进 行
CRH2动车组拖车车轮滚动接触疲劳分析

CRH2动车组拖车车轮滚动接触疲劳分析1. 引言1.1 研究背景CRH2动车组是中国高速铁路的重要交通工具,其拖车车轮滚动接触疲劳问题一直备受关注。
随着高铁运营速度的不断提高和运营里程的增加,车轮滚动接触疲劳问题对列车运行安全和运行成本产生了重要影响。
研究背景中,我们需要考虑到CRH2动车组拖车车轮滚动接触疲劳问题的研究历史、现状以及存在的问题和挑战。
在过去的研究中,人们对车轮滚动接触疲劳问题进行了不少探讨,但随着高铁运营条件的不断演变和高铁技术的不断进步,需要重新审视并深入探讨这一问题。
车轮滚动接触疲劳是指车轮与轨道接触时由于频繁的滚动和受力作用而导致的裂纹与断裂现象。
了解车轮滚动接触疲劳的原理及影响因素,对于提高列车运行安全性和减少运营成本至关重要。
本研究旨在对CRH2动车组拖车车轮滚动接触疲劳进行深入分析,为优化车辆设计和提高运行安全性提供理论支持和技术参考。
1.2 研究目的研究目的是为了对CRH2动车组拖车车轮滚动接触疲劳进行深入分析和研究,探讨其疲劳寿命预测模型及优化方法。
通过对车轮滚动接触疲劳原理和影响因素的分析,结合试验方法与结果分析,建立疲劳寿命预测模型,为车轮的使用和维护提供科学依据。
通过疲劳寿命优化方法的探讨,可以有效延长车轮的使用寿命,提高运输效率,减少成本。
研究的最终目的是为了提高CRH2动车组的运行安全性和可靠性,为铁路运输的发展做出贡献。
通过研究车轮滚动接触疲劳的相关问题,可以为铁路行业提供技术支持和参考,对于提高铁路运输设备的性能和效率具有重要意义。
1.3 研究意义研究意义是本文的重要部分之一,对于CRH2动车组拖车车轮滚动接触疲劳的分析具有重要意义。
首先,通过对车轮滚动接触疲劳的研究,可以帮助我们更好地了解车辆运行中可能出现的问题和隐患,有助于提高车辆的安全性和可靠性。
其次,疲劳是材料在动态载荷作用下引起的破坏过程,疲劳寿命的研究不仅可以帮助我们延长车轮的使用寿命,还可以节约维护成本,提高整个铁路运输系统的效益。
CRH2动车组拖车车轮滚动接触疲劳分析
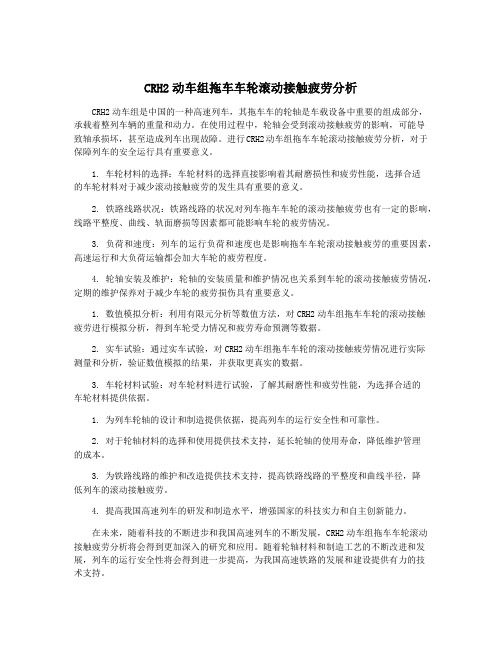
CRH2动车组拖车车轮滚动接触疲劳分析CRH2动车组是中国的一种高速列车,其拖车车的轮轴是车载设备中重要的组成部分,承载着整列车辆的重量和动力。
在使用过程中,轮轴会受到滚动接触疲劳的影响,可能导致轴承损坏,甚至造成列车出现故障。
进行CRH2动车组拖车车轮滚动接触疲劳分析,对于保障列车的安全运行具有重要意义。
1. 车轮材料的选择:车轮材料的选择直接影响着其耐磨损性和疲劳性能,选择合适的车轮材料对于减少滚动接触疲劳的发生具有重要的意义。
2. 铁路线路状况:铁路线路的状况对列车拖车车轮的滚动接触疲劳也有一定的影响,线路平整度、曲线、轨面磨损等因素都可能影响车轮的疲劳情况。
3. 负荷和速度:列车的运行负荷和速度也是影响拖车车轮滚动接触疲劳的重要因素,高速运行和大负荷运输都会加大车轮的疲劳程度。
4. 轮轴安装及维护:轮轴的安装质量和维护情况也关系到车轮的滚动接触疲劳情况,定期的维护保养对于减少车轮的疲劳损伤具有重要意义。
1. 数值模拟分析:利用有限元分析等数值方法,对CRH2动车组拖车车轮的滚动接触疲劳进行模拟分析,得到车轮受力情况和疲劳寿命预测等数据。
2. 实车试验:通过实车试验,对CRH2动车组拖车车轮的滚动接触疲劳情况进行实际测量和分析,验证数值模拟的结果,并获取更真实的数据。
3. 车轮材料试验:对车轮材料进行试验,了解其耐磨性和疲劳性能,为选择合适的车轮材料提供依据。
1. 为列车轮轴的设计和制造提供依据,提高列车的运行安全性和可靠性。
2. 对于轮轴材料的选择和使用提供技术支持,延长轮轴的使用寿命,降低维护管理的成本。
3. 为铁路线路的维护和改造提供技术支持,提高铁路线路的平整度和曲线半径,降低列车的滚动接触疲劳。
4. 提高我国高速列车的研发和制造水平,增强国家的科技实力和自主创新能力。
在未来,随着科技的不断进步和我国高速列车的不断发展,CRH2动车组拖车车轮滚动接触疲劳分析将会得到更加深入的研究和应用。
动车组车轮踏面磨耗对动力学性能的影响

轮踏面磨耗是车轮缺陷表现的主要形式[1],对轮轨接触关系和车辆系统运行的稳定性、平稳性、安全性,以及运营成本产生较为明显的影响。
目前,在役动车组运营一段时间后常出现晃车和垂向振动加剧等现象[2],这是由于车轮踏面不断磨耗造成的。
在此以实测磨耗后的踏面为基础,以CRH 2型动车组为研究对象,针对动车组的新踏面、实测小磨耗踏面及大磨耗踏面与标准轨道匹配,研究车辆在不同磨耗踏面下的运行动力学性能,以求对保证高速列车安全可靠运行有一定的指导意义,并为踏面外形的优化设计提供一定参考。
1 不同踏面对比目前,我国动车组主要采用3种不同踏面。
其中,CRH 1型和CRH 2型动车组采用LMA踏面,CRH 3型动车组采用S1002CN踏面,CRH 5型动车组采用XP55踏面[3]。
动车组运行一段时间后,踏面出现磨耗现象,根据实测踏面形状,选取2种不同磨耗程度的LMA踏面,与新踏面进行对比(见图1)。
动车组车轮踏面磨耗对动力学性能的影响徐 凯:西南交通大学机械工程学院,博士研究生,四川 成都,610031李 芾:西南交通大学机械工程学院,教授,四川 成都,610031李东宇:中国铁路物资北京有限公司,助理工程师,北京,100053杨 阳:西南交通大学机械工程学院,博士研究生,四川 成都,610031摘 要:比较不同磨耗程度下LMA踏面的形状和轮轨接触特征,建立CRH 2型动车组计算模型,使用不同磨耗程度的LMA踏面配合60 kg/m钢轨轨面,对其动力学性能进行仿真计算。
结果表明,在踏面出现磨耗后,车辆稳定性、车体振动加速度和平稳性指标均较新轮状态恶劣;车体振动功率谱密度分布表明,车体摇头振动能量明显增大,垂向振动特征没有发生变化;随着踏面的磨耗,车辆曲线通过性能得到改善;对于在役动车组,应严格控制其车轮踏面磨耗。
关键词:高速动车组;转向架;踏面磨耗;动力学性能中图分类号:U260.11 文献标识码:A 文章编号:1001-683X(2016)09-0040-05车图1 磨耗踏面与新踏面对比Y /m m302010-50 0 50X /mm小磨耗踏面大磨耗踏面 新踏面动车组车轮踏面磨耗对动力学性能的影响 徐凯 等从新踏面和磨耗踏面对比可以看出,磨耗主要出现在踏面与轨道接触区域,即名义滚动圆附近。
CRH2动车组拖车车轮滚动接触疲劳分析

CRH2动车组拖车车轮滚动接触疲劳分析1. 引言1.1 研究背景动车组在现代铁路运输中扮演着重要的角色,其安全性和可靠性是保障铁路运输顺畅的关键因素之一。
而动车组的车轮滚动接触疲劳是影响动车组安全运行的重要问题之一。
在列车运行过程中,车轮与轨道接触会产生滚动磨损,长时间的运行会导致车轮表面疲劳裂纹和损伤,最终影响车轮的安全性和运行稳定性。
针对CRH2动车组的车轮滚动接触疲劳问题,有必要开展深入研究和分析,以解决这一问题并提高动车组的运行安全性和寿命。
通过系统地分析车轮滚动接触疲劳的原理和影响因素,可以为制定有效的防护和维护措施提供科学依据。
对CRH2动车组拖车车轮滚动接触疲劳进行分析研究具有重要的理论和实践意义,对提高动车组的运行效率和安全保障具有积极的推动作用。
1.2 研究目的研究目的是为了深入了解CRH2动车组拖车车轮滚动接触疲劳的机理,探讨影响车轮疲劳寿命的因素,提出相应的改进措施以提高车轮的使用寿命和安全性。
通过分析车轮疲劳损伤的原因和规律,可以为制定维护保养计划、优化车轮设计提供理论支持和实验依据。
研究车轮的滚动接触疲劳特性还可以为铁路运输安全和效率提供重要的参考依据,为进一步提升中国高铁运行的水平和品质做出贡献。
通过对CRH2动车组拖车车轮滚动接触疲劳的分析研究,可以揭示其内在机理,探讨解决方案,为提升铁路运输安全和效率提供理论指导和技术支持。
1.3 研究意义车轮滚动接触疲劳是动车组运行过程中不可避免的问题,其发生可能会对列车的安全性和运行稳定性造成影响。
对CRH2动车组拖车车轮滚动接触疲劳进行分析具有重要的研究意义。
研究CRH2动车组拖车车轮滚动接触疲劳有助于深入了解车轮在实际运行中的工作状态和性能表现。
通过对疲劳特性的深入研究,可以为改进车轮设计、制造工艺和维护保养提供重要参考,进而提高车轮的使用寿命和运行安全性。
研究CRH2动车组拖车车轮滚动接触疲劳可以为相关领域提供有益的经验总结和技术积累。
CRH2型动车组车轮滚动接触疲劳问题分析

87中国设备工程Engineer ing hina C P l ant中国设备工程 2018.02 (下)1 问题的提出随着铁路高速重载技术的快速发展,轮轨滚动接触疲劳现象越来越严重,这不但会造成运营和维修成本的大幅增加,同时也直接影响列车运营安全。
CRH2型动车组车轮采用ER8材质的车轮,近年来发生了多起车轮滚动接触疲劳故障,其中头尾车导向轮发生车轮滚动接触疲劳概率相对较高。
2 原因分析材料在循环应力作用下,产生局部永久性积累损伤,经过一定的循环次数后,接触表面产生麻点、浅层或深层剥落的过程称为接触疲劳。
车轮载荷通过一个相对很小的接触区域传递给了钢轨,通常会使局部载荷超过车轮和钢轨材料的弹性极限,这就会导致滚动接触疲劳裂纹的萌生。
CRH2型动车组车轮滚动接触疲劳主要为两类,第一类主要由横向力和纵向力引起,一般发生在车轮滚动圆外侧15~30mm 范围内,裂纹与踏面间倾斜约45°,车轮周圈均存在;第二类主要由车轮硌伤引起,发生在名义滚动圆至外侧15mm 范围内,一般发生在个别点,表现为镟轮后内部出现月牙形缺陷。
滚动接触疲劳如不及时进行镟修,均会导致剥离。
2.1 由横向力和纵向力引起的滚动接触疲劳动车组运行过程中,车轮承受纵向力、横向力和垂向力,其中纵向力主要由牵引、制动产生,横向力主要由车辆过曲线和蛇形运动产生,垂向力主要由车辆自身重量及垂向冲击产生。
车轮表面材料反复承受上述疲劳载荷作用,踏面材料发生塑性变形,此类滚动接触疲劳主要由横向力和纵向力引起,在应力超过剪切强度的条件下(主要在过曲线时),塑性应变累积而形成微裂纹,最终导致滚动接触疲劳,并在上述应力作用下裂纹沿45°方向向内部扩展,最终形成剥离。
此类缺陷起源于踏面表面,由于表面裂纹萌生阶段尺寸很小,肉眼看不到缺陷。
动车组的头尾车在进入弯道时导向轮对首先进入弯道,此时导向轮对车轮受到的横向力及纵向力较中间车更大且更为复杂,因此动车组的头车位置轮对更易发生滚动接触疲劳现象。
- 1、下载文档前请自行甄别文档内容的完整性,平台不提供额外的编辑、内容补充、找答案等附加服务。
- 2、"仅部分预览"的文档,不可在线预览部分如存在完整性等问题,可反馈申请退款(可完整预览的文档不适用该条件!)。
- 3、如文档侵犯您的权益,请联系客服反馈,我们会尽快为您处理(人工客服工作时间:9:00-18:30)。
CRH2车轮磨耗分析
老CRH2A车轮现状
目前,我段配属的15组老CRH2A动车组(2028、2044除外),车轮轮径接近到限,部分已到限。
现对部分动车组车轮踏面磨耗和轮缘磨耗情况进行统计分析如下:
一、运行磨耗
运用中车轮平均磨耗量:踏面1.5mm(最大值9.5mm);轮缘磨耗1mm(最大值2.2mm)。
二、镟修磨(损)耗
1. 踏面平均镟修量(直径):4.7mm,镟修最大值13.5mm。
2. 轮缘厚度与踏面镟修量的关系。
三、一个高级修周期磨耗量
一个高级修周期(60万公里)磨耗量最小4.9mm,最大31.1mm。
其中,磨耗量大于10mm(800-790mm)车轮占总数的80.3%,为减少运用中换轮,建议运用中换轮比例不大于10%~20%,高级修轮径需控制在810mm左右。
四、当前到限情况
1.接近或已到限车轮分布情况 2002、2003、2004、2005、2006、2007、2008、2009、2020、2024、2025部分轮对轮径小于800mm
2. 轮径小于800mm轮对,2024 28条、2003 14条、2008 14条、2004 12条、2006 2条、2007 12条、2020 12条、2009 10条、2025 8条、2005 6条、2002 4条。
其中,2024 3车4条动轮、5车2条拖轮、6车4条动轮已到限;2020 5车2条拖轮已到限。
3. 老CRH2A动车组均已进行过次轮三级修,其中2030、2014、2023已进行或正进行第一次五级修, 2021、2020、2004、2005已接近五级修(距五级修10万公里以下),详见附表1。
4. 除2021,2023、 2004、2005、2009外,其余7组车在五级修前均需进行1次轮对修形。
现轮径和轮缘厚度大于800mm,28mm的轮对,基本能保证一次镟修并运行20万公里不超限。
2006、2008将在6月份镟修,2002、2007、2024将在7月份镟修,2003、
2020、2025将在8月份镟修。
5、按现车轮对的轮径磨耗情况分析,各动车组轮对磨耗到限见附表1。
至6月底,2003 1车4条,2004 1车2条,2008 3车2条、4车2条、5车2条、6车2条,2009 2车2条,2024 2车2条、3车4条、 4车2条、5车2条、6车4条、7车2条,共计20条动轮、10条拖轮到限。
至7月底,2002 3、4、5、
6、8车各2条、7车3条,2003 1、23、4、5、6车各2条,2007 3、6车各2条,2024 1、2、3、4、5、6、7车各2条、8车4条,1、5车各4条、2车2条,
详见附表1。
五、备用轮对及更换方案
1. 轮对周转更换。
1.1 目前已有四条动轮和四条拖轮用于周转更换。
1.2 轮对更换及检修周期。
轮对更换1天,送修3~4天,换轮检修动轮8~9天,拖轮6~7天。
总计,动轮12~14天,拖轮10~12天。
运营、调车、换轮计划的协调等其他原因,轮对一次周转约需半个月,每月最多周转更换2次。
1.3 6月底前到限轮对20条动轮,10条拖轮,动轮需周转5次,拖轮需周转3次。
2024轮对5月底,6月初集中到限,周转较困难。
2 到限轮对更换替修方案
2.1 选定替修车组
2028的轮对轮径值在804~812mm之间,适中,与其余车组轮对的轮径容易匹配;其距第一次五级修时间较长,若将其轮对换至其他车组上,符合新换上轮对走行公里数小于现车公里数要求,能确保下次高级修时新换上的轮对检修不超期。
2.2 2024到限轮对数量较多,可立即安排更换。
2.2.1 轮对到限车组优先更换2028对应轴位轮对,并成对更换。
2.2.2 若轮对到限车组对应2028轴位的轮对已更换,则按附表2中要求更换。
2.2.3 2028 轮对使用完后,使用2.3条修复轮对进行选配。
2.3其他车组的到限轮对换装至2028后,其轮对履历较乱。
建议2007的轮对换下后,全部更换新轮(包括新轴),其他车换下的到限轮对,车轮报废,换上2014的旧车轮,检修后待用。