齿轮蜗轮蜗杆参数
蜗轮蜗杆设计参数选择

圆柱蜗轮、蜗杆设计参数选择蜗轮和蜗杆通常用于垂直交叉的两轴之间的传动(图1)。
蜗轮和蜗杆的齿向是螺旋形的,蜗轮的轮齿顶面常制成环面。
在蜗轮蜗杆传动中,蜗杆是主动件,蜗轮是从动件。
蜗杆轴向剖面类是梯形螺纹的轴向剖面,有单头和多头之分。
若为单头,则蜗杆转一圈蜗轮只转一个齿,因此可以得到较高速比。
计算速比(i)的公式如下:i=蜗杆转速n1蜗轮转速n2=蜗轮齿数z2蜗杆头数z11、蜗轮蜗杆主要参数与尺寸计算主要参数有:模数(m)、蜗杆分度圆直径(d1)、导程角(r)、中心距(a)、蜗杆头数(或线数z1)、蜗轮齿数(z2)等,根据上述参数可决定蜗杆与蜗轮的基本尺寸,其中z1、z2由传动要求选定。
(1)模数m 为设计和加工方便,规定以蜗杆轴项目数mx和蜗轮的断面模数mt 为标准模数。
对啮合的蜗轮蜗杆,其模数应相等,及标准模数m=mx=mt。
标准模数可有表A查的,需要注意的是,蜗轮蜗杆的标准模数值与齿轮的标准模数值并不相同。
表A图1图2(2)蜗杆分度圆直径d1 再制造蜗轮时,最理想的是用尺寸、形状与蜗杆完全相同的蜗轮滚刀来进行切削加工。
但由于同一模数蜗杆,其直径可以各不相同,这就要求每一种模数对应有相当数量直径不同的滚刀,才能满足蜗轮加工需求。
为了减少蜗轮滚刀数目,在规定标准模数的同时,对蜗杆分度圆直径亦实行了标准化,且与m 有一定的匹配。
蜗杆分度圆直径d1与轴向模数mx之比为一标准值,称蜗杆的直径系数。
即q=蜗杆分度圆直径模数=d1m d1=mq有关标准模数m 与标准分度圆直径d1的搭配值及对应的蜗杆直径系数参照表A (3) 蜗杆导程角r 当蜗杆的q 和z1选定后,在蜗杆圆柱上的导程角即被确定。
为导程角、导程和分度圆直径的关系。
tan r=导程分度圆周长 = 蜗杆头数x 轴向齿距分度圆周长 =z1px d1π =z1πm πm q =z1q相互啮合的蜗轮蜗杆,其导程角的大小与方向应相同。
(4) 中心距a 蜗轮与蜗杆两轴中心距a 与模数m 、蜗杆直径系数q 以及蜗轮齿数z2间的关系式如下:a=d1+d22 =m q(q+z2)蜗杆各部尺寸如表B蜗轮各部尺寸如表C2、 蜗轮蜗杆的画法(1) 蜗杆的规定画法 参照图1图2 (2)蜗轮的规定画法 参照图1图2 (3)蜗轮蜗杆啮合画法 参照图1图2.。
齿轮与蜗轮蜗杆设计计算
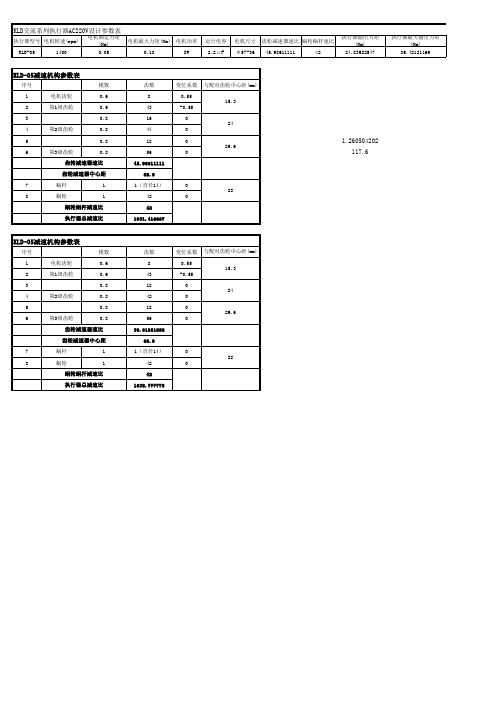
1.260504202 117.6ຫໍສະໝຸດ KLD-05减速机构参数表
序号 1 2 3 4 5 6 第3级齿轮 第2级齿轮 电机齿轮 第1级齿轮 模数 0.6 0.6 0.8 0.8 0.8 0.8 齿数 8 43 18 42 18 56 39.01851852 68.9 1(直径14) 42 42 1638.777778 0 28 8 蜗轮 蜗轮蜗杆减速比 执行器总减速比 1 0 变位系数 0.55 15.3 -0.55 0 24 0 0 29.6 0 齿轮减速器速比 齿轮减速器中心距 7 蜗杆 1 与配对齿轮中心距(mm)
KLD-05减速机构参数表
序号 1 2 3 4 5 6 第3级齿轮 第2级齿轮 电机齿轮 第1级齿轮 模数 0.6 0.6 0.8 0.8 0.8 0.8 齿数 8 43 16 44 18 56 45.98611111 68.9 1(直径14) 42 42 1931.416667 0 28 8 蜗轮 蜗轮蜗杆减速比 执行器总减速比 1 0 变位系数 0.55 15.3 -0.55 0 24 0 0 29.6 0 齿轮减速器速比 齿轮减速器中心距 7 蜗杆 1 与配对齿轮中心距(mm)
额定扭矩(Nm) 50
动作时间 18s
KLD交流系列执行器AC220V设计参数表
执行器型号 电机转速(rpm) 电机额定力矩(Nm) 电机最大力矩(Nm) KLD-05 1400 0.05 0.18 电机功率 8W 运行电容 2.2μ F 电机尺寸 φ 57-36 齿轮减速器速比 蜗轮蜗杆速比 执行器输出力矩(Nm) 执行器最大输出力矩(Nm) 45.98611111 42 24.83922547 89.42121169
蜗轮蜗杆设计参数
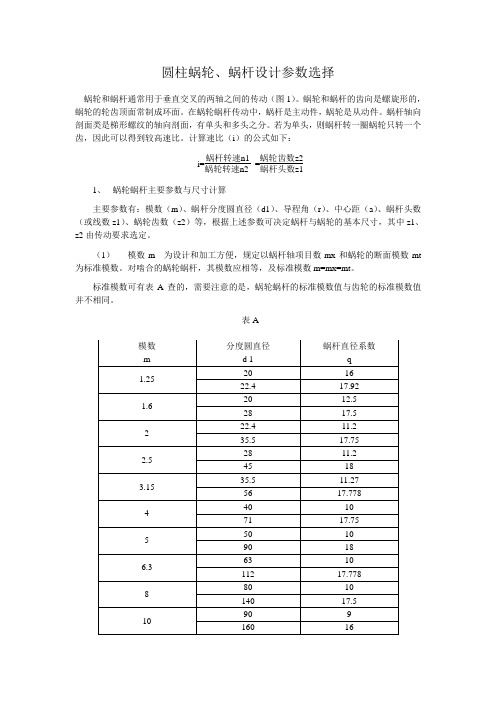
圆柱蜗轮、蜗杆设计参数选择蜗轮和蜗杆通常用于垂直交叉的两轴之间的传动(图1)。
蜗轮和蜗杆的齿向是螺旋形的,蜗轮的轮齿顶面常制成环面。
在蜗轮蜗杆传动中,蜗杆是主动件,蜗轮是从动件。
蜗杆轴向剖面类是梯形螺纹的轴向剖面,有单头和多头之分。
若为单头,则蜗杆转一圈蜗轮只转一个齿,因此可以得到较高速比。
计算速比(i)的公式如下:i=蜗杆转速n1蜗轮转速n2=蜗轮齿数z2蜗杆头数z11、蜗轮蜗杆主要参数与尺寸计算主要参数有:模数(m)、蜗杆分度圆直径(d1)、导程角(r)、中心距(a)、蜗杆头数(或线数z1)、蜗轮齿数(z2)等,根据上述参数可决定蜗杆与蜗轮的基本尺寸,其中z1、z2由传动要求选定。
(1)模数m 为设计和加工方便,规定以蜗杆轴项目数mx和蜗轮的断面模数mt 为标准模数。
对啮合的蜗轮蜗杆,其模数应相等,及标准模数m=mx=mt。
标准模数可有表A查的,需要注意的是,蜗轮蜗杆的标准模数值与齿轮的标准模数值并不相同。
表A图1图2(2)蜗杆分度圆直径d1 再制造蜗轮时,最理想的是用尺寸、形状与蜗杆完全相同的蜗轮滚刀来进行切削加工。
但由于同一模数蜗杆,其直径可以各不相同,这就要求每一种模数对应有相当数量直径不同的滚刀,才能满足蜗轮加工需求。
为了减少蜗轮滚刀数目,在规定标准模数的同时,对蜗杆分度圆直径亦实行了标准化,且与m 有一定的匹配。
蜗杆分度圆直径d1与轴向模数mx之比为一标准值,称蜗杆的直径系数。
即q=蜗杆分度圆直径模数=d1m d1=mq有关标准模数m 与标准分度圆直径d1的搭配值及对应的蜗杆直径系数参照表A (3) 蜗杆导程角r 当蜗杆的q 和z1选定后,在蜗杆圆柱上的导程角即被确定。
为导程角、导程和分度圆直径的关系。
tan r=导程分度圆周长 = 蜗杆头数x 轴向齿距分度圆周长 =z1px d1π =z1πm πm q =z1q相互啮合的蜗轮蜗杆,其导程角的大小与方向应相同。
(4) 中心距a 蜗轮与蜗杆两轴中心距a 与模数m 、蜗杆直径系数q 以及蜗轮齿数z2间的关系式如下:a=d1+d22 =m q(q+z2)蜗杆各部尺寸如表B蜗轮各部尺寸如表C2、 蜗轮蜗杆的画法(1) 蜗杆的规定画法 参照图1图2 (2)蜗轮的规定画法 参照图1图2 (3)蜗轮蜗杆啮合画法 参照图1图2.。
螺旋齿轮参数计算公式
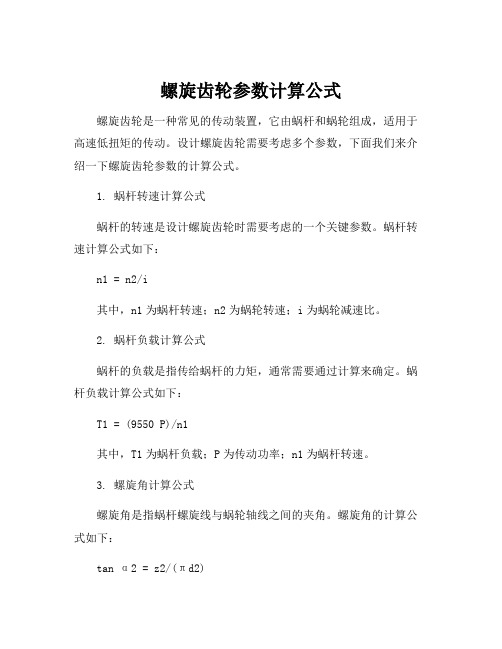
螺旋齿轮参数计算公式
螺旋齿轮是一种常见的传动装置,它由蜗杆和蜗轮组成,适用于高速低扭矩的传动。
设计螺旋齿轮需要考虑多个参数,下面我们来介绍一下螺旋齿轮参数的计算公式。
1. 蜗杆转速计算公式
蜗杆的转速是设计螺旋齿轮时需要考虑的一个关键参数。
蜗杆转速计算公式如下:
n1 = n2/i
其中,n1为蜗杆转速;n2为蜗轮转速;i为蜗轮减速比。
2. 蜗杆负载计算公式
蜗杆的负载是指传给蜗杆的力矩,通常需要通过计算来确定。
蜗杆负载计算公式如下:
T1 = (9550 P)/n1
其中,T1为蜗杆负载;P为传动功率;n1为蜗杆转速。
3. 螺旋角计算公式
螺旋角是指蜗杆螺旋线与蜗轮轴线之间的夹角。
螺旋角的计算公式如下:
tan α2 = z2/(πd2)
其中,α2为螺旋角;z2为蜗轮齿数;d2为蜗轮节圆直径。
4. 螺旋齿计算公式
螺旋齿计算公式是设计螺旋齿轮时必不可少的公式之一,它用来确定蜗轮的齿数。
螺旋齿计算公式如下:
z2 = (d1 tan α1)/π
其中,z2为蜗轮齿数;d1为蜗杆节圆直径;α1为蜗杆螺旋角。
5. 其他参数计算公式
除上述参数外,设计螺旋齿轮还需要考虑其他参数,如模数、齿距、齿顶高等。
这些参数的计算公式需要根据具体情况确定,并结合实际生产需要进行调整。
综上所述,螺旋齿轮的参数计算公式是设计螺旋齿轮必不可少的工具之一,不同的参数相互关联,需要综合考虑。
在实际应用中,设计人员需要根据具体用途和工作条件进行特别设计,以确保螺旋齿轮的可靠性和性能。
蜗杆传动主要参数及几何尺寸.

为了限制 滚刀数目
d1=mq
4. 蜗杆的导程角γ 轴面齿距 pa1=πm 导程 s=z1pa1=z1πm
tan z1 pa1 z1πm z1m z1
πd1 πd1 mq q
二. 蜗杆传动的几何尺 寸
三、蜗杆蜗轮啮合传动 1. 正确啮合条件
中间平面:蜗杆传动似齿轮齿条传动
ma1=mt2=m αa1=αt2=α γ=β (旋向相同)
中间平面:
在阿基米德蜗杆传动中,通过蜗杆轴线垂直蜗 轮轴线的平面
在中间平面内,阿基米德蜗杆传动 相当于齿轮于齿条传动。因此,蜗杆传 动的设计计算以中间平面的参数和几何 几何关系为准。
一、蜗杆传动的主要参数
1. 模数m、压力角a、齿顶高系数h*a和顶隙系数c*
蜗杆的参数
蜗轮的参数
①轴面模数ma1=m ②轴面压力角αa1= α ③齿顶高系数h*a=1 ④顶隙系数c*=0.2
2. 标准中心距
a
1 2
(d1
d2)
m 2
(q
z2 )
传动比i 5~6
z1
6
z2 30~36
7~13 4
28~52
14~27 2
28~54
28~40 2、1 28~80
>40 1
>40
3. 蜗杆的分度圆直径d1 蜗轮配对加工法
①采用与蜗杆参数相同的滚刀;
②滚刀的安装位置同蜗杆传动的 工作位置;直径系数
有多少d1就有多少滚刀
①端面模数mt2=m ②端面压力角αt2=α ③齿顶高系数h*a =1 ④顶隙系数c*=0.2
2. 传动比i、蜗杆头数z1和蜗轮齿数z2
i 1 z2 2 z1
z1少,传动比大,效率低; z1多, 加工难,常取1、2、 4、6。
蜗杆传动的基本参数

蜗杆传动的基本参数蜗杆传动是一种常见的传动机构,其主要由蜗轮与蜗杆组成。
蜗轮是一种齿轮,其齿形特殊,呈蜗旋线形状,而蜗杆是一种圆柱形的螺旋状轴。
蜗杆传动具有结构紧凑、承载能力大、传动比大、传动效率高等优势,在各种机械设备和工业领域中广泛应用。
蜗杆的蜗杆头径是指蜗杆轴上蜗杆的直径大小。
蜗杆头径会影响蜗杆传动的承载能力,一般来说,蜗杆头径越大,蜗杆传动的承载能力越大。
蜗杆步距是指蜗轮一次旋转所推动蜗杆前进的距离。
蜗杆步距决定了蜗杆传动的细分能力,即蜗轮每转一周,蜗杆前进一个步距,从而确定了蜗杆传动的传动比。
蜗杆长度是指蜗轮的宽度。
蜗杆长度会影响蜗杆传动的工作平稳性和传递扭矩的能力。
蜗杆的模数是指蜗轮齿廓和蜗杆螺旋线的截面形状的尺寸之比,是一个重要的参数。
模数的选择需要综合考虑蜗杆传动的应力和变形。
压力角是指蜗杆螺旋线与轴向的夹角,是蜗杆传动的设计中重要的参数之一、压力角的大小会影响蜗杆传动的接触性能和传动效率。
旋向是指蜗杆螺旋线的旋转方向,一般分为左旋和右旋两种。
蜗轮的模数是指蜗轮齿廓和蜗杆螺旋线的截面形状的尺寸之比。
蜗轮的模数需要与蜗杆的模数匹配,以确保传动的精度和工作平稳性。
压力角是指蜗轮齿廓与垂直于传动方向的线之间的夹角。
压力角的选择需要综合考虑蜗轮的齿强度和接触性能。
齿数是指蜗轮上齿的数量,影响蜗杆传动的传动比。
齿宽是指蜗轮齿廓沿蜗轮轴向的宽度。
齿宽需要满足传动扭矩和载荷要求。
螺旋角是指蜗轮上蜗杆螺旋线的扭曲角度。
螺旋角的选择需要考虑蜗杆传动的传动比和传动效率。
蜗轮蜗杆参数_蜗轮蜗杆传动特点
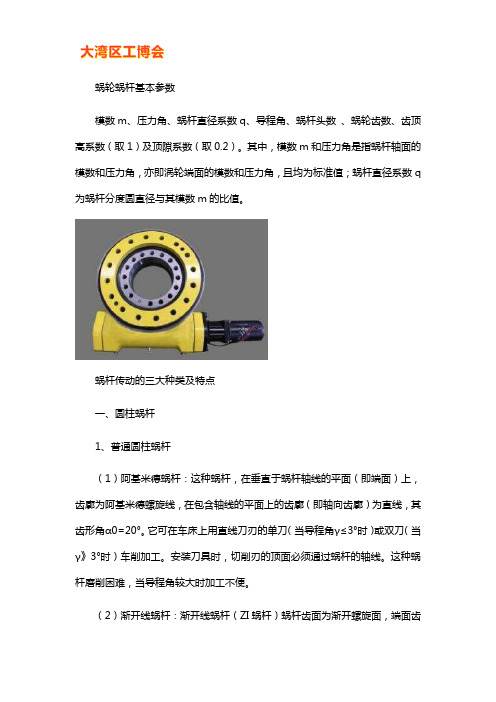
蜗轮蜗杆基本参数模数m、压力角、蜗杆直径系数q、导程角、蜗杆头数、蜗轮齿数、齿顶高系数(取1)及顶隙系数(取0.2)。
其中,模数m和压力角是指蜗杆轴面的模数和压力角,亦即涡轮端面的模数和压力角,且均为标准值;蜗杆直径系数q 为蜗杆分度圆直径与其模数m的比值。
蜗杆传动的三大种类及特点一、圆柱蜗杆1、普通圆柱蜗杆(1)阿基米德蜗杆:这种蜗杆,在垂直于蜗杆轴线的平面(即端面)上,齿廓为阿基米德螺旋线,在包含轴线的平面上的齿廓(即轴向齿廓)为直线,其齿形角α0=20°。
它可在车床上用直线刀刃的单刀(当导程角γ≤3°时)或双刀(当γ》3°时)车削加工。
安装刀具时,切削刃的顶面必须通过蜗杆的轴线。
这种蜗杆磨削困难,当导程角较大时加工不便。
(2)渐开线蜗杆:渐开线蜗杆(ZI蜗杆)蜗杆齿面为渐开螺旋面,端面齿廓为渐开线。
加工时,车刀刀刃平面与基圆相切。
可以磨削,易保证加工精度。
一般用于蜗杆头数较多,转速较高和较精密的传动。
(3)法向直廓蜗杆:这种蜗杆的端面齿廓为延伸渐开线,法面(N-N)齿廓为直线。
ZN蜗杆也是用直线刀刃的单刀或双刀在车床上车削加工。
车削时车刀刀刃平面置于螺旋线的法面上,加工简单,可用砂轮磨削,常用于多头精密蜗杆传动。
(4)锥面包络蜗杆:这是一种非线性螺旋曲面蜗杆。
它不能在车床上加工,只能在铣床上铣制并在磨床上磨削。
加工时,盘状铣刀或砂轮放置在蜗杆齿槽的法向面内,除工件作螺旋运动外,刀具同时绕其自身的轴线作回转运动。
这时,铣刀(或砂轮)回转曲面的包络面即为蜗杆的螺旋齿面,在I-I及N-N截面上的齿廓均为曲线。
这种蜗杆便于磨削,蜗杆的精度较高,应用日渐广泛。
2、圆弧圆柱蜗杆圆弧圆柱蜗杆传动和普通圆柱蜗杆传动相似,只是齿廓形状有所区别。
这种蜗杆的螺旋面是用刃边为凸圆弧形的刀具切制的,而蜗轮是用范成法制造的。
在中间平面(即蜗杆轴线和蜗杆副连心线所在的平面)上,蜗杆的齿廓为凹弧,而与之相配的蜗轮的齿廓则为凸弧形。
蜗轮蜗杆设计计算
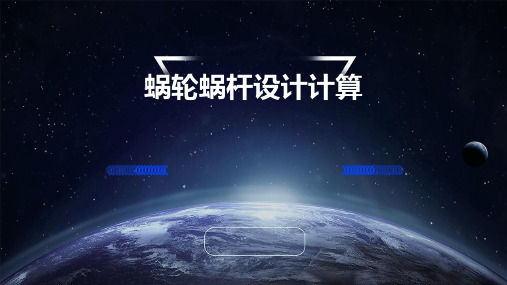
蜗杆传动的效率计算
总结词
根据蜗轮蜗杆的设计参数和工况,计算出蜗杆传动的效率。
详细描述
蜗杆传动的效率计算是评估蜗杆传动性能的重要指标之一。通过分析蜗轮蜗杆的设计参 数和工况,如蜗杆的导程角、模数、转速和载荷等参数,可以计算出蜗杆传动的效率。
蜗轮齿面接触疲劳强度的计算
总结词
根据蜗轮齿面上的载荷分布和材料属性 ,计算出蜗轮齿面的接触疲劳强度。
刚度分析
进行蜗轮蜗杆的刚度分析, 以减小传动过程中的变形 和振动。
可靠性设计
为确保自动化设备的可靠 性,对蜗轮蜗杆进行可靠 性设计和寿命预测。
THANKS
感谢观看
材料应具备较好的抗疲劳性能,以承受交 变载荷的作用;
04
材料应具有良好的工艺性能,易于加工制 造。
04
蜗轮蜗杆设计计算方法
蜗轮齿面载荷分布计算
总结词
根据蜗杆传动的实际工况,通过分析蜗轮齿面上的受力情况,计算出蜗轮齿面上的载荷分布。
详细描述
在进行蜗轮齿面载荷分布计算时,需要考虑蜗杆传动的实际工况,如传动比、转速、载荷大小和方向 等因素。通过分析蜗轮齿面上的受力情况,可以确定蜗轮齿面上的载荷分布,为后续的设计计算提供 基础。
蜗轮蜗杆设计计算
• 蜗轮蜗杆简介 • 蜗轮蜗杆设计参数 • 蜗轮蜗杆材料选择 • 蜗轮蜗杆设计计算方法 • 蜗轮蜗杆设计实例分析
01
蜗轮蜗杆简介
蜗轮蜗杆的定义
01
蜗轮蜗杆是一种常用的传动装置 ,由两个交错轴线、相互咬合的 齿轮组成,其中一个是蜗杆,另 一个是蜗轮。
02
蜗轮蜗杆具有传动比大、传动效 率高、传动平稳、噪音低等优点 ,因此在各种机械传动系统中得 到广泛应用。
VS
- 1、下载文档前请自行甄别文档内容的完整性,平台不提供额外的编辑、内容补充、找答案等附加服务。
- 2、"仅部分预览"的文档,不可在线预览部分如存在完整性等问题,可反馈申请退款(可完整预览的文档不适用该条件!)。
- 3、如文档侵犯您的权益,请联系客服反馈,我们会尽快为您处理(人工客服工作时间:9:00-18:30)。
一、蜗轮、蜗杆齿轮的功用与结构
蜗轮、蜗杆的功用主要用于传递交错轴间运动和动力,通常,轴交角∑=90°。
其优点是传动比大,工作较平稳,噪声低,结构紧凑,可以自锁;缺点是当蜗杆头数较少时,传动效率低,常需要采用贵重的减摩有色金属材料,制造成本高。
蜗轮是回转形零件,蜗轮的结构特点和齿轮基本相似,直径一般大于长度,通常由外圆柱面、内环面、内孔、键槽(花键槽)、轮齿、齿槽等组成。
根据结构形式的不同,齿轮上常常还有轮缘、轮毂、腹板(孔板)、轮辐等结构。
按结构不同蜗轮可分为实心式、腹板式、孔板式、轮辐式等多种型式。
蜗杆的结构和轴相似,其结构特点是长度一般大于直径,通常由外圆柱面、圆锥面、螺纹及阶梯端面等所组成。
蜗杆上啮合部分的轮齿呈螺旋状,有单头和多头之分,单头蜗杆的自锁性能好、易加工,但传动效率低。
二、普通圆柱蜗轮、蜗杆的测绘步骤
蜗轮、蜗杆的测绘比较复杂,要想获得准确的测绘数据,就必须具备较全面的蜗杆传动方面的知识。
同时应合理选择测量工具及必要的检测仪器,掌握正确的测量方法,并对所测量的数据进行合理的分析处理,提出接近或替代原设计的方案,直接为生产服务。
测绘蜗轮、蜗杆时,主要是确定蜗杆轴向模数m a(即蜗轮端面模数m t),蜗杆的直径系数q和导程角γ(即蜗轮的螺旋角β)。
下面以普通圆柱蜗轮蜗杆测绘为例,说明标准蜗轮蜗杆的基本测绘步骤。
1. 首先对要测绘的蜗轮、蜗杆进行结构和工艺分析。
2. 画出蜗轮、蜗杆的结构草图和必须的参数表,并画出所需标注尺寸的尺寸界线及尺寸线。
3. 数出蜗杆头数z1和蜗轮齿数z2。
4. 测量出蜗杆齿顶圆直径d a l、蜗轮喉径d a i和蜗轮齿顶外圆直径d ae。
5. 在箱体上测量出中心距a。
6. 确定蜗杆轴向模数m a (即涡轮端面模数m t)
7. 确定蜗杆的导程角γ(蜗轮的螺旋角β),并判定γ及β的方向。
根据计算公式tgγ= z
1m a / d1,因d1= d a1-2m a则
γ= tg -1 z1m a/ (d a1-2m a) 8. 确定蜗杆直径系数q
根据计算公式q = d
1/ m a 或q = z
1/ tg
γ计算出q值,且应按标准系列选取与其相近的标
准数值。
9. 根据计算公式,计算出其它各基本尺寸,如齿根圆直径d f1、d f2,齿顶高h a1、h a2,齿根高h f1、h f2等。
10. 所得尺寸必须与实测中心距a核对,且符合计算公式:
a = m a / 2 (q+z2)
11. 测量其它各部分尺寸,如毂孔直径、键槽尺寸等。
12. 根据使用要求,确定蜗轮、蜗杆的精度,一般为7~9级。
13. 用类比法或查资料确定配合处的尺寸公差和形位公差。
14. 用粗糙度量块对比或根据各部分的配合性质确定表面粗糙度。
15. 尺寸结构核对无误后,绘制零件图。
三、普通圆柱蜗杆、蜗轮的测绘
1. 几何参数的测量
(1)蜗杆头数z1〔齿数)、蜗轮齿数z2
目测确定z1,并数出z2。
(2)蜗杆齿顶圆及蜗轮喉圆直径d a1,d a2
可用高精度游标卡尺或千分尺直接测量,用游标卡尺测量蜗轮喉圆直径d a2的方法如图8-16所示。
测量时,可在三、四个不同直径位置上进行,取其中的最大值。
当蜗轮齿数为偶数时,齿顶圆直径就是将卡尺的读数减去两端量块高度之和,当蜗轮的齿数为奇数时,可按圆柱齿轮奇数齿所介绍的方法进行。
(3)蜗杆齿高h l
蜗杆齿高h l可按以下方法测量:
①用高精度游标卡尺的深度尺或其他深度测量工具直接测量蜗杆齿高,如图8-17所
示。
图8-16 蜗轮喉圆直径d a2的测量图8-17 蜗杆齿高h l的测量
②用游标卡尺测量蜗杆的齿顶圆直径d a1'和蜗杆齿根圆直径d f1',并按下式计算:
a1f1
1
d'd'
h
2
-
=
(4)蜗杆轴向齿距p z'
测量蜗杆轴向齿距p z'可以用直尺或游标
卡尺在蜗杆的齿顶圆柱上沿轴向直接测量,如图
8-18所示。
为了精确起见,最好多跨几个轴向齿
距,然后将所测得的数除以跨齿数,就是蜗杆的
轴向齿距。
(5)蜗杆齿形角α
蜗杆齿形角可用角度尺或齿形样板在蜗
杆的轴向剖面和法向剖面内测量,将两个剖面的
数值都记录下来,作确定参数时的参考。
也可以
用不同齿形角的蜗轮滚刀插入齿部作比较来判
断。
(6)蜗杆副中心距a'
蜗杆副中心距的测量对蜗杆传动啮合参数的确定以及对校核所定参数的正确性都是很重要的。
因此,应该仔细测量,力求精确。
需要注意的是:只有当根据测绘的几何参数所计算出来的中心距与实测的中心距a'相一致时,才能保证蜗杆传动的正确啮合。
测量中心距时,可利用设备原有的蜗杆和蜗轮
轴,清洗后重新装配进行测量。
测量时,首先要测量
这些轴的本身尺寸(D'1,D'2)与形位公差,以便作为
修正测量结果的参考。
常用的测量方法有:
图8-18 蜗杆轴向齿距的测量
① 用高精度游标卡尺或千分尺,测出两轴外侧间的距离L ',如图8-19所示,并按下式计算中心距:
12D'D'a 'L'2
+=-
② 用内径千分尺测出两轴内侧间的距离M ',如图8-20所示,并按下式计算中心距。
12D'D'a 'M'2
+=+
③ 当中心距不大,用上述方法测量有困难时,
可用量块测量两轴内侧间的距离K ',如图8-21所示,并按下式计算中心距。
齿轮的基本参数 2009-11-15 16:36
10.1.2直齿圆柱齿轮的基本参数、各部分的名称和尺寸关系
当圆柱齿轮的轮齿方向与圆柱的素线方向一致时,称为直齿圆柱齿轮。
表10.1.2-1列出了直齿圆柱齿轮各部分的名称和基本参数。
表10.1.2-1 直齿圆柱齿轮各部分的名称和基本参数
名称 符号 说 明 示意图
齿 数 z
图8-19 测蜗杆蜗轮轴外侧间的距离L '
模数 m πd=zp, d=p/πz, 令m=p/π
齿顶圆da 通过轮齿顶部的圆周直径
齿根圆df 通过轮齿根部的圆周直径
分度圆 d 齿厚等于槽宽处的圆周直径
齿高 h 齿顶圆与齿根圆的径向距离
齿顶高ha 分度圆到齿顶圆的径向距离
齿根高hf 分度圆到齿根圆的径向距离
齿距p 在分度圆上相邻两齿廓对应点的弧长
(齿厚+槽宽)
齿厚s每个齿在分度圆上的弧长
节圆d'一对齿轮传动时,两齿轮的齿廓在连心线O1O2上接触点C处,两齿轮的圆周速度相等,以O1C和O2C为半径的两个圆称为相应齿轮的节圆。
压力角α齿轮传动时,一齿轮(从动轮)齿廓在分度圆上点C的受力方向与运动方向所夹的锐角称压力角。
我国采用标准压力角为20°。
啮合角α'在点C处两齿轮受力方向与运动方向的夹角
模数m是设计和制造齿轮的重要参数。
不同模数的齿轮要用不同的刀具来加工制造。
为了便于设计和加工,模数数值已标准化,其数值如表10.1.2-2所示。
表10.1.2-2 齿轮模数标准系列(摘录GB/T1357-1987)
注:选用模数时,应优先选用第一系列;其次选用第二系列;括号内的模数尽可能不用。
标准直齿圆柱齿轮各部分的尺寸与模数有一定的关系,计算公式如表10.1.2-3。
表10.1.2-3 标准直齿圆柱齿轮轮齿各部分的尺寸计算。