蜗轮蜗杆设计参数选择
小模数蜗轮蜗杆设计标准

小模数蜗轮蜗杆设计标准一、设计基础小模数蜗轮蜗杆的设计应遵循以下基础原则:1. 标准化:设计时应尽可能遵循已有的标准,以提高设计的通用性和互换性。
2. 高效性:设计时应追求高效传动,以降低能耗,提高设备性能。
3. 可靠性:设计时应考虑可靠性,选用耐磨、耐腐蚀的材料,并采取适当的热处理工艺。
4. 经济性:设计时应考虑成本因素,选用价格合理的材料和工艺,以降低制造成本。
二、蜗轮设计蜗轮设计应考虑以下因素:1. 材料:蜗轮材料应具有良好的耐磨性和耐腐蚀性,一般选用铸铁、铜合金或铝合金等材料。
2. 齿形:蜗轮齿形应符合设计要求,以确保与蜗杆的正确啮合。
常用的齿形有阿基米德蜗轮、法向直廓蜗轮等。
3. 参数选择:蜗轮参数选择应考虑传动比、效率、寿命等因素,以确保蜗轮蜗杆传动的性能和可靠性。
4. 结构设计:蜗轮结构设计应合理,以确保安装方便、维护简单。
三、蜗杆设计蜗杆设计应考虑以下因素:1. 材料:蜗杆材料应具有良好的耐磨性和耐腐蚀性,一般选用合金钢、不锈钢等材料。
2. 齿形:蜗杆齿形应符合设计要求,以确保与蜗轮的正确啮合。
常用的齿形有阿基米德蜗杆、法向直廓蜗杆等。
3. 参数选择:蜗杆参数选择应考虑传动比、效率、寿命等因素,以确保蜗轮蜗杆传动的性能和可靠性。
4. 结构设计:蜗杆结构设计应合理,以确保安装方便、维护简单。
四、精度要求小模数蜗轮蜗杆的精度要求应符合相应的国家标准或行业标准。
一般来说,精度等级应与传动性能要求和使用场合相匹配。
对于一般传动系统,推荐采用IT7~IT9级精度等级;对于高精度传动系统,推荐采用IT6~IT5级精度等级。
在选择精度等级时,还需考虑使用环境、工作条件等因素的影响。
五、热处理工艺小模数蜗轮蜗杆在制造过程中需要进行适当的热处理工艺以提高其耐磨性和耐腐蚀性。
常用的热处理工艺包括表面淬火、渗碳淬火、氮化处理等。
在选择热处理工艺时,应根据材料种类和使用要求进行选择,并控制好热处理温度、时间等参数,以确保热处理质量。
蜗轮蜗杆设计步骤

蜗轮蜗杆设计步骤蜗轮蜗杆设计步骤:步骤一:确定工作参数首先需要确定蜗轮蜗杆的工作参数,例如传递功率、转速、转矩、受力方向等。
这些参数将决定蜗轮蜗杆的基本设计参数。
步骤二:选择材料在确定工作参数之后,需要根据工作条件选择适合的材料。
蜗轮一般选用高强度的材料,例如硬质合金、铸钢、铸铁等。
对于蜗杆来说,一般选用高硬度、高强度的材料,例如45钢、40Cr、35CrMo等。
步骤三:计算传动比传动比 = 蜗轮齿数 ÷蜗杆螺旋线高度。
传动比决定了蜗轮和蜗杆的相对转速和转矩大小。
步骤四:选择蜗杆模数蜗杆的模数可以根据蜗轮和蜗杆的传动比和齿数来选择,一般在0.2~2之间。
步骤五:计算齿距和齿宽齿距和齿宽需要结合蜗轮和蜗杆的模数和齿数来计算,保证蜗轮蜗杆的齿轮啮合平稳。
步骤六:计算螺距角螺距角是蜗杆的重要参数。
螺距角过大会造成摩擦力过大,螺距角过小则会导致螺杆摩擦力不足。
一般螺距角为5°至30°。
步骤七:计算轴心距和啮合角轴心距和啮合角是设计蜗轮蜗杆过程中非常重要的参数,需要根据传动比、模数、齿数等因素来计算。
步骤八:校核设计参数设计蜗轮蜗杆的参数后,需要进行校核检验,确保设计参数的合理性和可靠性。
校核包括强度校核、接触应力校核等。
步骤九:设计蜗轮蜗杆装配尺寸蜗轮蜗杆装配尺寸需要考虑啮合状态下的轴向间隙、径向间隙和公差等因素。
在设计装配尺寸时需要考虑到装配的方便性和精度要求。
步骤十:绘制蜗轮蜗杆图纸蜗轮蜗杆图纸需要按照设计参数进行详细绘制,包括蜗轮和蜗杆的各项参数和装配尺寸等。
绘制时需要考虑到制造的方便性和加工精度要求。
以上是蜗轮蜗杆的设计步骤,设计时需要注意各个参数的合理性和可靠性,同时考虑到加工和制造的实际情况。
蜗轮蜗杆设计参数
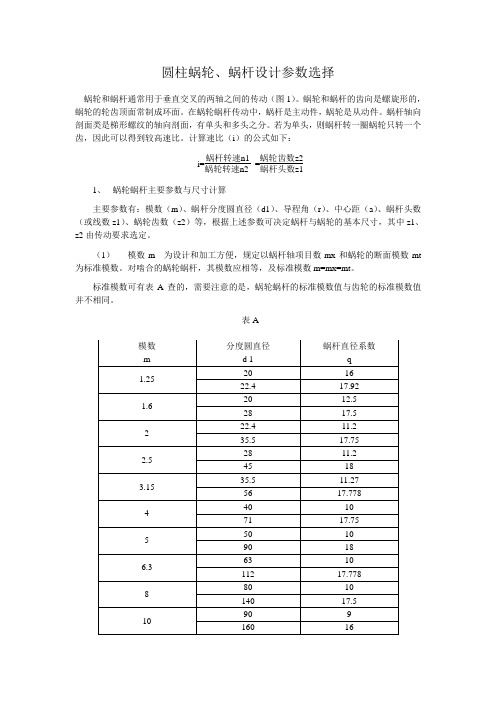
圆柱蜗轮、蜗杆设计参数选择蜗轮和蜗杆通常用于垂直交叉的两轴之间的传动(图1)。
蜗轮和蜗杆的齿向是螺旋形的,蜗轮的轮齿顶面常制成环面。
在蜗轮蜗杆传动中,蜗杆是主动件,蜗轮是从动件。
蜗杆轴向剖面类是梯形螺纹的轴向剖面,有单头和多头之分。
若为单头,则蜗杆转一圈蜗轮只转一个齿,因此可以得到较高速比。
计算速比(i)的公式如下:i=蜗杆转速n1蜗轮转速n2=蜗轮齿数z2蜗杆头数z11、蜗轮蜗杆主要参数与尺寸计算主要参数有:模数(m)、蜗杆分度圆直径(d1)、导程角(r)、中心距(a)、蜗杆头数(或线数z1)、蜗轮齿数(z2)等,根据上述参数可决定蜗杆与蜗轮的基本尺寸,其中z1、z2由传动要求选定。
(1)模数m 为设计和加工方便,规定以蜗杆轴项目数mx和蜗轮的断面模数mt 为标准模数。
对啮合的蜗轮蜗杆,其模数应相等,及标准模数m=mx=mt。
标准模数可有表A查的,需要注意的是,蜗轮蜗杆的标准模数值与齿轮的标准模数值并不相同。
表A图1图2(2)蜗杆分度圆直径d1 再制造蜗轮时,最理想的是用尺寸、形状与蜗杆完全相同的蜗轮滚刀来进行切削加工。
但由于同一模数蜗杆,其直径可以各不相同,这就要求每一种模数对应有相当数量直径不同的滚刀,才能满足蜗轮加工需求。
为了减少蜗轮滚刀数目,在规定标准模数的同时,对蜗杆分度圆直径亦实行了标准化,且与m 有一定的匹配。
蜗杆分度圆直径d1与轴向模数mx之比为一标准值,称蜗杆的直径系数。
即q=蜗杆分度圆直径模数=d1m d1=mq有关标准模数m 与标准分度圆直径d1的搭配值及对应的蜗杆直径系数参照表A (3) 蜗杆导程角r 当蜗杆的q 和z1选定后,在蜗杆圆柱上的导程角即被确定。
为导程角、导程和分度圆直径的关系。
tan r=导程分度圆周长 = 蜗杆头数x 轴向齿距分度圆周长 =z1px d1π =z1πm πm q =z1q相互啮合的蜗轮蜗杆,其导程角的大小与方向应相同。
(4) 中心距a 蜗轮与蜗杆两轴中心距a 与模数m 、蜗杆直径系数q 以及蜗轮齿数z2间的关系式如下:a=d1+d22 =m q(q+z2)蜗杆各部尺寸如表B蜗轮各部尺寸如表C2、 蜗轮蜗杆的画法(1) 蜗杆的规定画法 参照图1图2 (2)蜗轮的规定画法 参照图1图2 (3)蜗轮蜗杆啮合画法 参照图1图2.。
蜗轮蜗杆设计计算
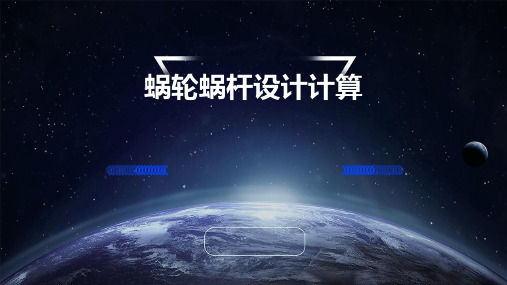
蜗杆传动的效率计算
总结词
根据蜗轮蜗杆的设计参数和工况,计算出蜗杆传动的效率。
详细描述
蜗杆传动的效率计算是评估蜗杆传动性能的重要指标之一。通过分析蜗轮蜗杆的设计参 数和工况,如蜗杆的导程角、模数、转速和载荷等参数,可以计算出蜗杆传动的效率。
蜗轮齿面接触疲劳强度的计算
总结词
根据蜗轮齿面上的载荷分布和材料属性 ,计算出蜗轮齿面的接触疲劳强度。
刚度分析
进行蜗轮蜗杆的刚度分析, 以减小传动过程中的变形 和振动。
可靠性设计
为确保自动化设备的可靠 性,对蜗轮蜗杆进行可靠 性设计和寿命预测。
THANKS
感谢观看
材料应具备较好的抗疲劳性能,以承受交 变载荷的作用;
04
材料应具有良好的工艺性能,易于加工制 造。
04
蜗轮蜗杆设计计算方法
蜗轮齿面载荷分布计算
总结词
根据蜗杆传动的实际工况,通过分析蜗轮齿面上的受力情况,计算出蜗轮齿面上的载荷分布。
详细描述
在进行蜗轮齿面载荷分布计算时,需要考虑蜗杆传动的实际工况,如传动比、转速、载荷大小和方向 等因素。通过分析蜗轮齿面上的受力情况,可以确定蜗轮齿面上的载荷分布,为后续的设计计算提供 基础。
蜗轮蜗杆设计计算
• 蜗轮蜗杆简介 • 蜗轮蜗杆设计参数 • 蜗轮蜗杆材料选择 • 蜗轮蜗杆设计计算方法 • 蜗轮蜗杆设计实例分析
01
蜗轮蜗杆简介
蜗轮蜗杆的定义
01
蜗轮蜗杆是一种常用的传动装置 ,由两个交错轴线、相互咬合的 齿轮组成,其中一个是蜗杆,另 一个是蜗轮。
02
蜗轮蜗杆具有传动比大、传动效 率高、传动平稳、噪音低等优点 ,因此在各种机械传动系统中得 到广泛应用。
VS
蜗轮蜗杆的设计方案
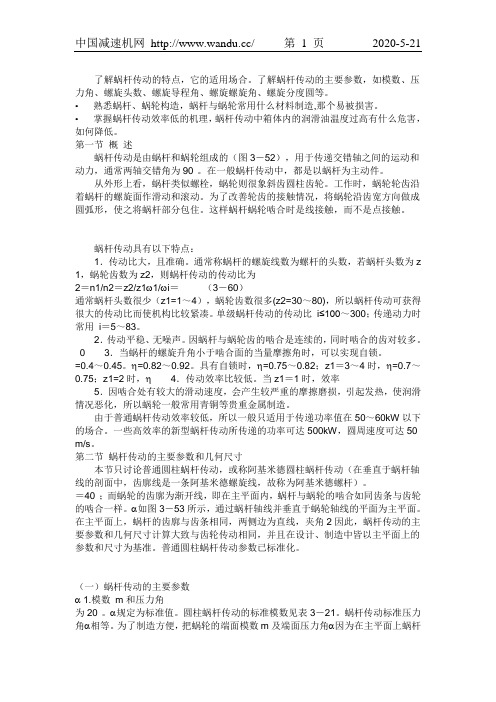
了解蜗杆传动的特点,它的适用场合。
了解蜗杆传动的主要参数,如模数、压力角、螺旋头数、螺旋导程角、螺旋螺旋角、螺旋分度圆等。
•熟悉蜗杆、蜗轮构造,蜗杆与蜗轮常用什么材料制造,那个易被损害。
•掌握蜗杆传动效率低的机理,蜗杆传动中箱体内的润滑油温度过高有什么危害,如何降低。
第一节概述蜗杆传动是由蜗杆和蜗轮组成的(图3-52),用于传递交错轴之间的运动和动力,通常两轴交错角为90°。
在一般蜗杆传动中,都是以蜗杆为主动件。
从外形上看,蜗杆类似螺栓,蜗轮则很象斜齿圆柱齿轮。
工作时,蜗轮轮齿沿着蜗杆的螺旋面作滑动和滚动。
为了改善轮齿的接触情况,将蜗轮沿齿宽方向做成圆弧形,使之将蜗杆部分包住。
这样蜗杆蜗轮啮合时是线接触,而不是点接触。
蜗杆传动具有以下特点:1.传动比大,且准确。
通常称蜗杆的螺旋线数为螺杆的头数,若蜗杆头数为z 1,蜗轮齿数为z2,则蜗杆传动的传动比为2=n1/n2=z2/z1ω1/ωi=(3-60)通常蜗杆头数很少(z1=1~4),蜗轮齿数很多(z2=30~80),所以蜗杆传动可获得很大的传动比而使机构比较紧凑。
单级蜗杆传动的传动比i≤100~300;传递动力时常用i=5~83。
2.传动平稳、无噪声。
因蜗杆与蜗轮齿的啮合是连续的,同时啮合的齿对较多。
03.当蜗杆的螺旋升角小于啮合面的当量摩擦角时,可以实现自锁。
=0.4~0.45。
η=0.82~0.92。
具有自锁时,η=0.75~0.82;z1=3~4时,η=0.7~0.75;z1=2时,η4.传动效率比较低。
当z1=1时,效率5.因啮合处有较大的滑动速度,会产生较严重的摩擦磨损,引起发热,使润滑情况恶化,所以蜗轮一般常用青铜等贵重金属制造。
由于普通蜗杆传动效率较低,所以一般只适用于传递功率值在50~60kW以下的场合。
一些高效率的新型蜗杆传动所传递的功率可达500kW,圆周速度可达50 m/s。
第二节蜗杆传动的主要参数和几何尺寸本节只讨论普通圆柱蜗杆传动,或称阿基米德圆柱蜗杆传动(在垂直于蜗杆轴线的剖面中,齿廓线是一条阿基米德螺旋线,故称为阿基米德螺杆)。
蜗轮蜗杆的选择及校核示例
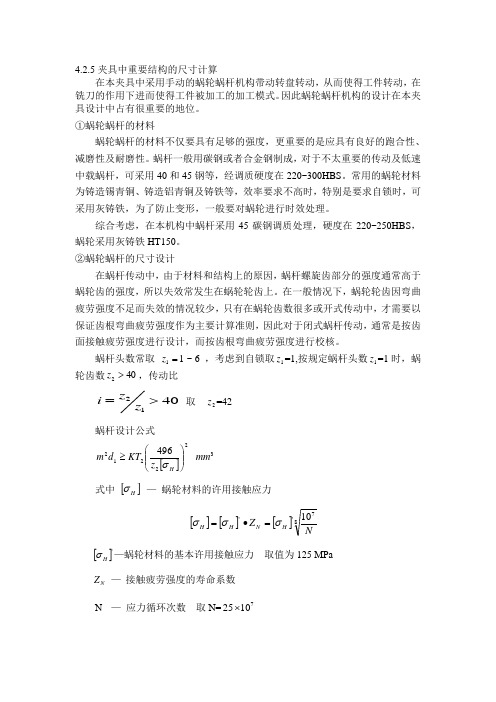
4.2.5夹具中重要结构的尺寸计算在本夹具中采用手动的蜗轮蜗杆机构带动转盘转动,从而使得工件转动,在铣刀的作用下进而使得工件被加工的加工模式。
因此蜗轮蜗杆机构的设计在本夹具设计中占有很重要的地位。
①蜗轮蜗杆的材料蜗轮蜗杆的材料不仅要具有足够的强度,更重要的是应具有良好的跑合性、减磨性及耐磨性。
蜗杆一般用碳钢或者合金钢制成,对于不太重要的传动及低速中载蜗杆,可采用40和45钢等,经调质硬度在220~300HBS 。
常用的蜗轮材料为铸造锡青铜、铸造铝青铜及铸铁等,效率要求不高时,特别是要求自锁时,可采用灰铸铁,为了防止变形,一般要对蜗轮进行时效处理。
综合考虑,在本机构中蜗杆采用45碳钢调质处理,硬度在220~250HBS ,蜗轮采用灰铸铁HT150。
②蜗轮蜗杆的尺寸设计在蜗杆传动中,由于材料和结构上的原因,蜗杆螺旋齿部分的强度通常高于蜗轮齿的强度,所以失效常发生在蜗轮轮齿上。
在一般情况下,蜗轮轮齿因弯曲疲劳强度不足而失效的情况较少,只有在蜗轮齿数很多或开式传动中,才需要以保证齿根弯曲疲劳强度作为主要计算准则,因此对于闭式蜗杆传动,通常是按齿面接触疲劳强度进行设计,而按齿根弯曲疲劳强度进行校核。
蜗杆头数常取 =1z 1 ~ 6 ,考虑到自锁取1z =1,按规定蜗杆头数1z =1时,蜗轮齿数402>z ,传动比4012>=z z i 取 2z =42蜗杆设计公式[]22212496⎪⎪⎭⎫ ⎝⎛≥H z KT d m σ 3mm 式中 []H σ — 蜗轮材料的许用接触应力[][][]87''10N Z H N H H σσσ=•=[]'H σ—蜗轮材料的基本许用接触应力 取值为125 MPaN Z — 接触疲劳强度的寿命系数N — 应力循环次数 取N=71025⨯2T = 9.7 M N •K= 1代入数据得 312194mm d m ≥由查表得标准模数 m 和蜗杆分度圆直径 1d 的值分别为 2.5和35.5 蜗杆的分度圆柱导程角 γ11tan d m z =γ 代入数据得 γ=︒4○3蜗轮蜗杆的尺寸校核 []F Fa F Y md d KT σγσ≤•=2212cos 53.1 [][]9610N F F •'=σσ 代入数据得 []MPa F 15=σ MPa F 73.3=σ 满足条件 []F F σσ≤由以上分析和计算得出蜗轮蜗杆的几何参数为 mm d 5.351= d 2=105mm 11=Z 422=Z 5.2=m ︒=4γ。
蜗轮蜗杆设计参数选择
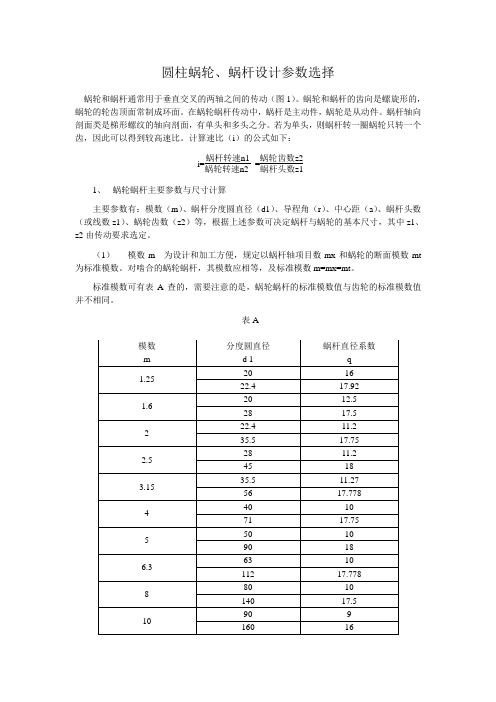
圆柱蜗轮、蜗杆设计参数选择蜗轮和蜗杆通常用于垂直交叉的两轴之间的传动(图1)。
蜗轮和蜗杆的齿向是螺旋形的,蜗轮的轮齿顶面常制成环面。
在蜗轮蜗杆传动中,蜗杆是主动件,蜗轮是从动件。
蜗杆轴向剖面类是梯形螺纹的轴向剖面,有单头和多头之分。
若为单头,则蜗杆转一圈蜗轮只转一个齿,因此可以得到较高速比。
计算速比(i)的公式如下:i=蜗杆转速n1蜗轮转速n2=蜗轮齿数z2蜗杆头数z11、蜗轮蜗杆主要参数与尺寸计算主要参数有:模数(m)、蜗杆分度圆直径(d1)、导程角(r)、中心距(a)、蜗杆头数(或线数z1)、蜗轮齿数(z2)等,根据上述参数可决定蜗杆与蜗轮的基本尺寸,其中z1、z2由传动要求选定。
(1)模数m 为设计和加工方便,规定以蜗杆轴项目数mx和蜗轮的断面模数mt 为标准模数。
对啮合的蜗轮蜗杆,其模数应相等,及标准模数m=mx=mt。
标准模数可有表A查的,需要注意的是,蜗轮蜗杆的标准模数值与齿轮的标准模数值并不相同。
表A图1图2(2)蜗杆分度圆直径d1 再制造蜗轮时,最理想的是用尺寸、形状与蜗杆完全相同的蜗轮滚刀来进行切削加工。
但由于同一模数蜗杆,其直径可以各不相同,这就要求每一种模数对应有相当数量直径不同的滚刀,才能满足蜗轮加工需求。
为了减少蜗轮滚刀数目,在规定标准模数的同时,对蜗杆分度圆直径亦实行了标准化,且与m 有一定的匹配。
蜗杆分度圆直径d1与轴向模数mx之比为一标准值,称蜗杆的直径系数。
即q=蜗杆分度圆直径模数=d1m d1=mq有关标准模数m 与标准分度圆直径d1的搭配值及对应的蜗杆直径系数参照表A (3) 蜗杆导程角r 当蜗杆的q 和z1选定后,在蜗杆圆柱上的导程角即被确定。
为导程角、导程和分度圆直径的关系。
tan r=导程分度圆周长 = 蜗杆头数x 轴向齿距分度圆周长 =z1px d1π =z1πm πm q =z1q相互啮合的蜗轮蜗杆,其导程角的大小与方向应相同。
(4) 中心距a 蜗轮与蜗杆两轴中心距a 与模数m 、蜗杆直径系数q 以及蜗轮齿数z2间的关系式如下:a=d1+d22 =m q(q+z2)蜗杆各部尺寸如表B蜗轮各部尺寸如表C2、 蜗轮蜗杆的画法(1) 蜗杆的规定画法 参照图1图2 (2)蜗轮的规定画法 参照图1图2 (3)蜗轮蜗杆啮合画法 参照图1图2.。
小模数蜗轮蜗杆设计标准

小模数蜗轮蜗杆设计标准一、引言小模数蜗轮蜗杆传动是一种常见的传动形式,具有传动效率高、噪音低、可靠性高等优点,广泛应用于工业生产中。
为了保证小模数蜗轮蜗杆传动的设计和制造质量,制定并实施设计标准是非常必要的。
二、技术要求1. 材料选择小模数蜗轮蜗杆的制造材料应符合国家标准,具有良好的韧性和耐磨性,常见材料有45钢、40Cr等。
2. 设计参数小模数蜗轮蜗杆的设计参数应满足传动比、效率、载荷等要求,同时考虑传动的可靠性和稳定性。
3. 绘图要求设计图纸应包括蜗轮蜗杆的主要尺寸、公差、表面粗糙度等内容,标注清晰,方便制造和检验。
4. 蜗轮蜗杆的加工工艺制造工艺应满足蜗轮蜗杆的质量要求,包括车削、磨齿、热处理等工艺流程,确保产品的精度和可靠性。
5. 性能测试蜗轮蜗杆传动装置应进行性能测试,包括传动效率、噪音、温升等指标的测试,确保产品符合设计要求。
三、质量控制1. 接受检验蜗轮蜗杆传动装置应进行全面的检验,包括外观检查、尺寸测量、齿轮啮合检查等,确保产品质量符合标准要求。
2. 过程控制在生产过程中应加强质量控制,防止缺陷产品流入市场,保证产品的可靠性和安全性。
3. 衍生产品衍生产品的设计和制造应遵循相关标准,不得出现设计缺陷和生产质量问题,确保产品安全可靠。
四、标准修订小模数蜗轮蜗杆设计标准应随着技术的发展不断修订和完善,包括材料、工艺、测试方法等方面的更新,以适应市场需求和技术发展。
五、结论小模数蜗轮蜗杆设计标准的制定和实施对于保证产品质量、提高产业竞争力具有重要意义,需要加强标准的宣传和执行,促进企业提升产品品质,推动产业健康发展。
- 1、下载文档前请自行甄别文档内容的完整性,平台不提供额外的编辑、内容补充、找答案等附加服务。
- 2、"仅部分预览"的文档,不可在线预览部分如存在完整性等问题,可反馈申请退款(可完整预览的文档不适用该条件!)。
- 3、如文档侵犯您的权益,请联系客服反馈,我们会尽快为您处理(人工客服工作时间:9:00-18:30)。
圆柱蜗轮、蜗杆设计参数选择
蜗轮和蜗杆通常用于垂直交叉的两轴之间的传动(图1)。
蜗轮和蜗杆的齿向是螺旋形的,蜗轮的轮齿顶面常制成环面。
在蜗轮蜗杆传动中,蜗杆是主动件,蜗轮是从动件。
蜗杆轴向剖面类是梯形螺纹的轴向剖面,有单头和多头之分。
若为单头,则蜗杆转一圈蜗轮只转一个齿,因此可以得到较高速比。
计算速比(i)的公式如下:
i=蜗杆转速n1
蜗轮转速n2
=
蜗轮齿数z2
蜗杆头数z1
1、蜗轮蜗杆主要参数与尺寸计算
主要参数有:模数(m)、蜗杆分度圆直径(d1)、导程角(r)、中心距(a)、蜗杆头数(或线数z1)、蜗轮齿数(z2)等,根据上述参数可决定蜗杆与蜗轮的基本尺寸,其中z1、z2由传动要求选定。
(1)模数m 为设计和加工方便,规定以蜗杆轴项目数mx和蜗轮的断面模数mt 为标准模数。
对啮合的蜗轮蜗杆,其模数应相等,及标准模数m=mx=mt。
标准模数可有表A查的,需要注意的是,蜗轮蜗杆的标准模数值与齿轮的标准模数值并不相同。
表A
图1
图2
(2)蜗杆分度圆直径d1 再制造蜗轮时,最理想的是用尺寸、形状与蜗杆完全相同的蜗轮滚刀来进行切削加工。
但由于同一模数蜗杆,其直径可以各不相同,这就要求每一种模数对应有相当数量直径不同的滚刀,才能满足蜗轮加工需求。
为了减少蜗轮滚刀数目,在规定标准模数的同时,对蜗杆分度圆直径亦实行了标准化,且与m 有一定的匹配。
蜗杆分度圆直径d1与轴向模数mx之比为一标准值,称蜗杆的直径系数。
即
q=
蜗杆分度圆直径模数
=d1
m d1=mq
有关标准模数m 与标准分度圆直径d1的搭配值及对应的蜗杆直径系数参照表A (3) 蜗杆导程角r 当蜗杆的q 和z1选定后,在蜗杆圆柱上的导程角即被确定。
为导程
角、导程和分度圆直径的关系。
tan r=
导程分度圆周长 = 蜗杆头数x 轴向齿距分度圆周长 =z1px d1π =z1πm πm q =z1
q
相互啮合的蜗轮蜗杆,其导程角的大小与方向应相同。
(4) 中心距a 蜗轮与蜗杆两轴中心距a 与模数m 、蜗杆直径系数q 以及蜗轮齿数z2
间的关系式如下:
a=d1+d22 =m q
(q+z2)
蜗杆各部尺寸如表B
蜗轮各部尺寸如表C
2、 蜗轮蜗杆的画法
(1) 蜗杆的规定画法 参照图1图2 (2)蜗轮的规定画法 参照图1图2 (3)蜗轮蜗杆啮合画法 参照图1
图2.。