连杆零件锤上锻模工艺及模具设计
锻造工艺与模具设计-锤上模锻

锻造工艺与模具设计-锤上模锻引言锤上模锻是一种传统的金属锻造工艺,它使用锤子和模具将金属加热至一定温度后进行锤击,使其塑性发生变化,并通过模具的形状来塑造金属的最终形态。
本文将介绍锤上模锻的工艺流程以及模具设计的要点和注意事项。
锤上模锻的工艺流程锤上模锻的工艺流程通常包括以下几个步骤:1.材料准备:选择适当的金属材料,并对其进行预处理,如去除表面氧化物、清除杂质等。
2.加热:将金属材料加热至适当的温度,以增加其塑性。
加热温度通常根据材料的种类和要求的锻造效果来确定。
3.锤击:在金属材料达到适当温度后,使用锤子对其进行锤击。
锤击力度和频率需根据材料的塑性和形状来调整,以达到锻造工件的要求。
4.模具设计:根据锻造工件的形状和尺寸要求,设计制作适用的模具。
模具应具有足够的强度和刚度,以承受锤击的力量,并能形成金属的预期形状。
5.成品处理:锻造完成后,对锻造工件进行必要的处理,如退火、淬火、表面处理等,以提高其性能和外观质量。
模具设计的要点和注意事项1. 模具材料的选择模具材料应具有足够的硬度和强度,以抵抗锤击力量的作用。
常用的模具材料有合金工具钢、高速钢等。
在选择模具材料时,还需要考虑其热膨胀系数和导热性能,以确保模具在高温条件下能保持形状稳定性。
2. 模具结构设计模具的结构设计应考虑到工件的形状和尺寸要求,以及锤击的力量和频率。
模具应具有足够的强度和刚度,以承受锤击的力量,并能准确地形成金属的预期形状。
同时,模具的结构应合理,方便装卸和调整,以提高生产效率。
3. 模具表面处理模具的表面处理对于形成工件的表面质量和精度非常重要。
常用的表面处理方法包括电火花加工、抛光、渗碳等。
表面处理可以改善模具的耐磨性和抗粘附性,以减少模具的磨损和延长使用寿命。
4. 模具的维护与保养模具在锤上模锻过程中会受到较大的冲击和热应力,因此需要定期进行维护和保养,以确保其性能和使用寿命。
维护和保养包括清洁、修复损坏、润滑等工作。
连杆的模锻工艺及模具设计

连杆的模锻工艺及模具设计任务书1.课题意义及目标意义:通过本课题的研究,培养学生综合运用所学知识的能力及用基本知识和专业知识解决生产中实际问题的能力,培养学生探索未知开拓创新的科学精神以及从事工程实践的基本能力。
目的:根据开式模锻成形理论和连杆零件图的要求,结合连杆锻造的技术和特点,对连杆锻造工艺进行具体分析,确定合理的连杆模锻工艺。
以所学专业为基础,以实用为目的,通过对连杆锻造工艺的分析及相关参数计算,进行模具设计。
2.主要任务1)、完成开题报告2)、零件图和模具装配图3)、设计说明书一本4)、电子资料一份3.主要参考资料[1]崔柏伟.发动机连杆模锻工艺及模具[J].机械工程师,2007,12:87-88 .[2]张昌明.铝合金连杆模锻工艺研究[J].机械设计与制造,2008,11:105-106.[3]刘昱虹.大型连杆锻造成形工艺分析[J].锻压机械,2000,35,04:25-26[4]陈晓华.典型零件模具图册[M].机械工业出版社,2006.审核人:年月日连杆的模锻工艺及模具设计摘要:本次毕业设计主要是对给定的连杆进行分析,然后进行锻件图的设计,确定锻锤吨位,然后选择模锻工步,再计算毛坯,确定坯料的尺寸,设计拔长模膛和滚压模膛,设计终锻模膛和预锻模膛,还需要设计锁扣、燕尾、键槽等。
本设计还涉及PROE、CAD软件,还有绘制表格,生成曲线图。
最后绘制了零件图和模具装配图。
通过这次设计,让我巩固了我大学所学的知识,受益良多。
关键词:连杆,模膛Abstract:The graduation project is mainly on a given link is analyzed and then design forging figure, and then select the forging step, and then calculate the blank determine the blank size, design stretching grooves and rolling grooves,determine the tonnage hammer,design the final forging die bore and blockers bore, also I need to design lock, dovetail, keyway and so on. This design also involves PROE, CAD software, and draw tables, generate graphs. Finally, draw spares and mold assembly drawing. Through this design, let me consolidate my knowledge of the university,and I benefited a lot. Keywords: link, bore1 前言 (3)2 锻件图的设计 (4)2.1 分模位置 (4)2.2 估算零件质量 (4)2.3 锻件形状复杂系数S (4)2.4 确定加工余量 (5)2.5 锻模斜度 (5)2.6 确定锻件公差 (5)2.7 锻件圆角半径 (5)2.8 冲孔连皮 (6)2.9 冷锻件图 (6)3 确定锻锤吨位 (8)4 飞边槽的确定 (9)5.1 计算毛坯图 (10)5.2 计算毛坯图的分析利用 (13)6 坯料的尺寸确定 (14)6.1 坯料体积和重量 (14)6.2 坯料规格的确定 (15)7 模锻工步选择 (16)8 拔长模膛 (17)8.1 作用 (17)8.2 型式 (17)9 滚压模膛设计 (19)9.1 作用 (19)9.2 型式 (19)9.3 纵向截面形状设计 (19)9.4 宽度B (21)9.5 尾部及钳口 (21)10 终锻模膛 (23)10.1 热锻件图设计 (23)10.2 钳口设计 (24)11 普通锁扣设计 (25)12 模锻锤的锻锤参数 (26)13 燕尾 (27)14 锻模结构设计 (28)14.1 模膛的布置 (28)14.2 模膛中心的确定 (28)14.3 模膛壁厚确定 (28)14.4 模块尺寸的确定 (29)14.5 模锻材料的选择 (29)14.6 连杆模锻工艺流程的最终确定 (29)参考文献 (30)致谢 (31)1前言连杆指的是在机构中的两端分别和主动、从动构件连接,用来传递运动的杆件。
下篇第8章-锤上模锻工艺与模具设计
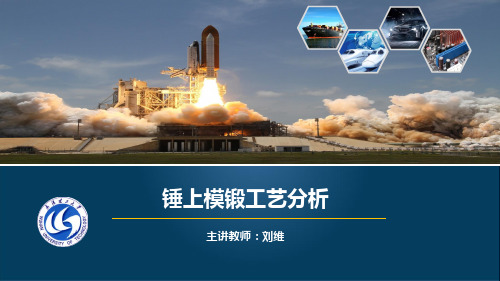
主讲教师:刘维锤上模锻工艺根据所用锻压设备及其锻造变形方式,通常将模锻分为锤上模锻、压力机模锻及平锻机模锻等。
模锻锤包括蒸汽空气模锻锤、无砧座锤、高速锤和液压模锻锤。
蒸汽空气模锻锤应用最普遍,一般简称为模锻锤。
锤上模锻工艺在压力作用下,毛坯在锻模型腔中被迫产生塑性变形,从而获得比自由锻更高质量的锻件。
它是大批量锻件生产的主要方法,具有以下特点:①金属在型腔中的变形时在锤头的多次打击下逐步完成的,锤头的冲击力使金属变形,可利用金属的流动惯性,迫使金属充填型腔。
②在锤上可实现多工步成形,锤头打击速度快,生产效率高。
③模锻锤的导向精度不高,锤头行程不固定,模锻件的尺寸精度不高。
④无顶出装置,锻件出模困难,模锻斜度可适当大些。
⑤生产操作方便,劳动强度比自由锻小。
模锻件的分类●按照锻件分模线和主轴线(通过锻件各截面重心的连线在平面图上的投影)的形状以及锻件在平面图上轮廓尺寸比例,将模锻件分为:短轴类锻件长轴类锻件复杂类锻件模锻件的分类短轴类锻件:锻件在平面图上两个相互垂直方向的尺寸相等或相接近,在水平面上的投影为圆形或方形。
主要变形工步的锤击方向与主轴线平行,模锻时金属沿高度、宽度、长度方向同时流动,属于体积变形。
如齿轮、法兰盘、十字头等锻件。
模锻件的分类长轴类锻件:轴线的长度大于其它两个方向的尺寸,锤击方向与轴线垂直,金属沿主轴线流动小,主要沿高度和宽度方向流动。
如连杆和直轴等。
模锻件的分类复杂类锻件:具有短轴类和长轴类两类锻件特征的组合。
模锻件的工艺性便于锻后拔模:如图所示零件,上、下端面及柱面上均带有侧凹,不论将分型面设于什么位置,都不能保证锻后拔模,因此,必须增设锻造余块(敷料)改变锻件外形轮廓。
模锻件的工艺性力求形状简单、对称,避免截面差别过大的凸起、凹入或壁厚过薄:图a)所示零件最小和最大截面之比小于0.5,而且凸缘直径与壁厚相差过大,模锻时,凸缘端部不易充满,容易粘模。
而且凸缘厚度过薄,锻模散热性差。
连杆零件的锻模设计

连杆零件的锻模设计目录一.设计锻件图 (3)二.绘制锻件图 (8)三.设计终锻模膛 (9)四.确定锻造设备吨位 (13)五.设计预锻模膛 (14)六.绘制计算毛坯图 (15)七.确定坯料尺寸 (25)八.制坯模膛设计 (26)九.连杆锤锻模结构设计 (31)总结 (33)参考文献 (35)一.设计锻件图1.确定分模面分模面选在最大直径中部,如图下图所示。
把复杂形状放在上模,利用锻锤打击惯性使上模成型饱满,又可以利用锻件自重从上模容易脱出。
根据零件图很容易确定上下模对称直线分模。
分模面零件图2.确定加工余量和公差初估算锻件的质量为1.4kg;经查表40钢材质系数为M1;形状复杂系数属s3级。
S= mfmn=140024⨯⨯4⨯7.8510=0.19,查表5—3得水平方向和厚度方向的单边加工余量为 1.7~2.2mm,取2mm。
经查表5—4得高度公差为2.0 1.40.6+-mm,长度公差为2.8 1.90.9+-mm,宽度公差为2.2 1.50.7+-mm,错差公差为0.6mm残留飞边公差为0.7mm。
厚度公差经查表5—5,为2.0 1.50.6+-mm。
因该连杆机械加工时以大小头断面为定位基准,为保证平面度锻件在热处理、清理后要增加一道压印工序(平面冷精压)。
压印后机加工余量单边取0.75mm压印所需余量单边为0.4mm,则压印后大小头高度为(38+2×0.75)mm=39.5±0.2mm,模锻后大小头高度为(38+2×0.75+2×0.4)mm=40.3mm,考虑到保证压印有余量,模锻后厚度公差调整为1.3 1.00.3+-mm.考虑到大头叉部成型困难,故宽度公差增加,压印后,水平方向压印略有增加,故加工余量可适当减少,表现在宽度公差取3.5 2.51.0+-mm,长度公差取1.5 1.50+mm.表2-6 锤上模锻水平方向尺寸公差(mm)表2-7 内、外表面的加工余量Z1(单面)(mm)3.确定模锻斜度为了使锻件易于从模堂中取出,一般锻件与模堂壁接触部分须带一定的斜度,这斜度称为模锻斜度。
基于Proe的连杆及盖锻件锤锻模设计

榔
l
( 4) 终 锻 与 预 锻 模 膛 的 最 小 壁 厚 符 合
舶 m 撕
匹 / 口 ,
滩 撬 鏖
、I 90
S o: k 1 × h( 当h <3 0 时, k 1 取1 . 5 ) 。
/
I f 嵫
I
: 帚
一
2 . 3 . 2 坯 料尺 寸的 确 定
模 膛 宽 度B应 按 B= ( 1 . 4 ~1 . 6 )d 坯, 最
坯料 截 面 的 计算 根 据 变 形工 步 计 算 后 确 定 为7 0 宽。 坯 料 截 面 F 对 于 采 用 拔 长 滚 压 且 聚 料 作 用 显 著 坯 设 计 的滚 压 模 膛 如图 2 所示。
( 上接8 9 页)
免 交流 1 l 5 V、 4 0 0 HZ 的 插 针 与低 功率 插 于 空 间限制 或 其 他 原 因, 无 法 满 足设 计 要求
电缆 屏蔽 层在 连 接 器尾附 件 处 的屏 蔽端 接 ;
针( 如直流2 8 V和5 V) 相邻布局。 工程 上 时 , 可采 取 其 他效 果 相 当的措 施 电 磁防 护 偏
原料, 是 一种 科学 实用 的 模 具 设 计 方 法 , 在
轴头 、 转 向壁 等 同 类 锻 件 模 具 设 计 中采 用
1
后, 效 果显 著。
6 0一 _ 了 Q
7 0
l 巧 一
= I 二一
‘ 5 O
图2
2 1 0
.
参考 文献
… 1 锻模设计手册编写组编著. 锻 模 设 计 手 册[ M】 . 机 械 工业 出版 社 , 1 9 9 0 . [ 2 】詹 友 刚 . P r o /E 高级 应 用 教 程 [ M] . 机 械 工业 出版 社 , 2 0 0 8 . 【 3 】周大 隽 . 锻 压 技 术数 据 手 册【 M】 . 机 械 工
锤上模锻工艺及模具设计

二、飞边槽的确定
开式模锻的终锻型腔周边必需有飞边槽,其形式及尺寸大小
对锻件成形影响很大。
1、金属变形分析:
第一阶段:从开始模压到金属与模具侧壁接触为止的镦粗变形 阶段。高度减小,径向尺寸逐渐变大,变形力不是 太大。
第二阶段:飞边形成阶段:金属一方面充填模腔,一方面由桥 口处流出形成飞边,并逐渐减薄。这时由于模壁阻 力,特别是飞边桥口部分的阻力作用,迫使金属充 满型腔。金属处于三向压应力状态,变形抗力迅速 增大。
模壁产生一个脱模分力P型Sin 来抵消模壁 对锻件的摩擦阻力Tcos ,从而减小取出
锻件所需的力P取出:
P取出 Sin
= Tcos
),
- P 型 Sin =P 型 ( Cos – 越大,P取出就越小,大到一
定值后锻件会自行从型槽中脱开。
3、常用斜度:锻件冷却后,其外壁因收缩而离开型腔,容易出模, 而内壁收缩,则使锻件包住型腔突出部分,出模困难,因此,内斜 度应比外斜度大一级。
⑴ 锻件热处理及硬度要求,测试硬度的位置;
⑵、未注明的模锻斜度和园角半径;
⑶、允许的表面缺陷深度(包括加工表面和非加工表面);
⑷、允许的错移量和残余毛边的宽度;
⑸、需要取样进行金相组织和机械性能实验时,应注明锻
件上的取样位置;
⑹、表面清理方法;
⑺、其他特殊要求,如同心度,弯曲度等。
第四节 终锻型腔的设计
⑵、当设备吨位不足产生模锻不足(打不靠),可适当减小 锻件的高度尺寸(因为锻件在高度方向有个打不靠的值),其值 可接近负偏差;相反,当设备吨位偏大或锻模承击面不够时,易 产生承击面塌陷时,可适当增加热锻件图的高度尺寸,其值可接 近正公差;
塑性成形工艺第十一章锤上模锻工艺及模具设计

第三节 终锻型腔的设计
四、飞边槽的确定
1)容纳多余的金属; 2)增加金属流入型腔的阻力,迫使金属更好地充满型 腔; 3)起缓冲作用,减轻上下模打击,防止锻模早期破裂 和压塌; 4)容易切边。
第三节 终锻型腔的设计
四、飞边槽的确定 1.飞边槽的形式
第三节 终锻型腔的设计
五、钳口的选定
钳口是供放置钳子夹持毛坯用,当浇型检验型腔 时,钳口可作浇型的浇口。在终锻型腔和预锻型腔的 前端一般要设计钳口。
β=Lj/dP越大,金属沿轴向移动的距离越大,应采用 拔长效率较高的制坯工步; 锥度K=(dk-dmin)/Lg越大,金属在制坯型腔中变形时 作用在金属上的水平分力越大;
锻件的质量M越大,标志着流动金属的体积越大;
第四节 预锻型腔的设计
2、制坯工步的确定 需综合考虑如下因素:
第五节 其它腔的设计
第四节 预锻型腔的设计
一、预锻型腔的设计
2.型腔的宽与高;
预锻后的毛坯在终锻过程中应以镦粗成形为主。 因此,预锻型腔的高度应比终锻型腔的大2~5mm, 宽度则比终锻型腔小1~2mm;横断面积应比终锻 型腔稍大一些,即预锻型腔的容积略大于终锻型腔, 预锻型腔不设飞边槽。
第四节 预锻型腔的设计
一、预锻型腔的设计 3.模锻斜度;
第十一章 锤上模锻工艺及模具设计
锤上模锻的特点:
4.由于无顶出装置,锻 件出模困难,模锻斜 度可适当大些;
5.生产操作方便,劳动 强度比自由锻小。
第一节 模锻件的分类
按照锻件分模线和主轴线的形状,以及锻件在平 面图上轮廓尺寸比例,将模锻件分为三类:
第二节 模锻件图的制定
模锻件图是确定模锻工艺和设计锻模的依据,它又 是指导模锻工进行生产和检验人员验收锻件的主要技术 文件。
锻造工艺与模具设计-锤上模锻

带连皮的模锻件,不需绘出连皮的形状和尺寸。产品 图的主要轮廓线要用点划线在模锻件图上表示,便于表示 各部分的加工余量。
锻造工艺与模具设计-锤上模锻
6.3.6 锻件图和锻件技术条件
锻件图(冷)是在零件图基础上,加上余量、余块 或其它特殊留量后绘制的图,图中锻件外形用 粗实线表示,零件外形用双点划线表示。 锻件的公称尺寸与公差注在尺寸线的上面,而 零件的尺寸注在尺寸线的下面的括号内。
α大到一定值时,可自动脱模,但α太大将会增大 金属的消耗量和余量。
但是,为了便于出模,高度较小的锻件可采用较
大的斜度,这时,多消耗的金属量不大。如:
H<50mm,查到3°改为5°;H<30mm,查的3°
、5°一律改为7°。
锻造工艺与模具设计-锤上模锻
(2) 同一锻件上内模锻斜度要比外模锻斜度大。 (大小原则)原因在于锻件冷却时,外壁趋向离开模 壁,而内壁正相反。
锻造工艺与模具设计-锤上模锻
1、热锻件图设计
热锻件图是将冷锻件图的所有尺寸计入收缩 率而绘制的。钢锻件的收缩率取1.2%-1.5%; 钛合金锻件取0.5%-0.7%;铝合金锻件取 0.8%-1.0%;铜合金锻件取1.0%-1.3%;镁合 金锻件取0.8%左右。 加放收缩率时,对无坐标中心的圆角半径不 加放收缩率;对于细长的杆类锻件、薄的锻 件、冷却快或打击次数较多而终锻温度较低 的锻件,收缩率取小值;带大头的长杆类锻 件,可根据具体情况将较大的头部和较细杆 部取不同的收缩率。
状越复杂,见表6-2:
级别 代号 形状复杂系数值S 形状复杂程度
Ⅰ S1
0.63~1
简单
Ⅱ S2
0.32~0.63
一般
Ⅲ S3
0.16~0.32
- 1、下载文档前请自行甄别文档内容的完整性,平台不提供额外的编辑、内容补充、找答案等附加服务。
- 2、"仅部分预览"的文档,不可在线预览部分如存在完整性等问题,可反馈申请退款(可完整预览的文档不适用该条件!)。
- 3、如文档侵犯您的权益,请联系客服反馈,我们会尽快为您处理(人工客服工作时间:9:00-18:30)。
2.7 热锻件图 2.8 飞边槽 作用:容纳多余金属,对锻造时飞边起缓冲作用
飞边槽设计
2.9 钳口 2.10 吨位计算 2.11 终段 型腔建模
选取最大截面处分模 2.2 余量及公差 由《模锻简明设计手册》可确定模锻件长度,宽度,高度的公差 长度公差:+1.3������������ − 0.7������������ 宽度公差:+1.1������������ − 0.5������������ 高度公差:+1.2������������ − 0.6������������ 大小头的加工余量为:1.7~2.8������������ 水平尺寸加工余量为:2.0~2.5������������ 2.3 拔模斜度 查设计手册可得本次零件的拔模斜度为7° 2.4 冲孔连皮 一般情况下孔径大于 30mm 的时就需要考虑冲孔连皮,连皮厚度可按以下 操作
ℎ < 0.4������������ = 0.12������ + ������������������������������ = 1.35������������ ������������������������ = 0.65������������
2.5 圆角 一般锻件圆角为 1mm,1.5mm,2mm,2.5mm 等数值 该锻件大段去 2mm 圆角 小端部位取 3mm 圆角 2.6 终段件与零件之间的比较“连杆零件来自上锻模工艺及模具设计”基本流程
“连杆零件锤上锻模工艺及模具设计”基本流程
1. 连杆零件分析 1.1 锤上模锻的特点及设计方法 特点: ①工艺灵活, 适应性广, 可以生产各类复杂锻件; 可单型槽模锻, 也可多型槽模锻;可单件模锻,还可多件模锻或一料多件连续 模锻; ②锤头的行程、打击速度和打击能量均可调节; ③冲填型槽能力强; ④可以提高零件的使用寿命; ⑤生产效率高; ⑥模锻件机械加工余量小,材料利用率高,锻件生产成本较低; 设计方法:1.锻件图设计;2.计算锻件的主要参数;3.锻锤吨位的确定;4.确定 飞边槽的形式和尺寸;5.终锻模膛的设计;6.预锻模膛设计; 7.绘制计算毛胚图;8.制胚工步选择;9.确定胚料尺寸;10. 其他模膛设计;11.模锻结构设计;12.模锻工艺流程设计。 1.2 零件的基本特征 连杆: 作用是传递活塞与曲轴间的作用力,并将活塞的往复运动变成曲 轴的旋转运动。 连杆为模锻件, 由连杆小头、 杆身和连杆大头组成,
小头为薄壁圆环结构,杆身为长杆零件,零件结构复杂 连杆总长度:230mm,最宽处:88mm,大头厚度:18mm,小头厚度:30mm,大头孔直 径:38mm,小头孔直径:22mm 材料:一般采用 45 钢、40Cr、或 40MnB 等调质钢 1.3 连杆零件建模 1.4 文件检索,连杆锻造成形方法 2. 连杆终段件设计及模具型材设计 2.1 分模面