轿车连杆精密辊锻_模锻复合锻造工艺
浅谈汽车连杆模锻工艺及其配套设备

GF 轿车连杆重量要求 390 克~410 克,即重量公差±10 克,实际测量 120 件,控制在 388 克~398 克,即实际重量公差控制在±5 克。
h
lj
GF轿车连杆 材料:40Cr
技术要求 1.连杆体经调质处理,硬度为223~280HBW,硬度差不大于 35HBW。 2.连杆纵向剖面的金属宏观组织的纤维方向应沿连杆中心线 并与外形相符,无紊乱及间断现象。 3.成品连杆的金相显微组织在连杆头工字形截面应均匀晶粒 索氏体结构,不允许有片状铁素体和非金属夹杂物存在,脱 碳层在工字形表面不得大于0.1。 4.尺寸按交点标注,[]为精锻尺寸,模锻斜度为5-7°,未 注圆角R2-3。 5.连杆不得有因金属未充满锻模而产生的缺陷,不得焊补。 6.连杆毛坯应进行抛丸强化处理。 7.连杆非加工面不得有裂纹、夹层、夹渣、折叠、氧化皮、 锈蚀等缺陷,分模面飞边高度不大于0.5,错模量小于0.3。 8.连杆应进行磁力探伤,并应退磁处理。 9.未注锻造尺寸公差按GB12362-90《钢质模锻公差及机械教 加工余量》精密级执行。 10.其余按JB/6721-93《内燃机连杆技术条件》执行。 12.连杆锻件重量应为(390~410)kg。
图 4 GF 轿车发动机连杆体锻件图
Ii
图 5 生产过程
|:!
图 6 辊锻毛坯图
63
1■—■——r——互 图 7 GF 轿车连杆终锻锻件图(一模两件)
k√’
图 8 切边后的连杆
自动锻造连杆生产线
由于汽车规模的迅猛扩张及结构的转变,发动机连杆的需求量也日益增加,一些企业也专业从事连杆
、 的锻造生产,可以形成批量生产,由于生产制造过程人力成本的上升,原有的多台组线手工锻造生产线已
■曹 成形。增设“解除闷车装置”满足一旦操作不当造成机床闷车,能够方便的解除,不损坏机床和模具。
轿车连杆精密辊锻_模锻复合锻造工艺_杨慎华

轿车连杆精密辊锻—模锻复合锻造工艺
杨慎华 邓春萍 金文明
( 吉林大学)
【 摘要】 针对轿车连杆锻件的特点、 技术条件与要求, 提出一种精密辊锻—液压模锻锤模锻复合工艺, 并进行 了 精密锻造工艺设计及模具设计。以广州本田轿车连杆体精密锻造成型为例, 进行了精密辊锻制坯—液压模锻锤模锻 复合工艺研究。研究结果表明, 采用此工艺生产轿车连杆件, 产品质量高, 生产稳定可靠, 比传统锤上模锻工艺节约 能耗降低 #$ ! , 锻件成本降低 !$ ! 。 原材料 !" ! 以上,
:)
从图 ! 可知, $%&& 经台架试验后表面平整
没有划痕, 含油 %’( 材料经试验后的表面有划痕及 空洞。 说明 $%&& 结构致密、 韧性好; 含油 %’( 表面 疏松, 易被较硬材料划伤。
( #) $%&& 图! ( 含油 %’( ")
$%&& 及含油 %’( 与钢摩擦后的表面形貌
$
结论
#) ")
图! 本田发动机 VEE 连杆锻件图
=
轿车连杆锻造工艺分析与方案
轿车发动机连杆在高速运动中承受着很大的交
针对本田轿车发动机 VEE 连杆锻件的特 点 以 及其严格的加工精度与很小的质量差要求,确定了 辊锻制坯—液压模锻锤模锻复合锻造工艺的流程和 工艺方案。 工艺流程:下料 ! 中频感应加热 !- 道次精密 辊锻制坯!预锻!终锻!切边! 热处理!喷丸 ! 荧 光探伤! 精压!检验。
./01 234035/67401 83509:016;:0 <40=:01
( ;:>:0 ?0:@4AB:CD ) 【 !7’6#4%6】 EFFGAH:01 CG C34 I4/C5A4B6C4F30:F/> FG0H:C:G0B /0H A4J5:A4=40CB GI 9/BB4014A F/A FG004FC:01 AGHB6/ 9A4K
汽车连杆加工工艺及夹具设计

汽车连杆加工工艺及夹具设计汽车连杆是发动机中非常重要的零部件,它连接活塞和曲轴,传递活塞的运动力到曲轴上,是发动机正常运转的关键。
因此,汽车连杆的加工工艺及夹具设计显得尤为重要。
本文将就汽车连杆的加工工艺及夹具设计进行详细介绍。
汽车连杆的加工工艺是指对汽车连杆进行加工时所采用的工艺方法和步骤。
汽车连杆的加工工艺主要包括锻造、粗加工、精加工和热处理等环节。
首先是锻造环节,汽车连杆的锻造是通过将金属坯料放入锻造模具中,利用冲击力和压力使其产生塑性变形,从而得到所需形状和尺寸的加工方法。
然后是粗加工环节,汽车连杆的粗加工主要包括车削、铣削和钻削等工艺,通过这些工艺将锻造后的汽车连杆进行初步的成型。
接着是精加工环节,汽车连杆的精加工主要包括磨削、镗削和拉削等工艺,通过这些工艺将汽车连杆进行精细加工,以满足其精度和表面质量的要求。
最后是热处理环节,汽车连杆的热处理是为了提高其强度和硬度,使其具有良好的机械性能。
在汽车连杆的加工工艺中,夹具设计起着至关重要的作用。
夹具是用来固定工件,保证工件在加工过程中的位置精度和加工质量的工具。
汽车连杆的加工对夹具的设计要求非常高,因为汽车连杆的形状复杂,加工难度大,所以需要设计出合理的夹具来保证加工质量和效率。
首先,夹具的选择要根据汽车连杆的形状和加工工艺来确定。
汽车连杆的形状复杂,需要设计出符合其形状的夹具,以保证汽车连杆在加工过程中的稳定性和精度。
其次,夹具的刚性和稳定性是夹具设计的关键。
汽车连杆在加工过程中需要承受较大的切削力和振动力,所以夹具的刚性和稳定性要能够满足这些要求。
再次,夹具的使用要方便和安全。
夹具的设计要考虑到操作人员的使用习惯和安全要求,使其能够方便地安装和拆卸,并保证操作人员的安全。
最后,夹具的成本也是夹具设计的考虑因素之一。
夹具的设计要尽量减少成本,提高经济效益。
综上所述,汽车连杆的加工工艺及夹具设计是汽车发动机制造中非常重要的环节。
合理的加工工艺和夹具设计能够保证汽车连杆的加工质量和效率,提高汽车发动机的性能和可靠性。
缪桃生:精锻连杆锻造工艺及生产线配置

[1]中国锻压协会.《现代模锻技术》培训班专用资料之连杆模锻生产技术.
为了减少投资,也可以选用小型热模锻单件生产,如北京现代连杆,其连杆生产线配置如下:
中频感应加热炉(300KW)楔横轧600T热模锻80吨单点切边机小型单点压机热校正。
楔横轧可以轧2件,自动切断,节拍7秒一件,生产效率较高。但楔横轧模具设计要求较高。
5结束语
生产线的合理配置需综合考虑产品质量要求特点、设备能力、人员素质要求、企业发展要求等各方面因素,还需不断学习国内外先进技术,以发展的眼光长远考虑,如在装备操作上逐步采用全自动生产,提高生产效率,国内锻造业只有不断提高自身的技术水平才能缩短与国外的差距,增强竞争力。
上述工艺流程中锻造成形是关键,它关系到连杆锻件的质量和生产效率及生产成本。
4生产线的配置
根据连杆质量要求及投资规模选定不同的生产线进行生产,常见的连杆生产线配置如下:
1.辊锻制坯——摩擦压力机模锻生产线配置
采用250KW中频感应加热炉进行加热, Ф400辊锻机制坯,两台摩擦压力机分别预锻和终锻,250吨闭式单点压力机进行切边,如是整体式连杆,需要配备2台切边压机分别冲孔切边或一台压机上进行复合模冲孔切边,一台摩擦压力机进行热校正,锻后冷却线或锻后余热淬火回火。
图1连杆成形方案
表1连杆成形方案比较
方案1
方案2
方案3
方案4
特点
需配备制坯手段,模具结构简单,设计方便,锻件质量容易控制,材料利用率高,所需设备吨位小,投资少,适合质量要求高的连杆;但生产效率低
无需制坯,模具设计复杂,装配要求高,杆部容易出现折叠,材料利用率低;由于受力面积均匀,偏离设备压力中心小,厚度比较均匀
3.辊锻(楔横轧)制坯——机械压力机生产线
连杆合件加工工艺及关键工序工装设计

连杆合件加工工艺及关键工序工装设计连杆是汽车发动机的重要部件之一,其质量和加工精度直接影响着发动机的性能和可靠性。
连杆的合件加工工艺及关键工序工装设计是保证连杆质量的重要环节。
本文将对连杆合件加工工艺及关键工序工装设计进行详细介绍。
连杆的合件加工工艺一般分为以下几个步骤:毛坯加工、粗加工、热处理、精加工和表面处理。
其中的关键工序包括毛坯加工、粗加工和精加工。
毛坯加工是制造连杆的第一步,主要是通过锻造、冷镦和精轧等工艺将毛坯材料加工成近似形状的连杆毛坯。
在毛坯加工中,对材料的选择、加工工艺的确定以及设备的选用都会对连杆的质量产生重要影响。
粗加工是将毛坯加工成近似形状的连杆,并完成孔的粗加工。
粗加工主要包括铣削、钻削和车削等工艺,通过这些工艺可以将连杆的外形和孔的位置精确到一定的范围。
关键在于工艺参数的确定,如切削速度、进给量和切削液的选择等。
精加工是将粗加工后的连杆进行进一步的加工,使其外形和孔的位置精确到的要求。
精加工包括磨削、钻削和车削等工艺,通过这些工艺可以实现高精度的加工要求。
关键在于工艺参数的确定和加工设备的稳定性。
在连杆的合件加工过程中,还需要进行热处理和表面处理。
热处理是通过控制材料的组织结构和性能来提高连杆的力学性能和抗疲劳性能。
表面处理是通过涂覆、喷涂或热处理等工艺来改善连杆的表面性能,增加其防锈和耐磨性能。
关键工序工装设计是保证连杆加工质量和提高生产效率的重要手段。
工装的设计要满足以下几个要求:定位准确、刚性稳定、便于调整和保持工装的寿命。
根据不同的加工工序和要求,设计具有专门功能的工装,如定位工装、夹紧工装和切削工装等。
在连杆合件加工工艺及关键工序工装设计中,需要注意以下几点:合理选择材料和加工工艺,确保连杆的质量和性能;严格控制加工工艺参数,保证每一个关键工序的加工质量;合理设计工装,保证加工精度和提高生产效率。
总之,连杆合件加工工艺及关键工序工装设计对于保证连杆质量和提高生产效率起着重要作用。
汽车连杆的加工工艺流程

汽车连杆的加工工艺流程英文回答:The manufacturing process of a connecting rod for an automobile involves several steps. Let's take a look at the typical process flow:1. Material selection: The first step is to select a suitable material for the connecting rod. Common materials used include steel alloys, aluminum alloys, and titanium alloys. The choice of material depends on factors such as strength requirements, weight considerations, and cost.2. Billet preparation: The selected material is obtained in the form of billets, which are cylindrical or rectangular blocks. The billets are inspected for any defects or impurities and then cut into appropriate lengths for further processing.3. Heating: The billets are heated to a specifictemperature to make them more malleable for the subsequent forging process. This temperature is carefully controlled to ensure proper grain structure and mechanical properties.4. Forging: The heated billets are placed in a forging press and subjected to high pressure to shape them into the desired form of the connecting rod. The forging process helps to align the grain structure, improve strength, and eliminate any porosity or voids in the material.5. Trimming and piercing: After forging, the connecting rods are trimmed to remove excess material and pierced to create holes for bolts or pins. This step helps to achieve the final shape and dimensions of the connecting rod.6. Machining: The forged and trimmed connecting rods undergo various machining operations to achieve the required accuracy and surface finish. This includes processes like milling, drilling, boring, and grinding. CNC machines are commonly used for precise and efficient machining.7. Heat treatment: The machined connecting rods are heat-treated to improve their mechanical properties. This involves processes like quenching and tempering, which help to enhance the strength, hardness, and toughness of the material.8. Surface treatment: Depending on the requirements, the connecting rods may undergo surface treatments such as shot peening, plating, or coating. These treatments help to improve corrosion resistance, wear resistance, and overall durability.9. Inspection and quality control: Throughout the manufacturing process, various inspections and quality control measures are implemented to ensure that the connecting rods meet the specified standards. This includes dimensional checks, material testing, and visual inspections.10. Assembly: Finally, the finished connecting rods are assembled with other engine components to complete the production of an automobile engine. This involves precisefitting and tightening of bolts or pins.中文回答:汽车连杆的加工工艺流程包括以下几个步骤:1. 材料选择,首先需要选择适合的材料来制造连杆。
连杆辊锻工艺

连杆辊锻工艺连杆是发动机的重要部件之一,它连接曲轴和活塞,将曲轴的旋转运动转化为活塞的往复运动,从而推动汽车前进。
因此,连杆的质量和性能直接影响着发动机的工作效率和寿命。
为了提高连杆的质量和性能,人们发明了连杆辊锻工艺。
辊锻是一种金属成形加工方法,它利用辊子的旋转和压力,将金属材料压制成所需形状。
辊锻工艺具有高效、高精度、高质量等优点,因此被广泛应用于航空、航天、汽车、机械等领域。
连杆辊锻工艺就是将连杆的毛坯材料放在辊锻机上,经过多次辊锻和热处理,最终得到符合要求的连杆。
连杆辊锻工艺可以分为以下几个步骤:1. 材料准备:选择合适的材料,进行切割、清洗、热处理等预处理工作,以保证材料的质量和性能。
2. 辊锻成形:将毛坯材料放在辊锻机上,经过多次辊锻,逐渐将其压制成连杆的形状。
辊锻过程中需要控制好温度、压力、速度等参数,以保证连杆的尺寸和形状精度。
3. 热处理:将辊锻后的连杆进行热处理,以消除内部应力和组织缺陷,提高材料的强度和韧性。
4. 机加工:将热处理后的连杆进行机加工,包括车削、铣削、钻孔等工序,以达到精度和表面质量的要求。
5. 检测:对机加工后的连杆进行检测,包括尺寸、形状、表面质量、硬度等方面的检测,以保证连杆的质量和性能。
连杆辊锻工艺的优点在于可以生产出高精度、高质量、高强度的连杆,同时还可以节约材料和能源,提高生产效率和降低成本。
因此,连杆辊锻工艺已经成为现代发动机制造业的重要工艺之一。
总之,连杆辊锻工艺是一种高效、高精度、高质量的金属成形加工方法,它可以生产出符合要求的连杆,提高发动机的工作效率和寿命。
随着科技的不断进步和发展,连杆辊锻工艺将会得到更广泛的应用和发展。
汽车典型零件制造工艺之连杆制造工艺PPT课件
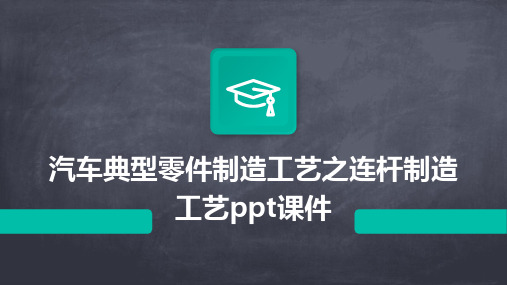
连杆制造的技术要求
精度要求
连杆的精度要求非常高,一般要求形位公差在几道甚至几 微米之内,表面粗糙度也要求非常高。
材料要求
连杆要求具有高的强度和韧性,一般采用优质合金钢或铝 合金等材料制造。
热处理要求
连杆在制造过程中需要进行多次热处理,以改善材料的力 学性能和加工性能,保证连杆的质量和寿命。
检测设备要求
。通过编程控制,可实现连杆的多道工序加工。
02
磨床
磨床用于连杆的磨削工艺,根据连杆的不同部位和加工要求,可选用平
面磨床、外圆磨床等不同类型的磨床。
03
专用工装
为了保证连杆的加工精度和效率,通常会根据连杆的结构特点设计专用
工装,如定位夹具、钻孔模板等。这些工装能够确保连杆在加工过程中
的稳定性和一致性。
3
数据分析与优化
利用大数据和人工智能技术,对连杆制造过程中 的数据进行分析,实现工艺参数的优化和质量控 制。
绿色制造在连杆制造中的实践与应用
精益生产
通过减少制造过程中的浪费,降 低能源消耗和原材料消耗,实现 连杆制造过程的绿色化。
能源管理
采用高效节能设备和能源管理系 统,降低连杆制造过程中的能源 消耗,实现低碳生产。
剪切、激光切割等。
铣削
铣削是连杆粗加工中常用的工艺, 主要用于去除连杆毛坯上的多余材 料,并为后续的精加工打下基础。
热处理
在粗加工阶段,连杆通常需要进行 热处理,以提高其机械性能,如硬 度、韧性等。
连杆的精加工工艺
磨削
磨削是连杆精加工的主要工艺之 一,通过砂轮对连杆表面进行磨 削,以提高其表面光洁度和尺寸
01 02 03 04
环保材料
选择环保型原材料和切削液等辅 助材料,降低连杆制造过程中的 环境污染。
- 1、下载文档前请自行甄别文档内容的完整性,平台不提供额外的编辑、内容补充、找答案等附加服务。
- 2、"仅部分预览"的文档,不可在线预览部分如存在完整性等问题,可反馈申请退款(可完整预览的文档不适用该条件!)。
- 3、如文档侵犯您的权益,请联系客服反馈,我们会尽快为您处理(人工客服工作时间:9:00-18:30)。
!"#
讨论
由图 * 可知, #) $%&& 材 料 不 论 硬 度 高 低 ( , 台架试验后启动力矩均保持在 *)0.1)0 +,-./0-) ・ 启动力矩下降的速度均低于含油 %’(。说明 2 3, 对于球头销与座间, 在要求紧密贴合、 一定应力、 往 复运动的场合, 主链既有一定刚性、 又有韧性的弹性 体( 显示了较好的耐磨性。 $%&&)
./01 234035/67401 83509:016;:0 <40=:01
( ;:>:0 ?0:@4AB:CD ) 【 !7’6#4%6】 EFFGAH:01 CG C34 I4/C5A4B6C4F30:F/> FG0H:C:G0B /0H A4J5:A4=40CB GI 9/BB4014A F/A FG004FC:01 AGHB6/ 9A4K
:)
从图 ! 可知, $%&& 经台架试验后表面平整
没有划痕, 含油 %’( 材料经试验后的表面有划痕及 空洞。 说明 $%&& 结构致密、 韧性好; 含油 %’( 表面 疏松, 易被较硬材料划伤。
( #) $%&& 图! ( 含油 %’( ")
$%&& 及含油 %’( 与钢摩擦后的表面形貌
$
结论
#) ")
$
结论
#)
采用精密辊锻制坯工艺生产轿车连杆锻件,
其产品尺寸精度高、 表面质量好, 与传统的锤上模锻 工艺相比, 可节约原材料 *= !以上, 能耗降低 +, ! , 锻件成本降低 *, !。
")
精密辊锻制坯—液压模锻锤模锻复合工艺
是生产轿车连杆的理想工艺,可用于其它类型连杆 锻件的大批量生产, 具有显著的技术经济效果。
F:B4 FG=9G50H IGA1:01 9AGF4BB GI AG>>:01 IGA1:01 /0H 3DHA/5>:F H:4 IGA1:01 :B 9A4B40C4H /0H C34 9A4F:B4 IGA1:01 9AGF4BB /0H H:4B /A4 H4B:104HL<:C3 C34 9A4F:B4 IGA1:01 9AGH5FC:G0 GI C34 FG004FC:01 AGHB GI 9/BB4014A F/A &?EM&NOP? OPM7E /B C34 4Q/=9>46BC5HD G0 C34 9A4F:B4 FG=9G50H 9AGF4BB GI =/R:01 S:>>4CB T:C3 AG>>:01 IGA1:01 /0H 3DHA/5>:F H:4 IGA1:01 /0H 3/==4A H:4 IGA1:01 :B F/AA:4H G5CLUC :B B3GT0 SD C34 A4B5>CB C3/C J5/>:CD GI 9AGH5FCB :B 1GGH /0H 9AGH5FC:G0 :B BC4/HD /0H A4>:/S>4 T340 C34 FG=9G50H 9AGF4BB :B /99>:4H :0 C34 9AGH5FC:G0 GI FG004FC:01 AGHB6/0H FG=9/A4H T:C3 C34 CD9:F/> 3/=K =4A H:4 IGA1:016FGBC GI =/C4A:/>B :B A4H5F4H SD G@4A !" ! 6404A1D FG0B5=9C:G0 :B A4H5F4H SD #$ ! /0H FGBC GI C34 IGA14H 9:4F4 :B A4H5F4H SD !$ !L
!)21 程控液压模锻锤,模具上设置预锻和终锻 !
个模腔, 液压模锻锤采用计算机程序控制, 可按具体 锻件品种设置打击次数、 打击能量。
!
!"#
精密辊锻制坯工艺与模具设计
辊锻毛坯的设计 辊锻制坯是为模锻提供合理的毛坯。设计时, 首
先根据锻件图给出截面图和计算毛坯图。辊锻毛坯 的设计应该以计算毛坯的尺寸和形状为基础,同时 要求:
按上述辊锻工艺、 模具设计与制造方法, 在广 州乐从三条锻造公司生产的本田轿车 %<< 连杆在
的表面形貌如图 ( 上接第 !! 页)
!"所示。
回复所致。
9)
从图 0 可知, $%&& 不论硬度高低( +,-./0
均有吸油现象, 但随硬度的增加吸油量减少。而 -) 因原料中含油已基 含油 %’( 材料制备的球头销座, 本饱和, 故吸油率较低。
汽 车 技 术
变应力, 因而要求连杆不仅要有很好的机械性能, 对 其尺寸精度、 质量公差、 表面质量也有严格要求。轿 车连杆锻件的质量差一般只有W*X, 1 ,这表明锻件 只有 $L! == 以下的厚度差。 图 ! 所示为广州本田发 — ’- —
・ 材料 ・ 工艺 ・ 设备 ・ 工艺方案:采用国产 !!" %& 中频感应加热炉 加热, 加热温度为 ’ ’""(’ ’)" * 。此加热设备可保 证锻件表面质量、稳定工艺过程,也可提高生产效 率、 改善劳动环境, 同时能满足自动化生产节拍的要 求。 精密辊锻制坯是该工艺方案中最关键的工序, 其 辊锻主机采用国产 +,!-,"" 型双支承辊锻机, 并配 备吉林大学锟锻工艺研究所研制的辊锻机械手, 生 产 节 拍 可 达 到 $ . / 件 。 模 锻 工 序 采 用 国 产 01$#截面积。 辊锻道次按下式计算:
水平直接影响发动机整机的制造水平与产品质量。 就制造工艺而言,连杆属于难锻造与难加工的一种 零件。为此, 针对轿车连杆锻件的特点、 严格的技术 条件与要求,提出了采用精密辊锻—液压模锻锤模 锻复合工艺并以广州本田轿车 VEE 连杆体精密锻 造成型为例,进行了精密辊锻制坯—液压模锻锤模 锻复合工艺研究。
甲醛制备球头销座。 晨光化工研究院) 的聚酯弹性体启动力矩保持平稳, 强度、 硬度高降低摩擦
参 考 文 献
因数及磨损量。
* 0
胡 萍 等)热 塑 性 聚 酯 弹 性 体 的 性 能 及 在 汽 车 工 业 中 的 应 用 ) 湖北汽车 ;*774 , 1+ ( 1) 朱 绍 忠 等 译) 热 塑 性 弹 性 体 手 册)北 京 : 化学工业出版社,
图! 本田发动机 VEE 连杆锻件图
=
轿车连杆锻造工艺分析与方案
轿车发动机连杆在高速运动中承受着很大的交
针对本田轿车发动机 VEE 连杆锻件的特 点 以 及其严格的加工精度与很小的质量差要求,确定了 辊锻制坯—液压模锻锤模锻复合锻造工艺的流程和 工艺方案。 工艺流程:下料 ! 中频感应加热 !- 道次精密 辊锻制坯!预锻!终锻!切边! 热处理!喷丸 ! 荧 光探伤! 精压!检验。
段形状和尺寸。 按上述基本原则确定的本田轿车 <== 连杆的 辊锻毛坯图如图 ! 所示。
的制造方法及制造精度都直接影响精辊毛坯的尺寸 精度和表面质量。 在选取了型槽系、 各道次辊锻延伸 系数及各道次辊锻毛坯形状尺寸后,可以按相应矩 形法或图解方法设计计算各道次辊锻型槽的具体参 数和尺寸, 然后进行型槽的纵向尺寸设计。 辊锻型槽 的纵向尺寸设计不同于模锻型槽,因为在辊锻过程 中, 在坯料延伸的同时伴有前后滑移现象。 由于有前 滑, 型槽的长度要比毛坯相应区段的长度短。 对型槽 的每一特征段长度按下式计算: ( ! ’9! ( / ( ’D)) #) 式中, ! ’ 为型槽长; ! ( 为相应区段的毛坯长度; )为 前滑值。 前滑值 ) 的理论计算较复杂, 设计时可根据 经验选取。 对于等截面区段一般取 )9, !(8 !; 在过 渡区段前滑值 ) 与辊锻的类型有关,在增压下辊锻 时, 前滑值 ) 一般取 8 ! (’! ! , 在减压下辊锻 时 取 ! !(, !。 — #) —
图!
<== 连杆辊锻毛坯图
!"$
辊锻道次与型槽系的选择 多道次辊锻制坯可有效地解决复杂件截面差大
的问题,使制坯形状更接近于锻件展开后的直线形 状和尺寸, 减少锻件飞边, 节约原材料。辊锻道次的 计算首先要求出总延伸系数 ! $>
!""# 年
第$期
・ 材料 ・ 工艺 ・ 设备 ・ 研究设计的本田轿车 %<< 连杆第 1 道辊锻模 具如图 1 所示。 由于轿车连杆技术条件要求很高, 要得到高质 量、 高精度、 质量差小的连杆锻件, 精密辊锻毛坯必 须与模锻型槽匹配合理。因此在对连杆辊锻模具加 工时,首先采用了数控铣加工各道次辊锻型槽电 极, 再用精密数控电火花机床加工各道次辊锻模具 型腔, 最后对模具型腔进行抛光处理。同样, 对于预 锻、 终锻模具型腔也采用精密电火花加工方法。 调试中取得了满意的效果。
! $9"" / "%
( ’)
式中, "" 为 原 始 毛 坯 截 面 积 ; "% 为 辊 锻 毛 坯 的 最 小
%9?@! $ / ?@! &
( !)
通常在 ’4,(’48 内选择。 式中A! & 为平均延伸系数, 经过计算, <== 连杆的 ! $ 9B4"8。 按 ! &9’48 选 取, 则 %9,4’, , 即取 , 道次辊锻为宜。 由上述计算得 <== 连杆的 ! $ 值比较大,必须 采用 , 道次辊锻才能得到较理想的精确辊锻毛坯形 状和尺寸, 故辊锻型槽系的选择显得尤为重要。 为提 高每一道次的延伸系数, <== 连杆辊锻时选择了椭 圆 - 方型槽系, 如图 # 所示。采用椭圆 - 方型槽系可 以取大的变形量, 以减少辊锻道次、 提高生产效率, 并可避免各道次辊锻中出现折叠的现象。因为在辊 锻成型过程中, 如果辊锻工序出现折叠, 则模锻势必 带有折叠, 连杆锻件在荧光探伤时将被定为废品。